 |
 |
 |
 |
 |
 |
 |
 |
 |
 |
 |
 |
 |
 |
 |
 |
 |
 |
 |
 |
 |
 |
 |
 |
 |
 |
 |
 |
 |
 |
 |
 |
 |
 |
 |
 |
 |
 |
 |
 |
 |
 |
|
|
|
|
|
|
|
|
|
|
|
|
|
|
|
|
|
|
|
|
|
|
|
|
|
|
|
|
|
|
|
|
|
|
|
|
|
|
|
|
|
|
|
|
|
|
|
|
|
|
|
|
|
|
|
|
|
|
Manufactured from early in the 1940s, and based on a pre -WW2 German design by G. Boley, the beautifully-made Smart & Brown Model L 4.5" x 13.5" was typical of the multi-purpose, precision plain-turning lathe as widely employed from the late 19th century until the final decade of the 20th. Similar lathes were also made in Europe by, amongst many others, G.Boley, Schaublin, Lorch, Leinen and Mikron, as well as a host of American manufacturers. All followed a similar design philosophy with the bed and stand remaining virtually unchanged but with a variety of drive systems, headstocks, collet closers, slide rests (including capstan types) and tailstocks offered to convert the basic lathe into one suitable for the finest toolroom use, light-duty continuous production or "second-operation" work. Although later versions of the Model L were mounted on fabricated-steel bases, the very first was fitted to cast aluminium stands (light enough for one man to lift) - though these were soon replaced by a much heavier and more rigid cast-iron unit - some of these having a special, heavy-duty drive system. The headstock of all models was "bullet-proof" and, providing the bearings were adequately lubricated, could be run daily for many years without attention or adjustment. At first, model types were divided into the Series 25 for toolroom use, Series 30 for production (or second-operation work) and the Series 35 for continuous production when fitted with a 6-station indexing capstan unit, cut-off slide and a lever-operated collet closer. Each Series was produced as four models, A, B, C and D, with each specified for a particular purpose and equipped with the most appropriate type of drive system, speed range and collet capacity. The 25A, 30A and 35A had a 3-step cone pulley fitted to the shaft of a 960 r.p.m. motor driving by a 1-inch wide flat belt to a matching pulley on the headstock - this arrangement giving speeds of 500, 860 and 1420 r.p.m. The 25B, 30B and 35B were better specified and, with a speed-reducing countershaft inside the cabinet base, enjoyed a wider and more useful range of 6 spindle speeds: 250, 430, 500, 760, 860 and 1550 r.p.m. Alternatively, the high-speed Models 25C, 30C and 35C could be supplied: these had drive direct from a 3-step cone pulley but with a 2-speed 720/1440 r.p.m. motor to give speeds of 370, 630, 740, 1065, 1260 and 2130 r.p.m. Some versions of the "direct-drive" models were fitted with an ingenious and very heavily-built two- jockey pulley arrangement that both tensioned the belt and gave it a little extra wrap-around on the pulleys. Another (very rare) version used a Carter hydrostatic variable-speed unit - of a type