 |
 |
 |
 |
 |
 |
 |
 |
 |
 |
 |
 |
 |
 |
 |
 |
 |
 |
 |
 |
 |
 |
 |
 |
 |
 |
 |
 |
 |
 |
 |
 |
 |
 |
 |
 |
 |
 |
 |
 |
 |
 |
 |
 |
 |
 |
 |
|
|
|
|
|
|
|
|
|
|
|
|
|
|
|
|
|
|
|
|
|
|
|
|
|
|
|
|
|
|
|
|
|
|
|
|
|
|
|
|
|
|
|
|
|
|
|
|
|
|
|
|
|
|
|
|
|
|
|
email: tony@lathes.co.uk Home Machine Tool Archive Machine-tools Sale & Wanted Machine Tool Manuals Catalogues Belts Books Accessories
Britannia Milling Machines, Shapers and Planers Britannia Home Ornamental Turning Attachments Britannia Lathe Photographs
A Britannia publication is available - a wonderful 225 page technical book detailing the lathes and how to use them - with an emphasis on ornamental turning of which the author, J. Lukion B.A.,was an acknowledged expert. The back of the book has an additional and well-illustrated 194-page advertising section. In comparison with the great variety of types and sizes of lathe that Britannia offered, their milling machines appeared to have been few both in the type and number of variations offered. Typical of their vertical milling machines listed in the last years of the 19th century was the No. 14, a simply designed, modestly-sized affair with a 24" x 8.5" table power driven along the 18 inches of its longitudinal axis - but requiring hand feed on the 7.5-inches of cross feed, as well as on the generous 14 inches of vertical travel. None of the feed screws were fitted with micrometer dials. Because the belts driving the table feed were flat, and needed to go round rather small pulleys, a mechanism was devised that gave them the maximum amount of "wraparound" - and hence grip. The arrangement of the belts was, of necessity, rather a convoluted one and began with a small 3-step pulley mounted on a extension to the back of the horizontal drive spindle; this drove down to a matching pulley carried in a bracket at floor level to the rear of the main column. From there the drive was carried forwards to a system of three parallel pulleys - around which the final drive belt must have been wrapped - and hence to the small pulley and its attached worm gear at table level. Echoing Britannia lathe practice, the miller's 1.625-inch diameter vertical spindle had an adjustable thrust plate supported outboard on two columns; unfortunately, this type of arrangement precluded the fitting of cutters held in place with a draw bar - the spindle being blocked at the end and unable to be bored clear through. The spindle carried a 4-step cone pulley, driven by a 2.25" wide flat belt, with a largest