 |
 |
 |
 |
 |
 |
 |
 |
 |
 |
 |
 |
 |
 |
 |
 |
 |
 |
 |
 |
 |
 |
 |
 |
 |
 |
 |
 |
 |
 |
|
|
|
|
|
|
|
|
|
|
|
|
|
|
|
|
|
|
|
|
|
|
|
|
|
|
|
|
|
|
|
|
|
|
|
|
|
|
|
|
|
E-Mail Tony@lathes.co.uk Home Machine Tool Archive Machine Tools For Sale & Wanted Machine Tool Manuals Machine Tool Catalogues Belts
Emwee PR-8 Turret Lathe
Manufactured by L.P.Grothauzen in Venlo, Netherlands during the late 1940s and early 1950s, the interesting 7-inch centre height by 15 inches between centres EMWEE turret lathe was handled in the United Kingdom by Industrial Machine & Equipment Co. Ltd. of 41 Murray Road, London S.W.19. Heavily built (it weighed just over half a ton) the bed and headstock cast were cast as-one in Mehanite iron and carried on a stand made from welded steel plate. A tool storage cabinet was built into the stand's right-hand face, a lift-off door for access to the drive system provided on the left-hand face and another hinged door at the rear on which was carried the optional coolant equipment. Of an unusual and interesting design for a small production machine, the indexing cutting and threading tools were carried not by the usual type of bed-mounted rotating turret, but in a massive, patented, horizontal revolver-type 'tailstock' that could be specified with either four or six No. 2 Morse taper holders formed in the end of its large diameter, rotating spindle. The stroke, driven by a long handle, was 4.375", with each holder having its own screwed stop and indexed round in the usual way to line up with the headstock spindle. If required, for conventional between-centres work the spindle could be locked and, if the lathe was intended for just for simple boring or drilling jobs (though at a very expensive £575 in 1952 this would have been a hopelessly uneconomic proposal), a much lighter, ordinary No. 2 Morse taper single-spindle lever-action tailstock was offered in lieu of the capstan version. One special extra offered by the makers to fit the turret was a set of threading taps and dies; the length of thread to be cut could be pre-set on the diehead with the system claiming to be unusually fast. Made from high-tensile steel, the 1.375" bore headstock spindle ran in adjustable, high-precision twin-type SKF roller bearings with SKF ball races for thrust. The nose, in standard form, was fitted for collets only, though at extra cost it could be modified to accept a 3-jaw chuck. Hardened, ground and tempered in the usual way and manufactured to an accuracy of better than 0.0004", the collets were available in sets to hold round, square or hexagon stock and had a maximum through bore of 1.1875". The collet opening and closing action was by a lever working through two toggles (all the revolving and sliding parts being hardened and ground) with a separate lever-operated spindle lock provided to allow easy changing of collets or fittings on the spindle nose. Three options were available for the drive system with single, two and four-speed motors all listed. The drive, on all types of motor, was taken upwards by a single V-belt to a countershaft fitted with a 4-step V-pulley (early models had just 3) that in turn drove upwards to a matching pulley mounted on the spindle outboard of the left-hand spindle bearing. With the single speed motor and backgear, eight spindle speeds were available from 300 to 2100 r.p.m.; the two-speed motor and backgear gave 16 that spanned 150 to 2100 r.p.m. while the four-speed provided 16 speeds from 120 to 3360 r.p.m. The latter arrangement allowed the operator to go from the highest to the slowest speed in one movement, a great time-saving feature when turning small diameters that then had to the threaded. Electrical controls were, of course, built-in with a neutral, forwards and reversing switch was mounted centrally on the front face of the headstock. To tension and slacken the belt to allow for changes of speed, both the motor platform and intermediate countershaft were connected together by a vertical rod split into upper and lower sections with each threaded so that the belts could be individually tensioned - while the operating lever being connected to a pivot point between the two parts that allowed the whole system to be slackened by in just one movement. Instead of the expected simple lever-operated cut-off (forming) slide, the Emwee was fitted as standard with a conventional form of screw-feed compound slide rest - though the details of its arrangement construction were far from ordinary. Costing an extra £40 (only a little less than a complete backgeared and screwcutting contemporary Myford ML7 lathe) it was mounted on and able to rotate about a separate circular boss fitted in front of the bed - the whole assembly able to be slide along for a short distance and locked down by a through-bolt with the clamping levers emerging from the underside of a recess in the centre of the stand. The slide rest had 7 inches of longitudinal travel, 5 inches across and could be had in various specifications with either all-screw or all lever feed or fitted with a capstan-handle-operated longitudinal feed with a combination screw and lever-feed cross-motion. When fitted with screw feeds the micrometer dials had vernier scales that allowed settings down to as fine as 0.002". Both cross and top slides had beautifully made and adjustable 4-position drum-type stops, each being rotated into position as required. A 4-way toolpost was fitted as standard, its mechanism cleverly designed so that one-handed operation was possible - a one-quarter turn of the handle rotating the next tool into position and locking the unit down. As an additional refinement, as the toolpost turned it was not lifted, so avoiding the ingress of swarf and dirt. Fitted as part of the ordinary equipment was a mechanical copying device; this consisted of the necessary template, attached by three screws to a bar protruding from the rear of the headstock's front face, and a pilot rod fixed to the rear of the cross slide. Several accessories were listed including a bar-feed unit at £30 : 0s : 0d; a 3-jaw chuck; coolant equipment at £41 : 8s : 6d; a slide rest with just cross travel - but with this operated by both screw and lever feeds - at £40 : 0s : 0d; a set of round collets from 5 to 30 mm at £2 : 15 ; 0s each; collets for square material at £3 : 16 : 3d each and collets for hexagon material at £5 : 0s : 0d each.; Pafix tapholder £27 : 18s : 0d; Pafix dieholder £28 : 11s : 0d and Jacobs Boring Heads £4 : 8s : 0d each. Other examples of might be termed "late-type, professional-class compact capstan lathes" (as distinct from the smallest Ward and Herbert models) include the Italian Ceriotti, the British Accuratool, Britan, Exacta, the Spanish Elgo and versions of the German Weiler 260..
