 |
 |
 |
 |
 |
 |
 |
 |
 |
 |
 |
 |
 |
 |
 |
 |
 |
 |
 |
 |
 |
 |
 |
 |
 |
 |
 |
 |
 |
 |
 |
 |
 |
 |
 |
 |
 |
 |
 |
 |
 |
 |
 |
|
|
|
|
|
|
|
|
|
|
|
|
|
|
|
|
|
|
|
|
|
|
|
|
|
|
|
|
|
|
|
|
|
|
|
|
|
|
|
|
|
|
|
|
|
|
|
|
|
|
|
|
|
|
|
|
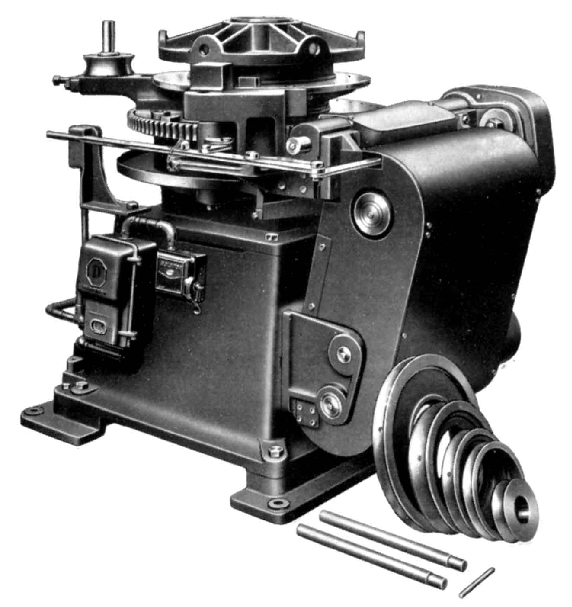 |
|
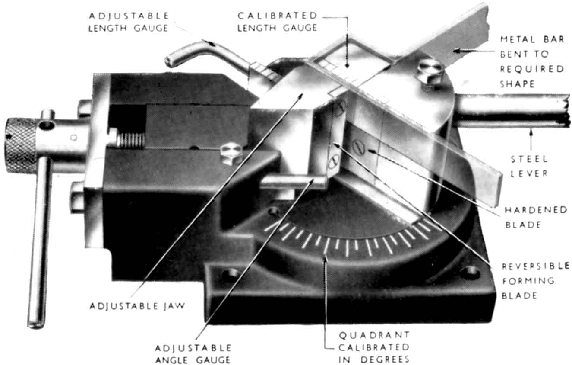 |
|
|
|
|
|
Kennedy No. 1149 Flat-strip Bending Machine. Maximum capacity with flats of 3" x 1/8", 2" x 1/4" and 13/4" x 5/16" and 1/2" on round and square stock.
|
|
|
|
|
|
|
|
|
|
|
|
|
|
Kennedy No. 1425 Electric Semi-automatic Pipe-bending Machine. Maximum capacity 2-inch standard pipes. Also produced in a version capable of bending steel bar up to 2-inches in diameter.
|
|
|
|
|
|
|
|
|
|
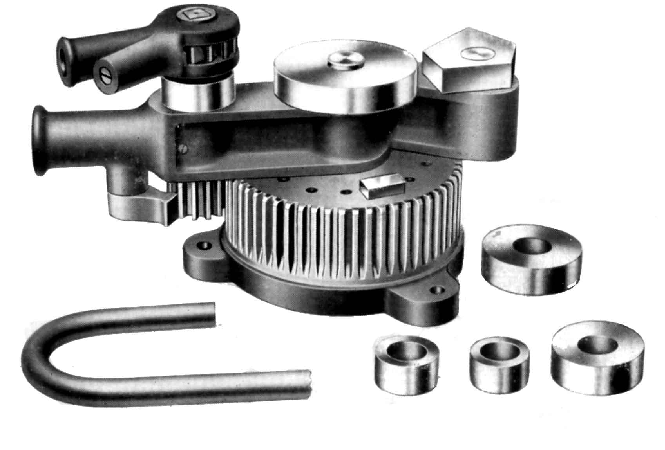 |
|
|
|
|
|
|
Kennedy No. 1213 gear-driven Bar-bending machine with interchangeable formers and rollers. Maximum capacity 1-inch.
