 |
 |
 |
 |
 |
 |
 |
 |
 |
 |
 |
 |
 |
 |
 |
 |
 |
 |
 |
 |
 |
 |
 |
 |
 |
 |
 |
 |
 |
 |
 |
 |
 |
 |
 |
 |
 |
 |
 |
 |
 |
 |
 |
 |
 |
 |
 |
 |
 |
 |
 |
 |
 |
 |
 |
 |
 |
 |
 |
 |
 |
 |
 |
 |
 |
 |
 |
|
|
|
|
|
|
|
|
|
|
|
|
|
|
|
|
|
|
|
|
|
|
|
|
|
|
|
|
|
|
|
|
|
|
|
|
|
|
|
|
|
|
|
|
|
|
|
|
|
|
|
|
|
|
|
|
|
|
|
|
|
|
|
|
|
|
|
|
|
|
|
|
|
|
|
|
|
|
|
Introduced in 1938, and built until 1960, this was the most successful and widely sold large Rivett lathe of all time with some 2100 examples manufactured. Very similar in overall execution to the smaller 715 - and contemporary with it - the Rivett 918 (9" swing by 18" between centres) was described by the makers as reflecting 53 years experience of its builder. As the Company's first attempt at more modern, compact "bench precision" lathes (in comparison with the long-established No. 3, No. 4, No. 5 and newer 507 Types) both the 918 and 715 (the latter a smaller version of the 918) continued the tradition of providing very high-quality machines that could be fitted with a range of accessories to expand their usefulness as a miniature machining centre or repetition lathe. The design, obviously the result of careful thought by the patent holders Frederick Blanchard and Ralph Robbins, incorporated several novel features that enhanced both ease of use and essential maintenance. However, this was a crowded market, with very strong competition from a number of other American makers - including Hardinge, Wade, Stark and Ames* - and the number produced must have been relatively small. Model 918 Bed Of box-section form and strongly ribbed, the 39-inch long, 4-inch wide and 5.25-inch deep cast-iron bed was heat-treated (for stress relief) and formed as a rigid beam with, at the headstock end, an integral rectangular housing to which the separate headstock was bolted. Bolted down at the headstock end by through bolts onto cork pads (that sealed against coolant leaks into the cabinet) at the tailstock end the bed was retained by just a single bolt against a spherical, self-aligning washer. This arrangement (like that used on the English Raglan lathe and some other types) helped to guard against the assembly being pulled out of line and distorted. As a plain-turning lathe, there was no need for bed was to guide a sliding carriage, instead, like most other lathes of this type, a flat top was used together with bevelled edges and a central T-slot to ensure that headstock, carriage, tailstock and any other fittings would all remain in exact alignment. Headstock Enclosed in a particularly stiff, very modern-looking angular-style headstock (with three flat faces at the front compared with the two on the 715) the dynamically balanced spindle (made from a heat-treated alloy-steel) ran in high-precision ball races, a design change (from the usual plain bearings) that was also adopted during the 1930s on some contemporary models from other American makers including