 |
 |
 |
 |
 |
 |
 |
 |
 |
 |
 |
 |
 |
 |
 |
 |
 |
 |
 |
 |
 |
 |
 |
 |
 |
 |
 |
 |
 |
 |
 |
 |
 |
 |
 |
 |
 |
 |
 |
 |
 |
 |
 |
 |
 |
 |
 |
 |
 |
 |
 |
 |
 |
 |
 |
 |
 |
 |
 |
 |
 |
 |
 |
 |
 |
 |
 |
 |
 |
|
|
|
|
|
|
|
|
|
|
|
|
|
|
|
|
|
|
|
|
|
|
|
|
|
|
|
|
|
|
|
|
|
|
|
|
|
|
|
|
|
|
|
|
|
|
|
|
|
|
|
|
|
|
|
|
|
|
|
|
|
|
|
|
|
|
|
|
|
|
|
|
|
|
|
|
|
|
|
|
|
|
|
As its name implies, "backgear" is a gear mounted at the back of the headstock (although in practice it is often located in other positions) that allows the chuck to rotate slowly with greatly-increased turning power (torque). For a novice the ability to run a workpiece slowly might seem unnecessary, but a large-diameter casting, fastened to the faceplate and run at 200 r.p.m. (around the bottom speed commonly found on a lathe without backgear) would have a linear speed at its outer edge beyond the turning capacity of a small lathe. By engaging backgear, and so reducing r.p.m. but increasing torque, even the largest faceplate-mounted jobs can be turned successfully. Screwcutting also requires slow speeds, typically between 25 and 50 r.p.m. - especially if the operator is a beginner, or the job tricky. A bottom speed in excess of those figures (as found on most Far Eastern and some European "Continental" machines) means that screwcutting - especially internally, into blind holes - is, in effect, impossible. These lathes are advertised as "screwcutting" but what that really means is just power sliding - a power feed along the bed. With these machines, even if you go to the trouble of making up a complex pulley system to reduce the spindle speed (like the early Atlas 9-inch), you will find the torque required when turning large diameters at slow speeds causes the belts to slip. The only solution is a gear-driven low speed - and so a properly-engineered small lathe, with a backgear fitted, not only becomes capable of cutting threads but can also tackle heavy-duty drilling, big-hole boring and large-diameter turning and facing; in other words, it becomes possible to use it to the very limits of its capacity and strength. To show how important backgear has always been considered, examine the specification of the many small English-made metal turning lathes made from the mid 19th century onwards: nearly every one was so equipped - or could be retro fitted for a modest charge. For more on lathe parts and functions click here and for a further explanation of the desirable features required in a small lathe, click here.
|
|
|
|
|
|
|
|
|
Small gear (SG) and 4-step V-pulley (V) are connected together permanently.
|
|
|
|
|
|
|
|
Oil hole - there will be another in the pulley assembly
|
|
|
|
|
|
|
|
 |
|
|
|
|
|
Backgears (BG) mounted on an eccentric shaft.
|
|
|
|
|
|
|
|
|
|
|
Handle to rotate the eccentric mounting shaft and so engage the backgears
|
|
|
|
|
|
|
|
|
|
|
Pin (P) to connect and disconnect Bull Wheel and V-pulley. Instead of a pin, some lathes use a stud and nut arrangement - or even a quick-release fitting.
