 |
 |
 |
 |
 |
 |
 |
 |
 |
 |
 |
 |
 |
 |
 |
 |
 |
 |
 |
 |
 |
 |
 |
 |
 |
 |
 |
 |
 |
 |
 |
 |
 |
 |
 |
 |
 |
 |
 |
 |
 |
 |
 |
 |
 |
 |
 |
 |
 |
 |
 |
 |
 |
 |
 |
 |
 |
 |
 |
 |
 |
 |
 |
 |
 |
 |
 |
 |
 |
 |
 |
 |
 |
 |
 |
 |
 |
 |
 |
 |
 |
 |
 |
 |
 |
 |
 |
 |
 |
 |
 |
 |
 |
 |
 |
 |
 |
|
|
|
|
|
|
|
|
|
|
|
|
|
|
|
|
|
|
|
|
|
|
|
|
|
|
|
|
|
|
|
|
|
|
|
|
|
|
|
|
|
|
|
|
|
|
|
|
|
|
|
|
|
|
|
|
|
|
|
|
|
|
|
|
|
|
|
|
|
|
|
|
|
|
|
|
|
|
|
|
|
|
|
|
|
|
|
|
|
|
|
|
|
|
|
|
|
|
|
|
|
|
|
|
|
|
|
|
|
Cataract-branded machine tools had their origins in two firms: the Cataract Tool and Bicycle Company (allegedly named after the waterfalls visible from the factory grounds) and the Cataract Tool and Optical Company the latter being incorporated in Buffalo (New York) and probably, in reality, not a separate organisation but part of Tool and Bicycle. In order to acquire rights to the company's rifle scopes, the Cataract enterprise had been bought out in 1902 by the well-known gun and tool maker J. Stevens Arms & Tool Company, of Chicopee Falls, Massachusetts. Stevens, who employed the skills of former Cataract manager Mr. F. L. Smith, continued to market the scopes under their original name but, shortly afterwards, passed the machine-tool side of the business on to Hardinge Brothers. The first catalog of the newly acquired organisation was issued in 1903 and, under a Hardinge heading, showed the Company's first "Cataract" branded bench lathe. However, improvements were soon in hand and in November 1903 Hardinge filed patents (Nos. 894634 and 894635) concerning modifications to the headstock spindle and bearing assembly and spindle nose. A successful design, both the bearings (together with the novel spindle fitting) were to remain in use for several decades. Very early headstocks can be recognised by the lack of a cast-in boss to the left-hand end of the rear face, a fitting used to provide a mount for the pivot point of a lever-action collet closer. With the addition of the Cataract brand (it was to survive until about 1940 as a marketing name together with Elgin, another Hardinge brand whose story is related here), Hardinge expanded their range considerably and went on to manufacture (as Hardinge Bros. and from 1931 onwards as the newly-formed Hardinge Mfg. Co.) a superb precision backgeared and screwcutting toolroom lathe (made from approximately 1912 to 1925), a limited range of milling machines, their famous collets and other work-holding devices and a number of watchmakers' and toolmakers' plain-turning lathes (for details of WW2 and after, look in the Hardinge section of the Archive). The toolmaker's plain-turning lathes, beautifully constructed and finished, were by far the most important and profitable models in the company's catalogue: they evolved through three distinct models - all with the same bed and each being an improvement on its immediate predecessor - yet with the earlier version always remaining in production for some time alongside the newer. Although the term "Bench Lathe" no longer implies a very-high quality, precision tool, when these lathes were at the height of their popularity, in the first half of the 20th century, that was the expression often used to designate this class of machine. Supported on elegant round feet (a trade mark feature of the maker) the bed was almost exactly similar in section to that used on many watchmaker's lathes with a largely round under section topped by a flat surface with bevelled edges to locate the headstock, compound slide and tailstock. Later models had a bed of modified section that was stiffened by the addition of a long rectangular section along the underside - a feature visible in the pictures immediately below. A slot was cut vertically through the bed to allow the compound slide rest (or other components) to be repositioned and secured with the usual sort of capstan-handwheel bearing against a flat machined along the underside of the bed. While the compound slide rest was held against the bottom of the bed, the headstock, tailstock and various accessories were secured in place by bolts held in a T-slot cut into full length of the top surface. From ,it is believed, 1907, a distinctive cast-iron tool tray was fitted immediately below the headstock and secured with two slot-head 14-24 screws on 5 9/16" centers. A variety of headstocks was offered to take 3C, 4C, 5C, 6C and 7C collets. Of course, the higher the number the larger the collet with the suffix "C" standing for Cataract. Unfortunately, although Hardinge continued to make 3C, 4C and 5C collet lathes until 1955 period, after about 1931 the 7C