 |
 |
 |
 |
 |
 |
 |
 |
 |
 |
 |
 |
 |
 |
 |
 |
 |
 |
 |
 |
 |
 |
 |
 |
 |
 |
 |
 |
 |
 |
 |
 |
 |
 |
 |
 |
 |
 |
 |
 |
 |
 |
 |
 |
 |
 |
 |
 |
 |
|
|
|
|
|
|
|
|
|
|
|
|
|
|
|
|
|
|
|
|
|
|
|
|
|
|
|
|
|
|
|
|
|
|
|
|
|
|
|
|
|
|
|
|
|
|
|
|
|
|
|
|
|
|
|
|
|
|
|
|
|
|
When, in September 1934, Cecil Moore founded the Myford Engineering Company and rented a spare room in a 5-storey lace mill in Beeston, Nottinghamshire (the address in early sales sheets was given as Neville Works) few could have foreseen the day when, 10 years later, he was to occupy all but a fraction of the same building. The foundation of this success - and his Company's rise to pre-eminence amongst the then many competing makers of small lathes - was a range of just four machines: the ML.1, ML.2, ML.3 and ML.4, all designed and priced to appeal to the model engineer with the ML1 and ML3 being the cheaper, less-well-specified versions. Each version was of identical general arrangement, lightly built, using a "cantilever" bed of box-form section with flat-topped, 60 deg. edge ways. . With a standard-fit 6 : 1 ratio backgear they did not differ greatly in quality or accuracy from any number of other pre-WW2 competitors*. However, despite their limitations of size and strength, the machines proved immensely popular and the Myford Company, based on their reputation of offering value-for-money accuracy and a wide range of accessories, went from strength to strength to emerge as the pre-eminent maker of small lathes in the UK. Because of their very similar appearance and the confusing foundry marks - A1, A2, B1, B2 (etc.) sometimes found cast into their beds - recognition of a particular version by those unfamiliar with the model can be difficult (though a close reading of this article should help). The first known catalogue makes no mention of a Model type, just the Myford 3-inch at £6 : 7s 6d. However, this single lathe was to develop first into the ML.1 and ML.2 (Myford Lathe 1 and 2) both with a 31/8" centre height and admitting 15" between centres and then, a little later, into the 31/2" x 24" models ML.3 and ML.4. The ML1 and ML2 could swing 8.5" in the gap, the ML3 and ML4 a rather more useful 9.25". Both ranges were built from the early 1930s until, in 1941, instructions were received from the (war-time) Government's Machine Tool Control Rationalisation Board to stop production and take over from Drummond (busy with the important Maximatic production lathes) manufacture of the Armed Services' standard small lathe, the M-Type. The official directions relating to Myford's own lathes were undoubtedly cancelled for, although sales literature printed during 1939 (and distributed during 1940 and 1941) had stamps over the ML.1 and ML.3 entries stating: This type withdrawn for duration of war, later brochures listing the ML2 and ML4 continued to be produced. A catalogue for the latter types appeared in November 1941 and another (with 7,500 printed) in March 1943. The 1941 publication contained an official Machine Tool Control Price List and repeated the news that, for the duration, (of the war) the basic ML.1 and ML.3 types would be withdrawn from sale. According to a letter written by the Sales Department in September 1946, it was intended that production of the ML.2 would resume in the late summer of 1947 and the ML.4 a little later. Indeed, in October 1945 the company had a thousand copies of a redesigned ML2 and ML4 catalogue - together with a further one thousand in January 1946. Further confirmation of the intention to restart manufacture after the war came in May 1946 when a small, eight-page catalogue was issued showing the ML2, ML4, M-Type and the ML7 - with entries for the ML2 and ML4 marked: Not yet back in production; unfortunately no date can be given at the moment. However, very shortly afterwards, the new ML7 was given its first two dedicated catalogues: one was a simple, very small folded sheet with a single picture and the basic specification, the other, more substantial and over-stamped Provisional. Printed in the same A5 landscape format used for earlier ML2 and ML4 publicity material its card cover was dark-blue with the single word Myford (in the company's traditional script) picked out in gold. The pages were typed, reproduced on a Gestetner, and contained just one photograph showing the lathe mounted on its special "octagonal-form" braced sheet-steel cabinet stand. So, in 1946, with the factory fully occupied building the new ML7 (and with materials of all kinds still in very short supply and production of the M-Type continuing as well) the option of starting ML2 and ML4 production was almost certainly never taken up. However, that is not to deny some examples might have been constructed - and it remains a possibility that a number were constructed from spares for those with the "right connections" - so enabling them to avoid the cripplingly-long 60 to 100-week waiting list for both M-Type and ML7. Although by 1938 the ML.2 and ML.4 models were being listed as Superior (at £8 : 5s : 0d and £10 : 9s : 0d ) - and the ML.1 and ML.2 as Standard - (at £7 : 0s : 0d and £9 : 10s : 0d ) the precise specification of the latter could only be deduced, from the maker's literature, by what was omitted relative to the former. However, two important differences were that early versions of the ML.1 and ML.3 (until approximately 1941) appear to have been made with the headstock and bed cast "as-one" while the ML.2 and ML.4 both had a bolt-on headstock - at first with the front pair of securing bolts having their nuts at the top (very rare) but later underneath. In addition, the separate headstocks usually had a curved section, beneath the left-hand bearing, that could be machined to mount the optional tumble-reverse assembly. Other known differences were that the ML.2 and ML.4 had a shrouded ball-thrust race to the spindle - that ran in bronze bearings and not direct in the headstock casting as on the ML.1 and ML.2 - a 7-inch long cross slide with 4.5 instead of 3.5 inches of travel and a quick-action lever instead of a nut to release the tailstock clamp. By 1943 the flat cross-slide end plate had been change for a step-out one that resembled those to be fitted on the later ML7 - this new fitting enabling the slide to move inwards by an extra inch or so and so become rather more useful when using a vertical milling slide; unfortunately this fitting is hardly ever found, the writer having seen only a couple of examples. Incidentally, the run-direct-in-the-headstock spindles tend to last far longer than the bronze type that was a simple, but ineffective marketing ploy. Although it's rare to find an early ML1 or ML2 with bed and headstock cast as-one with tumble reverse with the bed cast to take a tumble reverse assembly, they do exist. Even so, it's rare to find one fitted with the mechanism - though they do exist and some may have been retro-fitted by keen owners - example of the type, almost certainly a factory job, can be found at