 |
 |
 |
 |
 |
 |
 |
 |
 |
 |
 |
 |
 |
 |
 |
 |
 |
 |
 |
 |
 |
 |
 |
 |
 |
 |
 |
 |
 |
 |
 |
 |
 |
 |
 |
 |
 |
 |
 |
 |
 |
 |
 |
 |
 |
 |
 |
 |
|
|
|
|
|
|
|
|
|
|
|
|
|
|
|
|
|
|
|
|
|
|
|
|
|
|
|
|
|
|
|
|
|
|
|
|
|
|
|
|
|
|
|
|
|
|
|
|
|
|
|
|
|
|
|
|
|
|
|
|
|
|
|
|
Shown below is series of photographs that illustrates, stage by stage, how the Kärger (and other makes) of sliding headstock spindle chase screwcutting operate. With thanks for the pictures to Wally Murray in the U.S.A. A thick plate, able to be moved vertically to engage the threading, was dovetailed to the outside face of the headstock casting. Instead of the threading tool being made to move along the job as with an ordinary chase-type or changewheel-driven screwcutting - the headstock spindle was arranged to slide forwards and backwards in its bearings and the cutting tool remained stationary. Widely used on ornamental turning lathes in the 1800s, in more recent times it was adopted by such German firms as Lorch ,Wolf Jahn, and Auerbach (the smallest model to incorporate it being the Wolf Jahn Model AA with a centre height of just 50 mm) and the Swiss-built Schaublin The arrangement was also a feature of most "Swiss-Auto" mass-production lathes used for the manufacture of tiny parts - and is still in widespread use today on such machines--though these are now, of course, fitted with CNC control. The last conventional lathe on which sliding-spindle screwcutting appears to have been available was a version of the Schaublin 102 marketed in in the early years of the 21st century. Designed originally for use by optical instrument makers, who needed a short but very accurate thread, a disadvantage of the "chase" system was the need to keep in stock a range of master threads and their matching star-shaped bronze followers. However, with the limited range of thread pitches required this was not unduly expensive and usually included in the set (to allow the manufacture chuck backplates and other work-holding units) would have been one coarse-pitch pair with the same thread as used on the lathe's spindle nose..
|
|
|
|
|
|
|
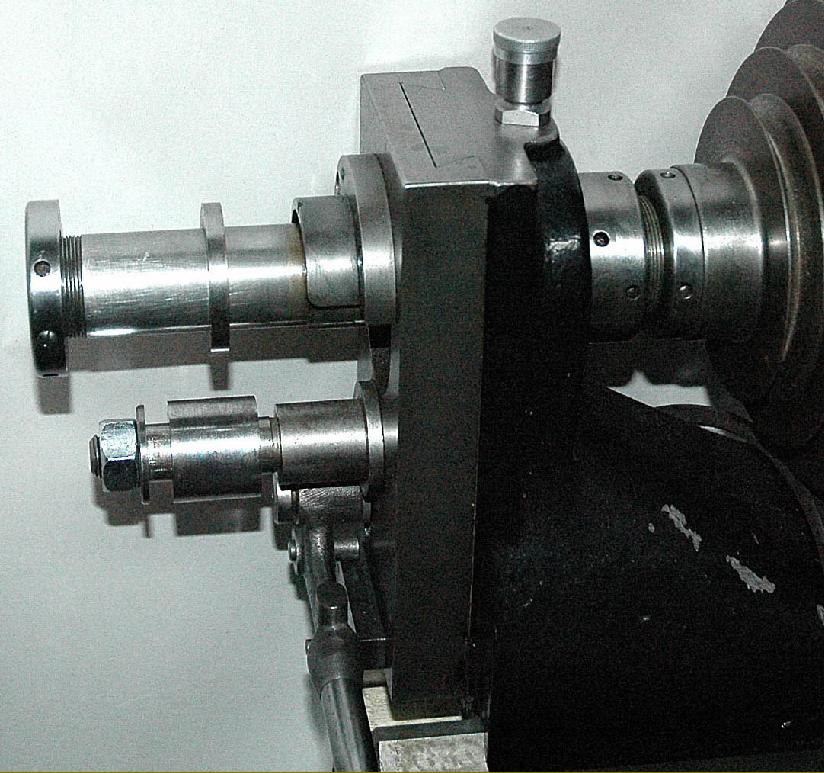 |
|
|
|
|
|
|
Left-hand end of the headstock showing the sliding plate dove-tailed to the outer face of the casting. There is no gib or adjustment to the ways, the fit being "dead-on" The left-hand end of the spindle accepts one of a number of a threaded "master" cylinders which determine the pitch of the advancement of the spindle across the threading tool. The cylinder is held between a hardened washer (loose on shaft) and a threaded collar on the left. The stepped shaft below, mounted rigidly to the sliding plate, accepts a corresponding partial "female" thread cut into the periphery of a bronze star wheel.
