 |
 |
 |
 |
 |
 |
 |
 |
 |
 |
 |
 |
 |
 |
 |
 |
 |
 |
 |
 |
 |
 |
 |
 |
 |
 |
 |
 |
 |
 |
 |
 |
 |
 |
 |
 |
 |
 |
 |
 |
 |
 |
 |
 |
 |
 |
 |
 |
 |
 |
 |
 |
 |
 |
 |
 |
 |
 |
|
|
|
|
|
|
|
|
|
|
|
|
|
|
|
|
|
|
|
|
|
|
|
|
|
|
|
|
|
|
|
|
|
|
|
|
|
|
|
|
|
|
|
|
|
|
|
|
|
|
|
|
|
|
|
|
|
|
|
|
|
|
|
|
|
|
|
E-MAIL Tony@lathes.co.uk Home Machine Tool Archive Machine-tools for Sale & Wanted Machine Tool Manuals Machine Tool Catalogues Belts Books Accessories
Carstens (& Swisten-branded) Lathes
Early Carstens Screwcutting Lathe Carstens Types DLZK, DLK & DZK
Carstens Miller & Grinder Carstens Model DLRN Accessories
DLZR Photographs If you have a Carstens or Swisten-branded miller, the writer would be pleased to hear from you.
A former precision mechanic, Arthur Carstens founded his Company Arthur Carstens & Co., Werkzeugmaschinenfabrik, Hamburg in 1913. After the First World War (1914-18) sales grew to include many overseas markets and, in 1924, Mr. Carstens was granted a patent for his epicyclic backgear, a speed-reducing system arranged by a planetary gearing built into the largest diameter of the spindle's flat-belt pulley. Although the factory concentrated on lathes, in 1928 a vertical milling machine was introduced and in 1938 a small cylindrical grinder. During WW2, on the night of 22/23 July, 1943, the original factory at Liebigstraße 33, Hamburg (and Mr. Carstens' home) were both destroyed by bombing. Accordingly Arthur Carstens and his wife Frl. Dietze moved to Salem, near Ratzeburg (on the outskirts of Hamburg) where initially, just a small workshop was established with 10 employees and 2 or 3 apprentices. After the war the factory expanded and the full range of lathes, millers and grinders resumed production. In 1951 Carstens build their first small lathe with electronic speed control. The Carstens organisation was self-contained and the factory made all the small (usually sub-contracted) parts and even had their own nitriding and hardening plant. Arthur Carstens died in 1957 and his factory was sold to ABA grinding machines of Aschaffenburg. After the bankruptcy of ABA in April, 2010, the new owners became the Hangzhou Machine Tool Group Co. Ltd. of China. Unfortunately little is known of the "Swisten" branding used on Carstens lathes in the UK, only that the earliest-known screwcutting example, estimated to have been from the early 1920s, also had the name "Carstens" cast into the front of its headstock and changewheel cover. Sales of the Swisten-branded machines continued in the UK until the 1950s, though as usual with such marketing exercises, most of the sales literature has an address and it was not until late in the day that the Mortimer Engineering Company of Harlesden, London, acting as agents, openly advertised the machine tools under their maker's name. Although very early catalogues show lathes with "British Made" on some castings (to comply with the law these removable part were UK-made) later ones were advertised as "Foreign". The importers were certainly capable of pulling off some naughty tricks: on some machines examined, the original engraved metric micrometer dials were covered with (crudely) hand-stamped inch versions. Presumably the sellers reckoned on most turners not being able to distinguish between 0.001 mm and 0.001". During the 1930s, at a time when lathes of this class were beginning to be