the bottom of the page. By 1939 (though it may have been available earlier) a tumble reverse mechanism was being listed (for the ML2 and ML4 only) at 10 shillings extra, or, if combined with the optional 5/8-inch bore spindle with a No. 2 Morse taper, £1 : 5s : 0d. At the left-hand end of the headstock spindle the method of attaching the gear differed according to whether or not tumble reverse was fitted: on non-tumble lathes (i.e. with a small diameter spindle) it was simply pushed on and connected to the shaft by a small pin passing into the face of a drive collar secured with a grub screw, this method allowing it to be changed in order to assemble the gear train necessary to generate the required thread pitch. On tumble-reverse equipped lathes the gear had to be set at a precisely fixed distance from the tumble gears and, in effect, become a semi-permanent fixture. To achieve this Myford (thankfully) avoided forming the gear as part of the shaft but instead made it a close fit on the (turned-down) end with a screw inserted longitudinally between gear and shaft (a method also employed on the ML7) so making it removable (with care). However, if you have an ML4 without tumble reverse - and regardless of whether it has the large or small bore spindle, the assembly as fitted to an ML7 can be grafted on (though the writer cautions that he not done this job himself, but seen examples - one is shown below and here - where the modification has been carried out successfully). Changewheels (20 D.P. and 14.5-degree pressure angle like those on the later 7 Series lathes) drove down to a 5/8" diameter, 8 t.p.i. leadscrew with its square thread clasped by cast-iron nuts running in short, V-edged guides fitted with adjustable gib strips. By 1943, in a rationalisation of production, the tumble reverse and larger spindle appear to have become part of the ordinary specification. Lathes with the smaller 1-inch diameter spindle carried a 7/8" diameter 9 or 12 t.p.i. thread while the larger were equipped with the same 11/8"12 t.p.i thread used on the post-war ML7 - though some examples of the latter have been found without the step-up register behind the thread as found on all 7-Series machines. Both spindles were bored through 19/32". Although modern-style V-belts had been available from just after WW1 (and used on small machine tools from around 1931 in the U.S.A.all early Myford lathes used a 0.75-inch wide flat belt running over a 3-step cone pulley (with diameters of 2.375", 3.125" and 3.875") - though occasionally machines with a 2-step pulley are found that take a 1-inch wide belt, this being a set-up originally offered for use on capstan-equipped models. By the late 1930s, for a mere two shillings and sixpence extra, a V-pulley could be ordered instead - and then finally, in 1943 when the ML.4 was fitted to the late-type 12-speed, all-V-belt-drive stand, it became part of the standard specification. Continued below:
|
|
|
|
|
|
|
|
|
|
|
|
|
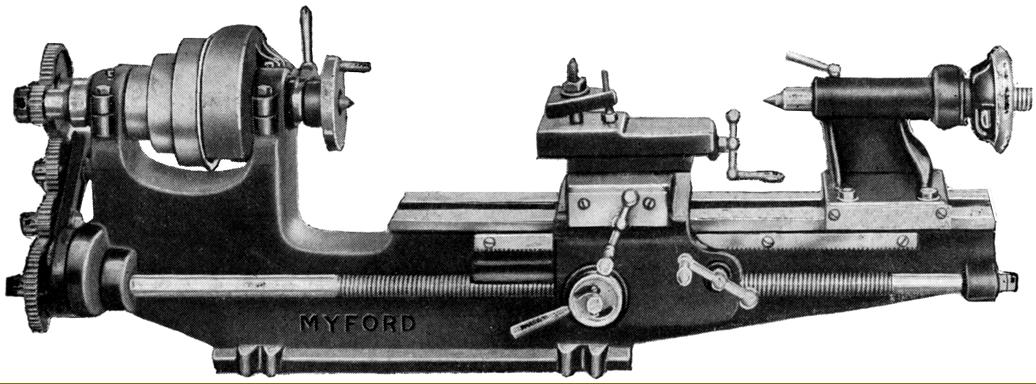 |
|
|
|
|
|
|
Cheapest of the early Myford lathes was the 31/8" x 15" ML1 with bed and headstock cast as one. This art-worked picture, though used in a 1938 catalogue , shows the lathe as sold from early 1935 with a single-bolt retained top-slide, cast-in leadscrew bearings and the very early tailstock side plate without adjuster screws. Note the headstock front face - there is no provision to mount a tumble-reverse mechanism - and the extra changewheel protruding above the centre line of the headstock - this was fitted to a forked bracket and allowed left-hand threads to be generated.
|
|
|
|
|
|
|
|
|
Continued: Like many contemporary small lathes the guarding of belts and gears was either rudimentary, or non-existent. However, by the late 1930s, several designs of changewheel cover appeared, obviously in search of a simple but economical solution and at first were offered as an option - 7/6d buying the first type, a rather crude hinge-up affair that lacked an inner cover. This was replaced by an assembly that used a cast-iron plate bolted to the end of the bed, with the cover located by a dowel at the back and a knurled thumb screw at the front (an arrangement similar to that used on ML7). Finally, but very rarely found, from 1943 onwards a cover was fitted (together with an inner guard plate) that hinged open in the manner of that fitted to the Super 7. Although the later division of the range into Standard and Superior models brought a choice of a spindle running directly in the cast iron of the headstock (an excellent situation if the spindle is hard and carefully finished) or bronze bearings, the early (very rare) catalogues failed to mention that for 10 shillings extra (in 1937) this option was available then. However, one owner of a new ML.4, purchased in 1937, reported to the writer that, because he found the headstock bearing housings to be roughly finished, alignment had to be obtained by pressing the bushes in and then boring them true. While this method might have been an excellent expedient to quick and easy production, it did nothing for the owner who subsequently wished to replace the bearings - just fitting new bushes resulted in hopeless misalignment of the spindle. The bearing housings were "split" on one side with a pinch bolt to provide a form of initial adjustment - care must be taken not to over-tighten the clamping screws as the assembly wears and it is very easy to snap the headstock casting - an effective repair being both difficult and expensive. If the "split" bearings on your early Myford (or other small lathe) are worn, it is much better to bite the bullet and have the spindle hard chromed, ground to size and a new pair of bearing made up and carefully bored true by your local precision engineer. In the 1930s, when money was tight, many lathes were sold without countershafts, the owners preferring to construct their own from handy scrap. If you were lucky enough to be able to afford the real thing Myford offered two basic units for bench mounting: a simple, non-adjustable affair and a rather superior one, not dissimilar in function to that offered for the 6-inch Atlas in the USA. The better countershaft resembled a tall angle plate, slotted for motor mounting and with a separate hinged top (tensioned by an over-centre, lever-operated cam) that held a pulley with its shaft rotating in cast-iron bearings located by pairs of opposing screws that allowed then to become "self-aligning". Continued below:
|
|
|
|
|
|
|
|
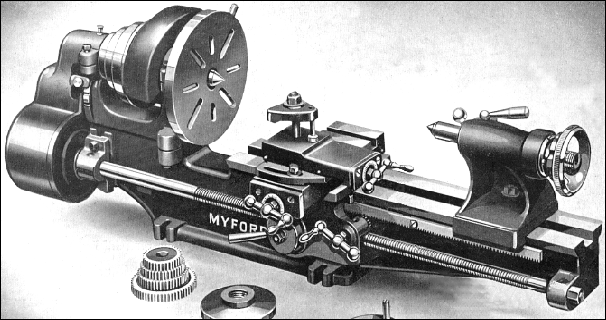 |
|
|
|
|
|
A very late Myford ML.2 with the headstock and left-hand leadscrew support bracket both bolted on. The top slide had a bolt at the front as well as the back, tumble reverse was fitted, as were graduated dials on the compound slide-rest feed screws. The changewheels were completely enclosed by a bolt-on cover and backplate - both in cast iron. In this publicity picture the tailstock has been art-worked to resemble the later, much-improved type.
