 |
 |
 |
 |
 |
 |
 |
 |
 |
 |
 |
 |
 |
 |
 |
 |
 |
 |
 |
 |
 |
 |
 |
 |
 |
 |
 |
 |
 |
 |
 |
 |
 |
 |
 |
 |
 |
 |
 |
 |
 |
 |
 |
 |
 |
 |
 |
 |
 |
 |
 |
 |
 |
 |
 |
 |
 |
 |
 |
 |
 |
 |
 |
 |
 |
 |
 |
 |
 |
 |
 |
 |
 |
 |
 |
 |
 |
 |
 |
 |
 |
 |
 |
 |
 |
 |
 |
 |
 |
 |
 |
 |
 |
 |
 |
 |
 |
 |
 |
 |
 |
 |
 |
 |
 |
 |
 |
 |
 |
 |
 |
 |
|
|
|
|
|
|
|
|
|
|
|
|
|
|
|
|
|
|
|
|
|
|
|
|
|
|
|
|
|
|
|
|
|
|
|
|
|
|
|
|
|
|
|
|
|
|
|
|
|
|
|
|
|
|
|
|
|
|
|
|
|
|
|
|
|
|
|
|
|
|
|
|
|
|
|
|
|
|
|
|
|
|
|
|
|
|
|
|
|
|
|
|
|
|
|
|
|
|
|
|
|
|
|
|
|
|
|
|
|
|
|
|
|
|
|
|
|
|
|
|
|
|
|
|
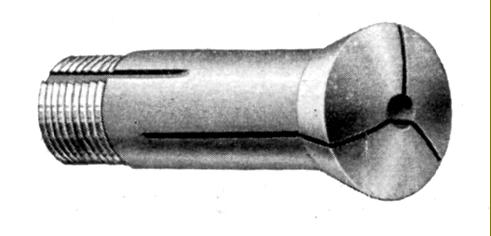 |
|
|
|
|
Known originally as a "chuck", a good set of what are now more often referred to as collets is an essential accessory for any watchmaker's lathe This type, the most common, goes under various names including "split" and "wire". They can also be had in the form of much small "brass-split" chucks, sometimes called "jewel chucks", these commonly being supplied in sets of up to 20 with bores ranging in size from 0.2 to 0.32 mm and often available to fit directly into a specially prepared tailstock spindle or headstock spindle sleeve-down adapter.
|
|
|
|
|
|
|
|
|
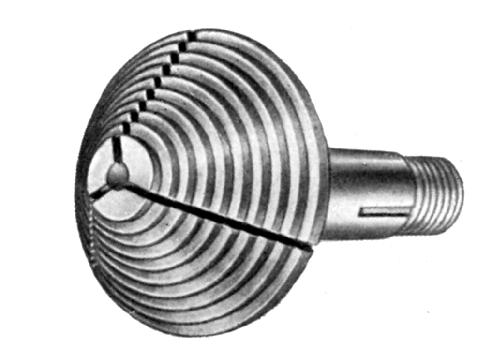 |
|
|
|
|
|
|
|
A "ring" or "fir-tree" collet intended to hold the inside face items such as rings or objects of a similar shape.
|
|
|
|
|
|
|
|
|
|
|
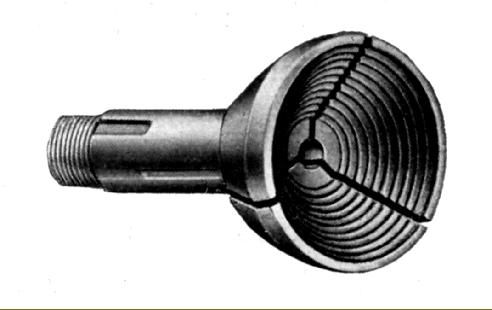 |
|
|
|
|
|
|
|
A "step" or "disc" collet intended to hold the outer face of cylindrical items
|
|
|
|
|
|
|
|
|
|
|
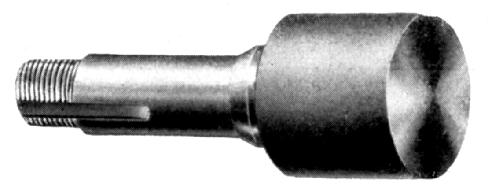 |
|
|
|
|
|
|
|
Blank-end collet - for the turner to modify as necessary for some special holding job
|
|
|
|
|
|
|
|
|
|
|
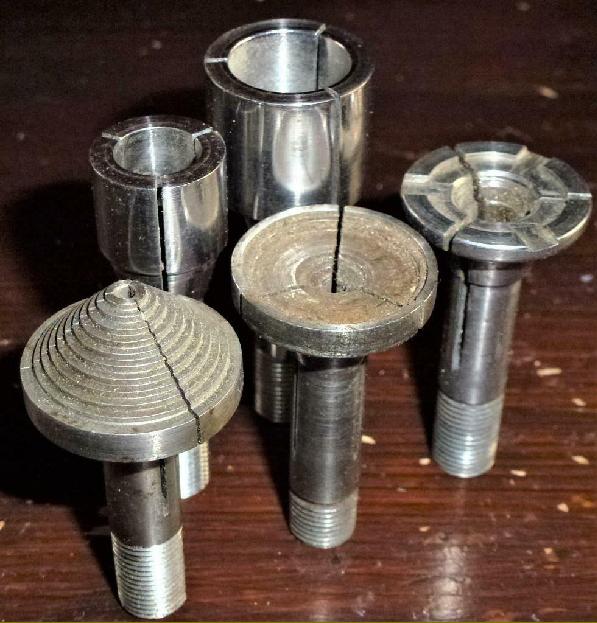 |
|
|
|
|
|
|
|
A variety of collets: at the back two "step-up collets with large sockets to hold larger work. On the right an unusual, heavy-duty form of step or disc collet.