Ames, Wade and Hardinge. The front bearing assembly was constructed from a matched pair of races, set back-to-back and pre-loaded - while the single bearing at the rear was free to move and allow for expansion. All versions of the 918 are believed to have been fitted, from first to last, with sealed-for-life, grease-lubricated bearings. The all-important spindle nose was formed as an L000 version of the then popular and effective American long-taper key-drive type - the smallest "official" size being L00, This was a fitting that provided a robust and secure mounting and also allowed high speeds to be run in reverse with complete safety. Unfortunately, as with so many Rivett components, although the dimensions of the nose matched the standard fitting for L00, it is believed that a different thread pitch was used for the retaining ring. In order to stop the spindle rotating as fittings were changed (an important point often neglected by many makers) a locking pin was arranged to engage with a notched wheel at the left-hand end of the spindle. In order to ensure absolute concentricity between the spindle nose and its various fittings and collets, the headstock was first assembled and then locked to the bed (twin eccentric screws engaging in the bed's central T-lot). Once in place the usual trick of grinding the spindle mouth, chuck seat and tapered nose was adopted, the bed acting as a reference plane and mounting for the grinding head. Collets were retained by either a simple screw-type draw-tube or by a lever-action assembly, in each case end thrust being taken against a separate ball-thrust bearing. With a spindle able to pass a 1-inch bar, the maximum round collet capacity was 11/8", square 23/32" and across the flats of hexagon stock 7/8". Interestingly, the drive pulley was mounted outboard of the left-hand end bearing, a rather daring design for the time (though adopted post-WW2 by a number of precision lathe makers including Pultra, IME and on some Lorch models) that allowed certain advantages to be enjoyed. The headstock (being a closed box) remained immensely stiff and, by incorporating a circular opening around the end of the spindle, it was possible (having first removed the hand turning ring and collet-closing assembly) to change the drive belts without disturbing the bearings. Continued below:
|
|
|
|
|
|
|
|
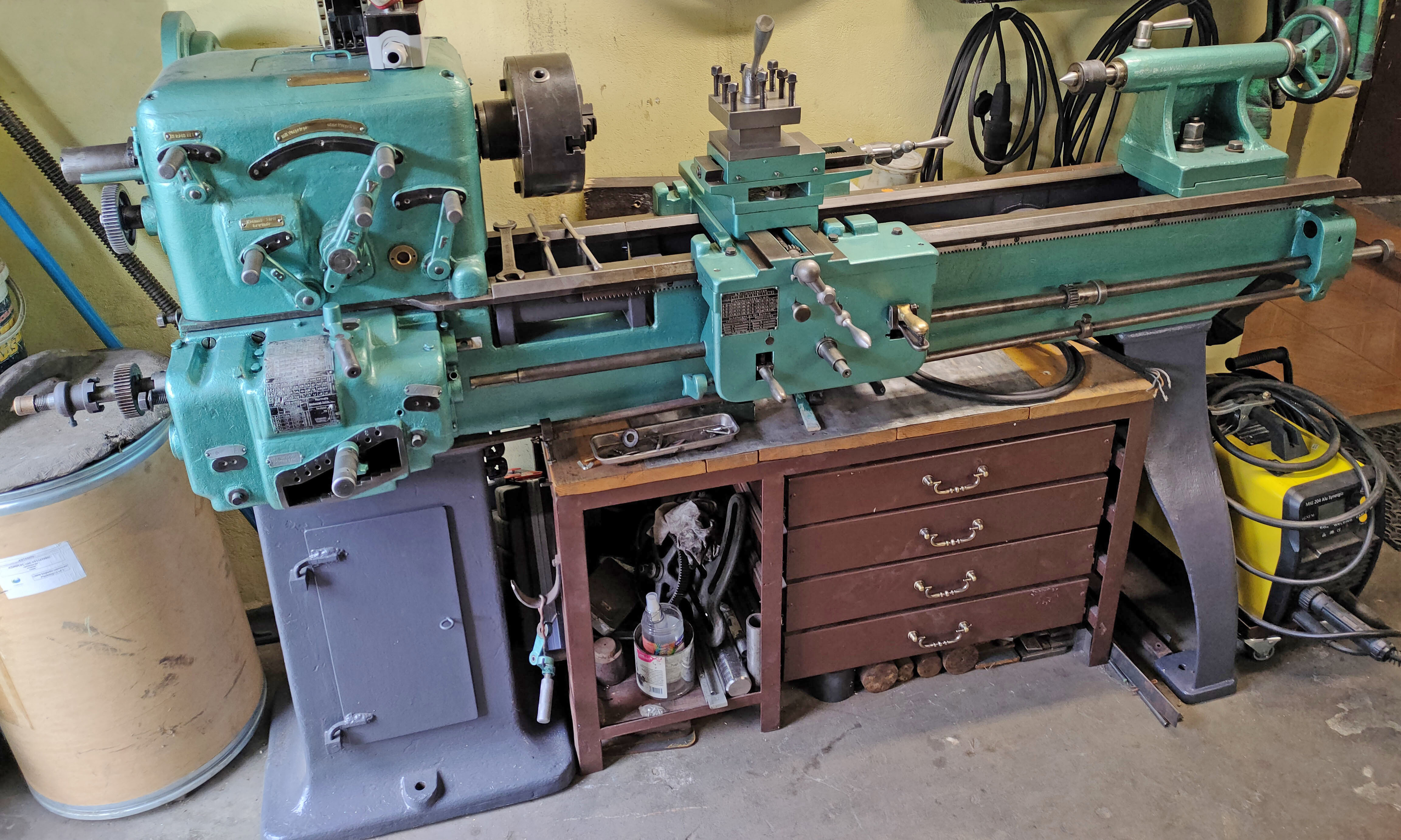 |
|
|
|
|
|
|
Basic Rivett 918 - bed, electrical controls, headstock, collet draw tube, catchplate, tailstock and clamp assembly to mount bed fixtures
|
|
|
|
|
|
|
|
|