|
|
|
|
|
|
|
|
|
Continued: Every ML.1, ML.2, ML.3 and ML.4 had a carriage of similar construction with a simple, lightweight apron secured to the saddle by two slotted-head screws and a direct rack-and-pinion drive - a small movement of the handle producing a disproportionately long travel of the cutting tool together with a "cack-handed" operation i.e. turning the handle to the left produced a carriage movement to the right - a situation easy enough to get used to when just one lathe is in use, but potentially disastrous when another of conventional arrangement was in the same workshop. To ease this problem the makers offered a handwheel for the leadscrew end by which means the carriage could be advanced more slowly and a steadier cut taken. All versions were given a useful T-slotted cross slide (shorter on some but not all examples of the ML1 and ML2) and a 3.25-inch travel swivelling top slide with, on early lathes, a simple etched micrometer dial (with its 80 divisions giving a slightly inaccurate 0.96 thou per division) fitted to just the cross-slide feed screw - although very occasionally an original lathe is found where the owner must have pushed out the boat and ordered one for the top slide as well. Later lathes, from an indeterminate date, appear to have been fitted with both dials as standard. The slides (which were hand scraped and fitted only by experienced slide fitters) carried square-thread feed screws of 12 t.p.i. with proper balanced ball handles; unfortunately the screws, instead of running through replaceable nuts, ran directly in the saddle casting making replacement awkward. Retained by just a single stud that passed through its pivot point, the first lathes had a top slide that was insufficiently rigid and the familiar curved slot on the front, to provide an extra clamping point, must have been introduced very quickly judging by the very few examples of the first type encountered. Although dating a Pre-war Myford with any degree of precision can be difficult, other pointers to early machines include a very short guard over the spindle bull gear, a lack of knurling on the tailstock handwheel and a tailstock side-plate without the gib-adjustment screws. Continued below:
|
|
|
|
|
|
|
|
|
|
|
|
|
|
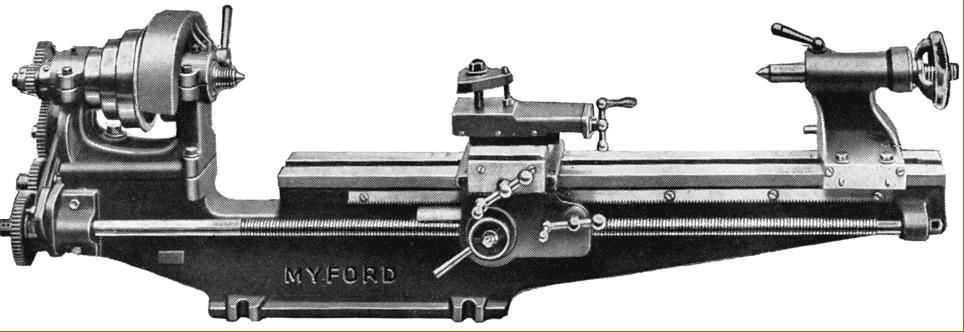 |
|
|
|
|
|
|
1938 3.5" x 23" ML.3. Another advertising picture created by art working pictures of earlier versions. Note the bolt-on headstock with front retaining nuts on top, the lack of tumble reverse, the top slide still held by just one bolt (at the back) - and the new and improved tailstock side plate recognisable by the four screw heads.
|
|
|
|
|
|
|
|
|
Continued: As a point of interest, the writer has seen many examples of early Myford lathes where an owner has attempted to engage backgear by disengaging the bull-wheel from the spindle; unfortunately this wrecks both gear and spindle and the correct method is to release the pulley from the spindle (look for a grub screw through the smallest-diameter pulley or the end boss). By far the weakest part of any early Myford lathe was the tailstock with its 8 t.p.i. square-thread, 3-inch travel spindle: the first design had no horizontal "gib-type" setting screws on the side plate though later ones (the majority) were so equipped and allowed the plate to be accurately set whilst the two vertical clamp bolts were fastened. Unfortunately, on both types, tightening the nuts or operating the lever to clamp the tailstock to the bed caused the plate to flex and the in-line setting to be lost. In fact, so poor was the original tailstock that Myford, just post WW2, issued a sales leaflet extolling the virtues of a much-improved (and expensive) replacement. However, one good point about all Myford tailstocks, both old and new, was (and is) the locking arrangement provided for the barrel. Unlike the horrid slit in the casting, closed down by a bolt that has featured on so many other inexpensive (and occasionally expensive) machines, all Myford lathes have a proper split-cylinder clamp that acts directly on the barrel - and with its mounting stud screwed deep into the casting. Two stands were produced, early and late, both of cast-iron construction. The older model - lightly built and easily recognised by the large decorative letter "M" cast into each leg - was sized differently for the 3.125 and 3.5-inch lathes. It could be had as a plain assembly (in 1939, for the ML2, it cost £3 : 0s : 0d) or complete with either a treadle-and-flywheel drive or a rather clumsy, cast-iron countershaft that bolted to the underside of the chip tray with the drive section cantilevered backwards behind the headstock. Although the fully-motorised stand was just £5 : 13 : 6d this represented an almost 50% increase in price over the basic unit and more than half the price of a basic ML2 - no wonder that, today, so few are found. Not helped in the least by hanging the motor from a thin bar between the stand legs (with no tensioning arrangement) the flat-belt drive from motor to countershaft was utterly hopeless. Although today, with a modern endless belt fitted, it is not necessary to alter the headstock drive to a V-belt, the drive from the motor is definitely a candidate for change. The later stand, from 1943, was of very more substantial construction and, with its deep chip tray and three sheet steel shelves resting on cast-in plates was, in effect, a miniature version of that superb design used by Myford on their version of the Myford/Drummond M-Type. The tall countershaft assembly, also a smaller replica of the type used on the M-Type, was heavily constructed and pivoted from a plate bolted to the back of the headstock end leg; fitted with double-step motor and top pulleys (and in conjunction with backgear) 12 all-V-belt-drive speeds were available. Locked tight by an over-centre lever, the tension of the headstock drive belt could be finely adjusted by a left-and-right-hand threaded turnbuckle - a system still used years later on the ML10. Unfortunately the only ML.1, ML.2, ML.3 