 |
 |
 |
 |
 |
 |
 |
 |
 |
 |
 |
 |
 |
 |
 |
 |
 |
 |
 |
 |
 |
 |
 |
 |
 |
 |
 |
 |
 |
 |
 |
 |
 |
 |
 |
 |
 |
 |
 |
 |
 |
 |
 |
 |
 |
 |
 |
 |
 |
 |
 |
 |
 |
 |
 |
 |
 |
 |
 |
 |
 |
|
|
|
|
|
|
|
|
|
|
|
|
|
|
|
|
|
|
|
|
|
|
|
|
|
|
|
|
|
|
|
|
|
|
|
|
|
|
|
|
|
|
|
|
|
|
|
|
|
|
|
|
|
|
|
|
|
|
|
|
|
|
|
|
|
|
|
|
|
|
|
|
|
email: tony@lathes.co.uk Home Machine Tool Archive Machine-tools Sale & Wanted Machine Tool Manuals Catalogues Belts Books Accessories
Britannia Lathes & Other Machine Tools
Britannia Lathes Continued Here
Britannia Shapers, Planers & Milling Machines
Britannia Lathe Photographs Ornamental Turning Attachments
A Britannia publication is available - a wonderful 225 page technical book detailing the lathes and how to use them - with an emphasis on ornamental turning of which the author, J. Lukion B.A.,was an acknowledged expert. The back of the book has an additional and well-illustrated 194-page advertising section.
Britannia was an English engineering company with roots in Colchester, Essex, where they are known to have had a foundry making nails in the early years of the 19th century. Over the decades their product range bevcame extensive and included, amongst many others items, sewing machines, machine tools, industrial oil engines, and electric and conventional passenger cars. Names associated with the company include Tommy Bear who, together with an ironmonger called Bloomfield, began the "Britannia Sewing Machine Company" (does anyone have a 'Britannia' sewing machine ?) with the Bloomfield side of the Business continuing into the 1980s. With the increasing market dominance of the efficiently mass-produced Singer machines, Bear & Bloomfield found their sales shrinking and were forced to diversify; they found a ready market for model-engineering tools kits and simple lathes for the amateur and hobbyist that led, in 1871, to the formation of the "Britannia Lathe and Oil Engine Company Ltd." In 1896 the company formed the "Britannia Electric Carriage Syndicate Ltd.", based in Colchester, and started to build electric passenger cars. By 1898 the company was known as "The Britannia Motor Carriage Company Ltd." and had moved its production facility to the Britannia Motor Mills, Woodstock Road in Shepherd's Bush, Middlesex. Company advertising of the time showed that the firm was not only able to manufacture over 250 different kinds of metal and wood-working machines, but were also capable of fitting out an entire factory with them - complete with installed line shafting and gas and oil engines to drive them. Specialist departments within the company also undertook more difficult tasks - some beyond the capabilities of other well-known lathe makers - including the production of leadscrews (up to 40 feet in length) change wheels and precision machine-cut gears of all types. Besides these high-value products, the company also diversified into the manufacture of forges and bellows, hoisting grabs, grindstones, stocks, dies and taps, tube cutters and expanders, vices, castings, iron-founders' moulding machines, cupolas, ladles, machine cutting tools, slide-rest tools - and a variety of technical publications issued under their own name. By 1899, just as the company were experimenting with an "oil-engined" car, control passed into the control of the Nicholson family; sensing the increasing demand for cars, a more conventional design was put into production, powered by a petrol engine with sales in the hands of the Victoria Carriage Works, Ltd. at 24-26 & 122-122 Long Acre. Unfortunately, the cars were not a success and, faced with stiff competition from the emerging motor manufactures in the English midlands - who had ready access to specialist raw materials and a easy supply of skilled labour - production had ceased by 1909. The company then concentrated on machine-tool and other engineering products and survived until the early 1930s - when they disappeared without trace. Early Britannia lathes (of which the smaller examples are relatively common) were of very light construction, with little in the way of unusual features or advanced engineering; later machines were much more heavily built but are, strangely, almost unknown today Britannia made such a bewildering variety of lathes that today it is unusual to find two exactly the same; unfortunately, very little Britannia sales literature seems to have survived - it appears to have been mainly produced in book form, or as a supplement to a book - and should any reader possess catalogues or sales folders (or has an original lathe they would be willing to photograph) the author would very much like you to hear from you.
