 |
 |
 |
 |
 |
 |
 |
 |
 |
 |
 |
 |
 |
 |
 |
 |
 |
 |
 |
 |
 |
 |
 |
 |
 |
 |
 |
 |
 |
 |
 |
 |
 |
 |
 |
 |
 |
 |
 |
 |
 |
 |
 |
 |
 |
 |
 |
 |
 |
 |
 |
 |
 |
 |
 |
 |
 |
 |
 |
 |
 |
 |
 |
 |
 |
 |
 |
 |
 |
 |
 |
 |
 |
 |
 |
 |
 |
 |
 |
 |
 |
 |
 |
 |
 |
 |
 |
 |
 |
 |
 |
 |
 |
 |
 |
 |
 |
 |
 |
 |
 |
 |
 |
 |
 |
 |
 |
|
|
|
|
|
|
|
|
|
|
|
|
|
|
|
|
|
|
|
|
|
|
|
|
|
|
|
|
|
|
|
|
|
|
|
|
|
|
|
|
|
|
|
|
|
|
|
|
|
|
|
|
|
|
|
|
|
|
|
|
|
|
|
|
|
|
|
|
|
|
|
|
|
|
|
|
|
|
|
|
|
|
|
|
|
|
|
|
|
|
|
|
|
|
|
|
|
|
|
|
|
|
|
|
|
|
|
|
|
|
|
|
|
|
|
|
|
|
|
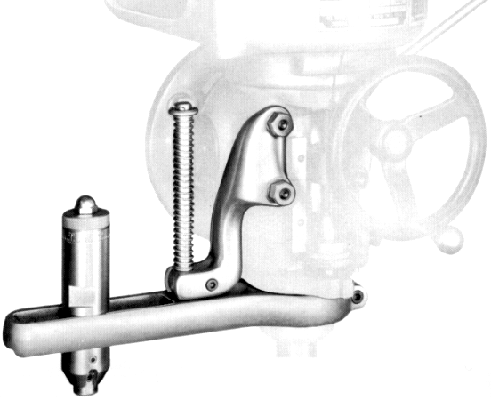 |
|
|
|
|
|
|
|
Profiling Attachment PM-1 for to fit the M head, and PJ-1 for the J heads. Designed for use in tracing and duplicating work where irregularly-shaped dies and mounds were involved.
|
|
|
|
|
|
|
|
|
|
|
|
|
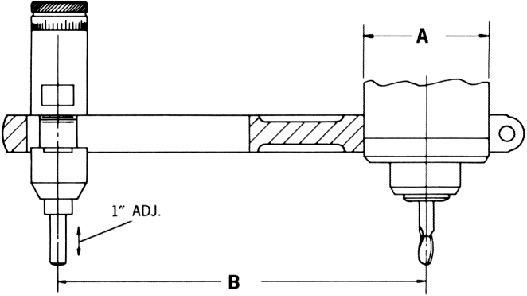 |
|
|
|
|
|
|
|
|
|
|
|
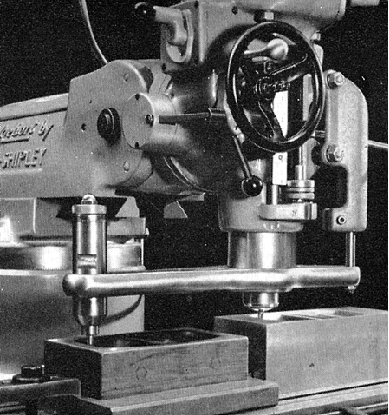 |
|
|
|
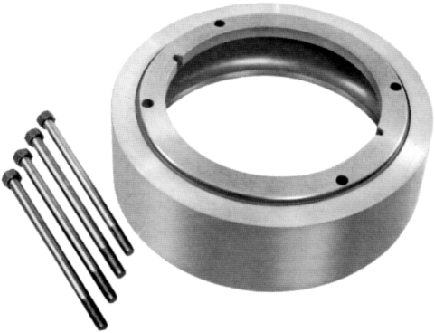 |
|
|
|
|
|
|
|
|
|
|
|
Raiser block for the head - available in 4-inch and 7-inch sizes.
