 |
 |
 |
 |
 |
 |
 |
 |
 |
 |
 |
 |
 |
 |
 |
 |
 |
 |
 |
 |
 |
 |
 |
 |
 |
 |
 |
 |
 |
 |
 |
 |
 |
 |
 |
 |
 |
 |
 |
 |
 |
 |
 |
 |
 |
 |
 |
 |
 |
 |
 |
 |
 |
 |
 |
 |
 |
 |
 |
 |
 |
 |
 |
 |
 |
 |
 |
 |
 |
 |
 |
 |
 |
 |
 |
 |
 |
 |
 |
 |
 |
 |
 |
 |
 |
 |
 |
 |
 |
 |
 |
 |
 |
 |
 |
|
|
|
|
|
|
|
|
|
|
|
|
|
|
|
|
|
|
|
|
|
|
|
|
|
|
|
|
|
|
|
|
|
|
|
|
|
|
|
|
|
|
|
|
|
|
|
|
|
|
|
|
|
|
|
|
|
|
|
|
|
|
|
|
|
|
|
|
|
|
|
|
|
|
|
|
|
|
|
|
|
|
|
|
|
|
|
|
|
|
|
|
|
|
|
|
|
|
|
|
|
|
|
|
|
|
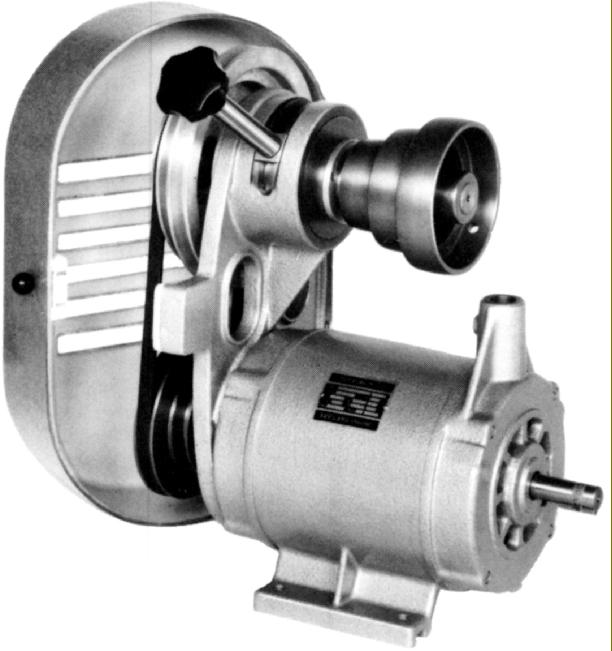 |
|
|
|
|
|
|
Motor countershaft unit for bench mounting - this unit was available under Attachment Numbers: 102.96.000 single-speed 1500 r.p.m. 0.7 kW motor and 3-step motor pulley 102.96.150 two-speed 750-1500 r.p.m 0.5/0.9 kW motor and 3-step motor pulley 102.96.200 two-speed 750-3000 r.p.m. 0.4/0.9 kW motor with 2-step motor pulley The swivel-open guard - 102.96.270 - was an extra
|
|
|
|
|
|
|
|
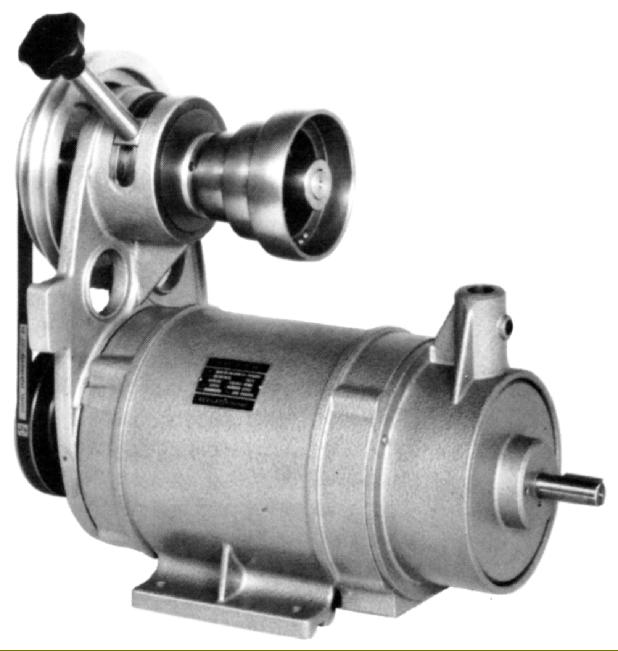 |
|
|
|
|
|
|
Motor countershaft unit for bench mounting - this unit was available under Attachment Numbers: 102.96.005 braked 1-speed 1500 r.p.m 0.7 kW motor and 3-step motor pulley 102.96.155 braked 2-speed motor 750-1500 r.p.m. 0.5/0.9 kW and 3-step motor pulley 102.96.200 2-speed motor 750-3000 r.p.m. 0.4/0.9 kW and 2-step motor pulley 102.96.205 braked 2-speed motor 750-3000 r.p.m. 0.4/0.9 kW and 2-step motor pulley
|
|
|
|
|
|
|
|
|
|
|
|
|
|
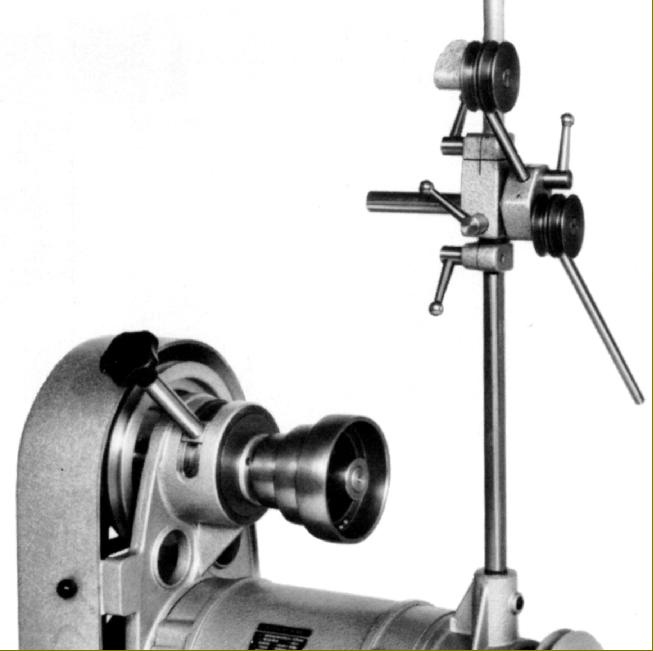 |
|
|
|
|
|
|
|
|
To drive the toolpost-mounted milling and grinding attachments on lathes that were not mounted on the maker's cabinet stand Attachment 102.95.100 socketed into the countershaft to provided a neat, self-contained solution. The unit could also be removed and transferred to another lathe by the use of a cast-iron trumpet bracket (102-95.207) that could be bolted to any flat surface.