|
|
|
|
|
|
|
|
|
|
|
|
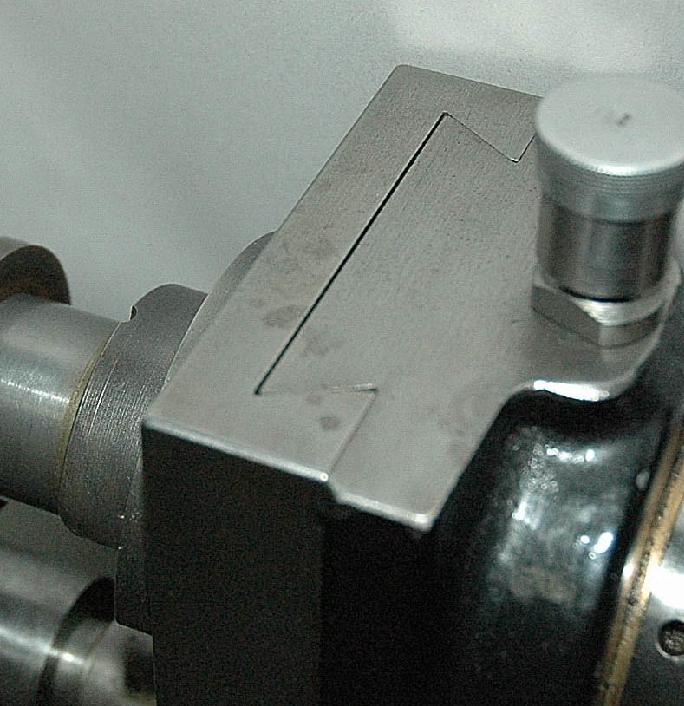 |
|
|
|
|
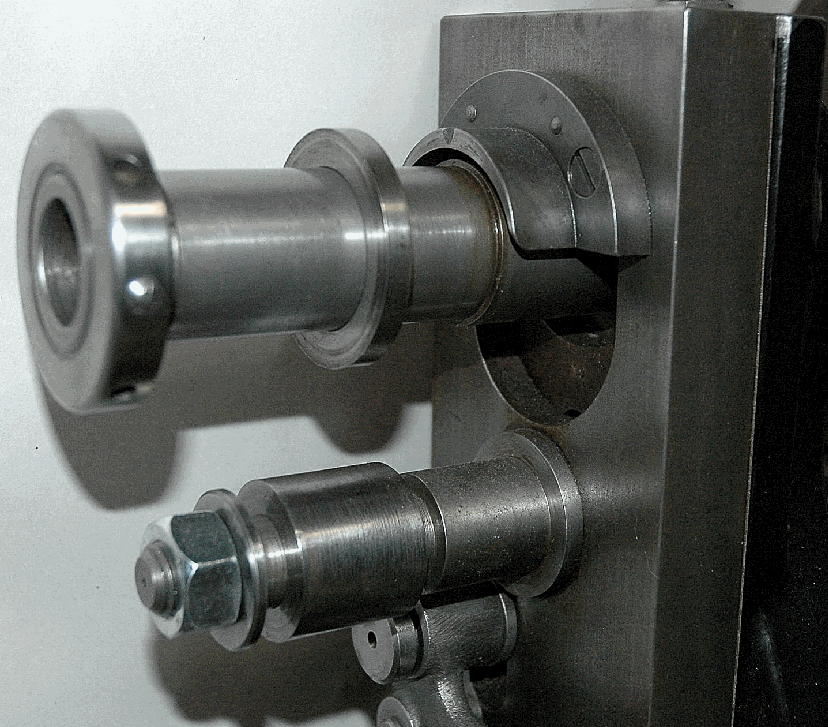 |
|
|
|
|
|
|
A slotted hole in the end-plate gives clearance for the spindle as the plate slides up or down. The semi-circular "cowling", complete with a groove for keeping the contact oiled, provides a bearing surface for the hardened washer.
