 |
 |
 |
 |
 |
 |
 |
 |
 |
 |
 |
 |
 |
 |
 |
 |
 |
|
|
|
|
|
|
|
|
|
|
|
|
|
|
|
|
|
|
|
|
|
|
|
|
|
|
|
|
|
|
|
Martin lathes were made by K. Martin Machinenfabrik of 76 Offenburg, Germany, a company long established in the field of high-quality precision machine tools. In the UK the brand was handled by Stanton Machine Tools Ltd. of Rembrant House, Hagden Lane, Watford. Over many years Martin offered a wide variety of lathe but probably their most popular and widely exported were the DLZ502, DLZ602, DLZ702 and the D Series consisting of the D36, D42, D51, DS36, DS42 and DS51 "High Production and Toolroom" type. These were machines developed from an earlier series and noted for their very heavy construction, the use of fine-quality materials and scrupulous attention to detail. The D and DS ranges were of identical major construction but, whilst the former had 12 spindle speeds from either 22.4 to 1000 r.p.m or (optionally) 31.5 to 1400 r.p.m., the latter had 28 that spanned a much more useful and appropriate 22.4 to 2240 r.p.m or (optionally) 31.5 to 3150 r.p.m. Although the centre height of the models differed - D & DS-36 7-inch (180 mm), D & DS-42 8.25-inch (210 mm) and D & DS-51 10-inch (255 mm) - all were built on the same very deep, closely cross-ribbed (and hence very rigid) 13.25-inch wide bed fitted with hardened and ground steel ways to Rc 58-60. A detachable gap was optional on all versions and, when fitted, allowed material 22-inches (560 mm), 24.5-inches (620 mm) and 27.5-inches (700 mm) by 9.5-inches (245 mm) deep to be turned respectively according to centre height. The makers cautioned that the two machines with the largest centre height in each range were raised models and should not be used to the limit of their capacity but only for "light or medium-duty" turning of large workpieces. Eight bed lengths were offered for each version that gave between-centres capacities of: 20-inches (500 mm), 30-inches (750 mm), 40-inches (1000 mm), 60-inches (1500 mm), 80-inches (2000 mm), 98-inches (2500 mm) and 118-inches (3000 mm). The maximum weight allowed between centres was 900 Kg or, with two fixed steadies to assist, 1200 Kg. The bed was mounted on massive cast-iron plinths at each end with large cast-in lugs on their outer faces that allowed the lathe to be lifted with any risk of distorting the bed or damaging the control handles. Continued below:
|
|
|
|
|
|
|
|
|
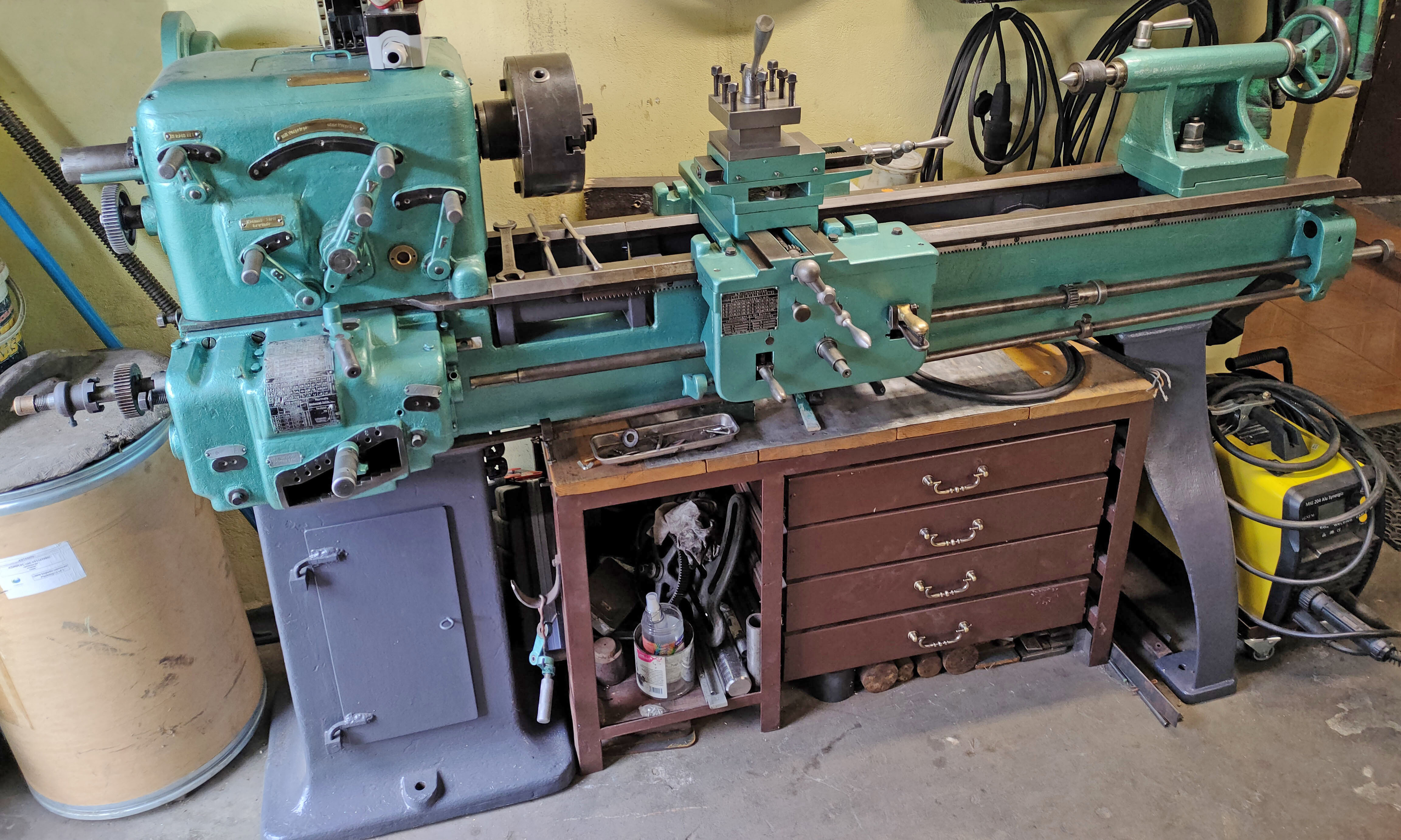 |
|
|
|
|
|
|
Martin D & DS lathe