was dropped. The 3C collet is very common and used on all South Bend 9 inch lathes and their various clones including Boxford and Hercus, etc. even more popular the 5C collet was become the most common collet in the world, with many lathes and fixtures designed specifically to use it. The 5C collet is 1-3/8 inch in diameter, the 6C collet 1-5/8 inch and the 7C collet 2 inches with a maximum bore of 1-11/16 inches. Hence a Cataract 7C headstock probably the largest ever bore fitted to a series production small lathe. Made from the finest grade of cast-iron, seasoned and heat-treated the headstock casting was hand scraped to fit the lathe bed; early machines followed the traditional design for this type of lathe with the smallest of the three headstock pulleys being positioned to the right, so allowing the all-important front bearings to be made larger and also (because the smaller pulley left a greater clearance) surrounded by as great a mass of supporting material as possible. However, in the case of earlier Cataract models, it is obvious that full advantage was not taken of this design point - some considerable "daylight" being left around the assembly. The headstock spindle, made from ball-bearing steel, was hardened and ground both internally and externally and ran in hardened plain bearings - this arrangement being the very best that the technology of the day could provide - and one that stood the test of time, with many lathes clocking up tens of thousands of hours of arduous service at high rpm without showing any signs of wear. The spindle nose carried a patented Hardinge quick-action taper fitting (that was to be used on all their lathes until modern times) although, if the customer preferred, an ordinary thread could be supplied instead. To assist with chuck and faceplate removal, the outside flange of the largest belt pulley was provided with four holes that could be engaged by a substantial sliding pin at the rear of the headstock; the same pulley face also carried a ring of 60 indexing holes.
|
|
|
|
|
|
|
|
|
|
|
|
|
|
|
Later lathes adopted an even more rigid headstock, with the spindle running in specially-made, high-precision, pre-loaded ball-bearing races; the makers rightly claimed that with this improved arrangement not only could speeds be higher for a given size of motor, but under heavy cuts the spindle was less likely to deflect and loose accuracy - and so critical jobs could be completed in a shorter time. Eventually, to obtain even greater rigidity, the headstock was completely enclosed (a design that had been used for some years on larger Hardinge lathes) and the belt changed from a flat to a twin or triple V. While the V-belts were claimed to be an advantage in terms of grip under high loads, when the maintenance fitters arrived to fit new ones they would not have been best pleased when faced with an extensive amount of dismantling work - followed by even more careful reassembly and the checking of bearing clearances, pre-loads and belt-run alignments. The makers had an interesting point to make about the headstock ball bearings; they explained that the loads on a plain bearing were supported by a film of oil: "…. the success of which depends upon such variable factors as the film thickness, the temperature and difference in the grades of oil used. With a pre-loaded ball bearing the pressure between balls and races is such as to prevent formation of an oil film and the contact of load carrying members is positively metal-to-metal. In other words the load is carried on perfect spheres of hardened steel instead of globules of oil whose load-carrying ability varies with the operating temperature. Naturally, accuracy with speed and long life is attained." This is an interesting point - but, have you ever tried degreasing a ball race and then seeing how long it lasts under a heavy load ? It is hardly an experiment that needs to be conducted. As important a part of a precision the lathe as the headstock, the compound slide rest had to offer the turner a component that was delicate to operate - yet strong enough to resist all the forces it was likely to encounter. However, a persistent criticism of the Cataract unit was the single T slot in the top slide; many European makers of precision bench lathes including two slots as standard, an arrangement that allowed the operator much great freedom to place tooling when dealing with awkwardly-shaped jobs. A unit that changed little over the years, some six examples (some shown below) have been identified that reflect its development from 1900 to 1946. From 1900 to the early 1920s the compound was made