diameter of 8.5 inches - and a smallest of 3.75 inches. A lathe-like backgear assembly was fitted, greatly increasing the capacity for heavy, slow work, whilst the head of the machine was braced by a cast-in overarm. The large hole through the centre of the machine's body was to accommodate extra long workpieces - a useful facility that allowed the miller to tackle jobs that might otherwise have demanded the use of a much larger and more-expensive-to-operate machine..
|
|
|
|
|
|
|
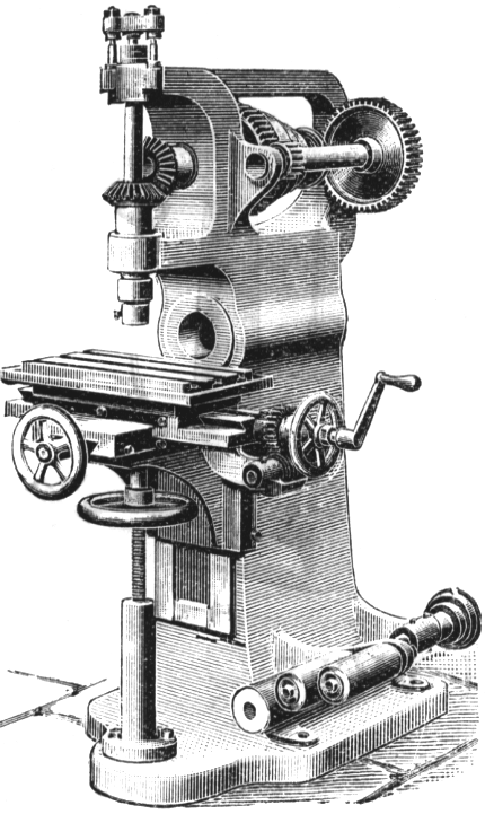 |
|
|
|
|
|
|
Britannia No. 14 Vertical Miller
|
|
|
|
|
|
|
|
|
|
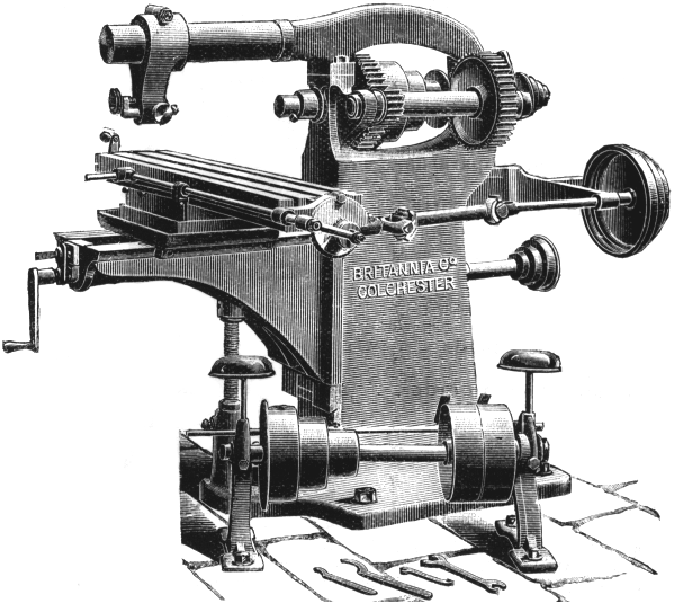 |
|
|
|
|
|
|
The Britannia No. 13 Horizontal Miller was a large machine with a 45-inch long table; the longitudinal travel was 21 inches, the cross feed 8 inches and the vertical movement 16 inches. The table power feed was arranged in a manner not dissimilar to that still employed today, with a pulley arrangement on the back of the miller's main body driving a universally joined and splined shaft connected to a gear that could be hinged up and down to engage with a worm fastened to the table feed screw. Automatic stops were provided to disengage at the feed at any point in its travel; the trip bar, operated by stops carried in a T slot on the front of the table, pushed the worm and wheel assembly out of engagement with the feed screw. The main spindle carried a 3-step pulley, driven by 3-inch wide flat belt, and incorporated a lathe-like backgear for amplified torque at low speeds. Only 4 feet 4 inches high, the work table must have been at an uncomfortably low position (even if it did save the makers a good deal of cast iron in its construction). 6 feet from to back the miller weighed 22 cwt.
|
|
|
|
|
|
|
|
|
|
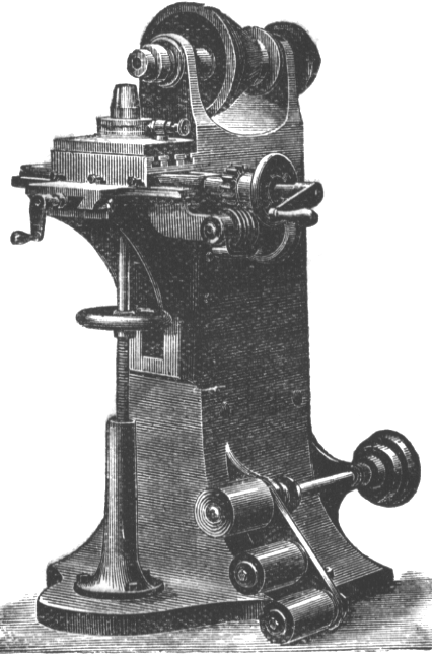 |
|
|
|
|
|
|
|
The Britannia No. 10 horizontal "stub" miller was intended for light use by "Engineers, Brass Finishers, Gunsmiths, Sewing machine, Bicycle and other small machine makers." The 4-step cone pulley was driven by 2-inch wide flat belt and the spindle nose was both threaded and coned internally to take "chucks" (collets) although no details have survived as to the type or size of their fitting. The work table was 11.75" x 6", with three large T slots and is shown in the illustration fitted with the maker's simple dividing apparatus. The same design of table power feed as used on the No. 14 miller was employed with more pulleys and belts than a Victorian engineer could shake a stick at.