|
|
|
|
|
|
|
|
|
|
|
Bull Wheel (BW) - in this case with a ring of useful indexing holes, the locating plunger passing through the front face of the headstock casting
|
|
|
|
|
|
|
|
|
|
|
|
The backgear is a clever but essentially simple mechanism probably conceived around 1817 by Richard Roberts, an English engineer and prolific inventor. If you have to read the following several time to understand how it works, don't worry, everybody does…. In the picture above (a 1934 Atlas lathe) the 4-step V-pulley (V) has a small gear (SG) permanently attached to its smaller end. The entire length of V-pulley and gear are bushed - and able to rotate freely on the headstock spindle. The large "Bull Wheel" (BW) is keyed or held to the spindle with some sort of through-bolt or grub screw and always rotates with it. It can be connected to the V-pulley - and disconnected from it - by a pin (P) which is often spring-loaded, or by a nut and stud arrangement or some sort of quick-release fastening. In normal use the V-pulley is rotated by the drive belt and the spindle turned through the action of the pin driving the Bull Wheel and hence the spindle to which it is connected. To engage backgear the lathe is stopped, the pin (P) withdrawn (leaving the pulley and small gear free to rotate) and the Backgear (BG) rotated on its eccentric shaft to bring it into mesh with the other gears. On starting the lathe the action is now as follows: the pulley is rotated by the drive belt with the small gear (SG) on the V-pulley (V) driving the larger of the two rear-mounted backgears - which in turn causes the smaller gear at the other end of its shaft to rotate. This smaller gear drives the Bull Wheel (B) , and hence the spindle at a much lower speed (normally in the order of a 6 : 1 reduction) but with greatly increased torque. *If, instead of a pin, a bolt head is found, slacken this just sufficiently so that it can be pushed downwards to disengage the bolt that holds the bull-wheel and pulley together. If the nut is removed the pin may fall to the inside, requiring the whole headstock assembly to be dismantled in order to recover it. Examination of the headstock pulley and the backgear shaft may well reveal the presence of oil holes; these are important for, when working in backgear, considerable forces are being transmitted and the whole assembly requires frequent lubrication if it is to work reliably. If the pulley is allowed to seize on the headstock spindle considerable time - and possibly money - will have to be spent in order to free it off. Not all backgears engage like the one above: some, like the one on the 1906 Drummond illustrated below, are just slide into position while others are held in a forked bracket with operating lever and also slide sideways. Some are even built into the larger end of the headstock pulley and operate on a "epicyclic" principle, not unlike that of a Sturmey-Archer hub gear on a bicycle (an epicyclic backgear arrangement is shown lower down the page). There is often a small mark on the pulley to show where the pin, that passes through