 |
 |
 |
 |
 |
 |
 |
 |
 |
 |
 |
 |
 |
 |
 |
 |
 |
 |
 |
 |
 |
 |
 |
 |
 |
 |
 |
 |
 |
 |
 |
 |
 |
 |
 |
 |
 |
 |
 |
 |
 |
 |
 |
 |
 |
 |
 |
 |
 |
 |
 |
|
|
|
|
|
|
|
|
|
|
|
|
|
|
|
|
|
|
|
|
|
|
|
|
|
|
|
|
|
|
|
|
|
|
|
|
|
|
|
|
|
|
|
|
|
|
|
|
|
|
|
|
|
|
|
|
|
email: tony@lathes.co.uk Home Machine Tool Archive Machine-tools Sale & Wanted Machine Tool Manuals Catalogues Belts Books Accessories
Clisby Lathe - Australia - also branded "Nextek" - Other Australian-built lathes: Advance, Burden, Clisby, Great Scott & Conrik, Hercus, A.E.Herbert, Premo, Qualos, Macson, Mars, Nuttall, Parkanson, Purcell, Rolfe, Sheraton, Tillico, T.N.C. Veem
|
|
|
|
|
|
|
|
|
|
|
|
|
|
|
|
|
|
|
|
With a 2.5" swing and admitting 4.5" (or 10.5") between centres lathe (63 mm x 114 mm and 266 mm), the Clisby lathe was designed by Harold Clisby - later responsible for the design, engineering and production of the first Sherline. Out of production for many years the lathe now appears (2013) to be back on the market - details can be found here Probably, at the time, the smallest "real" one in the world, the Clisby was a simple, plain turning type with its bed constructed from an extrusion of aircraft-quality aluminium (6061 temper 6) and using two dovetails, one on the outside for the saddle slides and a second in the centre to provide an accurate location for the headstock and tailstock. The "0" Morse taper headstock spindle had bore of 0.318" (8.1 mm) and carried a 1/2" 20 t.p.i. (N/F) thread; it ran on simple plain bearings lubricated by felt wicks - a very light sewing-machine oil was recommended - and proved a reliable unit over long periods of use. Although a compound slide rest was not fitted (nor were graduated dials on the feedscrews until 2001) the carriage could be propelled along the bed under the influence of a Flexispeed-like overhung leadscrew of 20 t.p.i. and 1/4" diameter. A wood-turning version, ideal for making the tiny parts needed for dolls' house furniture, was also produced - and supplied as standard with a 4-jaw chuck and hand-tool rest. An interesting feature of the machine was its drive system: included as standard equipment with all models was a 5-pole 12V DC motor that drove the spindle through a toothed belt at a fixed speed of 1500 rpm. (the makers recommend using a 12 volt car battery, DC battery charger or a 12 volt DC transformer as a power source). The limitation of just one turning speed could be overcome easily by using one of the many DC variable-speed controllers on the market (see below) or employing a second-hand variable-speed sewing machine motor - it was also very simple to arrange a drive to the large, overhung pulley on the end of the headstock spindle from either underneath or behind lathe - or even from above. A range of simple but useful accessories was produced: a larger 4-jaw chuck than the one provided as standard, a 3-jaw Jacobs drill chuck adapted for headstock mounting, faceplates for both the metal and wood lathes, miniature wood-turning tools, a wood-screw chuck and wood-turning "drive dog", a hand rest for the metal lathe, a two-way toolpost, tailstock drill chuck, vertical slide and various kinds of turning tools. One advantage of the machine was its very light weight (the metal lathe weighed 1.2 Kg, the wood lathe only 1 Kg ) and mounted on a small base board it was be possible even for a lady to lift on and off a workbench. It was also tiny - at 11" (279 mm) long, 3.5" (88 mm) high and 2 5/8" (67 mm) wide it must surely have rivalled even the incredible ManSon lathe for compactness. Whilst it would have been difficult to argue that a Clisby was the only lathe you needed, as a compliment to a larger machine - or for use in making the tiny fittings required for transport models of all kinds - it was as close to ideal (at the price) as you could find. Another advantage, seldom mentioned, is that with such a relatively inexpensive machine it was possible to engage in some creative engineering and modify its components for specialist purposes; if one wished, for example, to alter or adapt the headstock, slides or tailstock these items could be bought inexpensively as sub assemblies from the makers--and if the experiment failed, the cost incurred was very little. Clisby also manufactured a miniature vertical miller, the CVM500, that stood just 10 inches high and carried a tiny 6" x 19/16" table (153 mm x 40 mm) with a longitudinal travel of 33/4", a traverse of 21/2" and a vertical of 4". The machine was based upon what were, in effect, two lathe bed sections at right angles to each other. The machine was intended for light use on non-ferrous materials and again, whilst not the only machine a serious hobbyist would want it was, with its limited-power motor, an ideal tool for smaller, lighter intricate jobs and one on which the principals of milling could be safely taught to a young person. For the German market the Clisby appears to have been marketed under the name "Nextek"..