and ML.4 parts that can be replaced by those from an ML7 are the screwcutting changewheels, the complete 6 : 1 ratio tumble reverse assembly and (thinned down) the backgear "Cluster" - the pair of gears carried on an eccentric shaft at the back of the headstock on the older machines and under the spindle on the ML7. If the lathe is a late-model ML4 with a 1.125" hole through its bullwheel this item can also be adapted, again thinned-down a little, from that used on the ML7. The changewheels, which ran directly on their studs, when assembled in pairs as part of a compound drive train were joined by tiny pins (in silver steel) 3/32" in diameter and 3/8" long. Although the ML7 and Super 7 changewheels are the same D.P. as the ML1 to ML4 type, they are mounted in a much-improved way, with the centre of each gear accepting a keyed bush that turns on a hardened stud. This vastly improved system is one that can easily be adapted - with a little judicious filing of the banjo slot - to work on the early lathes. If necessary the later gears can be run on the original plain studs, but the additional cost of the keyed units is so small - and the improvement in the drive so great - that this should not be considered. To use existing changewheels on new studs means filing a keyway in them, a job eased by buying a good quality square-section needle file just a little smaller than the size of the finished slot. As a sign of lax quality control, some changewheel brackets have been found with the faces at each side of the long slot left as-cast - the uneven surface causing the gears to tilt over when their studs are tightened; the only solution is to have each side of the bracket ground or milled flat. Because the (stronger) ML7 tumble-reverse assembly is a direct replacement for the (flimsier) unit used on the ML4, there seems to be no good reason why a lathe without this facility could not retro-fitted with it - though care would be needed in positioning the mounting stud and marking out the indent positions for the location plunger. If the cast-in fork at the back of the headstock puzzles you, this was used to carry an extra changewheel to provide a reversal of the leadscrew drive and so cut left-hand threads. Most ML.1 to ML.4 lathes were supplied as standard with a 6.5" diameter faceplate, ten changewheels (together with two mounting studs, two driving collars and a distance washer) a chuck backplate and two Morse taper centres in tool steel. Myford lathes of the early 1930s were painted black, but at some point towards the middle of the decade the makers switched to what they described as a "grey/blue" finish but which, in fact, resembled a dreadful shade of "vomit green." A wide range of useful accessories was listed for all types including a very rare "foot motor" (a self-contained, treadle-powered 56 lb flywheel and flat-belt cone-pulley assembly) for bolting under the owner's own bench, cast-iron stands that varied from the flimsy to the robust, countershafts for bench, stand and ceiling mounting, plain and swivelling vertical milling slides (though these were much lighter in construction than those for the later 7 Series lathes) travelling and fixed steadies (the latter of the slenderest proportions) machine vices, V-blocks, thread-dial indicators, a wood-turning hand rest, 4-way toolpost, saw table (very rare) plain and V-drill pads for the tailstock and extra changewheels: 127t (for metric translation) and 38, 64, 70, 75, 80, 85, 90, 95 and 100t to extend the threading range. The lathe could also be adapted for light production work with the makers offering a cut-off slide and 4 and 6-hole bed and cross-slide mounted capstan heads. In addition, a number of ML2 and ML4 lathes were sold ready-converted with capstan equipment - while during WW2 (under pressure to make the most of all productive industry) a surprising number of other types, all branded as being variants of the ML6, were more seriously developed using different beds, headstocks and drive systems. Further details of Myford production lathes can be found on lathes.co.uk in the Myford section of the Archive. It's interesting to note that a version of the ML.4 continued in production until the early 1980s in the guise of the Perfecto in the UK, the Advance in Australia and the VLG in Sweden, though in the latter two case only until (it is believed) the late 1950s or very early 1960s. All three versions sold into a niche market that offered enthusiastic amateurs the chance of a new, good-capacity small lathe at a price considerable below that of the (admittedly far-superior) ML7. Surprising numbers of ML2 and ML4 lathes are still in use, to perform particular tasks, heavily modified by their owners - or just as an engineering exercise for their own sake. However, many are now seriously worn and little better than a rotary file, though some model engineers are able to produce the most amazing work on them and many have been ingeniously rebuilt. Myford have no spares for the ML1 to ML4 range and, unfortunately, cannot supply any written or illustrated material about them. Instead please contact tony@lathes.co.uk for details of an interesting literature pack. In order to obtain an idea of the rapid development of lathes for the amateur market during the 1930s, it is instructive to look to America where Atlas were offering the 3-inch centre height Model 6-inch, a mass-produced machine whose neat design and comprehensive guarding may well have inspired several features used on the post-war ML7. A comparison of these models, and their drive systems, makes for interesting reading. *Pre-WW2 the most popular English makers of small lathes for the amateur market included, amongst others: Adept, Britannia, Corbett's, Drummond, ETA, EXE, Granville, Grayson, Holmes, Ideal, Mellor, Patrick, Pools, Portass, Randa, Relm, Wade-CAV, Winfield and Zyto. Tony Griffiths
|
|
|
|
|
|
|
|
|
|
|
|
|
|
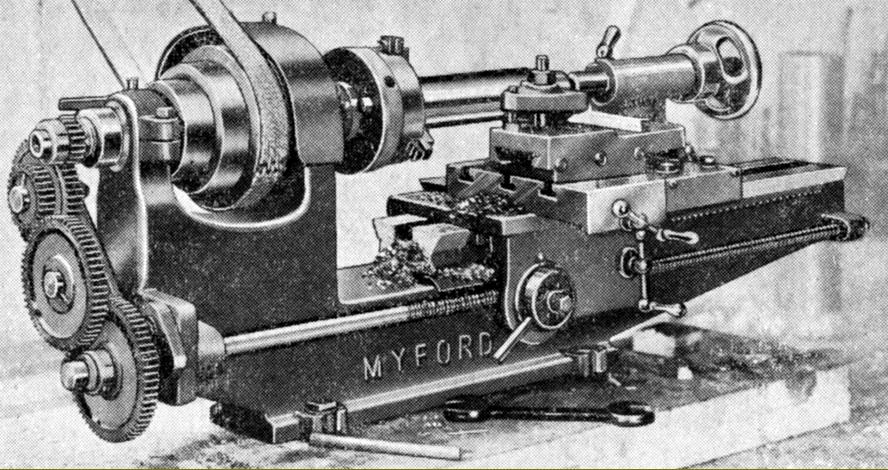 |
|
|
|
|
|
|
Myford ML.1. A heavily retouched illustration from the earliest-known catalogue.