Continued: The same basic headstock, used for every lathe in the range, was of robust construction with its 1.75-inch (45 mm) bore spindle running in English-made "Gamet" super-precision double-taper roller bearings at the front and two-row roller bearings at the rear. The spindle carried a No. 4-Morse taper bore with a DIN 55022 type nose-fitting as standard but with the option of a Cam-lock type. Power came from a motor of 5.5, 7.5, 10 or 15 h.p. (the latter only for lathes with the extra 16 higher speeds) mounted on a height-adjustable plate within the base of the headstock-end plinth. Multiple V-belts took the drive up to an intermediate spindle and from there through two multi-plate clutches (built into the headstock) by which means the spindle could be very quickly started or reversed - though to save wear and tear it was possible to disable the reverse setting. For stopping, an electro-magnetic multi-disc brake was fitted by which means the spindle could be brought to a very rapid and smooth stop from high speed. Spindle speeds were selected by the juxtaposition of three levers mounted co-axially on a large boss with a window cut into its face to show the speed selected. Control of the spindle start, stop, reverse and brake was by a long control-rod set below and parallel to the powershaft with duplicated control levers to the right of the gearbox and (to ensure it was always within safe reach of the operator) pivoting from the right-hand face of the apron. Whilst both Model D and DS shared the same 12-speed gear drive in a ratio of 1:45 (in a geometrical progression of 1.4) the DS had an additional 16 speeds (in a geometrical progression of 1.18) arranged through a wide flat "non-stretch" (and non-adjustable) belt that drove a pulley connected directly to the left-hand end of the main spindle. To prevent the considerable tension of the belt interfering with the spindle the pulley was carried on its own bearings. When driven in the high-speed range (through the flat belt) the large gear immediately behind the spindle's front bearing was not used - a system that contributed to an especially smooth drive and a high-quality turned finish. All headstock gears were hardened and ground and each layshaft ran on ball races with those carrying sliding gears having ground-finished splines. Lubrication of the headstock was by a filtered supply pumped from a large tank in the base of the headstock plinth; to ensure the operator knew the oil was flowing it was first sprayed upwards into a transparent dome on top of the headstock from where it fell onto a distribution "plate" that directed the supply around headstock gears and bearings. Oil collecting in the bottom of the headstock either drained directly back into the tank or, together with a supply collected from the distribution plate, was routed through the screwcutting and feeds' gearbox. Continued below:
|
|
|
|
|
|
|
|
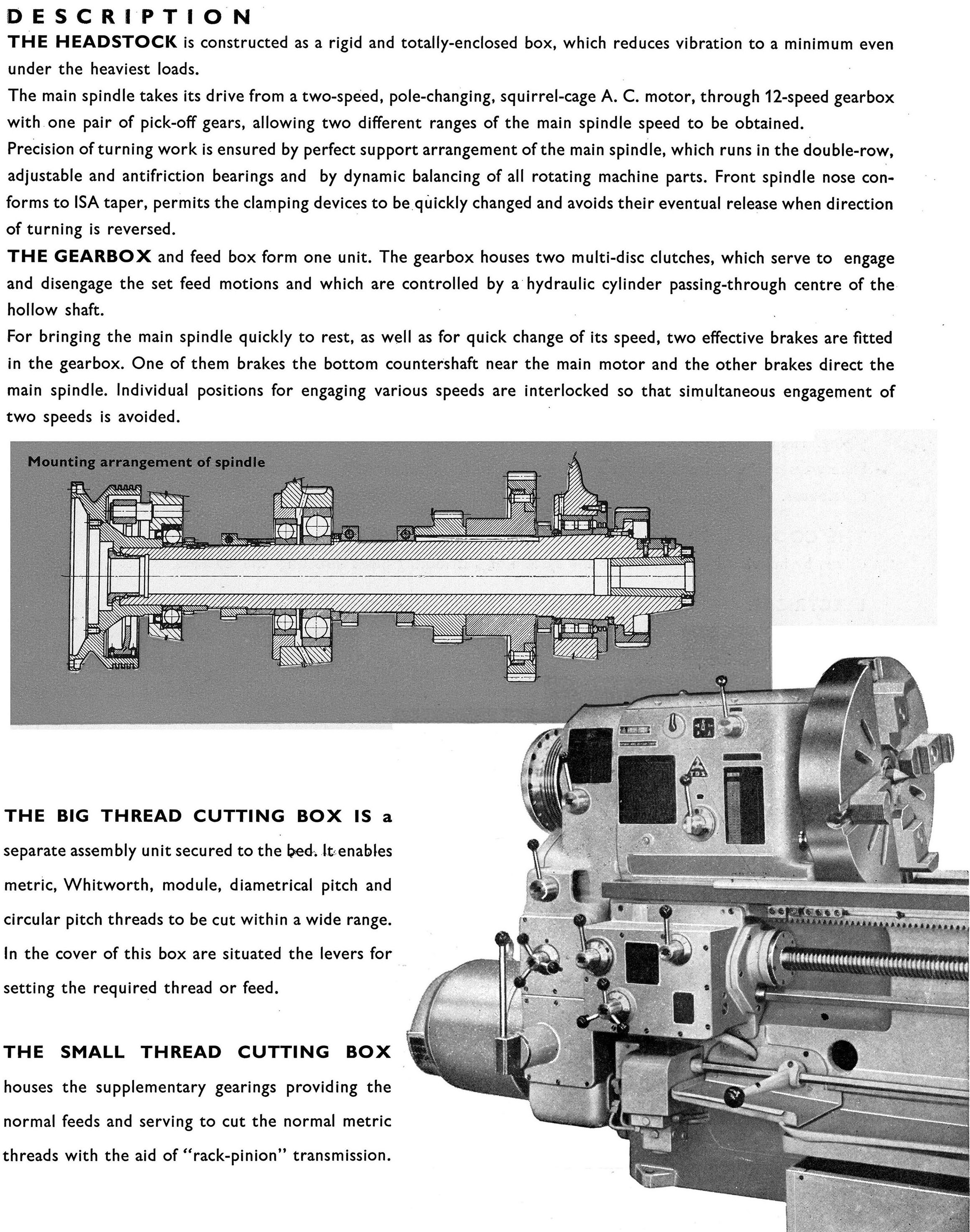 |
|
|
|
|
|
|
Neatly-arranged spindle, screwcutting and feed controls on the Models D and DS