|
|
|
|
|
|
|
|
|
|
|
|
|
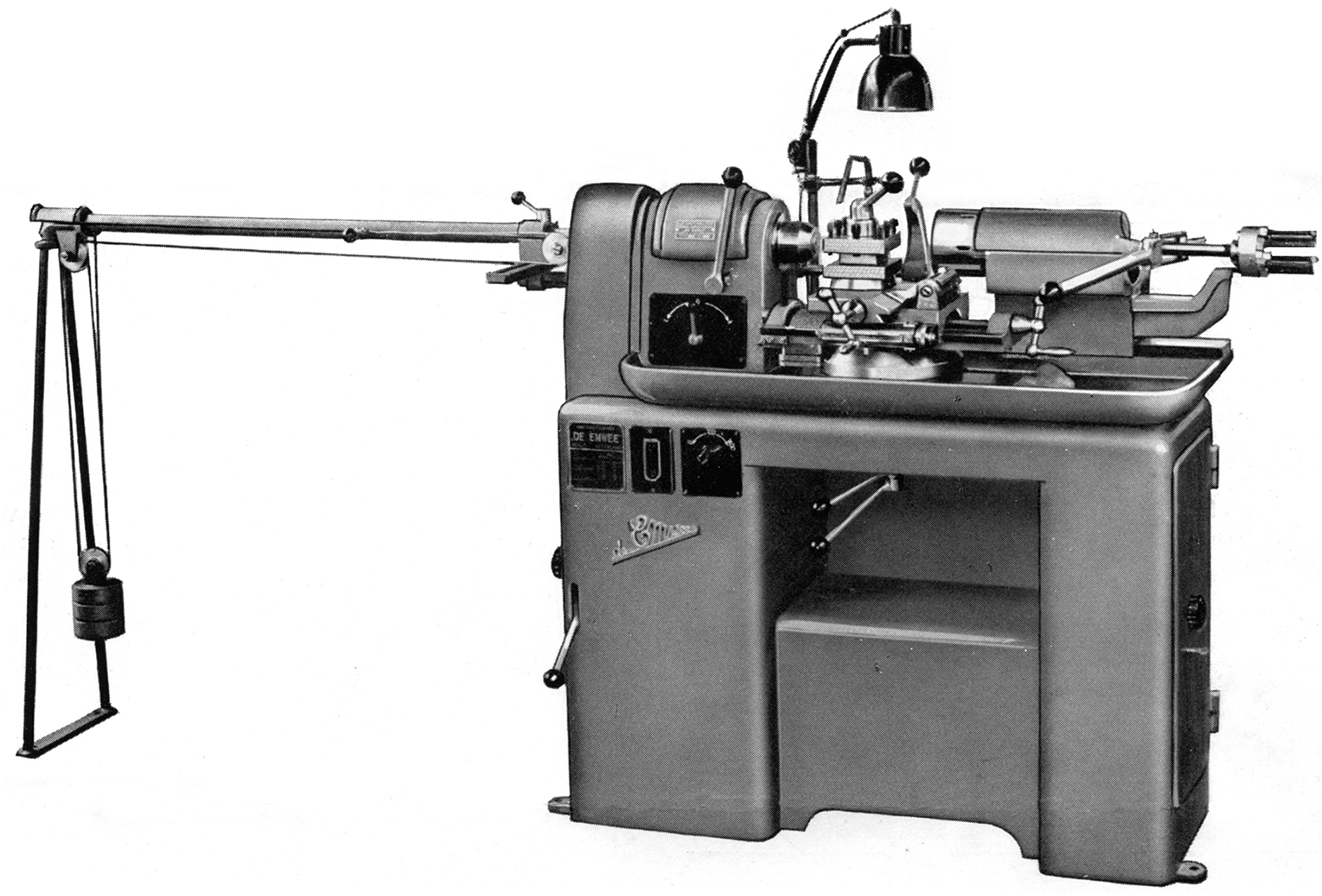 |
|
|
|
|
|
|
Emwee PR8 Turret lathe with a weight-powered bar-feed attachment
|
|
|
|
|
|
|
|
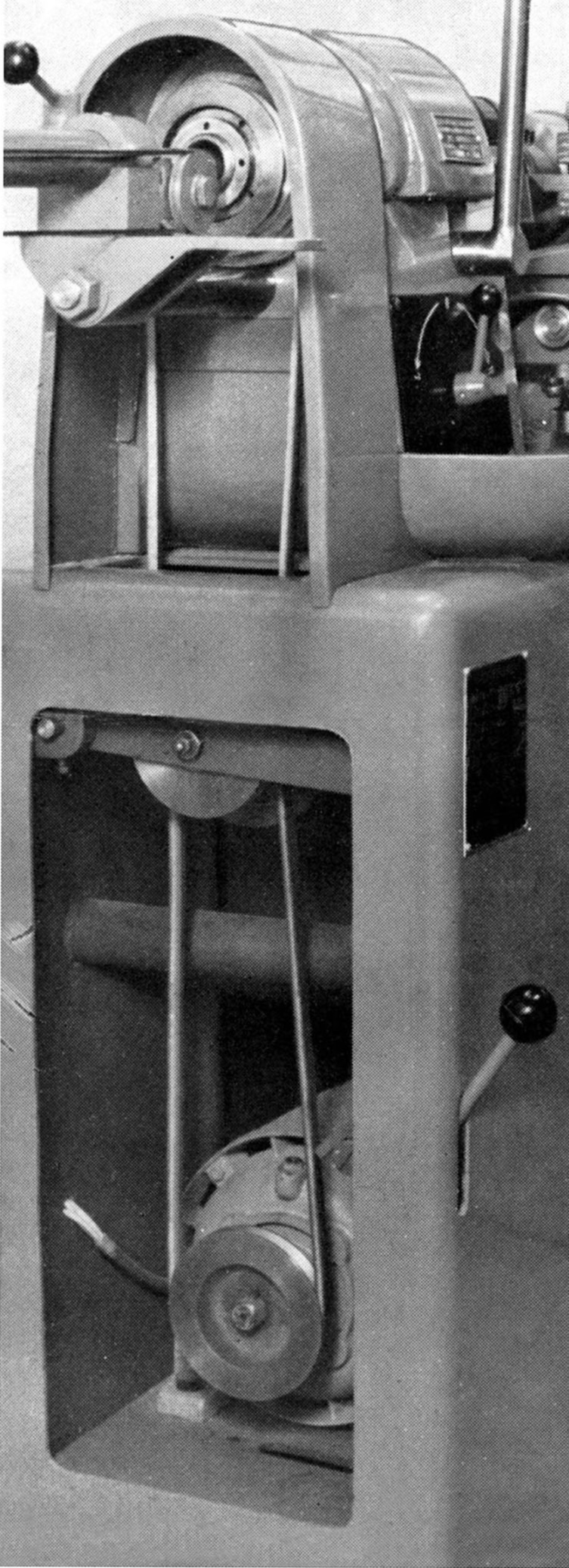 |
|
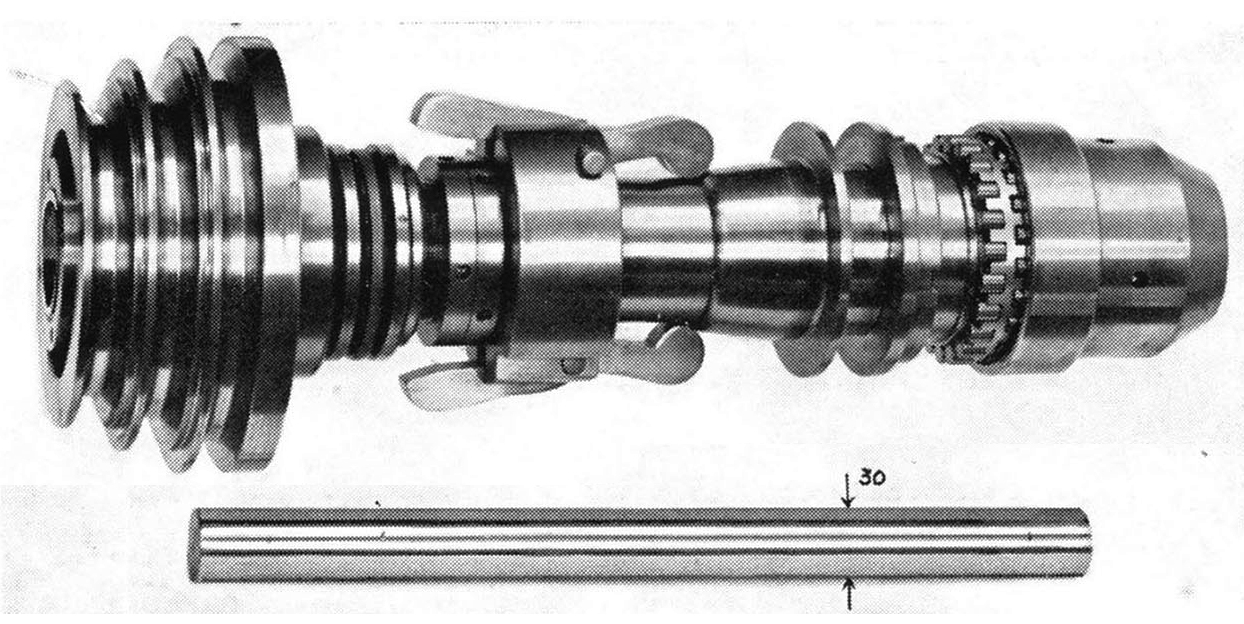 |
|
|
|
|
|
|
|
Made from high-tensile steel, the 1.375" bore headstock spindle ran in adjustable, high-precision twin-type SKF roller bearings with SKF ball races for thrust. The nose, in standard form, was fitted for collets only, though at extra cost it could be modified to accept a 3-jaw chuck.
|
|
|
|
|
|
|
|
|
|
|
Three options were available for the drive system with single, two and four-speed motors all listed. The drive, on all types of motor, was taken upwards by a single V-belt a countershaft fitted with a 4-step V-pulley that in turn drove upwards to a matching pulley mounted on the spindle outboard of the left-hand spindle bearing. With the single speed motor and backgear, eight spindle speeds were available from 300 to 2100 r.p.m.; the two-speed motor and backgear gave 16 that spanned 150 to 2100 r.p.m. while the four-speed provided 16 speeds from 120 to 3360 r.p.m. The latter arrangement allowed the operator to go from the highest to the slowest speed in one movement, a great time-saving feature when turning small diameters that then had to the threaded. Electrical controls were, of course, built-in with a neutral, forwards and reversing switch was mounted centrally on the front face of the headstock. To slacken the belt to allow for changes of speed, both the motor platform and intermediate countershaft were connected together by a vertical rod split into upper and lower sections with each threaded so that the belts could be individually tensioned - the operating lever being connected to a pivot point between the two parts.