|
|
|
|
|
|
|
|
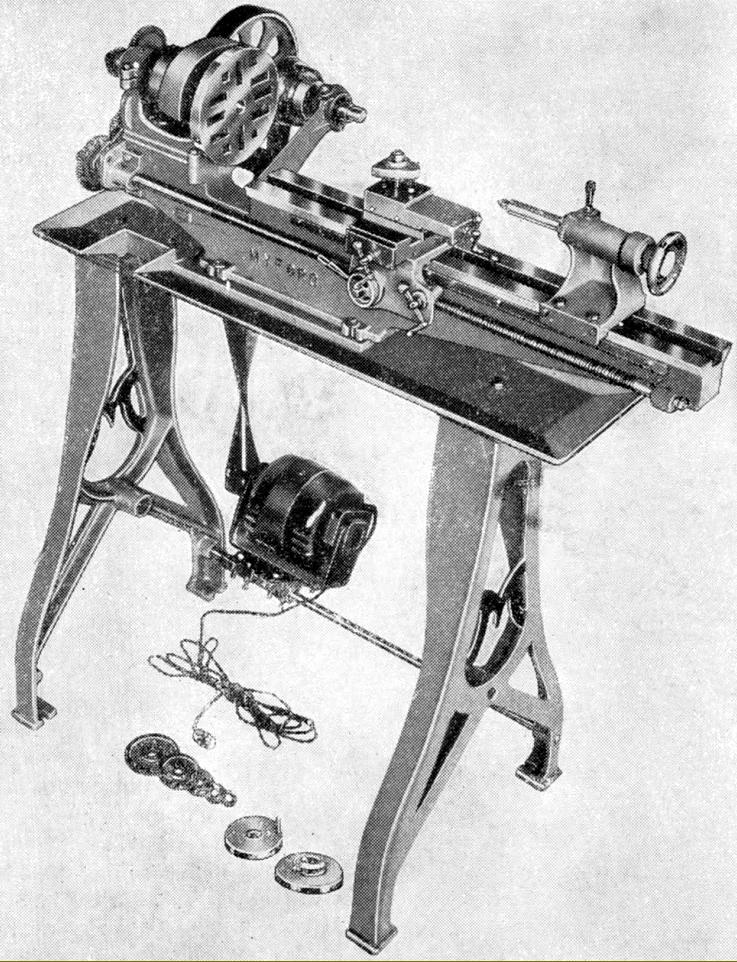 |
|
|
|
|
|
|
Of light construction, the early stand is easily recognised by a large decorative letter M cast into each leg. The unit could be fitted with either a treadle and flywheel drive or, as shown, with a motorised countershaft (of clumsy design) that bolted to the underside of the chip tray with the drive section cantilevered backwards behind the headstock. Not helped by simply hanging the motor from a thin bar between the stand legs, the flat-belt drive from motor to countershaft was, in practice, an utterly hopeless arrangement.
|
|
|
|
|
|
|
|
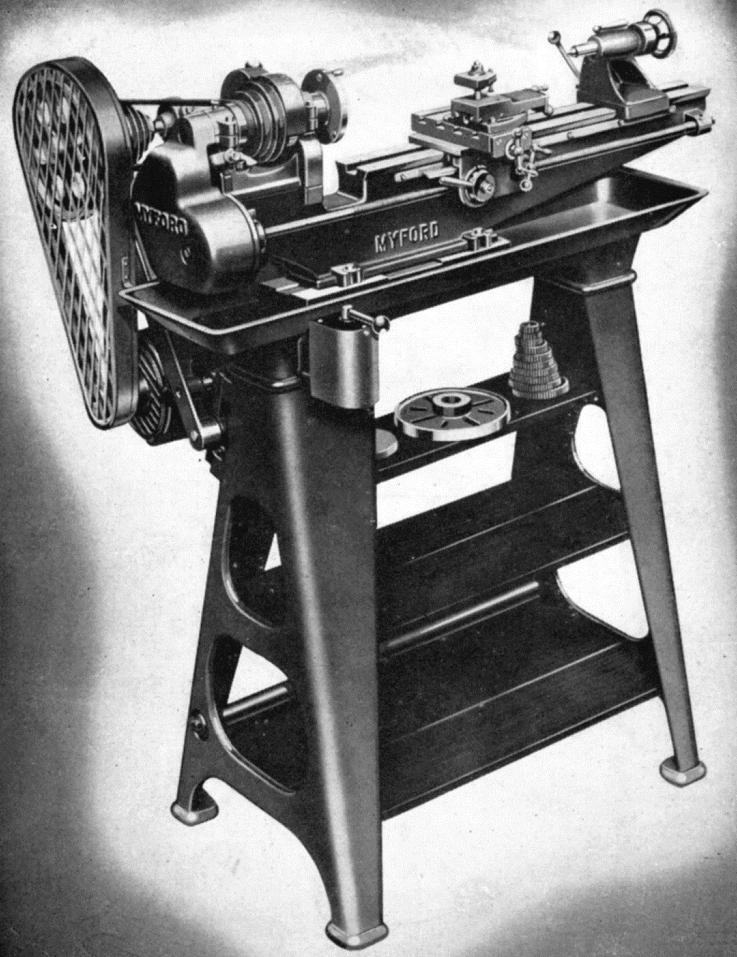 |
|
|
|
|
|
The final, most effective version of the ML.4 as built from 1939 to 1942. It was fitted to a greatly-improved all-V-belt drive stand with 12-speeds from a built-on countershaft, 3 shelves, wiring conduit and a Dewhurst reversing switch. This assembly was, in effect, a miniature version of that used on the Myford/Drummond M Type. The unit could also be ordered with flat-belt drive - though the writer has yet to see one so equipped.