fitted to stands with built-in drive systems, the UK importers offered an underdrive unit of a type shown on the right in the picture immediately below, taken in the late 1950s - obviously a case of the factory making economical use of an obsolete component. Several types have been identified including an early backgeared and screwcutting lathe (the forerunner of the very well made and heavy 5-inch DLZK, DLK and DZK models) and a "Precision Bench Lathe" of a type first made popular in the USA (from 1862) onwards by Stark and developed and refined by various companies including Levin, Bottum, American Watch Tool Company, B.C.Ames, Bottum, Hjorth, Potter, Pratt & Whitney, Rivett, Wade, Waltham Machine Works, Wade, Pratt & Whitney, Rivett, Cataract, Hardinge, Elgin, Remington, Sloan & Chace, W.H.Nichols, Crystal Lake and (though now very rare) Bausch & Lomb, Frederick Pearce, Van Norman, Ballou & Whitcombe, Sawyer Watch Tool Co., Engineering Appliances, Fenn-Sadler, "Cosa Corporation of New York" and UND. From 1928 the Swisten branding was also applied to a small precision milling machines - and the writer would be interested to hear from any reader with a machine tool of this type. Continued below:
|
|
|
|
|
|
|
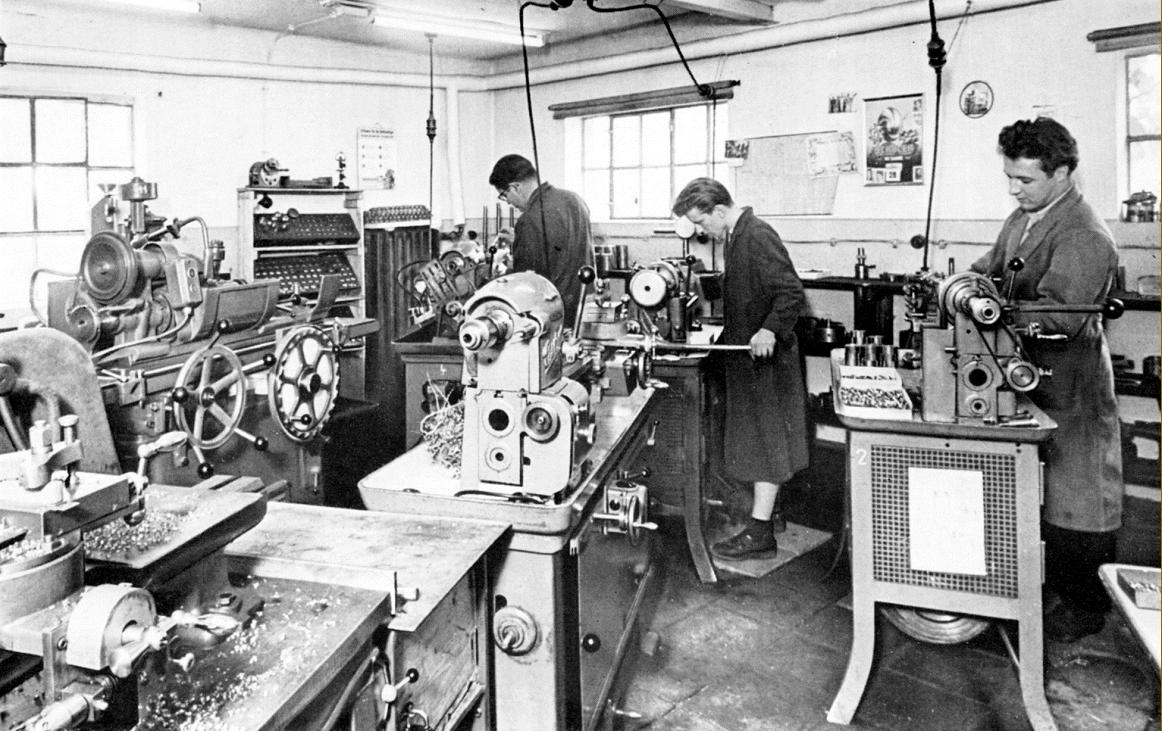 |
|
|
|
|
A picture taken inside the Carstens factory at Salem circa 1958. Small-scale production appear to be underway with versions of the D-Series lathes pressed into use with lever-operated slides. Note, on the left, the late-model Carstens cylindrical grinder.
|
|
|
|
|
|
|
|
|
|
|
|
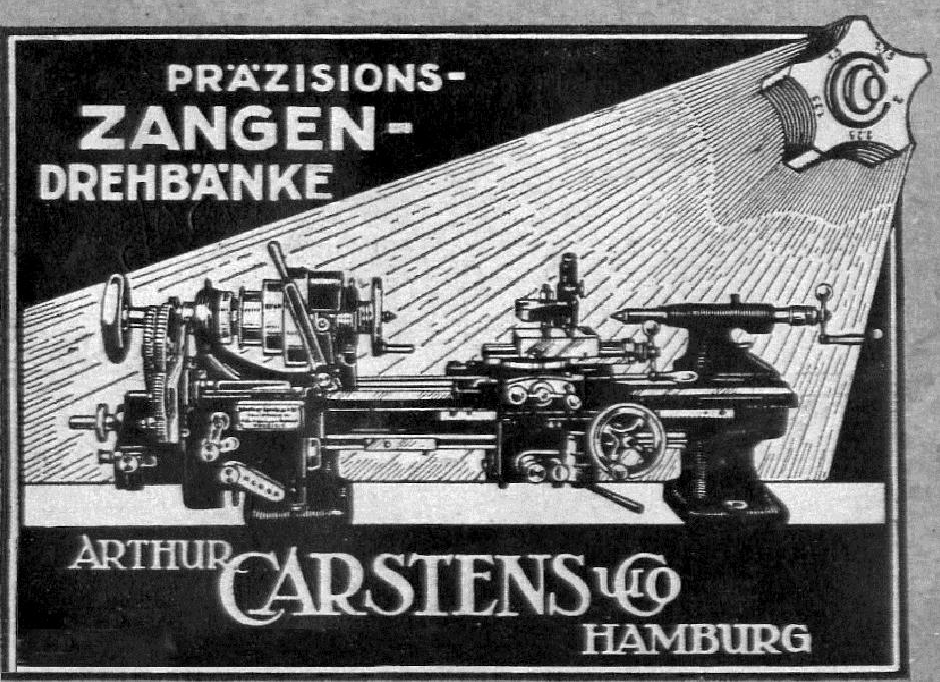 |
|
|
|
|
|
The superb Carstens DLRN lathe with a screwcutting gearbox, power sliding and surfacing feeds, epicyclic backgearing built into the headstock spindle and a leadscrew running down the centre leibe of the bed
Continued: Of conventional design for its type, the "Carstens-Swisten" 5.125" centre height precision plain-turning bench lathe had. apart from a taper screwcutting facility, no significant features that could be described as novel. Its construction also followed well-established principles for its class and was built from the "highest grade tested material, absolute interchangeability, guaranteed accuracy to limits by Professor Dr. Schlesinger for highest grade precision lathe." Flat topped, the bevelled-edged 29-inch long bed was, if not properly hardened, made in a chilled cast iron for which the makers claimed an unusual toughness; the ways were ground, as one would have expected in a machine of this quality, to "limit gauges" and the back of the bed was provided with a full-length T slot into which could be mounted a detachable screwcutting attachment of the classic and very accurate "chase" type. Of "the finest steel", case hardened and ground (on the bearing surfaces only) the headstock spindle ran in large phosphor-bronze alloy bearings that were adjustable against a hardened steel thrust ring and locking collars--the whole assembly being designed to require the minimum of attention over many years of high-speed use. In later years the maker also offered, at no additional cost, the option of taper-roller headstock bearings. The spindle could accept draw-in collets or, being threaded at the end, ordinary screw-on chucks and faceplates. Whilst many precision bench lathes had "reversed" headstock pulleys (with the smallest diameter