still available today and sold by the Renold Company in the UK. Bench-mount models (few can have been sold) were listed as the 25D and 30D and could be equipped for drive by the customer's own system or from a Smart & Brown ball-bearing countershaft with old-fashioned belt-shifter gear. By the mid-1950s the model designations had been revised, though the range remained unaltered, with a numbering system that ran from L1 to L16. Continued below:
|
|
|
|
|
|
|
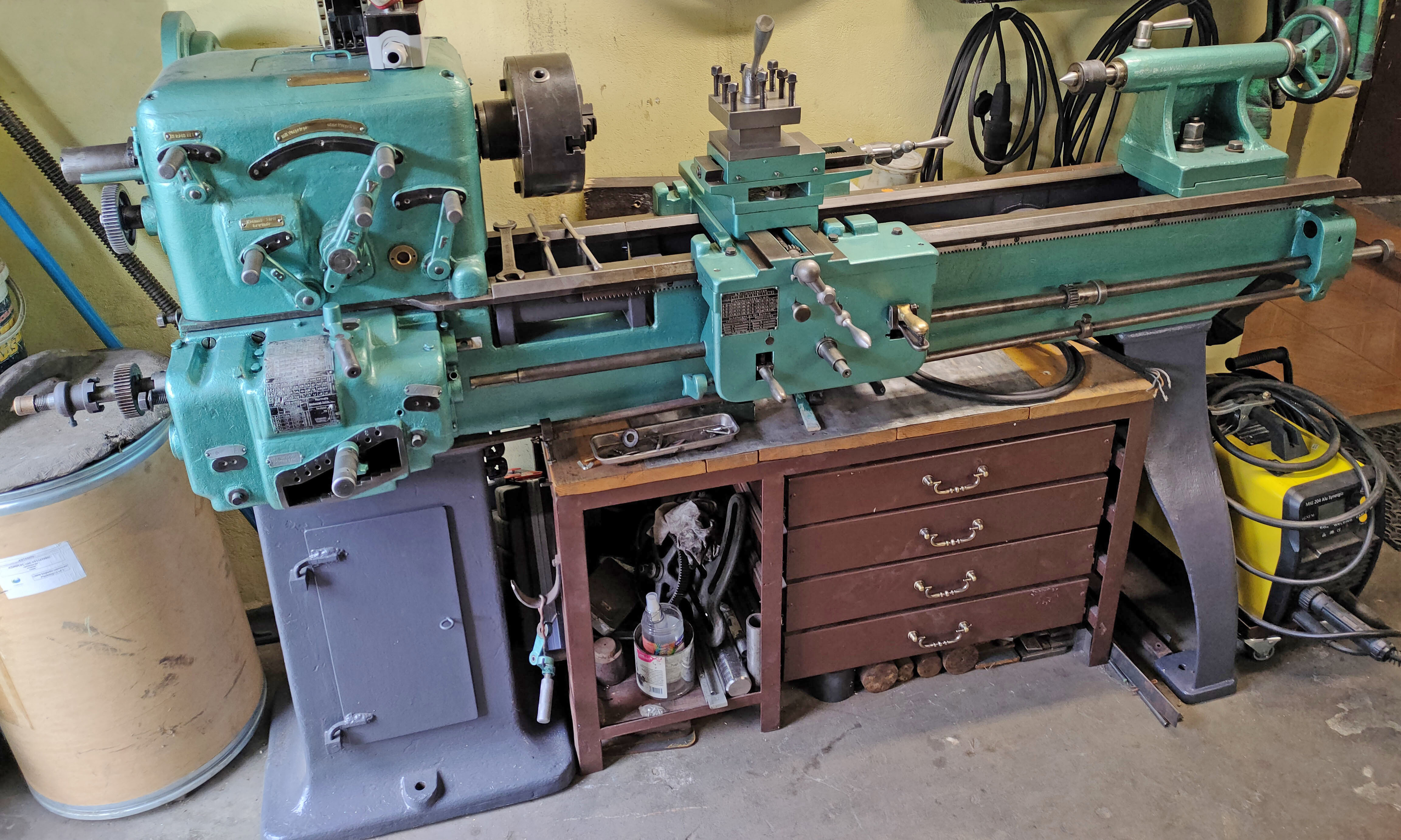 |
|
|
|
|
|
|
Smart & Brown Model 25 Toolroom plain-turning precision lathe
Continued: Originally six headstocks were manufactured: the Types PLH, PRH, PSH, PDH, PGH and PFH, all with a 4-inch centre height and driven by a 1-inch wide flat belt. The PLH used a nickel-steel spindle, hardened and ground and running in lapped phosphor-bronze bearings with a parallel bore and tapered on the outside for adjustment. Like many similar precision lathes, the pulley (to prevent belt pull interfering with the accuracy of the assembly) was supported in its own (ball journal) bearings with drive to the spindle through a peg. A pull-in, handwheel-operated collet closer was fitted as standard (with or without a ball race to help with larger collets) the spindle bore was 63/64" (25 mm) and the nose fitted with a 13/4" x 8 t.p.i thread. The PRH headstock was identical to the PLH, but with a lever-action collet closer, whist the PSH was designed especially for small work and fitted with a handwheel collet closer and a 21/32" bore spindle with a maximum collet capacity of 5/16". Speeds up to 2500 r.p.m. could be maintained with reliability and the spindle nose carried a 8 t.p.i. thread 13/16" in diameter. For even higher-speed work, up to 3,500 r.p.m., headstock PDH was recommended: this used a bronze front bearing, like the others, but fitted at the rear was a pair of high-precision, pre-loaded ball races that could take both journal and end thrust - and which required no adjustment. With a bore of 29/32" and a collet capacity of 11/16", the spindle was screwed on its nose, but only with a fine thread for mounting a collet-closing cap, it could not accept chucks or other screw-on fittings. As no draw-bar system was available - and the cap on the front was used to compress them - the collets had to be of the Smart & Brown Type 4B dead-length type. The rarest of the headstocks was the PGH: this was similar in arrangement to the PLH, but with the same bearing system as the PDH. However, it also incorporated a 3 : 1 epicyclic reduction gear within the pulley - this having to be keyed to spindle, the usual separate set of bearings for the pulley not being possible with this mechanism. The nose was 13/4" in diameter, with an 8 t.p.i. thread and a handwheel draw-bar to close the collets - if a lever-action collet closer was fitted the model type changed to PFH. Like the equivalent Mikron type, this rare and desirable