|
|
|
|
|
|
|
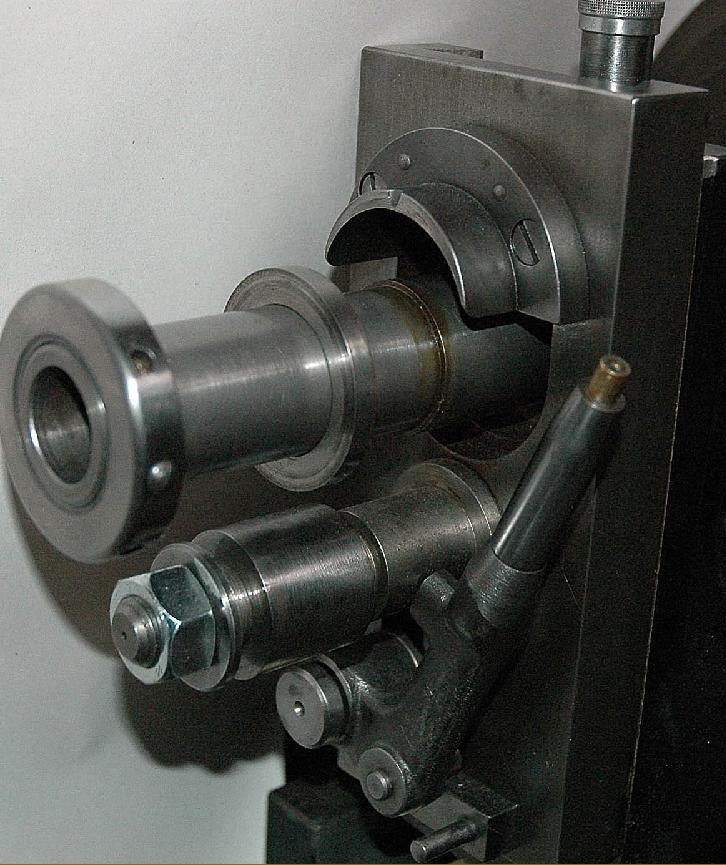 |
|
|
|
|
|
|
Still without a threaded "master" cylinder or "star" driver, the mechanism is shown here with the plate raised (by spring loading), to the "engaged" position. Notice how the bearing "cowling is now out of the way. In this arrangement, the spindle is free to be moved axially by hand for a distance of just under 2" (50 mm).
|
|
|
|
|
|
|
|
|
|
|
|
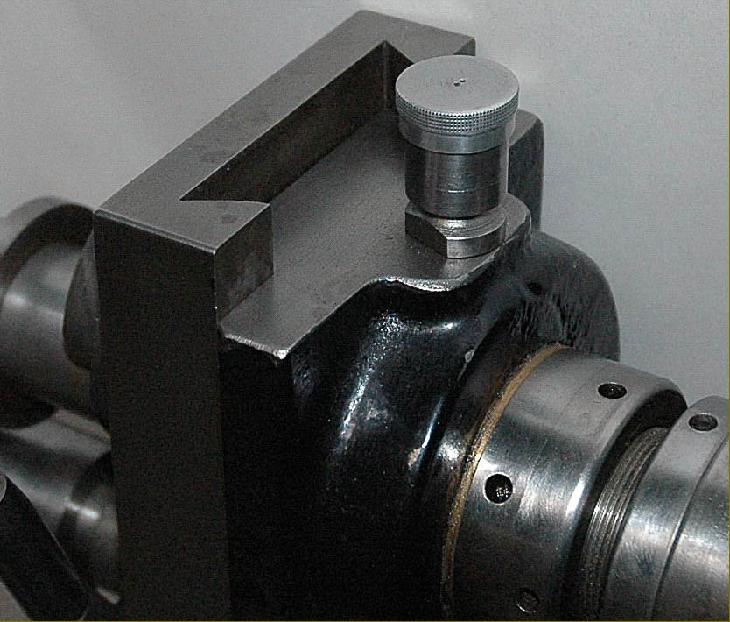 |
|
|
|
|
|
|
The dove-tailed plate in its raised position.