against the all-important right-hand bearing so that more metal could surround it) on the Swisten the pulley was arranged in the ordinary way with the smallest diameter to the left. With a long-travel top slide that could be rotated through 45 degrees in either direction, the compound slide rest had both micrometer dials of the zeroing kind and graduated in 1/1000" intervals. However, removing these dials has revealed underneath (on several machines) standard metric ones calibrated in 0.01 mm intervals - the makers had cheated, and retained the standard metric-pitch screws The feed-screws were claimed to be "large" (but of unspecified diameter and pitch) and of what the maker called "trapexoidal" (sic) and probably Acme form. The screw and their nuts were (unlike those on many other precision lathes) completely covered against the effects of swarf and the inevitable grit from the grinding operations that lathes of this type - their owners determined to make the most of their expensive accuracy - were often called upon to perform. The rear of the cross slide was machined to accept a parting-off toolholder. A bed-mounted hand rest was also provided and equipped with both long and short T-rests. As part of the specification the makers also boasted of their "pressure-gun" lubrication points - where the injected oil would not only have been more likely to reach its intended destination but also to have forced out any foreign bodies trapped between the surfaces. A chase-type screwcutting attachment, described and illustrated at the bottom of the page, was amongst the lathe's accessories - unfortunately the manufacturer's publicity department neglected to include a list of these in the machine's sales literature. Standard equipment was sufficient to press the lathe into immediate service: a draw-in collet tube together with collet-mounted male and female headstock centres and a spindle-thread protection nut; a catchplate of the dangerous type where the drive-pin slot was open to the outside; a compound slide rest and a separate bed-mounted hand-rest with two lengths of T; a pressure oil gun, tool tray, test chart, male and female tailstock centres, the necessary spanners and a single-speed countershaft with ring-oiled bearings. As might have been expected on a lathe of this class, the tailstock was fitted with a No. 1 "short" Morse taper "through barrel" that was always, no matter how far extended in either direction, fully supported within the casting; both an engraved barrel and a micrometer collar were fitted to indicate travel..
|
|
|
|
|
|
|
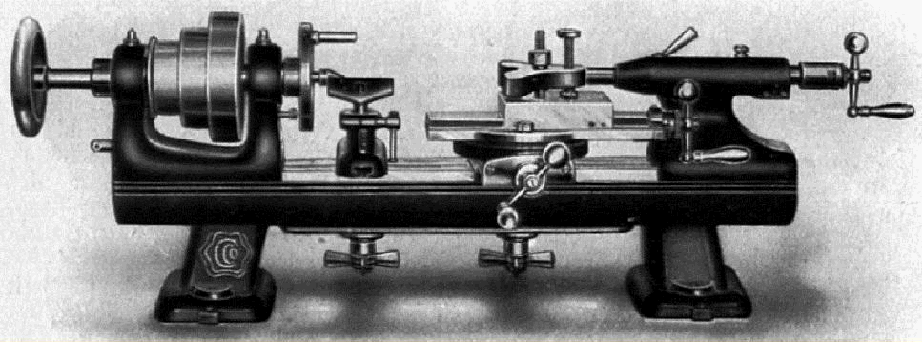 |
|
|
|
|
|
|
|
|
|
Carstens Model D as manufactured in the 1920s
|
|
|
|
|
|
|
|
|
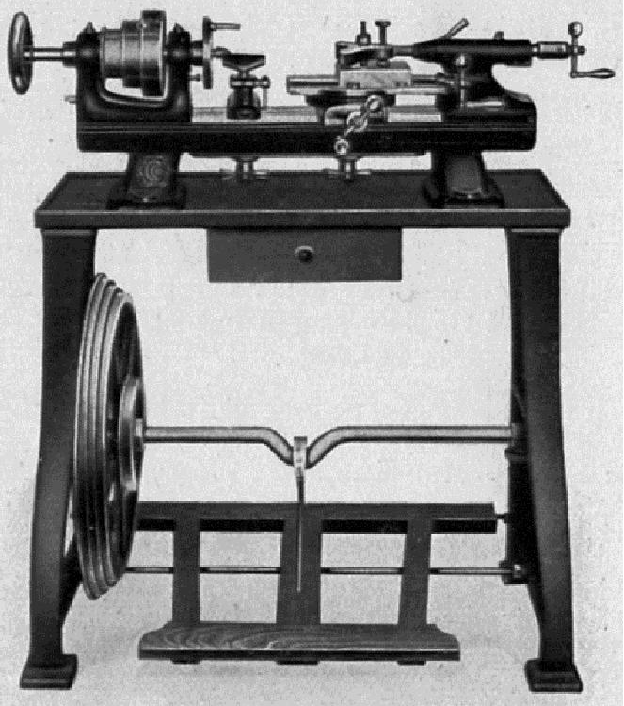 |
|
|
|
|
|
|
|
|
|
1920's Model D on treadle stand - sold as the Type DF
|
|
|
|
|
|
|
|
|
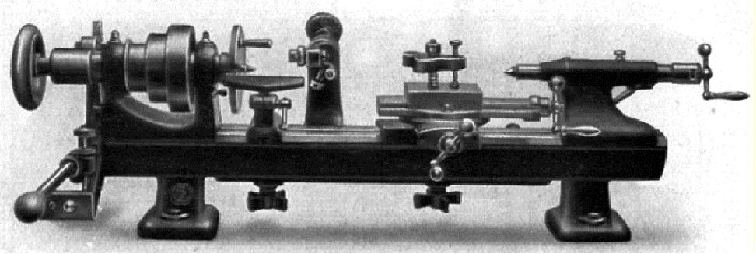 |
|
|
|
|
|
|
|
|
|
1920's Model DG with chase screwcutting
|
|
|
|
|
|
|
|
|
|
|
|
|