|
|
|
|
|
|
|
|
|
|
|
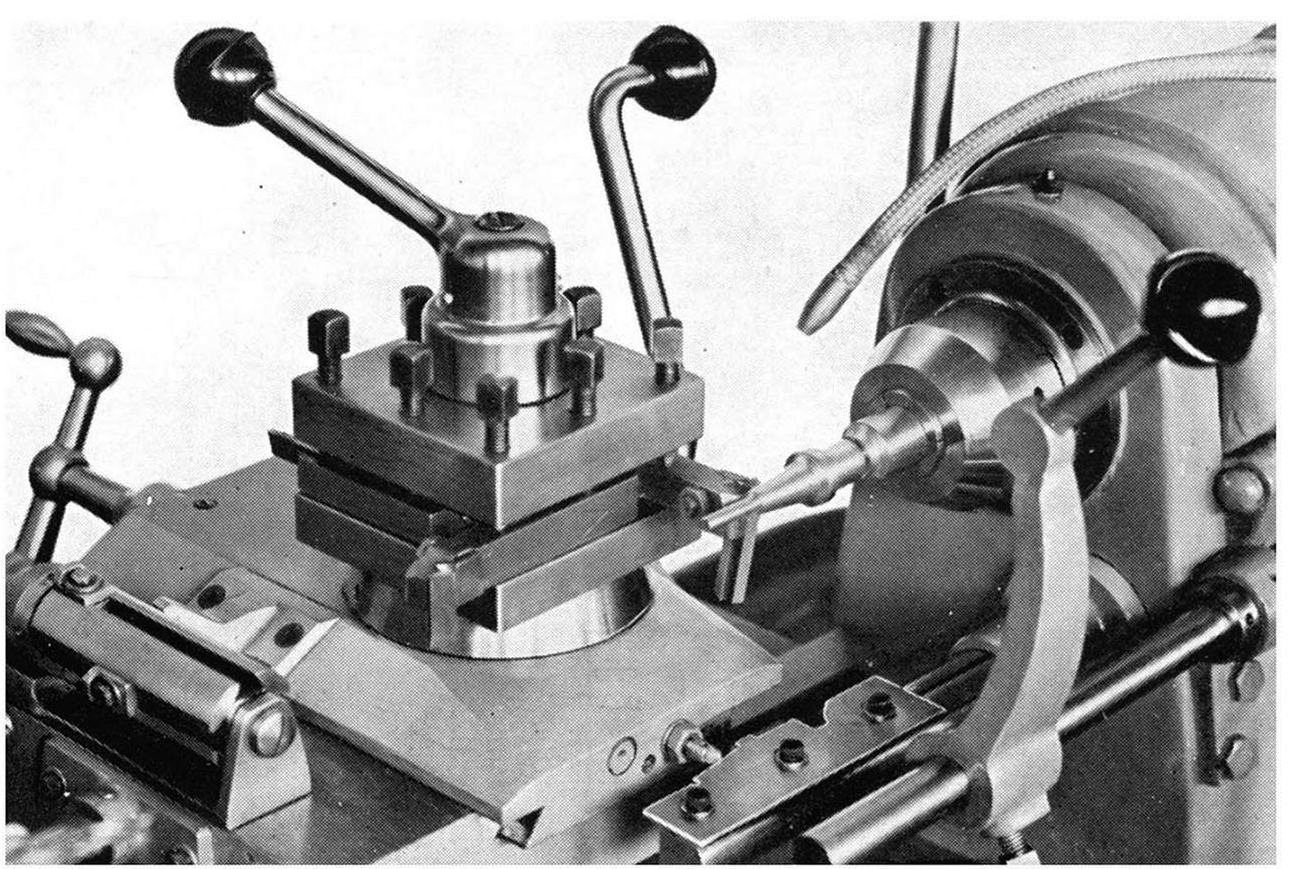 |
|
|
|
|
|
|
Copying Attachment Of simple design this unit consisted of a pilot rod, tracer and a suitable template. The pilot rod could be adjusted axially and, when not in use, easily removed. The template was fixed to the pilot rod with three screws.
|
|
|
|
|
|
|
|
|
|
|
|
|
|
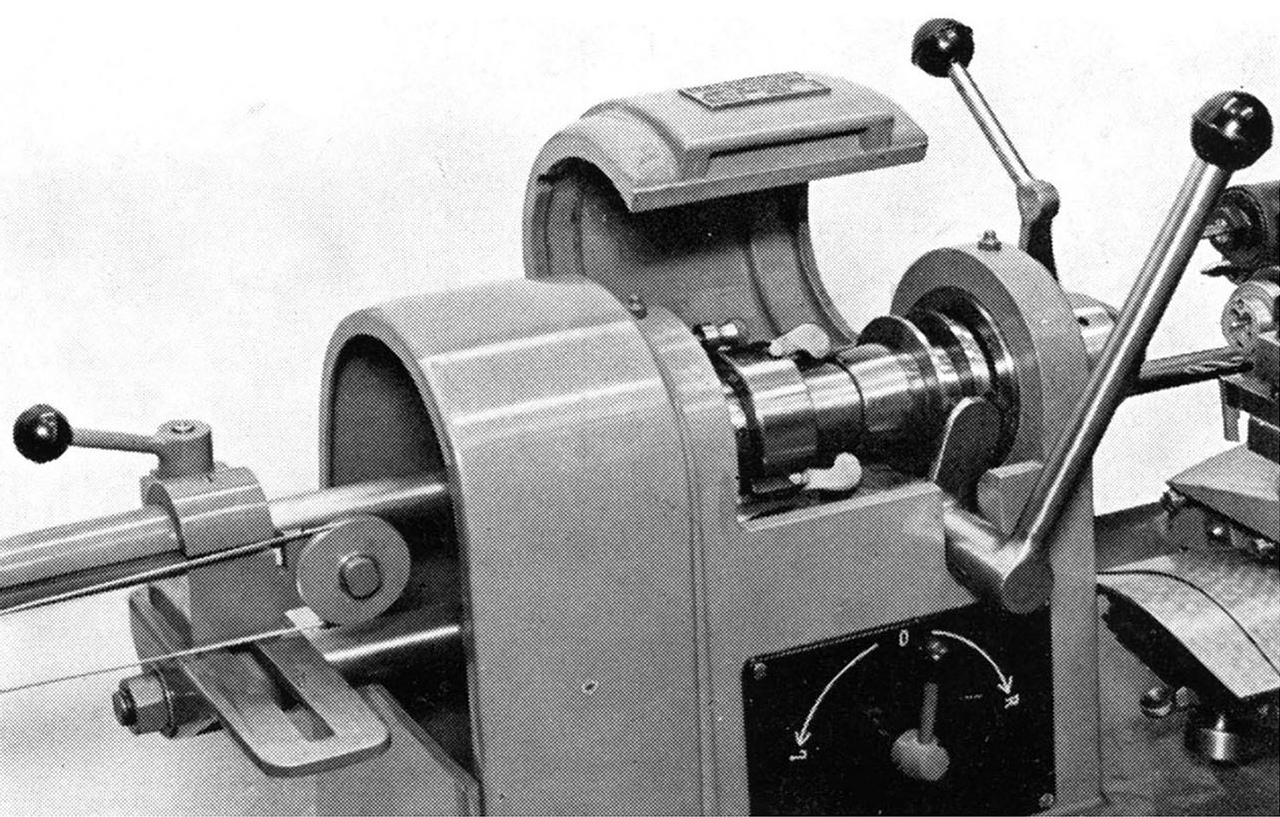 |
|
|
|
|
|
|
Made from high-tensile steel, the 1.375" bore headstock spindle ran in adjustable, high-precision twin-type SKF roller bearings with SKF ball races for thrust. The nose, in standard form, was fitted for collets only - though at extra cost it could be modified to accept a 3-jaw chuck.