|
|
|
|
|
|
|
|
|
|
|
|
|
|
|
|
|
|
|
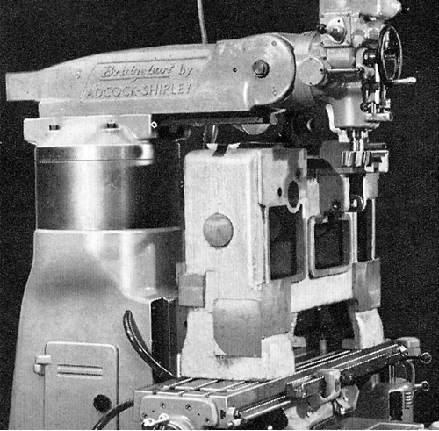 |
|
|
|
|
|
|
|
|
The Raising Block in use.
|
|
|
|
|
|
|
|
|
|
|
|
|
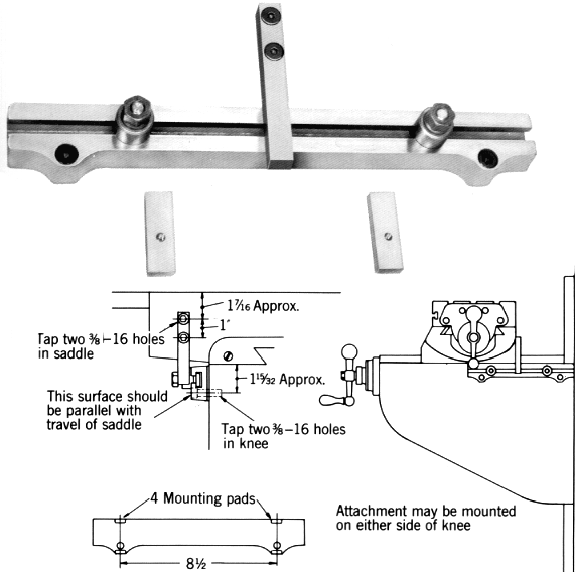 |
|
|
|
|
|
|
Adjustable cross-slide stop - with mounting dimensions
|
|
|
|
|
|
|
|
|
|
|
|
|
|
|
|
|
|
Measuring Equipment
Before the advent of electronic measuring systems, milling machines commonly had two methods of precisely locating work - mechanical and optical. The mechanical system relied upon holders of some kind being fastened to the edges of the table so that accurate "length bars" - usually in inch increments - could be held within them. The end of the bar rested against a micrometer head that in turn was backed by a dial test indicator - thus providing a way, with a little calculation and the exercise of sensitive fingers, of highly accurate setting and measurement.
|
|
|
|
|
|
|
|
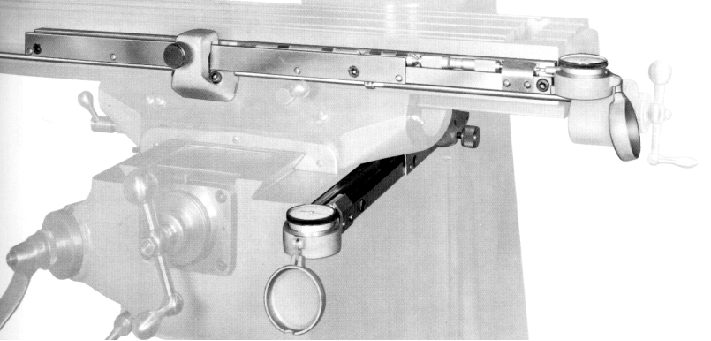 |
|
|
|
|
|
|
The Bridgeport Precision Measuring Attachment for longitudinal and cross feed. The unit consisted of attachments to the edges of the table that held length bars, micrometers and dial gauges. The end measures were used to set whole inches, the micrometers for fractions of an inch and the dial indicators for ten thousandths of an inch - or their metric equivalents.
|
|
|
|
|
|
|
|
|
|
|
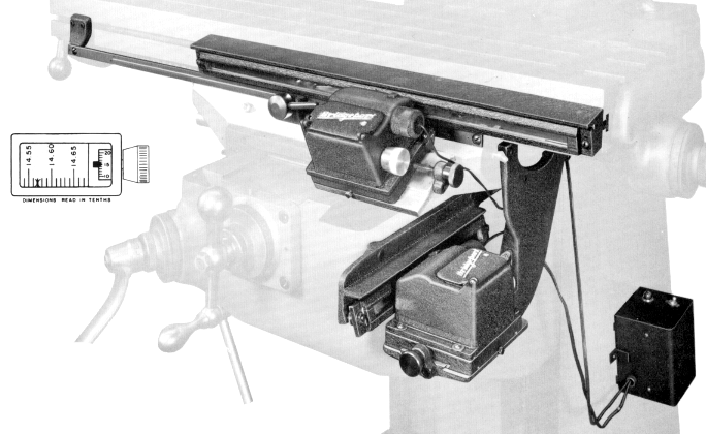 |
|
|
|
|
|
|
Optical Measuring System for longitudinal and cross feed. Another pre-electronic era device for the precise setting of work that involved no mechanical contact - and so avoided wear and consequent inaccuracy. The unit bolted to the machine using a majority of existing holes - and was protected in use by a neoprene guard. The longitudinal travel was 20 inches, cross travel 9 or 12 inches, the magnification x17 and the reading accuracy 0.0001 inches on a direct, single line scale.
