 |
 |
 |
 |
 |
 |
 |
 |
 |
 |
 |
 |
 |
 |
 |
 |
 |
 |
 |
 |
 |
 |
 |
 |
 |
 |
 |
 |
 |
 |
 |
 |
 |
 |
 |
 |
 |
 |
 |
 |
 |
 |
 |
 |
 |
 |
 |
 |
 |
 |
|
|
|
|
|
|
|
|
|
|
|
|
|
|
|
|
|
|
|
|
|
|
|
|
|
|
|
|
|
|
|
|
|
|
|
|
|
|
|
|
|
|
|
|
|
|
|
|
|
|
|
|
|
|
|
|
|
|
|
|
|
|
|
Founded in 1908, by the early 1920s Mikron had established a solid reputation for precision engineering with a range of very high quality precision bench lathes, small milling machines and gear hobbers. However, it was not until the 1960s that the Company decided to offer a more up-to-date range of conventional, " universal" milling machines constructed along lines similar to those made for many years by, for example, Deckel, Thiel and Maho, etc. The Mikron design was not, however, an in-house effort, but one supplied by Wilhelm Grupp Oberkochen (WIGO) - a German machine tool company organisation that was to close in 1984. Based on the WIGO WF-1, like all of its kind, the success of the Mikron lay in its ability to mount a number of different heads - horizontal, standard vertical, high-speed vertical and slotting - in combination with a variety of tables - plain, plain-tilting and compound swivelling. All the heads could be driven backwards and forwards across the top of the main column, by a handwheel working through reduction gearing (or under power), to provide an in-out feed, while the tables bolted to a flat, vertical T-slotted table equipped with power longitudinal and vertical feeds. By juggling the choice of heads and tables, and utilising other accessories, a skilled technician was seldom defeated in his attempts to produce the most complex of milled and drilled components - and all to a very high standard of accuracy. Mikron offered two basic models (upon which a variety of developed types were to be subsequently based): the smaller WF-2 and larger WF-3. Although both were very similar in general appearance, each was easily distinguished at a glance, one from the other, by the position of the head's external drive motor. On the WF-2 it was flange mounted against the rear face of the overarm-cum-spindle-gearbox unit while on the WF-3 it sat on the top, facing rearwards. In this respect, the Mikron differed from the majority of the type (where the motor was usually mounted inside the main column) and more resembled the accessory offered by the major producers of conventional milling machines (Cincinnati, Parkson, Rigiva, etc.) where such motorised overarms were employed to convert their ordinary horizontal models into more versatile vertical types. In later years the smaller of the two rams was dropped and the WF-2 fitted with that from the WF-3, the new model being given the (confusing) designation WF-2/3. Further development resulted in the WF-2S and WF-3S, these being fitted with infinitely variable speed table drive (and rapids) on all three axes. Also available were two special versions, the