Like many competing lathes, the Carstens could be fitted with traditional "chase screwcutting" (as shown above in the form of the Model DG) - and in this case of relatively simple construction where a T slot, which ran down the back of the bed, held supports that carried a horizontal sliding shaft to which was attached, on the top of vertical arm, a screw-adjustable toolholder capable of mounting special single-point thread-chasing tools. Above the shaft at the headstock end of the lathe, and held between the arms of a clevis pin, was a "Follower" that engaged under spring pressure with a threaded steel hob (or "Master Thread") fitted over the end of the headstock spindle. The Swisten "Follower" was unusual in being a phosphor bronze "star" that carried 5 different pitches of thread, so reducing the number of followers needed and the frequency with which they had to be changed. Besides being able to cut parallel threads the unit was also cleverly arranged so that short tapered threads could be generated. The arrangement for this appears to have been: the slotted arms of the clevis, the spring loading of the follower and the fitting of an adjustable two-part "guide plate" (to the left-hand end of the bed) against which a hardened screwed rod bore. With the spring pushing the follower against the spindle-mounted hob, lowering the engagement handle started the screwcutting process and the sliding shaft was driven along the bed; as it moved so the hardened pin was made to bear against the guide plate - though how the guide plate was set to the required angle is not clear - and the arm was moved backwards causing the cutting tool to move away from the workpiece. The angle of the taper was, of course, limited to the degree that the guide plate could be set over from parallel. Whilst this system produced absolutely accurate threads, and was especially suited to delicate operations such as the thin-wall tubes used to construct such items as microscopes and telescopes, the length of thread that could be cut, and the number of threads per inch or mm that could be generated, depended upon the availability of an appropriate Master. Other disadvantages of the system as fitted to the Swisten were the lack of any changewheels to increase the number of threads that could be generated and the lack of a backgear for the essential slow-speed running required for screwcutting on a lathe of this type.. Similar chase-screwcutting arrangements can be seen on many of the pages devoted to the American makers Goodell-Pratt, Wade, Ames, Waltham, Pratt & Whitney, Potter, Rivett, Cataract, Elgin and Hardinge.
|
|
|
|
|
|
|
|
|
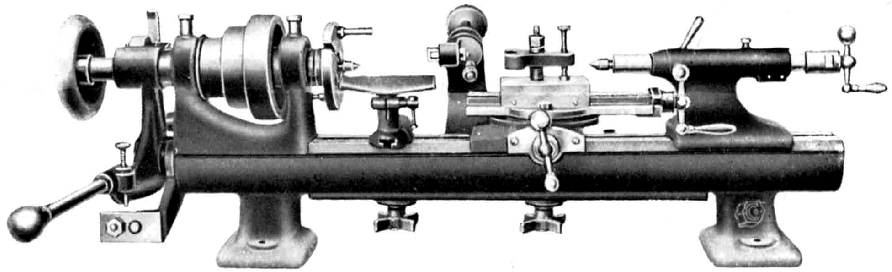 |
|
|
|
|
|
|
|
|
|
The DG chase screwcutting model
|
|
|
|
|
|
|
|
|
 |
|
|
|
|
|
|
The Chase Screwcutting Attachment mounted on the back of the lathe bed. A flat spring steel blade was screwed to the back of the lever clamp to press the "Follower" (held in a sliding holder) against the "Master Thread"
|
|
|
|
|
|
|
|
|
|
|
|
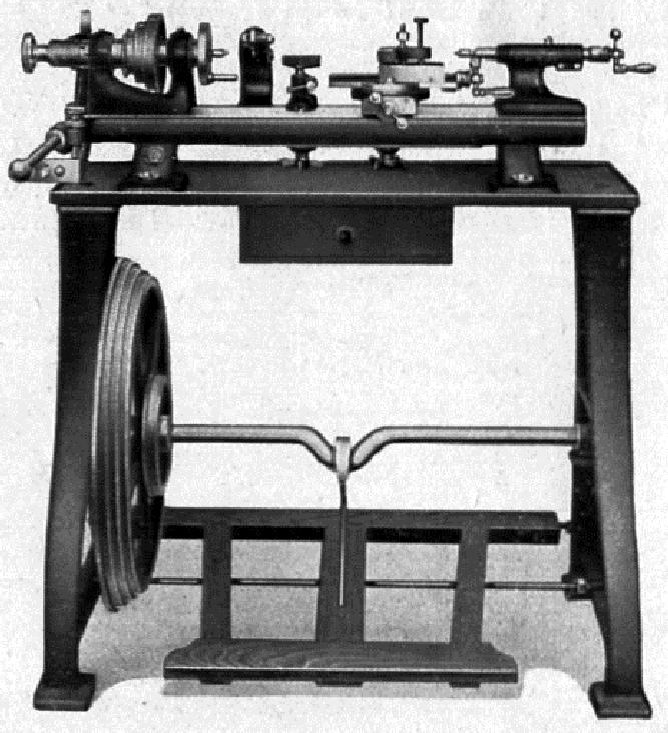 |
|
|
|
|
|
|
|
|
|
When mounted on a foot-operated, cast-iron treadle stand the chase screwcutting version was advertised, during the 1920s, as the Model DGF
|
|
|
|
|
|
|
|
|
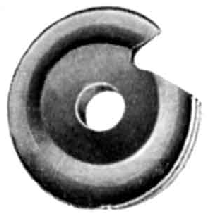 |
|
|
|
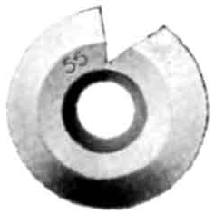 |
|
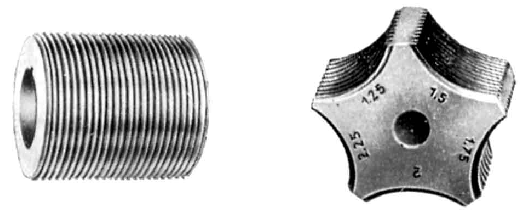 |
|
|
|
|
|
|
|
|
|
|
|
|
|
|
|
|
|
|
|
|
|
|
"Belt-point" thread chaser
|
|
|
|
|
|
|
|
|
|
Single-point thread chaser
|
|
|
|
|
|
|
|
|
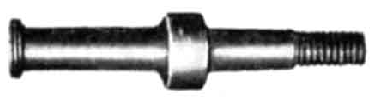 |
|
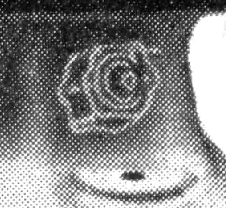 |
|
|
|
|
|
|
|
|
|
|
On the left the spindle-mounted steel hob - available in a variety of thread pitches. On the right the rotating bronze "Star Follower" with five different pitches in one compact unit.