|
|
|
|
|
|
|
|
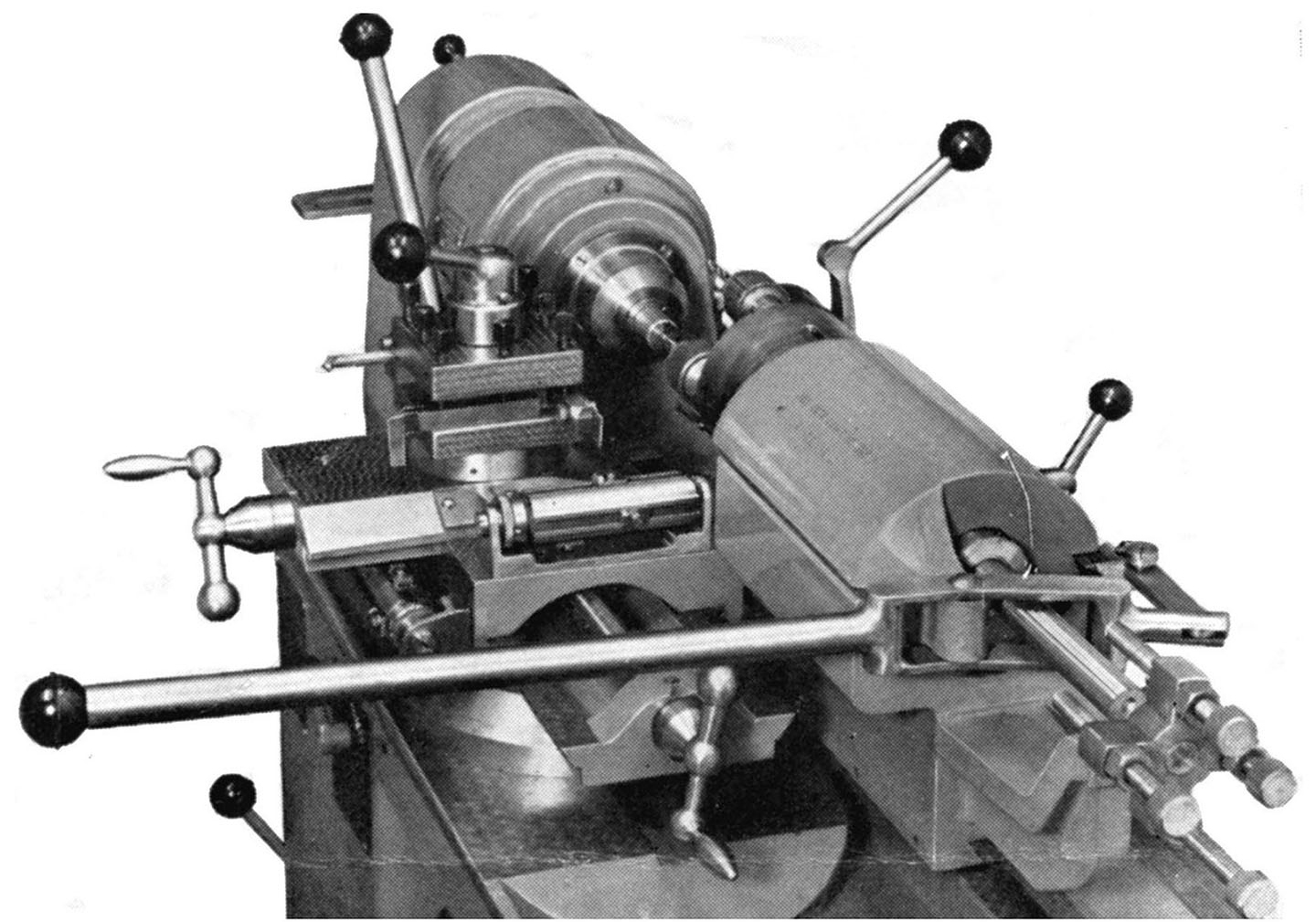 |
|
|
|
|
|
|
Of unusual design for a small production machine, the indexing cutting and threading tools were carried not by the usual type of bed-mounted rotating turret, but in a massive, patented tailstock that could be specified with either four or six No. 2 Morse taper holders formed in the end of its large diameter, rotating spindle. The stroke, driven by a long handle, was 4.375", with each holder having its own screwed stop and indexed round in the usual way to line up with the headstock spindle. If required for conventional between-centres work, the spindle could be locked.
