 |
 |
 |
 |
 |
 |
 |
 |
 |
 |
 |
 |
 |
 |
 |
 |
 |
 |
 |
 |
 |
 |
 |
 |
 |
 |
 |
 |
 |
 |
 |
 |
 |
 |
 |
 |
 |
 |
 |
 |
 |
 |
 |
 |
 |
 |
 |
 |
 |
 |
 |
 |
 |
 |
 |
 |
 |
 |
 |
 |
 |
 |
 |
 |
 |
 |
 |
 |
 |
 |
 |
 |
 |
 |
 |
 |
 |
|
|
|
|
|
|
|
|
|
|
|
|
|
|
|
|
|
|
|
|
|
|
|
|
|
|
|
|
|
|
|
|
|
|
|
|
|
|
|
|
|
|
|
|
|
|
|
|
|
|
|
|
|
|
|
|
|
|
|
|
|
|
|
|
|
|
|
|
|
|
|
|
|
|
|
|
|
|
|
|
|
|
|
|
|
|
|
|
|
This article should be read in conjunction with that about the 1950s and 1960s Student and Master In the early 1950s the Colchester company of England introduced three new lathes, the Student, Triumph and Mascot, all styled to closely resemble each other and with a common and easily used control system but few interchangeable parts. The lathes were assembled in what was, during the 1950s and early 1960s, Europe's largest plant devoted to the manufacture of lathes with two 300 feet-long moving-floors and a system of "flow-line" production based on automotive practice that aimed to produce a consistently high standard of quality and accuracy to "American toolroom limits of accuracy". However, like all production process, hidden factors contrived to make some lathes more accurate than others, a fact that Colchester turned to advantage by offering a special model, distinguished by black micrometer feed-screw dials, to an improved "toolroom" standard of accuracy - however, these lathes were not specially built but just those that inspectors had classified as the most accurate of a batch . Although the new design had its origins in earlier Colchester Triumph models, and had very similar-looking geared headstocks and apron controls, each of the new models was individually engineered and constructed for a particular class of work; the Student (which was to prove immensely popular during the next two decades in training establishments and small workshops) had a swing of 12 inches and a capacity between centres of 24 inches; the Triumph, with a relatively modest increase in swing to 15 inches and a capacity between centres of 30 inches/48 inches was a very much more massively constructed machine and weighted, at 19.5 cwt/20.5 cwt (2184 lbs/994 kg/ or 2296 lbs/1045 kg), almost exactly twice as much; the 17-inch swing by 54 (or 78) inch capacity Mascot was a further significant step up in mass, turning the scales at between 4620 lbs (2100 kg) in short-bed form and 5160 lbs (2345 kg) as a long-bed machine. Of the three models the Triumph is the most useful all-round machine: it takes up little room yet has a capacity and speed range that enable it to tackle most of the jobs that a repair and fabrication shop, garage, car racing team or similar outfit would be likely to undertake. All three models evolved steadily during the period 1950 to 1980 with the Triumph becoming first revised as what is sometimes jokingly referred to as the "Mark-one-and-a-half" and then, completely redesigned, as the Triumph 2000 together with a variable-speed drive version the VS2500 (there was no Mk. 2 Triumph). Although most Triumphs, especially those destined for the home market, were fitted with a bed having a detachable gap, T-slotted apron wings and an oil-bath screwcutting gearbox that was able, at the flick of a lever, to cut 36 English pitches from 4 to 60 t.p.i. and 11 metric pitches from 0.5 to 6 mm, another, cheaper model, the "Dominion 15-inch" was also manufactured. This lathe lacked the T-slotted wings, the gap bed and was fitted with English screwcutting only, although with two additional pitches of 11.5 and 23 t.p.i.. On both lathes 36 sliding feeds were available from 0.0033" to 0.048" per revolution of the spindle with the same number of surfacing feeds but at exactly half the rate (0.0015" to 0.024"). A set of extra changewheels was available to extend this range in both directions, though in some cases, when large changewheels were fitted, the otherwise inconvenient stud-mounted cast-aluminum gear and belt-drive cover had to be left off to avoid fouling the gears. Later models, probably coinciding with the introduction of the Mk. 2 in 1964, had a choice of three different gearboxes (Standard, Continental and Dominion) and, for the first time, a metric pitch leadscrew: the Standard was an improved dual English/metric unit run in conjunction with an inch-pitch leadscrew and gave 45 English pitches from 120 t.p.i. to 4 t.p.i. and 12 metric from 0,25mm to 6mm; the Continental was combined with a 6mm pitch leadscrew and generated 31 metric pitches from 0.3mm to 12mm, 32 English piches from 2.5 to 60 t.p.i. and 16 Module pitches from 0.3mm to 3.0mm. The Dominion gearbox, as before, produced only English threads but this time with the number increased to 45 and the range set from 4 to 112 t.p.i.. The lathe beds were seasoned outside for an unspecified length of time and could be ordered with induction-hardened ways at extra cost; lathes with gap-beds could turn a piece of metal 24.5 inches (620 mm) in diameter and 6 inches (150 mm) thick on their (optional-extra) 21-inch diameter faceplate and were also fitted with T slotted saddle wings, so allowing them to be used as a boring table or to accept toolposts and supplementary slides for special jobs. For the Mk. 1 and Mk. 2 models (both Triumph and Dominion) two capacities between centres were available of 30 and 48 inches (765 mm and 1220 mm). Continued below:
