 |
 |
 |
 |
 |
 |
 |
 |
 |
 |
 |
 |
 |
 |
 |
 |
 |
 |
 |
 |
 |
 |
 |
 |
 |
 |
 |
 |
 |
|
|
|
|
|
|
|
|
|
|
|
|
|
|
|
|
|
|
|
|
|
|
|
|
|
|
|
|
|
|
|
|
|
|
|
|
|
|
|
|
|
|
|
|
|
|
|
Rosenfors - Aktiebolaget Rosenfors Bruk of Malilla, Sweden - was a machine tool company well known for their heavily built, high quality general-purpose lathes and milling machines. During the 1950s and 1960s they manufactured a series of lathes, the RS-20, RS-25 & RS-30F (and RL-8H, RL-8M, RL-10H & RL-10M) all intended for either production or toolroom use. Whilst each of the three models in the series was of very similar design (and used identical controls), a number of significant differences were included to demonstrate that all were properly engineered for their size - and not just one model modified with thicker headstock and tailstock castings to cover as wide a market as possible. Each Model was given a number that referred to its approximate centre height - the exact figures being: RS-20 with 205 mm (8 inches); RS-25 with 268 mm (10.5 inches) and the RS-30F with 305 mm (12 inches). The RS-20 types was available with 1000 or 1500 mm between centres, whist the RS-25 and RS-30 could be had with a far wider choice from a minimum of 1000 to a maximum of 5000 mm - with any length available at intervals of 500 mm. Mounted on separate headstock and tailstock-end cast-iron plinths and with mid-way support for the longer versions, all beds were enormously deep and strong with hardened and ground V and flat ways. Width was 390 mm on the RS-20 and 415 mm on the other two, with strong U-shaped braces between the walls on the former and even heavier diagonal bracing on the latter. Whilst a gap option was not listed for the RS-20, it was on the others and enabled a disc some 810 mm (32 inches) in diameter and up to 300 mm (11.75 inches) thick to be turned on the standard faceplate. Continued below:
|
|
|
|
|
|
|
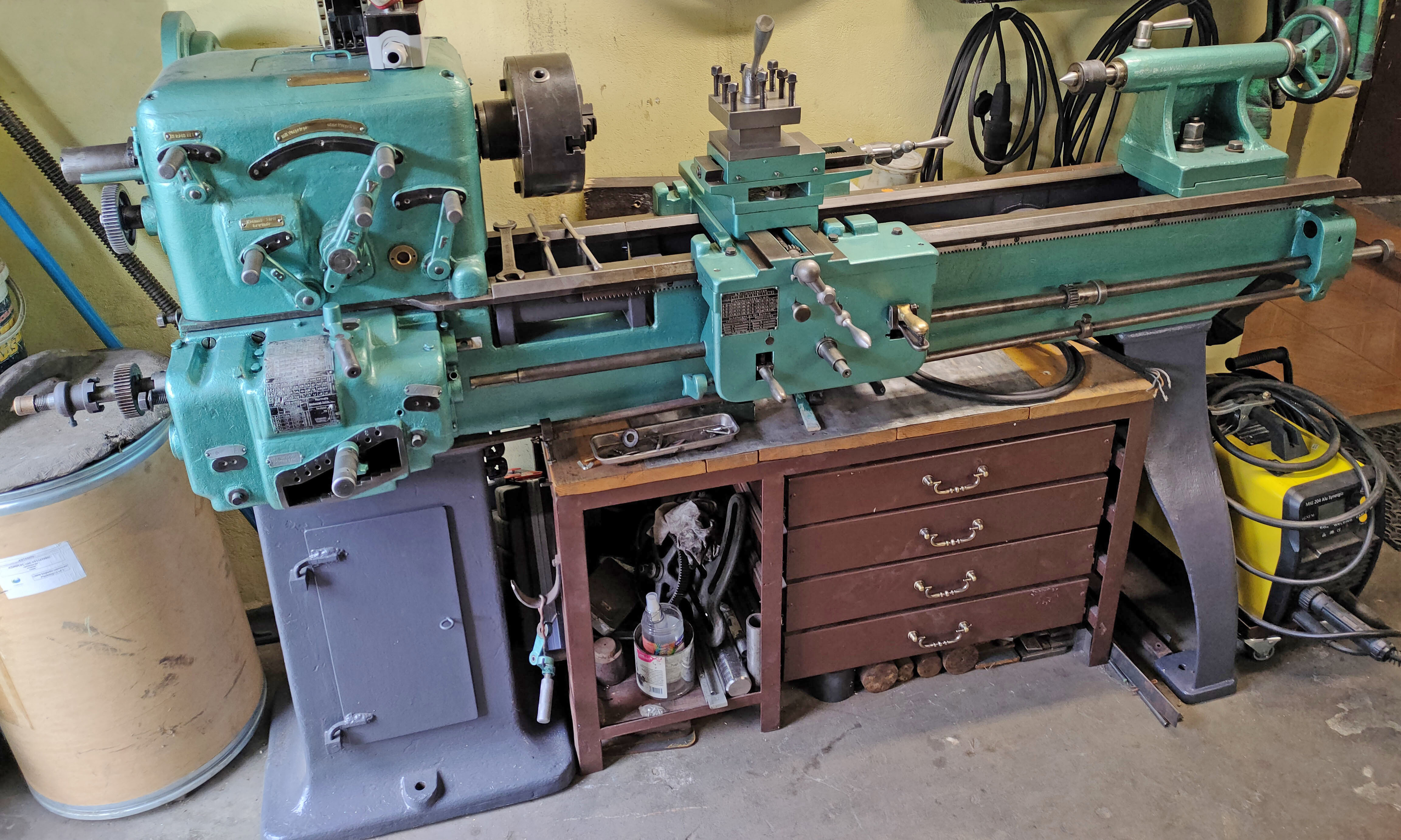 |
|
|
|
|
|
Rosenfors RS-20 fitted with the totally-enclosed "Universal" screwcutting gearbox
Continued: Of conventional, even simple design, the headstock was very heavily built with every shaft and gear hardened and ground and all spindles running on roller or ball races. As a point of interest, the method employed for grinding the headstock gears was, announced Rosenfors, that used by Maag (a Swiss producer of advanced grinding machines). However, as this