|
|
|
|
|
|
|
|
|
|
|
|
|
|
|
|
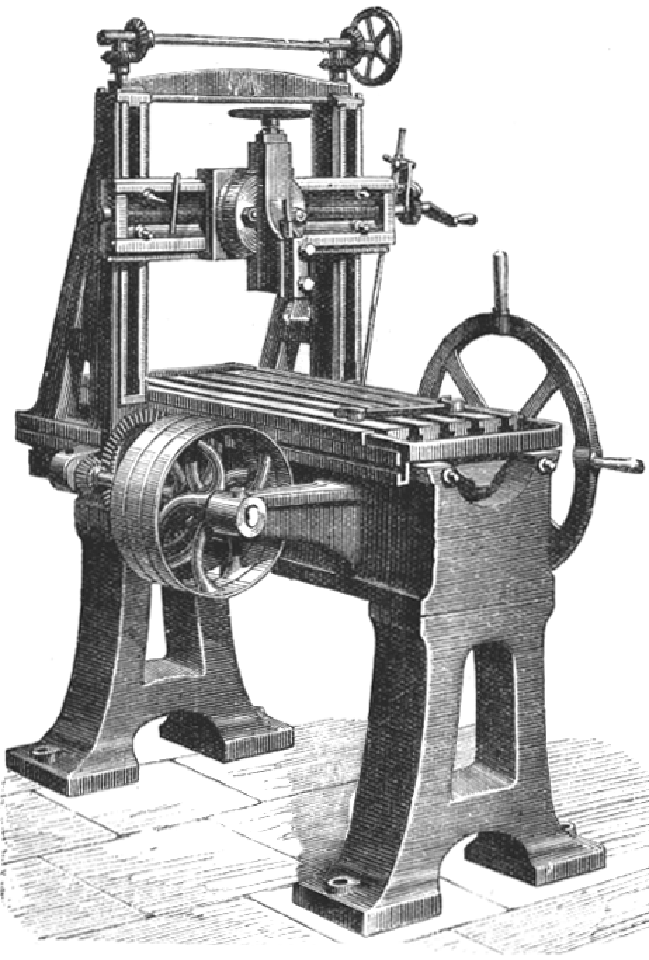 |
|
|
|
|
Not greatly different to any of a number of other similar-sized machines on the market during the later years of the 19th century, the Britannia used an interesting if not unique drive system: a countershaft unit with a 3-section "fast-and-loose" pulley set was driven by a single belt that passed between two striker "hooks"; the hooks were controlled by a mechanism linked into the machine's motion in such a way that they could throw the belt from one outside pulley to the other. If the belt-shifting mechanism was disengaged, the belt came to rest on the centre pulley that, being free to spin on the shaft, stopped the feed. Reference to one of the photographs below will show what appears to be a single shaft emerging from the drive pulleys and carrying two pinion gears, each engaged with its own crown wheel; in fact, there are two shafts, running concentrically one within the other - and each independently driven by one or other of the outer pulleys. With the belt positioned in the middle, or idle, position the drive was started by lifting a lever that engaged the belt-shifting mechanism and positioned the belt on the right-hand pulley. This pulley drove the outer of the two pinion gears that caused the table to be driven, at cutting speed, under the tool box. As the table came to the end of its travel a trip bar caused the belt shifter to fling the belt across to the left-hand pulley, and so engage the drive to the inner of the two pinions. Being "higher-geared" this returned the table at high speed to its starting point with the tool-carrying clapper box being knocked backwards on its hinge as the workpiece passed beneath it; from the returned position, the cycle automatically began again. For hand feeds a large-diameter wheel, with capstan-like handles, with was fitted to the input shaft - let us hope that this could be disengaged whilst the planer was being used under power. The cutter head was power fed across the job by the use of a simple ratchet feed, operated by a long rod that reached down and engaged with the table-drive mechanism..
|
|
|
|
|
|
|
|
|
|
Britannia "self-acting" planer with automatic table drive and quick-reverse mechanism.
|
|
|
|
|
|
|
|
|
|
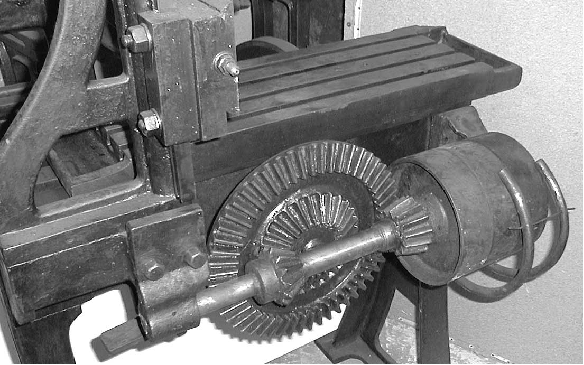 |
|
|
|
|
|
|
A Milnes planer fitted with a drive system identical to that used on the Britannia.