type can be instantly identified by the short epicyclic gear engagement lever in front of the left-hand bearing. By 1954 two additional headstocks were being offered, the PRH/1 and LPH. The PRH/1 could mount standard 5C collets and had a nickel-chrome steel spindle, case hardened and ground on all working surfaces and running in special high-precision, anti-friction bearings. Thrust and radial loads were taken by an angular-contact bearing at the front with radial loads only by a rear taper-roller race. The nose was a massive 2" x 8 t.p.i. , maximum speed 3000 r.p.m. and the largest bar that could be passed through the hole was 19/64". The LPH headstock was a modification of the earlier PDH unit; it retained the same bearing arrangement (plain at the front, ball races at the rear) and the nose-mounted arrangement for dead-length collets. However, its ease of operation was significantly improved by the incorporation of an ingeniously combined brake, clutch and collet-closer mechanism operated by a handle on its front face. With the work loaded into the collet one movement of the handle to the left released the brake, closed the collet and engaged the driving clutch. With the work complete, a further single movement of the handle to the right opened the clutch, applied the brake to stop the spindle (almost instantaneously) and opened the collet. To adjust the grip of the collet a handwheel was fitted to the left-hand end of the spindle. Continued below:
|
|
|
|
|
|
|
|
|
|
|
|
|
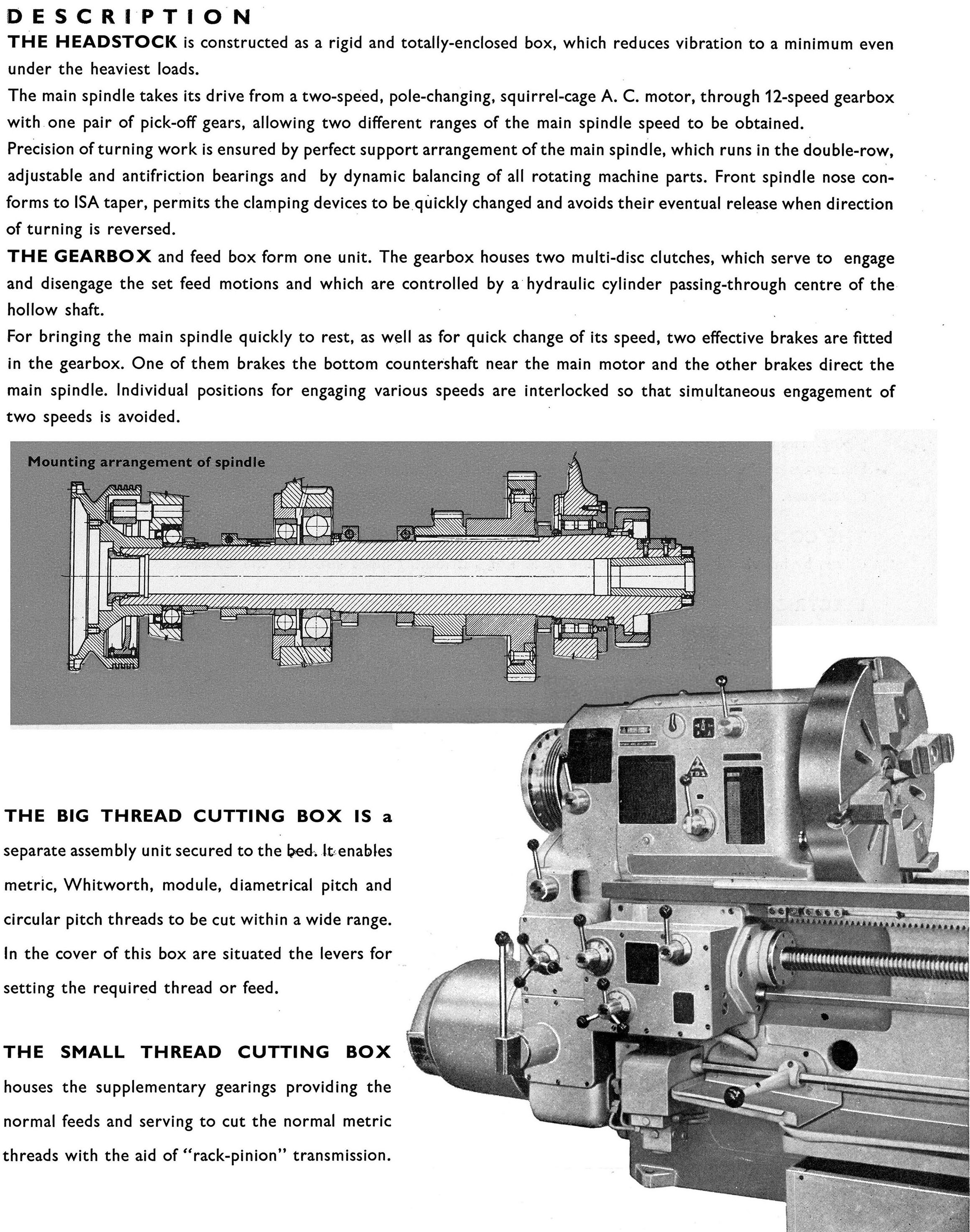 |
|
|
|
|
|
|
Compound slide rest Type CSP fitted to the Model 25
Continued: As might be expected, several different types of slide rests were available to convert the Model L from one type of operation to another. The standard compound screw-feed unit for toolroom work was the Type CSP; this had the usual type of long-travel top slide - 4.5 inches - that could be swivelled through 60° each side of zero, though the graduations only extended to 45°. The Acme feed screws ran through phosphor-bronze nuts, with only that on the cross slide adjustable (by means of a rotating flange) to take out backlash. Whilst the cross slide ways (and both screws) were covered, those on the twin-T-slot top slide were left exposed, the design, however, allowing the maximum of travel to be obtained. Unfortunately the 0.001" graduated micrometer dials were too small, a criticism, however, that could also be levelled against any number of similar slides from competing makers. For production work the compound rest type CTP was offered; this was an all-lever-feed slide, through rack-and-pinion gearing, with a maximum longitudinal travel of 3.5 inches and all ways covered against the wearing effects of swarf and dirt. Adjustable stops were fitted at both the front and back of the travel and the makers claimed that they would: ...maintain size irrespective of the degree of pressure exerted. For