system changed and developed over the years, this was probably a reference to a 1950 Maag invention of grinding spur and helical gears by the simultaneous use of two straight-sided grinding wheels, each moved with a stroking motion. Oil filled, with a sight-glass level window on the front, lubrication was by splash, the changes of speed being by the juxtaposition of three levers on the face of the headstock. Mounted within the left-hand plinth - and driving by five V-belts - the standard motor for the RS-20 was a single-speed, 1400 r.p.m., 5 h.p. unit, the twelve speeds provided spanning 18 to 1000 r.p.m. The larger RS-25 and RS-30 were, more sensibly, given a choice of a 7.5 or 10 h.p. motor and, on the RS-30 only, a slower speed range from 15 to 800 r.p.m. Massively built, the spindle on the RS-20 had a diameter of 80 mm diameter where it passed through the front bearing and, on all the others, 100 mm. Spindle bore was 46 and 60 mm respectively, with all types running in an adjustable double cylindrical roller bearing at the front and single roller bearings at the back and in a mid-way support. As the rollers bearings were not the tapered type, thrust had to betaken separately against a ball bearing at the rear. On all models the spindle nose was hardened, with the option of either a standard Rosenfors fitting (a thread with a ground register both in front and behind and a radial grub screw to give security when run in reverse) or, on the two smaller models, an American long-nose taper in an L1 size and, on the larger pair, an L2. Spindle tapers were described as metric 50 on the RS-20 and metric 70 on the others. Controlled by a third-rod system, with levers just outboard of the gearbox and pivoting from the right-hand face of the apron, all RS types had a powerful combined clutch and spindle brake fitted inside the headstock. The brake element was especially important on such a large lathe for a heavy job, being turned at high speed, would otherwise have taken over a minute to come to rest. An interesting feature fitted to long-bed models was a pair of arms that could be clamped to the bed at each side of the carriage; these reached down to support the otherwise rather flexible bar used to operate the third-rod control system. Continued below:
|
|
|
|
|
|
|
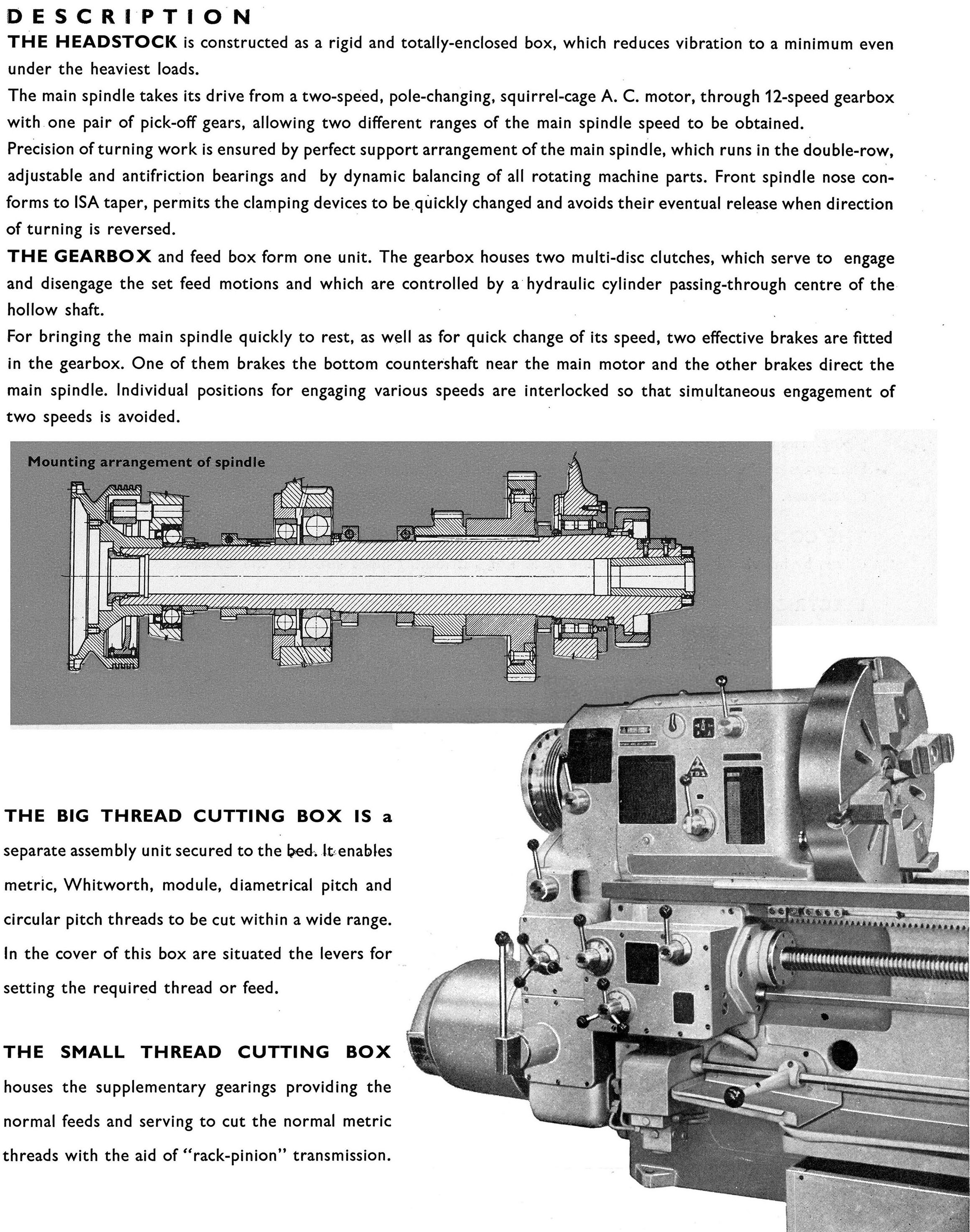 |
|
|
|
|
|
|
A less-expensive option - the Norton-type screwcutting gearbox