|
|
|
|
|
|
|
|
|
|
|
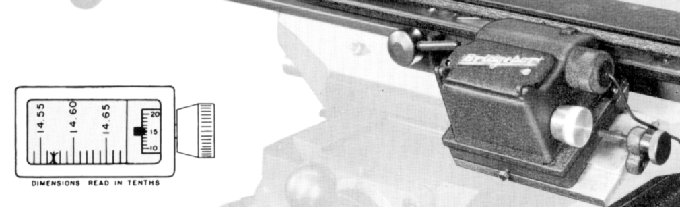 |
|
|
|
|
|
|
The scale had just one line to read - and no vernier estimations to be made.
|
|
|
|
|
|
|
|
|
|
|
|
|
|
|
Bridgeport Millers - Quick-set Tooling Although this system now out of production an alternative set can be supplied - please email for details
|
|
|
|
|
|
|
|
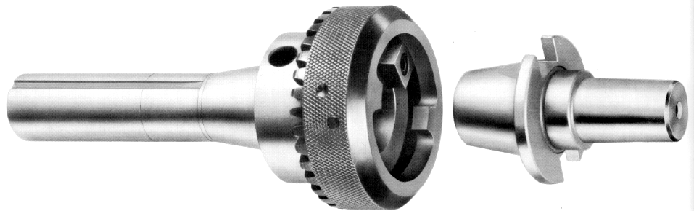 |
|
|
|
|
|
|
Above: quick-change tooling system for the Bridgeport R8 spindle fitting. The hardened and ground, alloy-steel "Master Adaptor" - with a key-driven retaining ring - was able to hold a variety of adaptors (shown below) designed to connect with straight and taper shank drills, boring heads, boring tools, reamers, end mills, fly cutters, chucks and a variety of other tooling. Unlike most other tooling, the Bridgeport set did not require the spindle to be locked when a change was made. Unfortunately the Bridgeport-manufactured system is long out of production - but lathes.co.uk can supply a similar system to take ER collets, end mills and Jacob chucks. Please email for details.
|
|
|
|
|
|
|
|
|
|
|
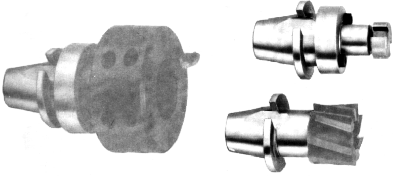 |
|
|
|
|
|
|
|
|
Fly-cutter Adaptor to accept both #3 and #4 Bridgeport-branded fly cutters.
|
|
|
|
|
|
|
|
|
|
|
|
|
|
|
|
Shell-mill Adaptor to accept 0.75-inch and 0.5-inch arbors.
|
|
|
|
|
|
|
|
|
|
|
|
|
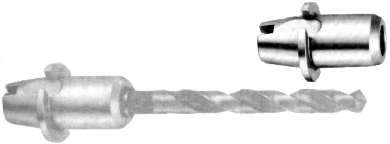 |
|
|
|
|
|
|
|
|
Taper-shank Adaptors - able to hold No. 1 and No. 2 Morse, and No. 5 and No. 7 B & S.
|
|
|
|
|
|
|
|
|
|
|
|
|
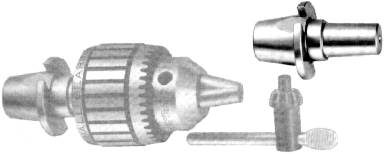 |
|
|
|
|
|
|
|
|
Jacobs-chuck Adaptor - made in a variety of sizes to accept the standard tapers found in the back of Jacobs drill chucks.