|
|
|
|
|
|
|
|
|
|
|
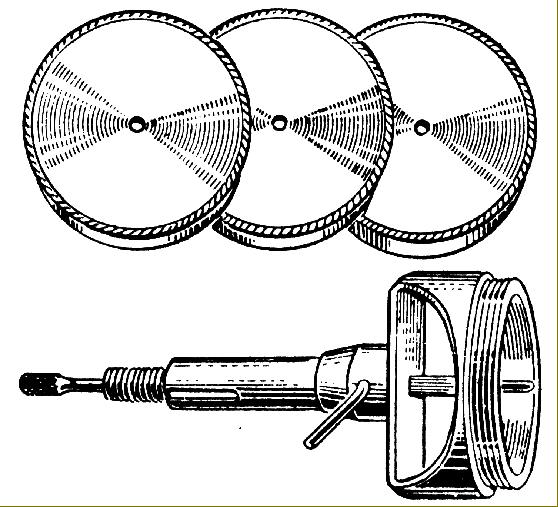 |
|
|
|
|
|
|
Balance chuck. A special collet to hold a watch "balance"
|
|
|
|
|
|
|
|
|
|
|
|
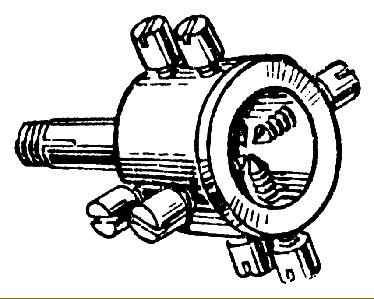 |
|
|
|
|
Box chuck - a collet intended to act as a crude form of 4-jaw chuck. Also known as a "bell chuck" and "eccentric chuck"
|
|
|
|
|
|
|
|
|
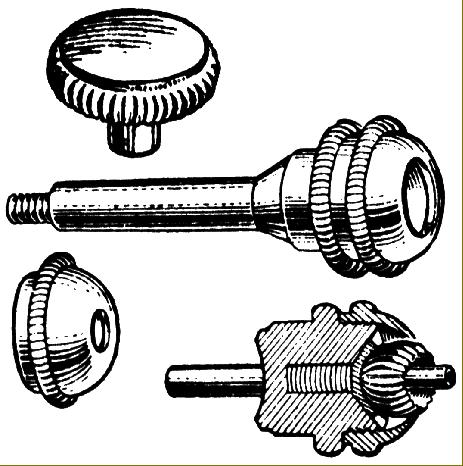 |
|
|
|
|
Button or crown chuck - intended to hold the winding button used on a watch (the external ring by which the owner winds the main spring). To held the many different sizes of winding buttons, these chucks are often supplied in sets of ten.
|
|
|
|
|
|
|
|
|
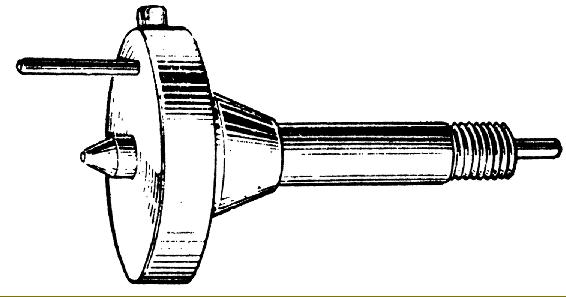 |
|
|
|
|
|
|
|
Carrier chuck, catch plate and drive plate, all names used for this fitting used to "catch" or drive a "dog" fasted to a job being turned between centres.
|
|
|
|
|
|
|
|
|
|
|
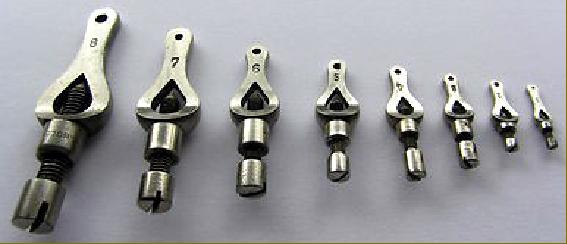 |
|
|
|
A set of lathe watchlathe style drive dogs. These are fastened to the work and "caught" by the catch plate and so turned by the spindle. This fitting is has been used since almost the very beginning of lathe work and all sizes of machine.
|
|
|
|
|
|
|
|
|
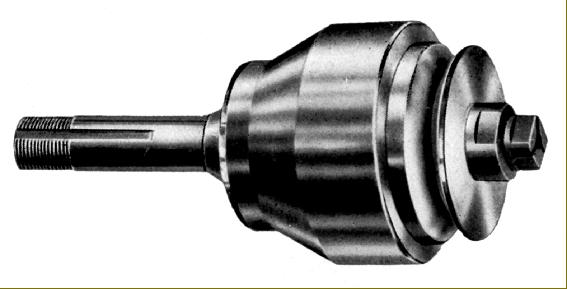 |
|
|
|
|
|
|
Collet with a tapping head for the threading of fine holes. The tap is held in a square collet at the end and driven by a friction clutch. Pressing the job into the chuck drives the tap in, pulling the job out automatically withdraws the tap.
|
|
|
|
|
|
|
|
|
|
|
|
|
|
|
|
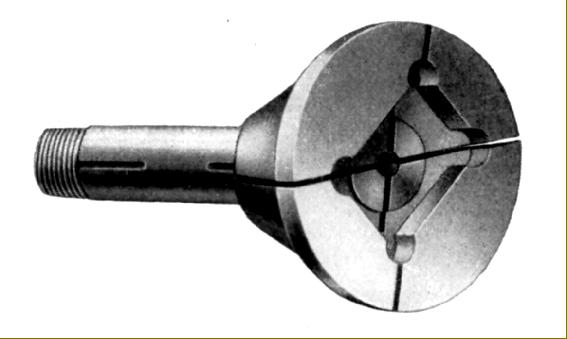 |
|
|
|
|
|
|
Another rare item, a collet with a spring-loaded, self-releasing mechanism. These collets were not a standard item but offered by the maker with custom-made sockets to assist in mass production
|
|
|
|
|
|
|
|
|
|
|
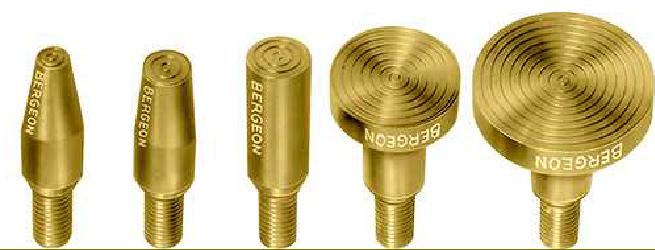 |
|
|
|
|
|
|
|
|
|
A set of wax chucks - used to mount work that cannot be gripped but has to be glued in place. The type shown screw into a collet holder.