|
|
|
|
|
|
|
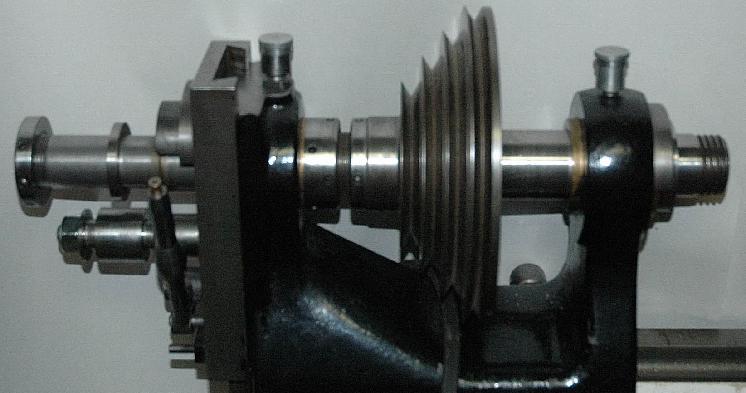 |
|
|
|
|
|
|
The spindle is at its full-left limit for the start of a thread pass.
|
|
|
|
|
|
|
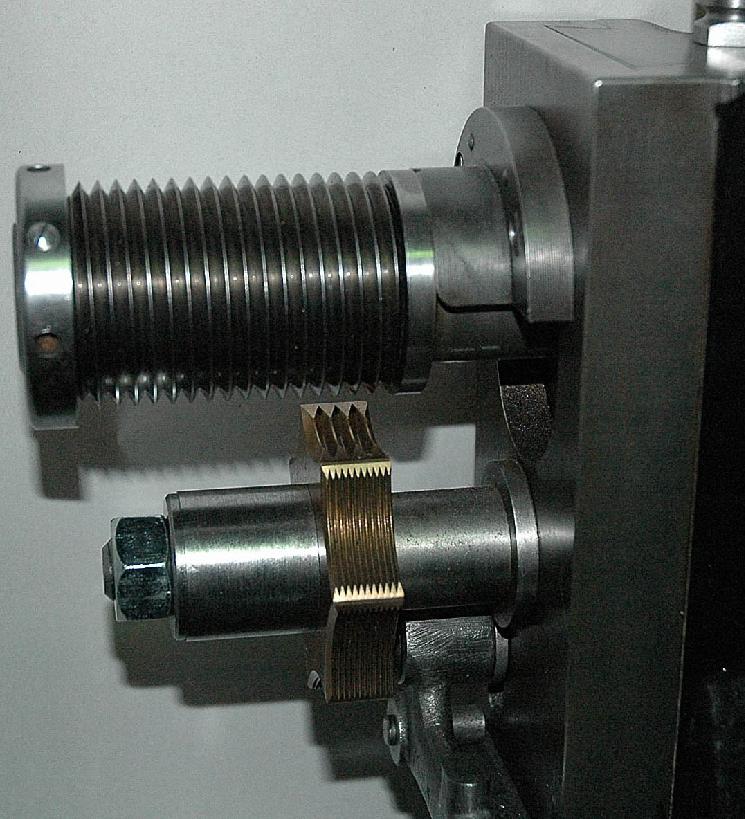 |
|
|
|
|
|
Upper "master" cylinder and bronze "star" driver in position. This is the special pair (provided by most makers of similar systems) to replicate the 4-mm pitch thread used on the spindle nose. The end-plate is in the disengaged (down) position, the hardened washer is abutting the thrust "cowling" and the collar at the left-hand end of the headstock spindle is adjusted and locked to allow free rotation with a minimum of axial play.