in different versions to suit the 7" and 9" swing lathes; the 7" version had 4.5" of movement on the cross slide and 3.5" on the top - while that for the larger lathe had 5.25" and 4.5" respectively. An adjustable stop was fitted to the cross-slide movement, the micrometer dials could be zeroed and the unit was well designed with a 4-bolt end plate to the cross slide and hardened thrust washers to each side of the feed screw thrust. The whole unit was made of the finest quality materials and beautifully finished - but the top slide was limited to 45 degrees of swivel each side of the zero line. Current during the 1920a and early 1930s, the next version had slightly diameter larger (17/16") micrometer dials and a rounded front edge to the top slide with recessed gib-strip adjustment screws - but seems to have lost the hand-scraped finish of the original. By the late 1930s the slide had been given a distinctive block-type top slide casting and micrometer dials with parallel faces. Although the 1940s version of the compound slide may have looked a more prosaic item in comparison with its glittering predecessors, it was considerably improved in several areas: the method of clamping the slide to the bed was changed to give a much broader support (it had originally been held by a single, central T slot; the change is illustrated below); the micrometer dials were at last of a reasonable size for a precision lathe - a full two inches - with the cross slide plate triangulated to support the dial housing; feed screws were hardened, ran in long bronze nuts and were supported in ball races where they passed through their end plates; the top slide could now be swivelled through a complete circle with the degrees graduations engraved into the flat surface of the cross slide; this also allowed the top slide to bear against a much wider ways instead of being less well supported at the extremes of its travel. One useful identification point for older slide rests is that all pre-1946 Hardinge/Cataract top slides had a lengthened feed screw to pick up the drive from the changewheel-driven screwcutting attachment. Post 1946, and with the introduction of the new dovetail bed lathes (based on the basic DV-59) an altered compound slide assembly was introduced that lacked the extension piece - the fitting of a proper "Chase" screwcutting attachment rendering its use unnecessary (with an eye to increased sales, Hardinge also made the new compound with a base to fit the older, "split-bed" models). Although the Chase screwcutting had been available on the early lathes, the new-for-1946 models had the bed machined on the rear face to accept the attachment together with redesigned master threads. After some years (and probably as a result of only a slight take-up of the attachment and to save costs) the machining of the bed rear was abandoned and by 1960, after a major redesign of the DV-59 Series, there was no provision for single-point threading at all. All early Cataract lathes came without a stand or drive system, a practise that was almost universally common at the time. However, the makers did offer various very expensive options all of a similar design and based on threaded, cast-iron feet into which fitted 1.25-inch diameter gas piping. The tops of the stands were made from clear pine lumber, sometimes covered with a 20-gauge thick sheet of steel that was galvanised and provided with a beaded and turned edge. The whole structure was bolted to both to the floor and often the ceiling as well (to a maximum recommended height of eleven feet) and braced by 1/2" guy rods, threaded left and right-hand for ease of adjustment. As an alternative, the stands could be provided as rather more rigid "free-standing" units with an additional system of pulleys mounted underneath and the overhead countershafts and electric motor carried on shorter acorn-topped posts braced by horizontal tie rods. Cataract provided not only complete stand and drive units but also all the small parts necessary for a customer to built their own. Later Cataract and Hardinge drive systems were simplified by redesigning the lathes to accept the drive from underneath. Unfortunately, while this resulted in a neater, safer and less-expensive assembly, it meant that the lathes could no longer be set up on the owner's own bench. The final solution to the problem of neatly integrating a small lathe and its drive system came in 1932 with the introduction of the American-made Atlas 9-inch model with Hardinge also up-to-date by fitting their precision plain turning lathes and screwcutting lathes to beautifully made underdrive stands..