|
|
|
|
|
|
|
|
|
|
|
|
|
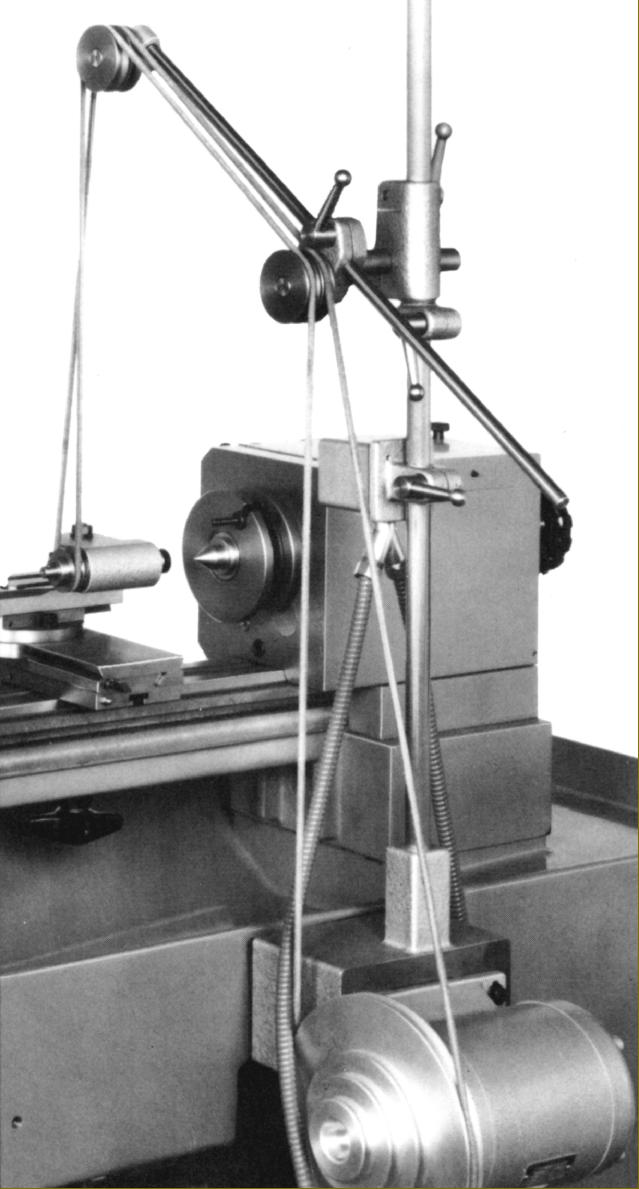 |
|
|
|
|
|
|
|
|
|
For use on the maker's stand Attachment 102-95.100/105-95.200 was supplied. This used a 150 r.p.m. 0.2 kW motor together with a special switch (71.206) carried on bracket (102-95.131) that clamped to the vertical bar of the belt-tensioning attachment. The unit was driven by a 6 mm Polycord belt.
|
|
|
|
|
|
|
|
|
|
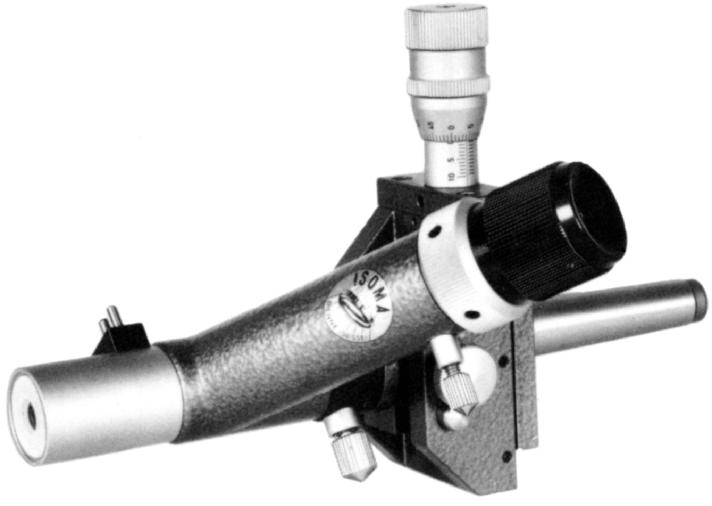 |
|
|
|
|
|
|
Attachment 102-76.200 Centring and Measuring Microscope on a No. 2 Morse taper for use in the tailstock or other applications. 60X magnification, 20 mm measuring capacity and an accuracy of 0.01 mm. This version was supplied complete with a built-in lighting unit, 220/3.5-v transformer, flex with miniature plug, 4 spare bulbs and a protective case.
|
|
|
|
|
|
|
|
|
|
|
|
|
|
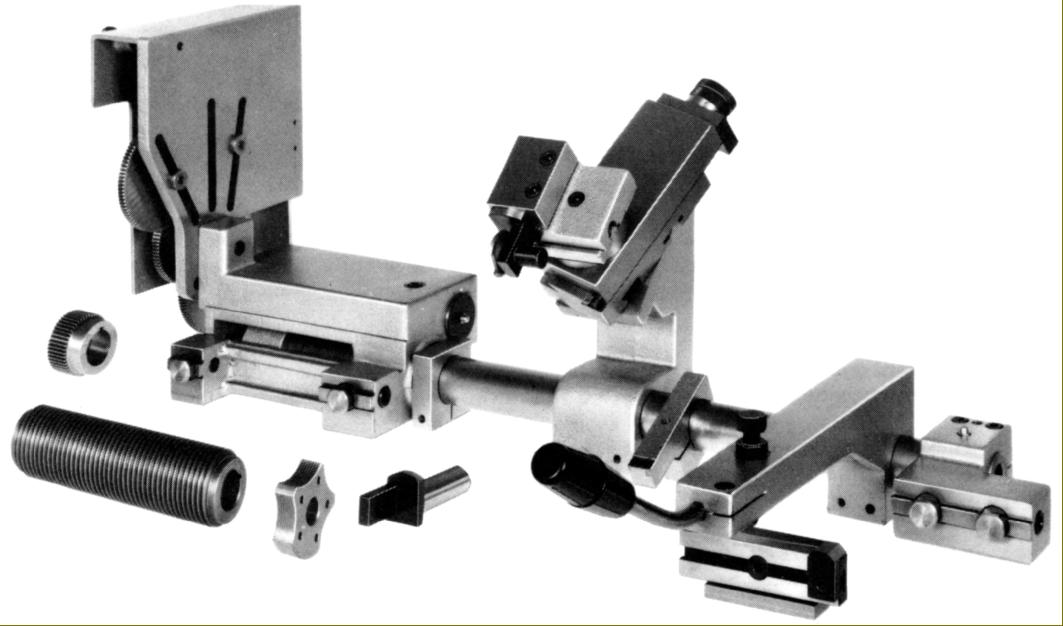 |
|
|
|
|
|
|
Attachment 105-85.200 - chase screwcutting (screwcutting by leader) combined with gears for external and internal threads. This was an accessory for the later 102N models and fitted standard W type headstock in open or closed forms with or without backgear. The maximum length that could be threaded was 100 mm and the largest diameter that could be tacked 120 mm. Pitches ranged from 0.25 to 3.00 mm and 90 to 8 t.p.i. The toolholder micrometer dial was fitted with a vernier scale that allowed positional readings down to an accuracy of 0.02 mm to be made. Drive to the unit was by a gear mounted on the headstock spindle - but on headstocks with a manually-operated collet closer the operating handle had to be changed for a special one (105-85.240) and closing sleeve modified so that it could serve as the driver.