|
|
|
|
|
|
|
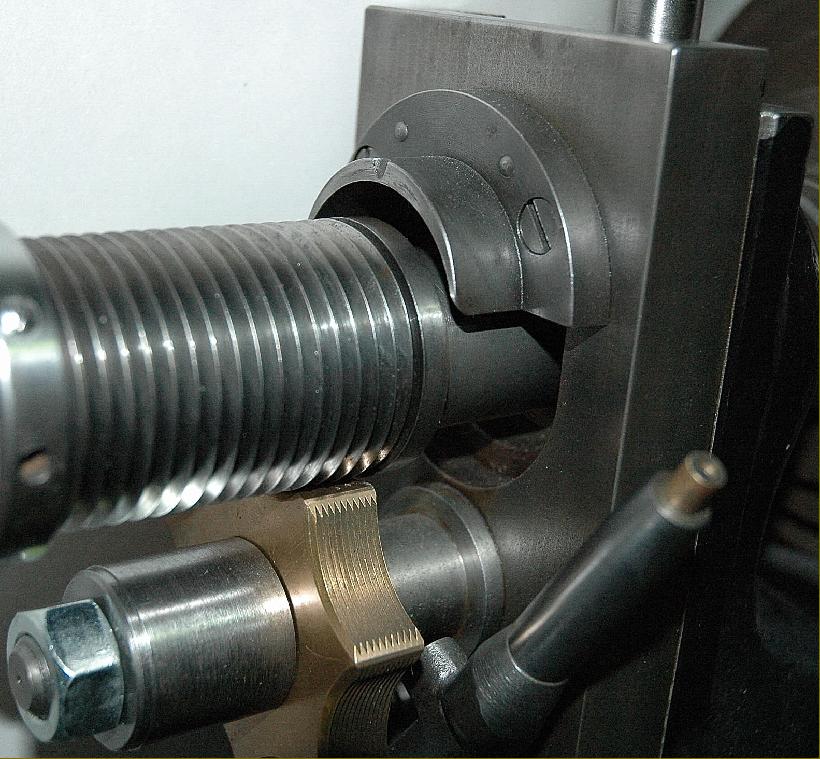 |
|
|
|
|
|
|
The lever is raised and the threads engaged.. The female thread is fixed (except for a small amount of radial freedom to best conform to the male contour). The thrust cowling is clear of the hardened washer and now, as the spindle rotates, it will advance 4.0 mm per revolution to
|
|
|
|
|
|
|
|
|
|
|
|
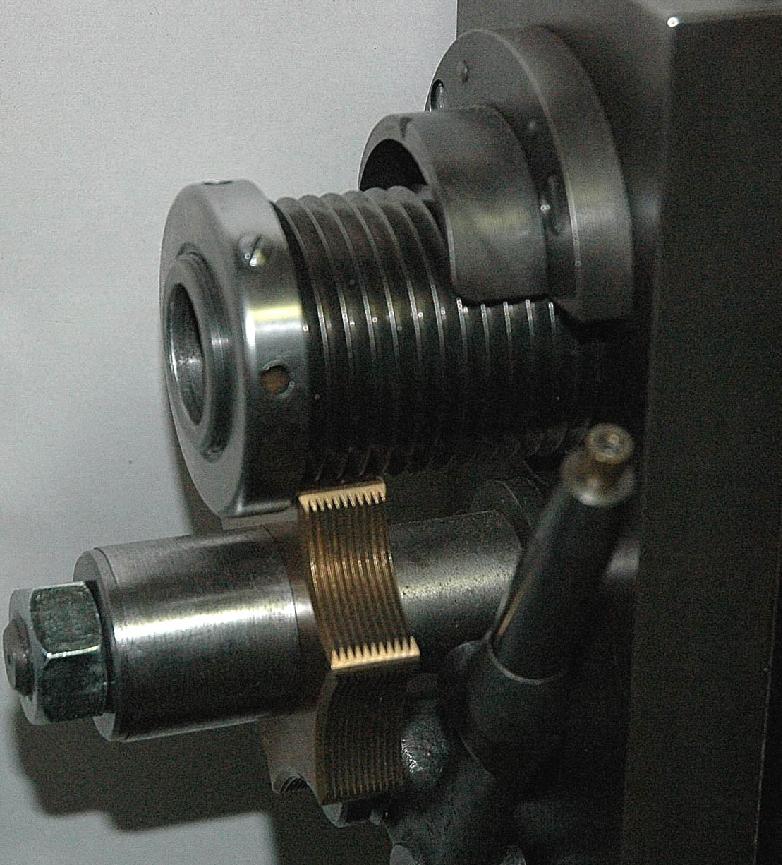 |
|
|
|
|
|
|
The rotation of the spindle has driven it all the way to the right.