|
|
|
|
|
|
|
|
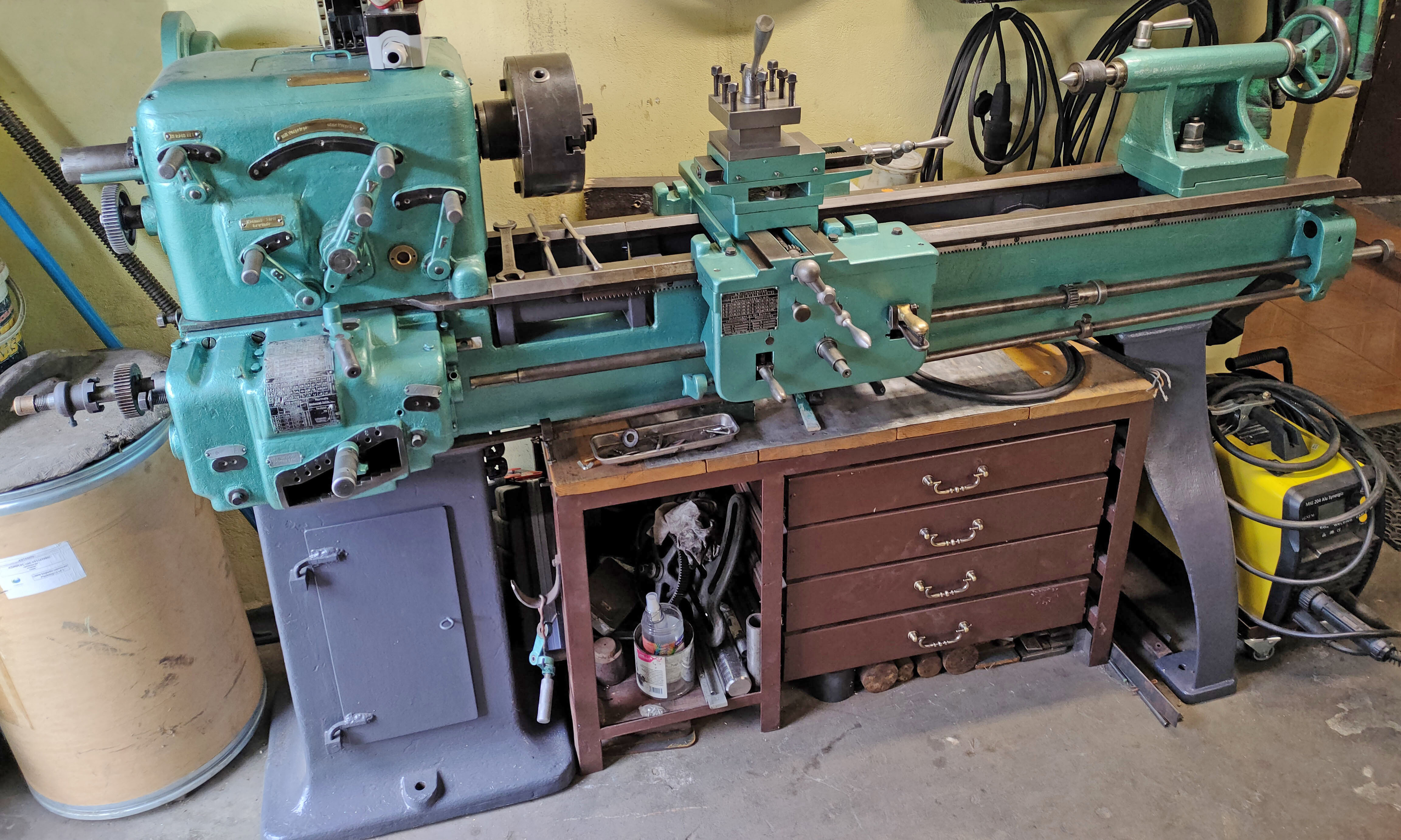 |
|
|
|
|
|
 |
|
|
|
|
|
|
IBM Workshops, Endicott, New York, in the early 1930s Ten Hardinge cataract underdrive bench lathes being used by uncomfortably well-dressed gentlemen who, though retaining their ties and waistcoats for the day's labours have, at least, taken off their jackets, rolled up their sleeves - and donned white aprons.