WF-DCM and WF-2/3DCM, equipped with recirculating ball screws on all 3 axes, DC table feed motors and the ability to be equipped with a variety of computer control systems. With this specification either straight-cut or continuous path travel (simultaneously in two or three axes) became possible together with an automatic gear change on the spindle drive that allowed a choice of a programmed or hand selection from the control panel. Continued below:
|
|
|
|
|
|
|
|
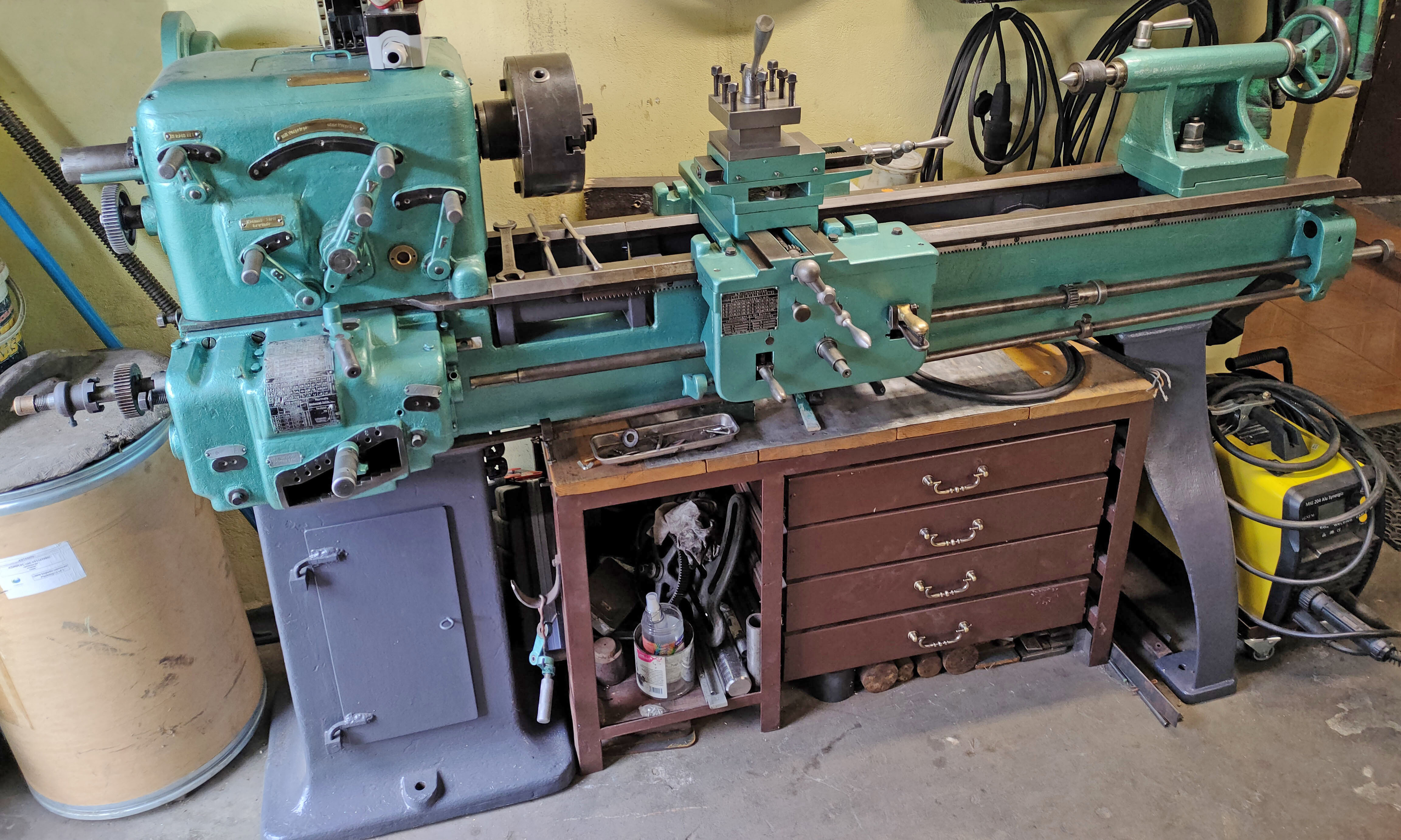 |
|
|
|
|
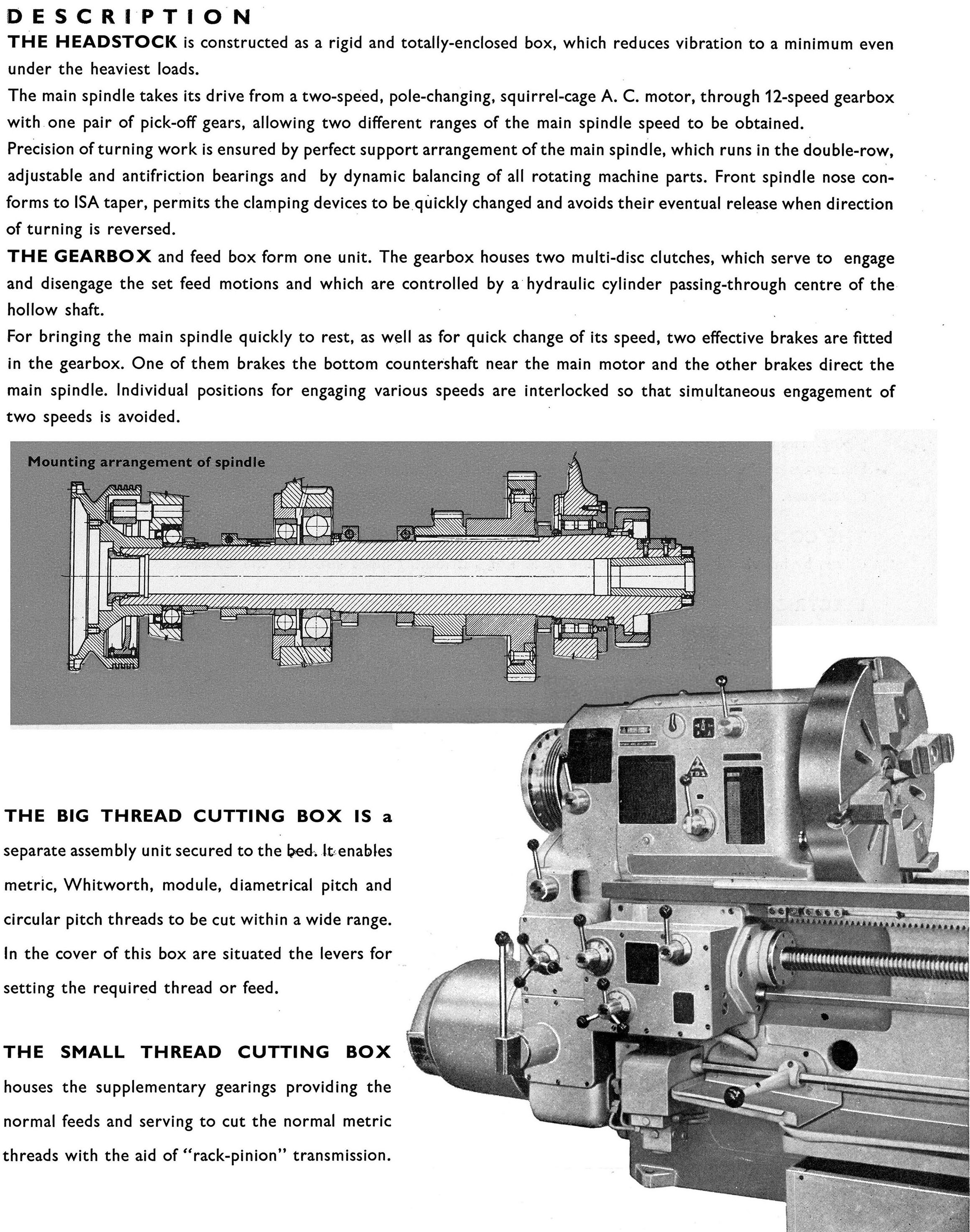 |
|
|
|
|
|
Above: the original Wilhelm Grupp WF1 - basis of the Mikron milling machine
Mikron WF-2 With 12 spindle speeds of 50, 71, 100, 140, 200, 280, 400, 560, 800, 1125, 1600 and 2240 r.p.m. driven by a two-speed (1500/3000 r.p.m. on 50 cycles) 2.5 kW motor, the WF-2 had both enough power and a sufficiently wide speed range to tackle a wide variety of work. The spindle ran in high-precision taper roller bearings with speeds changed by the juxtaposition of two levers mounted to the rear of the ram on its right-hand face. Gears and shafts were all made from high-quality, heat-treated steel with the gear teeth ground and the whole assembly running in an oil bath. Eighteen rates of table and head feed were available that spanned 8 to 400 mm/min together with a single rate of rapid feed (on all three axes and driven through a multi-disc clutch) of 1400 mm/minute. Power came from a 3-phase motor, mounted within the column, which drove by V-belt to an oil-immersed gearbox holding hardened and ground gears supported on shafts running in a mixture of taper-roller and ball races. Drive from the box was passed to the table and head by means of adjustable roller chains, power being fed through a safety over-load clutch (there were no shear pins) with all feeds able to be knocked off automatically by adjustable limit stops. The feed screws were hardened and their threads ground - a recipe for a long, trouble-free life - and, as a further aid to longevity, all the slideways were fitted with protective bellows. Driven by hand, the table travels were 420 mm horizontally and 345 mm vertically with the head having some 250 mm of in and out movement. Although power feed did not affect the cross feed travel, its use shortened the longitudinal by 10 mm and the vertical by 5 mm. In addition to a bolt-on unit to allow horizontal milling (Part 10.01), the WF-2 could be fitted with a 360° swivelling vertical head (part 11.01) equipped with a lever-operated, quick-feeds drilling quill with 63 mm of travel (no fine-feed attachment being offered). Driven at a 1:1 ratio, the 12 speeds were identical to those for the horizontal spindle (50 to 2240 r.p.m.) with the taper in the nose either an ISO 30 or ISO40 to the customer's choice. Dimensions were such that the spindle line could be set to within 91 mm of the column's inner face, or as far as 