 |
 |
 |
 |
 |
 |
 |
 |
 |
 |
 |
 |
 |
 |
 |
 |
 |
 |
 |
 |
 |
 |
 |
 |
 |
 |
 |
 |
 |
 |
 |
 |
 |
 |
 |
 |
 |
 |
 |
 |
 |
 |
 |
 |
 |
|
|
|
|
|
|
|
|
|
|
|
|
|
|
|
|
|
|
|
|
|
|
|
|
|
|
|
|
|
|
|
|
|
|
|
|
|
|
|
|
|
|
|
|
|
|
|
|
|
|
|
|
|
|
|
|
|
Taylor offered around twenty different models of screwcutting, "toolroom"bench and woodturning lathes during the 1920s and 1930s but, while some were unique, most were just simple variations on a single design and the majority concerned with the spinning trade and associated activities. They were described variously as: Brass-finishers' lathes in plain, reversing and hollow-spindle types; slide-rest (plain-turning) lathes in both small bench and heavier stand-mounted models where the compound tool rest had to be unclamped from the bed and moved by hand; Traversing lathes with a simple power-fed leadscrew to propel the carriage along the bed; Wood-turning and Pattern-makers' lathes of both light and heavy-duty pattern; a single gap-bed, backgeared screwcutting lathe with a remarkably comprehensive specification; what were described as "Toolmaker Standard" lathes (of incredibly old-fashioned appearance even for the early 1920s) and a variety of special-purpose Thread-chasing and Plugging, Beading and Trimming Lathes. Many were available with a slow-speed backgear assembly and some could be specified with either a solid spindle, where the end thrust was taken against a ball bearing supported in an extension bracket outboard of the left-hand bearing, or with a hollow spindle in which case thrust was absorbed in the usual (and more expensive) way by a either a ball race or hardened rings outboard of the left-hand bearing with (unusually) their own covered oil bath. Drive systems were either by bench, wall or ceiling-mounted countershaft for the spinning and brass-finishing lathes and with the option of self-contained treadle stands for the plain-turning and screwcutting lathes..
|
|
|
|
|
|
|
|
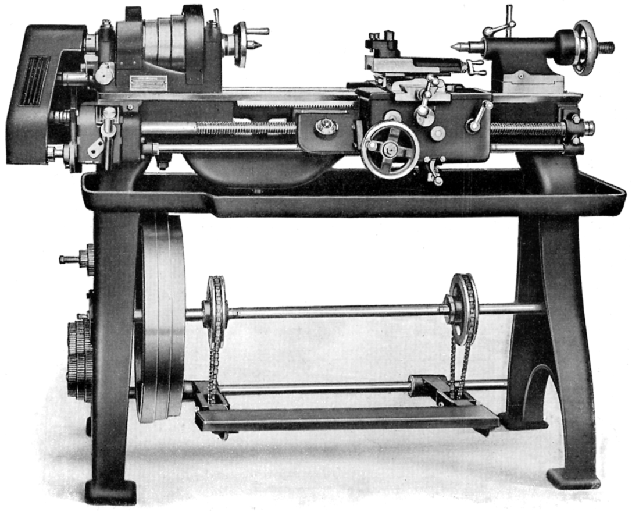 |
|
|
|
|
|
|
The Taylor "Model 658" 4.5-inch and 5.5-inch centre height by 24-inch and 31.5-inch between-centres lathe had a gap bed, backgear, screwcutting and power cross feed as standard; as such it was a surprisingly well-specified machine and stood in such contrast with the maker's other offerings that the writer entertains a slight doubt that it was built in Taylor's factory but may well have been "bought in" from another maker for finishing and re-badging - possibly even from abroad. The box-section bed was fitted with a large detachable gap as standard - it was drawn down into position by a single vertical through bolt - and test timertrapped between them. The lathe was driven by either a wall or ceiling countershaft or, mounted on the makers cast-iron legs, from a ball-bearing supported treadle drive system with a full-length foot bar and a single heavy 3-step flywheel-cum pulley. Unusually for this class of small lathe the 658 was fitted with a large diameter leadscrew - 1.125" on the 4.5" model and 1.25 on the 5.5" - and a separate keyed shaft to drive the power sliding and surfacing feeds. The drive from the feed shaft was taken though the (by then common) worm-and-wheel arrangement with the sliding or surfacing feed selected by a push button on the front of the apron and engaged and disengaged by a snap-action lever hanging below the centre of the apron's lower edge. Screwcutting was by changewheels (spares were stored on the headstock-end leg) with a proper tumble-reverse mechanism to isolate the gear train or cause the carriage to run either towards or away from the headstock. From the changewheels the drive passed through a tumble-action, 3-speed gearbox to provide, at any one setting of the gears, fine, medium and rapid rates of feed. To protect the leadscrew from swarf a long sloping cast-iron guard was fitted to the left-hand face of the carriage - the guard also being used to mount a built-in thread dial indicator in the same way as seen on some early Colchester lathes. The 0.75" bore (1" on the 5.5-inch version) hardened headstock spindle ran in adjustable bronze bearings lubricated from wicks dipping into reservoirs beneath the bearing housings. The 3-step flat-belt pulley was machined all over - the makers also claimed to have balance it - whilst a 6 : 1 ratio backgear was fitted as standard and engaged by rotating its eccentric shaft. At a time when some makers of inexpensive lathes used fragile "as-cast" iron gears and left the backgears and changewheels dangerously exposed, all the gears on the Taylor were cut from steel blanks and guarded with neat covers in cast-iron. The tailstock was provided with a set-over for taper turning and the square-thread barrel was hollow, passing clear through the handwheel..
