 |
 |
 |
 |
 |
 |
 |
 |
 |
 |
 |
 |
 |
 |
 |
 |
 |
 |
 |
 |
 |
 |
 |
 |
 |
 |
 |
 |
 |
 |
 |
 |
 |
 |
 |
 |
 |
 |
 |
 |
 |
 |
 |
 |
 |
 |
 |
 |
 |
 |
 |
 |
 |
|
|
|
|
|
|
|
|
|
|
|
|
|
|
|
|
|
|
|
|
|
|
|
|
|
|
|
|
|
|
|
|
|
|
|
|
|
|
|
|
|
|
|
|
|
|
|
|
|
|
|
|
|
|
|
|
|
|
|
|
|
|
|
|
email: tony@lathes.co.uk Home Machine Tool Archive Machine-tools Sale & Wanted Machine Tool Manuals Catalogues Belts Books Accessories
Mikron Types 102 and 102.05 Gear Hobbing Machines Switzerland
A Manual and Data Set is available for the Mikron 102 and Other Mikron Manuals & Catalogues as well
Mikron 79 Gear Hobber
Mikron Hobbers 1960s-1970s reproduction of a General Catalogue
Mikron Lathes Mickron Large Millers WF-2 & WF-3
Small Mikron Milling Machines
Another of the popular, successful but smaller Mikron gear hobbing machines, the 102 and later 102.05 were made from the 1950s into the 1980s. Designed as a universal machine, they were able to produce all tooth forms by either hobbing or, using the "continuous indexing method", with fly cutters. The 102 was claimed by its makers to be not only suitable for continuous production work under multiple shift working - and in the most demanding of circumstances - but also equally at home in a toolroom or experimental workshop. To ensure that it met the highest of traditional Swiss standards, the 102 was built from top-class materials and constructed with enormous care, its consequent accuracy and reliability enabling it to tackle the most demanding of precision work. Before dispatch, each machine was subjected to a variety of tests including making sample gears, checking the indexing accuracy by measuring the adjacent and accumulated pitch errors and differences between pitches. The testing of the sample gears cut was, naturally, carried out on Mikron's own gear-testing equipment. Always supplied on a self-contained cabinet stand that held the motor (1 h.p. on the Type 102 and 1.5 h.p. on the Type 102.02), a drive system, a built-in 0.08 h.p. electric coolant pump with storage tank and an automatic lubrication system. Constructed from high quality, non-porous cast iron the 102 had, like the Company's lathes, had a very fine surface finish that was neither primed nor painted. Instead, a metallising, anti-corrosion process was applied that would neither chip nor wear, the result being a fine-looking finish and a machine able to retain its ex-factory appearance for many years of hard service. The net weight of a basic machine with standard equipment was 620 kg and with all equipment, 800 kg. Work was held on special arbors that ran with great precision, these being combined with a bayonet-type, rapid clamping system; sets of collets were also available to hold special or awkward jobs. There was no need for subsequent deburring, the machine being equipped with such a device as part of the standard equipment. Indexing (for different numbers of gear teeth) was carried out by changewheels, these also being employed for changes of feed rate, pitch and cutter speed - the two separate housings being easily accessible and guarded with heavy, hinge-open doors. Although a standard Type 102 could produce work of a perfectly satisfactory standard, Mikron also offered a high-precision version, the EP. This type was capable of manufacturing gears to a standard that had previously been reserved - theoretically - for scraped and ground gears. Gears made to this standard required not