|
|
|
|
|
|
|
|
|
|
|
 |
|
|
|
|
|
|
Post 1907 Cataract bench lathe with the lighter, plain-bearing headstock and slim tailstock casting. This lathe was not displaced by the later versions, but continued to be offered alongside them. This lathe has the strengthened bed with an additional rectangular section underneath forming a face for the compound slide rest to bolt against. Note the trade-mark tool tray in front of the headstock, a fitting first believed to have been used after 1907 and a useful identification feature for this model. If the tray is missing (as in the colour photograph of a cataract on its maker's stand below) the two 14-24 tapped holes on 5 9/16" centers (or a raised boss) give the game away.
|
|
|
|
|
|
|
|
|
|
|
 |
|
|
|
|
|
|
The next version of the lathe featured a much more massive headstock with precision ball bearings - and a substantially improved tailstock.
|
|
|
|
|
|
|
|
|
|
|
|
|
|
|
|
|
 |
|
|
|
|
|
|
Development continued with a completely enclosed the headstock and the electrical speed-control levers mounted on a much larger foot beneath it. This new design gave vastly improved support to the spindle and its bearings. Available in five sizes, each model was based on the same 36" long bed that admitted around 17" between centres. Top speeds varied between 1500, 2000, 2500 and 3900 rpm. - depending upon the particular model and year of manufacture The various swings and collet capacities were as follows: BB37 swing 7", collet used: Hardinge 3C with 1/2" capacity through bore and draw tube BB47 swing 7", collet used: Hardinge 4C with 3/4" capacity through bore and draw tube BB49 swing 9", collet used: Hardinge 4C with 3/4" capacity through bore and draw tube BB57 swing 7", collet used: Hardinge 5C with 1" capacity through bore and draw tube BB59 swing 9", collet used: Hardinge 5C with 1" capacity through bore and draw tube Model Types also included a MD37, MD 47, (etc.) Series--again details depending upon the year of manufacture.
|
|
|
|
|
|
|
|
 |
|
|
|
|
|
|
|
|
|
Cataract headstocks contained ball-bearing races that were "pre loaded" - the idea can be better understood by referring to the illustration above: The left-hand picture shows the duplex double-row bearings before being correctly set, the clearance between the inner rings at point '"B" having been calculated by the bearing manufacturer to produce a pre-determined initial load suitable for bench lathe purposes. When the bearings had been pressed into the headstock casting they could be set to the correct pre-load by turning an adjustment ring nut (shown at A below) until the inner races met (as shown, right).
|
|
|
|
|
|
|
|
|
|
 |
|
|
|
|
|
|
Section through a late-model, completely enclosed, twin V belt driven Cataract headstock , showing the location of the pre-load setting screw A Early bearings were lubricated through wick-feeds from cups on the back of the headstock and sealed with cork rings with the ball separators made from Bakelite. A mechanical brake, actuated by an external lever marked "FORWARD - STOP - REVERSE, was located inside the headstock, with its band and friction lining arranged around the spindle. The Friction material was not riveted to the band, but free to move within it and so distribute wear as evenly as possible. Depending upon the drive unit selected, either six or eight speeds were available from 230 to a maximum of 1500, 2000, 2500 or 3900 rpm depending upon the particular model. Although the model illustrated used two V belts to drive the spindle, some versions were fitted with three. On this model backgear was not fitted.