|
|
|
|
|
|
|
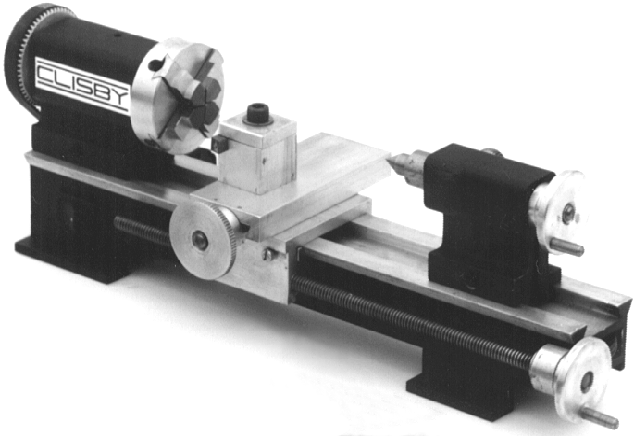 |
|
|
|
|
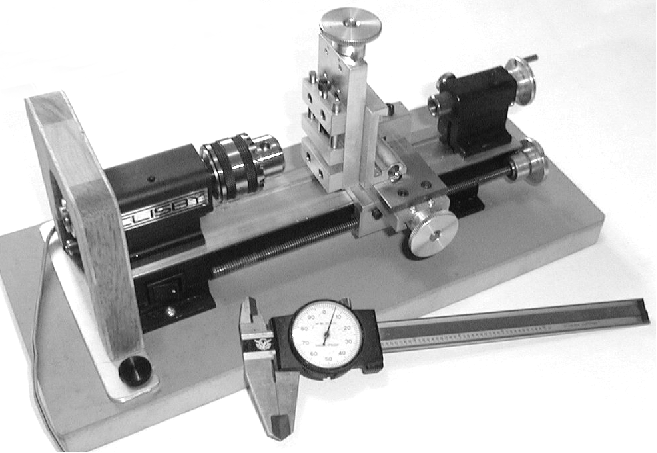 |
|
|
|
|
|
|
A Clisby mounted on a small board with a vernier caliper for size comparison. Note the simple but effective swing-open cover which has been installed to guard the drive pulley. Details of the Vertical Slide can be found below.
|
|
|
|
|
|
|
|
|
|
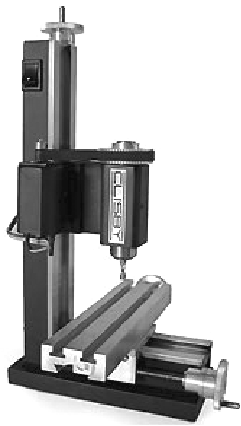 |
|
|
|
|
|
|
|
Clisby CVM500 miniature vertical miller
|
|
|
|
|
|
|
|
|
|
|
|
An American Clisby lathe owner, David Blocker, writes: I have a Clisby and it is kind of neat - and not at all the toy that owners of much bigger and more expensive lathes assume it must be. In order to increase the usefulness of mine I constructed an adaptor for the headstock spindle so that it will now take watchmaker-type WW collets. The Clisby spindle bore is 8 mm so a standard WW drawbar will fit. The tailstock, by the way, needed just a little shimming to get it perfectly true. I use a Steffco chuck; this is a WW collet-mounted 3-jaw made out of fiberglass resin and is slightly smaller in diameter than the typical WW chuck - the latter being too big to fit the spindle and clear the bed. I found a small DC 2 amp 12V power supply at the local surplus store to give variable-speed drive and took the stainless steel hub of an old (the new ones are disposable plastic) hypodermic needle and mounted it on the Clisby headstock as an oil cup. The handwheels are not calibrated so I keep a cheap vernier calliper with the lathe to measure slide rest travel directly. When I find a cheap digital read-out calliper I will make a bracket for that so I can clip in on and off the lathe as required. I intend to make a vertical-milling attachment/top slide for the Clisby out of a cut-down Clisby saddle and cross slide; Clisby are quite happy to sell individual components for owners to experiment with. I also intend to make an indexing plunger to bring the toothed belt-drive gear on the headstock spindle into action as a dividing attachment. The whole kit, including the power supply, a handful of WW collets, the Steffco 3-jaw chuck and the Clisby 4-jaw chuck fit into a wooden container a little smaller than a shoe box. The plastic or the metal three jaw chuck for the "Unimat 1" would also work with the Clisby if the spindle hole was filled in - and then rebored and tapped. If someone was enthusiastic enough they could probably adapt the Clisby for thread cutting, but it would be easier to make a die and tap holder for