|
|
|
|
|
|
|
|
|
|
|
|
|
|
|
|
|
The logo from the bed foot of a "Swisten" lathe was, of course, from a Carstens and represented the rotating master thread as used on the chase screwcutting attachment as shown below in the advertisement from the 1920s
|
|
|
|
|
|
|
|
|
|
|
|
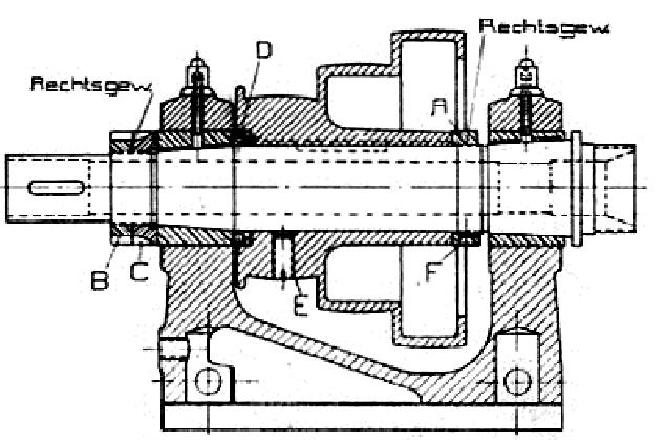 |
|
|
|
|
|
|
|
|
Standard, non-backgear headstock from the precision bench lathe
|
|
|
|
|
|
|
|
|
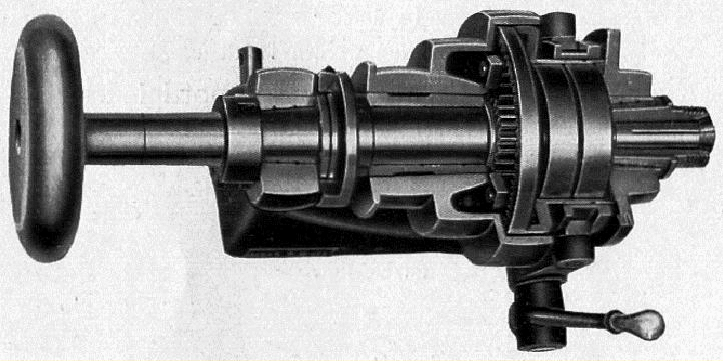 |
|
|
|
|
|
|
|
|
|
An early version of what was to become the well-known Carstens epicyclic reduction-geared headstock
|
|
|
|
|
|
|
|
|
|
|
|
|
|
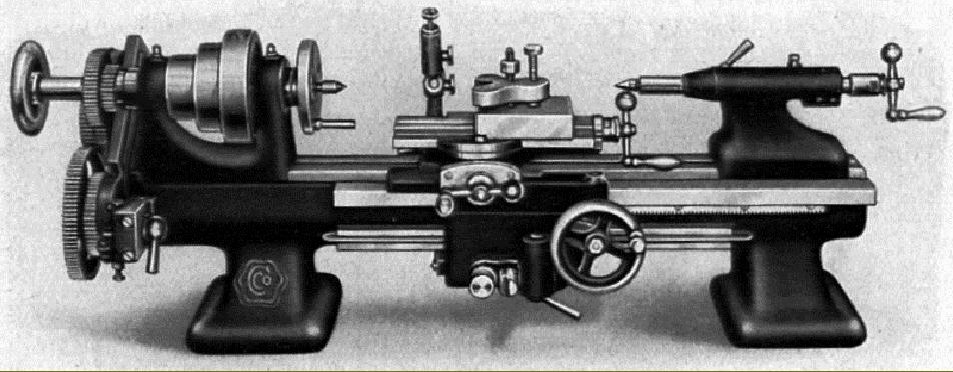 |
|
|
|
|
|
|
|
|
|
1920's Model DL with screwcutting with a central leadscrew running beneath the bed
|
|
|
|
|
|
|
|
|
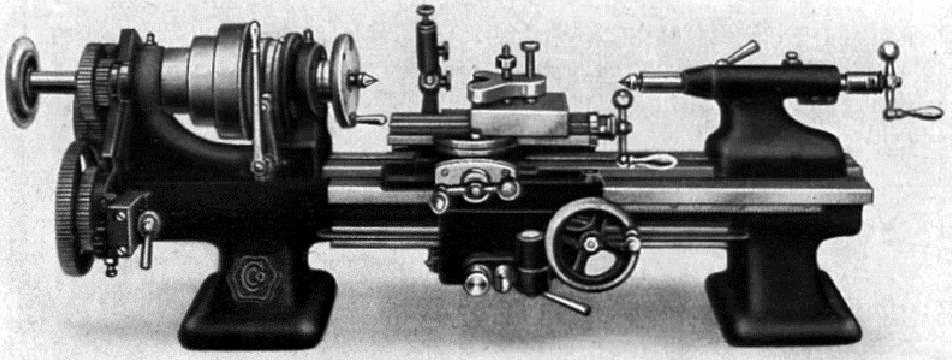 |
|
|
|
|
|
|
|
|
|
Top-of-the-range Model DLRN - full screwcutting gearbox and epicyclic headstock reduction gearing
|
|
|
|
|
|
|
|
|
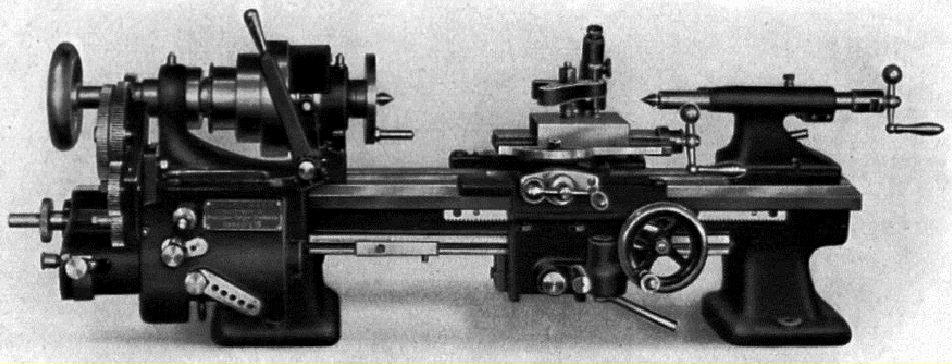 |
|
|
|
|
|
|
|
|
|
Plan view of the DLRN - this example being fitted with taper turning
|
|
|
|
|
|
|
|