|
|
|
|
|
|
|
|
|
|
|
|
|
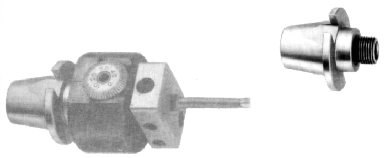 |
|
|
|
|
|
|
|
|
Boring-head Adaptor - made to accept the No. 1 and No. 2 Bridgeport boring heads.
|
|
|
|
|
|
|
|
|
|
|
|
|
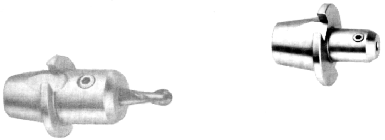 |
|
|
|
|
|
|
|
|
Straight-shank Adaptor - made to accept 1/8", 3/16", 1/4", 3/8", 1/2", 5/8", 11/16", 3/4" 13/16" and 7/8" - and doubtless metric sizes as well.
|
|
|
|
|
|
|
|
|
|
|
|
|
|
|
|
|
Bridgeport Millers Collets & Adaptors
|
|
|
|
|
|
|
|
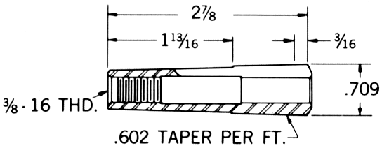 |
|
|
|
|
|
|
|
|
No. 2 Morse Collet for the Model M and T heads. Holds tools from 1/16 to 1/2 inch.
|
|
|
|
|
|
|
|
|
|
|
|
|
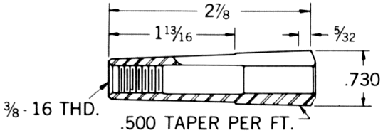 |
|
|
|
|
|
|
|
|
7 B & S Collet for the Model M and T heads. Holds tools from 1/16 to 1/2 inch.
|
|
|
|
|
|
|
|
|
|
|
|
|
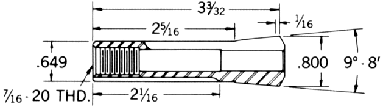 |
|
|
|
|
|
|
|
|
B-3 Collet for the Model C and T heads. Holds tools from 1/16 to 1/2 inch.
|
|
|
|
|
|
|
|
|
|
|
|
|
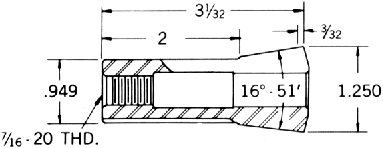 |
|
|
|
|
|
|
|
|
No. 16-S Collet for Model R milling head (old style). Holds tools from 1/8 to 3/4 inch.
|
|
|
|
|
|
|
|
|
|
|
|
|
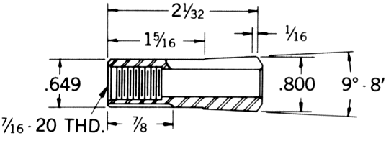 |
|
|
|
|
|
|
|
|
B-2 Collet for No. 1 Right-angle Attachment. Holds tools from 1/16 to 1/2 inch.
|
|
|
|
|
|
|
|
|
|
|
|
|
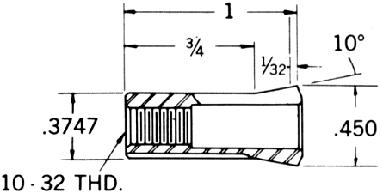 |
|
|
|
|
|
|
|
|
N-2 Collet for No. 2 Right-angle Attachment. Holds tools from 1/16 to 1/4 inch.
|
|
|
|
|
|
|
|
|
|
|
|
|
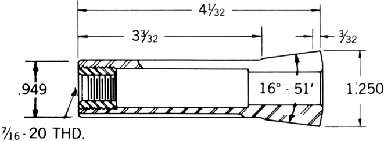 |
|
|
|
|
|
|
|
|
R-8 Collet for Model J and R Heads and No. 3 Right-angle Attachment. Holds tools from 1/8 to 3/4 inch.