only a gear hobber made to an exceptional high level of precision, but several other considerations also needed to be taken into account including the use of high-quality blanks; precision clamping equipment; profile-ground hobs of a quality class described during the 1970s as being to the standard "AA-EP"; close attention to the choice of measuring equipment and operators familiar with its use and, where possible, operated in an environment that was both dust and vibration-free - and preferably air-conditioned. In addition, Mikron also offered a service to design, manufacture and supply any special equipment needed by a customer to solve a particular gear-manufacturing problem. Even in standard form, without employing any of the many accessories available, the Type 102 could cut spur and spiral-tooth gear wheels of all types as well as pinions, multi-start worms, worm wheels and multi-start external threads - with both left and right-hand spirals able to be produced. By spending (considerably) more money, a buyer could choose from a wide range of accessories (shown and described below) that allowed the Type 102 to produce bevel gears, both external and internal threads, worm wheels and gears of a larger diameter than the machine's normal limit. Continued below:
|
|
|
|
|
|
|
|
|
|
|
|
|
|
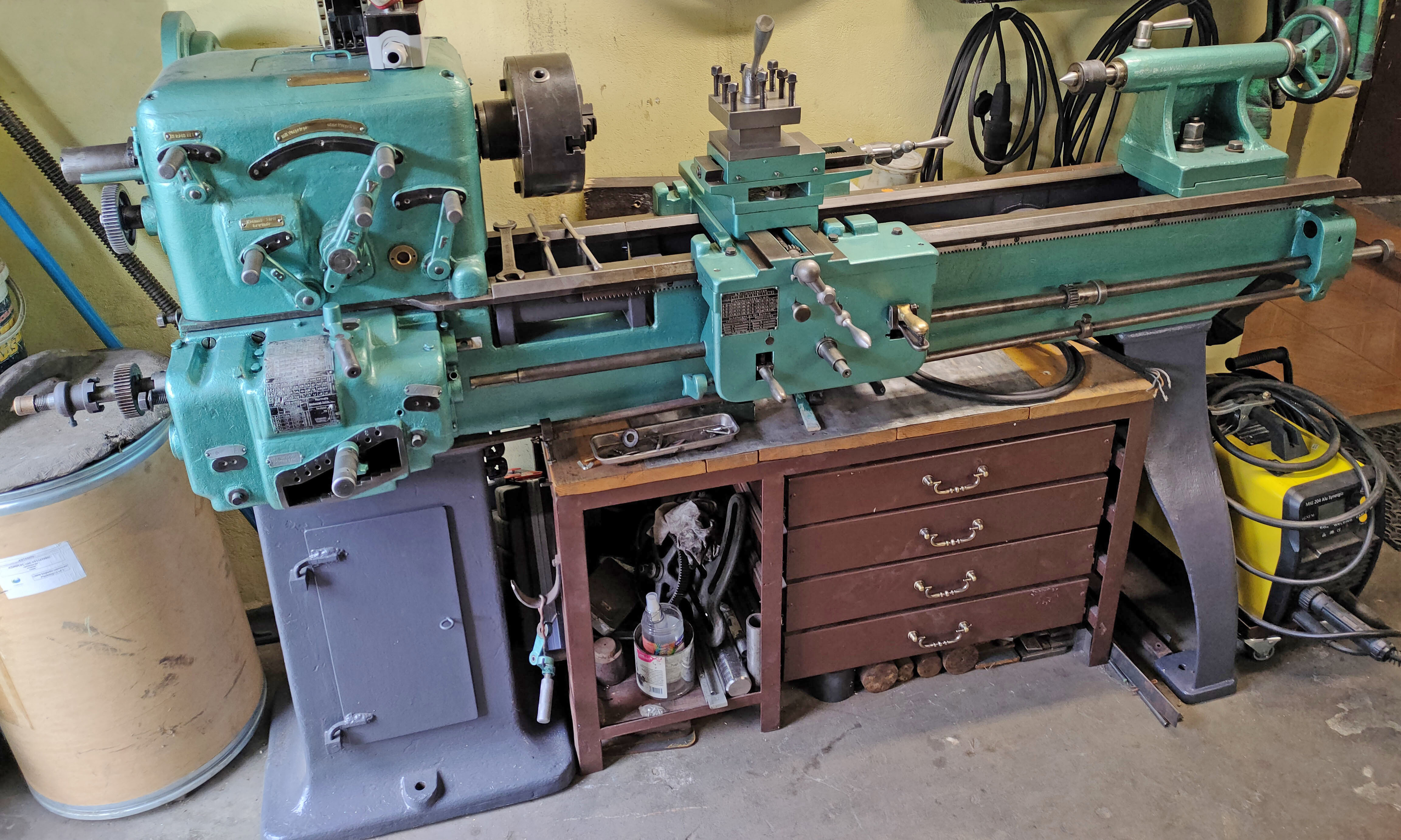 |
|
|
|
|
|
|
|
|
|
|
|
|
Continued: Further development by Mikron for the 102 was 'continuous indexing', a process by which bevel gears were produced using fly cutters - this being subject to further improvement and re-named the "Conikron Method". This system involved machining the profile of a gear by a cutter having seven successive teeth - the first and last tooth developing the accurate profile while the ones in between acted to rough the shape and cut the root of the teeth. Advantages claimed for the method included an increased tooth depth (by 1/3 the cone length compared to 1/5 by the former), thus giving a longer meshing surface; the roughing teeth gave a slight increase in productivity while a better surface finish was achieved and the parts - due to ground profile cutters - were made to a higher standard of accuracy. As well as newer models being able to employ the system, older models such as the 120 could also use it. Of considerably greater capacity than the other popular, small Mikron hobber, the Type 79, the largest gear that the Type 102.02 could cut was 4.75" (120 mm) in diameter with a length of 5.125" (130 mm). Numbers of teeth from 6 to 325 could be accommodated (though numbers below and above this could also be arranged) while the maximum pitch was 12 D.P. (2 Module). The thirteen feed rates spanned 0.05 to 3 mm ( the earlier 102 had 7 spanning 0.05 to 0.6 mm) with cutter speeds ranging from 140 to 1870 r.p.m. Spiral pitches ranged from 3/32" to 196" (2 to 5000 mm) with the pitch angle of spirals, left or right-handed, being from ) to 0 to 89°. A wide range of accessories was offered, including: a Multi-program control (Part 164.30.20.00/0) that provided an automatic sequence of four operations and a return to their starting points; once set up, all the operator had to do was load and unload the jobs. Equipment for Cutting Large Gears (Part 30.23.00/0) consisting of a cutter support with the cutter shaft mounted at a lower level for producing large diameter gears in the range 4" to 7 7/8; Cutting Internal Threads (Part 30.22.00/0 This was a cutter