|
|
|
|
|
|
|
|
|
|
|
|
|
|
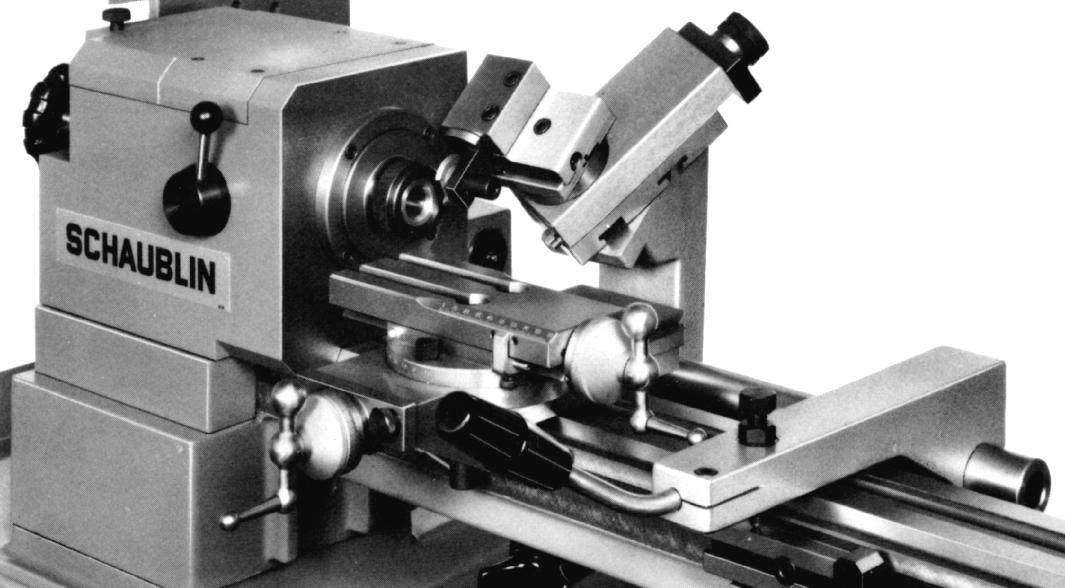 |
|
|
|
|
|
|
Chase screwcutting Attachment 105-85.200 mounted on the lathe
|
|
|
|
|
|
|
|
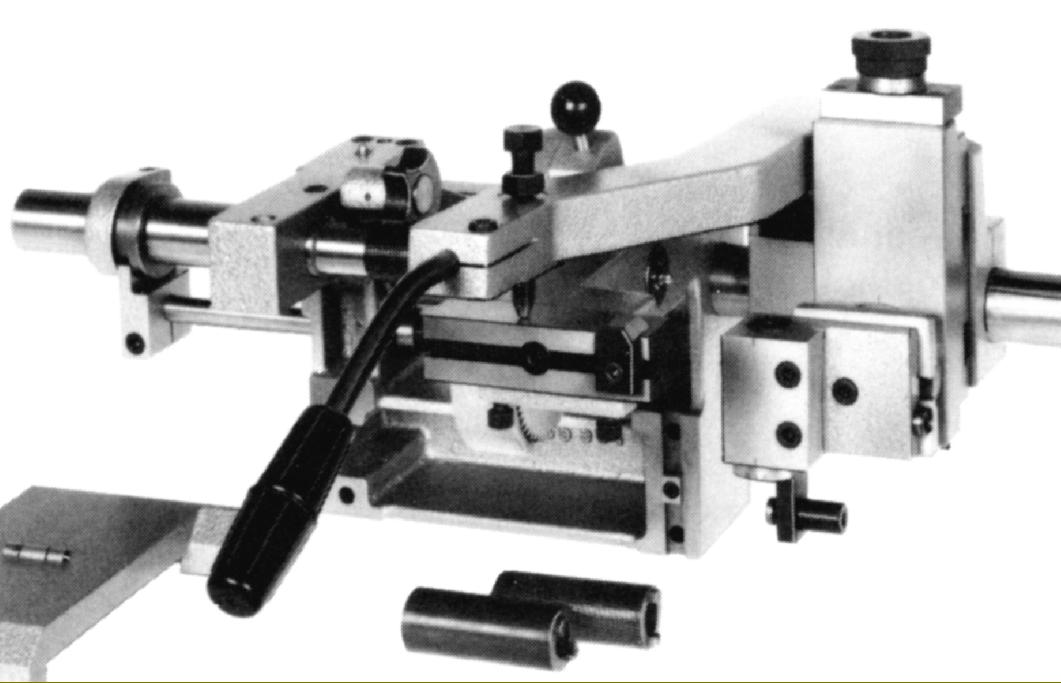 |
|
|
|
|
|
|
Attachment 105-35.500 - chase screwcutting by master thread for use only 102N lathes fitted with closed headstocks types F27, F38, W and F. Because the unit was more tightly integrated with the headstock than other chase systems the design allowed a rapid switch from right to left-hand threading and back again.
|
|
|
|
|
|
|
|
|
|
|
|
|
|
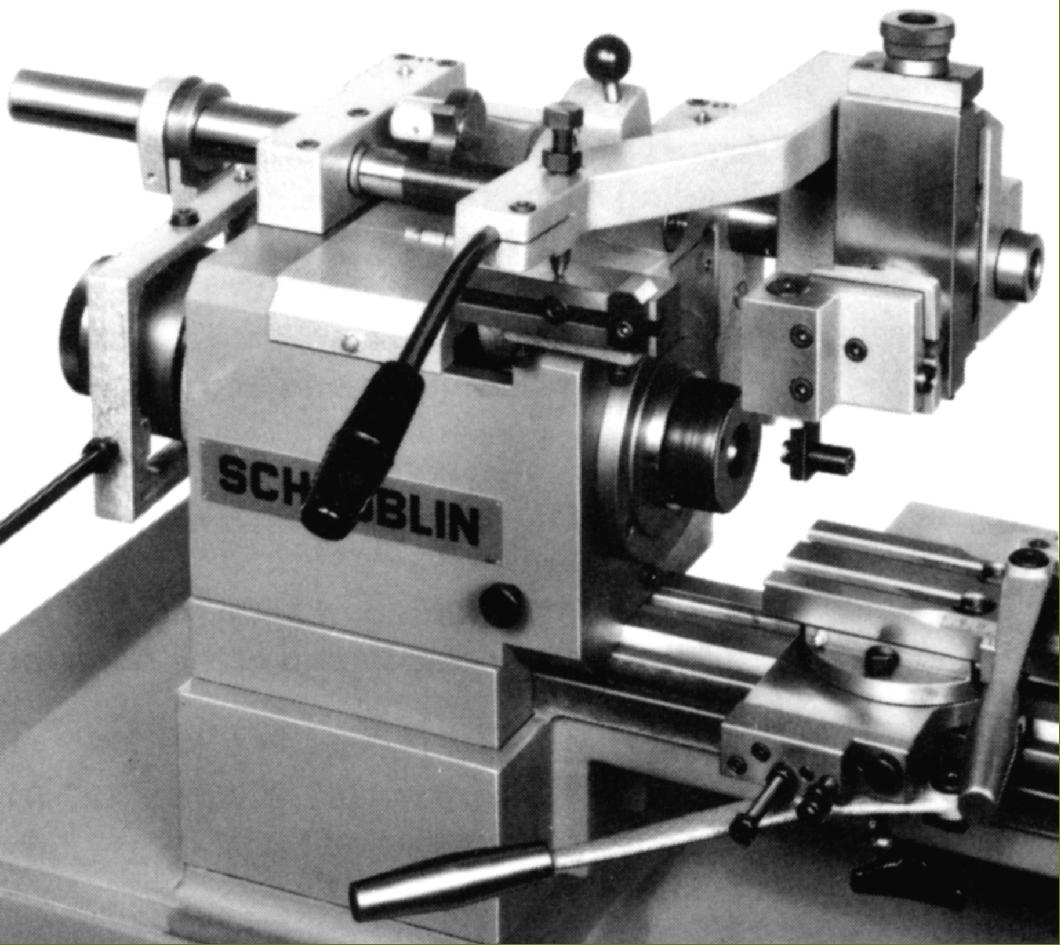 |
|
|
|
|
|
|
Attachment 105-35.500 - chase screwcutting by master thread--in place on a 102N lathe
|
|
|
|
|
|
|
|
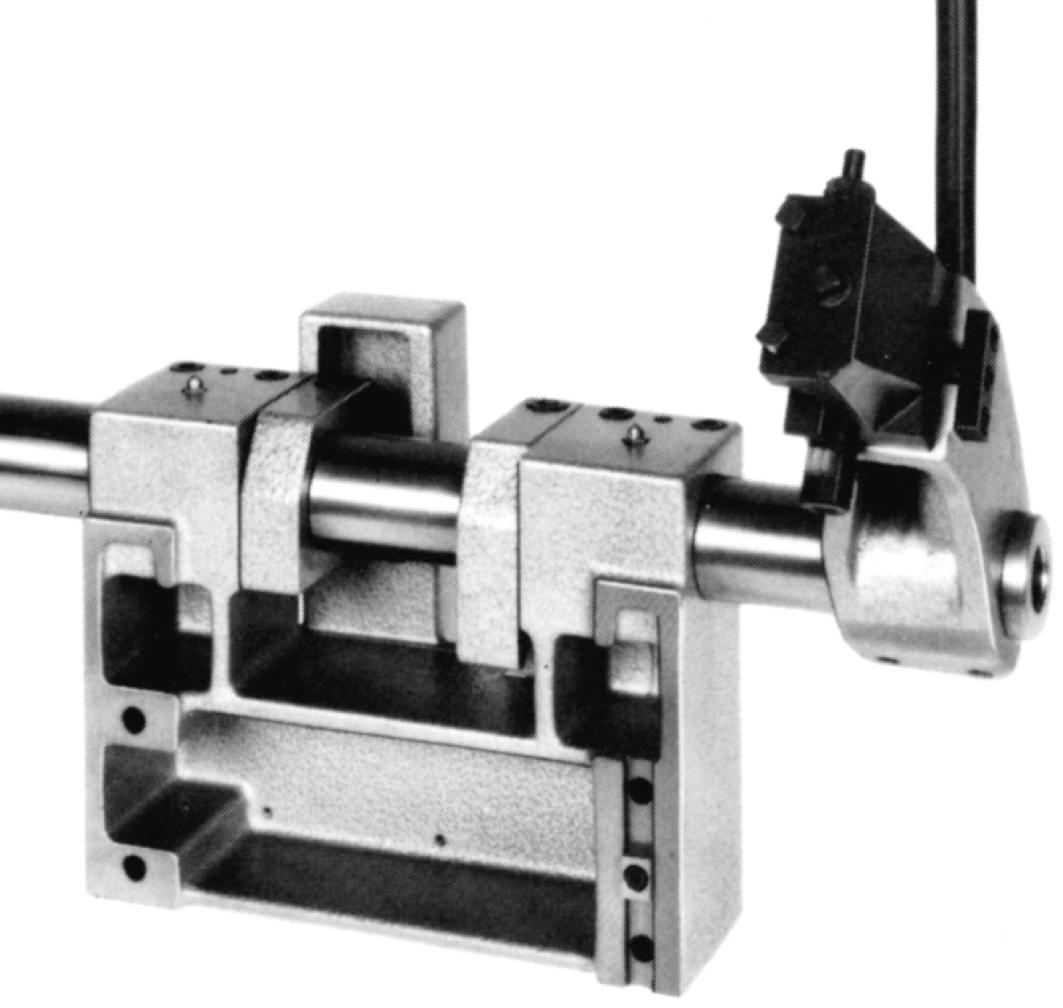 |
|
|
|
|
|
|
Attachment 105-35.600. If, when working on very small jobs, the turret tooling had to be held close to the spindle nose there was often insufficient room to accommodate the normal bed-mounted cut-off slide. This attachment got round the problem by mounting the parting-off tool holder on the headstock.
|
|
|
|
|
|
|
|
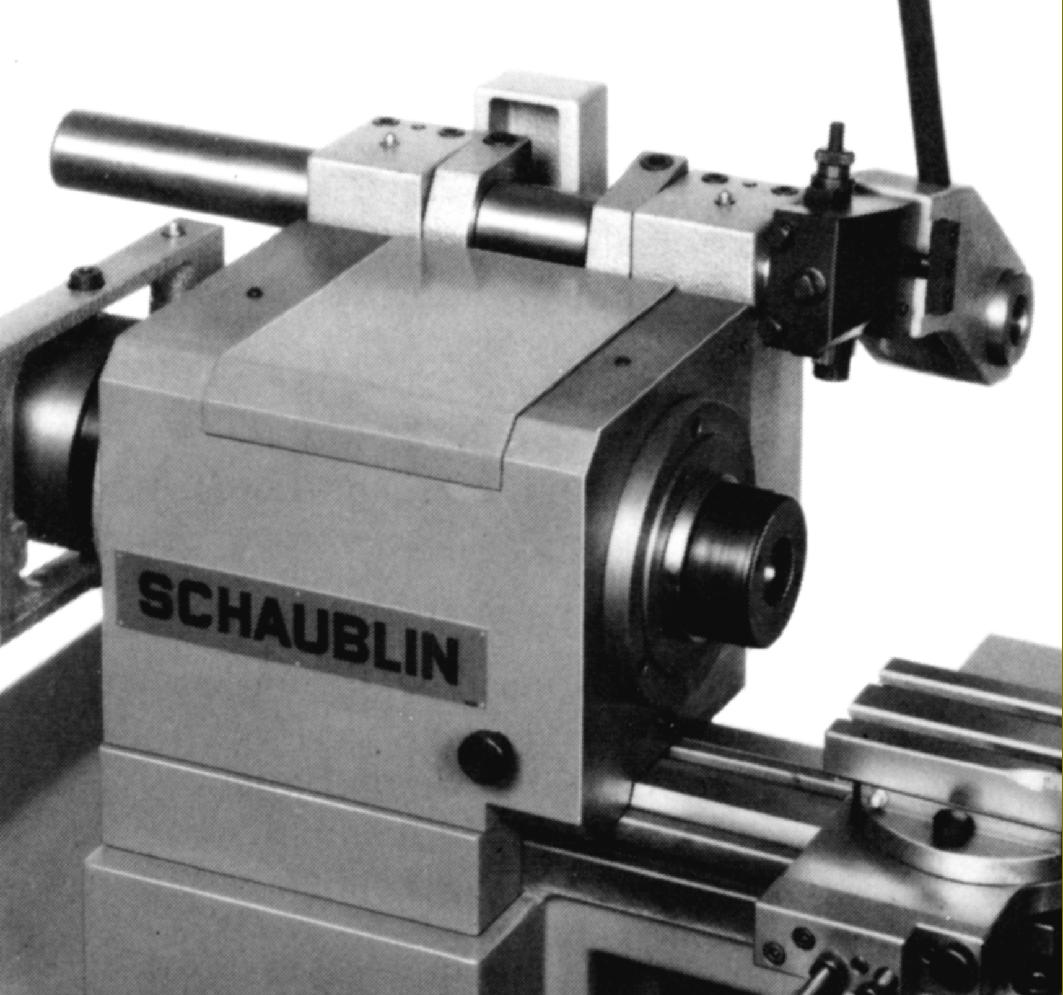 |
|
|
|
|
|
|