Continued: Compound Side Rest Assembly Of conventional design (though the top slide T-slot was in steel and bolted on) the compound slide rest registered against the front bed bevel and featured the usual long-travel (5.25") exposed-ways top slide. Both feed screws were of Acme form, 7/16" x 10 t.p.i. (or, optionally, 2 mm pitch) with that on the cross slide (with 5.25" of travel) completely enclosed, so protecting it from the wearing effects of swarf and dirt. Balanced handwheels were fitted, the retaining screws, as on most other Rivett lathes, passing down the stem of the ball-ended section. Micrometer dials (13/16" in diameter) also followed Rivett tradition in being clearly graduated in 0.001" intervals (or 0.02 mm) and fitted with very effective and sensitive knurled-edge locking screws (protruding through the ends of the balanced handwheels) that did not cause the setting to alter when tightened. Long bronze feed nuts were fitted, though (surprisingly) neither could be adjusted to remove backlash. The cross slide was equipped with a screw-adjustable rear stop (that could be transferred to the top slide) to aid threading and repetitive production work while the top slide, fitted with a full-circle graduated degree disc, could be rotated through 360°. An "American" toolpost was used, held in a T-Slot, and able to take an Armstrong or similar brands of toolholder. Tailstocks Able to be set over for the turning of slight tapers, the No. 2 Morse taper tailstock mirrored the headstock in its use of clean, sharp-edged, very modern styling. With its outer end covered (an adaptation of the usual precision lathe design where this was left exposed) the hardened, ground and lapped 1.125-inch diameter spindle remained fully supported within the casting, no matter what its position. 3.5-inches of travel was provided, driven by Acme screw running through a bronze nut, with the casting cut away across its central section, to expose a finely engraved ruler scale 3.5-inches long graduated at intervals of 1/16". In addition - and fitted as standard - was a micrometer dial marked in divisions of 0.001" Stand and Drive System A choice of two stands was offered: a compact 45" x 24" all-welded, heavy steel-plate cabinet or a traditional open-type with a wooden top and cast-iron legs. The steel cabinet had an oil-pan top 53: x 21" x 1.75" deep (that drained into a 1.5-gallon sump) with two heavy-duty drawers both running on rollers and one having a collet-storage tray. Beneath the drawers was a locking tool and accessory cabinet and, to the left of that, a motor/countershaft compartment whose back wall was louvred for ventilation and removable to give access for maintenance. Electrical control gear was neatly contained within a separate chamber built into the left-hand face of the stand and fitted with an access door. Instead of being enclosed down to floor level, a space was left at the front, in the middle, sufficient for a seated operator to place his or her legs. As a final touch, at each end of the stand a pair of holes, fitted with blanking plates, was provided to take lifting hooks. With its structure braced by steel tie rods, the open stand was topped by a large 2.25-inch thick, 60" x 26" by 5-ply laminated wooden top with side and backboards. Also included were