 |
 |
 |
 |
 |
 |
 |
 |
 |
 |
 |
 |
 |
 |
 |
 |
 |
 |
 |
 |
 |
 |
 |
 |
 |
 |
 |
 |
 |
 |
|
|
|
|
|
|
|
|
|
|
|
|
|
|
|
|
|
|
|
|
|
|
|
|
|
|
|
|
|
|
|
|
|
|
|
|
|
|
|
|
|
|
|
|
|
|
|
|
Manufactured by a long-established machine-tool maker, Doria S.A.S. of Turin, Italy - and in competition with the similar machines from the Merli Company in Codevilla - the FTC range of very large capacity lathes was offered in four standard specifications as the Models "41", "51", 61" and "71". The Model 41 could be had with a single centre height of 410 mm; the Model 51 was offered with a choice of 460 and 510 mm; the Model 61 with 560, 610 and 660 mm and the Model 71 with 660, 710 and 760 mm. A wide range of between-centres capacities was available that varied from a shortest of 1500 mm on the Models 41 and 51 (2000 mm on the Models 61 and 71) to a maximum of 8000 mm on all versions. However, the makers also stated that they had the capacity to build (to special order) larger or modified versions some with increased centre heights, the ability to take work pieces up to 15 metres long or to act as large facing or special-purpose machines. An important option on the large FTC lathes was the spindle bore size. The Model 41 was supplied as standard with a 104 mm diameter hole, but optionally either 120 or 150 mm. The Model 51 had a 120 mm bore as standard but was capable of being fitted with a choice of three others: 140, 200 or 220 mm Larger still, the Model 61 could pass work up to 130 mm in diameter or, to special order, 160, 200 or 220 mm. largest of all, the Model 71 had a 150 mm as standard but was capable of holding others with 200, 220, 260 or even 360 mm. All models lathes in the series were built to the same specification and included the same range of features with a typical arrangement being a bed heat treated to eliminate internal stresses and cast in one section that rested on the ground over its full length. Ways were of conventional V and flat type, induction hardened to 450 Brinell, finish ground and with the front V made much wider and set at a shallower angle on its outside surface than the shorter and steeper inside. Deep, rectangular webs braced the front and back walls and a detachable gap section was offered as an optional