special work a slide having quick-feed, coarse-pitch threads was offered, the Type CUP. This utilised the standard screw-feed cross-slide casting (though no doubt it could have been built onto a lever-feed unit if required) but fitted with a rear toolpost and a heavily-constructed top-slide equipped with extra-wide and deep (but exposed) bevelled ways. Both screws had Acme threads, with a 1/5" lead, running through backlash-adjustable bronze nuts with front and back stops provided on the cross feed - and one stop on the top. The unit was, in many ways, very similar to the No. 27 slide produced for the Swiss Mikron lathe, though the Swiss company offered several additional variations on the same theme. If an indexing 4-way toolpost was needed the covered-way slide Type CXP could be fitted in place of the top slide on the Type CSP. The slide had a maximum travel of 3 inches, an Acme-form feed screw running through a backlash-adjustable bronze bush and six closely-spaced gib-strip adjustment screws to ensure the best possible sliding action with the minimum of flex. Some versions of the slide have been found with a tapered grip strip, though these are few and far between. To complement the bed-mounted 6-station capstan unit, a 3-inch travel cut-off slide (a forming slide in American parlance) was listed; this unit, the Type CWP, could be either lever or screw-operated and was fitted with stops and toolposts at front and back. Although rival makers listed as many as ten alternative tailstocks, Smart & Brown offered only three. The ordinary unit was the Type TSC with a one-piece casting, a conventional screw-feed 1-inch diameter barrel with a No. 1 Morse taper and a travel of 2.5 inches. For heavier-duty work the Type TUC was offered; this very rare version had a sole plate, to allow set-over for the turning of slight tapers, a 1.25-inch diameter barrel with a No. 2 Morse taper, a travel of 3.25 inches and an Acme feed screw that ran through an adjustable bronze nut. For production use, or sensitive drilling, the Type TTC could be supplied. Fitted with a 1-inch diameter barrel it was adapted to carry 4C collets, with a maximum capacity of 5/16" retained by a screw-on drawbar passing down the barrel. The operating handle could be swivelled to suit the task in hand, an adjustable stop was fitted and, for work between centres, a solid collet with a centre could be fitted. Repetition production work was catered for by the addition of a six-station bed-mounted capstan slide the Type RST. Automatic indexing was fitted and each tool position had an adjustable length stop fitted to a boss that rotated with the slide. The unit was built for long and arduous service with all working parts hardened and ground and the turret head rotating on compound bearings..
|
|
|
|
|
|
|
 |
|
|
|
|
|
|
Smart & Brown Series 25 Model A toolroom plain-turning precision lathe
|
|
|
|
|
|
|
|
|
|
|
|
 |
|
|
|
|
|
|