|
|
|
|
|
|
|
|
|
|
|
|
|
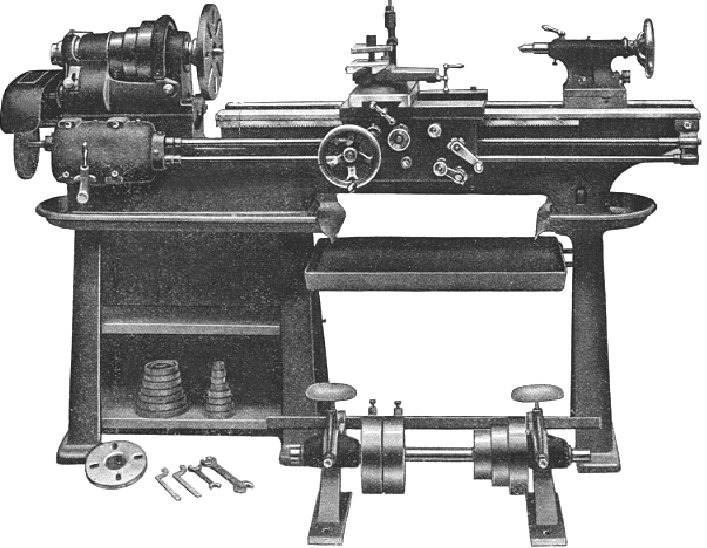 |
|
|
|
|
From the early 1930s, this Britannia would have been one of the last made. It was available in two versions: the 6.5" centre height model had a 1.375" spindle bore and admitted 44" between centres while the 7" centre-height version had a 1.5" bore and took a generous 56" between the headstock and tailstock - or loose headstock, or poppet head - as older manufacturers called it. The lathe was available in a wide range of specifications to suit a customer's needs and pocket; the headstock was either "all-geared", or a simple, belt-driven affair, with a choice of adjustable bronze or taper-roller bearings and the feed to the leadscrew (via a conventional tumble reverse) could be through an economical 3-speed box (illustrated) - or a full Norton-type quick-change screwcutting gearbox with the ability to generate 33 English threads. Even though the makers offered a further option in the form a replacement headstock-end leg containing a motor-countershaft drive system with endless, automatically self-tensioning belts for the geared-head model, they still mentioned the availability of an old-fashioned treadle drive with "forged-steel arms". The separate power shaft for sliding and surfacing speeds, shown parallel to the leadscrew in the picture above, was also an optional extra. Although of conventional appearance and construction, the lathe did feature one Britannia Trademark - an unusual toolpost base, just visible in the illustration above, that carried a wedge-like mechanism by which means the tool height could be set without the need to find loose packing
|
|
|
|
|
|
|
|
|
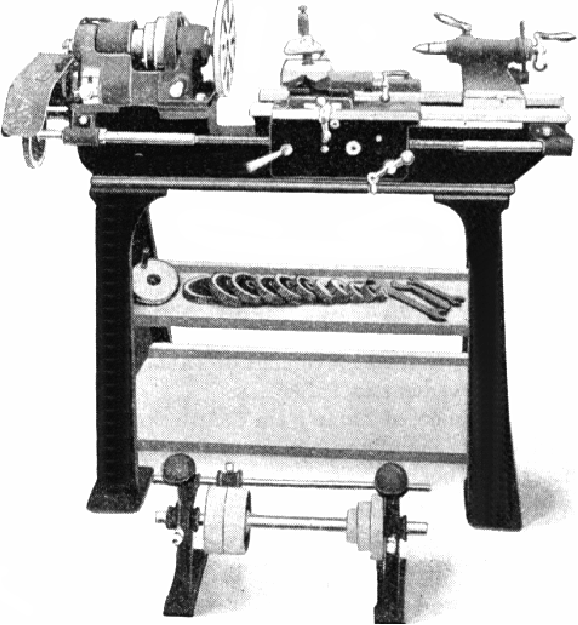 |
|
|
|
|
4.5" and 5" Britannia lathe with 20" and 38" inches between centres respectively. The smaller lathes appeared almost as miniatures of their bigger brother, and retained the option of screwcutting by changewheels or a screwcutting gearbox - and with or without a power shaft for sliding and surfacing feeds; however, on this model, there was no 3-speed leadscrew gearbox available. The bed had a "fixed" gap, able to swing 15" for the 4.5" model (Probably the Model "GO" ) and 16" for the 5", whilst the saddle arms were almost disproportionately long for the bed - although this would certainly have helped to even out wear along its length.