extra. All-geared and cast from a high-strength iron, the headstocks held a spindle machined from a forging in a Cr-Ni alloy steel that was heat treated, case-hardened and ground . Supported at three points, the spindle ran at its nose end in a special double-row roller bearing with an adjustable tapered seat; in its middle section by a pre-loaded taper-roller bearing was used and at the rear two bearings, one an SKF 30228 taper roller and the other an adjustable thrust type. A single, helical-form gear was attached to the spindle and picked up the drive from a lower shaft - the spindle stop, start and reverse being through double multi-disc, hydraulically operated clutch and combined brake units. Spindle control was by duplicated levers, one on the headstock with the other (following conventional practice) on the apron. Continued below:
|
|
|
|
|
|
|
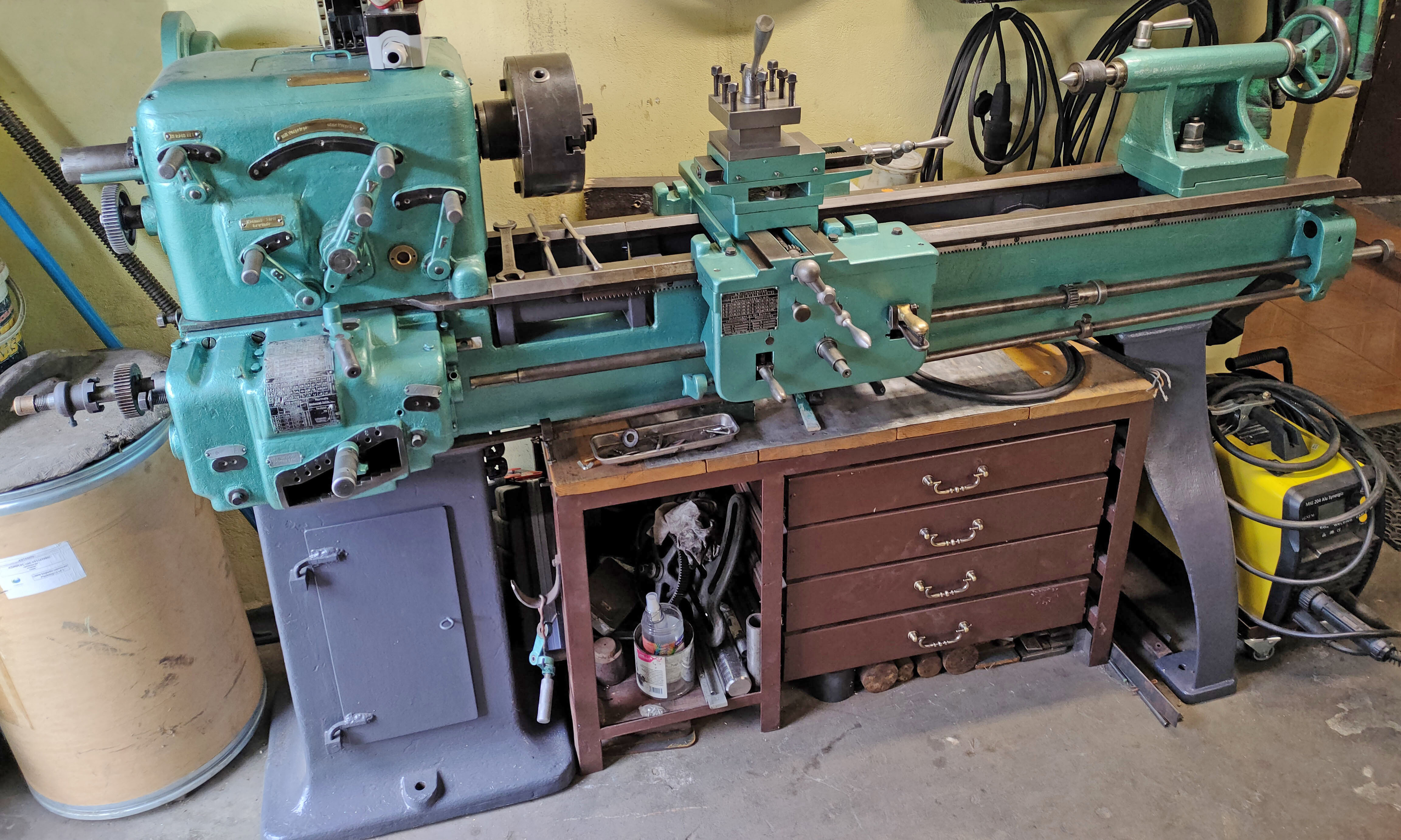 |
|
|
|
|
|
|
Continued: Spindle speeds provided on the Model 41 were eighteen from 10 to 650 r.p.m. while on the Model 51 the same number ran from 7 to 550 r.p.m. Both the two larger models the 61 and 71 had (in all their various sizes), twenty-four speeds, the former from 5 to 500 r.p.m. and the latter from 4 to 400 r.p.m. Other gears and shafts within the headstock were all made in a Cr-Ni alloy steel that was heat treated, case-hardened and ground and ran in high quality ball races. Headstock lubrication was by a pump lifting filtered oil from a reservoir in the bed beneath the headstock through a system of pipes that directed it to the various sections of the headstock. Although as standard the compound slide rest assembly fitted was an ordinary arrangement of a cross and top slide (the latter with the option of a power-feed attachment for taper work) customers could order a variety fittings according to their preferences and the lathe's centre height. A triple-slide arrangement was listed (with various sizes of packing block to bring the elements up the correct height), together with a single cross slide for extra heavy-duty turning and even a pair of independent front and rear cross slides, each with its own feed screws, the handles and micrometer dials being positioned side by side at the front of the saddle. However, no matter what