two locking wooden drawers, one fitted with a collet board. This stand was intended for laboratory and toolroom use - where it was necessary to mount the auxiliary motor unit and "overhead" to power high-speed grinding and milling spindles, or if space was needed for tools, small parts and sub-assemblies to be laid out and a trial fit of components made. Both stands used an identical drive system with a 2-speed 900/1800 r.p.m. motor, fitted with a 2-step V-pulley that drove to a matching pulley mounted on the rear of two shafts that extended from a simple clutch-gearbox unit bolted to the underside of the bench. Fitted to the output side of the rear shaft were high and low-speed pulleys that drove pulleys on the front shaft that were free to turn until locked by a sliding dog clutch. Continued below:
|
|
|
|
|
|
|
|
|
|
|
|
|
|
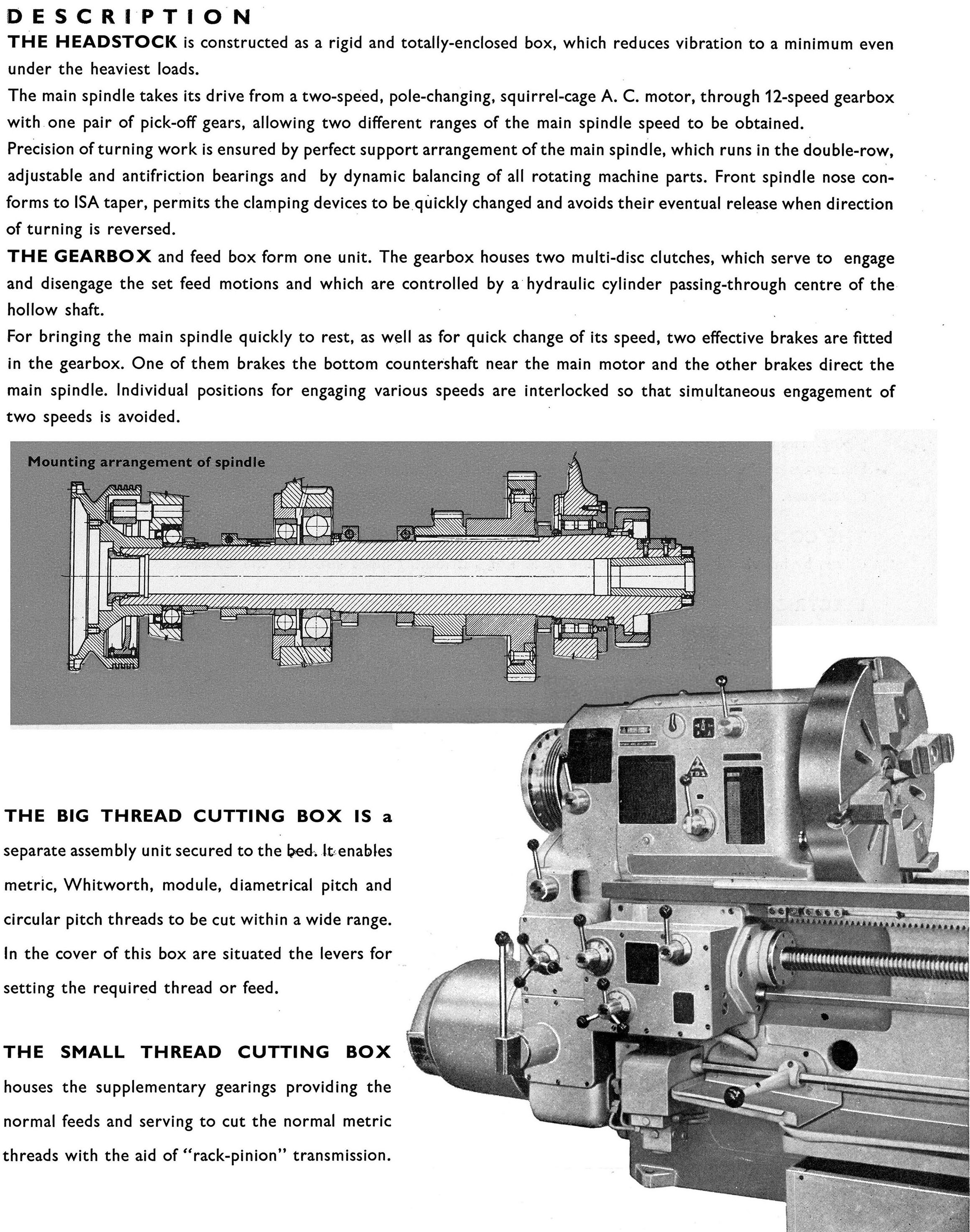 |
|
|
|
|
|
|
Rivett 918 precision plain-turning bench lathe
|
|
|
|
|
|
|
|
|
Continued: Final drive to the spindle was by twin V-belts, assembled as a specially matched pair. In order to allow a quick release of belt tension for speed changes the motor was mounted on a hinged plate controlled by a lever hinged on a bracket bolted to the front face of the stand's lower shelf. By this (relatively complex) means the operator could juggle belt and clutch lever positions to give eight spindle speeds that spanned a very useful 150 to 3500 r.p.m. To promote smooth, vibration-free running, all rotating parts were dynamically balanced and ran in self-aligning ball races. Usefully, in addition to individual screw adjustment for each belt's tension, all could be changed without any dismantling being necessary. With its use as a production lathe in mind, the electrical controls were more considerable more sophisticated than on the 715 - an automatic brake being provided that engaged whenever the control lever was moved to the central stop position. Combined with a pilot light (to indicate current on or off) the switch was moved to the right for high and low forward speeds and to the left for low and high reverse - a separate brake release switch being provided to allow the operator to turn the spindle by hand when the brake was on. In order to prevent burning of the switch, an electro-mechanical interlock prevented current from flowing until the finger contacts were in place. Sensibly, the makers made the switch handle of a decent size so that it could be gripped easily by an oily hand. Accessories A wider range of accessories was offered for the 918 in comparison with the 715 and, in addition to the usual wide range of collets, collet closers and centres, the expected T and triangular rests in various sizes (hinged and plain) for handwork, drive dogs, fixed and travelling steadies, a faceplate with radial T-slots and a saw table, Rivett also offered a number of more advanced extras. Amongst these more expensive items were attachments for