 |
 |
 |
 |
 |
 |
 |
 |
 |
 |
 |
 |
 |
 |
 |
 |
 |
 |
 |
 |
 |
 |
 |
 |
 |
 |
 |
 |
 |
 |
 |
 |
 |
 |
 |
 |
 |
 |
 |
 |
 |
 |
 |
 |
 |
 |
 |
 |
 |
 |
 |
 |
 |
 |
 |
 |
 |
 |
|
|
|
|
|
|
|
|
|
|
|
|
|
|
|
|
|
|
|
|
|
|
|
|
|
|
|
|
|
|
|
|
|
|
|
|
|
|
|
|
|
|
|
|
|
|
|
|
|
|
|
|
|
|
|
|
|
|
|
|
|
|
|
|
|
|
|
|
|
email: tony@lathes.co.uk Home Machine Tool Archive Machine-tools Sale & Wanted Machine Tool Manuals Catalogues Belts Books Accessories
Matheys Semi Jig Boring & Universal Toolroom Milling Machines" FPN-28, FPN-28-PO, FPN-2S, FPN-2S-PO SP.30, SP.35, 35.NC & 3A
Matheys Continued on Page 2
Matheys Drilling Machines
A detailed Catalogue is available for Matheys machines
Manufactured by Etablissements G. Matheys of 36 Rue Gallait, Brussels, Belgium, the Matheys "Semi-jig boring" machines were sold from the late 1940s until the 1970s. They were especially well-made machines, carefully finished and designed to be capable of undertaking both light milling work and accurate jig boring, the specification including an internally ribbed main column and chill-cast slideways. So far, five main versions have been identified: the early FPN-28 miller and FPN-28PO semi-jig borer from the late 1940s, the SP.30 from the early 1950s, the rather different and heavier mid-1950s SP.35 and the final models, from the 1960s, the 35-NC and 3-A (the latter shown towards the bottom of this page). Introduced during 1949, the FPN-28 and FPN-PO, began life with their heads capable of movement up and down some 7.85" on a long, round bar that was secured in a square casting bolted to the top of the main column. Combined with the knee's movement, a total vertical travel of 13.37" was available with a maximum clearance between the table and spindle nose of 20". As the sliding head assembly must have proved less rigid than desired, it was abandoned and a new model, the Type SP.30 introduced. Fitted with the same knee and table assembly as before, the SP.30 had its head fixed and formed as part of a very much more massive, bolt-on casting that held a modified drive system - this new arrangement adding approximately 240 lbs to the overall weight that now stood at 1250 lbs for a basic model. The maximum distance from spindle nose to table was, of course, reduced slightly - but only by just over 1 inch Three drive options were offered originally, though these were to be altered over the years with a number