|
|
|
|
|
|
|
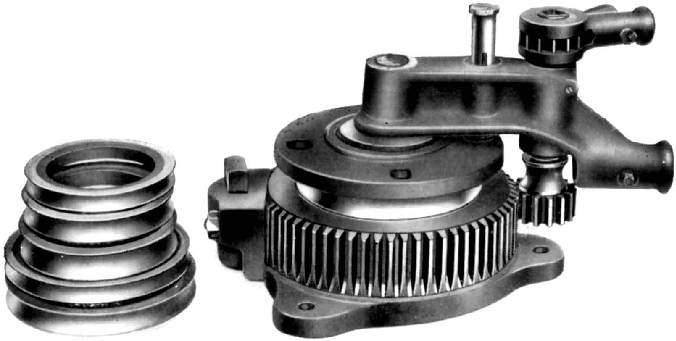 |
|
|
|
|
|
|
Kennedy No. 2 Geared Universal Bending Machine. By using suitable formers angles, Tees, channels and other sections could all be bent. Maximum capacity 1-inch on high-pressure tubing and gas and steam pipes; 11/4" on conduit tubing; 11/4" x 3/8" copper strip on edge (bent at 21/2" radius) and 11/2" x 1/4" mild-steel strip on edge (bent at 21/2" radius).
|
|
|
|
|
|
|
|
|
|
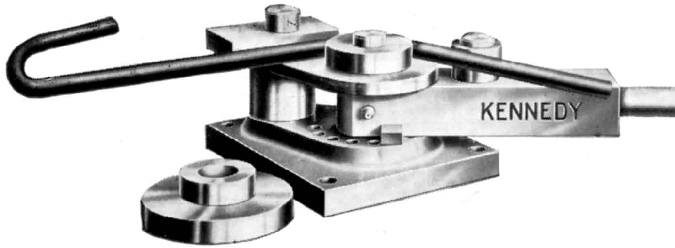 |
|
|
|
|
|
|
Kennedy No. 1212 Direct-lever Bar-bending Machine with a maximum capacity of 3/8"
|
|
|
|
|
|
|
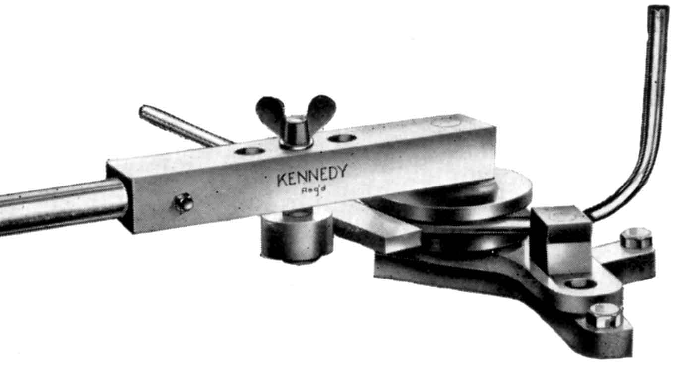 |
|
|
|
|
|
|
Kennedy No. 16 Direct-lever Tube-bending Machine with a maximum capacity of 1"
|
|
|
|
|
|
|
|
|
|
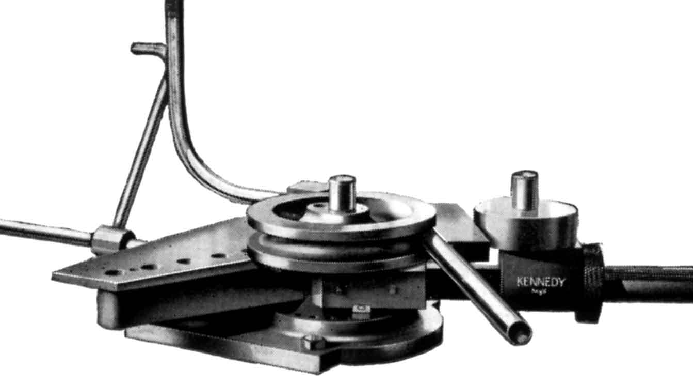 |
|
|
|
|
|
|
Kennedy No. 12 Direct-lever bending Machine for tubes with a maximum diameter of 1 1/4" on light-gauge steel and 1 1/2" on light-gauge copper, brass or alloy.