Continued: Screwcutting and feeds on all models was by a choice between two completely different designs of screwcutting and feeds gearbox. Of the pair, the more expensive "Universal" was a completely enclosed, oil-bath unit with all-lever changes that could generate 50 English pitches and rates of feed without changing or demounting any gears together with an additional seventeen metric pitches by using alternative changewheels. English pitches spanned 2 to 56 t.p.i., metric from 0.5 to 12 mm and sliding feeds from 0.08 to 2.24 mm (0.0032" to 0.089") per revolution of the spindle - the cross-feed rate being set, as was common practice, at half those figures. If Modul or Diametral pitches were required, a separate set of changewheels has to be mounted on the gear quadrant. A less-expensive option, and adequate for general or production work, was a Norton quick-change type with an open front and a conventional sliding tumbler. Fitted with this box (it provided eighteen inch pitches and feeds together with seventeen) the model designation for the smallest machine became RS-20S - though on the larger versions, as this was just a money-saving "delete" option, no specific model type was listed. Drive to the apron was by a slotted powershaft, working through an overload safety clutch, with the 35 mm diameter, 4 t.p.i. leadscrew driven from this by a gear that that could be slid (by a knurled ring) into and out of mesh as required. Continued below:
|
|
|
|
|
|
|
 |
|
|
|
|
|
|
Continued: Doubled-walled, with all shafts supported at both ends, the apron had an oil sump in the base with an automatic pump to distribute lubricant around the interior and to the cross-slide and bed ways. Longitudinal and cross feeds were controlled by that most desirable of features (first used by Hendey in the USA) of toothed-couplings operated by individual levers with a separate snap-in, snap-out engagement lever that put the worm-and wheel gearing into and out of mesh. Realising that few operators would bother to use the saddle as a boring table, Rosenfors wisely saved money by not bothering to machine the long saddle wings with T-slots. On straight-bed models the compound slide assembly was mounted centrally and, with the bed ways reaching a little way down past front and back of the headstock, the saddle could still be positioned so that the toolpost came right up to the spindle nose. On gap-bed types