|
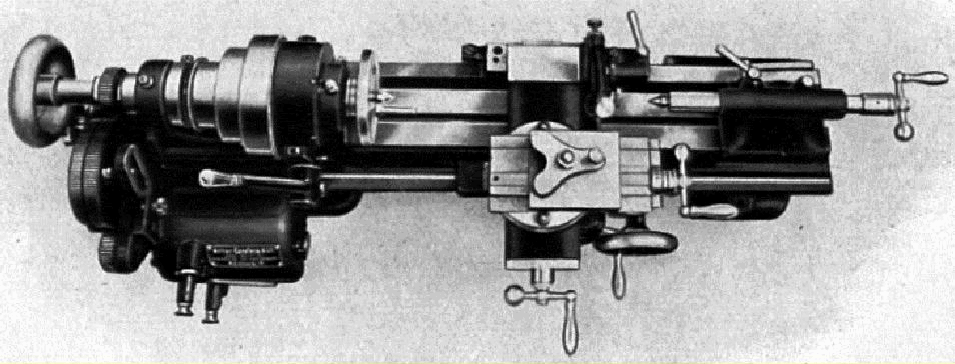 |
|
|
|
|
|
|
|
|
|
Plan view of the DLRN - this example being fitted with taper turning
|
|
|
|
|
|
|
|
|
|
|
|
|
|
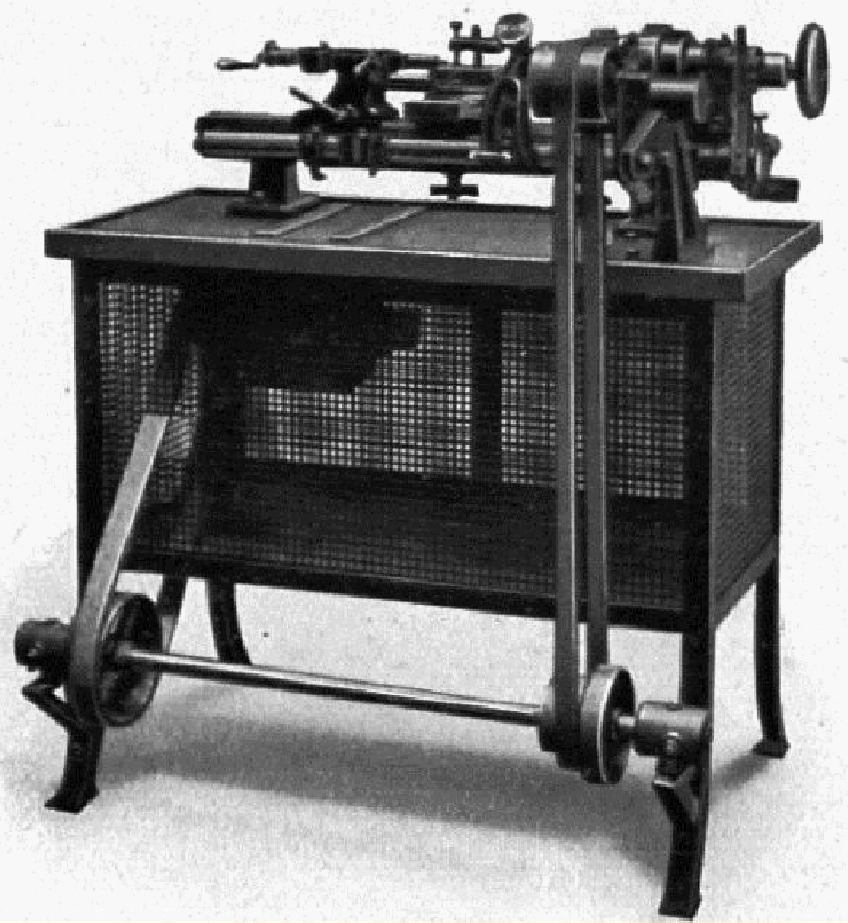 |
|
|
|
|
|
|
|
|
|
Although early lathes (see below) were offered for bench mounting - various stands were also listed that, besides the usual type of the era with cast-iron legs and wooden tool trays, also included some unusual examples made from angle iron with the faces sheeted in wire mesh. Early examples of the latter (as above) had the countershaft mounted externally, low at the back but (probably by the mid 1920s) this had been reposition rather more neatly to the inside. On the iron stands the top of the legs, where the contacted the lathe's feet, were hand scraped dead flat. Later models were supplied on either a particularly heavy cast-iron cabinet, formed in one piece for maximum rigidity and strength and intended for use on the shop floor, or on a lighter yet still strong stand rather like the earlier pattern (but improved in detail) and ideal for use in a toolroom.