|
|
|
|
|
|
|
|
|
|
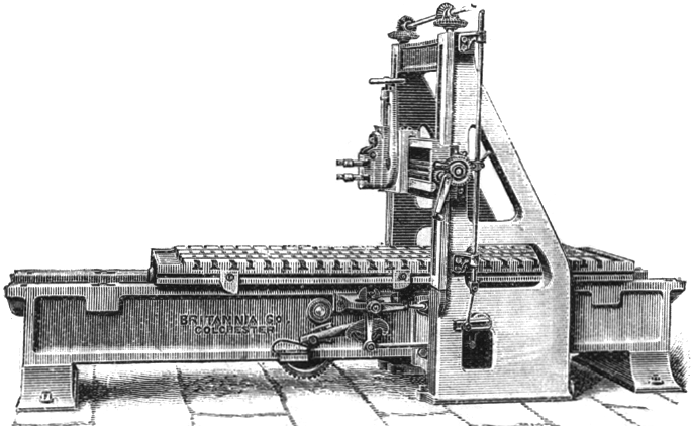 |
|
|
|
|
|
|
Britannia No. 8 Planing Machine with a 12 foot long by 25-inches wide bed. Built to special order only, this was one of the company's largest planers, the tool able to travel 8 feet horizontally and 39 inches laterally.
|
|
|
|
|
|
|
|
|
|
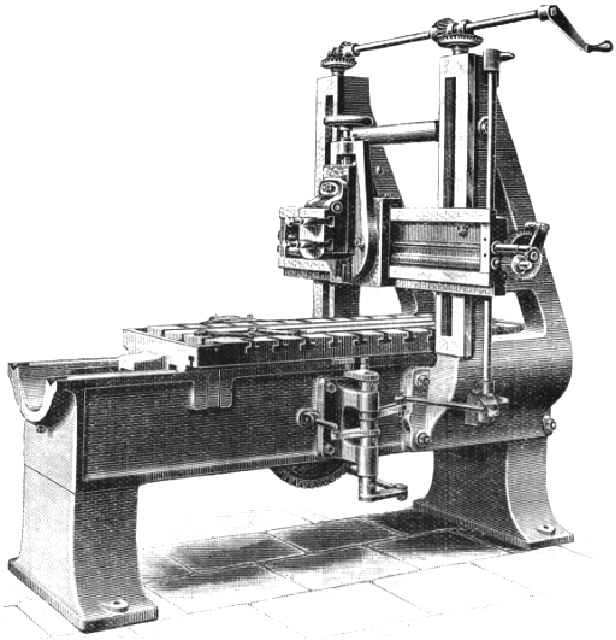 |
|
|
|
|
Britannia No. 6 Planing machine. This was a heavily-built machine, able to plane a piece of metal 4 feet long, 2 feet wide and 2 feet high. The table, which ran on V ways, was carefully designed to allow the clamping of unusually-shaped workpieces, being made unusually thick, and carrying T slots both longitudinally and cross-ways. The table feed was automatically reversed at high speed, but by an enclosed gear mechanism, rather than by an arrangement of belts and crown-wheel and pinions as in the company's smaller machines. The No. 7 planer was very similar, but had a planing capacity of 6 feet, by 2 feet 6 inches by 2 feet 6 inches.
