 |
 |
 |
 |
 |
 |
 |
 |
 |
 |
 |
 |
 |
 |
 |
 |
 |
 |
 |
 |
 |
 |
 |
 |
 |
 |
 |
 |
 |
 |
 |
 |
 |
 |
 |
 |
 |
 |
 |
 |
 |
 |
 |
 |
 |
 |
 |
 |
 |
 |
 |
 |
 |
 |
 |
 |
 |
 |
 |
 |
 |
|
|
|
|
|
|
|
|
|
|
|
|
|
|
|
|
|
|
|
|
|
|
|
|
|
|
|
|
|
|
|
|
|
|
|
|
|
|
|
|
|
|
|
|
|
|
|
|
|
|
|
|
|
|
|
|
|
|
|
|
|
|
|
|
|
|
|
|
|
|
email: tony@lathes.co.uk Home Machine Tool Archive Machine-tools Sale & Wanted Machine Tool Manuals Catalogues Belts Books Accessories Potts Milling Spindles, Milling Column and Tailstock Capstan Unit
Potts Page 2
During the 1940s and 1950s, the G.P. Potts Company, based in Troutbeck, Windermere, was best known for three versions of their cleverly designed, beautifully made, column-type high-speed milling and grinding unit that was used in place of a lathe's top slide. The device could be had as a complete, ready-to-use unit or as a set of casting for the buyer to complete. If considering one of these units, do examine it carefully, it might be that one finished by an amateur might not be entirely satisfactory and require some ratification. slide of small lathes to assist with more complex milling operations, gear-cutting and ornamental turning. The Potts milling attachment has proved to be a most In addition to a six-station capstan head, fitted with a Morse taper arbor and used in a lathe's tailstock, Potts also manufactured a range of independent high-speed milling heads intended to be mounted on the top useful unit; it allows almost any small lathe to be used for clock-making work including milling, indexing and gear cutting. Supplied as standard with a through-T-bolt, the base of the unit is easily modified to fit almost any lathe cross slide, including ones like the Boxford with its "inverted cone" fitting. Unfortunately, if the top slide is held on fixed post like the Raglan "Little John" or Myford/Drumming M-Type lathe with its Norman Patent height-adjustable toolpost, the fitting is very much more difficult, though a special clamp-on version was available for the latter machine. With their spindles running in hardened bearings, two of the three attachments for the milling unit were designed to mount on a hinged bracket (that allowed them to be used for milling and toolpost grinding) while the third was as built as an integral part of a milling slide. The latter type consisted of a 1.75" diameter column some 6.5" long (intended to be secured to a lathe's cross slide) with the spindle assembly able to be moved up and down through a range of 3.75" and also swivelled. A feed-screw of Acme form was fitted, complete with a finely-engraved bevelled-faced zeroing micrometer dial - and the rotating part of the head marked with similarly-clear degree graduations. The milling column might also, originally, have been intended to carry a simple dividing attachment fitted with changewheels taken from the owner's lathe - or even as a proper dividing attachment with an overarm and a selection of division plates. If the latter was factory made, it is very rare, with only one example being found in recent times. It was also possible to mount a high-speed milling spindle, powered from an "overhead" (often a complicated and expensive drive system arranged above the lathe) but today more easily driven from a small motor carried on a bracket. The writer has seen several home-made, self-powered milling, drilling and gear-cutting attachments made up for the Potts spindle, these being driven by small, 24-volt DC variable-speed motor or similar types. Had they been available in the 1950s, no doubt they would have offered something similar. In addition to the genuine Potts spindle, a good number of beautifully built home-made versions have also been found - probably from commercial kits or (with one found by the writer) made when the toolroom was less busy or surreptitiously on the night shift …. Shown towards the bottom of the page are two long-popular, sought-after independent high-speed heads for use on a lathe's top slide. Available with the pulley positioned between the bearings (as the Mk. 1) or overhung (Mk. 2), each was supplied with three 8 mm draw-in collets and a plastic-handled drawbar. Potts also offered a well-made 7" x 4.5" saw table designed to mount on the bed of almost any small lathe. In 1949 this was listed at £3 : 10s : 0d finished or, for just the casting, 16 shillings.