support with the cutter shaft mounted at a higher level and designed to take cutters with a special mounting shank that enabled multi-start threads of great accuracy to be generated. Precision Bevel Gear Cutting Attachment (Part 30.70.00/0). This unit was intended for the economic production in small to medium-sized production runs of spur and spiral-bevel gears. For bevel gears the attachment replaced the tailstock support and its overarm with the normal cutter support remaining in place. By using a centring microscope, the cutter could be adjusted accurately to the centre axis of the job with deburring taking place automatically as the work progressed. Special Worm Wheel Cutting Device (Part 30.80.00/0). This attachment enabled worm wheels to be cut using the automatic tangent feed. During the machining process, the cutter height did not need to be changed or adjusted, the cutter having the same form as the worn into which the wheel being cut was intended to engage. The teeth of the worm wheel were cut out across the entire arc in a constant width - the tooth width being neither cut short nor of an incorrect form. Pneumatic Clamping Device (Part 30.58.00/0) Like the pneumatic tailstock attachment for the Mikron Type 79, this attachment was intended to speed up the mounting and dismounting of jobs. The clamping pressure was adjustable to each job and the accessory could be fitted by a user himself to older machines - though the factory recommended that it was supplied ready installed. Microscope Centring Device. This accessory was made up of three parts, the microscope with a holder (Part 23.54.00/0), a centre with a collet shaft (Part 103.91.35/500) and a cutter centring pad (Part 30.21.50/0). Rapid Clamping Lever (Part 30.43.00/0) When using collets this device - identical in function to those used on the maker's precision plain-turning lathes - opened and closed the collets very much faster than the hand-screw method. Device for Cutting Single Start Threads on the Type 102.05. This attachment enabled the gear hobber to generate threads in a single operation, the root, flank and crest all being formed simultaneously. The method was claimed to give improved pitch accuracy and a fine surface finish. While a high-class machine was essential for the production of accurate gears, good quality hobs were equally important and Mikron offered a wide range including ones for involute teeth with both ground and unground profiles; for spur and spiral wheels; for worms and the the matching worm wheels; ones for epicycloidal teeth suitable for the watch and clock industries; hobs for splined shaft; setting cutters for ratchet wheels and thread and bevel gear cutters--and special teeth to a customer's requirement For the Type 102, hobs were available for any profile desired with pitches from 12 to 800 D.P. and for involute tooth forms ground hobs with pitches down to 200 D.P. For tooth forms that could not be generated, Mikron supplied a range of fly cutters. Standard hobs were made in diameters of 12, 14, 16, 18, 20, 24, 32 and 40 mm and with centre holes of 6, 8, 10, 13, and 16 mm and 0.5". These hobs had 15 gashes with the front rake directed towards the cutter centre and, to obtain the clean cutting of such as light metals and stainless steel, the front rake was set at 15°. Mikron also offered to make special hobs on demand - though doubtless this would have been at Swiss prices to the power of two...