the chosen fitting, the cross slide always ran on hardened and ground ways. Unless deleted from the standard specification, all models were fitted - in addition to the ordinary power feeds - with an electrically-driven rapid traverse mechanism to both the carriage and cross slide. Very heavily built, the tailstock was fitted with a quite ordinary, manually-operated screw-driven spindle (though an automatic power feed was optional) with the whole assembly moved along the bed by crank-handle-operated rack-and-pinion gearing. However, the manual drive could be supplemented, at extra cost, by an electrically-driven rapid feed, this being powered by its own, separate motor. Screwcutting and power feeds were provided by a totally enclosed, sealed gearbox with lubrication by an oil bath. Gears and shafts were all in a heat treated, case-hardened and ground a Cr-Ni alloy steel with ball races used throughout. Pitches available as standard - and available without disturbing the changewheels - included a wide range of English, metric, module and diametral - these varying in extent and number according to the particular model. Leadscrews were of the ordinary screwed type with sliding and surfacing feeds driven by a separate power shaft. Standard equipment provided with each new lathe consisted of: a complete electrical installation to suit the customer's voltage; 4-way rapid traverse (carriage and cross slide) with a 0.75 h.p. motor for the Models 41 and 51 and 1.5 h.p. for the 61 and 71; coolant system; combination faceplate and independent 4-jaw chuck; 4-way toolpost; drive plate; longitudinal carriage stop; fixed steady; travelling steady; two Morse centres and a headstock spindle reduction sleeve; a selection of maintenance tools and an instruction manual. Optional extras included both one-off items to a customer's design and a number of standard, off-the-shelf items: quick-change toolpost; rear toolpost; 3-jaw chucks and chuck backplates; automatic adjustable cross-feed stop; power feed to the top slide (the fitting of which reduced the swing over the carriage by 100 mm); taper-turning; a "differential" system of gears fitted to the apron that operated the longitudinal and cross feeds together to give taper turning over the entire