|
|
|
|
|
|
|
|
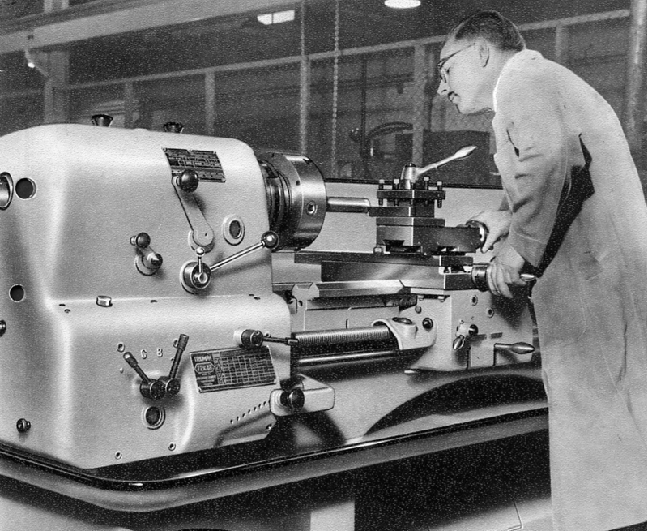 |
|
|
|
|
|
|
Above - a 1950s Triumph
Continued: The 21/16" (53 mm) bore high-tensile steel forged spindle carried an American-type long-taper key drive size L1 (with an L2 optional but seldom found) and ran in "Gamet" super precision bearings that, unusually for a lathe manufacturer, were produced in-house and supplied to other machine-tool makers (Gamet are now a separate company within the 600 Group) All the headstock gears were hardened and ground and moved by two levers on top of the headstock and one on the front; 8 speeds were provided that could, on the first models, be specified as either 30 to 600 rpm or 40 to 800 rpm; originally a single-speed 3 hp motor (later 5 hp) was fitted but within a few years machines were being offered with either an 8-speed 50 to 1000 rpm speed range or a two-speed motor that provided 16 speeds from 30 to 1200 rpm. The 3-jaw chucks fitted to these lathes when new were high-quality ones, with an integral L1 American long-nose taper backplate, made by in the UK by Burnerd. Today these special chucks are no longer available, but new standard ones can be fitted to a separate backplate - however, don't be tempted to use a cheap, unbranded import; the stresses encountered on top speed when holding large job are considerable. Instead, you are welcome to email for details of quality replacements that we can recommend.The earliest production Triumphs had their electric motor bolted to the back of the bed - but the design was quickly modified to replicate the system used on the Student and Master models where, from the start of their manufacture, the motor had been fitted in the base of the machine on a hinged platform. The drive from motor to headstock was by 3 V belts that should, when replaced, be exactly matched for length; if the geared headstock on any Colchester is unacceptably noisy, especially with rattles rather than whines, the cause may be unequal-length drive belts "fighting" each other, causing the input pulley to be accelerated and slowed in rapid succession. To check, try running on one belt to see if the headstock runs more smoothly; if it does fit a second belt, run a chalk line across the two, start the machine for a few seconds and check that the belts are still in line; they almost certainly will not be. If possible, a matched set of three should be obtained, if this cannot be done, buy a dozen belts and find the three that are the closest in length. As standard the lathe was fitted with a spindle brake, operated by a horizontal lever on the headstock front that also stopped and started the machine electrically. To start the lathe the lever had first to be pulled out against a safety spring (designed to prevent accidental engagement (a mechanism called "Safti-lok" by the makers) then lifted up. The lathe was stopped by returning the lever to its central position and then pressed down further to operate what was, when the lathe was new, a powerful drum brake built into the headstock input pulley - though Colchester's assertion that this stopped the spindle "instantaneously" revealed that writer of the handbook had either not used the lathe - or lacked a dictionary in his desk drawer. An electrical reversing switch was (at first) an optional extra and, if chosen, was neatly built onto the hub of the stop/start lever and worked concentrically with it. After many years of neglect the headstock brake first becomes ineffective and then may start to interfere with the free running of the spindle. If your Triumph (or any similar Colchester model) shows signs of slowing down or even "seizing up" after 10 to 30 minutes running the brake is the first place to look. If the shoe linings are worn out most industrial areas have a friction materials specialist who will be able to bond new material onto them. Unfortunately, unlike the competitor English Harrison lathes, a combined clutch and brake was not fitted as standard but the clutch manufactured by "Matrix" and available from the option's list was a well-designed, easily adjusted and reliable device that should still be working perfectly when the lathe reaches the end of its life. Choosing to have a clutch fitted (it was standard on machines supplied with DC or single-phase motors) meant loosing the brake, an important consideration with heavier jobs where piece-work operators would become very frustrated waiting for a 12-inch diameter 4-jaw chuck and a 100 lb job to stop spinning. On clutch-equipped lathes the motor was started by a switch on the front control panel and left running all the time the lathe was in use - the clutch being engaged by the handle previously used for the electrical stop/start. If you come across one, it is worth knowing that on the early clutch-equipped lathes the safety spring loading on the start handle was omitted. If needed, a clutch can easily be fitted to a second-hand machine (make sure you acquire all the operating linkages as well) and one is well worth seeking one to help a machine that is to be converted from 3 to 1-phase, or converter or inverter drive. Continued below:
|
|
|
|
|
|
|
|
|
|
|
|
|
|
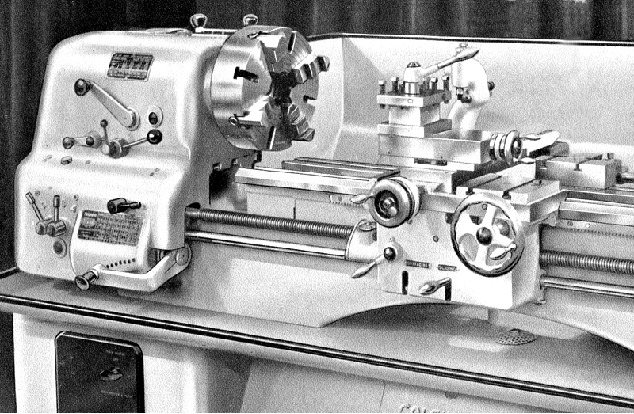 |
|
|
|
|
|
|
Continued: Double walled but open at the bottom, the apron was unable to run its gears in an oil bath; the power feed controls followed standard Colchester practice of the day being concentrated into a single lever that slid along the lower edge of the apron and was then lifted into one of two slots to engage either power sliding or surfacing. raising the lever automatically locked the engagement, whilst stopping the feed merely required the lever to be pressed downwards; unfortunately, the heavier the cut being taken, the greater the load on the mechanism and the more massive the effort required to disengage it. However, at least it was a positive action and did not require a knob to be unscrewed in order to release a clutch. Although not fitted to the first machines, most Triumphs had a cleverly-designed safety over-load ball-bearing "clutch" built into the powershaft feed to protect the apron gears; the leadscrew drive could be disengaged by a sliding gear and was only intended to be used for screwcutting. Lathes with a gap bed (as usually specified for the home market) had their carriage traverse handwheel on the right side of the apron and leadscrew clasp nuts on the left and were fitted with T-slotted saddle arms whilst on straight-bed versions (often listed in handbooks and sales catalogues as "Dominion" models) these locations were reversed and the saddle arms left flat. The last development of the Mk. 1 (before the advent of the completely different Triumph 2000) was updated in line with the Student and Master models in having a completely redesigned and much improved apron: for the first time the bottom of the assembly was enclosed, allowing the gears to run in an oil bath (although not all models had the sight-glass level indicator showing that this feature was utilised) and the selection and engagement of feeds was separated with a push-pull knob, that protruded from the middle of the front face, being to used to select the required feed with the engagement by lifting a lever at the bottom of the apron. The engagement lever had a threaded barrel (often found jammed tight) which could be screwed in and out to alter the "overload" point at which the drive automatically disengaged to protect the apron gears. By using a positive stop on the bed, and arranging for the feed to be "just held in", this formed a useful automatic disengage device by which means repeated runs could be made up to a shoulder. The "safety" apron continued to be used on the Mk. 2. Unlike early versions of the Student and Master, the Triumph's No. 3 Morse taper (later No. 4) tailstock barrel was locked not by that pet hate of the author, a slit in the casting closed down by the action of a screw thread but with a proper "split-clamp" that acted directly on the barrel at a point just before it emerged from the casting - a system that continues to work well no matter worn the components become. Although the early catalogues contained no mention of an option for dual inch and millimeter-engraved barrels some machines were so fitted and mixtures of inch, millimeter and dual-marked barrels have been found on dual English/metric and English-threading versions, presumably because that is what the original customers ordered. Later machines have dual-engraved barrels as standard with hardening on the outside and in the Morse taper - the latter also being fitted with a tang knockout slot. An option was also available for dual-marked English/metric micrometer dials to be fitted to the compound slide rest feed screws and, although the earliest catalogues from the 1950s omit any mention of them, their cover pictures shows a machine so equipped. The dual dials were beautifully made, with a sliding cover to reveal the inch or mm scales and particularly clear markings on a satin-chrome background. A version of the Triumph was sold in the USA and Canada as the "Clausing-Colchester 15-inch" this lathe had an English-threads-only gearbox but a hardened bed as standard, straight or gap, with a choice of 30" or 48" inches between centres and, on the Mk. 2 versions, an oil-bath apron version of the single-lever "Safety" apron..