|
|
|
|
|
|
|
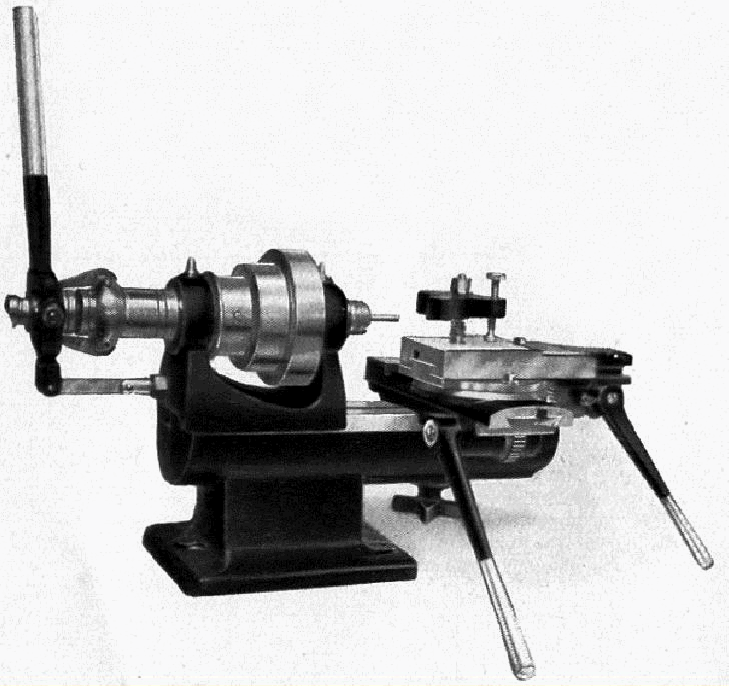 |
|
|
|
|
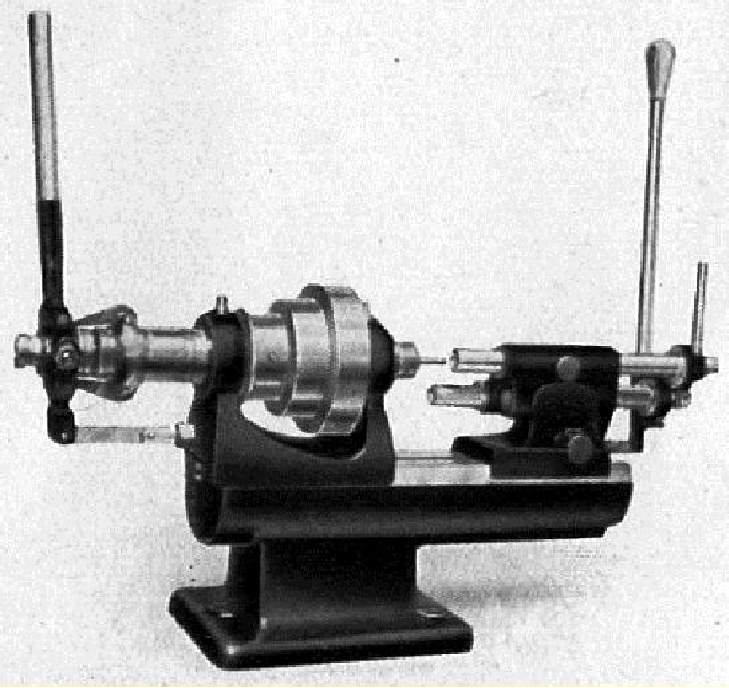 |
|
|
|
|
|
|
|
|
|