it. The Clisby would be a very suitable first lathe for a kid and, as long as he or she wore safety glasses, the would be hard put to really hurt himself with it - yet would still be able to make something worthwhile. By comparison, the Unimat 1 cannot really handle even brass, but the Clisby will happily chew its way through that - and even do mild steel if you are very patient and use a sharp tool and a little lubricant. The next lathe up in size, a Sherline or Unimat 3, is just big enough and powerful enough to cause some painful damage. The small size of the Clisby means it is portable; you can easily take it on a trip with you and set it up on the bathroom counter or desk of a hotel room and actually make stuff. For example, you could grind a form cutter at home and then, when on a business trip, enjoy the time after work by churning out railing spindles for a model ship. The Clisby headstock alone would make a useful light duty drilling/milling spindle - especially with the WW collet adaptor. Joe Martin of Sherline does not believe in mounting milling spindles on lathes and thinks that that operation should be done on a separate mill. However, to my mind, the Clisby lathe would make the basis of a tidy milling attachment for the Sherline. All things considered the Clisby is a neat little lathe - a light-duty miniature machine tool with which you can do real work. Of note: the Taiwanese manufacturers of the Unimat 4 have given up the classic system of screwcutting by the use of threading "formers and followers" which the original Austrian Unimat SL and Unimat 3 used - and have copied the system used on the current Sherline of a hand-cranked spindle and screwcutting changewheels..
|
|
|
|
|
|
|
|
|
|
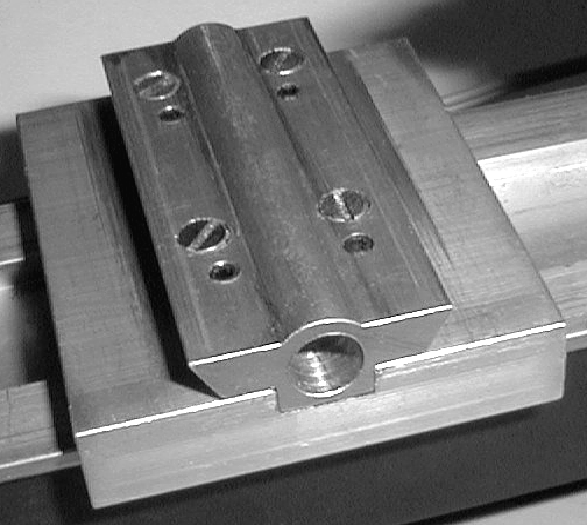 |
|
|
|
|
One of the Problems with the Clisby is the lack of any gib adjustment for the cross slide. To overcome this Dr. Peter Clark has modified the (separate) central part of the saddle - the "Saddle Insert" - by adding four tapped holes and screwing into them Allen screws which are allowed to protrude, by a small amount, through the base. It is thus possible to lower the section (having reduced the thickness of its base slightly) - and then, by trial and error, readjust its height with the Allen screws and remove any play which might exist between it and the cross slide.
|
|
|
|
|
|
|
|
|
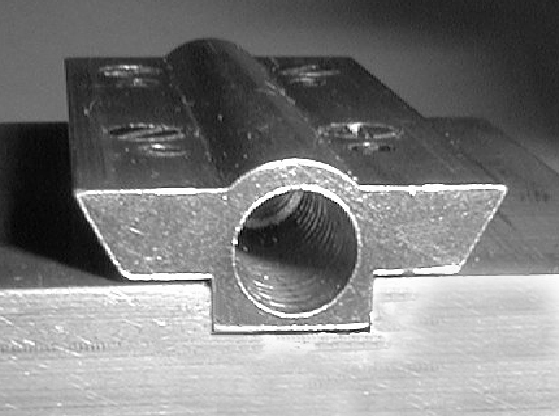 |
|
|
|
|
|
|
Another view of the adjustable "Saddle Insert" with a slight clearance visible beneath its base.