Continued: The screwcutting and feeds' gearbox was an engineering tour-de-force with even its drive gears (contained within their own compartment) including a specially-marked "indexing wheel" to assist with the production of multi-start threads. All shafts ran on ball races and 103 metric and 118 English threads (including 11.5 and 27 t.p.i.) were available without any alteration to the changewheel set-up; whilst not quite up to the 262 available from the (rather larger) Meuser S-type Selekta lathe, this was still a very considerable achievement. Additional changewheels allowed 72 Module and 118 Diametral pitch threads to be generated or, with the usual 127t gear, for English specification models to cut metric pitches. The box could also be set to give fine threads (or feeds) at one-fifth the normal rate, or coarse pitches stepped up in the ratios of both 4:1 and 16:1. Selection of threads and feeds was by an ingenious system of just two concentric control levers with additional controls that only required moving if a change was needed to change between leadscrew and powershaft drive, or to set coarse, fine or left-hand threads. Sliding feed rates varied from 0.00053 to 0.0375-inches (0.041 to 1 mm) and surfacing from 0.000236 to 0.017 (0.0063 to 0.45 mm) - all per revolution of the spindle. While very simple to arrange for some form of automatic disengage to the sliding feed it is not so easy to fit the same facility to the cross feed - and few lathes have been so equipped, even larger ones where it would have been a valuable addition. However, the system the Martin designers managed to incorporate not only allowed both feeds to be released in both directions but also provided an adjustment whereby (through variable spring pressure) the drive could be tripped before a damaging overload could occur. As an option a quick-traverse motor and gearbox was available to drive the feeds' powershaft from its right-hand end, though this had the effect of making the lathe some 10-inches (250 mm) longer. As standard the D and DS models were fitted with a 6 mm pitch leadscrew but could be supplied, if required, with one of 4 t.p.i. or, at extra cost, 2 t.p.i. - and in both cases with the corresponding set of changewheels. Continued below:
|
|
|
|
|
|
|
|
 |
|
|
|
|
|
|
Inside the headstock of the martin D & DS Models
Continued: The apron followed the rest of the lathe in being both carefully designed and of massive proportions. Of double-wall construction it contained an oil pump that forced lubricant from a sump within its base to the shafts and gears as well as to the lathe bed and leadscrew - though only when the latter's clasps nuts were closed. An oil reservoir was also provided to lubricate the bushes in the left and right-hand walls of the apron through which the leadscrew, power-shaft and control-rod passed. The carriage traverse handwheel was of an unusual pattern: formed without spokes as a safe, solid