Attachment 105-35.600 cutting-off attachment in place on a 102N lathe
|
|
|
|
|
|
|
|
|
|
|
|
|
|
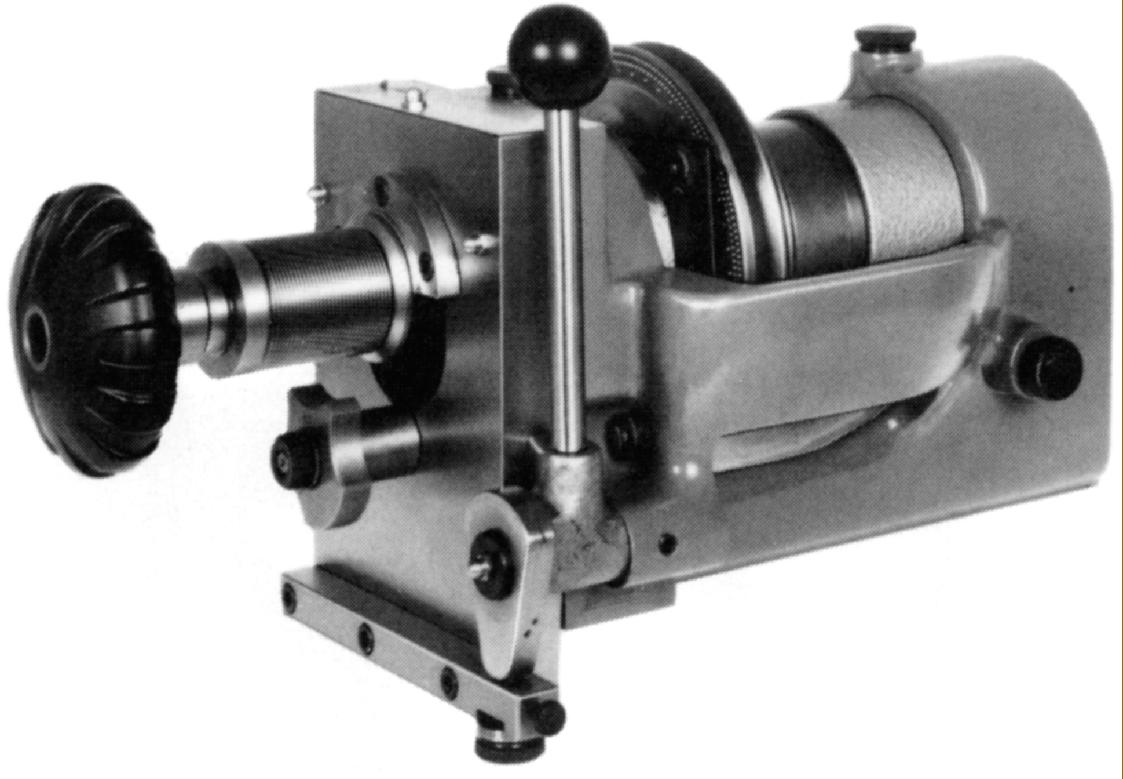 |
|
|
|
|
|
Attachment 102-28.000 Sliding-spindle headstock for screwcutting - this was a complete unit and could not be retro-fitted to other headstocks. The system used W20 collets that had a maximum through bore of 14.5 mm with the longest thread that could be cut being 30 mm and the coarsest pitch generated 2 mm. Designed originally for use by optical instrument makers, who needed a short but very accurate thread, a disadvantage of the "chase" system was the need to keep in stock a range of master threads and their matching star-shaped bronze followers. However, with the limited range of thread pitches required this was not unduly expensive and included in the basic set (to allow the manufacture of chuck backplates and other work-holding fittings) would have been one pair with the same pitch as that used on the lathe's spindle nose. The system was ingenious but of simple mechanical arrangement - a thick plate, able to be moved vertically to engage the threading, was dovetailed to the outside face of the