|
|
|
|
|
|
|
|
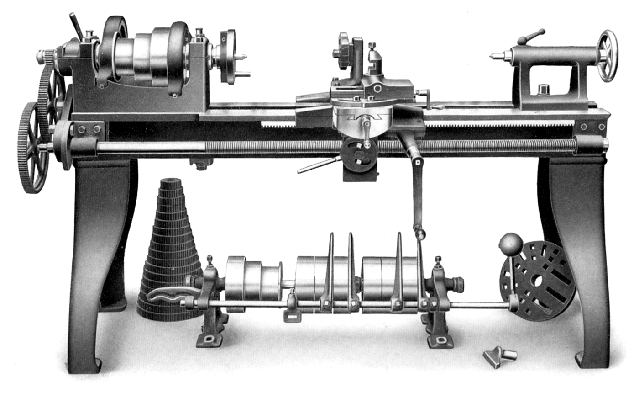 |
|
|
|
|
|
Toolmakers Standard With its exposed changewheels, minimal apron, giant handle to traverse the carriage, crank-handle levers on the compound slide and a lightweight, open tailstock casting the Taylor "Model 474" 6-inch and 7-inch centre height by 27-inch and 36-inch between-centres lathe looked more like a throwback to 1890s than a design for sale in the late 1920s. Taylor even had the bravery to list the lathe as their "Toolmakers' Standard" - and to compound the felony by admitting that, although well made, they could not be bothered to give it a suitable appearance: "No time or money is spent on unnecessary finish, but on the other hand, no expense is spared to make them accurate, durable, and suitable for the class of work they are intended for."
|
|
|
|
|
|
|
|
|
|
|
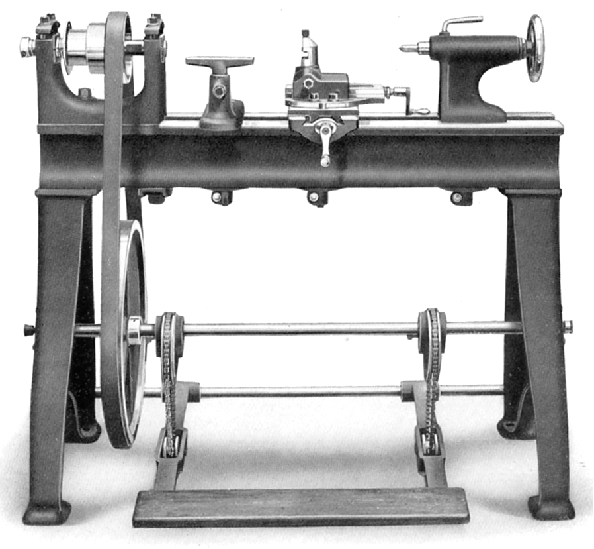 |
|
|
|
|
|
Taylor 4.5-inch and 5.5-inch "un-geared" (no backgear) plain-turning lathe with compound slide rest (part 100) and hand T rest. A simple, no-frills machine that might, because of the very light flywheel, have been reluctant to take more than a very modest cut. That the lathe was reduced to its simplest possible form is demonstrated by the method necessary to alter the spindle speed: the single-step flywheel had to be unlocked and slid along its axle to line up with the headstock pulley and a belt of different length clipped in place. The lathe was further limited in its usefulness by having, in line with common spinning-lathe practice, an internally-threaded headstock spindle.
