 |
 |
 |
 |
 |
 |
 |
 |
 |
 |
 |
 |
 |
 |
 |
 |
 |
 |
 |
 |
 |
 |
 |
 |
 |
 |
 |
 |
 |
 |
 |
 |
 |
 |
|
|
|
|
|
|
|
|
|
|
|
|
|
|
|
|
|
|
|
|
|
|
|
|
|
|
|
|
|
|
|
|
|
|
|
|
|
|
|
|
|
|
|
|
|
|
Designed in the early 1980s the Harrison M350 was to fit between the well-established (but approaching ten-year old) M300 and M400/450 lathes. As a model its production life was relatively short and, by 1998, it had been replaced by the almost identical M390 whose swing, in line with its model number, was 390 mm, whereas the swing of the M350 was actually 380 mm. Two bed lengths were offered: one gave 40 inches (1000 mm) between the centres the other 60 inches (1500 mm); either version could be had with or without a gap and both were induction hardened. With the gap section removed a piece of material 23 inches (585 mm) in diameter and 6 inches (150 mm) thick could be turned on the faceplate. With 12 speeds in geometrical progression from 40 to 2200 rpm the geared headstock was fitted with a cleverly-engineered speed-change system operated from a single dial, centrally positioned at the top of the headstock's front face. The spindle, able to accept a 2.125-inch (54 mm) diameter bar was fitted with a No. 6-D1 Camlock nose and ran in pre-loaded Gamet super-precision tapered roller bearings. Two types of drive system were offered: one, intended for serious production and industrial use was driven by a 5.5 kW motor and incorporated a Matrix mechanical forward-reverse clutch on the headstock-input shaft controlled by a lever mounted on the right-hand face of the apron (exactly as the M400 Model). The other system, better suited to lighter-duty and training establishment use, employed a 3.7 kW motor with electrical operation direct through a simple forward/reversing contactor - again controlled from the apron-mounted lever; both lathes were fitted with an electromagnetic fail-safe spindle brake. The headstock of 3.7 kW lathe, being lightly stressed, relied upon splash lubrication, whilst the more powerful model, with considerably greater forces to handle, was provided with pressure lubrication from a base-mounted pump and tank. Continued below:
|
|
|
|
|
|
|
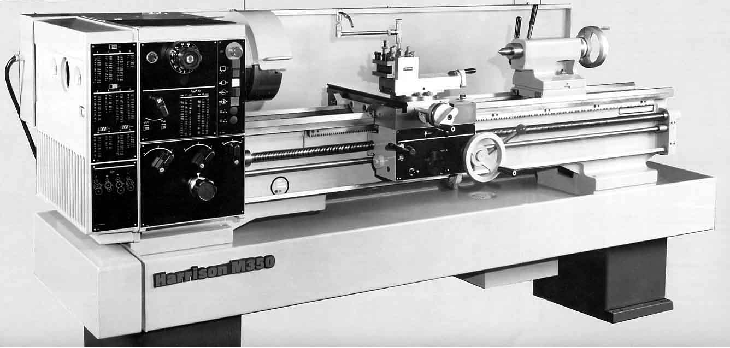 |
|
|
|
|
|
|
|
|
|
|
|
Continued: Fitted with induction-hardened gears the dual English/metric screwcutting gearbox was able to generate 51 metric pitches from 0.2 to 14 mm, 56 English pitches from 2 to 56 T.P.I., 20 Module pitches from 0.2 to 3.5 MOD and 20 Diametral pitches from 8 to 56 DP. 31 power-sliding feeds from 0.018 mm to 1.2 mm were available in the metric setting and another 31 from 0.0007 to 0.048 inches per revolution of the spindle in the English; the power cross feed rate was arranged to be half the sliding rate. The screwcutting gearbox was controlled by three smooth levers - that could be difficult to operate with oily hands - and a single rotary selector; an oil supply