headstock casting. Instead of the threading tool being made to move along the job - and so require a drive mechanism at the back of the headstock--the headstock spindle was arranged to slide forwards and backwards in its bearings. Other companies using the system included the German firms of Lorch ,Wolf Jahn, Auerbach, and Karger - the smallest lathe to incorporate it being the Wolf Jahn Model AA with a centre height of just 50 mm. The arrangement was also a feature of most "Swiss-Auto" mass-production lathes used for the manufacture of tiny parts - and is still in widespread use today on such lathes, though these now (of course) fitted with CNC controls. The Schaublin 102 was almost certainly the last lathe made on which the system was offered. An older version of the sliding headstock can be seen here
|
|
|
|
|
|
|
|
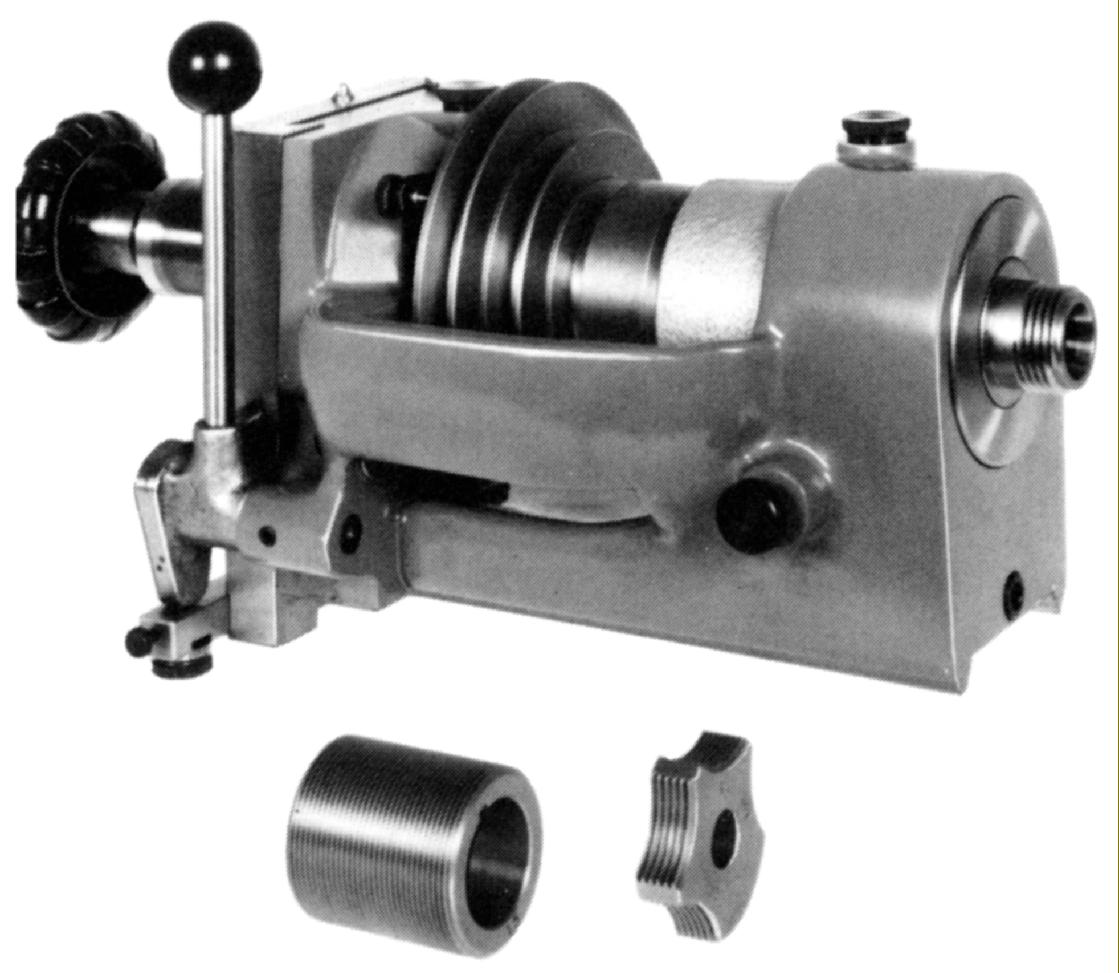 |
|
|
|
|
|
|
The Master Thread and star-shaped Follower
|
|
|
|
|
|
|
|
|
|
|
|
|
|
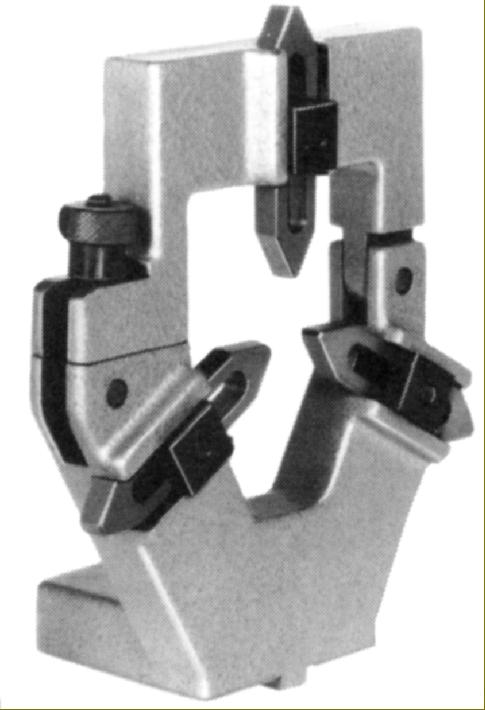 |
|
|
|
|
|
Not one, but three types of fixed steady were offered to suit virtually any job. Above the conventional closed type with well-clamped bronze fingers.