of different catalogue listings: however, at first, the choices offered were: a single speed 1.35 hp running at 700 rpm motor; a 3-speed of 1.25 h.p./700 r.p.m., 1.6 h.p./1000 r.p.m., 2.2 h.p./1500 r.p.m. and the 3-speed motor fitted to a continuously variable-speed drive unit of the swash-plate type, flange mounted to the motor body. Bolted to the back of the head, the motor drove forwards through a 5-step V-pulley to the spindle, speeds obtained from the single-speed motor being 180, 300, 540, 930, 1750 r.p.m. From the 3-speed motor a very much more useful range of fifteen was available, from a slowest of 180 through 275, 300, 360, 450, 540, 600, 810, 930, 1080, 1400, 1750, 1860, 2600 and 3750 rpm. The variable-speed unit, in all its forms, used a 2-step V-pulley drive that gave a high and a low speed ranges; when equipped with the 3-speed motor the speeds available spanned a very wide range, from 70 to 3500 r.p.m. Bored with a No. 3 Morse taper and supplied with a chuck to take Brown and Sharpe collets, the spindle was held in a 2.85-inch diameter quill, this being lapped to its housing and with a travel of 5.5". Quill feed was by either a quick-action lever for drilling (using rack-and-pinion gearing) or, controlled by a full-circle handwheel, through a worm-and-wheel gearbox for fine feeds. As an option, a clutched power feed was available that gave, per revolution of the spindle, three rates of feed set at 0.003", 0.006" and 0.009". When ordered as the "PO" jig borer, all three table feeds were by hand - though there was the option of a power-feed gearbox - with the 5 t.p.i. screws hardened and ground and passing through bronze nuts held within an anti-backlash enclosure. Large diameter, bevelled-faced micrometer dial were fitted and equipped with face-locking screws, this design obviating any change in reading when operated. The table, 9.25" wide, was available in two lengths, standard at 33.5" or, optionally, a shorter version at 25.625". Longitudinal table travel of the shorter type was 17.75" and the longer 25.75"; the cross travel, at 6.688", being the same for both. However, when fitted with power feed, the longitudinal travel was reduced to around 21.75". Both longitudinal and traverse travels were equipped with slides to hold slip gauges (Jo-blocks) that were used together with a combined micrometer barrel (that read to 0.0005" on its thimble) and a