|
|
|
|
|
|
|
|
|
|
|
|
|
|
|
|
|
Adaptors for use with tapered-shank end mills and drills
|
|
|
|
|
|
|
|
|
|
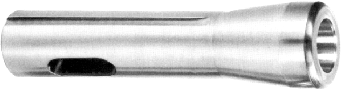 |
|
|
|
|
|
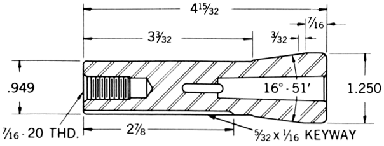 |
|
|
|
|
|
|
|
|
M-1 Adaptor R-8 taper, for use with Model J and R Heads and No. 3 Right-angle Attachment. Takes No. 1 Morse Taper
|
|
|
|
|
|
|
|
|
|
|
|
|
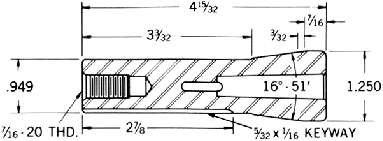 |
|
|
|
|
|
|
|
|
M-2 Adaptor R-8 taper, for use with Model J and R Heads and No. 3 Right-angle Attachment. Takes No. 2 Morse Taper
|
|
|
|
|
|
|
|
|
|
|
|
|
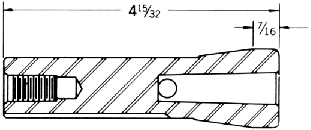 |
|
|
|
|
|
|
|
|
BS-5 Adaptor R-8 taper, for use with Model J and R Heads and No. 3 Right-angle Attachment. Takes No. 5 B & S Taper
|
|
|
|
|
|
|
|
|
|
|
|
|
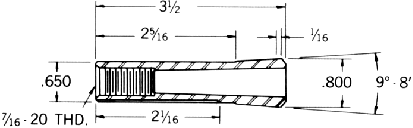 |
|
|
|
|
|
|
|
|
B-3 Adaptor For use with Model C and T Heads. Takes No. 1 Morse and No. 4 B & S Taper.
|
|
|
|
|
|
|
|
|
|
|
|
|
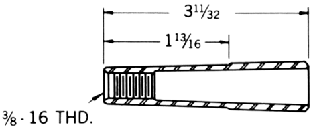 |
|
|
|
|
|
|
|
|
No. 2 Morse Adaptor For use with Model M and T Heads. Takes No. 4 and 5 B & S Taper.
|
|
|
|
|
|
|
|
|
|
|
|
|
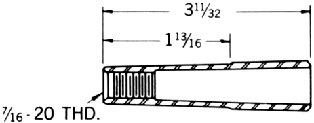 |
|
|
|
|
|
|
|
|
No. 7 B & S Adaptor For use with Model M and T Heads. Takes No. 4 and 5 B & S Taper.
|
|
|
|
|
|
|
|
|
|
|
|
|
|
Hydraulic Copying Attachments
|
|
|
|
|
|
|
|
|
|
|
|
|
|
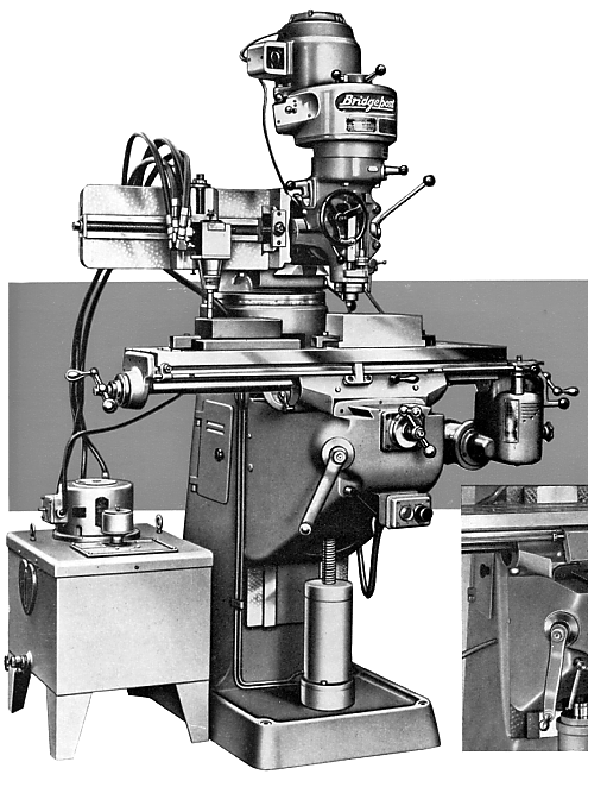 |
|
|
|
|
|
180° Hydraulic Copying Attachment Unlike the dedicated copy millers with hydraulically-powered tables shown on other pages, the unit above was intended as a complete accessory that could be added to, yet not interfere with the function of, a standard machine. The valve, made by the True Trace Corporation of California, featured a very light stylus pressure and was attached to the head in such a way that it could be adjusted relative to the head in all three planes. On the standard installation, whilst the vertical feed was completely automatic, the longitudinal feed had to be reversed by the operator at the end of each pass and the cross feed could only be applied by hand; however, as an option, a Hydraulic "Pick Feed" unit could be supplied that converted the machine to completely automatic operation. Machines fitted with hydraulic copying attachments were recommend to have hard-chrome plated slideways - the porous 0.002" thickness being applied to the back and top of the knee (for vertical and cross movements) and the top of the saddle (for longitudinal travel) as well as to the column-to-knee and cross-slide-to-table gib strips..