|
|
|
|
|
|
|
|
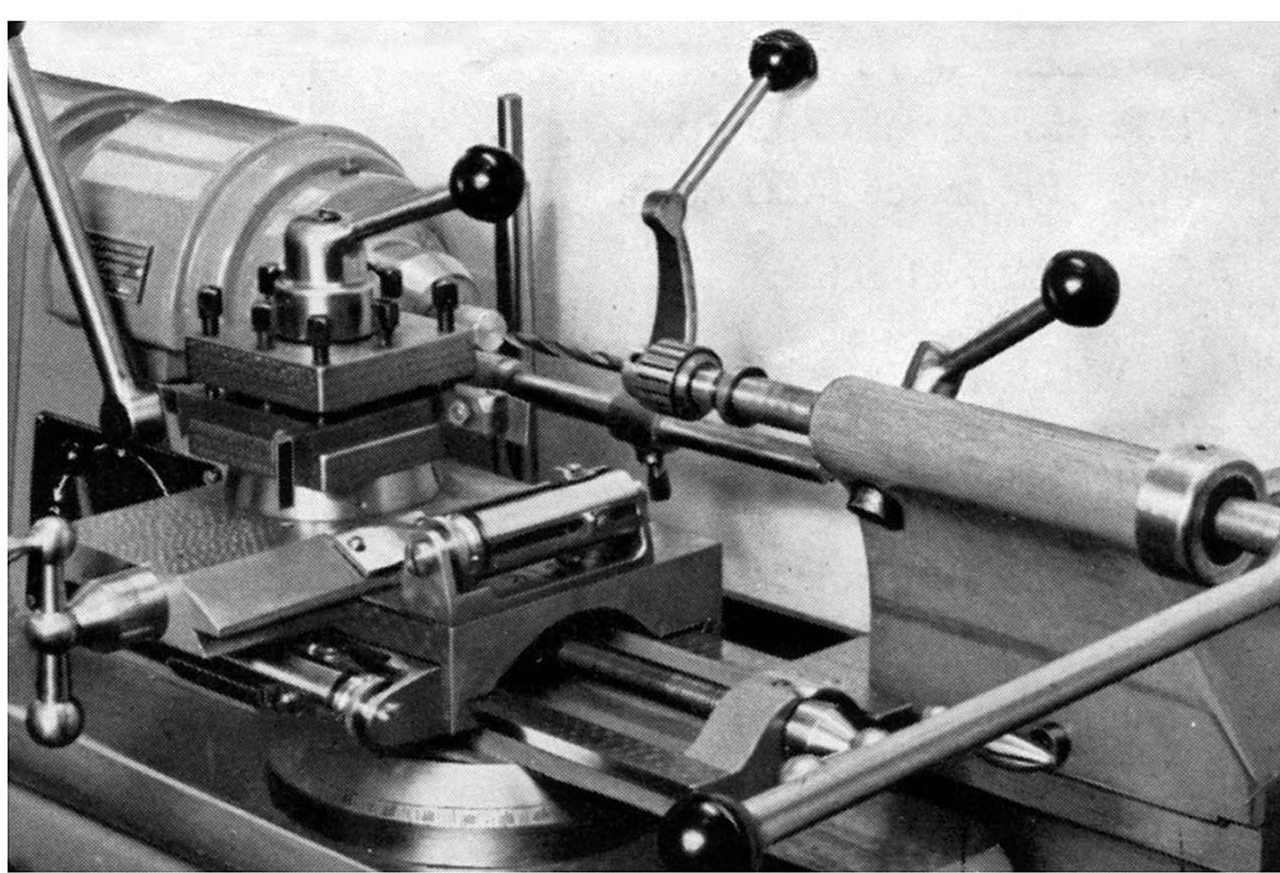 |
|
|
|
|
|
|
If the lathe was intended for just for simple boring or drilling jobs (though at a very expensive £575 in 1952 this would have been a hopelessly uneconomic proposal), a much lighter, ordinary No. 2 Morse taper single-spindle lever-action tailstock was offered in lieu of the capstan version.