quadrant-faced dial indicator graduated to 0.00005". With careful use the system allowed hole spacing to be maintained to within an accuracy of 0.004" with a maximum hole spacing of 24" If the machine was supplied as the Type FPN-28 for milling rather than jig-boring, the makers recommended the fitting of a table power-feed gearbox, this being bolted to the underside of the saddle left-hand end and equipped with a motor flange-mounted against its rear face. Six rates of feed were available, these being unchanged for all models up to, and including, the SP.35 at 0.64, 0.96, 1.28, 1.92, 2.56 and 3.84 inches per minute. Continued below:
|
|
|
|
|
|
|
|
|
|
|
|
|
|
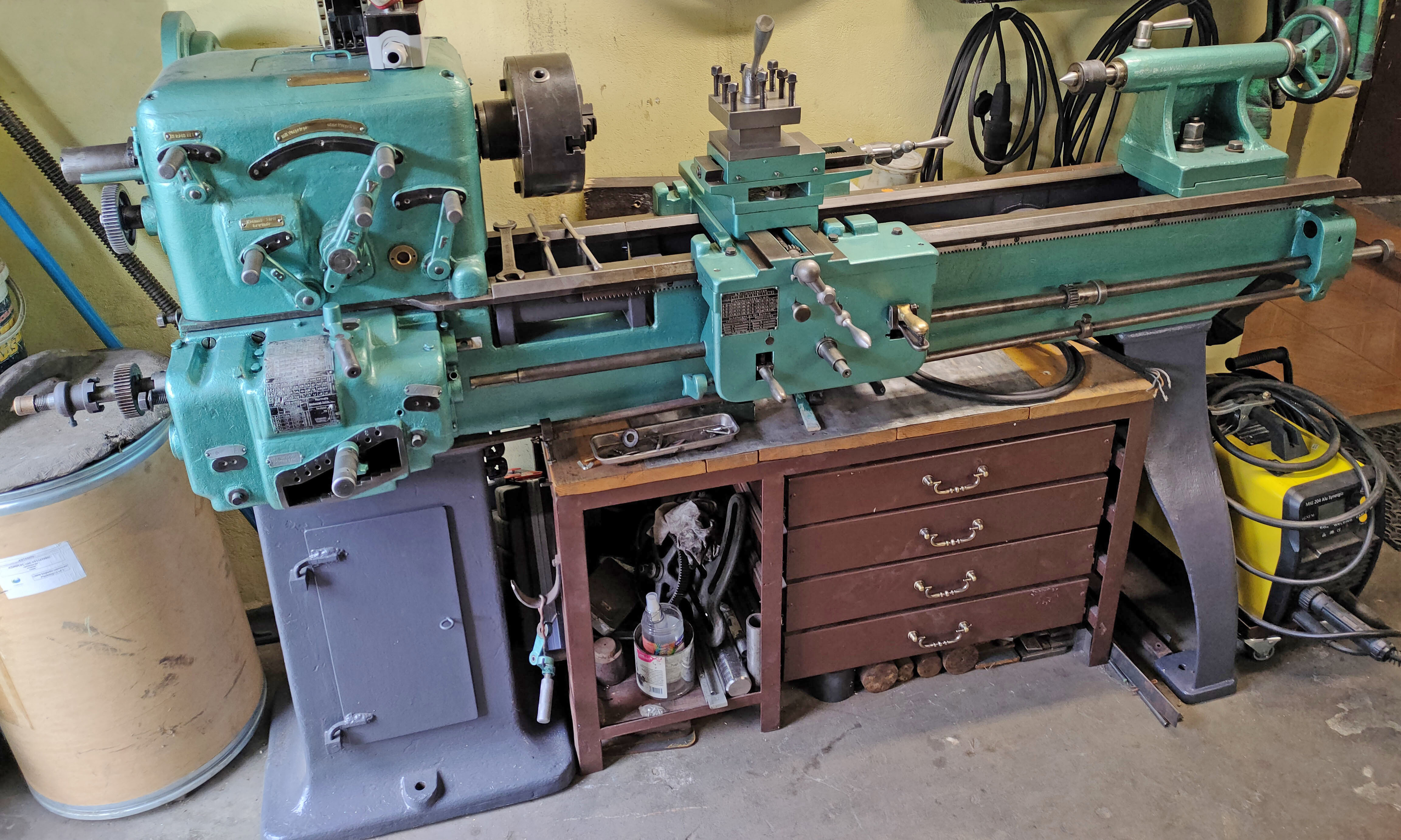 |
|
|
|
|
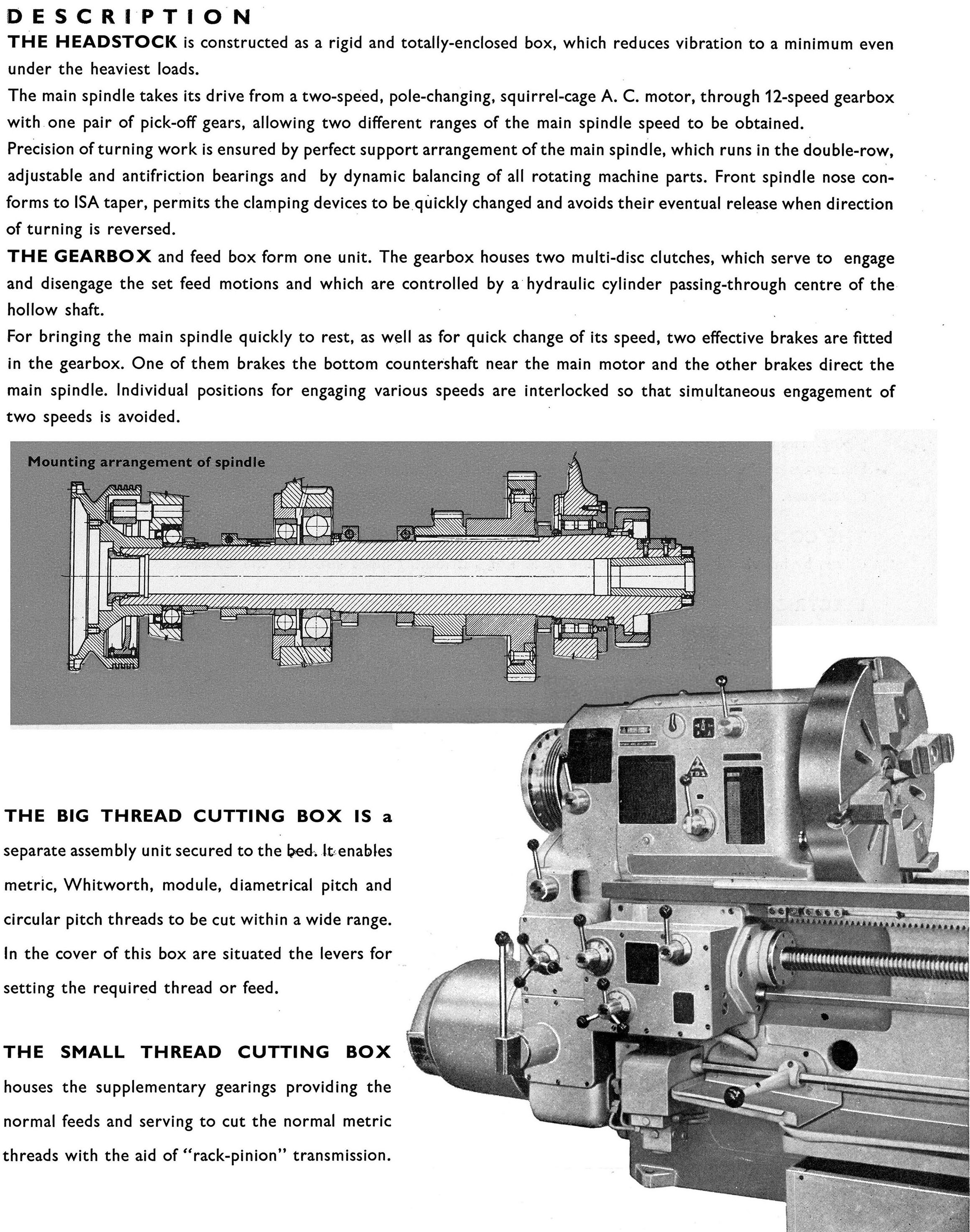 |
|
|
|
|
|
|
|
|
 |
|
|
|
|
|
|
Matheys FPN-28 miller and FPN-PO semi-jig borer
|
|
|
|
|
|
|
|
 |
|
|
|
|
|
|
Matheys SP.30, SP.30-PO as introduced in the very early 1950s. This example is shown as supplied for jig boring with hardened and ground table feed screws in a high tensile steel that ran though bronze nuts fitted with anti-backlash adjustment, V-groove holders for precision length rods and dial gauges on the table's longitudinal and traverse movements, a boring head with automatic radial feed and a standard, single-speed motor.
|
|
|
|
|
|
|
|
|
|
|
|
Continued: Built to the same standards as the earlier model, the SP.30 differed in several ways, including the previously mentioned change of head assembly. As before, the spindle-drive motor was bolted to the rear face but fitted, this time, with a 2-step V-pulley that drove forwards to an intermediate pulley formed to take the 2-speed drive on its lower section while the upper section had a 3-step that drove the spindle. The result was a range of 6 speeds - 130, 220, 380, 600, 1050 and 1800 r.p.m., only one more than before but arranged so that the slowest was 28% slower and, being driven through a 2-step drive, with greatly enhanced torque. Other alterations included a beefed-up knee-lift screw (fitted with a more easily operated crank handle instead of the former full-circle handwheel), the deletion from the sales catalogue of the 3-speed motor option and the replacement of the slip-gauge holders with V-shaped rails to held dead-length measuring rods. As before, the same combined micrometer barrel and quadrant-faced dial indicator was used and the accuracy remained