|
|
|
|
|
|
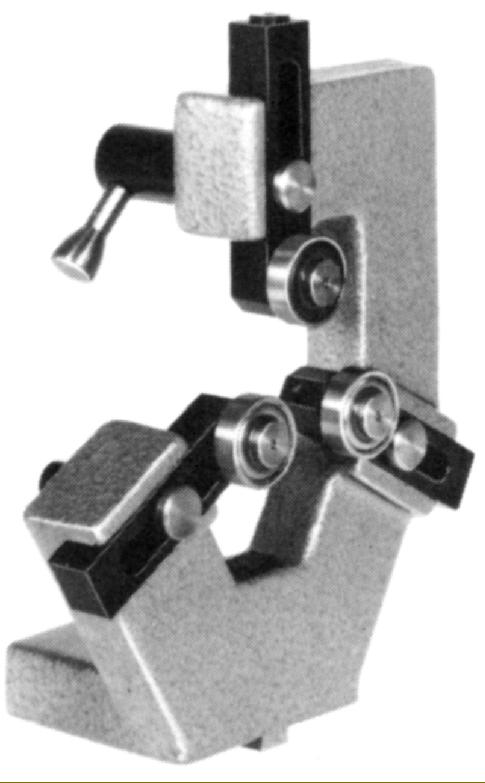 |
|
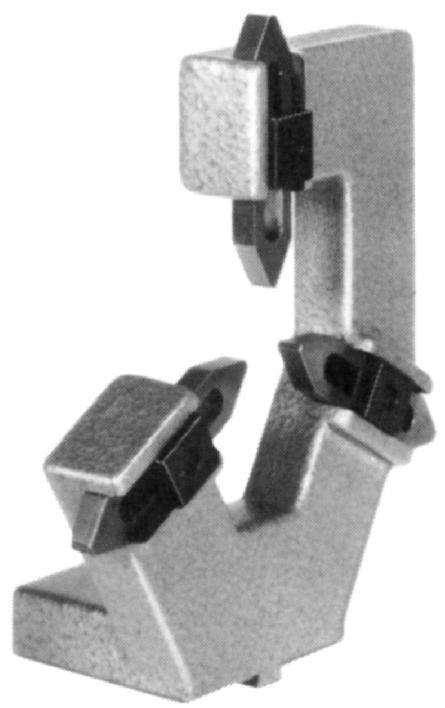 |
|
|
|
|
|
|
|
|
|
|
|
Fixed steady open type with bronze fingers.
|
|
|
|
|
|
|
|
|
|
|
|
|
|
Bottom left: open with roller fingers
|
|
|
|
|
|
|
|
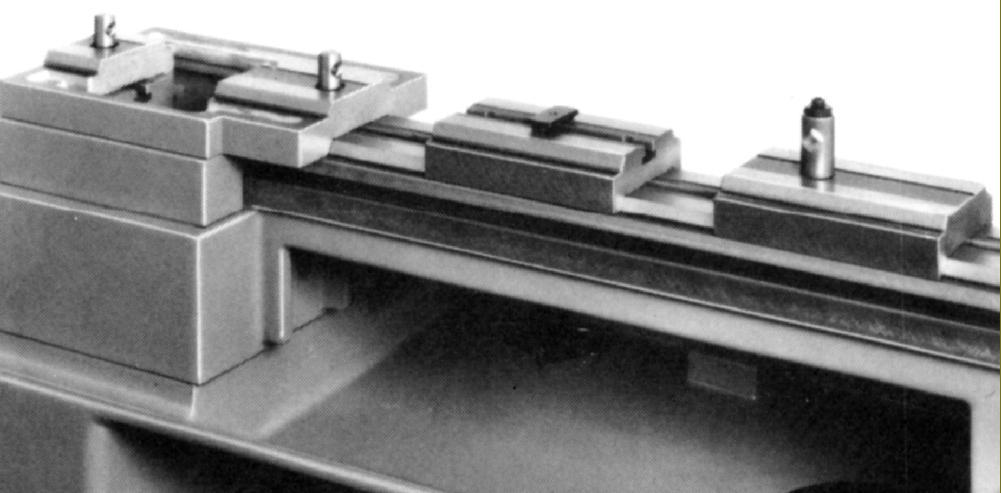 |
|
|
|
|
|
|
Raiser blocks to lift the headstock, carriage and tailstock
|
|
|
|
|
|
|
|
|
|
|
|
|
|
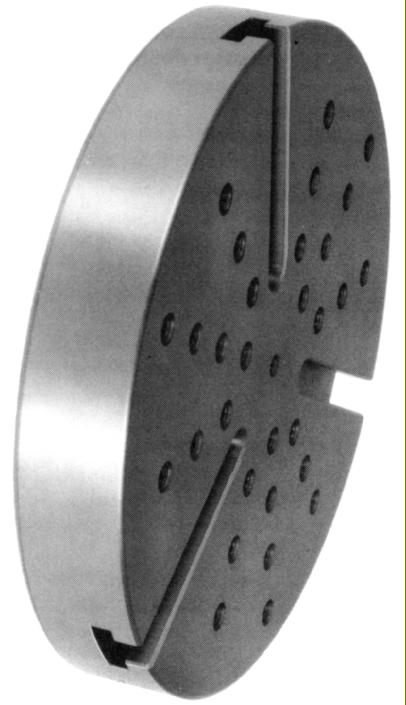 |
|
|
|
|
 |
|
|
|
|
|
|
|
|
|
|
|
|
Above High-class, toolroom-type faceplates: left with T-slots and tapped holes and on the right with eight radial T-slots
|
|
|
|
|
|
|
|
|
|
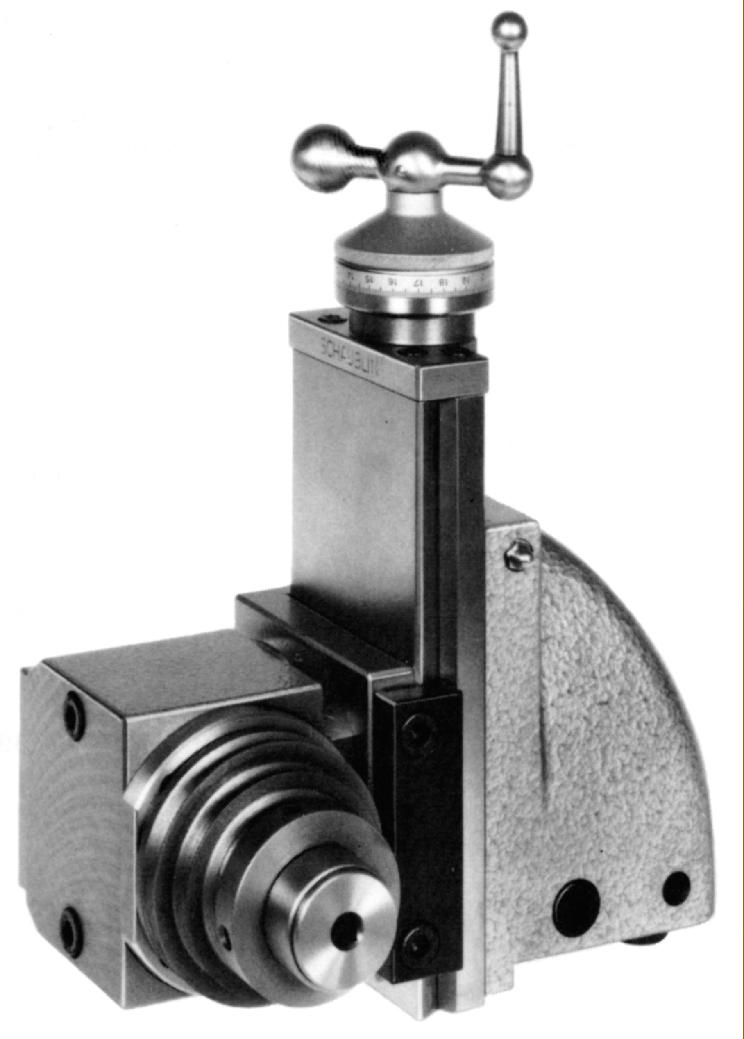 |
|
|
|
|
|
|
Complete Vertical Milling Attachment (listed as 125-87.350) comprising the Column Unit (125-87.300) and swivelling "headstock" (102-87.450) with high-precision ball-bearing quill to take W20 collets. A wide range of extras was available for this unit including: a pawl-operated dividing head, geared reduction unit, swivelling vice and T-slotted angle table, high-speed grinding and milling attachments and various collet holders. All milling accessories carried the part number "87".