|
|
|
|
|
|
|
|
|
|
|
|
|
|
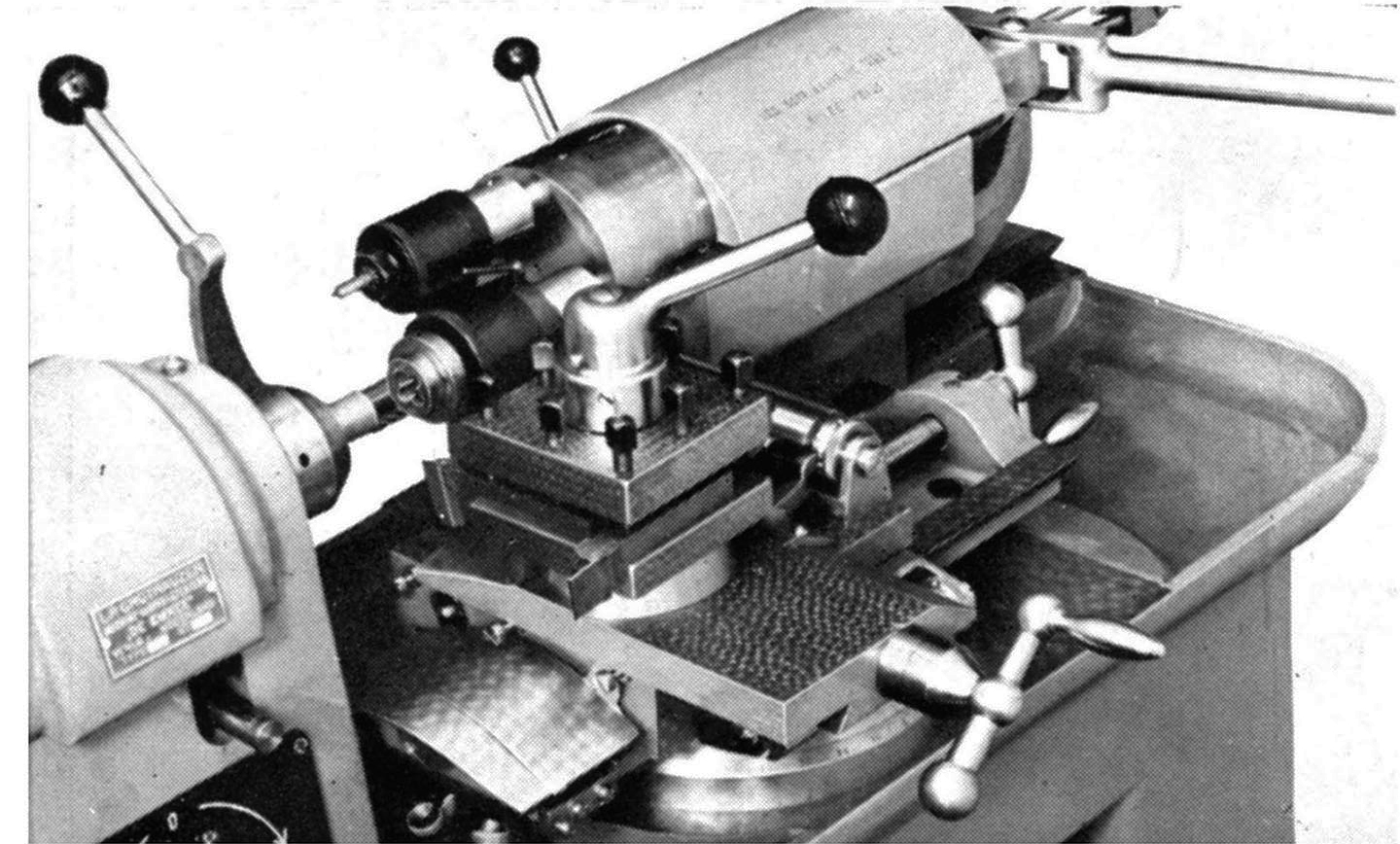 |
|
|
|
|
|
|
A 4-way toolpost was fitted as standard, its mechanism being cleverly designed so that one-handed operation was possible - a one-quarter turn of the handle rotating the next tool into position and locking the unit down. As an additional refinement, as the toolpost turned it was not lifted, so avoiding the ingress of swarf and dirt..
|
|
|
|
|
|
|
|
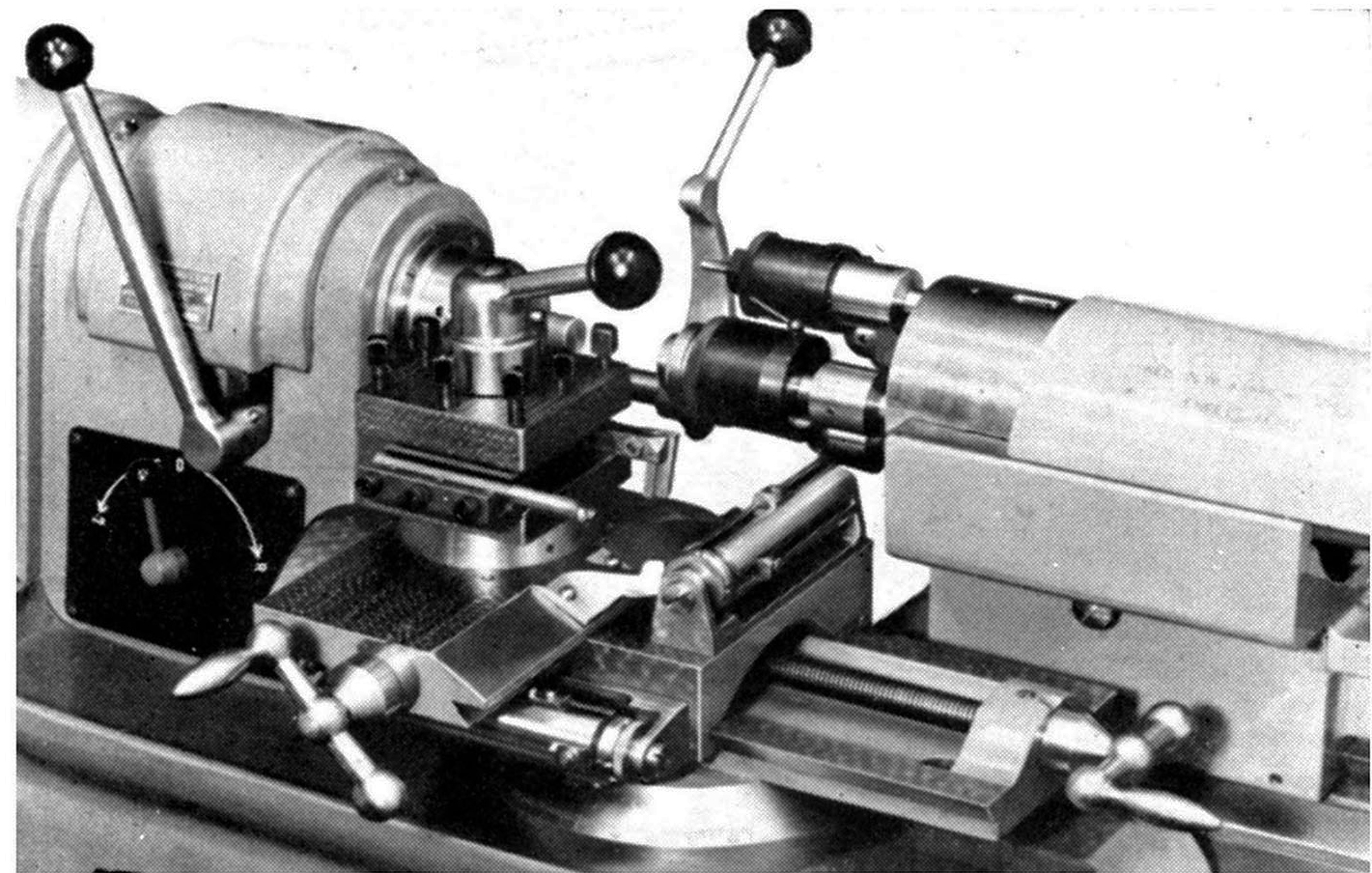 |
|
|
|
|
|
|
Instead of the expected simple cut-off (forming) slide, the Emwee was equipped with a conventional form of compound slide rest - though the details of its arrangement construction were far from ordinary. Costing an extra £40 (only a little less than a complete backgeared and screwcutting contemporary Myford ML7 lathe) it was mounted on and able to rotate about a separate circular boss fitted in front of the bed - the whole assembly able to be slide along for a short distance and locked down by a through-bolt with the clamping levers emerging from the underside of a recess in the centre of the stand. The slide rest had 7 inches of longitudinal travel, 5 inches across and could be had in various specifications with either all-screw or all lever feed or fitted with a capstan-handle-operated longitudinal feed with a combination screw and lever-feed cross motion.