unchanged - though costs were reduced and ease of use improved by the need for just six 1", 2", 3", 4" 6" and 8" long rods. Matheys SP.35 standard and SP35-PO Jig Borer Of much greater mass, the new-for-1955 SP.35 weighed, at 2340 lbs, nearly twice as much as the 1250 lbs of the SP.30. Instead of a two-part column with a top section bolted on, the SP.35 had one formed in a single, rigid piece with, machined into the upper front face, widely spaced ways on which a vertical head could be elevated, through a range of 5.75 inches. Control was by a large handwheel, the head being balanced by a counterweight within the column. Drive was standardised as the swash-plate variable-speed type, this being combined a 2.5 h.p. motor that gave a speed range spanning 80 to 1680 r.p.m.. As the arrangement used 2-step pulleys to give high and low ranges, the mechanism was not truly stepless but required a manual change between the two settings. From the motor the drive passed to a ball-bearing supported pulley whose mounting shaft passed downwards into the column. The lower section of the shaft was splined and carried a 3-step V-pulley that drove the spindle - the pulley sliding up and down the splines in sympathy with the head. Between the splined shaft and the spindle was a second vertical shaft, this holding a jockey pulley to tension the 3 V-belts and the bevel gearing to drive the spindle power down feed. Formed with an American Standard (AS) No. 30 taper, the spindle was held in a 3.23-inch diameter quill, this being lapped to its housing and with a travel of 5.5" moved by either a quick-action lever for drilling (using rack-and-pinion gearing) or, controlled by a full-circle handwheel, through a worm-and-wheel gearbox for fine feeds. Fitted as standard was a clutched power feed mechanism that gave, per revolution of the spindle, three rates of feed set at 0.003", 0.006" and 0.009". A single length of table was fitted as standard - 33.5" x 11.8" - with a longitudinal travel of 21.75", in traverse of 10" and vertically 12.75" with a maximum distance between spindle nose and table of 21.25". When specified for use as a jig borer, all three table feeds were by hand - though with the addition of a micrometer fine-feed 4:1 reduction drive to the longitudinal screw. However, the option did exist of ordering the same power-feed gearbox fitted to the milling machine version, this having six