|
|
|
|
|
|
|
|
|
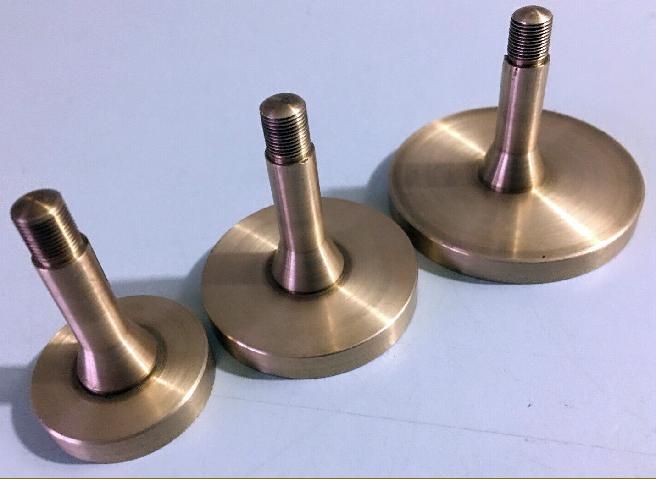 |
|
|
|
|
|
A set of wax chucks - this time formed with an integral collet shank.
|
|
|
|
|
|
|
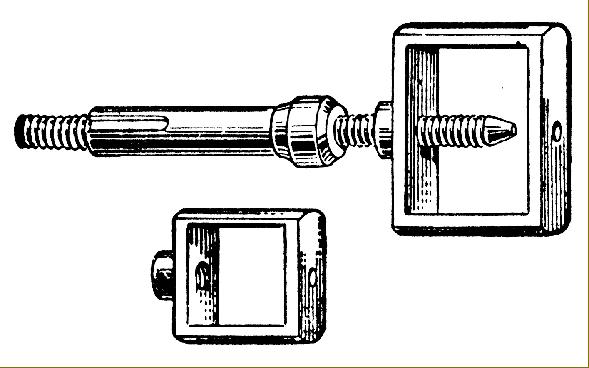 |
|
|
|
|
|
|
|
A large "lantern chuck" for clock work. Held on a collet shaft that fits into the headstock spindle, the square frame allows a screw or similar object to be pressed against its roof and so worked on in the lathe, or even by hand. Made in bronze, the lantern chuck is supplied in a set of three to accommodate the majority of work likely to be encountered. A smaller type, made in steel, is shown below and used for smaller jobs. Being tiny, the threaded end of the chuck is held in a split collet in the headstock spindle.
|
|
|
|
|
|
|
|
|
|
|
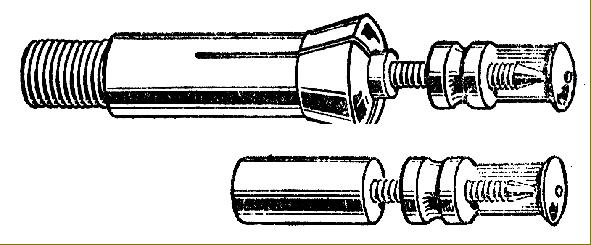 |
|
|
|
|
|
|
|
The tiny version of the lantern chuck used for work on watch parts and held in a standard collet using a screwed-on sleeve
|
|
|
|
|
|
|
|
|
|
|
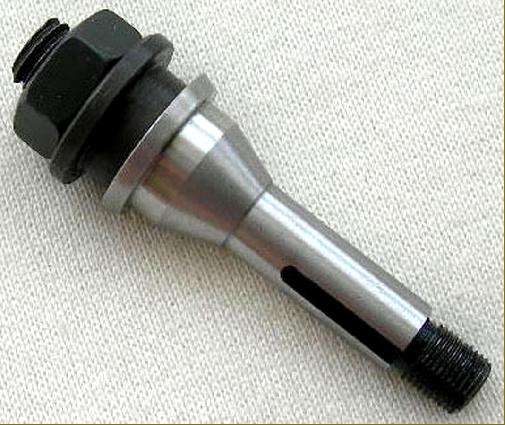 |
|
|
|
|
|
|
|
This design of chuck can take several forms: where the section beneath the nut is plain it can be fitted with a circular saw blade and known as an "arbor" or, obviously, a "circular saw chuck". In addition, the type also lends itself to be fitted with an emery wheel for grinding or cutting-off purposes. If the section below the nut is conical it will be intended to hold a wheel (a gear in layman's terms) - the conical section automatically aligning the wheel centrally. In this case the chuck would be known as a "wheel chuck".
|
|
|
|
|
|
|
|
|
|
|
|
|
|
|
|
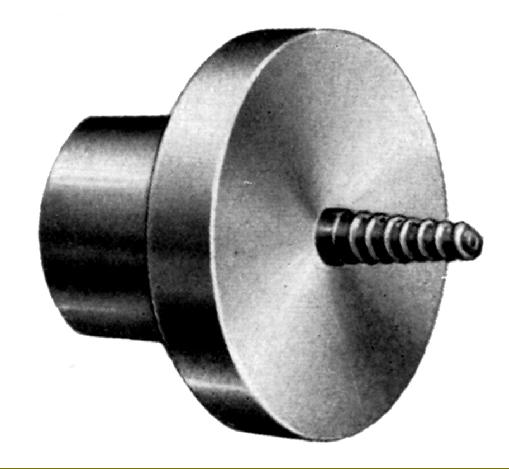 |
|
|
|
|
|
|
|
A "wood-screw" chuck for the gripping of wood or similar soft materials. This type would have either screwed onto the spindle nose or have been held in some sort of collet adapter/ versions were also made with an integral collet fitting.