was held in the base and circulated by the simple but effective means of the lower gears dipping into it and splashing it about. The carriage was fitted with a conventional spoked wheel for movement by hand (on some models this could be disengaged to stop it turning when power feeds were engaged) with the 32 mm (1.26") diameter leadscrew (of 6 mm pitch or 4 t.p.i.) engaged only for screwcutting and additionally protected by a torque-limiter. A separate powershaft provided the sliding and surfacing feeds used in ordinary turning and facing. A push/pull button was used to select the power sliding and surfacing feeds with engagement by single lever in the middle of the apron that could be moved under light hand pressure no matter how deep the cut being taken. Although a centralised low-voltage push-button control "Station" was mounted on the headstock (that controlled the main motor, spindle brake, emergency stop and coolant pump) electrical control of the spindle was intended to be primarily from a lever attached to the right-hand face of the apron, where it fell conveniently to hand and, of course, moved with the carriage as a cut was taken. Of the full-length type the cross slide and top slide (the latter able to be swivelled through 360 degrees) were fitted with taper-type gib strips; the handwheels were of the typical Colchester/Harrison "semi-lever" type with the micrometer dials (dual-reading metric/English units were an optional extra) finished in non-glare satin chrome; backlash in the cross-feed could be adjusted out through the use of a (Colchester design) split nut and wedge. Robustly built the tailstock was fitted with a 63 mm diameter (2.48") spindle with 140 mm (5.5") of travel and a No. 4 Morse taper. The spindle was engraved with ruler marks in either inch or metric graduations (or sometimes both) with a rotary micrometer dial fitted as standard. Unfortunately the stand, through heavily constructed and complete with a splash-back, was fitted with neither a slide-out chip tray nor any sort of storage for tools, accessories or work in progress - though this may have been an unlisted factory extra. An M350 weighed 1254 Kg (2759 lbs) in 1000 mm between-centres' form and 1404 Kg (3088 lbs) as a long-bed 1500 mm capacity model. Approximate 88 inches (2240 mm) long in short bed form and 108 inches (2740 mm) as a long bed; the width in both cases is around 42 inches (1065 mm)..
|
|
|
|
|
|
|
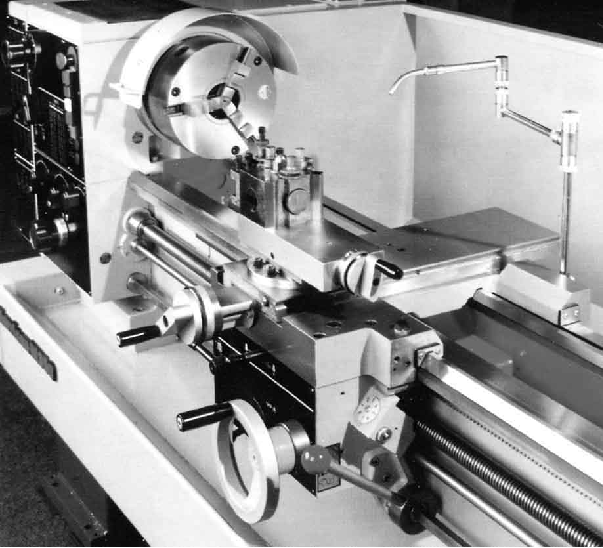 |
|
|
|
|
|
|
The cross slide was of the full-length type and both it and the top slide (which could be swivelled through 360 degrees) were fitted with taper-type gib strips; the handwheels were of the typical Colchester/Harrison "semi-lever" type with the micrometer dials (dual-reading metric/English units were an optional extra) finished in non-glare satin chrome; the cross feed screw nut could be adjusted to eliminate backlash.