rates of feed: 0.64, 0.96, 1.28, 1.92, 2.56 and 3.84 inches per minute. The 5 t.p.i. screws were hardened and ground and passed through bronze nuts, these being held within an enclosure that allowed backlash to be adjusted out. The same large diameter, bevelled-faced micrometer dials used on earlier models were retained together with their "non-upset" face-locking screws. A new option, where greater accuracy was needed for more general milling work, was a 4:1 ratio reduction micrometer fine-feed attachment for both longitudinal and cross-feed screws (it was fitted as standard on the jig borers). Both horizontal table travels were equipped with slides to hold slip gauges (Jo-blocks) that were used together with a combined micrometer barrel (that read to 0.0005" on its thimble) and a quadrant-faced dial indicator graduated to 0.00005". With the usual proviso of careful use by an experienced operator, the system allowed hole spacing to be maintained to within an accuracy of 0.004" with a maximum hole spacing of 24 inches. Supplied with each new SP.30 was a complete electrical installation and single-speed motor, the required V-belts, a collet chuck and three collets, a grease, spindle draw-bar, keys and an operator's handbook. In addition, the SP.30PO included the 4:1 reduction ratio micrometer fine-feed to the table's longitudinal feed, V-trays to hold the precision length rods (the rods were extra), two quick-setting rulers and four reducing sleeves for the spindle. Fitted as part of the standard equipment on every SP.35 was the attachment for holding measuring rods, infinitely-variable speed drive and motor unit, a set of belts, a hardened and ground collet chuck with eight collets, two draw-bars, four spindle reducing sleeves, a grease gun and Operator's handbook. Additional accessories included optical measuring equipment, table power feed gearbox, a boxed set of six measuring rods, coolant equipment, standard or low-voltage lighting, 3-jaw chucks, micrometer and plain and universal boring heads, a centring device with universal gauge, an optical centring attachment, circular and sine tables in plain and universal forms, a universal adjustable swivel and tilting unit able to take a T-slotted flat top or rotary table, a swivel and tilt machine vice and a pneumatic planetary jig grinding attachment complete with micrometer adjustment and a boxed set of grinding wheels..