chase screwcutting, slotting, changewheel screwcutting using the top slide, ball-turning, indexing and internal and external grinding and honing units (available with drive from either an "overhead" or a self-contained motorised drive assembly). A lever-operated tailstock for sensitive drilling; a revolving-spindle tailstock for the drilling of especially fine holes and lapping work (this required an overhead drive to give speeds of 6000, 8000 and 10,000 r.p.m. in reverse direction to the lathe spindle). An unusual design of milling attachment, almost certainly unique to Rivett, bolted to the bed in place of the compound slide rest. The unit consisted of consisted of a baseplate on top of which was a screw-controlled longitudinal slide able to be moved through 1.125" and swivelled through 360°. Mounted on the base and arranged vertically was a casting shaped to accept the ordinary compound slide rest (and indeed, other bed-mount fittings). This arrangement gave the assembly a wonderfully varied number of movements with its usefulness further increased by the availability of a large T-slotted table, an angle plate and machine vice. One important accessory - and a unit common to this class of lathe - was the Universal Grinding Attachment, a device that allowed the lathe to be pressed into use as small cylindrical grinding or honing machine for internal, external, parallel and taper work. Supplied complete, ready for mounting on the lathe bed, the assembly comprised a base plate, fitted with a 5-inch travel slide that could be swivelled through 360°. On top of this was a bearing housing carrying a hardened, ground and lapped spindle (with 2.5-inch of hand-fed travel) that could be hinged clear of the work (for measurement and inspection) and then dropped back into position without losing the previous setting. The spindle end was formed with a Pratt & Whitney No. 4 taper to mount grinding wheels and, using the 3-step pulley, could be made to run at 6000, 8000 and 10,000 r.p.m. in reverse direction to the lathe spindle. With both the lathe and grinding spindles on top speed, an effective maximum r.p.m. of 35,000 r.p.m. could be obtained, a figure high enough for all but the very smallest of work. Not listed, but almost certainly available if requested, was an attachment for the relief of cutters complete with its own drive pulley, gear set and a universally joined and splined shaft drive to the top slide. *Other American makers from the 19th and 20th centuries included: Levin, Bottum, American Watch Tool Company, B.C.Ames, Bottum, Hjorth, Potter, Pratt & Whitney, Rivett, Wade, Waltham Machine Works, Wade, Pratt & Whitney, Rivett, Cataract, Hardinge, Elgin, Remington, Sloan & Chace, W.H.Nichols, Crystal Lake and (though now very rare) Bausch & Lomb, Frederick Pearce, Van Norman, Ballou & Whitcombe, Sawyer Watch Tool Co., Engineering Appliances, Fenn-Sadler, "Cosa Corporation of New York" and UND..