|
|
|
|
|
|
|
|
|
|
|
|
|
|
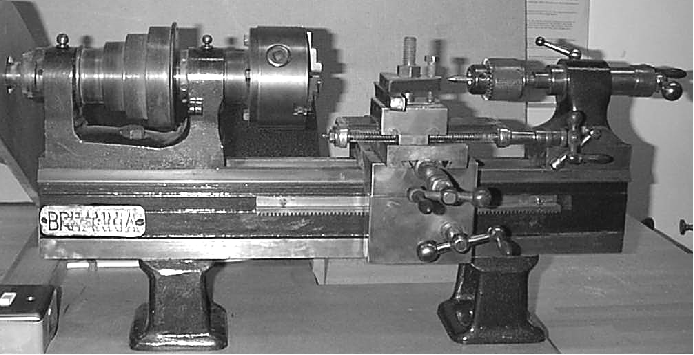 |
|
|
|
|
A small lathe, of obvious quality, carrying an aluminium plate proclaiming both "Colchester" and "Britannia". The twin raised Vees of the bed guide both the saddle and tailstock - the latter being of a most unusual pattern. The size and style of the micrometer dials would indicate a lathe built before about 1930, and possibly a lot earlier.
|
|
|
|
|
|
|
|
|
|
|
|
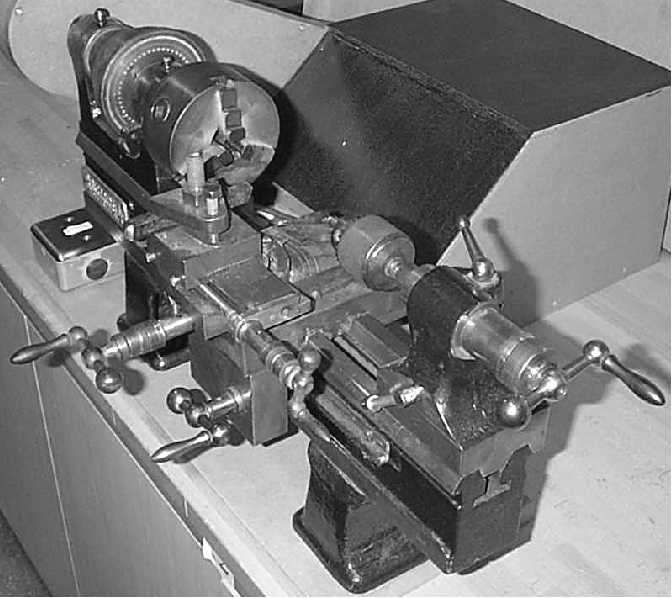 |
|
|
|
|
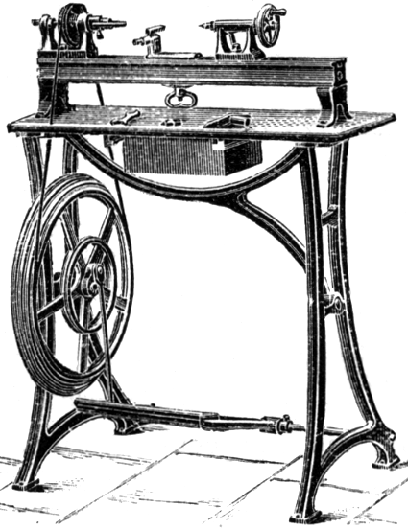 |
|
|
|
|
|
|
|
From the maker's catalogue of 1899 - showing the No. 2 and No. 3 lathe on its own special treadle-power stand.
|
|
|
|
|
|
|
|
|
|
|
|
|
|
|
|
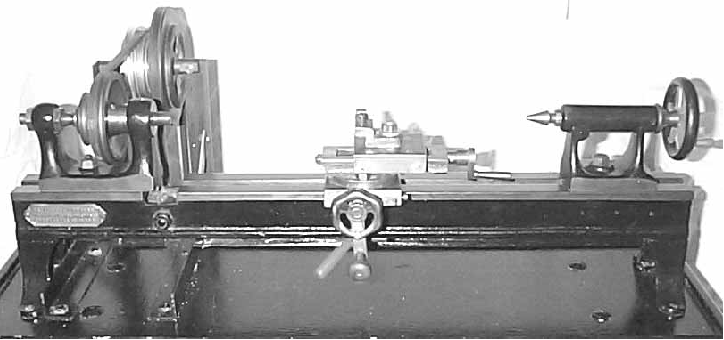 |
|
|
|
|
|
|
|
|
|
This very early, possibly pre-1880, plain turning Britannia lathe Model No. 3 shown above and in the photographs below has an overall length of 29.75", a height of 5.25 inches and a bed 2.5" wide. The centre height is 3 inches and the capacity between centres 18". The headstock spindle is carried in a single bearing - with its left-hand end held against a pointed support carried in an adjustable holder that fits into the space normally occupied by the left-hand bearing. This was a popular way, at the time, of arranging the headstock of a light-duty lathe and, despite its shortcomings, was a design that many makers persisted in using for several decades. The 3-step headstock pulley was not intended to use a V belt - it would be several decades before they appeared - but a round leather "rope", that is severely limited in the amount of torque it can transmit.. The tailstock is equally vestigial, though adequate for such a light-duty machine; two slender supports holding the barrel chamber. The cross feed handwheel in the photographs below is not correct - originally it would have been identical to that used on the top slide,. When originally supplied that lathe could have been ordered in one of three bed lengths: 3 feet, 3 feet 6 inches and 4 feet; at an extra cost of £1 a gap bed could also be supplied.