|
|
|
|
|
|
|
|
|
|
|
|
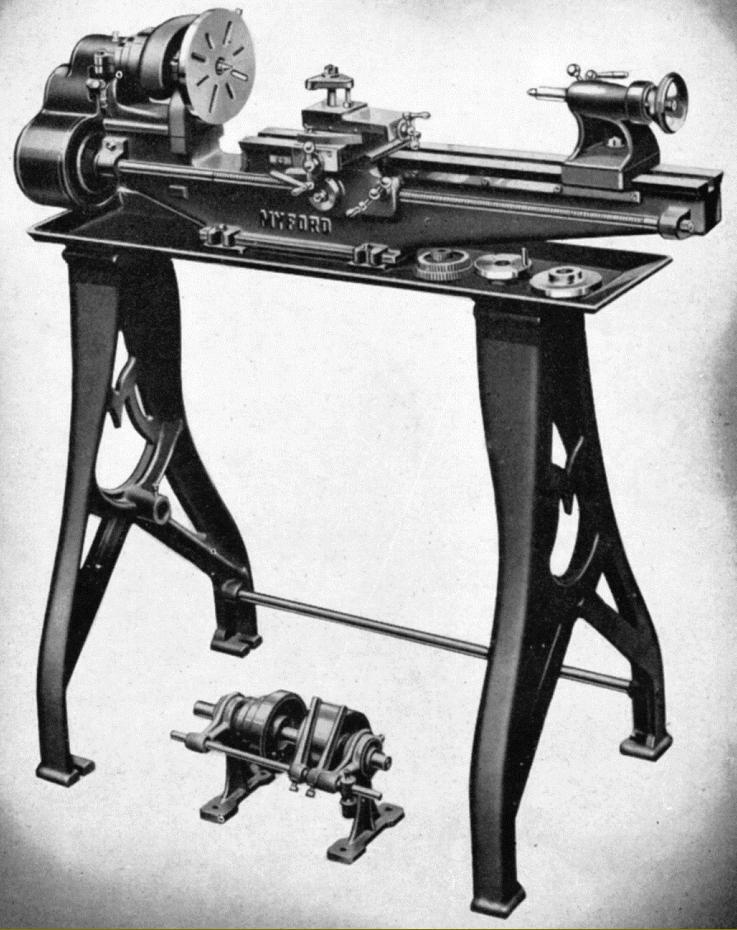 |
|
|
|
|
|
|
Basic stand with countershaft for wall or ceiling mounting
|
|
|
|
|
|
|
|
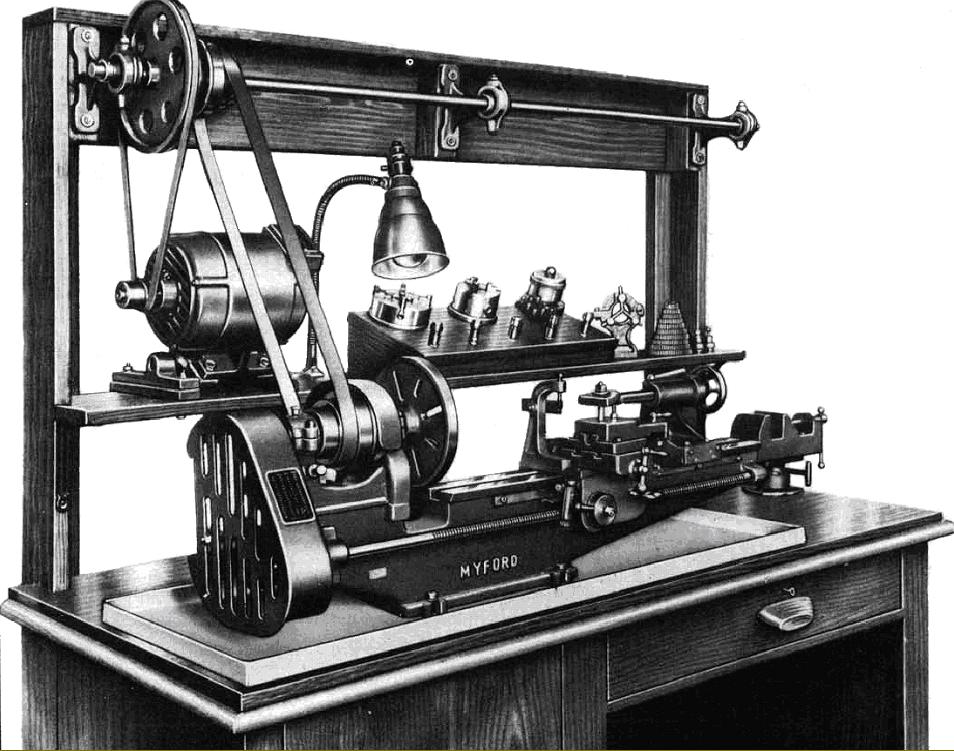 |
|
|
|
|
|
|
Never available from the factory - but Myford's idea of the perfect installation for an early ML2/ML4. Although there is no way of easily adjusting the tension of the headstock drive belt, the