|
|
|
|
|
|
|
|
|
|
|
|
|
|
|
|
|
 |
|
|
|
|
Late model Cataract lathes were available mounted on "Open" and "Enclosed" stands that, whilst well-thought out pieces of equipment (designed to insulate the lathe, as far as possible, from vibrations transmitted from the motor and its drive system) were rather over-complicated in their construction. A two-speed motor, fitted with a three-step V pulley, was supplied as standard, and drove via a three-step countershaft pulley to the triple V-belt headstock drive. The motor was rubber mounted onto a hinged plate - that itself was supported on a rubber cushion. The countershaft pulley shaft was fitted with self-aligning ball bearings and provision was made to allow individual adjustment of each belt run. How successful this design was must remain in question - although the triple V belts would have been perfectly matched for length when they left the factory, maintaining that degree of perfection would have been difficult in service conditions - and unmatched, multiple V belts are notorious for their vibration-inducing habits.
|
|
|
|
|
|
|
|
|
 |
|
|
|
|
|
Cataract Underdrive Cabinet Stand "Enclosed" Version with 6-speed drive. 40" long x 30" wide x 36" high. Made from clear, hard, northern maple this well-constructed cabinet stand, which weighed 450 pounds, featured an unusual hinged top, counterbalanced to stay in either the open or closed positions. Shellacked and waxed, the top, was 2.25" thick, made from laminated strip and braced by two 0.5" tie bolts; to add further stiffness the main cabinet rails were bolted to the legs with 4" x 0.5" machine bolts. Varnished in the natural colour of the wood and fitted with five drawers, the body of the cabinet was dovetailed at their front and with their backs grooved into the sides. One of the drawers was fitted out to accept a complete collet set. The internal drive unit was identical with that fitted to the "Open" version of the stand, with a reversing two-speed motor as standard. The cabinet was supplied fitted, wired - and ready to run
|
|
|
|
|
|
|
|
|
|
|
|
|
|
 |
|
|
|
|
|
An earlier pattern Cataract stand The 60" x 30" x 2.25" thick top, of clear hard maple, was reinforced by two steel tie rods and supported on 15/8" diameter steel legs made rigid by 1/2" diameter rods with their ends threaded left and right to make them adjustable for tension. The steel legs were also threaded into the supporting bosses - and could be screwed in and out to overcome irregularities in the floor level. The motor was a 220 volt, 60 cycle, 3-phase, two speed reversible unit driving a rather ornamentally-supported countershaft mounted fitted with self-aligning bearings - with provision for individual adjustment to each drive belt's tension. The floor pedals operated clutches which were able to engage, disengage - and probably reverse the drive.
|
|
|
|
|
|
|
|
|
|
|
|
|
|
 |
|
|
|
|
|
|
Early Cataract bench lathe with the much lighter, plain-bearing headstock and slender tailstock. This lathe was not displaced by the later versions, but continued to be offered alongside them.
|
|
|
|
|
|
|
|
|
|
|
|
|
|
|
|
|
 |
|
|
|
|
|
|
A rare survivor in this form - a Cataract on the maker's stand with built-on countershaft system
|
|
|
|
|
|
|
|
 |
|
|
|
|
|
 |
|
|
|
|
|
|
One popular option was a tool tray (in this case a simple horizontal type) clamped around the overhead drive support post
|
|
|
|
|
|
|
|
|
|
|
|
|
|
 |
|
|
|
|
|
|
Cataract precision bench lathe with the chase screwcutting attachment fitted
|
|
|
|
|
|
|
|
 |
|
|
|
|
|
|
Late version of the plain-bearing headstock
|
|
|
|
|
|
|
|
|
|
|
 |
|
|
|
|
|
|
Patented headstock from the No. 3 lathe with a 0.625" spindle bore and (right) the novel spindle nose. Key to the designs success was to arrange the thrust ball bearings separately to the (rather ingenious) cast-iron sleeve bearings - these being tapered to allow for a very fine adjustment with the hardened and ground spindle.