|
|
|
|
|
|
|
|
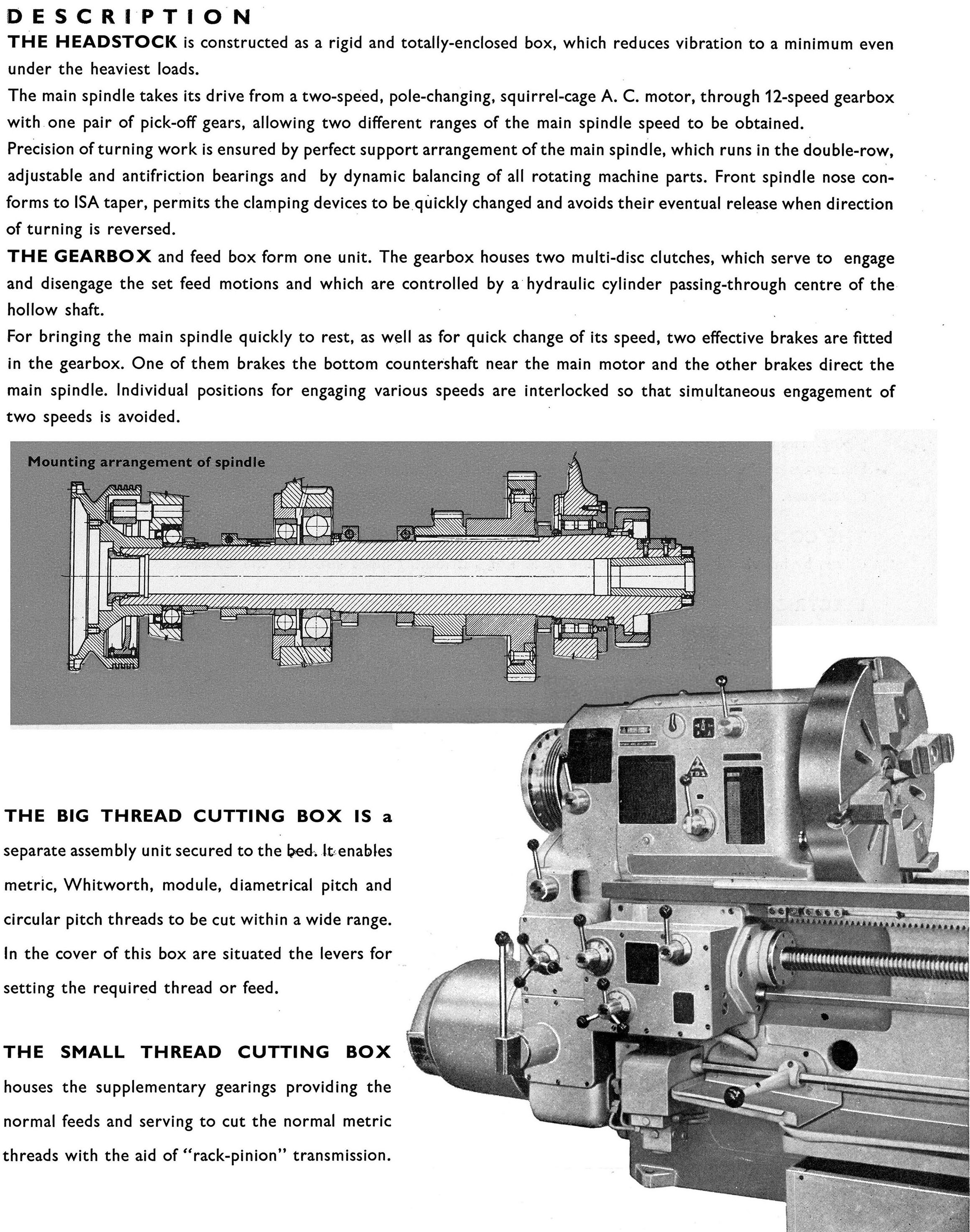 |
|
|
|
|
|
 |
|
|
|
|
|
|
|
|
|
Above and below: examples of parts that could be made on the Mikron 102 gear hobber
|
|
|
|
|
|
|
|
|
|
 |
|
|
|
|
|
|
|
|
|
|
|
 |
|
|
|
|
|
|
|
|
|
Hobbing a bevel gear on a standard Mikron 102
|
|
|
|
|
|
|
|
|
|
 |
|
|
|
|
|
 |
|
|
|
|
|
|
|
|
|
Differential drive unit from a Mikron 102 gear hobber. This was used when making high-accuracy helical gears - when spur gears were hobbed it could be replaced by a direct transmission shaft
|
|
|
|
|
|
|
|
|
|
 |
|
|
|
|
|
|
|
|
|
Indexing (for different numbers of gear teeth) was carried out by changewheels
|
|
|
|
|
|
|
|
|
|
|
|
|
|
|
|
 |
|
|
|
|
|
|
|
|
|
Changewheels were also employed for changes of feed rate, pitch and cutter speed
|
|
|
|
|
|
|
|
|
|
 |
|
|
|
|
 |
|
|
|
|
|
|
|
|
|
Multi-program control Helical gear being machined using radial and axial hobbing with a double pass of the ho. The gear is held in a collet and supported against a tailstock centre
|
|
|
|
|
|
|
|
|
|
 |
|
|
|
|
|
|
|
|
|
Multi-program control Axial hobbing of a helical gear held in a loading pin and against a tailstock centre (on a Mikron 102.05)
|
|
|
|
|
|
|
|
|
|
 |
|
|
|
|
|
|
|
|
|
Multi-program control Radial and axial hobbing of a single toothed pinion held in a collet and supported against a tailstock centre (on a Mikron 102.05)
|
|
|
|
|
|
|
|
|
|
|
|
|
|
|
|
 |
|
|
|
|
|
|
|
|
|
Multi-program control Radial hobbing of a worm wheel between centres (on a Mikron Type 102.05)
|
|
|
|
|
|
|
|
|
|
 |
|
|
|
|
|
|
|
|
|
Cutting Internal Threads (Part 30.22.00/0 This was a cutter support with the cutter shaft mounted at a higher level and designed to take cutters with a special mounting shank that enabled multi-start threads of great accuracy to be produced.
|
|
|
|
|
|
|
|
|
|
 |
|
|
|
|
|
|
|
|
|
Equipment for Cutting Large Gears (Part 30.23.00/0) consisting of a cutter support with the cutter shaft mounted at a lower level for producing large diameter gears in the range 4" to 7 7/8;
|
|
|
|
|
|
|
|
|
|
 |
|
|
|
|
|
|
|
|
|