|
|
|
|
|
|
|
|
|
|
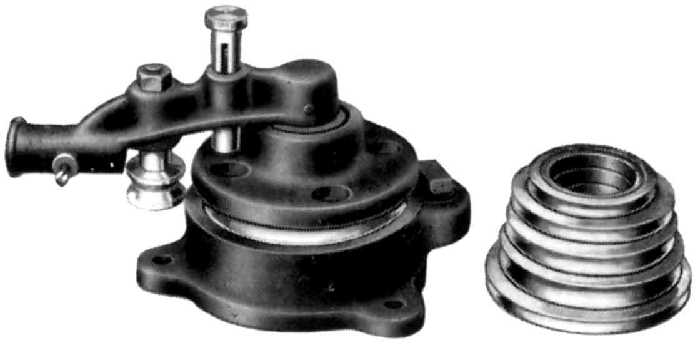 |
|
|
|
|
|
|
Kennedy No. 1 and No. 2 Universal Bending Machine. 1/2" and 1" capacities respectively using gas or steam pipe and 3/4" and 1 1/4" with conduit tubing.
|
|
|
|
|
|
|
|
|
|
|
|
|
|
|
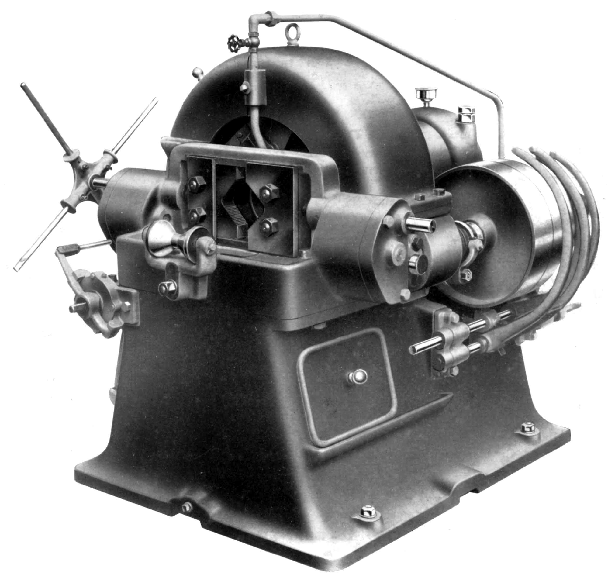 |
|
|
|
|
|
|
|
Early-model Taylor Rotary Cutting-off Machine with flat-belt drive and capstan-operated vice Taylor cutting-off machines were unique in that, instead of the stock revolving it was held stationary and the cutter head made to rotated around it. This had an immediate advantage in that the head did not need to be stopped; the cutters could be backed off, the stock slid through the hand, foot or air-operated vice by hand or under power and the next cut taken immediately. Made in several sizes each had a heavy iron casting formed the machine's main body and the cutter head, carried on a hollow cast-iron spindle, ran in massive spit bronze bearings. The cutters were held in slides fitted with adjustable stops and could be slid into and out of their cutting position by a toggle-mechanism similar to that used to open and close collets in a capstan lathe. For tube work the two high-speed steel cutter blades were formed as parting-off blades used in a lathe with side relief to ensure that only the front edge cut and space was left for swarf to clear. In addition the blades were off-set relative to each other so that each cut only part of the width and consequently left more space for swarf (that "expands" as it is generated) to clear. For cutting bars one blade was made with a vee point the other with a straight edge formed 1/16" higher that the general section of the cutter. The vee-point tool was set to lead by about half the depth of the vee so that the chip removed by the opposite cutter was split into two to prevent chip jamming. As a further refinement the pair of blades shared a common tension chain to ensure that they automatically centred on the job. To provide top rake both cutters were set in the cutter slides at an angle of 25 degrees to the direction of traverse - and thus only required grinding on their front ends to match the setting gauge supplied with each machine. An adjustable roller guide was positioned immediately outside the vice to guide stock centrally into the vice. Like many contemporary machine tools, the original models were driven by flat belts but later machines, following general developments in the field, used built-on motors together with V-belt pulleys.