|
|
|
|
|
|
|
|
|
|
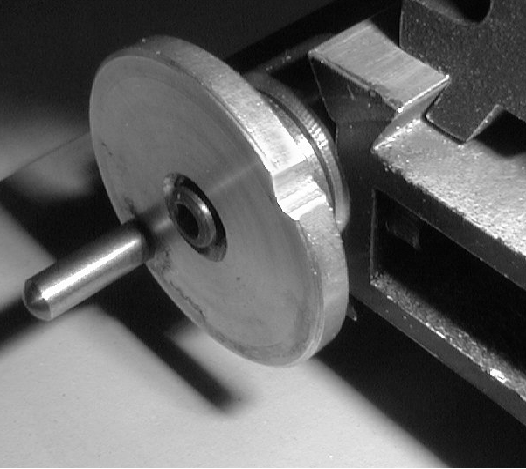 |
|
|
|
|
Before the tailstock can be slid off it is normally necessary to remove the feed screw handwheel - filing a small Vee groove in the wheel's periphery allows the tailstock to slide over it .
|
|
|
|
|
|
|
|
|
|
|
|
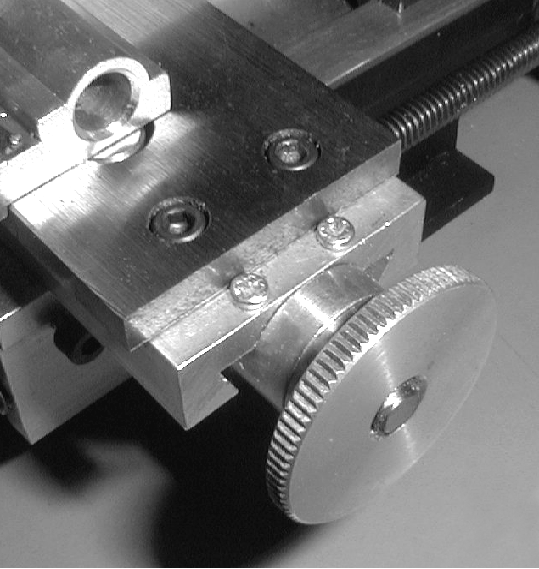 |
|
|
|
|
Simple, ungraduated handwheels. One quick, easy and (hopefully) temporary antidote is to use your desktop publishing system to draw a suitable scale, print it out on sticky paper - and wrap it around the dial. Those of you who remember "Technical Drawing" from their school days may recall the problem of a line, of an inconvenient length, which had to be divided into an equally inconvenient number of exact divisions. The solution lay in drawing a second line from one end of the first line, at an angle of around 45 degrees and roughly twice as long. This second line was then easily marked out with dividers into the required number of sections. To transfer the markings back to the original line, a straight line was drawn connecting the last mark on the divided line to the end of the first line. Lines parallel to this were then drawn from each division - and so the main line exactly divided into the required number of spaces. No doubt a CAD program could be persuaded to complete this task in the pulsing of a transistor.