341 mm away. In order to aid mounting of the head, a support arm was available (Part 12.01) that allowed the unit to be stored at the side and swung into place when needed. Unfortunately (and surprisingly) unlike the machines offered by many competitors, the WF-2 was not available with a high-speed motorised head, instead the Precision High-speed Spindle was offered, a unit that attached to the end of the ordinary head and gave speeds of up to 10,000 r.p.m. Two other interesting and useful accessories were also offered that mounted in the same way: the Adjustable Multi-angle Milling Head (that could be swivelled from vertical to horizontal) and the Right-angle Milling Head, a heavier-duty device that mounted the cutter horizontally and could be swivelled through 360 degrees. Both the latter pair were carefully built from high-class components that included heat-treated and ground spindles and bevel gears. For slotting and keyway work a special head (Part 14.01) was provided. This had a stroke adjustable between 0 and 80 mm and seven stroke rates that ranged from 28 to 224 per minute. The cutter could be set to within 115 mm of the inner face or up to 370 mm away. One essential requirement for success when using this type of universal miller was the availability of a number of different tables to fasten to the 200 x 630 mm vertical table (this being fitted with three 12-H7 T-slots on 45 mm spacing). For the WF-2 several such were available, starting with a fixed, horizontal type (Part 20.01) with a clamping area of 250 x 700 mm and equipped with five 12-H7 T-slots on 45 mm spacing. Carefully designed to be as versatile and as rigid as possible, it was machined with three slots on each of the front and back vertical surfaces (allowing it to be mounted either way round) and with the top surface extending over one end face. The table could be clamped level with the top surface of the vertical table (using two or three bolts) or one bolt hole below or one bolt hole above. An alternative fixed table (Part 22.01) was also available, being somewhat larger at 300 x 800 mm with six 12-H7 T-slots on the usual 45 mm spacing. Absolutely necessary to obtain full functionality from the miller was the tilting and swivelling table (Part 21.01) with a 250 x 700 mm clamping area and five 12-H7 T-slots on 45 mm spacing. Able to be swivelled ±30° in the horizontal plane, ±45° parallel to the longitudinal and slide and ±30° against the longitudinal slide it allowed complex workpieces to be machines with the minimum of resetting. Continued below:
|
|
|
|
|
|
|
|
|
|
|
|
|
 |
|
|
|
|
|
|