|
|
|
|
|
|
|
|
|
|
|
|
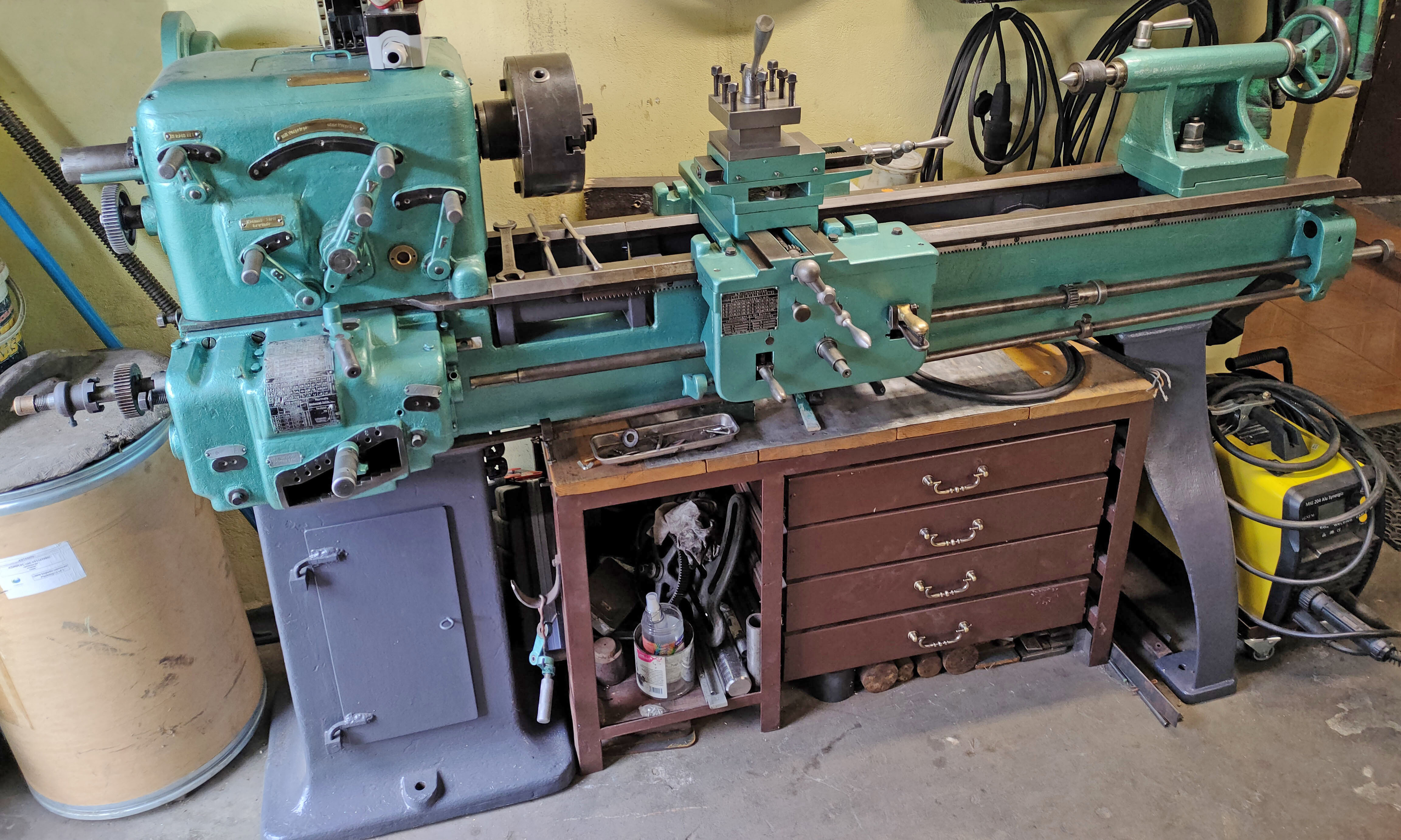 |
|
|
|
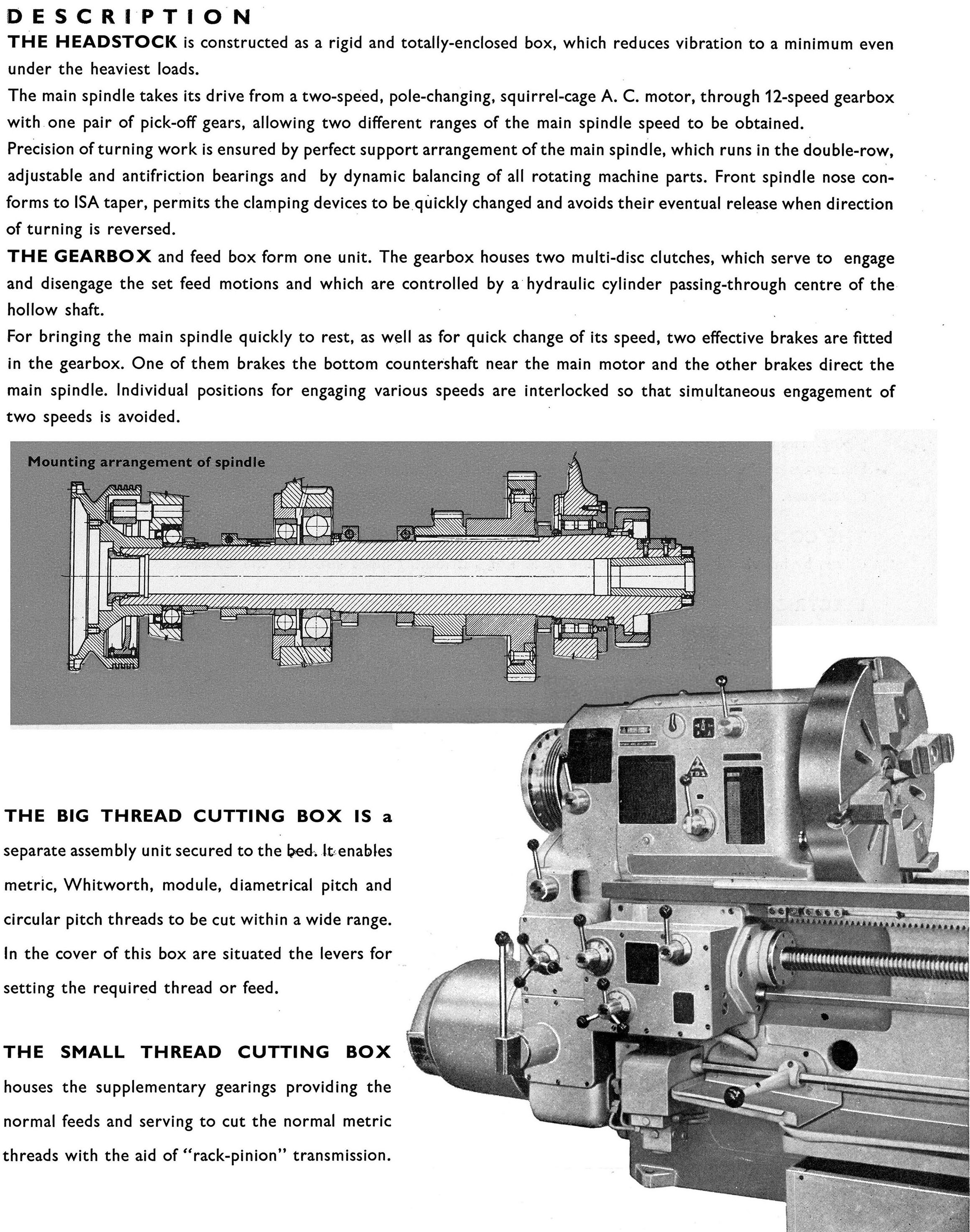 |
|
|
|
|
|
|
Versatility. Potts spindle set up on a lathe to machine job held in a wood-collet chuck.
|
|
|
|
|
|
|
|
|
|
|
The high-speed collet-holding spindle is held on a rotating boss
|
|
|
|
|
|
|
|
|
|
 |
|
 |
|
|
|
|
|
|
The heads can be moved up and down the column or clamped to it with a pinch bolt
|
|
|
|
|
|
|
|
|
|
|
|
|
A drive pulley should be fastened to the end of the keyed shaft
|
|
|
|
|
|
|
|
|
|
|
|
|
|
|
 |
|
 |
|
|
|
|
|
|
Finely engraved zeroing micrometer dial
|
|
|
|
|
|
|
|
|
|
|
 |
|
|
|
|
|
|
Degree graduations on the swivel boss
|
|
|
|
|
|
|
|
|
|
|
Acme-form feed screw with a neat, zeroing micrometer dial
|
|
|
|
|
|
|
|
|
|
 |
|
|
|
|
Possibly a early Potts fitted with a bracket and arm to engage with a simple dividing mechanism that would have accepted changewheels from the owner's lathe.
|
|
|
|
|
|
|
|
|
|
|
|
|
|
 |
|
|
|
|
|
|
Potts type vertical column fitted with a proper dividing attachment
|
|