|
|
|
|
|
|
|
|
|
|
|
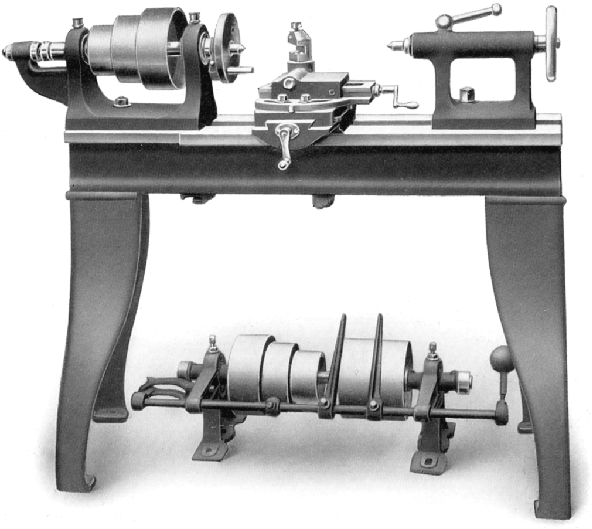 |
|
|
|
|
|
One of the stronger Taylor plain-turning lathes was Model S28 made in 5-inch, 6-inch and 7-inch centre heights and with both non-geared and backgeared headstocks. The non-geared model (illustrated above) had a solid, hardened-steel spindle running in hardened and tapered bearings with the end thrust taken using a (very old-fashioned) system where a hardened pin in the left-hand end of the spindle bore against an outboard extension bracket. Although the S28 was available with three centre heights only the backgeared version (illustrated below) could only be ordered as a 6 or 7-inch version. The between-centre capacity varied with centre height and specification: the smallest 5-inch model was restricted to a 3 foot bed (20 inches between centres); the 6-inch model could be had with beds 3.5 or 4-feet long bed whilst the 7-inch model was offered with a choice of 4 or 5-foot long beds. The 5-inch machine weighed a comparatively light 3 cwt (336 lbs) but the most comprehensively equipped 7-inch model was over three more massive at 10 cwt (0.5 tons). The compound slide rest fitted to these machines was the standard, very old-fashioned, "Type 100" with a non-removable swivelling toolpost built into the top slide and simple "square-socket" detachable handles that would have been familiar to a turner 50 years earlier. If the owner required a hollow headstock spindle (available only on the backgeared models) the makers charged extra..
|
|
|
|
|
|
|
|
|
|
|
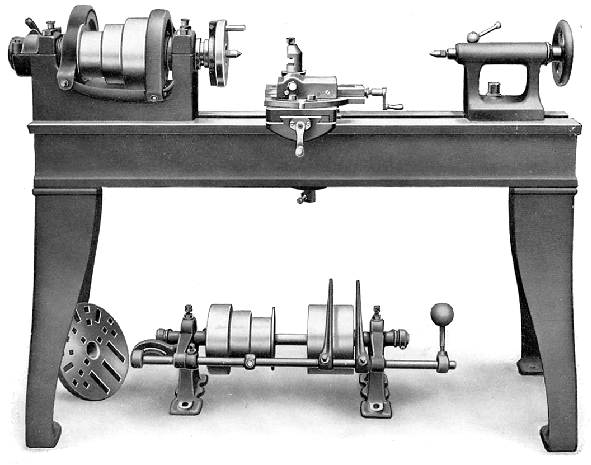 |
|
|
|
|
|
Taylor "Model S28" 5-inch, 6-inch and 7-inch centre height plain-turning lathe with backgeared headstock and hollow spindle running in split adjustable bearings. To the outboard of left-hand bearing was an extension of the headstock casting used to house the thrust arrangements of the spindle - a simple hardened collar - and form a covered oil bath for its lubrication.