|
|
|
|
|
|
|
|
|
|
|
|
|
|
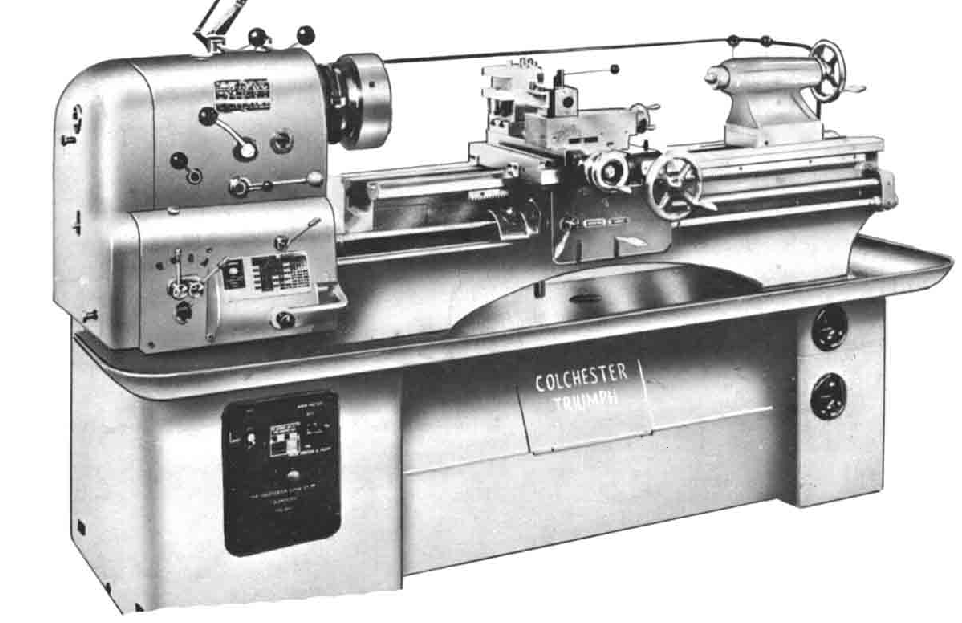 |
|
|
|
|
|
|
In this picture the distinctive arch of the bed is clearly visible - as is the short cover over the changewheels showing that this is an early lathe with the motor bolted to the back of the bed. Later versions, with the motor inside the cabinet on a hinged plate, had a shorter chip tray that allowed the gear cover to extend downwards and pick up a mounting stud on the end face of the stand.
|
|
|
|
|
|
|
|
|
|
|
|
|
|
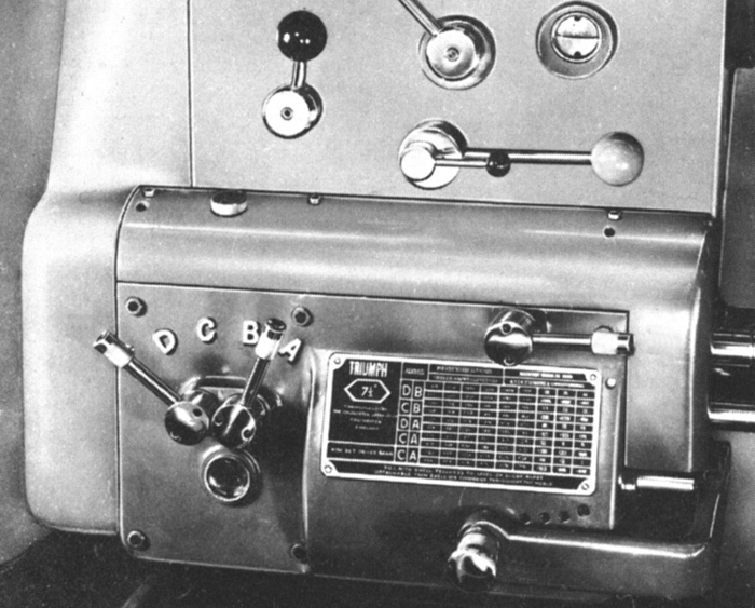 |
|
|
|
|
|
|
Although most Triumphs, especially those destined for the home market, were fitted with a bed having a detachable gap, T-slotted apron wings and an oil-bath screwcutting gearbox that was able, at the flick of a lever, to cut 36 English pitches from 4 to 60 t.p.i. and 11 metric pitches from 0.5 to 6 mm, another, cheaper model, the "Dominion 15-inch" was also manufactured. This lathe lacked the T-slotted wings, the gap bed and was fitted with English screwcutting only, although with two additional pitches of 11.5 and 23 t.p.i.. On both lathes 36 sliding and feeds were available from 0.0033" to 0.048" per revolution of the spindle with the same number of surfacing feeds but at exactly half the rate (0.0015" to 0.024"). A set of extra changewheels was available to extend this range in both directions, though in some cases, when large changewheels were fitted, the otherwise inconvenient stud-mounted cast-aluminum gear and belt-drive cover had to be left off to avoid fouling the gears. Later models had an improved gearbox with 45 English threads and feeds and 12 metric pitches; the English range stretched from 120 t.p.i. to 4 t.p.i. and the metric from 0,25 mm to 6 mm pitch with the sliding feeds varying from 0.0017" to 0.48" per revolution of the spindle and, as before, the surfacing speeds set to one-half of those values.