|
|
|
|
|
 |
|
|
|
|
|
|
What must be a "home-made" assembly complete with a high-speed milling/grinding head with a jockey-pulley arrangement to guide the drive belt
|
|
|
|
|
|
|
 |
|
|
|
|
|
|
Another well-made but non-Potts unit with both an indexing wheel and division plate
|
|
|
|
|
|
|
 |
|
|
|
|
|
|
|
|
|
 |
|
|
|
|
 |
|
|
|
|
 |
|
|
|
|
|
|
|
|
|
|
 |
|
|
|
|
|
|
Potts Mk. 1 high-speed milling and grinding spindle with drive pulley between the bearings
|
|
|
|
|
|
|
 |
|
|
|
|
|
|
Potts Mk. 2 high-speed milling and grinding spindle with overhung drive pulley
|
|
|
|
|
|
|
 |
|
|
|
|
|
|
Potts Mk. 1 high-speed milling spindle mounted using the toolpost clamp on the top slide of a Myford ML10 lathe
|
|
|
|
|
|
|
 |
|
|
|
|
 |
|
|
|
|
|
|
Potts Mk. 2 high-speed spindle unit mounted on the cross slide of a Myford ML10 lathe
|
|
|
|
|
|
|
 |
|
|
|
|
|
|
|
|
|
 |
|
|
|
|
 |
|
|
|
|
|
 |
|
|
 |
|
|
|
|
|
|
|
 |
|
|
|
|
|
|
|
|
|
 |
|
|
|
|
|
|
|
|
|
Potts 6-station tailstock-mounted capstan unit
|
|
|
|
|
|
|
|
|
 |
|
|
|
|
 |
|
|
|
|
|
|
|
|
|
|
|