Mikron WF-3 With 12 spindle speeds of 50, 71, 100, 140, 200, 280, 400, 560, 800, 1125, 1600 and 2240 r.p.m. driven by a two-speed (1500/3000 r.p.m. on 50 cycles) 2.5 kW motor, the WF-3 had both enough power and a sufficiently wide speed range to enable the tackling of a wide variety of work. The spindle ran in high-precision taper roller bearings with speeds changed by the juxtaposition of two levers mounted to the rear of the ram on its right-hand face. Gears and shafts were all made from high-quality, heat-treated steel with the gear teeth ground and the whole assembly running in an oil bath. Eighteen rates of table and head feed were available that spanned 8 to 400 mm/min together with a single rate of rapid feed (on all three axes and driven through a multi-disc clutch) of 1400 mm/minute. Power came from a 3-phase motor, mounted within the column, which drove by V-belt to an oil-immersed gearbox holding hardened and ground gears supported on shafts running in a mixture of taper-roller and ball races. Drive from the box was passed to the table and head by means of adjustable roller chains, power being fed through a safety over-load clutch (there were no shear pins) with all feeds able to be knocked off automatically by adjustable limit stops. The feed screws were hardened and their threads ground - a recipe for long, wear-free life - and, as a further aid to longevity, bellows were fitted to protect all the slideways. Driven by hand, table travels were 500 mm horizontally and 385 mm vertically with the head having some 500 mm of in and out movement. Use of power feed shortened all travels by a small amount - just 5 mm in any direction. In addition to a bolt-on unit to allow horizontal milling (Part 10.01), the WF-3 could be fitted with a 360° swivelling vertical head (part 11.10) equipped with a capstan lever-operated, fine-feed quill with 100 mm of travel. As an option, the head could be fitted with a very fine-feed attachment (Part 11.11) that gave 4 mm of travel per revolution of the handle, the micrometer scale being graduated in divisions of 0.02 mm. Driven at a 1:1 ratio, the 12 speeds were identical to those for the horizontal spindle (50 to 2240 r.p.m.) and the taper in the nose an ISO40. Dimensions were such that the spindle line could be set to within 121 mm of the column's inner face, or as far as 621 mm away. In order to aid mounting of the head, a support arm was available (Part 12.01) that allowed the unit to be stored at the side and swung into place when needed. Unfortunately (and surprisingly) unlike the machines offered by many competitors, the WF-3 was not available with a high-speed motorised head, instead the Precision High-speed Spindle was offered, a unit that attached to the end of the ordinary head and gave speeds of up to 10,000 r.p.m. Two other interesting and useful accessories were also offered that mounted in the same way: the Adjustable Multi-angle Milling Head (that could be swivelled from vertical to horizontal) and the Right-angle Milling Head, a heavier-duty device that mounted the cutter horizontally and could be swivelled through 360 degrees. It was carefully built from high-class components that included heat-treated and ground spindles and bevel