|
|
|
|
|
|
|
|
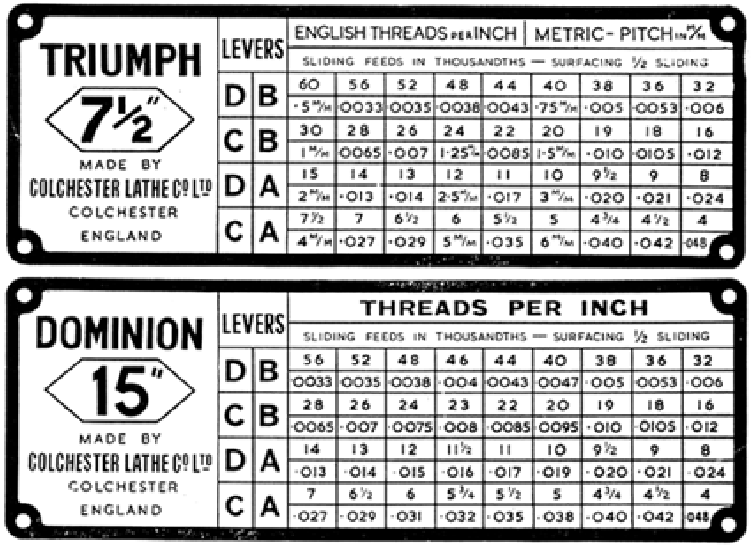 |
|
|
|
|
|
|
Screwcutting charts for early Triumph and Dominion models
|
|
|
|
|
|
|
|
|
|
|
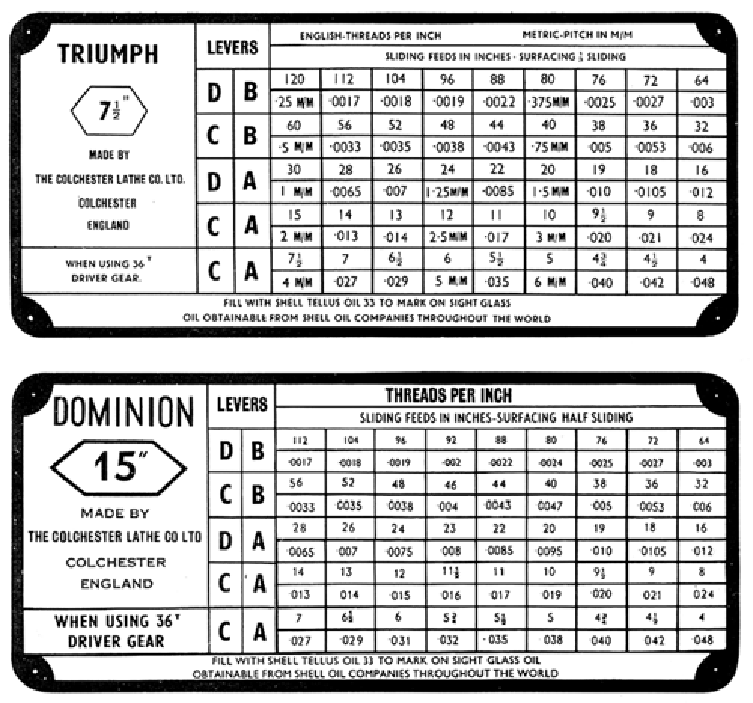 |
|
|
|
|
|
|
Screwcutting charts for later Triumph and Dominion models
|
|
|
|
|
|
|
|
|
|
|
 |
|
|
|
|
|
|
Gap-bed Triumph with T-slotted saddle wings, the apron traverse handwheel on the right and leadscrew clap nut handle on the left.
|
|
|
|
|
|
|
|
|
|
|
|
|
|
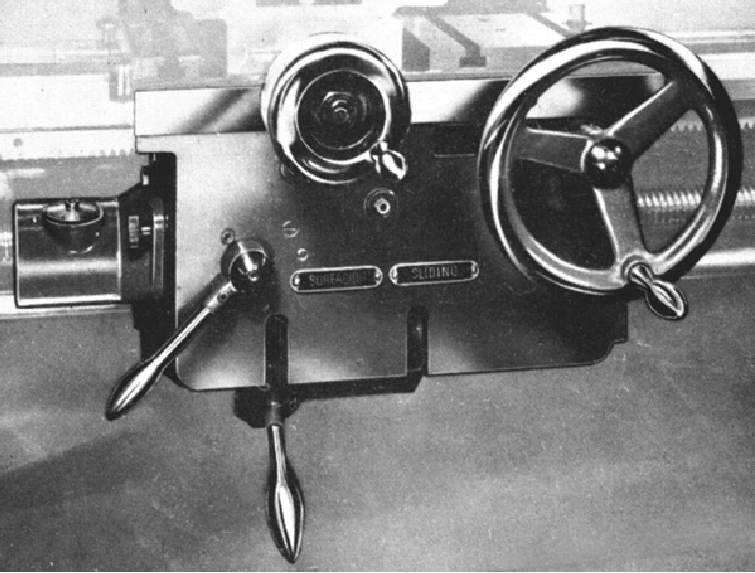 |
|
|
|
|
|
|
The apron was double walled but open at the bottom, so precluding any chance of the gears being run in oil; the power feed controls followed standard Colchester practice of the day being concentrated into a single lever that slid along the lower edge of the apron and was lifted into one of two slots to engage either power sliding or surfacing. Lifting the lever automatically locked the engagement whilst stopping the feed merely required the lever to be pressed downwards; unfortunately, the heavier the load on the feed the greater the effort required to disengage it, but at least it was a positive action and did not require a knob to be unscrewed in order to release a clutch.