the bull wheel, will engage (if this is missing, one could, with advantage, be scribed or punched). The face of the pulley is often not a simple, flat surface but hollowed out with a small drilled boss provided to carry the pin; if just pushed in at random and the lathe started, the pin will catch on the side of the boss and bend. If your backgear constantly jumps out of engagement there may be an adjustable friction screw with a locknut, hidden away at the back of the casting, that will bear against the shaft..
|
|
|
|
|
|
|
|
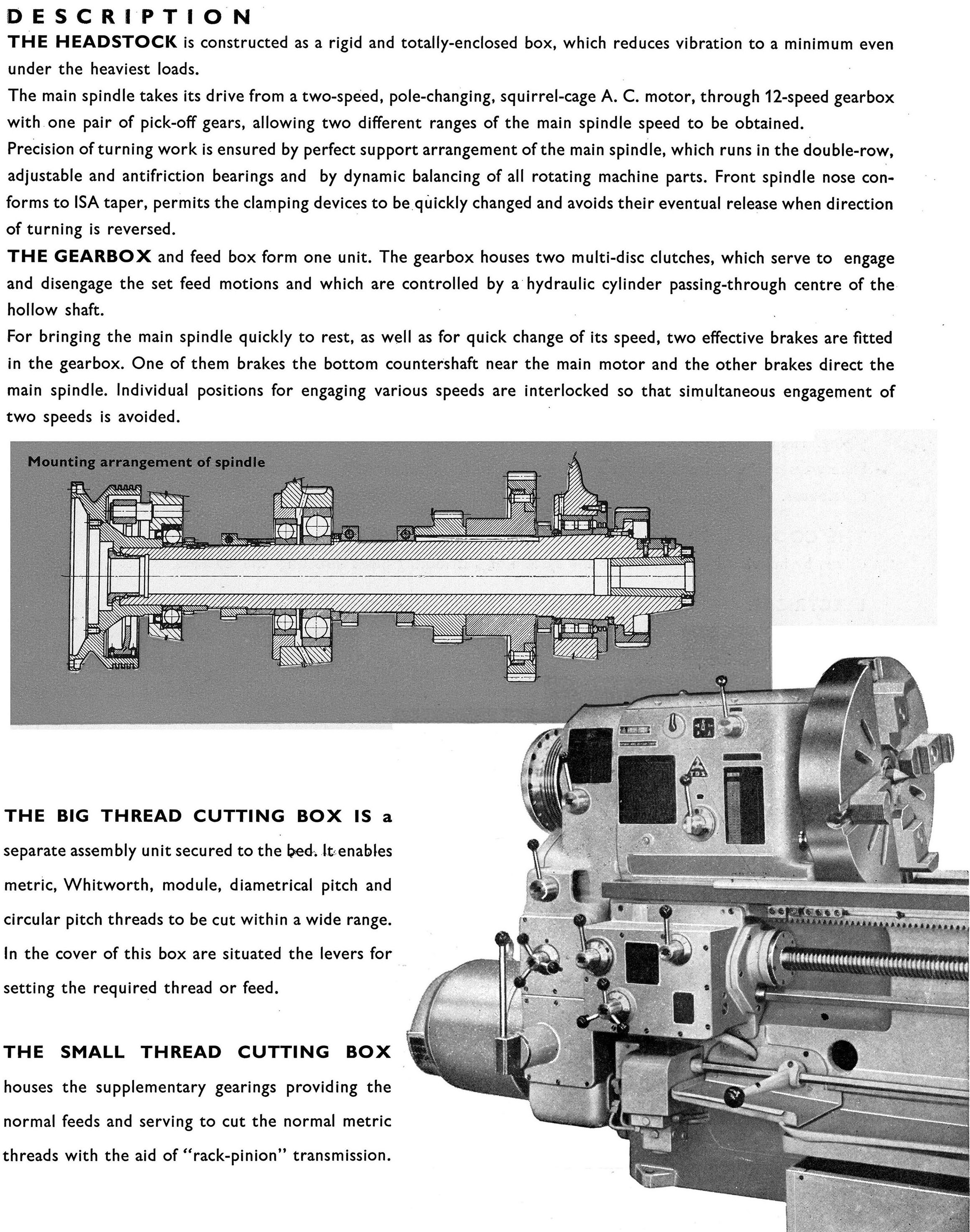 |
|
|
|
|
|
|
|
|
|
|
|
|
|
|
|
|
|
|
|
 |
|
|
|
|
|
 |
|
|
|
|
|
|
|
|
|
|
|
|
|
|
To engage the backgear on a Myford ML1 to ML4, the pulley has to be released from the spindle. DO NOT UNBOLT THE LARGE SPINDLE-MOUNTED GEAR - the bullwheel - THIS HAS TO STAY LOCKED, PERMANENTLY TO THE SPINDLE. To free the pulley and its integral gear, remove the screw that passed though the either the smallest pulley on flat-belt drive models or though a boss to the left of the smallest pulley on V-belt types; squirt some oil into the hole (the pulley is going to rotate around the spindle). Next, engage the backgears using the handle that rotates them around their eccentric shaft. Check that all is well by pulling on the drive belt; this will rotate the pulley and its small, attached gear that, in turn, rotates the larger of the two backgears. As the large backgear wheel has a smaller one attached to it, that engages with the spindle-mounted bull wheel - the result being something like a 6 : 1 drive ratio reduction.
|
|
|
|
|
|
|
|
|
|
|
|
|
|
 |
|
|
|
|
|
|
Late-model V-belt drive ML2/ML4 headstock pulley
|
|
|
|
|
|
|
|
 |
|
|
|
|
|
On this early and (wonderfully-original) Drummond lathe the Bull Wheel and Drive Pulley are connected together not with a pin, but a substantial nut and stud. The "head" of the stud engages with a slot in the periphery of the pulley wheel (note the notch cut in the pulley to show the operator where the slot is). To engage the drive, the nut is slackened (not removed, if it is, the bolt may well fall to the inside and require the headstock to be dismantled) and then pushed downwards to disengage the pin that joins the gear to pulley. The rear-mounted backgear is then slid sideways into its operating position and held in position by a pin that passes through the casting to engage with a slot turned in the backgear shaft.
|
|
|
|
|
|
|
|
|
|
|
|
|
|
 |
|
|
|
|
|
|
|
|
On the Myford ML7 the backgear was clustered at the front of the spindle, the lower pair of gears being mounted on an eccentric boss that was rotated by a lever immediately below the spindle nose. The bull wheel was connected to the pulley and its small gear by a claw that slid in a slot machined into the back of the gear. The claw was held in place by an Allen-headed bolt, visible in the picture positioned in line with the front bearing clamp bolt. The small bronze gear on the spindle was extended into the pulley as a long bush - so providing a bearing surface for it to run on when backgear was engaged.