|
|
|
|
|
|
|
|
|
|
|
 |
|
|
|
|
|
|
Headstock of the No. 4 lathe with a 0.75" spindle bore
|
|
|
|
|
|
|
|
|
|
|
|
|
|
|
|
|
 |
|
|
|
|
|
|
Headstock of the No. 5 lathe with a 1.21875" spindle bore
|
|
|
|
|
|
|
|
|
|
|
 |
|
|
|
|
|
|
The patented Hardinge Taper-nose spindle fitting
|
|
|
|
|
|
|
|
|
|
|
 |
|
|
|
|
|
|
|
|
The Hardinge spindle nose carrying a backplate-mounted chuck.
|
|
|
|
|
|
|
|
|
|
|
|
|
 |
|
|
|
|
|
Pre-1920 compound slide
As important a part of a precision the lathe as the headstock, the compound slide rest had to offer the turner a component that was delicate to operate - yet strong enough to resist all the forces it was likely to encounter. However, a persistent criticism of the Cataract unit was the single T slot in the top slide; many European makers of precision bench lathes including two slots as standard, an arrangement that allowed the operator much great freedom to place tooling when dealing with awkwardly-shaped jobs. The Cataract/Hardinge unit changed little over the years, the five examples below reflecting its development from 1900 to 1944. Made in different versions to suit the 7" and 9" swing lathes, the 7" version had 4.5" of movement on the cross slide and 3.5" on the top - whilst that for the larger lathe had 5.25" and 4.5" respectively. An adjustable stop was fitted to the cross-slide movement, the micrometer dials could be zeroed and the unit was well designed with a 4-bolt end plate to the cross slide and hardened thrust washers to each side of the feed screw thrust. The whole unit was made of the finest quality materials and beautifully finished - but the top slide was limited to 45 degrees of swivel each side of the zero line.
|
|
|
|
|
|
|
|
|
|
|
|
|
|
|
|
|
|
|
|
 |
|
|
|
|
|
|
The next version of the compound slide, current in the 1920 and early 1930s, had slightly 17/16" diameter larger micrometer dials and a rounded front edge to the top slide with recessed gib-strip adjustment screws - but seems to have lost the hand-scraped finish of the original.
|
|
|
|
|
|
|
|
|
|
|
 |
|
|
|
|
|
|
By the late 1930s the slide had a block-type top slide casting and micrometer dials with parallel faces.
|
|
|
|
|
|
|
|
|
|
|
 |
|
|
|
|
Although the 1940s version of the compound slide may have looked a more prosaic item in comparison with its glittering predecessors, it was considerably improved in several areas: the method of clamping the slide to the bed was changed to give a much broader support (it had originally been held by a single, central T slot; the change is illustrated below); the micrometer dials were at last of a reasonable size for a precision lathe - a full two inches - with the cross slide plate triangulated to support the dial housing; feed screws were hardened, ran in long bronze nuts and were supported in ball races where they passed through their end plates; the top slide could now be swivelled through a complete circle with the degrees graduations engraved into the flat surface of the cross slide; this also allowed the top slide to bear against a much wider ways instead of being less well supported at the extremes of its travel. One useful identification point for older slide rests is that all pre-1946 Hardinge/Cataract top slides had a lengthened feed screw to pick up the drive from the changewheel-driven screwcutting attachment. Post that 1946, and with the introduction of the new dovetail bed lathes (for example the DV-59) a new compound slide assembly was introduced - though with an eye to increased sales Hardinge also made the assembly with a base to fit the older, "split-bed" models.