|
|
|
|
|
|
|
|
|
|
|
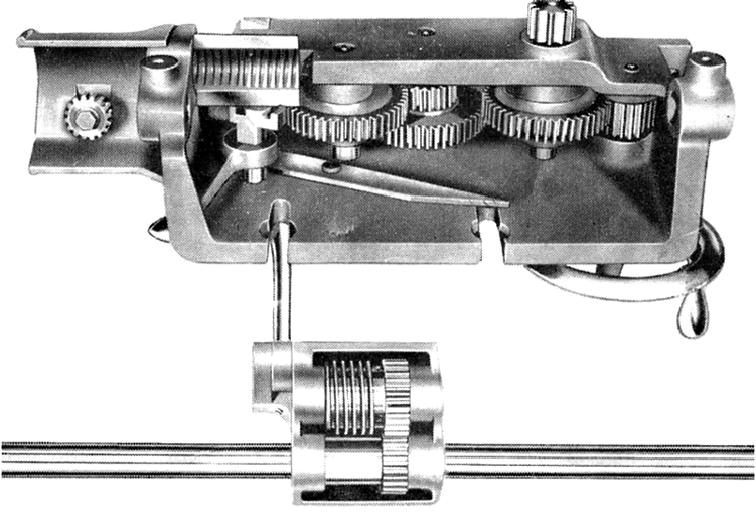 |
|
|
|
|
|
|
Interior of the apron. The long pointed arm laying against the inner wall was part of the interlock mechanism that prevented the simultaneous engagement of power feeds and screwcutting.
|
|
|
|
|
|
|
|
|
|
|
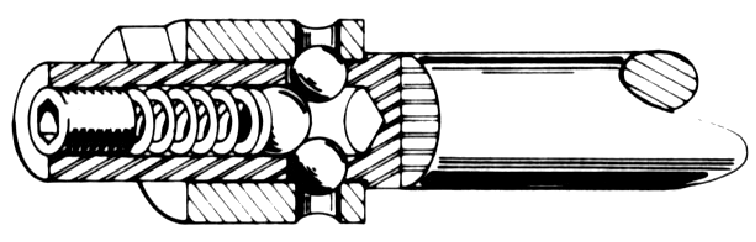 |
|
|
|
|
|
|
Although not fitted to the very first machines, most of the first-model Triumphs had a simple but ingeniously-contrived spring-loaded ball-bearing "clutch" built into the junction of the powershaft rod with its gearbox connection.. A similar design of overload protection was also used on some contemporary and as well as later Harrison lathes
|
|
|
|
|
|
|
|
|
|
|
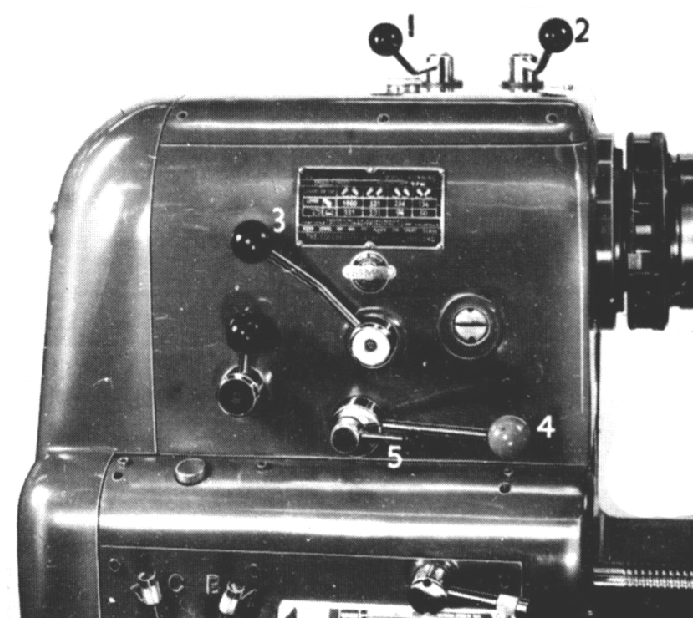 |
|
|
|
|
|
Headstock controls: 1 and 2 = spindle-speed selection levers. 3 = high/low speed range selector. 4 = electrical start/stop lever combined with brake or clutch engagement lever. 5= electrical reversing switch. The unnumbered short lever with a black knob to the left of lever 5 was used to reverse the direction of the leadscrew and power shaft.