gears. For slotting and keyway work a special head (Part 14.01) was provided. This had a stroke adjustable between 0 and 80 mm and seven stroke rates that ranged from 28 to 224 per minute. The cutter could be set to within 115 mm of the inner face or up to 370 mm away. Essential to obtain full functionality from this type of universal miller was the availability of a number of different tables to fasten to the 270 x 990 mm vertical table (this being fitted with five 12-H7 T-slots on 45 mm spacing). For the WF-3 several such were available, starting with a fixed, horizontal type (Part 20.50) with a clamping area of 350 x 800 mm and equipped with seven 12-H7 T-slots on 45 mm spacing. An alternative fixed table (Part 20.60) was also offered, being somewhat larger at 450 x 800 mm with nine 12-H7 T-slots on the usual 45 mm spacing. For the WF-3 two types of swivelling and tilting table were available, a standard version (Part 21.50) and two sizes of a more complex type, the "Universal" the base section of which had a built-in indexing mechanism. The ordinary table had a 350 x 800 mm clamping area, seven 12-H7 T-slots on 45 mm spacing and was able to be swivelled ±30° in the horizontal plane, ±30° towards and away from the operator and ±30° swivelling left and right. The Universal was sold as Parts 24.01 and 24.02, the difference being the size of T-slotted rectangular table supplied, the former having a useful surface area of 590 x 310 mm with six T-slots and the latter 680 x 395 mm with eight. The unit could be swivelled through 360° on two axes, and tilted 15° away from the machine and 45° towards it and allowed the machining of components on five sides without re-clamping. In addition the two rectangular tables, it was also possible to mount a rotary table, a fixture to hold components between centres as well as the usual vices and other work-holding attachments. Additional accessories for both the WF-2 and WF-3 included a powered helical milling device (in two sizes, Parts 53.21 and 53.25) which took their drive, via changewheels from the end of the vertical table's feed screw; a 100 mm centre height universal-vertical indexing unit (Parts 54.01 and 54.05) with overarm and drop bracket that could be used for direct and indirect indexing; a punch-milling accessory (Part 54.11) that attached to a vertical indexing unit (Part 54.01); a 250 mm rotary table (Part 55.01 and 55.11) with micrometer drum, three indexing discs and a 24-notch ring for direct indexing; a 320 mm rotary table of similar design to Parts 55.01 and 55.11; a 20x magnification centering microscope (Part 56.11 and 56.13) with built-in illumination, a 70° eyepiece, a field of view of 6.5, a focal length of 30 mm and a built-in graticule with cross wires and 12 concentric circles. Two facing and boring heads were offered, one able to bore and face from 0 to 260 mm and the other, the Piccolo, from 2 to 180 mm..