|
|
|
|
|
|
|
|
|
|
|
|
|
|
 |
|
|
|
|
|
|
Rivett 918 arranged as a hand-screw (capstan) lathe
|
|
|
|
|
|
|
|
 |
|
|
|
|
|
|
Rivett 918 on one version of the neat, all-welded steel cabinet stand
|
|
|
|
|
|
|
|
|
|
|
|
|
|
 |
|
|
|
|
The three flat faces on the front of the headstock make for an easy recognition point
|
|
|
|
|
|
|
|
 |
|
|
|
|
|
|
The all-important spindle nose was formed as a miniature version (in effect an L000) of the then popular and effective American long-taper key-drive type, a fitting provided a robust and secure mounting and also allowed high speeds to be run in reverse with complete safety. Unfortunately, as with so many Rivett components, although the dimensions of the nose matched the standard fitting for L00, it is believed that a different thread pitch was used for the retaining ring.
|
|
|
|
|
|
|
|
 |
|
|
|
|
|
|
Smaller even than smallest (official) L00 American long-nose-taper spindle fitting, the Rivett version was a miniature copy - we might call it the L000
|
|
|
|
|
|
|
|
|
|
|
|
|
|
 |
|
|
|
|
|
|
Mounting the spindle drive pulley outboard of the left-hand bearings brought some advantages, for example, the headstock (being a closed box) remained immensely stiff and, by incorporating a circular opening around the end of the spindle, it was possible (having first removed the hand turning ring and collet-closing assembly) to change the drive belts without disturbing the bearings
|
|
|
|
|
|
|
|
 |
|
|
|
|
|
|
Of conventional design (though the top slide T-slot was bolted on and ) the compound slide rest registered against the front bed bevel and featured the usual long-travel (5.25") exposed-ways top slide. Both feed screws were of Acme form, 7/16" x 10 t.p.i. (or, optionally, 2 mm pitch) with that on the cross slide (with 5.25" of travel) completely enclosed, so protecting it from the wearing effects of swarf and dirt.
|
|
|
|
|
|
|
|
 |
|
|
|
|
|
|
|
|
|
The No. 2 Morse taper tailstock mirrored the headstock in its use of clean, sharp-edged, very modern styling. The hardened, ground and lapped 1.125-inch diameter spindle remained fully supported within the casting, no matter what its position. 3.5-inches of travel was provided, driven by Acme screw running through a bronze nut, with the casting cut away across its central section, to expose a finely engraved ruler scale 3.5-inches long graduated at intervals of 1/16".
|
|
|
|
|
|
|
|
|
|
|
|
|
|
|
|
 |
|
|
|
|
|
|
Cross slide lever-operated tailstock. This unit combined the action of a normal lever tailstock with 2.5-inches of cross feed and was intended for recessing, circular grooving, facing and slotting. On this model the spindle's 3.25-inches of travel was driven through rack-and-pinion gearing
|
|
|
|
|
|
|
|
 |
|
|
|
|
|
|
Standard lever-action tailstock for sensitive drilling
|
|
|
|
|
|
|
|
 |
|
|
|
|
|
|
Universal Grinding Attachment, a device that allowed the lathe to be pressed into use as small cylindrical grinding or honing machine for internal, external, parallel and taper work. Speeds of 6000, 8000 and 10,000 r.p.m. in reverse direction to the lathe spindle were available.