motor is fitted mounted on a frame that allows it to pivot - its weight applying the required tension
|
|
|
|
|
|
|
|
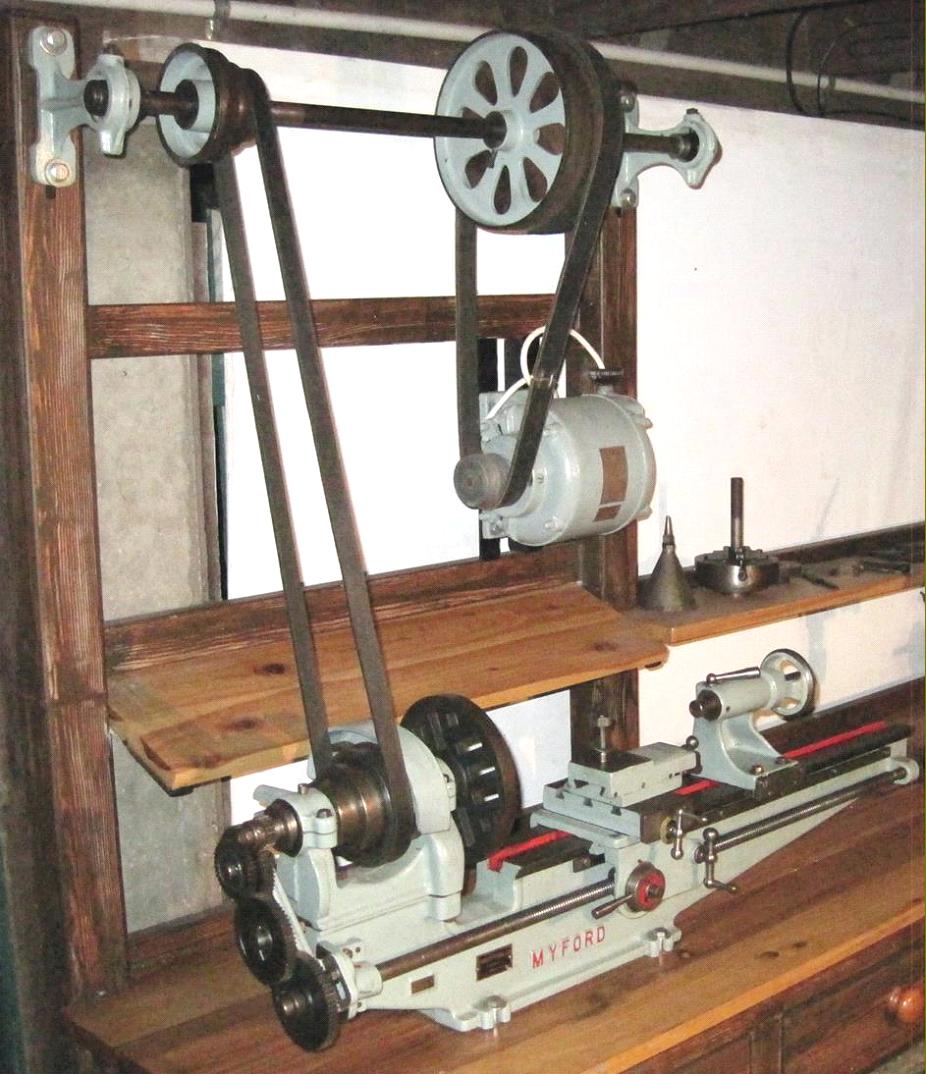 |
|
|
|
|
|
|
… and an owner's fine interpretation of the vintage scene as shown in the catalogue. Note the slots, cut into the uprights, to allow the plumber block countershaft bearings to be moved up and down to adjust the belt tension. The "vomit green" colour is close to the original