|
|
|
|
|
|
|
|
|
|
|
 |
|
|
|
|
|
|
Rear view of the 1940s style compound slide rest
|
|
|
|
|
|
|
|
|
|
|
|
|
|
|
|
|
 |
|
|
|
|
|
On the left is the method adopted in the 1940s to more securely hold the slide to the bed. The original method, using a single central T slot, is shown on the right.
|
|
|
|
|
|
|
|
|
|
|
|
|
|
 |
|
|
|
|
|
Tight and Loose Headstock A very unusual headstock fitted with a Tight and Loose (in the UK "Fast and Loose") pulley system - designed to aid the rapid manufacture of parts where a method of quickly starting and stopping the headstock was required. An electric motor with a wide pulley was positioned behind the lathe, and the headstock driven directly from it; a belt-shifter fork, connected to a foot pedal, aided instant selection of the drive and left the turner's hands free to position lathe tools and operate the collet closer.
|
|
|
|
|
|
|
|
|
|
|
|
|
|
 |
|
|
|
|
|
Cataract "Enclosed Head Precision Hand Screw Machine" shown here with a lever-action collet closer, lever cross slide with twin tool posts and a six-station, self-indexing turret head. Although many varieties of faster, automatic lathes were in contemporary use during the period 1900 to 1940 simple but high-precision machines like the Cataract still found a place in workshops where there was need for "second-operation" machining, short production runs of identical parts - or where an easily-handled lathe was need to carry special tooling made up by the resident "wizard" to get round some particularly thorny production problem. This type of smaller capstan lathe has, incidentally, been the backbone of many a successful home business, run in the evening and at weekends, turning out (in the author's experience) a bewildering variety of parts for consumption by local businesses and educational institutes. A good selling point was that the lever-action, double-tool cross slide and the turret head could both accepted the same tooling as used on the very popular and widely-used Brown & Sharpe Automatic Screw Machines.
|
|
|
|
|
|
|
|
|
|
|
|
|
 |
|
|
|
|
|
6 station self-indexing turret head with adjustable stops. This unit could be rested in the middle of a stroke, and the head turned by hand past any turret stations not fitted with tooling.
|
|
|
|
|
|
|
|
|
|
|
|
|
|
|
|
|
|
|
|
 |
|
|
|
|
|
|
|
|
|
Double Tool, lever-action Cross Slide for forming, rounding, knurling, cutting-off, etc.
|
|
|
|
|
|
|
|
|
|
 |
|
|
|
|
|
Automatic Collar Closer with adjustable closing tension A common fitting on lathes equipped for repetition and production work - and ideal for feeding bar stock through the headstock
|
|
|
|
|
|
|
|
|
|
|
|
|
|
 |
|
|
|
|
|
Double-Tool Cross Slide with Right-angle Slide With rack-and-pinion feed to both longitudinal travel (1.25") and cross travel (1.5") this unit was provided with twin housings on each axis to allow the operating levers to be mounted at either the back or front.
|
|
|
|
|
|
|
|
|
|
|
 |
|
|
|
|
|
Double Tool Cross Slide with Swivel Attachment This unit, designed to be mounted at the rear of the twin-toolpost cross slide and with a 2.5" slide travel, could be employed for straight or taper turning.
|
|
|
|
|
|
|
|
|
|
|
 |
|
|
|
|
|
|
Cataract changewheel screwcutting attachment. The unit shown above and below has been beautifully preserved and rebuilt by Larry Vanice in the USA
|
|
|
|
|
|
|
|
|
|
|
|
|
|
 |
|
|
|
|
|
|
|
|
|
|
|
 |
|
|
|
|
|
 |
|
|
|
|
|
|
|
|
|
End face f the cataract lathe bed showing the fittings provided to mount the screwcutting attachment
|
|
|
|
|
|
|
|
|
|
|
|
|
|
|
|
|
|