|
|
|
|
|
|
|
|
|
|
|
|
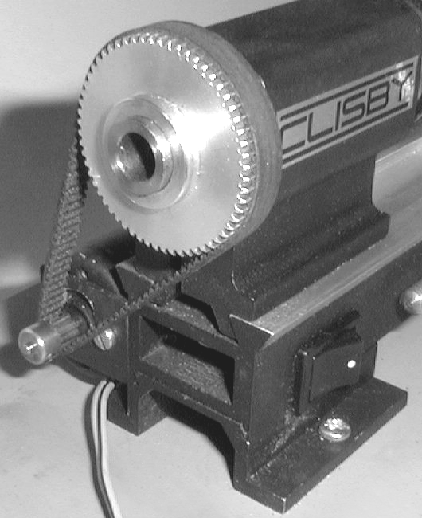 |
|
|
|
|
|
|
|
|
|
|
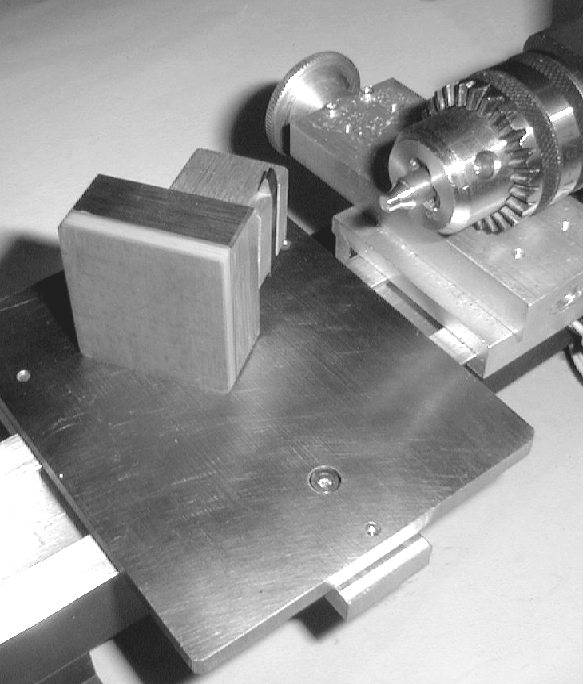 |
|
|
|
|
|
|
|
This special hand-turning unit was made by Dr. Peter Clark in England and based on an accessory first advertised by Lorch as a means of assisting with "Graving" work - a watchmaker's term for what might best be described as "freehand" turning. The unit consists of a smooth metal plate fastened to the lathe saddle and a series of steel toolholders with plastic-covered bases. For light work a single tool block is used and manoeuvred freely on the plate; for heavier tasks the toolholders are made larger and incorporate a long handle to add stability and leverage. A remarkable wooden lathe, the 'fonly )if only I had a lathe) has been built around this system of hand-controlled toolholders.
|
|
|
|
|
|
|
|
|
|
Each toolholder has it base lined with hard plastic
|
|
|
|
|
|
|
|
|
|
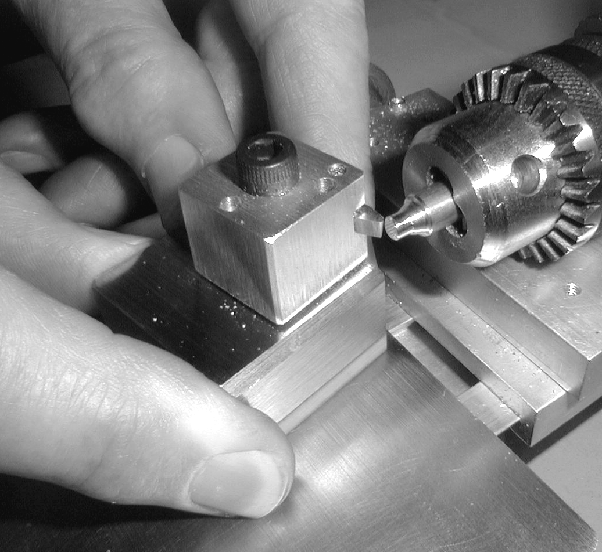 |
|
|
|
|
The toolholder in use turning a brass rod. It is easy to forget just how accurate "Jacobs-type" drill chucks are - it being perfectly possible to press them into service for light-duty turning on larger lathes as well. Atlas, in the United States, offered a specially-commissioned Jacobs chuck for direct headstock spindle mounting in their first catalogue of (circa) 1932 - and it remained listed until the last 12-inch machines left the factory in the 1980s.
|
|
|
|
|
|
|
|
|
|
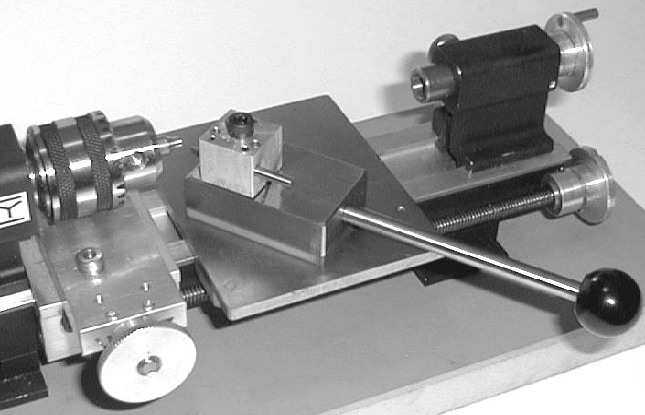 |
|
|
|
|
|
|
For "heavy-duty" turning a larger toolpost is used assisted by a long handle which offers both greater stability and extra leverage.