|
|
|
|
|
|
|
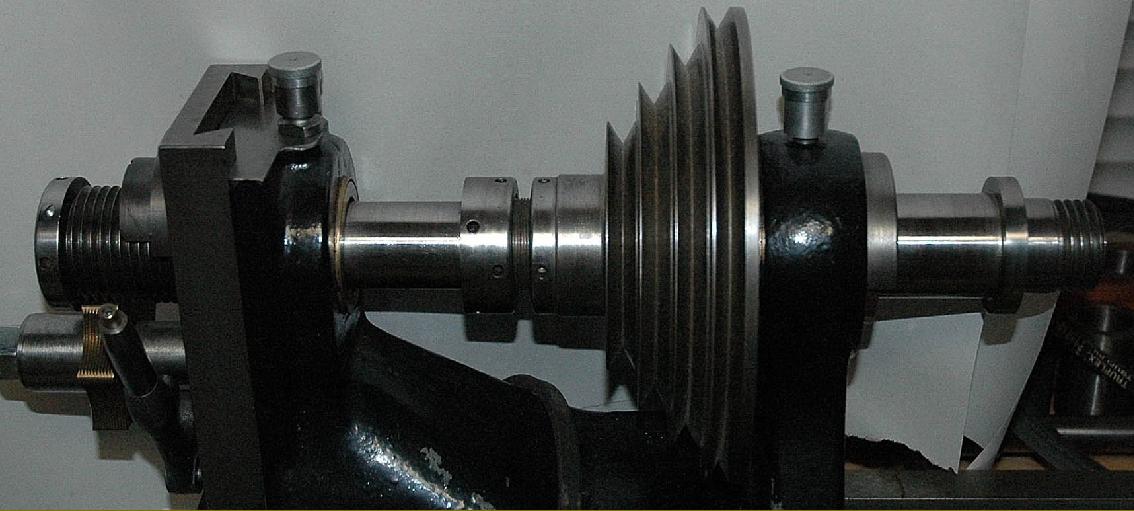 |
|
|
|
|
|
The headstock spindle advanced fully to the right
|
|
|
|
|
|
|
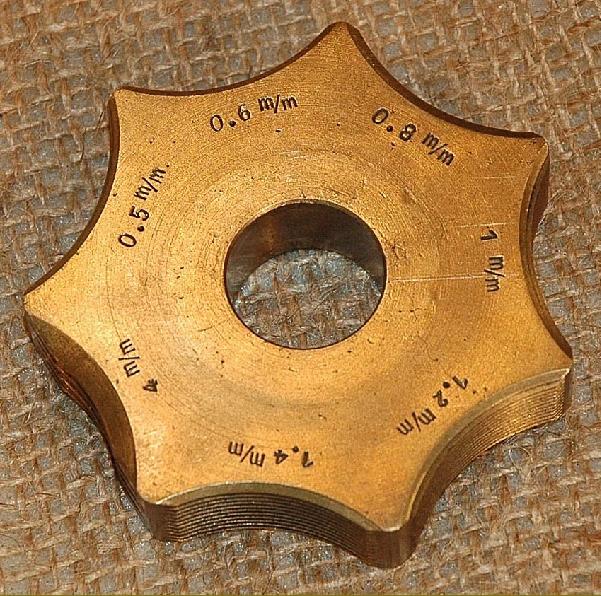 |
|
|
|
|
|
|
|
|
|
|
|
|
|
|
|
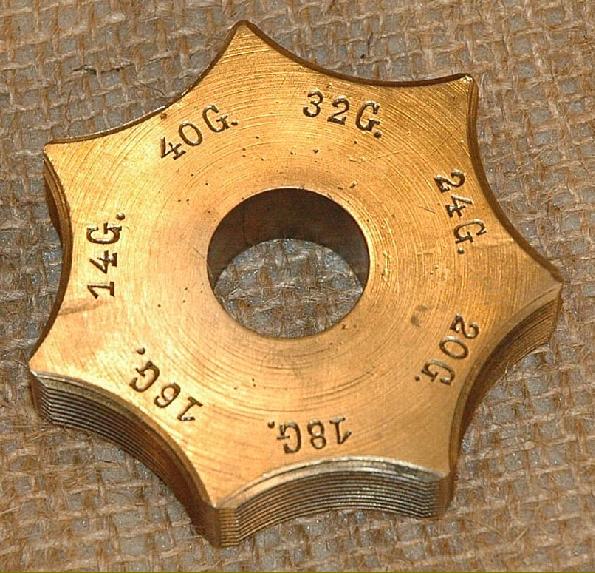 |
|
|
|
|
|
|
Whitworth (inch) pitch star wheel