|
|
|
|
|
|
|
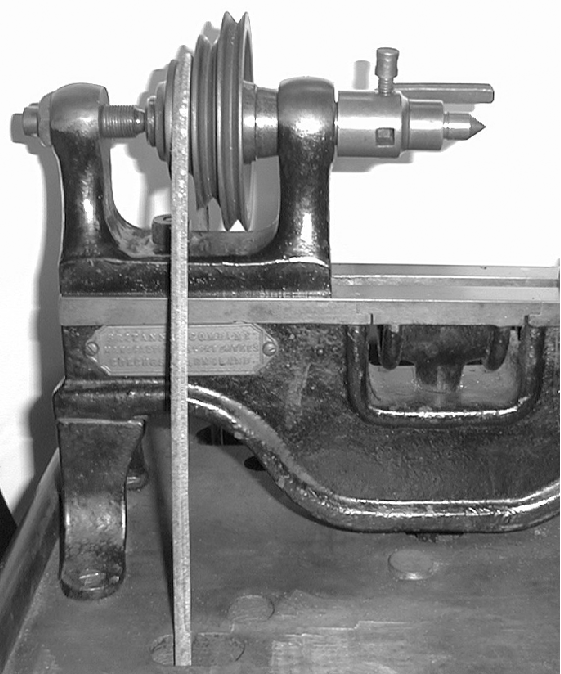 |
|
|
|
|
The headstock spindle runs in a single bearing with the left-hand end of the shaft supported against a hardened steel centre. Because the spindle is solid the No. 1 Morse taper centre is held in a screw-on extension piece which doubles as a simple catch plate for driving work between centres.
|
|
|
|
|
|
|
|
|
|
|
|
|
|
|
|
|
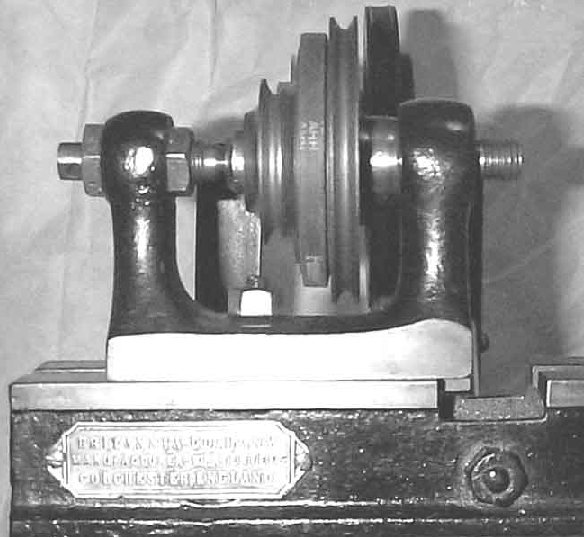 |
|
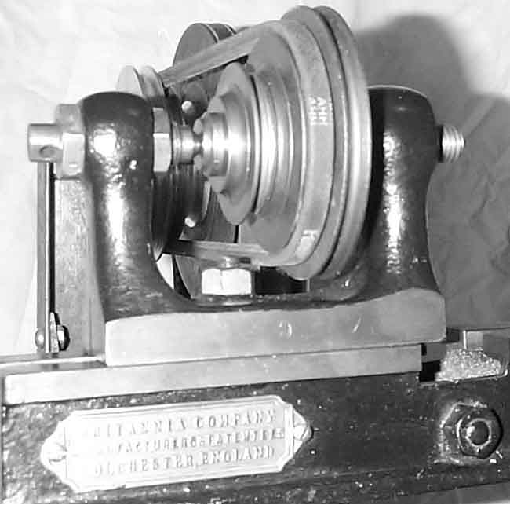 |
|
|
|
|
|
|
The headstock sockets into the bed ways - but is held in place by just a single bolt. The point which supports and acts as a bearing for the left-hand of the headstock spindle can be clearly seen.
|
|
|
|
|
|
|
|
|
|
|
|
|
Designed to accept round leather "rope", the profile of the headstock belt pulley is clearly visible in this picture.