body its face was deeply recessed to form finger grips around the inside periphery so allowing the wheel to be gripped at any point for work that required a sensitive touch. Further evidence of Martin attention to detail lay in the long saddle fitted with bed-way swarf guards that, on the headstock side, were both enormously long and arranged (cleverly) to slide under the headstock as the carriage moved towards it. The compound slide rest was of substantial proportions with the cross slide of the full-length type with two longitudinal T slots. For a lathe of this size the "balanced" feed-screw handwheels appear to have been on the small size but, bearing in mind the care with which these lathes were assembled, and the smoothness with which they operated, this was almost certainly not a drawback. The cross-feed nut was in two sections that allowed adjustments to be made to eliminate backlash and the zeroing micrometer dials on both slides were clearly engraved, black markings on a white background. With a travel of 6.75-inches (170 mm) the 2.5-inch diameter 4-Morse taper tailstock barrel was ideally sized to the lathes capabilities. It was locked by a traverse compression bolt and the tailstock itself secured to the bed by a double-cam-action bar operated by a lever protruding from the rear of the assembly. Although the precise level of equipment would have varied from market to market for the UK the list price included complete electrical equipment for 400/440V 3-phase (with a 5.5 h.p. motor as standard) a long T-slotted cross slide, thread-dial indicator, a graduated handwheel for the carriage drive, gearing for coarse-pitch threads and fine feeds, single longitudinal and cross feed stops, a set of changewheels including one marked for multi-start threads, chromium-plated handwheels, a single toolpost, headstock reduction sleeve, oil tray, Ampere-meter, set of spanners, two No. 4-Morse taper centres, grease gun and handbook. The lightest short-bed standard D/DS model weighed approximately 4000 lbs (1820 Kg) and the heaviest long-bed high-speed version around 7820 lbs (3310 Kg.) Prices for the same models during the mid 1960s varied from £2621 to £3321..
|
|
|
|
|
|
|
|
 |
|
|
|
|
|
|
|
|
|
|
|
|
|
|
|
|
|
 |
|
|
|
|
|
|
Gear train to the screwcutting and feeds gearbox was contained within its own compartment and included a specially-marked "indexing wheel" to assist with the production of multi-start threads. Note the large cast lugs on the end face of the stand that (in conjunction with ones at the other end of course) allowed the lathe to be lifted with any risk of distorting the bed or damaging the control handles.
|
|
|
|
|
|
|
|
 |
|
|
|
|
|
|
Neatly arranged but inaccessible electrical contactors in the back of the headstock-end plinth
|
|
|
|
|
|
|
|
|
|
|
|
|
|
|
|
|
|
|