|
|
|
|
|
|
|
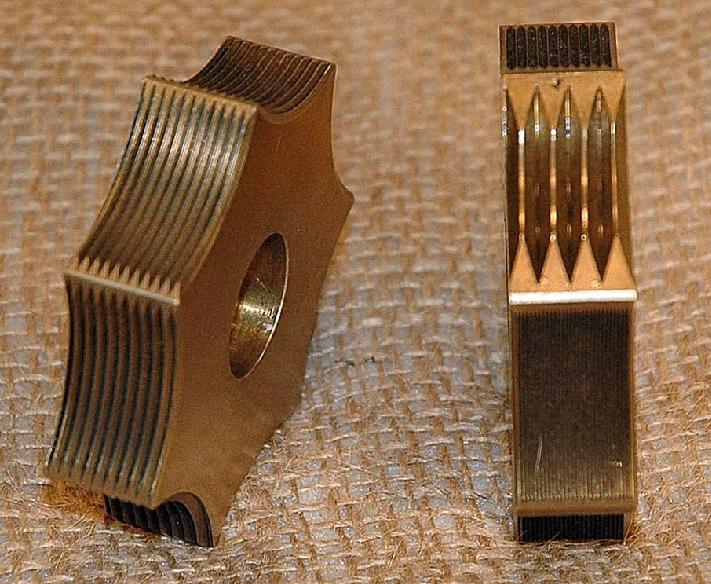 |
|
|
|
|
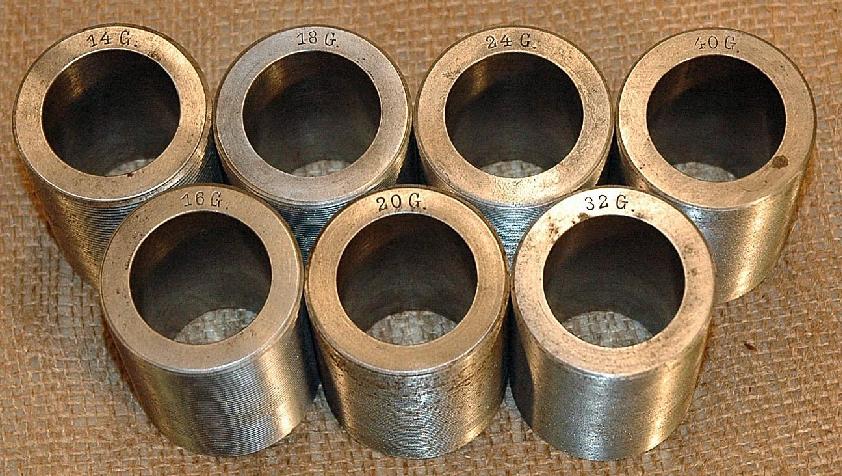 |
|
|
|
|
|
|
A set of Whitworth (inch-pitch) master cylinders. The letter "G" stands for "gewinde", German for thread or worm and also grad = pitch
|
|
|
|
|
|
|
|
|
|
|
|
|
|