|
|
|
|
|
|
|
|
|
|
|
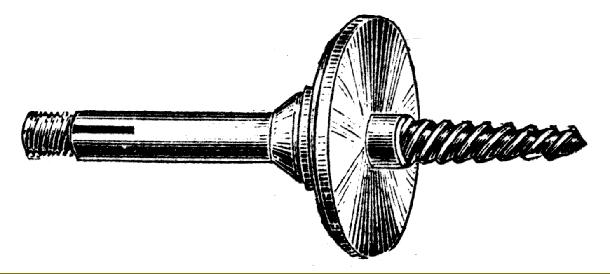 |
|
|
|
|
|
|
|
A "wood-screw" chuck with an integrals collet shank
|
|
|
|
|
|
|
|
|
|
|
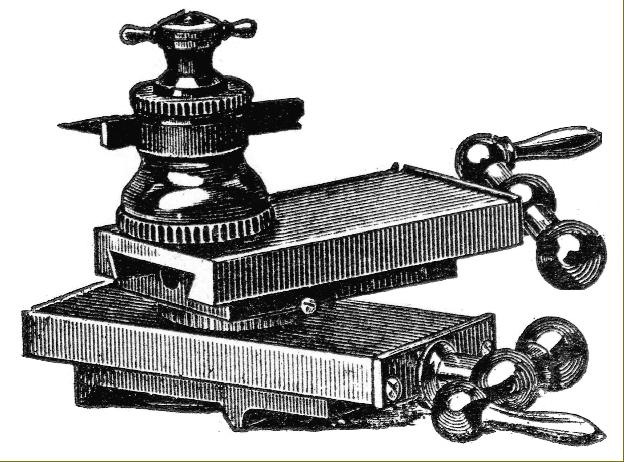 |
|
|
|
|
|
|
|
As can be seen from the fact that type appeared as an engraving in 19th century catalogues, the compound slide rest assembly has long been a desirable accessory to accompany any watchmaker's lathe. This model is designed to fit the bed of a WW lathe
|
|
|
|
|
|
|
|
|
|
|
 |
|
|
|
|
|
|
|
Even the lighter round-bed Geneva-pattern lathes could be fitted with a compound slide rest - through this fitting on that type of lathe is rather less common
|
|
|
|
|
|
|
|
|
|
|
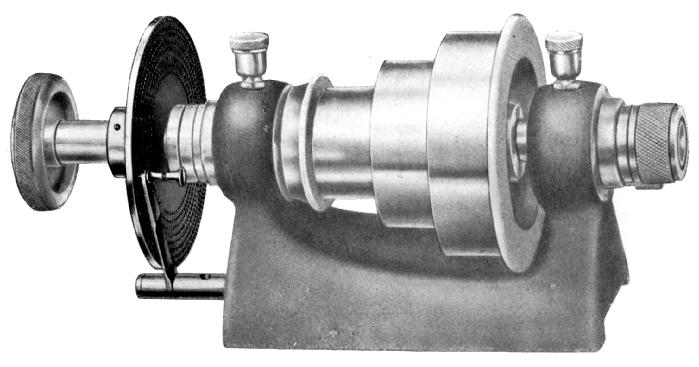 |
|
|
|
|
|
|
A division plate with indexing pin attached to the end of the headstock spindle/ Thus equipped all manner of operations may be carried out including, for example, holding work in a collet or chuck and employing a double filing rest to make a number of regularly-spaced flats or other shapes on it.
|
|
|
|
|
|
|
|
|
|
|
|
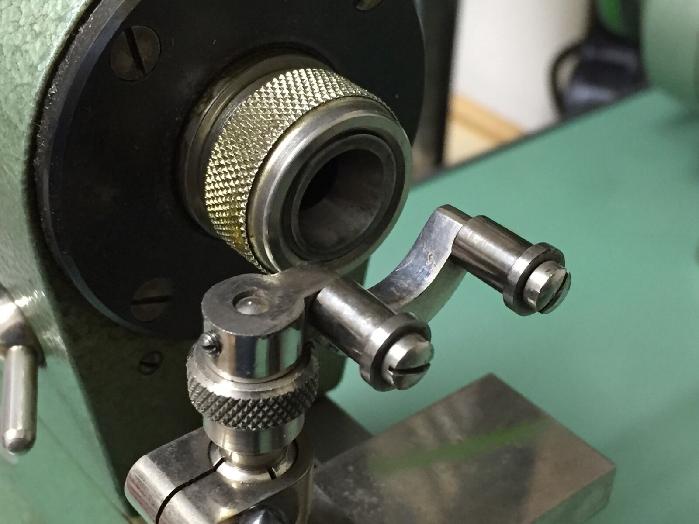 |
|
|
|
|
|
Double filing rest in place. Ones with a single roller are also available
|
|
|
|
|
|
|
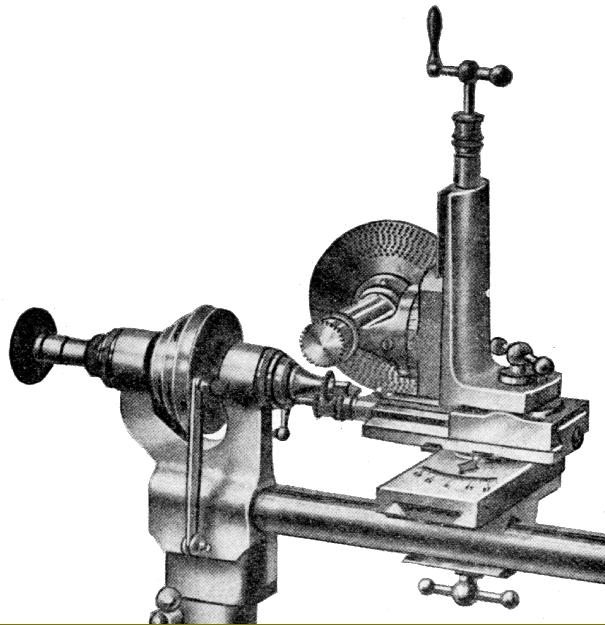 |
|
|
|
|
|
|
|
A vertical slide with attached dividing plate. In combination with other attachments gear cutting and other operations become possible. Some dividing attachments were of far greater complexity, like this made by Lorch
|
|
|
|
|
|
|
|
|
|
|
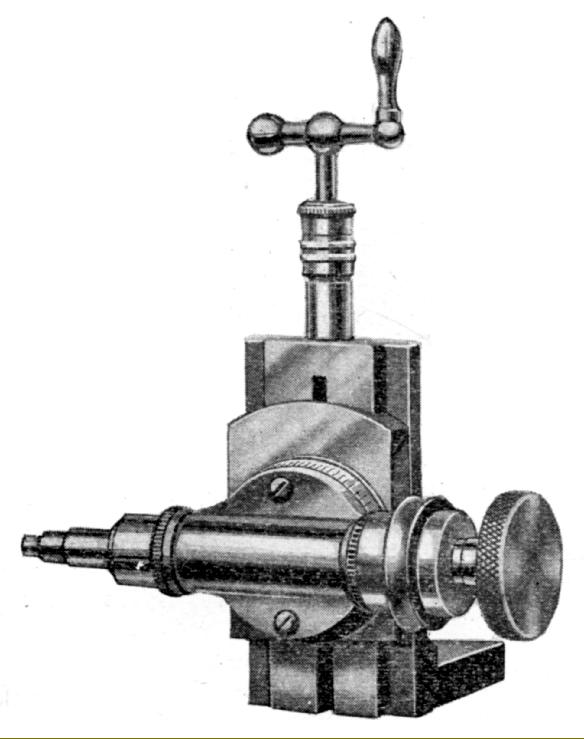 |
|
|
|
|
|
|
|
Vertical slide with a high-speed milling and grinding spindle. The pulley at the right-hand end was driven by an "overhead" attachment.