Lever-operated compound slide rest Type CTP
|
|
|
|
|
|
|
 |
|
|
|
|
|
|
Smart & Brown Series 30 Model C. This lathe used a drive system also employed on the Models 25C and, 35C - directly from a 3-step cone pulley on the shaft of a 2-speed 720/1440 r.p.m. motor to give speeds of 370, 630, 740, 1065, 1260 and 2130 r.p.m.
|
|
|
|
|
|
|
 |
|
|
|
|
|
|
Smart & Brown L lathe in Series 35C form for continuous production fitted with a 6-station indexing capstan unit, cut-off slide, a lever-operated collet closer and 12-speed drive
|
|
|
|
|
|
|
|
|
|
|
|
 |
|
|
|
|
|
|
Toolroom lathe fitted with a lever-operated collet closer Type SB111
|
|
|
|
|
|
|
 |
|
|
|
|
|
|
Smart & Brown Model L set up as a second-operation lathe will all-lever control of collet-closer, slide rest and tailstock
|
|
|
|
|
|
|
 |
|
|
|
|
|
|
Another view of the all-lever controlled second-operation lathe
|
|
|
|
|
|
|
|
|
|
|
|
 |
|
|
|
|
|
Late Model L (1970s) Dimensionally identical to the earlier models, these late machines featured 'squared-off' styling to make them look 'modern'. Shown above is the Type L.2.PLH/1 the direct drive single-speed motor, the PLH/1 capacity headstock with a draw-bar operated collet closer, the CSP screw-feed compound slide rest and TSC screw-feed tailstock. Several other versions were available, all similar in general specification to the original types and with the same varieties of drive system and optional equipment. Unfortunately the nomenclature used to describe them was, in comparison with the original simple three types and three models within each type, needlessly complicated and appears to have varied overtime LCC - fitted with a 6-station capstan unit and lever-operated cut-off slide LCP - lever-operated tailstock and lever-operated compound slide rest assembly (i.e. both top and cross slide) LCL - screw operated tailstock and screw-operated compound slide rest (the "toolmakers" version) LCO - lever-operated cur-off slide only LCS - lever-operated compound slide rest only The Types LCC, LCP and LCL models had a cast-iron bed mounted on a fabricated cabinet stand that held a 4 : 1 reduction drive powered by a 2-speed Demag motor/brake unit with thermistor protection that gave 12 spindle speeds from 150 to 3000 r.p.m. The Types LCO and LCS models had a direct drive unit that gave 6 spindle speeds from 416 to 2518 r.p.m. These lathes were all finished in a green "Hammerite" finish. Motors were all 3-phase running on 415 volts and 50 cycles. Alternative electrical equipment could be supplied upon request. At one point, two basic lever-operated collet closers were available for the headstock that took non-interchangeable collets as follows: Type BD for drawback spring collets: L4-4360 Type 5 1" (25 mm) capacity L4-909 Type 4A 3/4" (19 mm) capacity Type DL for dead-length spring and bladed collets: L4-10120 Brown & Sharpe (BS) Type 21 1" (25 mm) capacity L4-857 Type 4B 11/16" (17 