|
|
|
|
|
|
|
|
|
|
|
|
|
|
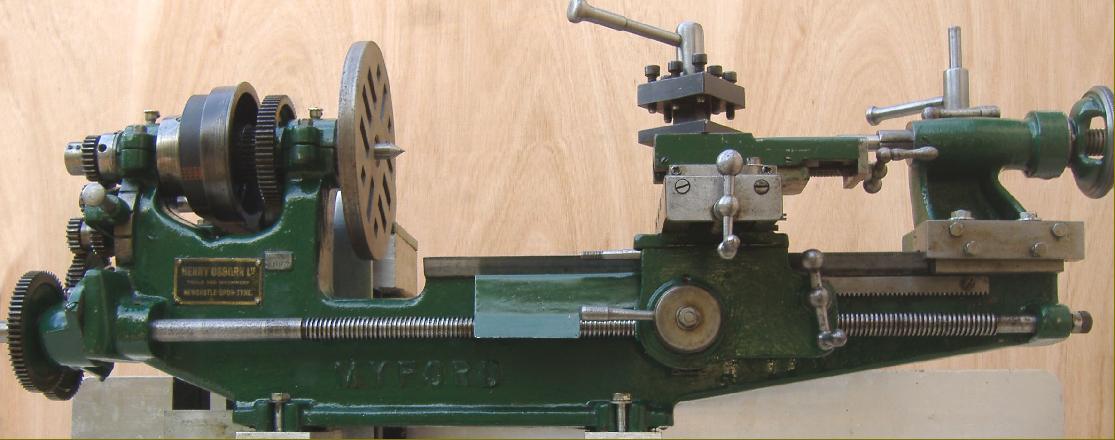 |
|
|
|
|
|
|
|
|
An early ML1 or ML2 fitted with tumble reverse and admitting 13.5" between centres
|
|
|
|
|
|
|
|
|
|
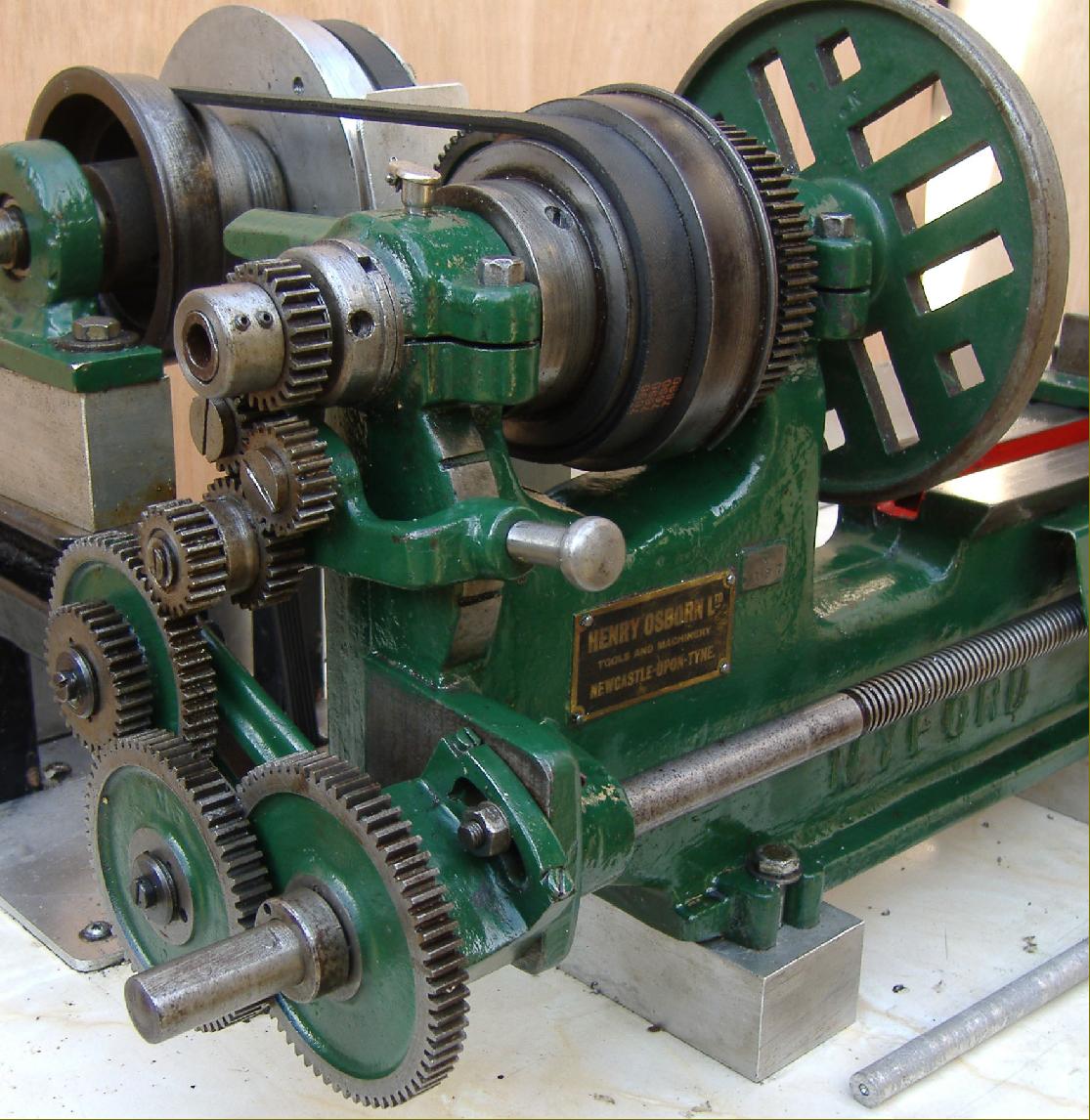 |
|
|
|
|
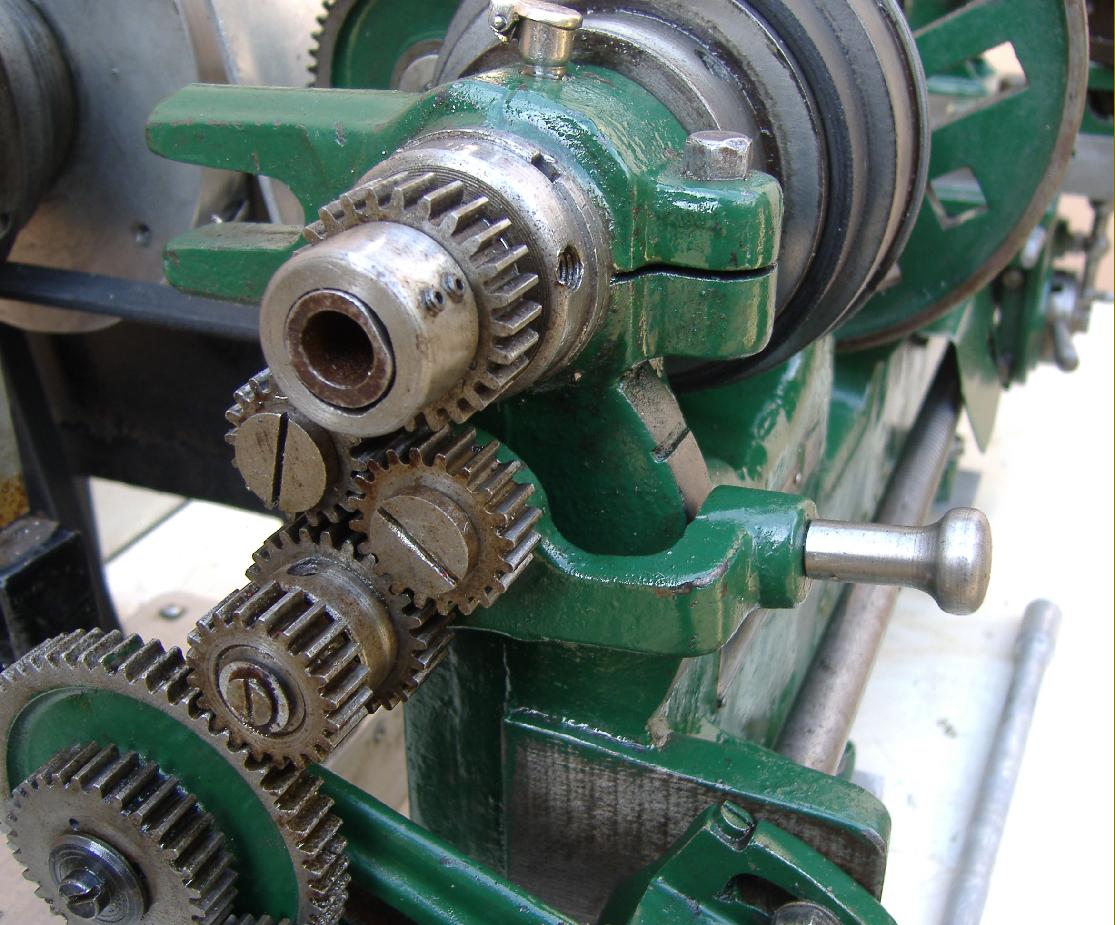 |
|
|
|
|
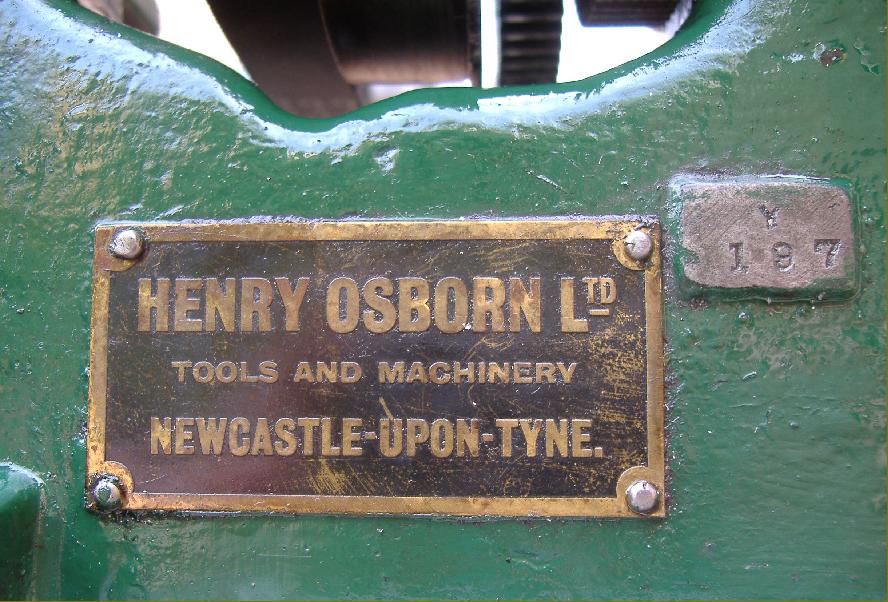 |
|
|
|
|
|
|
|
|
|
|
|
|
|