|
|
|
|
|
|
|
|
|
|
|
|
|
|
|
|
|
|
|
|
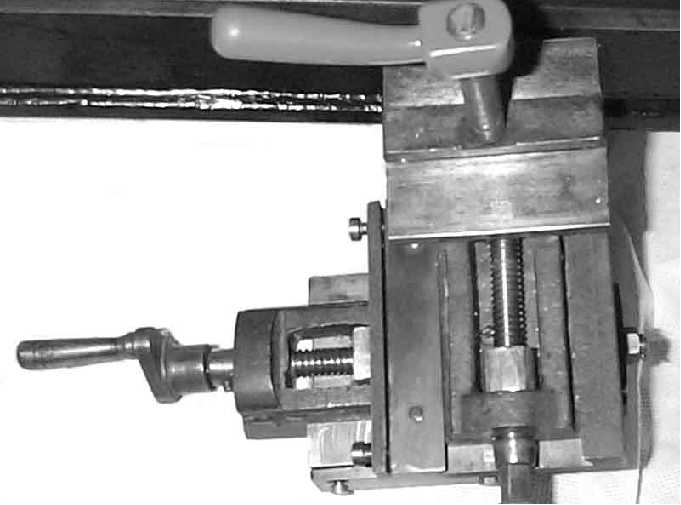 |
|
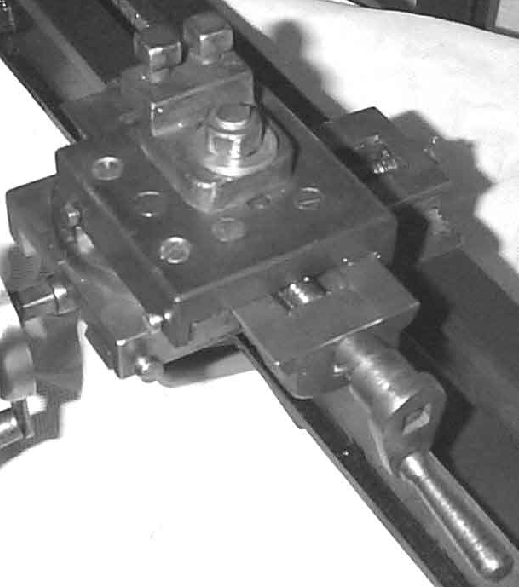 |
|
|
|
|
|
|
A view beneath the compound slide rest. Note the cross feed nut, hard up against the end of the casting.
|
|
|
|
|
|
|
|
|
|
|
|
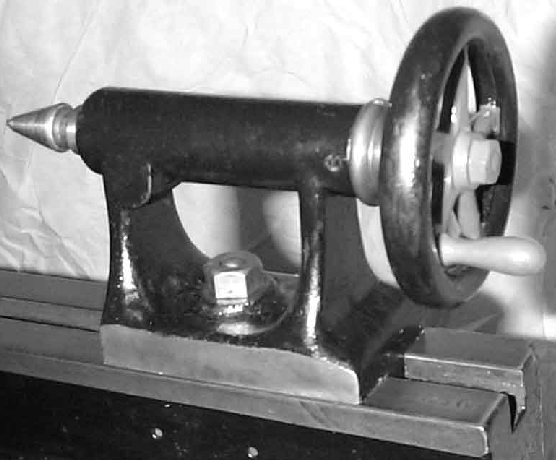 |
|
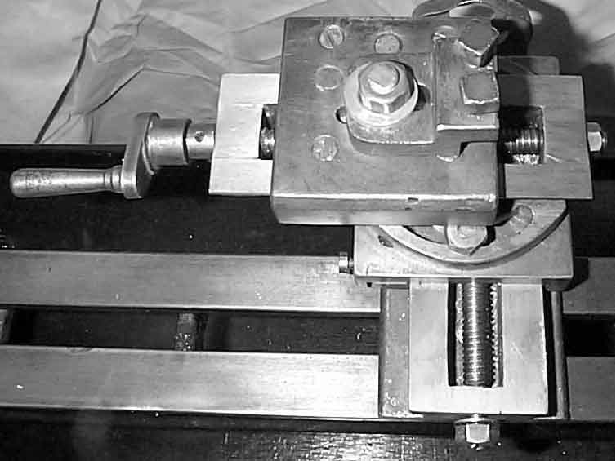 |
|
|
|
|
|
|
Though cast from a minimum of material the tailstock, was entirely adequate for so light a machine. Instead of the usual quick-wearing, Whitworth-form thread and hopelessly-inadequate screw-in barrel lock, Britannia gave their customers a proper square-form thread, an efficient barrel lock of the split-clamp type and a comfortably large handwheel.