|
|
|
|
|
|
|
|
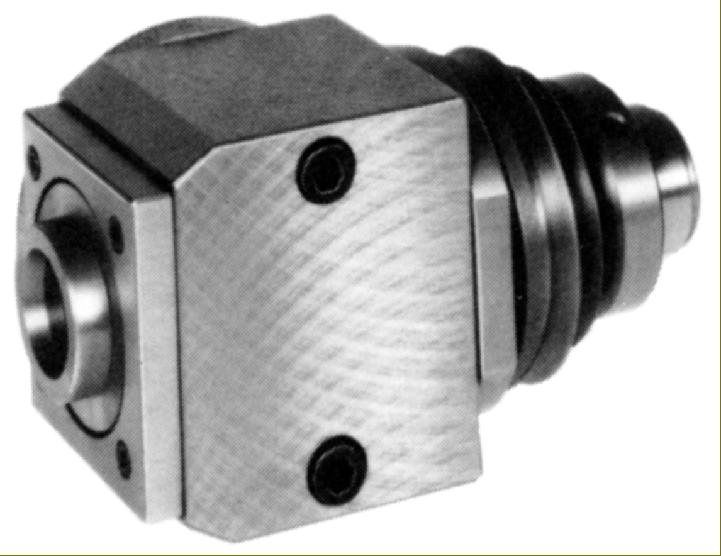 |
|
|
|
|
|
|
Part No. 102 Inclinable Attachment with a spindle to take W20 collets
|
|
|
|
|
|
|
|
|
|
|
|
|
|
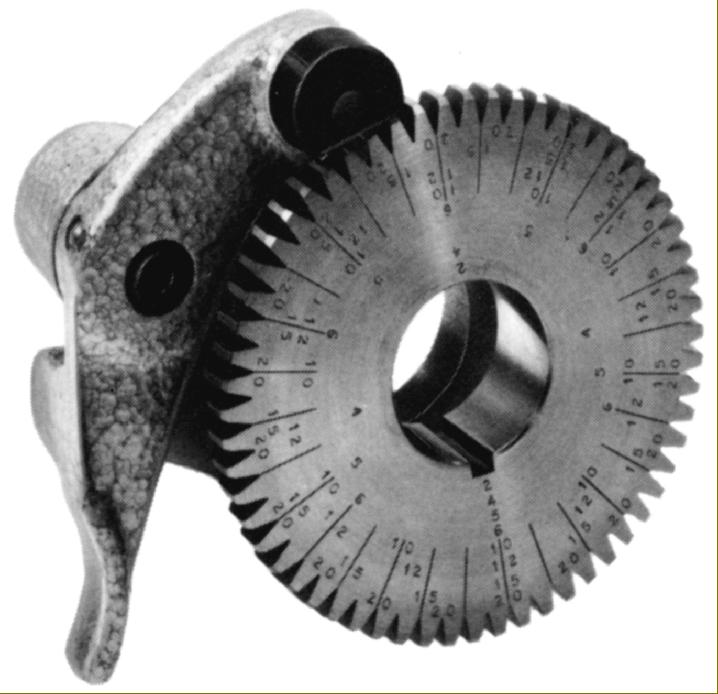 |
|
|
|
|
|
|
Pawl-operated (simple) Dividing Head (102-87.410). This was fitted as standard with a 60-notch plate though others, to a maximum of 128 notches, were also available.
|
|
|
|
|
|
|
|
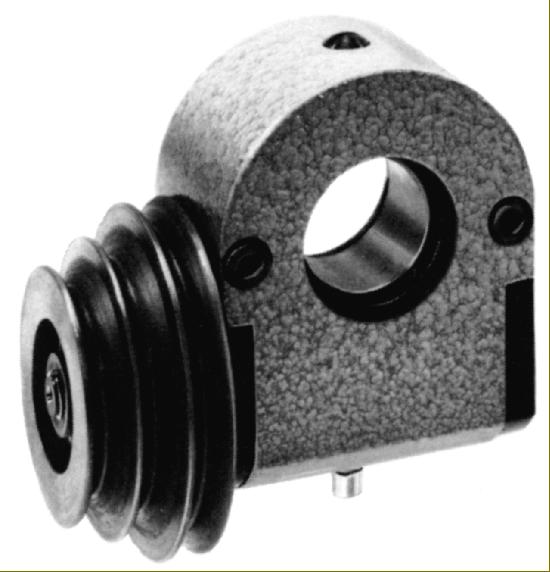 |
|
|
|
|
|
|
4.5 : 1 (or 5 :1) ratio Speed Reduction unit (102-87.380). Fitted in an oil-tight housing the spindle and gears ran on ball bearings. Speed range 220 to 1080 r.p.m.