|
|
|
|
|
|
|
 |
|
|
|
|
|
|
|
|
|
|
|
|
|
|
|
 |
|
|
|
|
|
|
Mikron WF2/3-S. This example is fitted with a vertical head having both quick-action drilling and fine feeds
|
|
|
|
|
|
|
 |
|
|
|
|
|
|
Mikron WF2/3-DCM and WF3-DCM
|
|
|
|
|
|
|
|
|
|
|
|
 |
|
|
|
|
|
|
Right-angle milling head Part 12.10
|
|
|
|
|
|
|
 |
|
|
|
|
|
|
Vertical milling head Part 11.24 together with the infinitely-variable fine-feed attachment part 12.05
|
|
|
|
|
|
|
|
 |
|
|
 |
|
|
|
|
|
|
Vertical Swivelling Head for the WF2 Part No. 11.01. With 63 mm of quill travel under the control of a detachable handle, this unit has 12 speeds from 50 to 2240 r.p.m.
|
|
|
|
|
|
|
|
|
|
|
|
|
Vertical Swivelling Head for the WF3 Part No. 11.10. With 100 mm of quill travel under the control of a capstan handwheel, this unit had 12 speeds from 50 to 2240 r.p.m.
|
|
|
|
|
|
|
|
|
|
|
|
 |
|
|
|
 |
|
|
|
|
|
Part No. 11.11 Manual fine-feed attachment. Intended for mounting on the vertical milling head part No. 11.10, this assembly gave a very fine feed rate for use when boring. One turn of the micrometer dial gave 4 mm of linier movement.
|
|
|
|
|
|
|
|
Swivelling Slotting Attachment Part No. 14.01 for use on the WF2 and WF3. The stroke could be adjusted from 0 to 8 mm and the seven stroke rates set at between 28 and 224 per minute.
|
|
|
|
|
|
|
|
|
|
 |
|
|
|
 |
|
|
|
|
|
|
|
Part No. 60.01 and 60.15 Adjustable Multi-angle Milling Head. Able to be swivelled through 360° vertically, it could be angled though 180° horizontally and contained heavy-duty gearing made from hardened and ground materials.
|
|
|
|
|
|
|
|
|
|
|
|
Art No. 60.20 and 60.25 Right-angle milling head
|
|
|
|
|
|
|
|
|
|
 |
|
|
|
 |
|
|
|
|
|
|
|
|
The third-party test and inspection "Centricator", sold as Part Nos. 74.01 (reading to 0.01 mm) and 74.02 (reading to 0.02 mm). A rotating probe was used to check the deviation of a workpiece from the required position
|
|
|
|
|
|
|
|
Precision High-speed Spindle. This attached unit, with step-up gearing of 6:1 gave (depending upon the exact model) a maximum speeds of either 9,000 or 10,000 r.p.m.
|
|
|
|
|
|
|
|
|
|
|
|
|
|
|
|
|