|
|
|
|
|
|
|
|
|
|
|
|
|
|
The Planer
At one time the planer was considered an indispensable part of any machine shop; using very inexpensive tooling they were able to machine large components with relative ease. Some examples were gigantic, with beds fifty or sixty feet long and able to accommodate work sixteen feet high, whilst other were fitted with either fixed or pivoting grinding or milling heads in place of the ordinary "clapper-box" tool holder and so became known as "planer-millers" or "planer-grinders" - or, in some regions, "plano-millers"and "plano-grinders". On larger examples it was common to find more than one tool box fitted; the cross-rail (or cross-head) would often carry two, side by side, with several extra ones sometimes mounted at the bottom and sides of the cross-rail support columns. In addition, even smaller examples were sometime fitted with two cross heads, often adjustable in position along the bed and each fitted with multiple toolboxes. Some planers were made "open-sided" to accommodate even larger jobs that could hang over one edge of the table, and as the species developed it became increasingly difficult to differentiate between planers and true millers - examples made by the huge American Niles-Bement-Pond Company included: Multiple Spindle Horizontal Milling Machines, Horizontal Slab Milling Machines, Horizontal Slab milling machine, Rod Milling and Fluting Machine, Duplex Milling Machines, Forge Milling Machines, Plate Planers, Rotary Planers and End Milling Machines. Although the name changed according to the specific use, the principal of operation remained essentially the same, a long sliding table passing beneath (or between) single or multiple cuttings heads. Variations on the theme include Pit and Breast planers where the workpiece rested in a pit (or on a massive table) and the columns carrying the cross-rail and toolheads were made to travel over it; these huge machines were generally reserved for heavier kinds of armour-plate work. Planers have been made in almost every size increment imaginable, the smallest being tiny hand-operated units designed for bench mounting. Although rare, examples of planers suitable for the smaller workshop do occasionally turn up and are very sought after, not only for their novelty and historical value, but because they are still capable of their original task - the economical machining of large components in a limited space.
|
|
|
|
|
|
|
|
|
|
|
|
|
|
|
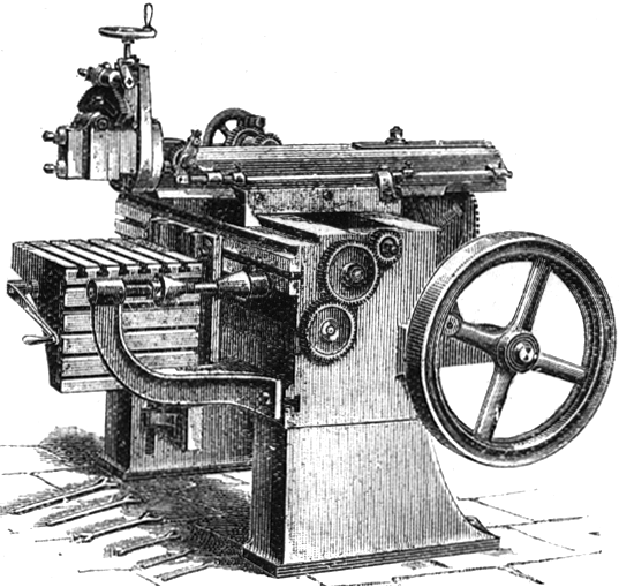 |
|
|
|
|
Britannia shapers, even the smaller models, were industrial-class machines and fitted with many features designed to enhance both their speed of working and versatility. The 1.25 ton, 12-inch stroke No. 33 machine, illustrated above, had a 16 inch by 14.5" table with 6 closely-spaced T slots machined in the top (and a T-slotted right-hand vertical surface) that could be traversed a total distance of 24 inches from side to side under either hand or power feed. The ram was fitted with a rack on its underside and driven directly from a large-diameter gear beneath. The toolholder not only swivelled on the end of the ram - as was normal - but was also fitted with an ingeniously-designed power feed, operated through a ratchet mechanism tripped by a rod fastened to the side of the ram; the details are just visible in the picture below. In addition the toolbox was fitted with worm-and-quadrant gearing that allowed it to be independently tilted and so aid, so the makers claimed, the process of shaping "internal curves". The worm could be released from the wheel, and quickly reset to its original position. In order to support longer jobs, which may have hung off the table, a bracketed roller support was provided that could be placed at either side of the table. Although heavily built - it weighed just under half a ton, the machine was not as rigid as it might have been; the two supporting legs were separate castings, and not joined at floor level - if they had been, and extended forwards, the table could have been given a (sliding) support under its front edge to resist the bending action of the ram when it was being used to the limit of its longest stroke.