|
|
|
|
|
|
|
|
|
|
|
|
|
|
|
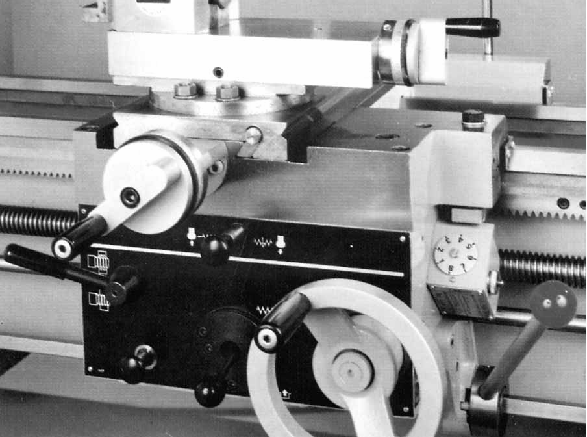 |
|
|
|
|
|
|
Fitted with a conventional spoked wheel for movement by hand, the apron carried both leadscrew and power-shaft driven feeds; the 32 mm (1.26") diameter leadscrew (of 6 mm pitch or 4 t.p.i) was engaged only for screwcutting (and carried a torque-limiter) whilst the powershaft provided the sliding and surfacing feeds used in normal work. A push/pull button selected the power sliding and surfacing feeds, with engagement by single lever in the middle of the apron.
|
|
|
|
|
|
|
|
|
|
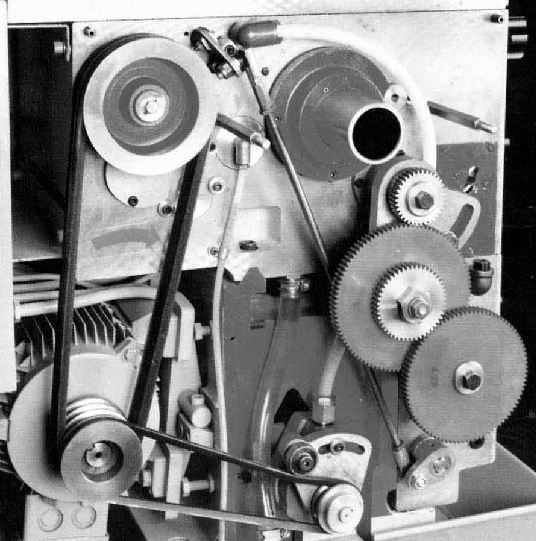 |
|
|
|
|
|
|
With the end cover removed from a heavy-duty headstock M350 the simple but effective rocking motor mount, quiet-running, non-metallic intermediate changewheels, the V belt drive to the headstock pressure lubrication pump (bottom) and long spindle clutch control rod are all clearly visible.
|
|
|
|
|
|
|
|
|
|
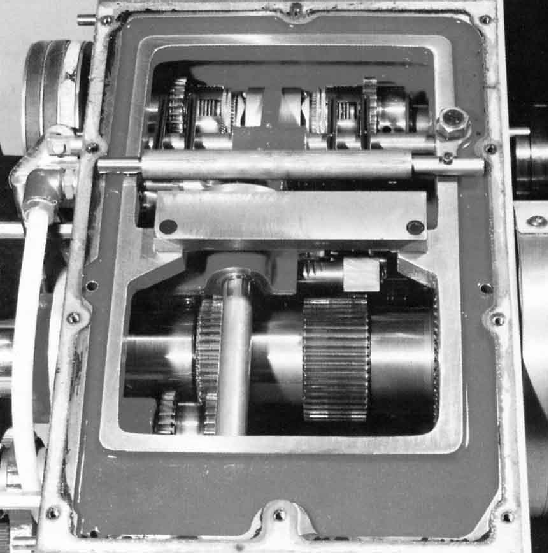 |
|
|
|
|
|
|
|
|
|
|
|
The geared headstock provided 12 speeds in geometrical progression from 40 to 2200 rpm all selected by a cleverly-engineered system from a single dial, centrally positioned at the top of the headstock's front face.