|
|
|
|
|
|
|
|
|
|
|
|
|
|
|
|
|
|
|
|
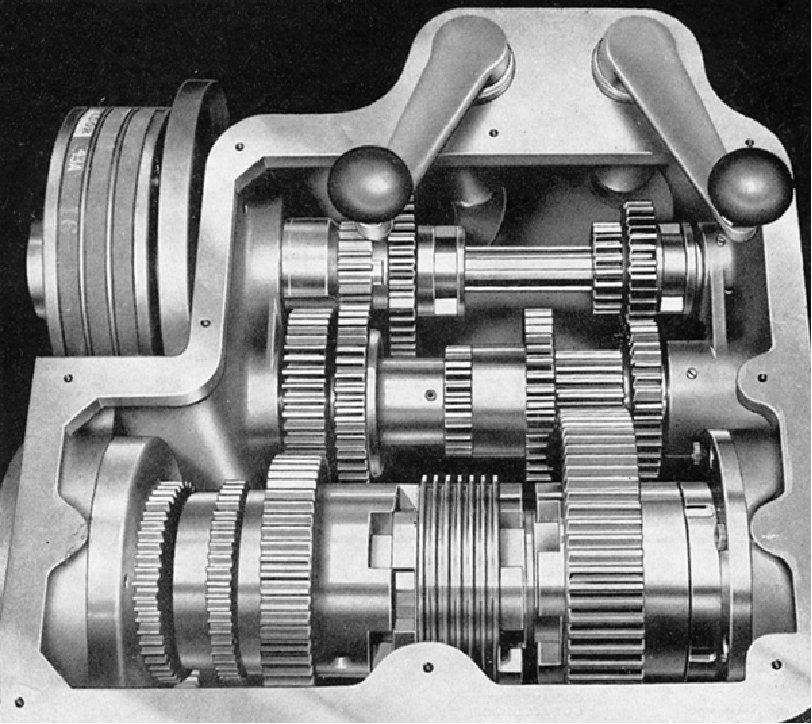 |
|
|
|
|
|
|
The 2 1/16" (53 mm) bore high-tensile steel forged spindle carried an American-type long-taper key drive size L1 and ran in "Gamet" super precision bearings that, unusually for a lathe manufacturer, were produced in-house and supplied to other machine-tool makers (Gamet are now a separate company within the 600 Group) All the headstock gears were hardened and ground and moved by two levers on top of the headstock and one on the front; 8 speeds were provided that could, on the first models, be specified as either 30 to 600 rpm or 40 to 800 rpm; originally a single-speed 3 hp motor (later 5 hp) was fitted but within a few years machines were being offered with either an 8-speed 50 to 1000 rpm speed range or a two-speed motor that provided 16 speeds from 30 to 1200 rpm. Some late models (with the single-lever safety apron) could be ordered with a top speed of 1500 rpm.
|
|
|
|
|
|
|
|
|
|
|
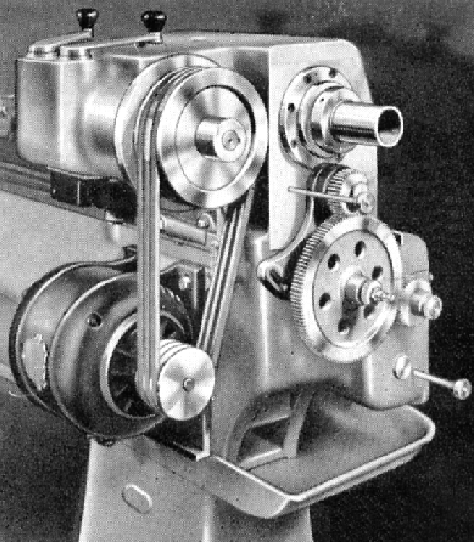 |
|
|
|
|
|
A very early Triumph with the headstock end supported on a box-section, cast-iron base and the motor fastened to the back of the bed. This machine, one of the first production batch, did not have the later standard-fitment spindle brake. Some even earlier models had a motor and gearbox reduction unit mounted close to the headstock-end leg
|
|
|
|
|
|
|
|
|
|
|
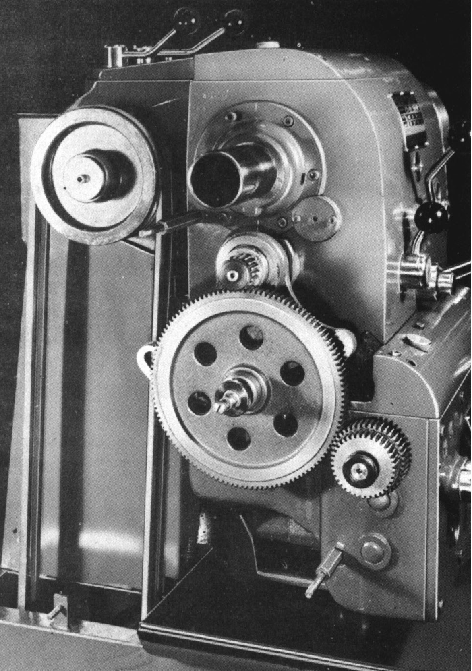 |
|
|
|
|
|
Later-model Triumph with the motor inside the cabinet stand on an adjustable plate. With the cast-aluminium changewheel cover removed from its two securing studs the whole of the end of the machine became available for inspection and maintenance.