|
|
|
|
|
|
|
|
|
|
|
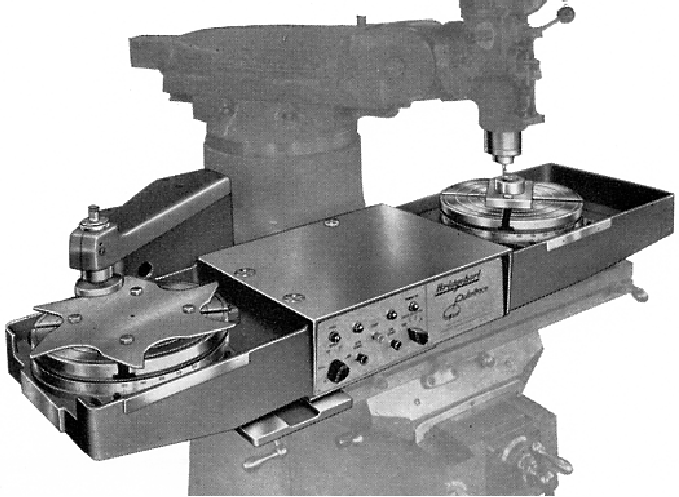 |
|
|
|
|
|
|
Polartrace Unit This unit was intended for the automatic production of extremely accurate two-dimensional parts made from a master between 5 and 10 times as large as the finished component; the accessory was self-contained and consisted of a base casting that fastened to the ordinary table. Pivoted on the base was a housing that mounted two special Bridgeport-manufactured rotary tables joined by a common electric drive. A follower, held by a weighted arm against a sample mounted on the left-hand table, transmitted the form to a workpiece on the right-hand table; the ratio between the two could be set at either 5 to 1 or 10 to 1 and, of course, any error in the master was accordingly reduced by the same factor; the diagram below shows the principle of operation of the unit, The control system was built into the front of the unit and allowed both the speed to be varied and inputs from limit stops to reverse the direction of rotation of the tables.
|
|
|
|
|
|
|
|
|
|
|
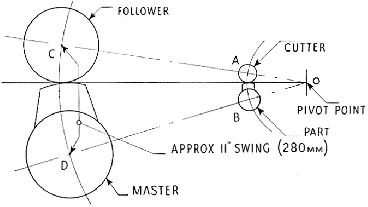 |
|
|
|
|
|
 |
|
|
|
|
|
|
Tandem Rotary Tables. Designed for use in duplicating work - or for making more than one part at once from a single master - the tables were driven by a hydraulic motor.
|
|
|
|
|
|
|
|
|
|
|
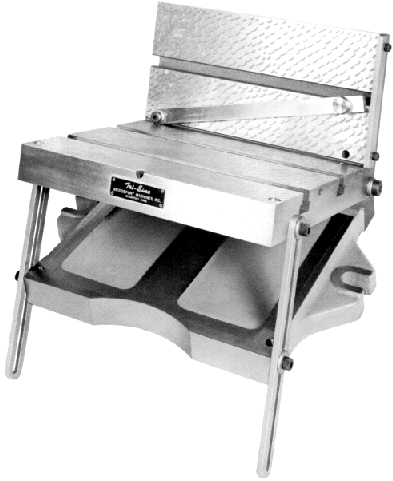 |
|
|
|
|
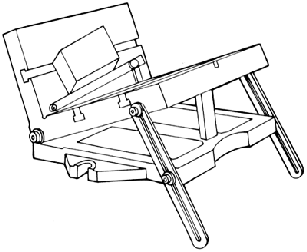 |
|
|
|
|
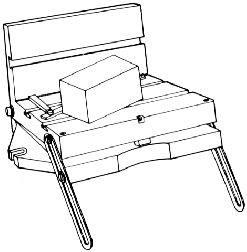 |
|
|
|
|
|
|
|
|
|
|
|
|
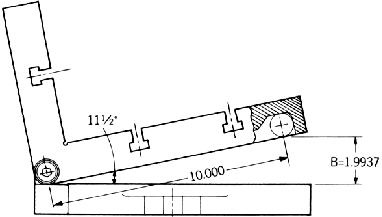 |
|
|
|
|
|
|
|
|
|
Combination angle plate and 10-degree sine table. With 10 inch x 12 inch horizontal, and 6 inch x 12 inch vertical surfaces, the unit was fastened to the milling machine table with two bolts. Adjustable side supports and hinge bolts were provided for additional rigidity. By tightening two screws that passed through the base the device was turned into a solid angle plate.