|
|
|
|
|
|
|
|
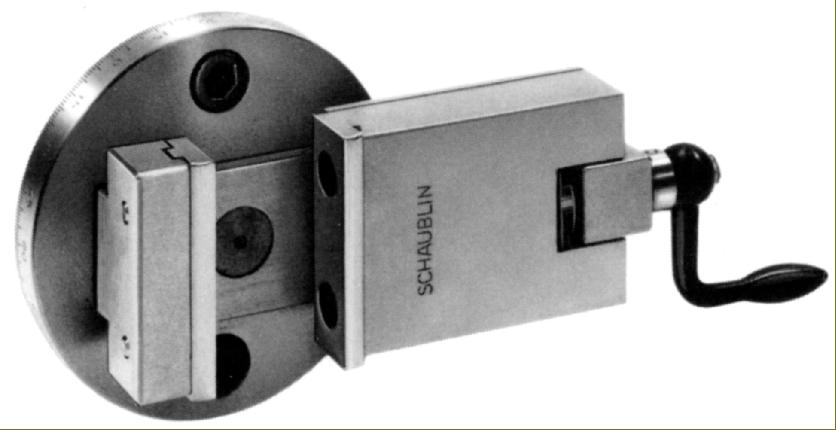 |
|
|
|
|
|
|
For work holding the vertical slide could be equipped with two swivelling attachments both marked with 360-degree divisions a vice and a T-slotted table. Above is the parallel-jaw vice (102-87.510) with 50 mm wide jaws and a maximum opening width of 50 mm
|
|
|
|
|
|
|
|
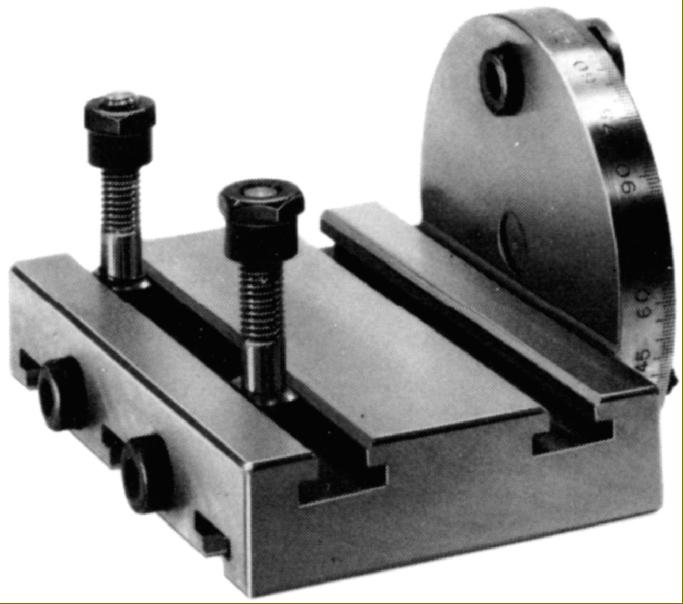 |
|
|
|
|
|
|
The ingenious angle plate (102.87.530) with 8.5 mm T slots on both bottom and top surfaces (set at 90-degrees to each other) and a working surface of 120 x 80 mm. Two clamping bolts (102-87.536 were supplied with the unit.
|
|
|
|
|
|
|
|
|
|
|
|
|
|
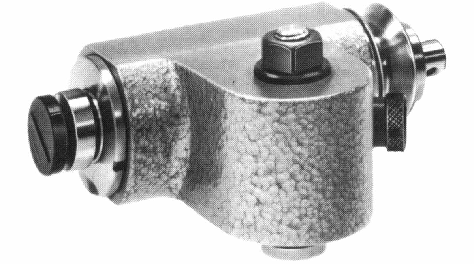 |
|
|
|
|
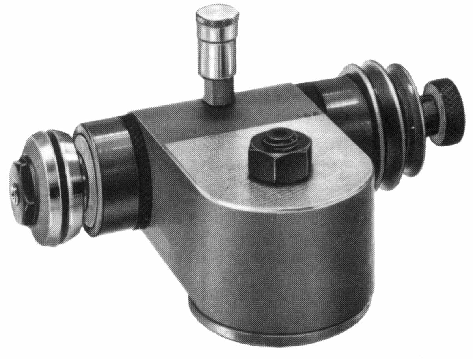 |
|
|
|
|
|
|
Grinding Attachment (102-87.550). Supplied with 1 wheel adaptor (102-87.700), drawbar and a 39 mm diameter pulley the spindle ran on ball bearings and had a maximum speed of 15,000 r.p.m. Slack in the bearings was taken up automatically.
|
|
|
|
|
|
|
|
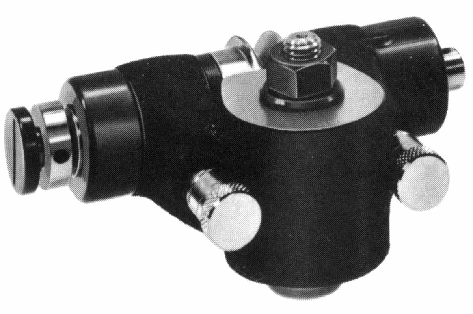 |
|
|
|
|
|
|
|
|
Grinding Attachment (102-87.650). Supplied with 1 wheel adaptor (102-87.700), drawbar and a two-step 34-39 mm diameter pulley. The carbide-faced spindle ran on plain bearings and had a maximum speed of 12,000 r.p.m.
|
|
|
|
|
|
|
|
|
Grinding Attachment (102-87.600). Supplied with 1 wheel adaptor (102-87.700), drawbar and a 39 mm diameter pulley the spindle ran on plain bearings and had a maximum speed of 10,000 r.p.m.
|
|
|
|
|
|
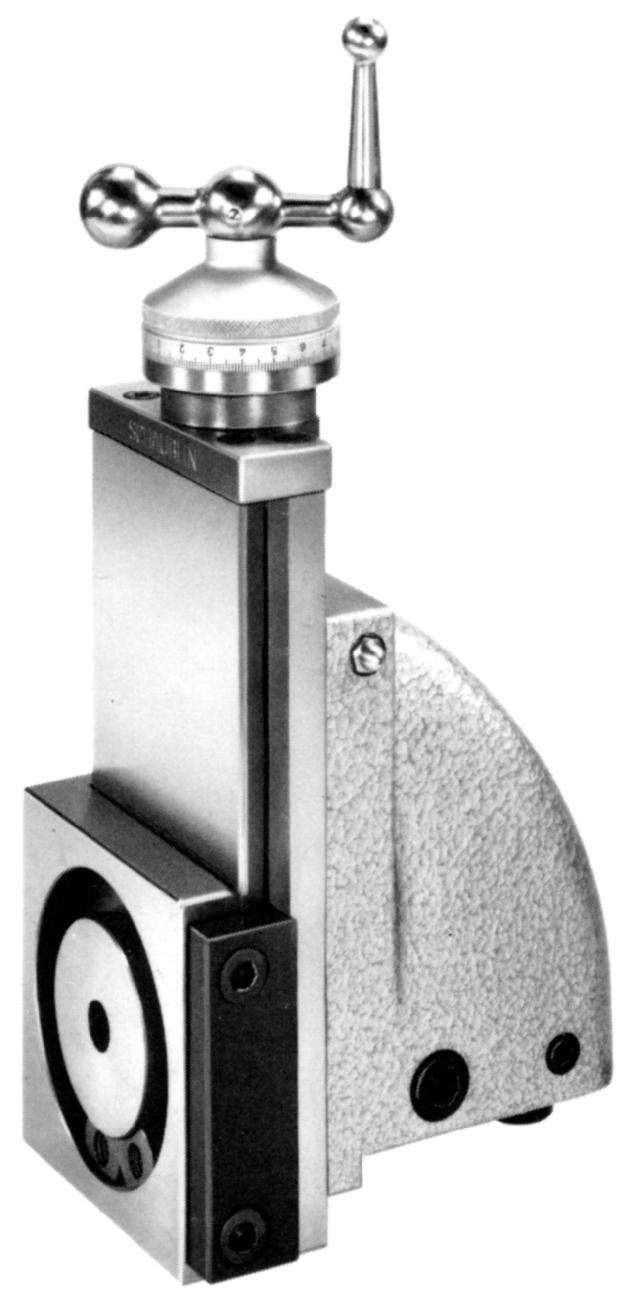 |
|
|
|
|
|
|
The basic milling slide without attachments
|
|
|
|
|
|
|
|
|
|
|
|
|
|
|
|