the slide rest was moved to the extreme left-hand end of the saddle, the better to reach over the gap with the bridge piece out. With tapered gib strips on top and cross slides the compound slide assembly was ruggedly constructed, equipped with a ball-thrust bearing on the cross-feed - but fitted with rather small micrometer dials. Although the cross-slide was wide, it was (in order to provide room for the taper-turning attachment link piece) rather short. However, an alternative full-length slide could be fitted that had a machined surface at the rear to mount either a "Roscop" No. 1 or No. 2 hydraulic copying attachment or rear toolpost - the latter also available as an unusual assembly that could mount a series of posts side by side for profiling work. The longer cross slide would have been the preferred choice for day-to-day work: the greater bearing area, more rigid assembly and even wear of the ways all being important considerations. Bolted to the cross slide by 4 T-bolts, the top slide had, for the convenience of the operator, rotational degree engravings at both front and rear. The slide was available with either a T-slot to mount the owners toolpost of choice, or an integral post to fit the maker's indexing 4-way type. Looking as though it might have been an orphan from an earlier model, the smoothly rounded tailstock was quite at variance with the angular lines of the rest of the lathe. Nevertheless, it was well designed, with a hardened and ground barrel running in a lapped bore. Spindle diameter for the two smaller lathes was 55 mm, with 160 mm of travel and a No. 4 Morse taper and 65 mm on the larger pair with a travel of 200 mm and a No. 5 Morse nose. If any reader has a Rosenfors machine tool the writer would be interested to hear from you..
|
|
|
|
|
|
|
|
|
|
|
|
|
 |
|
|
|
|
|
|
Rosenfors compound slide rest with an extended, full-length cross slide mounting a battery of rear toolpost for forming of parting-off work. A multi-position stop can be seen bolted to the front right-hand wing of the saddle
|
|
|
|
|
|
|
 |
|
|
|
|
|
|
Long-bed Rosenfors RS-25/RS-30 with central support plinth for the bed
|
|
|
|
|
|
|
 |
|
|
|
|
 |
|
|
|
|
|
|
Standard Rosenfors spindle nose
|
|
|
|
|
|
|
 |
|
|
|
|
|
|
Alternative American Long-nose Taper spindle end
|
|
|
|
|
|
|
 |
|
|
|
|
|
|
Rosenfors "Roscop" hydraulic copying attachment
|
|
|
|
|
|
|
 |
|
|
|
|
|
|
|
|
|
|
|