|
|
|
|
|
|
|
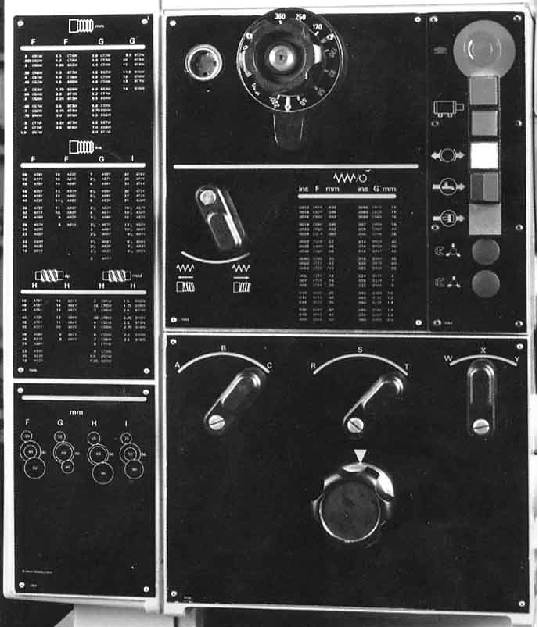 |
|
|
|
|
|
|
Clearly labelled and logically laid out headstock control panel. Although a centralised low-voltage push-button control "Station" was mounted on the headstock (which controlled the main motor, spindle brake, emergency stop and coolant pump) electrical control of the spindle was intended to be primarily from a lever attached to the right-hand face of the apron, where it fell conveniently to hand and, of course, moved with the carriage as a cut was taken.
|
|
|
|
|
|
|
|
|
|
|
|
|
|
|
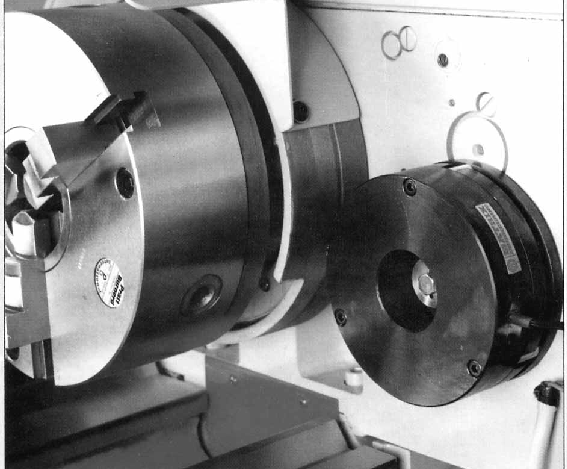 |
|
|
|
|
|
|
The black cylinder in the picture above is the end section of the Matrix forward-reverse clutch fitted to the headstock-input shaft .
|
|
|
|
|
|
|
|
|
|
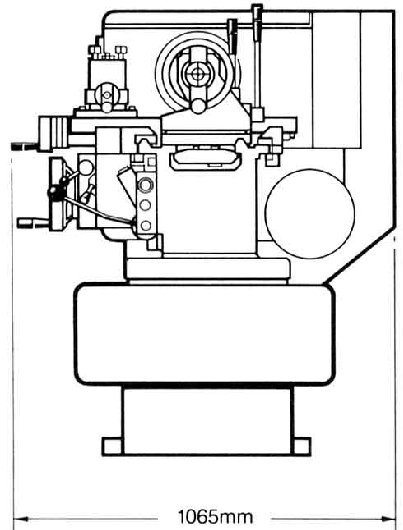 |
|
|
|
|
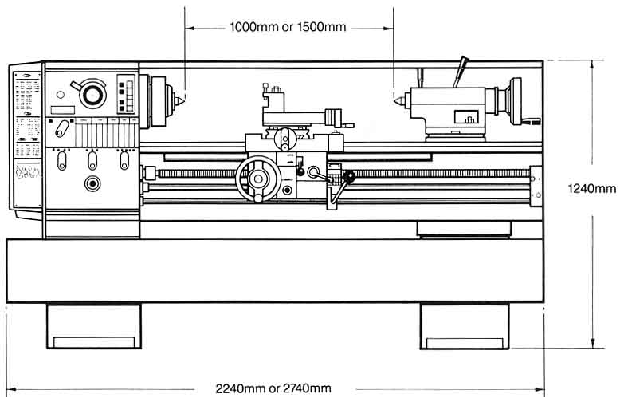 |
|
|
|
|
|
|
|
|
|
|
|