centre distance; electrically-driven tailstock rapid traverse along the bed; automatic drive to the tailstock spindle; concave and convex (ball-turning) attachment - probably of a type intended for turning paper-mill and other large rollers); hydraulic copying; thread-chasing dial; double (stacked) cross slide; cross and top-slide combinations to customer's order; self-centring 3-jaw chuck mounted on the rear end of the spindle to support long shafts (and the likelihood that outboard, floor-mounted 3-point steadies to help perform the same task could also be provided) and a machine light(s)..
|
|
|
|
|
|
|
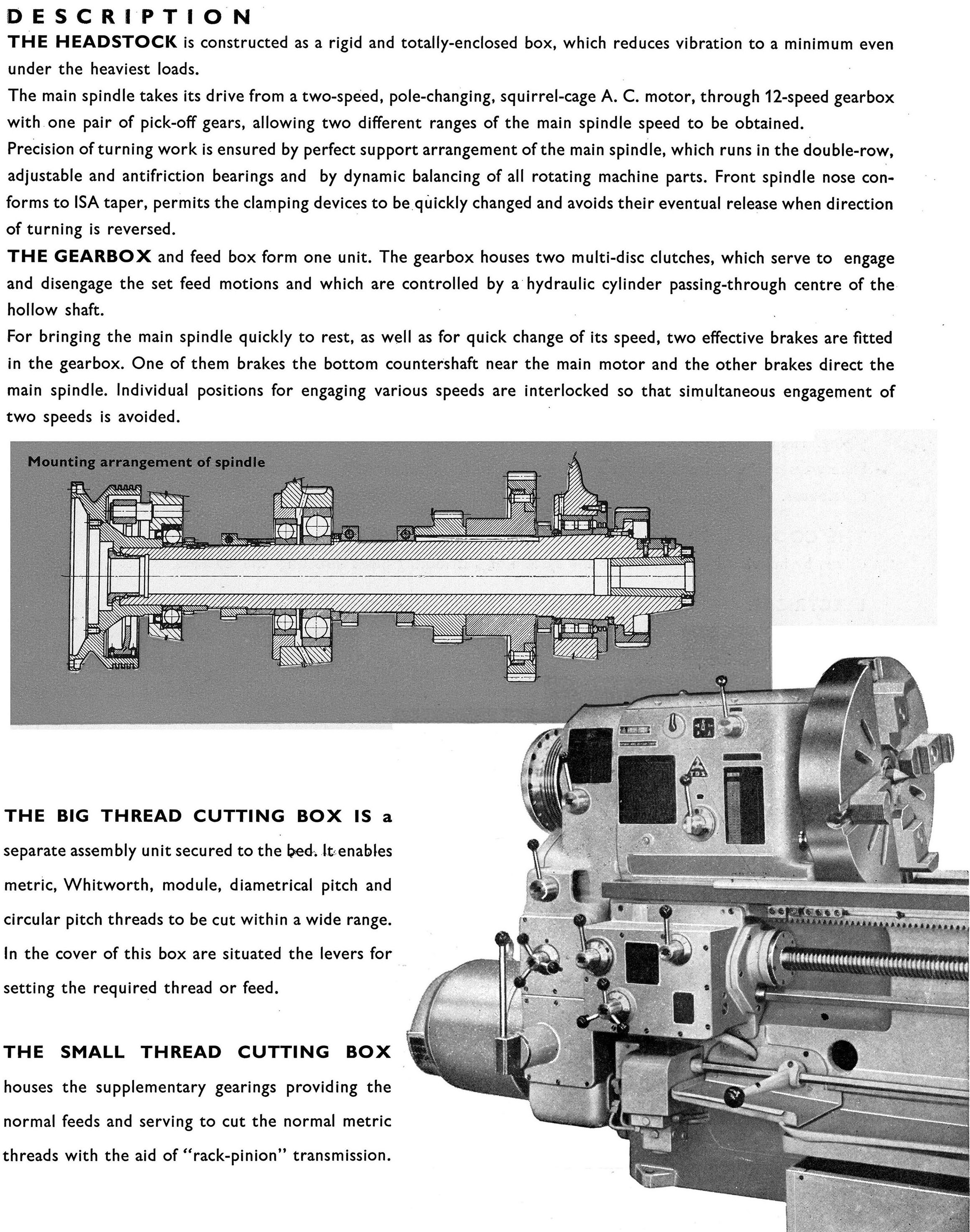 |
|
|
|
|
|
|
|
|
|
 |
|
|
|
|
|
Headstock end of the Model 41-51
|
|
|
|
|
|
|
 |
|
|
|
|
|
Tailstock end of the Model 41-51
|
|
|
|
|
|
|
 |
|
|
|
|
|
Headstock end of a very long bed Model 61-71
|
|
|
|
|
|
|
 |
|
|
|
|
Tailstock end of a very long bed Model 61-71
|
|
|
|
|
|
|
 |
|
|
|
|
|
|
Big-bore Torni fitted with a 3-tier "compound" slide rest assembly
|
|
|
|
|
|
|
|
|
|
|
|
 |
|
|
|
|
|
|
Torni Model FTC 900/1020 with power-driven tailstock and tread plates on the carriage for the operator to climb aboard
|
|
|
|
|
|
|
 |
|
|
|
|
|
3-jaw chuck mounted on the outboard end of the spindle to support long, heavy shafts
|
|
|
|
|
|
|
 |
|
|
|
|
|
3-bearing headstock spindle
|
|
|
|
|
|
|
 |
|
|
|
|
|
|
Torni lathe bed: heat treated to eliminate internal stresses and cast in one section that rested on the ground over its full length. Ways were of conventional V and flat type, induction hardened to 450 Brinell, finish ground and with the front V made much wider and set at a shallower angle on its outside surface than the shorter and steeper inside. Deep, rectangular webs braced the front and back walls and a detachable gap section offered as an optional extra.
|
|
|
|
|
|
|
 |
|
|
|
|
|
|
One-off, special-purpose, short-bed facing lathe
|
|
|
|
|
|
|
 |
|
|
|
|
|
|
Triple "compound" slide rests with front and rear 4-way toolposts
|
|
|
|
|
|
|
 |
|
|
|
|
|
|
A mechanism was fitted to the apron, a "differential" system of gears that operated the longitudinal and cross feeds together to give taper turning over the entire centre distance.
|
|
|
|
|
|
|
 |
|
|
|
|
|
|
|
|
|
|
|
|
|
|
|
|
|