|
|
|
|
|
|
|
|
|
|
|
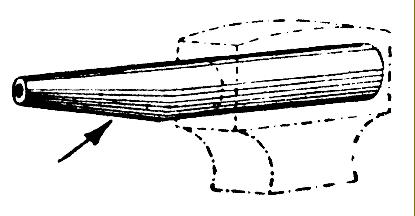 |
|
|
|
|
|
|
|
Eccentric runner. As no watch lathe has the facility to set the tailstock over on a separate base for the turning of slight tapers, the "eccentric runner is used instead. As the centre is offset to the main body, rotating it causes the centre to move out of line with that in the headstock spindle.
|
|
|
|
|
|
|
|
|
|
|
|
|
|
|
|
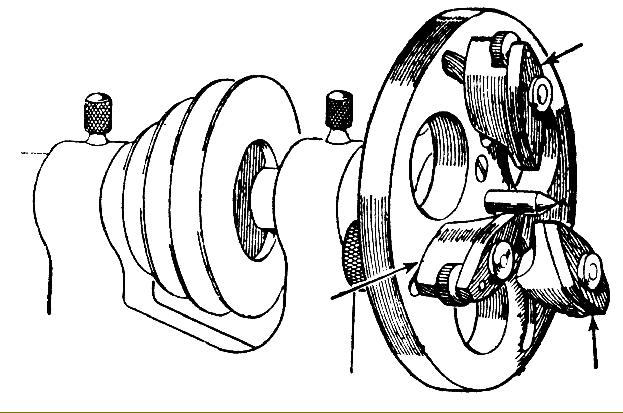 |
|
|
|
|
|
|
|
Another long-established watch lathe accessory - a faceplate with integral, finely-adjustable clamps (arrowed) to hold work. Faceplates came in two forms: one that could be removed from lathe and another built as part of the spindle and supplied complete with a headstock - this arrangement ensuring the greatest possible accuracy.
|
|
|
|
|
|
|
|
|
|
|
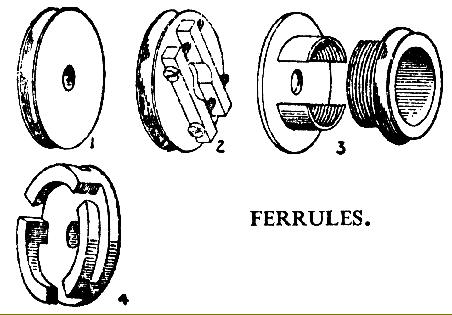 |
|
|
|
|
|
|
|
"Ferrules" - these are pulleys adapted to hold and turn work in the lathe. The basic type is a simple brass plate (No.1) to which a job can be glued. No. 2 carries a clamp on its face closed by two screws. To hold balances, the screw type No. 3 is used while No. 4 is a special spring type to hold a balance.
|
|
|
|
|
|
|
|
|
|
|
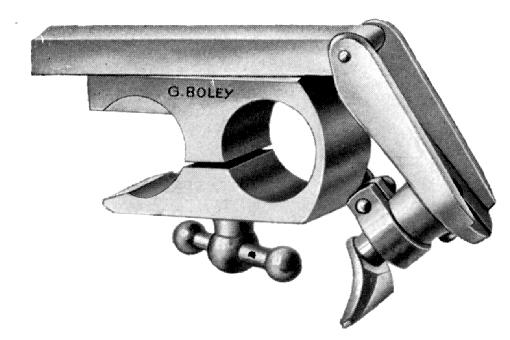 |
|
|
|
|
Flip-up tool rest - virtually a standard fitment on all watchmaker's lathes
|
|
|
|
|
|
|
|
|
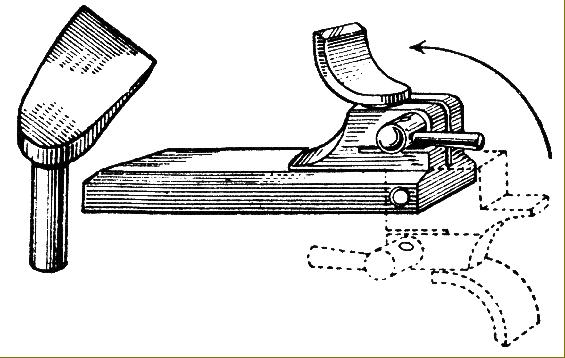 |
|
|
|
|
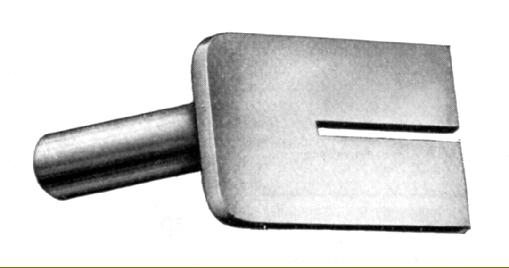 |
|
|
|
|
A simple sawbench that fitted into the socket used to hold the ordinary T-rest in a flip-up or standard hand-rest holder. The saw blade was held either on an arbor running between centres or an saw blade arbor like the one below.