mm) capacity Crawford Type T980 Multibore 1" (25 mm) capacity Pratt & Burnerd Type EA Multisize 1" (25 mm) capacity) Other models that followed included: LCT-PLH - as the L.2.PLH/1 but mounted on a stand with 12-speed countershaft drive with brake and reverse. L.4-PRH/1 - on a cabinet with a direct drive, single-speed motor, collet-closing mechanism guard, a lever-operated collet drawbar, the CSP screw-feed compound slide and the TSC screw-feed tailstock. LCL-PRH/1 - identical to the L.4-PRH/1 but for the fitting of a 12-speed drive with brake and reverse and a collet-closure mechanism guard. L.6PDH/1 - a direct-drive single speed motor, a collet-closing mechanism guard, the PDH 1-inch collet capacity headstock, CTP lever operated slide and the TTC lever-operated tailstock. LCP-PDH/1 - as the L.6PDH/1 but on a cabinet fitted with a 12-speed countershaft drive. L.8.PDH/1 - used the direct-drive single-speed motor with reverse, the PDH 1-inch collet capacity headstock, the RST six-station capstan turret slide and the CWP lever-operated cut-off slide. When fitted with a 12-speed drive system the L.8.PDH/1 became the LCC-PDH/1. If required, all types could also be ordered for bench mounting. In the late 1990s, approaching the end of production, prices hovered around the £5000 to £5800 mark..
|
|
|
|
|
|
|
 |
|
|
|
|
|
|
A very rare (circa 1961) Model L on a "Knee-type Cabinet and fitted with a foot-operated quick-change, spindle-speed gearbox
|
|
|
|
|
|
|
|
|
|
 |
|
|
|
|
|
|
The superbly-constructed headstock Type PRH with a fully-hardened and ground spindle running in massive lapped bronze bearings. Note the pulley with its own bearing set, an arrangement designed to eliminate the effect of belt pull of the spindle
|
|
|
|
|
|
|
|
|
|
|
|
|
|
|
 |
|
|
|
|
|
|
The late model headstock spindle was hardened all over and ran in precision angular-contact pre-loaded ball bearings at the nose end and a roller bearing at the rear. The nose accepted "5C" collets with a maximum through bore of 1 inch with either screw draw bar or lever-action closers. On the 12-speed models power was transmitted to the spindle by a toothed belt running over two sizes of pulley whilst the 3-speed model retained the original flat belt and 3-step cone pulley. The 12-speed model had six speeds from 600 to 3000 rpm in open drive - with a 4 : 1 reduction available from the two-speed electric motor to give a slower range suitable for 'threading or reaming' of 150 to 750 rpm. This spindle has been found with a 2.5" x 8 t.p.i. nose
|
|
|
|
|
|
|
|
|
|
 |
|
|
|
|
|
Headstock Type PLH. This used a nickel-steel spindle, hardened and ground and running in lapped and adjustable phosphor-bronze bearings. Like many similar precision lathes the pulley (to prevent belt pull interfering with the accuracy of the assembly) was supported in its own (ball journal) bearings with drive to the spindle though a peg.
|
|
|
|
|
|
|
|
|
|
|
|
|
|