|
|
|
|
|
|
|
|
|
|
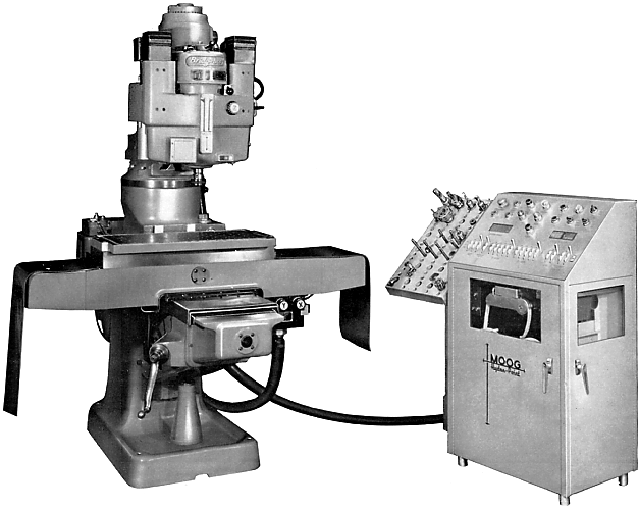 |
|
|
|
|
|
|
Typical of the many variations on a theme produced by third-party suppliers, and included in the main Bridgeport catalogues, the Moog Hydra-point three-axis, numerically-controlled miller was manufactured in England during the 1960s by Moog Hydra-point Ltd. on a machine made by the Bridgeport subsidiary, Adcock & Shipley Ltd. The machine was designed for straight-line milling, drilling, reaming, boring and tapping and was controlled by a numerical control unit, with pneumatic tape reading, that took standard 1-inch wide 8-track paper tape. Both the cutting tool and the workpiece were positioned hydraulically.
|
|
|
|
|
|
|
|
|
|
|
|
|
|
|
|
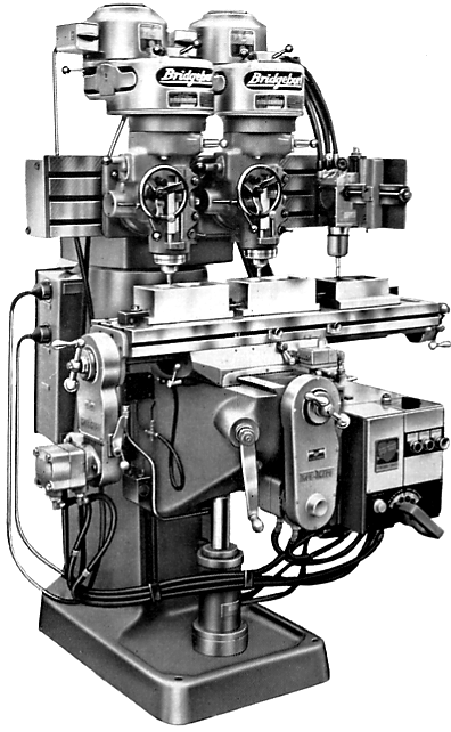 |
|
|
|
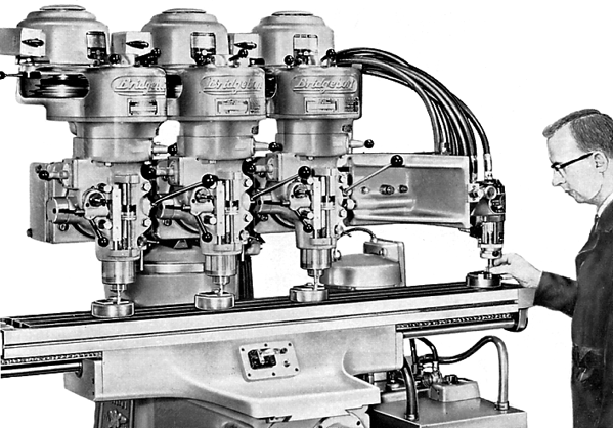 |
|
|
|
|
|
Model 3-D Hydraulic Copying Machine This Bridgeport had its extra-long table movements controlled by hydraulic cylinders, so precluding its use as an ordinary miller. The general layout was very similar to the Synchro-Trace illustrated above, but with manual rather than automatic controls. The operator is seen guiding a stylus around the work sample whilst each of the three heads produces an identical copy.