|
|
|
|
|
|
|
|
|
|
|
|
|
|
 |
|
|
|
|
|
|
Screwcutting with changewheel attachment - drive to the long-travel top slide was through a splined and universally-joined shaft. With the standard set of changewheels thirty-eight pitches could be generated from 10 to 108 per inch - including 11.5 and 27 t.p.i. By employing extra gears pitches as fine as 240 t.p.i could be cut. The gears were fully guarded and fitting the unit did not interfere with the lathe's normal operation.
|
|
|
|
|
|
|
|
 |
|
|
|
|
|
|
Chase Screwcutting Attachment - on a lathe like this ideal for batch production of fine threads on delicate components such as brass microscope and telescope tubes. Each "Master" thread (a large set was available) had a hardened hob on one end to allow the corresponding brass leadscrew nut to be re-cut. By using a set of changewheels pitches could be varied from one to six times that of the installed Master Thread
|
|
|
|
|
|
|
|
 |
|
|
|
|
|
A beautifully made ball-turning attachment - a fitting offered by surprisingly few makers. The unit could produce both concave and convex surfaces up to a maximum diameter of 3"
|
|
|
|
|
|
|
|
|
|
|
|
|
|
 |
|
|
|
|
|
|
Indexing Attachment and bed-mounted Slotting Attachment. The index plates were carried on the outer of the headstock spindle and the index unit fitted to a bracket that bolted to the left-hand face of the headstock casting. Plates with divisions of 45, 56, 60, 64, 72, 80, 84 and 100 divisions were available - with others available to special order. The Slotting Attachment (of a design as used for many decades on Rivett lathes) was intended for the cutting of keyways, slots and holes of odd contour. By combining its use with the indexing attachment, and suitable tools, holes of square, hexagon and other shapes could be produced. The tool holder, intended to take round bits of 5/16" diameter, had 1.125" of vertical screw adjustment with a secondary adjustment for rake. The cross slide travel was 2 inches.
|
|
|
|
|
|
|
|
 |
|
|
|
|
|
|
Self-contained motorised toolpost grinder adaptable for both internal and external work
|
|
|
|
|
|
|
|
 |
|
|
|
|
|
|
Internal grinding spindle
|
|
|
|
|
|
|
|
|
|
|
|
|
|
 |
|
|
|
|
|
|
An unusual design of milling attachment, almost certainly unique to Rivett, bolted to the bed in place of the compound slide rest. The unit consisted of consisted of a baseplate that clamped to the bed on top of which was a screw-controlled longitudinal slide able to be moved through 1.125" and swivelled through 360°. Mounted on the base and arranged vertically was a casting shaped to accept the ordinary compound slide rest (and indeed, other bed-mount fittings). This arrangement gave the assembly a wonderfully varied number of movements with its usefulness further increased by the availability of a large T-slotted table, an angle plate and machine vice.
|
|
|
|
|
|
|
|
 |
|
|
|
|
|
 |
|
|
|
|
|
|
|
|
|
Angle plate and small machine vice in position
|
|
|
|
|
|
|
|
|
|
|
|
|
|
|
|
 |
|
|
|
|
|
|
|
|
|
A miniature boring head in use with the work clamped using the traditional method of T-bolts and spacers
|
|
|
|
|
|
|
|
|
|
 |
|
|
|
|
|
|
|
|
|
Automatic Universal Slide Rest. This very unusual accessory was designed for the repetition manufacture of small tapered parts such as needle valves, metering pins and for parallel turning where the cut ran out to a recess. The operation was entirely automatic and duplicated exactly on every component. By using tungsten or diamond-tipped tools - and using high spindle speeds - it was possible to obtain a very fine surface finish and extreme precision. A self-contained unit, it bolted to the bed in the usual way and was driven by a 1/20 h.p. motor mounted on a bracket at the rear of the rest with the drive passing through a set of pick-off gears by which means the rate of feed could be varied. In use the cutting tool was raised to its working position by depressing an operating handle; this movement engaged the power feed which then traversed for the pre-set length of cut. With the cut complete, the tool holder dropped away from the work automatically and was instantly retracted to its starting position.
|
|
|
|
|
|
|
|
|
|
|
|
|
|
|
|
 |
|
|
|
|
|
|
|
|
|
|
|
|
|