|
|
|
|
|
|
|
|
|
|
|
|
|
|
|
|
|
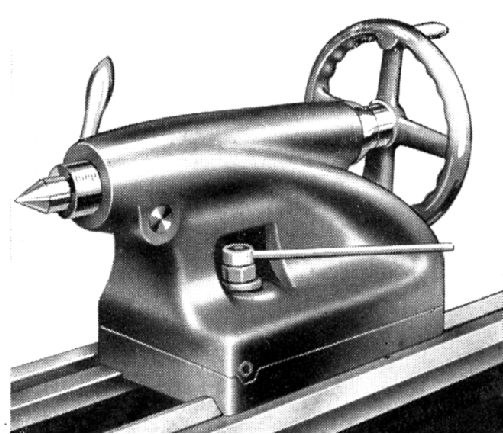 |
|
|
|
|
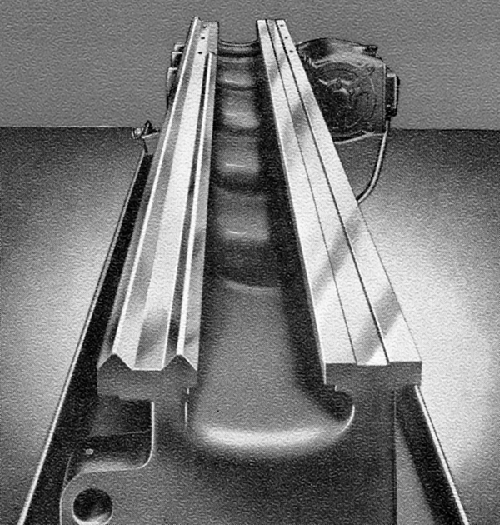 |
|
|
|
|
|
|
|
|
|
|
Unlike early versions of the Student and Master, the Triumph's No. 3 Morse taper tailstock barrel was locked not by that pet hate of the author, a slit in the casting closed down by the action of a screw thread but with a proper "split-clamp" that acted directly on the barrel at a point just before it emerged from the casting - a system that continued to work well no matter worn the components become.
|
|
|
|
|
|
|
|
|
|
|
|
|
|
|
|
|
|
|
|
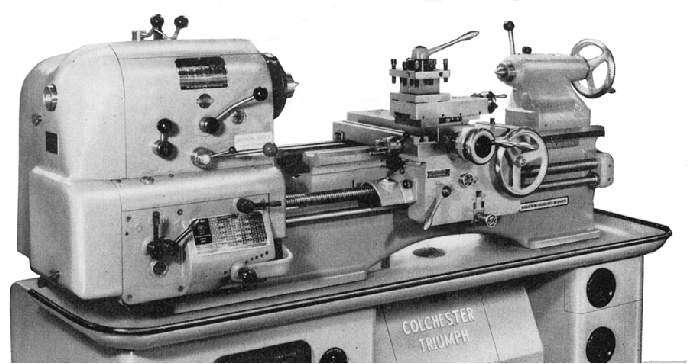 |
|
|
|
|
|
|
A "Mark-one-and-a-half" Colchester Triumph/Clausing 15-inch (the Student, Master and Clausing 13-inch were laid out in an identical fashion) with the same rounded headstock but fitted with the improved design of "Safety" apron shared with the Student and Master models. These late-models could be ordered with a top speed of 1500 rpm rather than the standard 1200 rpm.
|
|
|
|
|
|
|
|
|
|
|
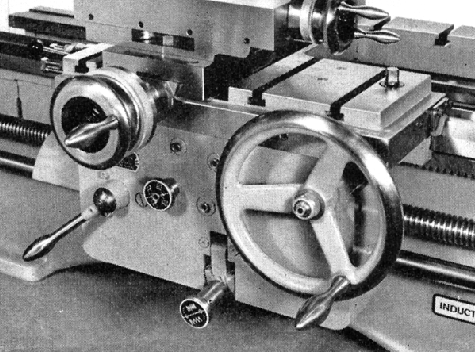 |
|
|
|
|
|
"Safety" apron as fitted to the last of the original geared-head Triumph lathes. The push/pull knob to select either power sliding or surfacing was in centre of the apron's front face and the engagement lever, which could be adjusted by turning its handle to vary the load under which the feed would automatically disengage, in the middle of the apron's bottom edge. Interestingly, the two pictures left and above are the only ones known to show a "black dial" toolroom-specification
|
|
|
|
|
|
|
|
|
|
|
|
|
|
|
|
|
|
|
|
|
|