|
|
|
|
|
|
|
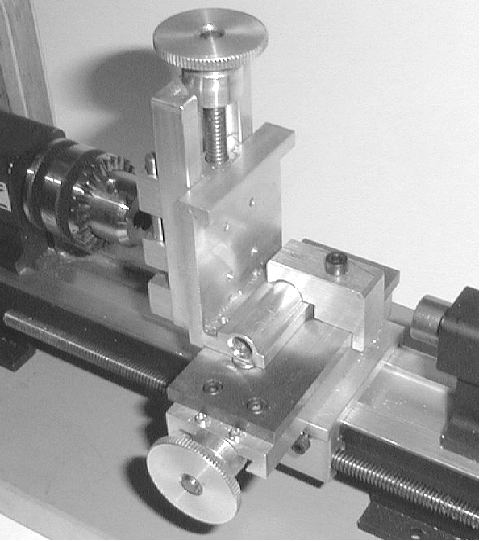 |
|
|
|
|
|
|
|
This vertical slide is not a Clisby production, but a simple, neat and clever adaptation by Dr. Peter Clark of England. It utilises a standard cross slide, mounted on bracket which in turn is held by a clamp to a steel plate secured to the lathe cross slide with 4 Allen screws.
|
|
|
|
|
|
|
|
|
|
|
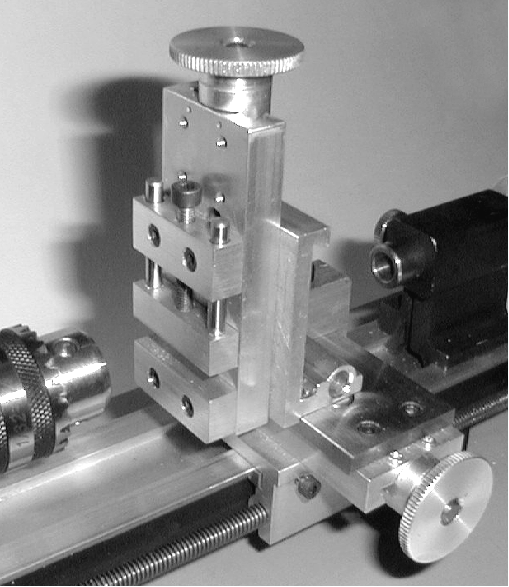 |
|
|
|
|
|
|
|
A simple (but beautifully made) vice is fastened to the top of the slide - the elements of its construction are obvious from the picture.
|
|
|
|
|
|
|
|
|
|
|
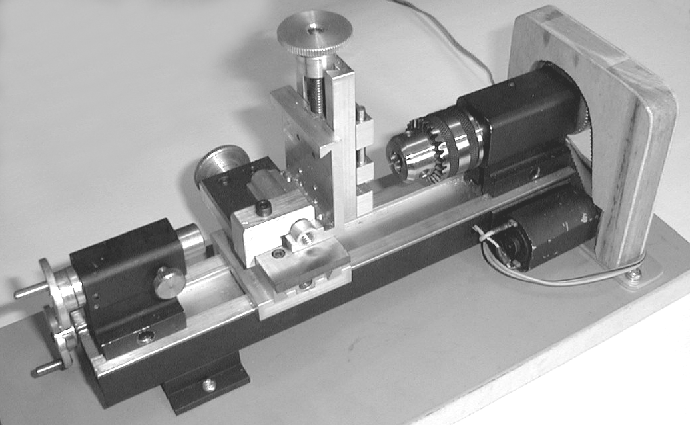 |
|
|
|
|
|
|
A rear view of the Vertical Slide mounting - also showing the simple swing-open cover that guards the drive pulley
|
|
|
|
|
|
|
|
|
|
|
|
|
|
|
|
|
|
|
|
|
email: tony@lathes.co.uk Home Machine Tool Archive Machine-tools Sale & Wanted Machine Tool Manuals Catalogues Belts Books Accessories
Clisby Lathe - Australia - also branded "Nextek" - Other Australian-built lathes: Advance, Burden, Clisby, Great Scott & Conrik, Hercus, A.E.Herbert, Premo, Qualos, Macson, Mars, Nuttall, Parkanson, Purcell, Rolfe, Sheraton, Tillico, T.N.C. Veem
|
|
|
|
|
|