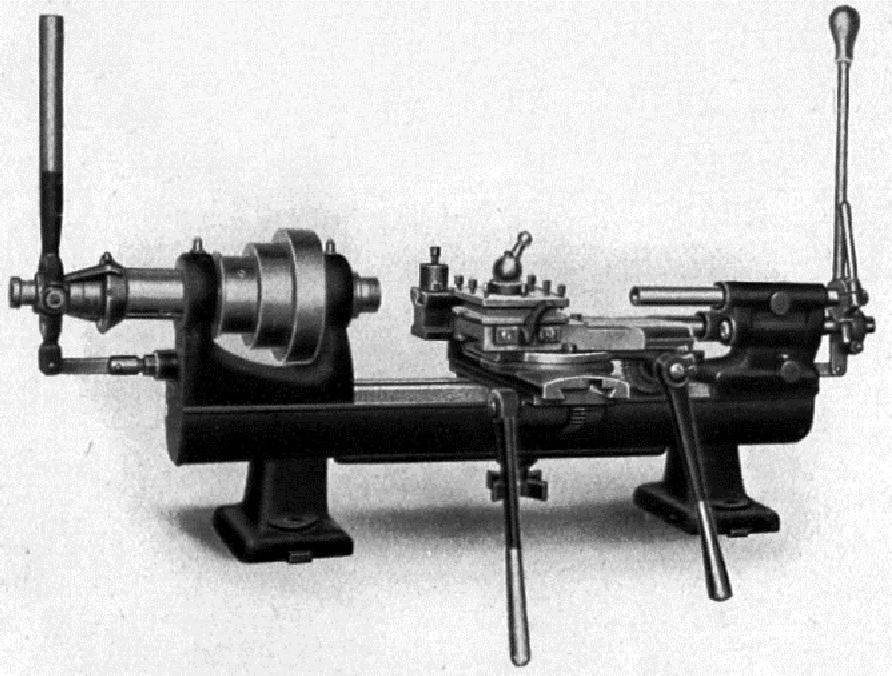 |
|
|
|
|
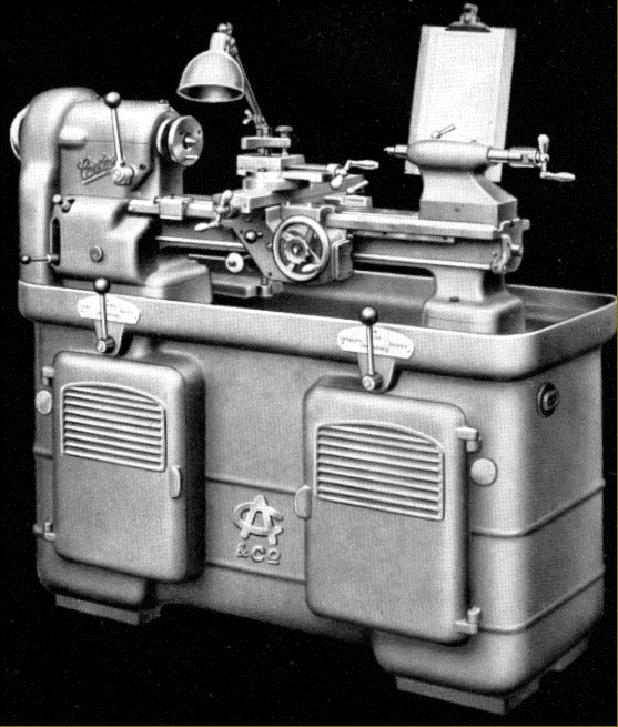 |
|
|
|
|
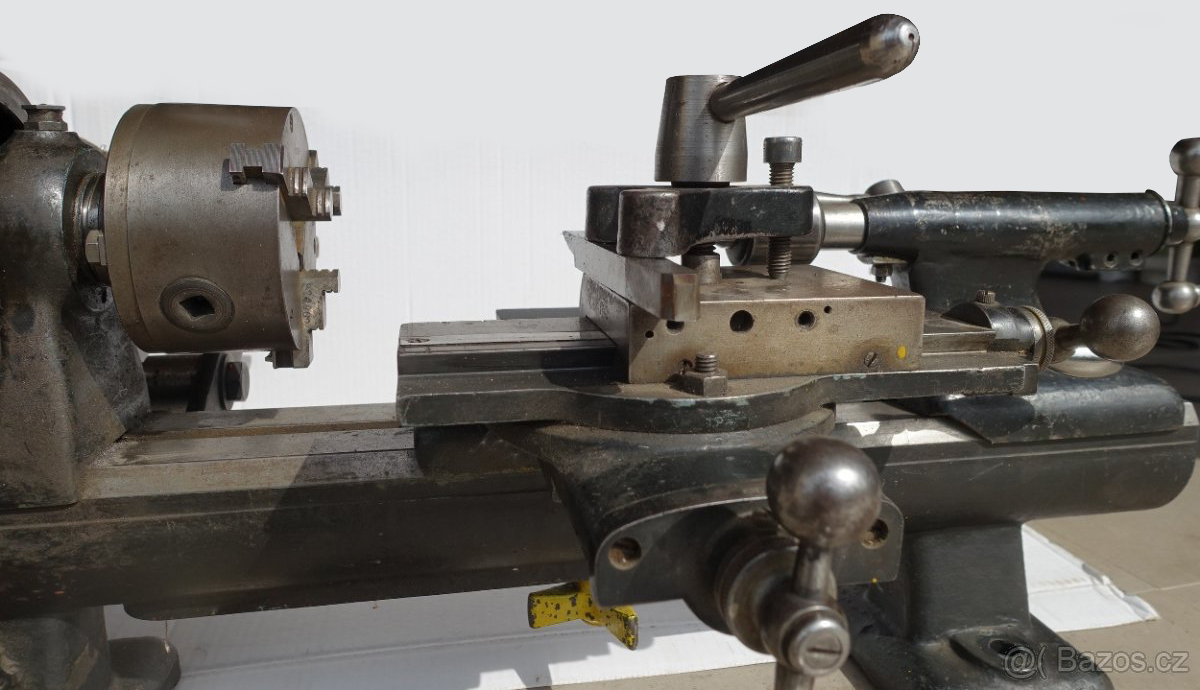 |
|
|
|
|
|