|
|
|
|
|
|
|
|
|
|
|
|
|
|
|
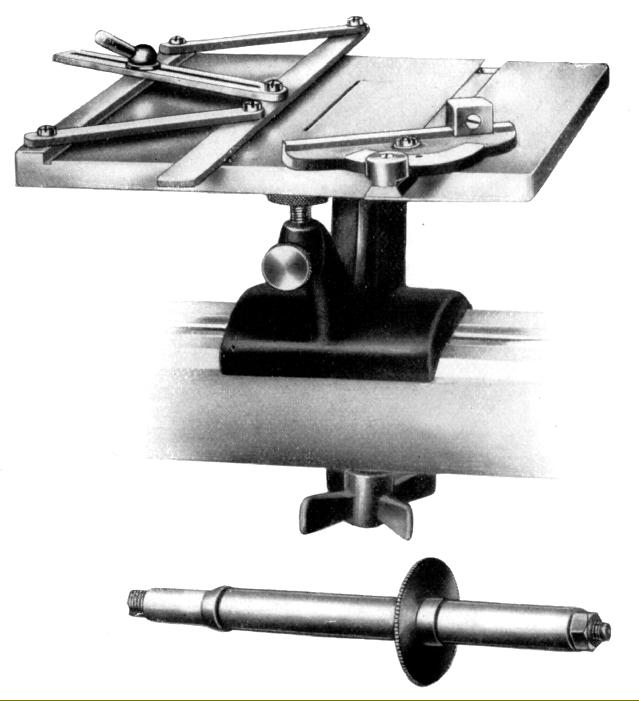 |
|
|
|
|
|
|
|
Universal saw bench with a pantograph-controlled ruler, a swivelling fence and the saw blade held on a between-centres arbor
|
|
|
|
|
|
|
|
|
|
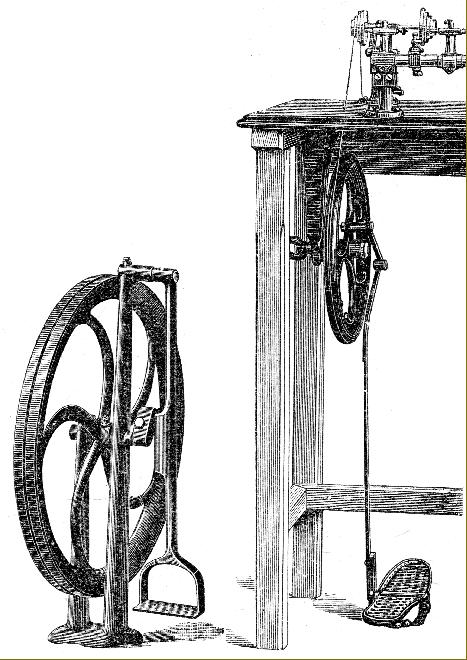 |
|
|
|
|
Before the widespread availability of electric motors, many types of smaller machine tool could be operated by leg or arm power. The two illustrations show typical installations spanning the late 1800s to the early 1900s with some types continuing even into the 1930s. The unit to the left of the bench is a foot motor, sometimes called a foot wheel, as is the larger item in the illustration below Drive was usually by a round leather rope, a "gut drive" in contemporary parlance. Today, with the easy availability of inexpensive, variable-speed motors from sewing machines, running any watchmaker's lathe is both easy and inexpensive.
|
|
|
|
|
|
|
|
|
|
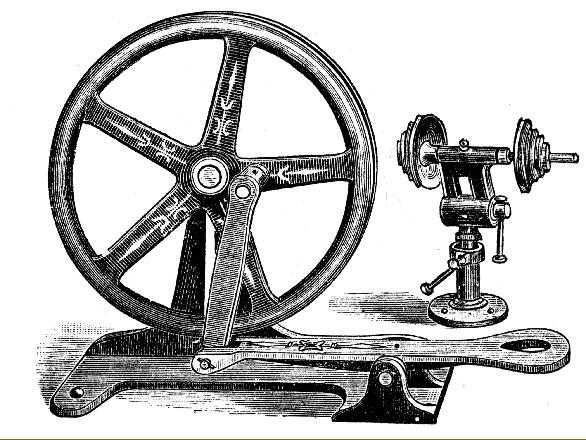 |
|
|
|
|
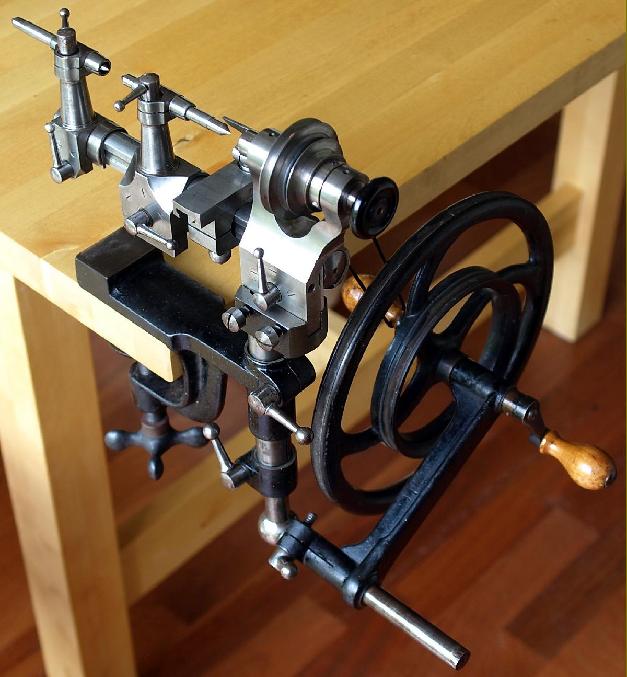 |
|
|
|
|
|
|
|
Hand-cranked drive - a rather awkward-to-use device while trying at the same time, to use the lathe. An assistant is handy to have....