|
|
|
|
|
|
|
|
|
|
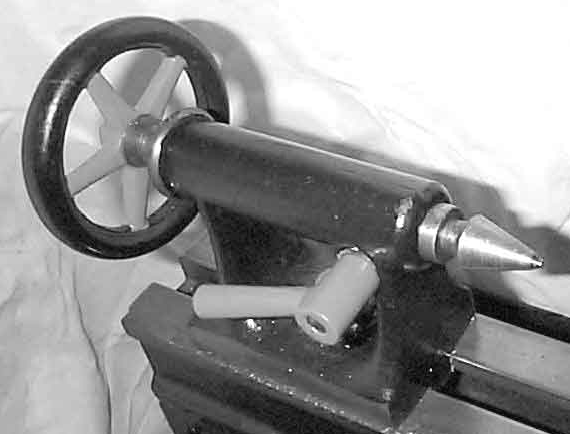 |
|
|
|
|
|
|
|
|
|
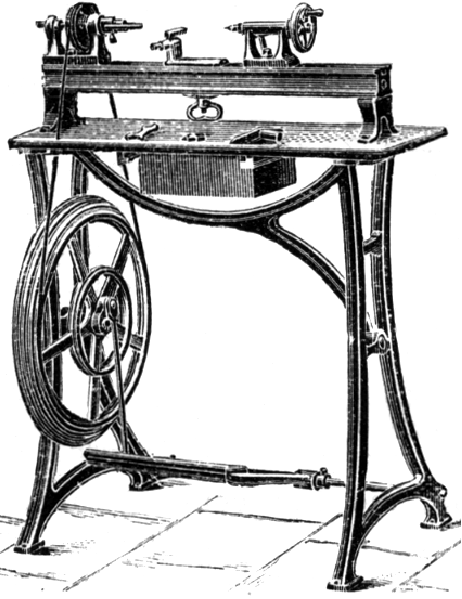 |
|
|
|
|
The Britannia Nos. 2, 3 and 6 plain-turning lathes were described by the makers as being suitable for, "Amateurs, Jewellers, Dentists or any Light Use." The No. 2 lathe had a 24-inch long bed that allowed 14 inches to be admitted between the centres - that themselves were 2.5" above the planed, cast-iron bedways. The cost of the basic machine was £1 : 15s : 0d. - but when fitted to the cast-iron stand with its tool drawer, polished wood top, treadle assembly and 18-inch diameter flywheel this rose to £3 : 10s : 0d. The No. 6 lathe, somewhat displaced in the model numbering sequence, was Britannia's cheapest offering at £2 : 15s : 0d and came complete with a treadle stand. In appearance the No. 6 was identical to the No. 2 - but with a shorter bed admitting 11 inches between centres. Photographs of a No. 3 lathe can be seen here.
|
|
|
|
|
|
|
|
|
|
|
Britannia Lathes 2, 3, 4, 5 & 6 Britannia lathes closely reflected the standard design practices of their day, that is, they already had many of the features of lathes that would still be in production a hundred years later - but were of a comparatively light build. Because all the larger Britannia lathes featured a "plate", supported on twin posts, that passed across the left-hand end of the headstock spindle to absorb spindle-end thrust, they (the spindles) could not be made hollow. The makers, with their Victorian training, must have assumed that the machines would have been largely used in the traditional way, with work supported between centres, and did not consider the needs of the general repair shop or mechanic to whom a hollow spindle (or "mandrel" in contemporary language) would have been of great use. The increasing use of self-centring 3-jaw chucks also created a demand for hollow spindles and, by the early years of the twentieth century, Britannia, together with most other makers, followed the practice, established more than 50 years previously, of arranging for the spindle thrust to be taken on the inside face of the headstock casting, allowing the end of the spindle to be left and open and clear…. The smaller, plain-turning lathes Numbers, 2, 3, 4, 6 and 8 (illustrated on this page) had a headstock spindle carried in a single bearing - with its left-hand end held against a pointed support carried in an adjustable holder that fitted into the space normally occupied by the left-hand bearing. This was a popular way, at the time, of arranging the headstock of a light-duty lathe and, despite its many shortcomings, was a design that many makers persisted in using for several decades. The 3-step headstock pulley was not intended to be driven by a V belt - it would be several decades before they appeared - but a round leather "rope", "gut band" or "cord" as it was variously called, that severely limited the amount of torque it was possible to transmit. The lathes were designed for bench mounting, but were generally offered on a very slim, cast-iron stand with a treadle flywheel assembly; the design of this stand differed somewhat during the years of production with an even lighter assembly used for the No. 2 and No. 3 lathes.