|
|
|
|
|
|
|
|
|
|
|
 |
|
|
|
|
|
The Model 641 was of similar design to the lighter S28 and 421 plain-turning models and available as either a 6" x 17" or 7" x 20". Both were fitted with a more robust compound slide than the usual 100 Type (with a proper 4-way toolpost) and a heavier headstock with a hollow spindle - 1 5/8" bore on the 6-inch and 17/8" on the 7-inch - as standard. The lathes were mounted on an ugly assembly of "double legs" separated by a sheet-steel chip tray. The 6-inch weighed 7 cwt (784 lbs) and the 7-inch 10 cwt (1120 lbs). The 6.5-inch centre height Model 657 "Traversing Lathe" was a unique model in the range being fitted with a carriage that had both a hand-operated rack-and-pinion drive and a simple power feed from a two-step pulley on the end of the headstock spindle. The power feed drove through a keyed shaft to a worm-and-wheel mechanism in the apron and could be arranged to trip out by stops - a useful function that allowed the lathe to be set up for simple repetition manufacturing use. The makers had an interesting description of its functionality that revealed a little about contemporary working practices: "...they are excellent lathes for boy or apprentice labour, and one operator can attend to four or more lathes."
|
|
|
|
|
|
|
|
|
|
|
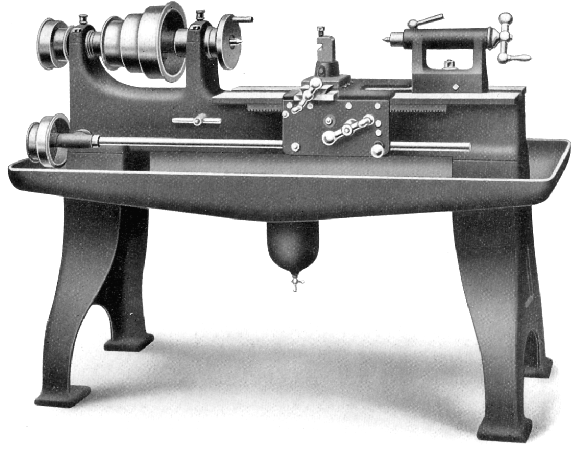 |
|
|
|
|
|
The 6.5-inch centre height Model 657 "Traversing Lathe" was a unique model in the range being fitted with a carriage that had both a hand-operated rack-and-pinion drive and a simple power feed from a two-step pulley on the end of the headstock spindle.The power feed drove through a keyed shaft to a worm-and-wheel mechanism in the apron and could be arranged to trip out by stops - a useful function that allowed the lathe to be set up for simple repetition manufacturing. The makers had an interesting description of its functionality that revealed a little about contemporary working practices: "...they are excellent lathes for boy or apprentice labour, and one operator can attend to four or more lathes."
|
|
|
|
|
|
|
|
|
|
|
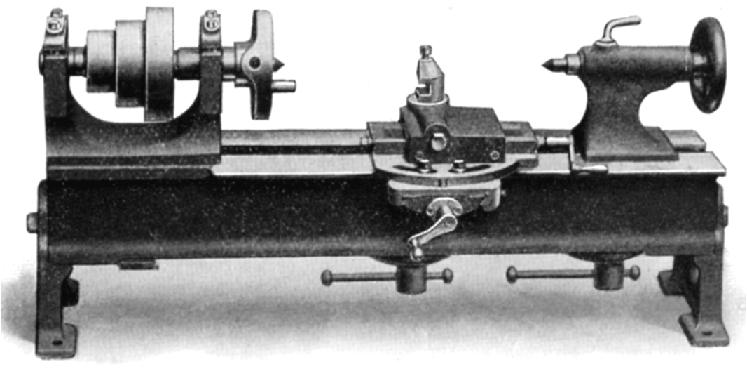 |
|
|
|
|
|
Although afforded scant publicity in the sales literature a number of smaller bench lathes, based upon at least two and possibly three different beds with simple bracketed feet bolted to their end faces, were also made by Taylor. Only one, the Model D20, shown above, was a conventional machine likely to interest the repair mechanic, model-engineer or experimental worker, the others (the Model 434, N9 and A8 below) were special-purpose machines for manufacturing use. With a centre height of 4.5" and a capacity between centres of 21" the headstock spindle was designed to run a high speed and, consequently, was hardened and ground and ran in gun-metal bearings. Instead of the internal thread of the spinning-lathe based 571 the spindle had a conventional external thread to allow the mounting of ordinary chucks and faceplates. The tailstock betrayed the company fondness for cutting corners by allowing the use of a threaded lever to bear directly against the barrel to lock it in position.