|
|
|
|
|
|
|
|
|
|
|
|
|
|
 |
|
|
|
|
|
|
Cross section through the head of the Matheys SP.35
|
|
|
|
|
|
|
|
 |
|
|
|
|
|
|
Matheys Jig Boring and Universal Milling Machine Model SP.30 as supplied for milling. The specification recommended included standard, non-hardened table feed screws, a infinitely variable-speed swash-plate drive unit fitted to the spindle drive motor (speed control was by a handwheel on the unit's left-hand side) a table power-feed gearbox bolted to the underside of the saddle's left-hand end and the maker's "Universal" swivel and tilting table. Lighting and coolant were also available, the cast-iron tank and its pump being mounted on the back of the column
|
|
|
|
|
|
|
|
 |
|
|
|
|
|
|
Matheys Model SP.35 left-hand view. Fitted as part of the standard specification to a machine that weighed twice that of an SP.30, was equipment that allowed it to be used as both a jig borer and milling machine with items including: swash-plate infinitely variable-speed spindle drive, power downfeed to the spindle, hardened and ground table feed screws in a high tensile steel that ran though bronze nuts fitted with anti-backlash adjustment, V-groove holders for precision length rods and dial gauges on the table's longitudinal and traverse movements and coolant equipment and lighting
|
|
|
|
|
|
|
|
|
|
|
|
|
|
 |
|
|
|
|
|
|
Matheys Jig Boring and Universal Milling Machine Model SP.35 right-hand view
|
|
|
|
|
|
|
|
 |
|
|
|
|
|
|
An accurate though now obsolete way of setting a job where the longitudinal and cross feeds were equipped with V-shaped rails, these holding dead-length measuring rods whose position could be adjusted by a combined micrometer barrel (that read to 0.0005" on its thimble) and a quadrant-faced dial indicator graduated to 0.00005". With careful use the system allowed hole spacing to be maintained to within an accuracy of 0.004", the range limit from hole to hole being 24" with just six rods required, these being in lengths of 1", 2", 3", 4" 6" and 8".
|
|
|
|
|
|
|
|
 |
|
|
|
|
|
|
Where greater accuracy was needed for more general milling work, the makers offered a 4:1 ratio reduction micrometer fine-feed attachment for both longitudinal and cross-feed screws (it was fitted as standard on the jig borers). Note the large diameter, bevelled-faced micrometer dial and its face-locking screw, the latter a design that obviated any change in reading when operated.
|
|
|
|
|
|
|
|
 |
|
|
|
|
|
|
Another contemporary option (during the 1940s and 1950s) was an optical system that read from high-precision graduated rulers
|
|
|
|
|
|
|
|
|
|
|
|
|
|
 |
|
|
|
|
|
|
Jig boring using a micrometer-adjustable boring head
|
|
|
|
|
|
|
|
 |
|
|
|
|
|
|
Matheys Model SP.35 being used for fine jig drilling in a London toolroom
|
|
|
|
|
|
|
|
 |
|
|
|
|
|
 |
|
|
|
|
|
|
Milling a spindle between centres using a plain dividing head
|
|
|
|
|
|
|
|
|
|
|
|
|
|
 |
|
|
|
|
|
|
An ordinary vertical milling operation
|
|
|
|
|
|
|
|
 |
|
|
|
|
|
|
The longitudinal and traverse feed screws on the jig-boring model were each fitted with a compensating nut in bronze to take out backlash
|
|
|
|
|
|
|
|
 |
|
|
|
|
|
|
A selection of maker's accessories for the SP.30
|
|
|
|
|
|
|
|
 |
|
|
|
|
|
A selection of maker's accessories for the SP.30
|
|
|
|
|
|
|
|
|
|
|
|
|
|
 |
|
|
|
|
|
|
A micrometer-adjustable pneumatic planetary jig grinding attachment with its accessories
|
|
|
|
|
|
|
|
 |
|
|
|
|
Swivel and tilting universal table with a detachable table that could be either a flat-topped T-slotted or rotary type.
|
|
|
|
|
|
|
|
|
|
|
 |
|
|
|
|
|
|
A line of SP.35 machines awaiting their final tests before dispatch
|
|
|
|
|
|
|
|
 |
|
|
|
|
|
|
Matheys SP.30 or SP.30-PO with a hand-feed table - but no provision for mounting length rods
|
|
|
|
|
|
|
|
|
|
|
|
|
|
 |
|
|
|
|
|
|
|
|
|
As before, on earlier machines, the spindle-drive motor was bolted to the rear face of the column but fitted, this time, with a 2-step V-pulley that drove forwards to an intermediate pulley formed to take the 2-speed drive on its lower section while the upper section had a 3-step that drove the spindle. The result was a range of 6 speeds - 130, 220, 380, 600, 1050 and 1800 r.p.m., only one more than before but arranged so that the slowest was 28% slower and, being driven through a 2-step drive, with greatly enhanced torque.
|
|
|
|
|
|
|
|
|
|
|
|