|
|
|
|
|
|
|
|
|
|
|
|
|
|
|
|
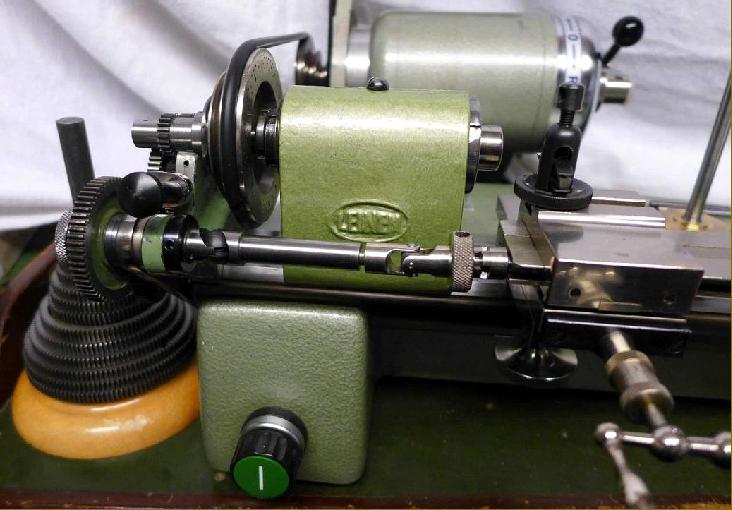 |
|
|
|
|
|
|
Unusual on a watchmaker's lathe - but possible. A screwcutting and power-feed attachment driving the top slide through a set of changewheels
|
|
|
|
|
|
|
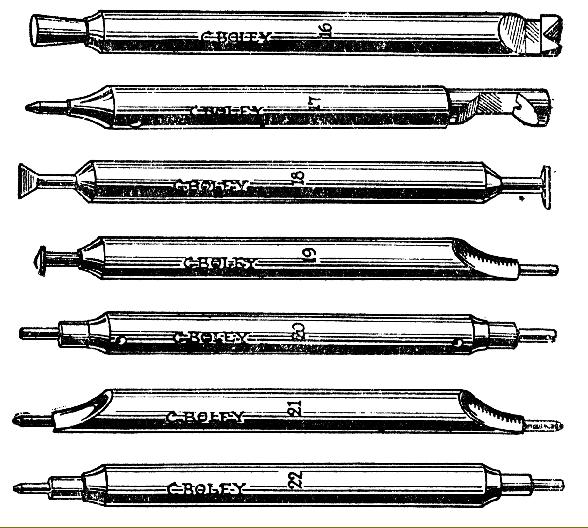 |
|
|
|
|
|
|
|
"Runners" - often used in the tailstock as a "spindle combined with a centre" and designed to allow the turning of various items. They can also be used on turns and Jacot tools and employed to hold work while it's being turned or at rest when polishing pivots - or to hold a jobs when its ends are being polished.
|
|
|
|
|
|
|
|
|
|
|
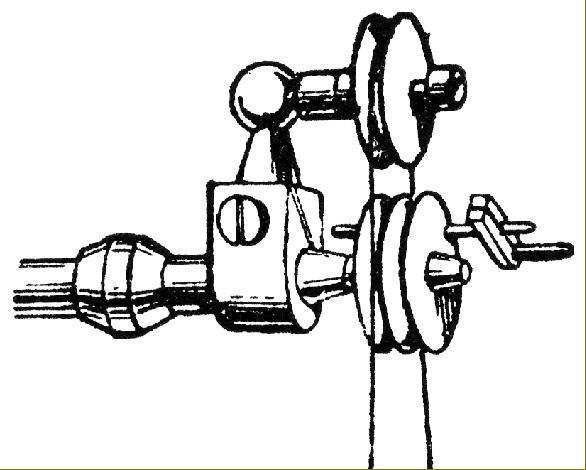 |
|
|
|
|
Above and below: the double "safety pulley". Carried in a headstock collet the "safety pulley" is used as a form of "safety clutch". Instead of the drive belt being wrapped around the pulley connected to the catch plate that drives the work, instead it is first wrapped around a second pulley (the one at the top in this illustration) and then can be arranged (by swivelling the housing) to press lightly against the drive pulley. The device also allows the belt tension to be precisely adjusted, an advantage when dealing with particularly delicate work.