|
|
|
|
|
|
|
|
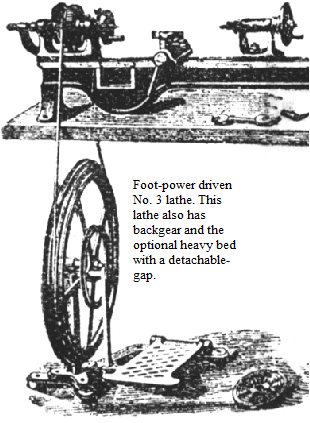 |
|
|
|
|
|
The headstock pulleys of the No. 2, 3 and 6 lathe all had 3 belt grooves but, whilst the flywheel of the No. 6 lathe had 3 belt grooves to match, the flywheels of the other models all had 4. This arrangement allowed the drive belt to be run at an angle from the flywheel to headstock - and so provide an extra two speeds. The belts could be joined with a variety of fasteners, from a simple wire hook to a quick-release twist fitting that, if properly organised, allowed an extra length of belt to be spliced in allow even greater cross-over angles from flywheel to headstock pulley. The No. 3 lathe was a little larger, the bed being some 6 inches longer and the centre height increased to 3 inches. The stand and treadle were identical to those used on the No. 2 lathe, but the flywheel was made 2 inches greater in diameter and a little heavier. The price was £2 : 5s : 0d as a bench model, or £4 : 5s : 0d. on the treadle stand A gap in the bed was optional for both the No.2 and No. 3 models and cost an extra 10 shillings - however, at this price, this gap did not bring with it a new bed of deeper section; instead, a small portion of the bed was simply cut away in front of the headstock….. Both models could also be ordered, for £1 : 10s : 0d extra, with its headstock spindle and bearings in hardened steel. Backgear was also available on the No. 3 lathe but, as this involved an entirely different headstock with two
|
|
|
|
|
|
|
|
|
|
|
spindle bearings, and the end thrust taken by a swan-neck casting bolted to the end of the bed (the arrangement can just be made out in the picture above), the cost almost doubled to £4 : 0s : 0d. When fitted with backgear the lathe could also be specified with a heavier pattern of bed, based on that used for the No. 13 lathe, where the section that bowed downwards as it approached the headstock held a proper detachable bridge - and all for an extra charge of just £1. Besides the maker's self-contained treadle stand, a "foot-motor" was offered so that the owner could make his own mounting arrangements - yet still enjoy the benefits of human-powered turning. With the basic machine, the first owner received two hardened centres, a driver chuck or catchplate for between centres work and a hand rest with two different lengths of Tee. Detailed photographs of a No. 3 lathe, as well as can a version on a different design of stand, can be seen here,
|
|
|
|
|
|
|
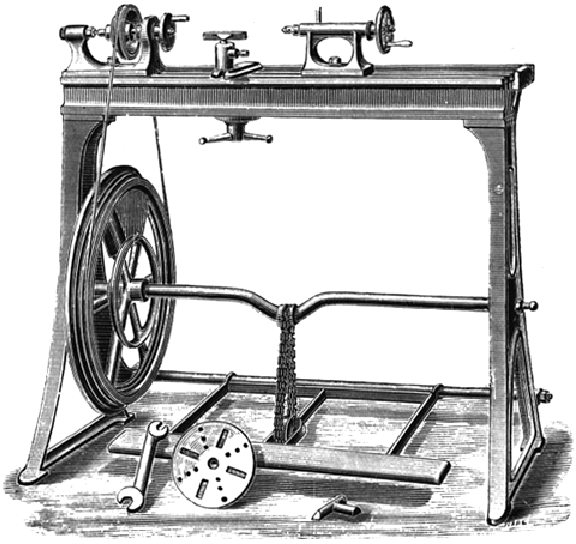 |
|
|
|
|
The No. 4 Britannia "Improved Foot Lathe" was available with centre heights of 3.5, 4, 4.5 and 5 inches, and in bed lengths of 36, 42 and 48 inches - the 36 inch bed accepting 18 inches between centres. It was the smallest of the Britannia lathes to bolt directly to the legs of its stand rather than having bed feet to allow bench mounting. This was a much more expensive lathe than the No. 3, costing some £8 in basic form and as much as £11 : 10s : 0d in long-bed , 5-inch centre height form. The machine was supplied from the factory on a treadle-power stand with an adjustable hand rest with two sizes of T, two faceplate (large and small) a pair of centres, a spanner and a wooden tool-table fastened to the back of the stand.