|
|
|
|
|
|
|
|
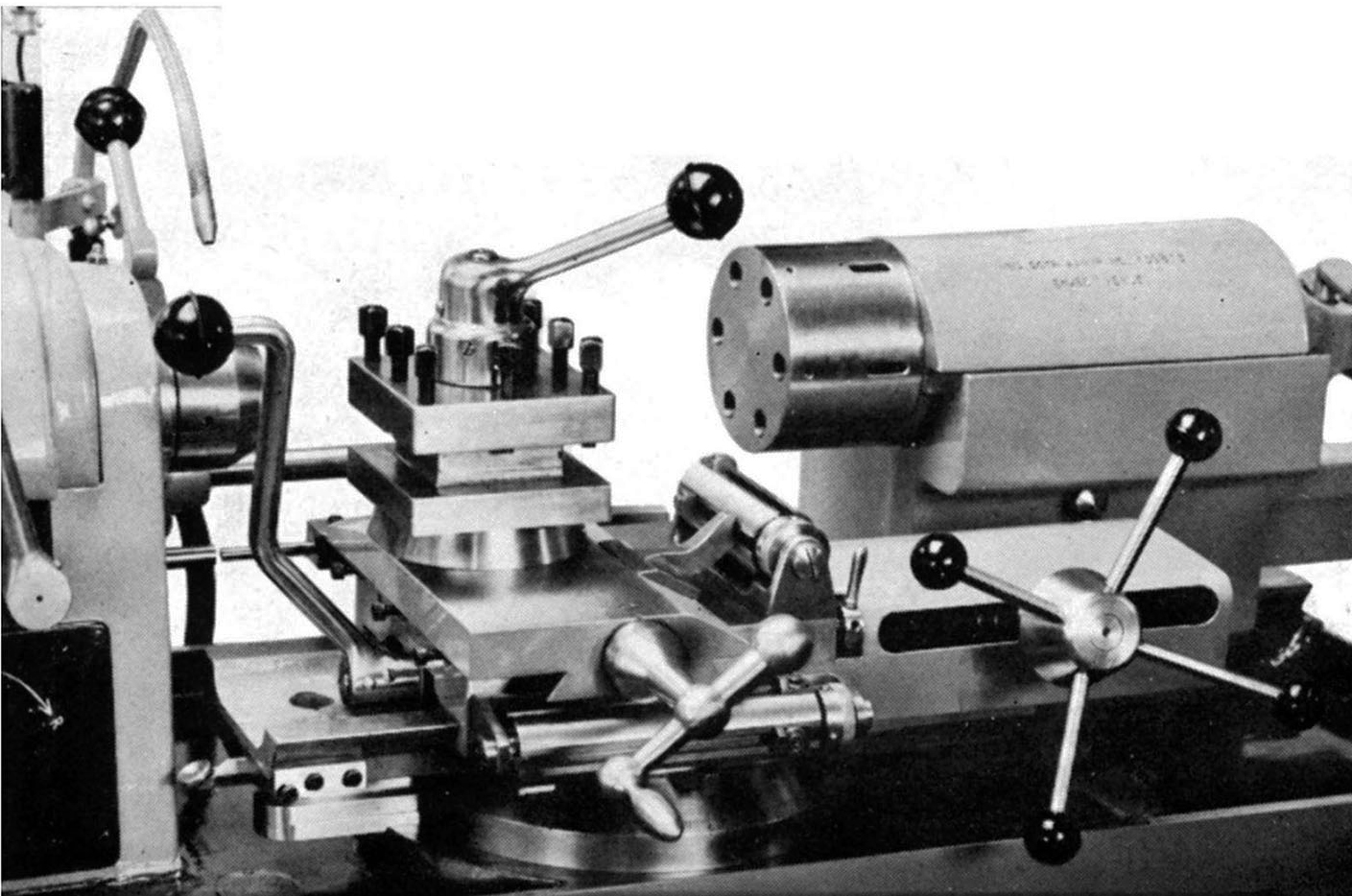 |
|
|
|
|
|
|
Compound slide assembly with lever-action feeds. The cross-feed could be operated by lever or screw - a small toggle handle being provided on the right-hand side of the slide to lock the lever when the screw was in use.
|
|
|
|
|
|
|
|
|
|
|
|
|
|
|
|