|
|
|
|
|
|
|
|
|
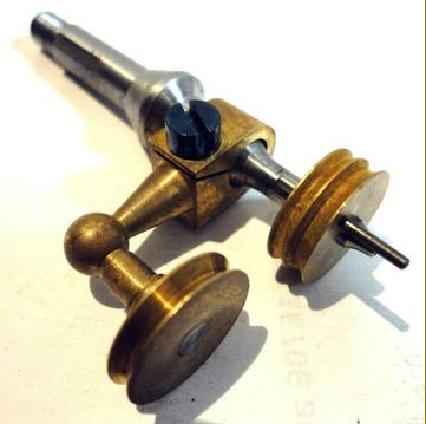 |
|
|
|
|
Another view of a "safety pulley"
|
|
|
|
|
|
|
|
|
|
|
|
|
|
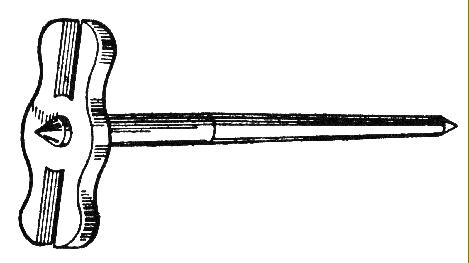 |
|
|
|
|
|
|
|
Tapered turning arbor. Used in various forms on all sizes of lathe, the shaft of the tapered arbor has a shallow taper onto which objects with a round bore can be pressed and held. The example shown has points at each end for running between hollow centres and a built-in "dog" to engage with the pin on a drive plate
|
|
|
|
|
|
|
|
|
|
|
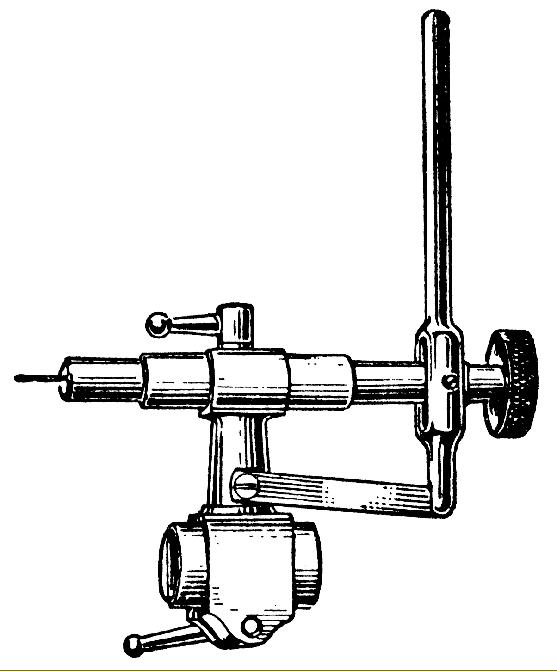 |
|
|
|
|
|
|
Tailstock with lever action - this provides a better feel on small drill bits than with a screw-feed mechanism
|
|
|
|
|
|
|
|
|
|
|
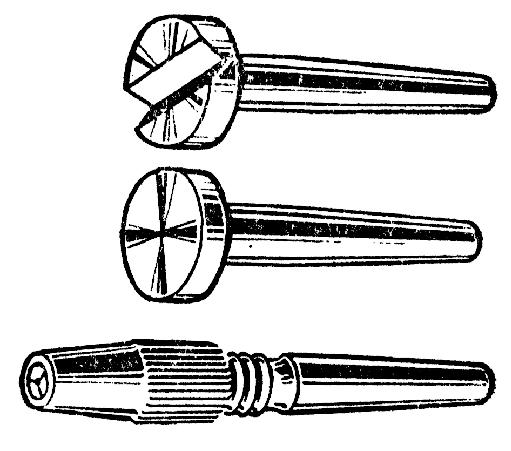 |
|
|
|
|
|
|
|
Miniature versions of tailstock fittings used on larger lathes. Top: a V-pad against which round components can be held while machined or drilled from a headstock held drill or cutter.
Middle: a plain drill pad
Bottom: a miniature drill chuck to hold very tiny drill bits
|
|
|
|
|
|
|
|
|
|
|
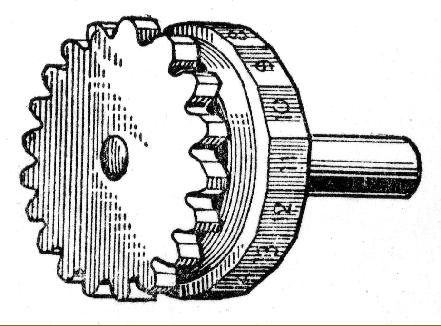 |
|
|
|
|
|
|
|
Jacot drum. Used for polishing clock pivots and fits into another accessory, the self-centring attachment seen below.
|
|
|
|
|
|
|
|
|
|
|
|
|
|
|
|
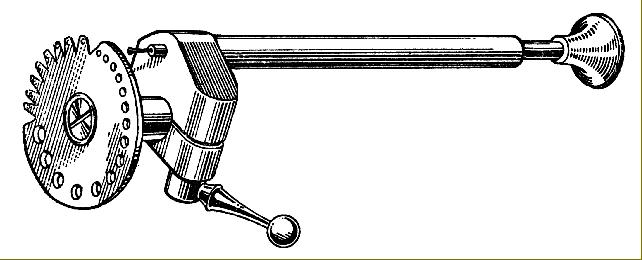 |
|
|
|
|
|
|
Self-centring attachment.
|
|
|
|
|
|
|
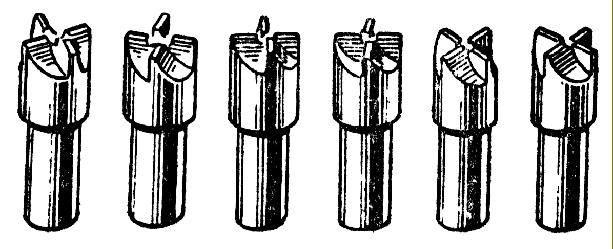 |
|
|
|
|
|
|
|
"Rose" cutters, used when making a recess or in sinking work. To guide the cutter - which otherwise might have a tendency to wander - a guide centre can be fitted. These cutters can be held in a headstock and made to rotate against a cutter held in the tailstock - or vice versa
|
|
|
|
|
|
|
|
|
|
|
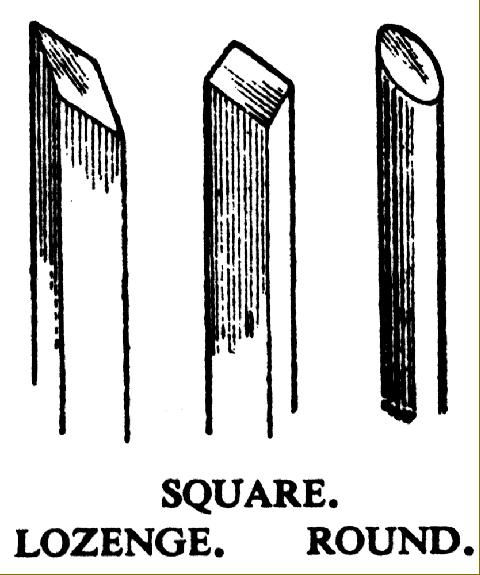 |
|
|
|
|
|
|
|
"Gravers" - used for simple hand turning using a graving rest - often a flat surface along which the tool could be slid and otherwise manipulated. The cutters are usually attached to wooden handles - for obvious reasons - and do require considerable skill to use effectively. Many watchmakers and repairs prefer to use a very fine-feed slide rest to control the cutting tools but many still persist with the ancient craft of hand turning.
|
|
|
|
|
|
|
|
|
|
|
|
|