|
|
|
|
|
|
|
|
|
|
|
|
|
|
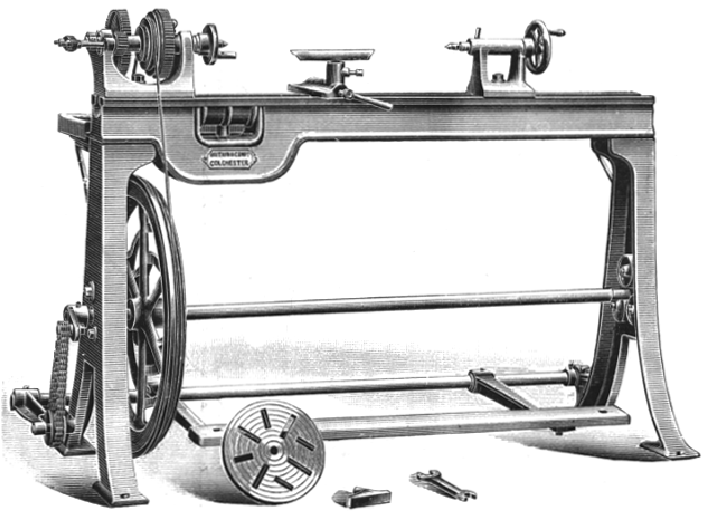 |
|
|
|
|
|
|
Plain-turning, light-duty Britannia lathe No. 5 shown with the optional backgear. The centre height could be 4, 4.5 or 5 inches to order and the bed 48 inches long. Because backgear is fitted to the headstock, the spindle (unlike that on the lighter version of the lathe illustrated here) has two bearings, but with the thrust still absorbed by a ball bearing held within a plate retained by two long studs at each side of the left-hand bearing. When used as a metal-turning lathe, the backgear assembly would have substantially improved the versatility of the lathe - and allowed the operator to overcome, to some extent, the severe limitations on rates of metal removal imposed by the round-rope drive. The counterbalanced flywheel was supported on a long shaft and, in an attempt to reduce the considerable drag induced by running this in plain bearings, the makers fitted an unusual "three-roller" system at each end; this mechanism can just be glimpsed within the tailstock-end leg. Unfortunately, each of the rollers ran on plain-bearings shafts …… The driving crank attached to the flywheel shaft was positioned outside the left-hand leg (Britannia called the legs "standards") and was fitted with a slotted arm so that the operator, or his assistant) could choose to vary the leverage (and speed) applied to the job. The counterbalancing of the flywheel avoided the time-wasting situation where it stopped at "dead centre", and refused to turn over - unless moved first by a persuading hand or foot. The smallest version, with a 4-inch centre height and no backgear, sold for £11 whilst the most expensive standard model, with 5 inches of centre height and backgear, retailed for £14 : 10s : 0d. A different model, but still marketed as a No. 4, was available with a 5 foot long bed, 1 inch wider than the standard 4 inches (and of heaver section) that admitted 28 inches between centres.
|
|
|
|
|
|
|
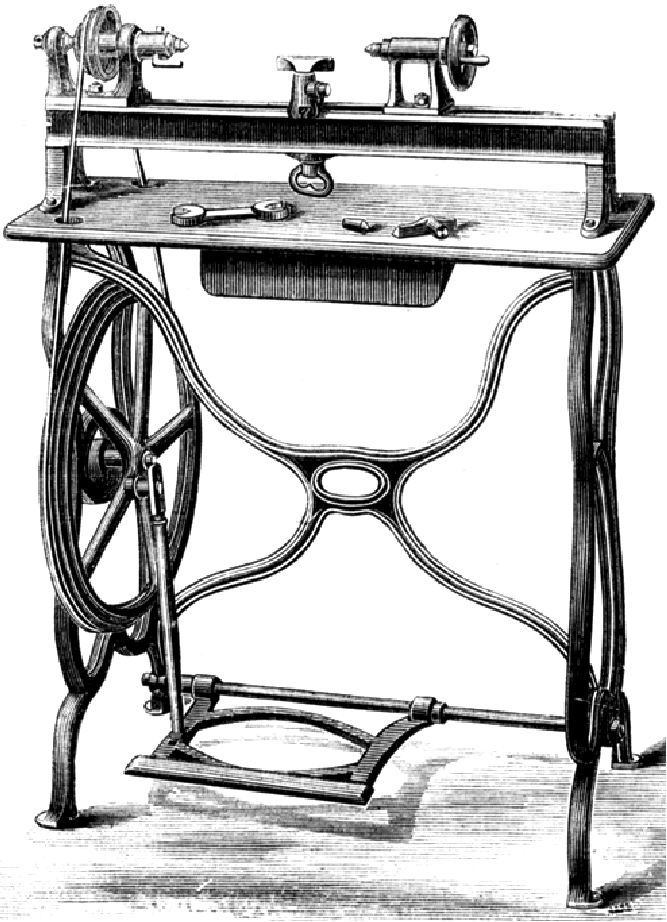 |
|
|
|
|
An ornate, X-shaped diagonal bracing points to this being one of the earlier-pattern stands for the Britannia Nos. 2, 3 and possibly No. 6 lathe.
|
|
|
|
|
|
|
|
|
|
|
|
|
|
|
|
|
|
|