|
|
|
|
|
|
|
|
|
|
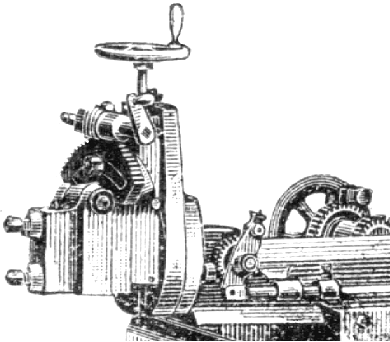 |
|
|
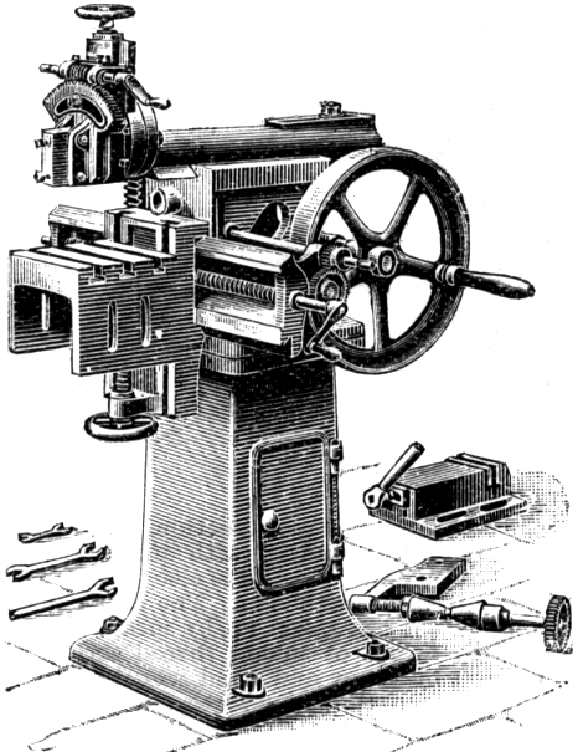 |
|
|
|
|
|
|
|
Britannia No. 33 shaper with Worm-and-quadrant gearing on the toolbox - and a rod and ratchet activated power feed to the tool slide.
|
|
|
|
|
|
|
|
|
|
|
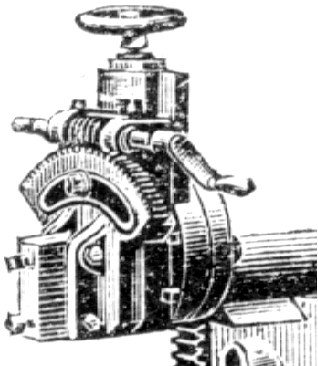 |
|
|
|
|
|
|
|
|
|
|
|
|
Above: a much smaller shaper, with a 6-inch stroke, the Britannia No. 31 could be bench mounted or fitted to this cast-iron column with shelves and a cupboard for tool and accessories storage. The 9-inch by 9-inch by 8-inch table had a movement of 25.5 inches across the bed - controlled by either hand or power feed - and 7.5 inches vertically with hand feed only. A self-acting circular motion was available as an extra. The driving pulley was a 3-step cone type (for flat-belt drive) and was fitted as standard with a handle so that the machine could also be used under hand feed - a useful feature for jobs requiring a particular sensitivity of touch.
|
|
|
|
|
|
|
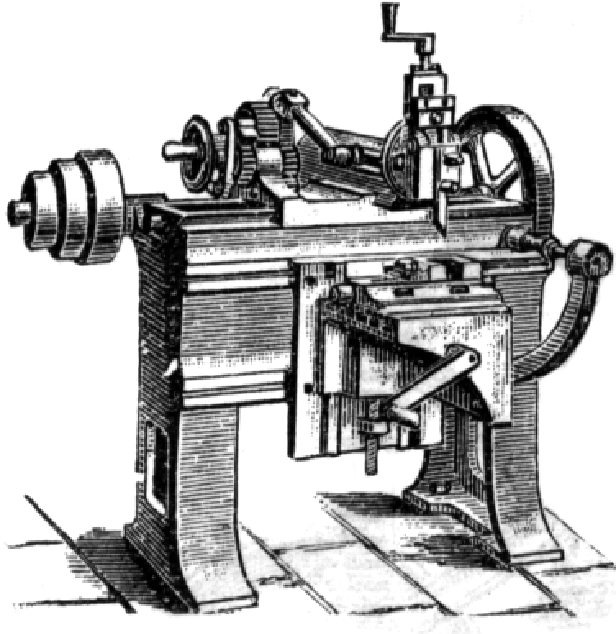 |
|
|
|
|
|
|
|
|
|
The 14.5 cwt. Britannia No. 29 9-inch stroke shaper carried its ram and driving mechanism on a sliding carriage which ran across the top face of the machine's body - design also used in Perfecto bench shapers between 1950 and 1970. The shaper could be ordered with an extra wide bedway, at £1 : 15s per foot - and even fitted with an additional tables at an additional cost of £6
|
|
|
|
|
|
|
|
|
|
|
|
|
|
|
|
|
|
|