|
|
|
|
|
|
|
|
|
|
|
|
|
|
|
|
|
|
|
 |
|
|
|
|
|
|
|
|
Backgear on the cheaper Myford ML10 lathe was also clustered at the front, but the gears were held in a simple forked bracket at the rear of the headstock and simply slid into place.
|
|
|
|
|
|
|
|
|
|
|
|
|
|
|
|
|
|
|
 |
|
|
|
|
|
 |
|
|
|
|
|
|
|
|
On the Randa lathe the backgear was clustered at the end of the headstock spindle - a design used on several less-expensive small British lathes
|
|
|
|
|
|
|
|
|
|
|
|
|
 |
|
|
|
|
|
Headstock epicyclic gear housing on the 109 Not as common on other makes as one might expect - especially given the transformation it can make to a lathe's capabilities - the compact epicyclic (or planetary) backgear assembly fitted to some AA-manufactured, Craftsman-branded machines gave a range of slow speeds that allowed screwcutting and the facing of large diameters to be undertaken with a greater chance of success. Consisting of three main elements, the mechanism comprised: a gear attached to a 3-step pulley, a carrier with 3 planet pinions and an annulus gear. The 3-step pulley, together with its attached "sun" gear, was free to rotate on the headstock spindle. Opposite was a large gear cut on the inside surface of a short cylinder so that its teeth faced inwards (an annulus gear): this assembly was also free to rotate on the spindle. The "sun" gear on the 3-step pulley engaged simultaneously with 3 "planet" gears (called pinions because they meshed with a larger gear) mounted on studs attached to a carrier plate that was both keyed (permanently) to the spindle and locked (temporarily, by a sliding block) to the annulus gear. Because the carrier was both keyed to the shaft and locked to the annulus gear, non of the gears could rotate and turning the pulley caused the spindle to rotate - so giving a direct drive. For any epicyclic gearing to work, one of the three gears sets has to be held stationary so that one of the other gear sets can act independently as an input and the third set independently as an output. In the case of the 109 lathe it was the annulus gear that was prevented from rotating (by a 2-position indented pin passing through the front face of the headstock into its face) and the carrier assembly that had to be released so that it could turn independently. The carrier had six slots cut in its periphery into which a block, sliding in a slot cut in the face of the annulus gear, could engaged and so lock them together. The block was clamped in place by a bolt and slackening this let the block slide out of engagement and allowed the carrier and its planet pinions to rotate. With this new arrangement set, turning the pulley caused the "sun" drive gear to rotate the planet pinions, mesh with the annulus gear and so reduce the drive ratio. When you see the mechanism in action, its function is obvious - though tortuous to explain. Another AA epicyclic backgear assembly, with the annulus gear held stationary by a clamp, can be seen in pictures of the company's last lathe, the 109.21290.
|
|
|
|
|
|
|
|
|
|
|
|
|
|
|
|
|
 |
|
|
|
|
|
|
The whole of the epicyclic gear assembly. On the left the annulus gear, free to rotate on the spindle: in the middle the carrier plate keyed to the spindle with its 3 "planet" pinions: on the right, and also free to spin on the headstock spindle, the 3-step pulley with its attached "sun" gear.
|
|
|
|
|
|
|
|
 |
|
|
|
|
|
|
The carrier plate with 6 slots in its periphery to accept the sliding block that locked it to the annulus gear
|
|
|
|
|
|
|
|
 |
|
|
|
|
|
|
The annulus gear showing the internal gear teeth and, at the top, the sliding block to lock into the carrier plate
|
|
|
|
|
|
|
|
 |
|
|
|
|
|
|
Two-position indent pin on the face of the headstock used to lock the annulus gear
|
|
|
|
|
|
|
|
|
|
|
|
|
|
 |
|
|
|
|
 |
|
|
|
|
|
|
|
|
|
A view of the mechanism in place but without the annulus gear
|
|
|
|
|
|
|
|
The MAZAK Planetary gears and their mounting plate
|
|
|
|
|
|
|
|
|
|
|
|
|
|
 |
|
|
|
|
|
|
"Sun" gear mounted on the pulley and "Planetary" gears on the spindle
|
|
|
|
|
|
|
|
|
|
|
 |
|
|
|
|
|
|
|
|
|
|
|
|