|
|
|
|
|
|
|
|
|
|
|
|
|
|
|
|
|
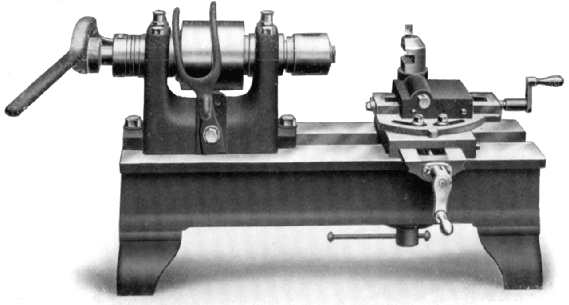 |
|
|
|
|
|
Taylor "Model 434" 5-inch centre height 34-inch long "second-operation" lathe fitted with a "draw-back" collet chuck closed by a heavy coil spring; the action of the lever was to open the chuck and release the workpiece. The spindle ran in long phosphor bronze bushes with two ball-race thrust washers to take spindle and operating lever end loads. A single 4-inch diameter fast-and-loose pulley to take 1.5-inch wide belt was fitted to the headstock spindle (the speed changes coming from the countershaft) with a simple hand-operated striker bar to engage and disengage the drive.
|
|
|
|
|
|
|
|
|
|
|
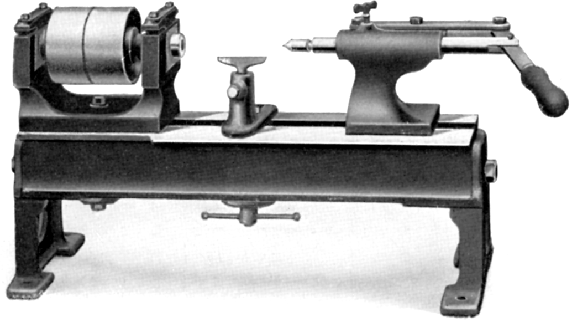 |
|
|
|
|
|
Taylor "Model N9" 5-inch centre height 24-inch long "drilling lathe" lathe with a high-speed hardened and ground spindle running in gun-metal bushes. A single 4-inch diameter fast-and-loose pulley to take 1.5-inch wide belt was fitted to the headstock spindle (the speed changes coming from the countershaft). A simple hand-operated striker bar to engage and disengage the drive could be fitted if required.
|
|
|
|
|
|
|
|
|
|
|
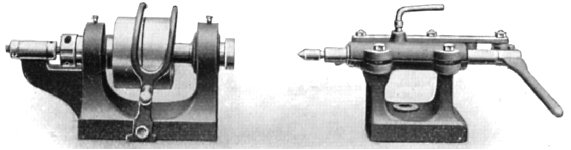 |
|
|
|
|
|
|
Taylor "Model A8" separate headstock and tailstock assembly for use by the customer in their own installations. The headstock spindle was threaded internally (3/4-inch Whitworth) hardened and ground and ran in conical gunmetal bearings. The tailstock could be supplied with either a lever or screw-feed barrel.
|
|
|
|
|
|
|
|
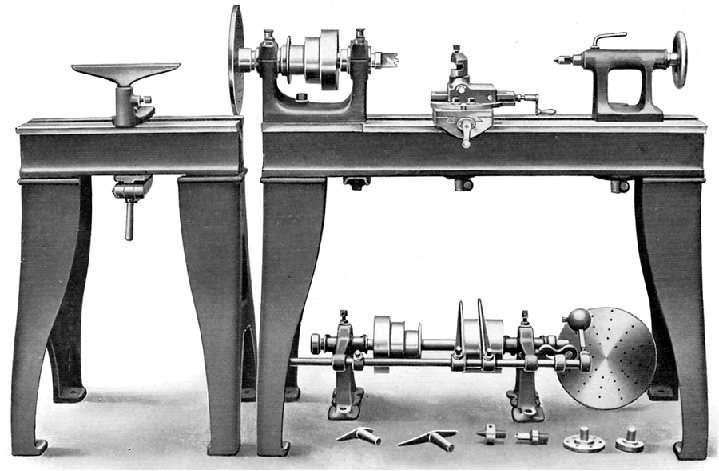 |
|
|
|
|
|
Taylor "wood-turning" lathe. In essence just a plain-turning machine with a left-hand faceplate turning against a separate bed section with a quick-release T rest.
|
|
|
|
|
|
|
|
|
|
|
|
|
|
|
|
|
|
|
|
|
|
|
|
|
|
|