Special Worm Wheel Cutting Device (Part 30.80.00/0). This attachment enabled worm wheels to be cut using the automatic tangent feed. During the machining process the cutter height did not need to be changed or adjusted, the cutter having the same form as the worn into which the wheel being cut was intended to engage. The teeth of the worm wheel were cut out across the entire arc in a constant width - the tooth width being neither cut short, nor of an incorrect form.
|
|
|
|
|
|
|
|
|
|
|
|
|
|
|
|
 |
|
|
|
|
|
|
|
|
|
Precision Bevel Gear Cutting Attachment (Part 30.70.00/0). This unit was intended for the economic production in small to medium-sized production runs of spur and spiral-bevel gears. For bevel gears the attachment replaced the tailstock support and its overarm with the normal cutter support remaining in place. By using a centring microscope, the cutter could be adjusted accurately to the centre axis of the job with deburring taking place automatically as the work progressed.
|
|
|
|
|
|
|
|
|
|
 |
|
|
|
|
|
|
|
|
|
Rapid Clamping Lever (Part 30.43.00/0) When using collets this device - identical in function to those used on the maker's precision plain-turning lathes - opened and closed the collets very much faster than the hand-screw method.
|
|
|
|
|
|
|
|
|
|
 |
|
|
|
|
|
|
|
|
|
Microscope Centring Device. This accessory was made up of three parts, the microscope with a holder (Part 23.54.00/0), a centre with a collet shaft (Part 103.91.35/500) and a cutter centering pad (Part 30.21.50/0).
|
|
|
|
|
|
|
|
|
|
 |
|
|
|
|
|
|
|
|
|
Pneumatic Clamping Device (Part 30.58.00/0) Like the pneumatic tailstock attachment for the Mikron Type 79, this attachment was intended to speed up the mounting and dismounting of jobs. The clamping pressure was adjustable to each job and the accessory could be fitted by a user himself to older machines - though the factory recommended that it was supplied ready installed.
|
|
|
|
|
|
|
|
|
|
|
|
|
|
|
|
 |
|
|
|
|
|
|
|
|
|
Device for Cutting Single Start Threads on the Type 102.05. This attachment enabled the gear hobber to generate threads in a single operation, the root, flank and crest all being formed simultaneously. The method was claimed to give improved pitch accuracy and a fine surface finish..
|
|
|
|
|
|
|
|
|
|
 |
|
|
|
|
|
|
|