|
|
|
|
|
|
|
|
|
|
|
|
|
|
|
|
|
Syncho-Trace Designed for die sinking and mould making this special T-head machine was fitted with automatic vertical, longitudinal and traverse feeds. The tracer unit could be mounted in any convenient position on the head - it is shown on the right-hand side of the T head in the illustration - and as the stylus followed the template outputs were generated that automatically directed both the depth and profile cuts - whilst simultaneously regulating the longitudinal and traverse feeds. A "pick-feed" mechanism could also be made to control, by means of a selector dial, the rate and amount of "pick". The device could be reversed or changed directionally during the course of a cut to allow cross-hatching on both rough and finishing cuts. The feed rate was infinitely variable at up to 13 inches a minute, with parts duplicated at a fixed ratio of 1 :1. Unlike other models of Bridgeport automatic copying machines, the table feeds were through the ordinary feed screws, activated by chain drive from hydraulic motors, not hydraulic cylinders, so permitting the machine to be pressed into service as an ordinary miller should the need have arisen.
|
|
|
|
|
|
|
|
|
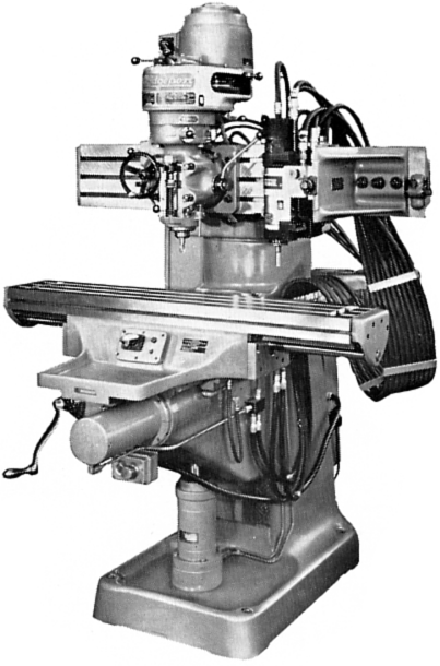 |
|
|
|
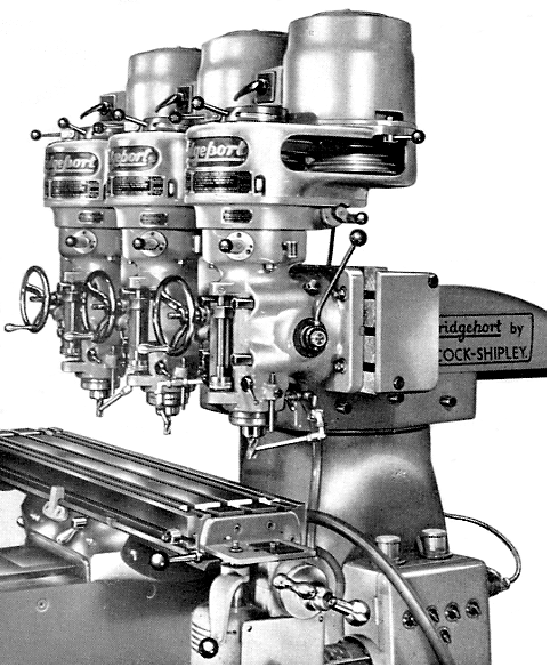 |
|
|
|
|
|
|
Model 3-DA This version of the hydraulic-copying Bridgeport was an automatic version of the 3-D Model shown above. A hydraulic valve controlled the longitudinal and traverse feeds whilst, through the control of a single knob, masters and templates could be automatically followed. Three-dimensional tracing was also possible by disengaging the hydraulic-control valve
|
|
|
|
|
Tee Ram A special ram was needed to carry the Tee head but, as it was interchangeable with any Bridgeport model, it allowed even older machines to be converted to production status while permitting the stylus on a hydraulic copy miller to be mounted much further away from the (single) head - and so increase its copying capacity.
|
|
|
|
|
|
|
|
|
|
|
|
|
|
|
|
|
|
|
|