|
|
|
|
|
|
|
|
|
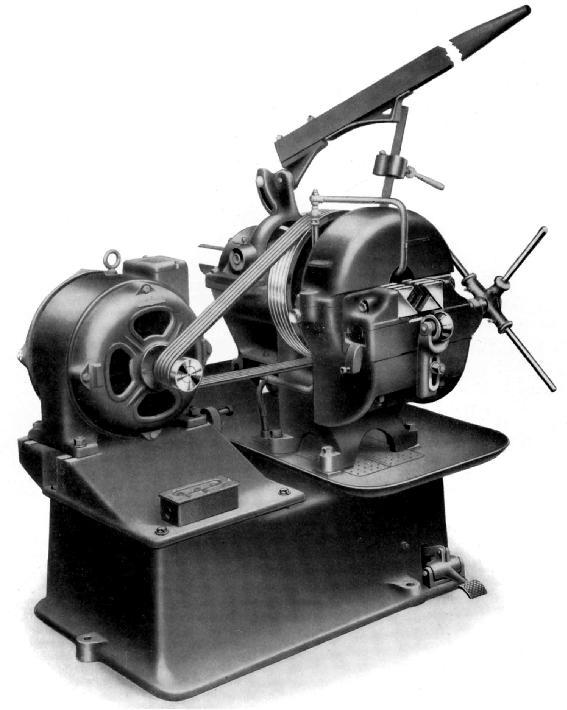 |
|
|
|
|
|
|
Taylor Rotary Cutting-off machine No. 1 with built-on motor and V-belt drive
|
|
|
|
|
|
|
|
|
|
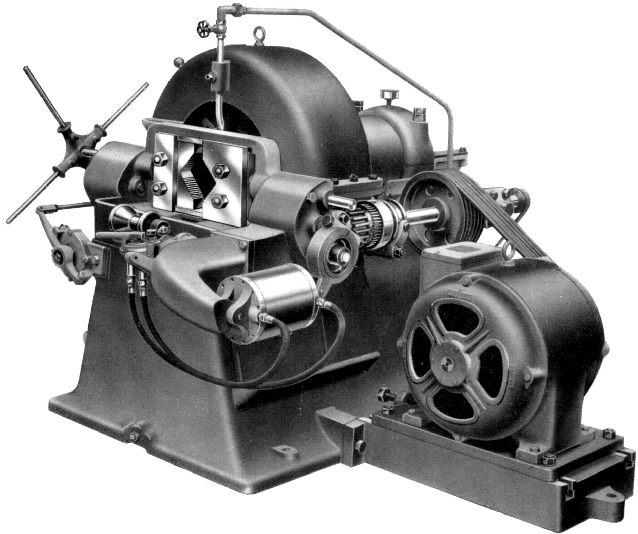 |
|
|
|
|
|
|
Taylor Rotary Cutting-off machine No. 2 with built-on motor, V-belt drive and a quick-action pneumatically-operated vice.
|
|
|
|
|
|
|
|
|
|
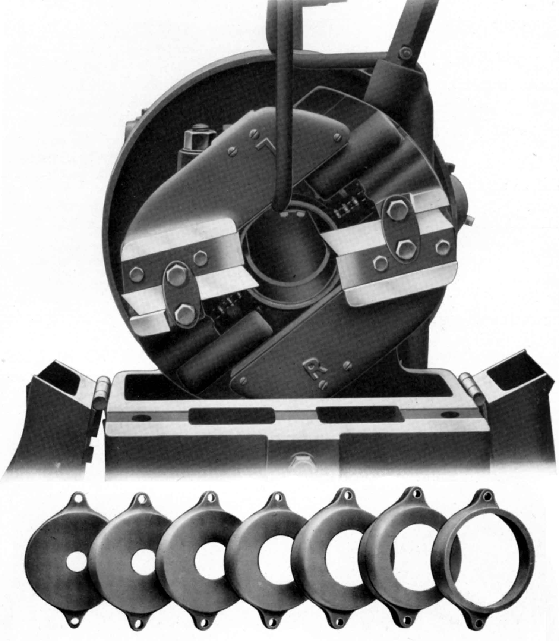 |
|
|
|
|
|
|
A picture of the mechanism with a Taylor cutting-off machine. The high-speed steel cutter blades were formed as parting-off blades used in a lathe with side relief to ensure that only the front edge cut and space was left for swarf to clear.
|
|
|
|
|
|
|
|
|
|
|
|
|
|
|
|
|