 |
 |
 |
 |
 |
 |
 |
 |
 |
 |
 |
 |
 |
 |
 |
 |
 |
 |
 |
 |
 |
 |
 |
 |
 |
 |
 |
 |
 |
 |
 |
 |
 |
 |
 |
 |
 |
 |
 |
 |
 |
 |
 |
 |
 |
 |
 |
 |
 |
 |
 |
 |
 |
 |
 |
 |
 |
 |
 |
 |
 |
 |
|
|
|
|
|
|
|
|
|
|
|
|
|
|
|
|
|
|
|
|
|
|
|
|
|
|
|
|
|
|
|
|
|
|
|
|
|
|
|
|
|
|
|
|
|
|
|
|
|
|
|
|
|
|
|
|
|
|
|
|
|
|
|
|
|
|
|
|
|
|
|
|
|
|
|
|
|
|
Manufactured by the Ikegai Iron Works, Ltd. (a lathe maker since 1889) at 1, 4 Chome, Shiba, Minato-ku, Tokyo in Japan), the Ikegai A-20 and DA63 and DA46 lathes were toolroom-class machines of very high quality With a 10-inch centre height, the A-20 was offered in short and long-bed versions that admitted, respectively, 40 and 60 inches between centres. Incorporating a number of interesting design and operating systems details, this lathe incorporated some interesting, purely mechanical precision measurement systems. Of conventional arrangement, the heavily-built bed carried V and flat ways, was flame hardened to 75 Hs and finish ground. Built in early and late versions, the latter had their rigidity improved by casting the bed and mounting plinth as one, increasing the bed width to 16.5 inches, deepening and strengthening the already massive "oval" cross bracing and stiffening the mounting points for the foundation bolts. Bed depth was 13.75 inches, the front face being enclosed behind a roller shutter to completely guard the leadscrew. Drive came from a 10 h.p. motor and speed-change gearbox, both rubber mounted on a plate within the headstock-end plinth. The makers reported that the motor was protected by an operator-selected "Star-Delta plugging control system" - presumably a reference to the motor running on either a low or high voltage - where, if the machine was being stopped and started frequently, the risk of overheating was removed by running it on the low-voltage "star" circuit. The drive system gave a wide range of thirteen spindle speeds - with a remarkable ratio span of 1:110, these being: 18, 25, 32, 63, 85, 130, 180, 320, 450, 560, 800, 1400 and 2000 r.p.m. As was usual on lathes of this era and power, an Ammeter was provided to indicate the cutting load in use. Final drive from gearbox to a sub-spindle on the headstock was by five V-belts with the high-speed range, from 560 r.p.m. to 2000 r.p.m., being direct to the spindle by a separate, wide, smooth-running flat belt, so eliminating any interference from gear thrash on fine finishing feeds - while also reducing vibration and noise. Spindle speeds were divided into three groups, a 3-position, gate-type lever on the front face of the headstock - the nearest of three to the operator - being used to set the chosen range: High from 560 to 2000 r.p.m.; Medium from 130 to 450 r.p.m. and Low from 18 to 80 r.p.m. Individual speeds were set by a second spring-loaded, 5-position gate-type lever mounted on the right-hand face of the apron, this being within easy reach of an operator standing in the usual working position - as was the to lever to control electrical start, stop and reverse. Continued below:
|
|
|
|
|
|
|
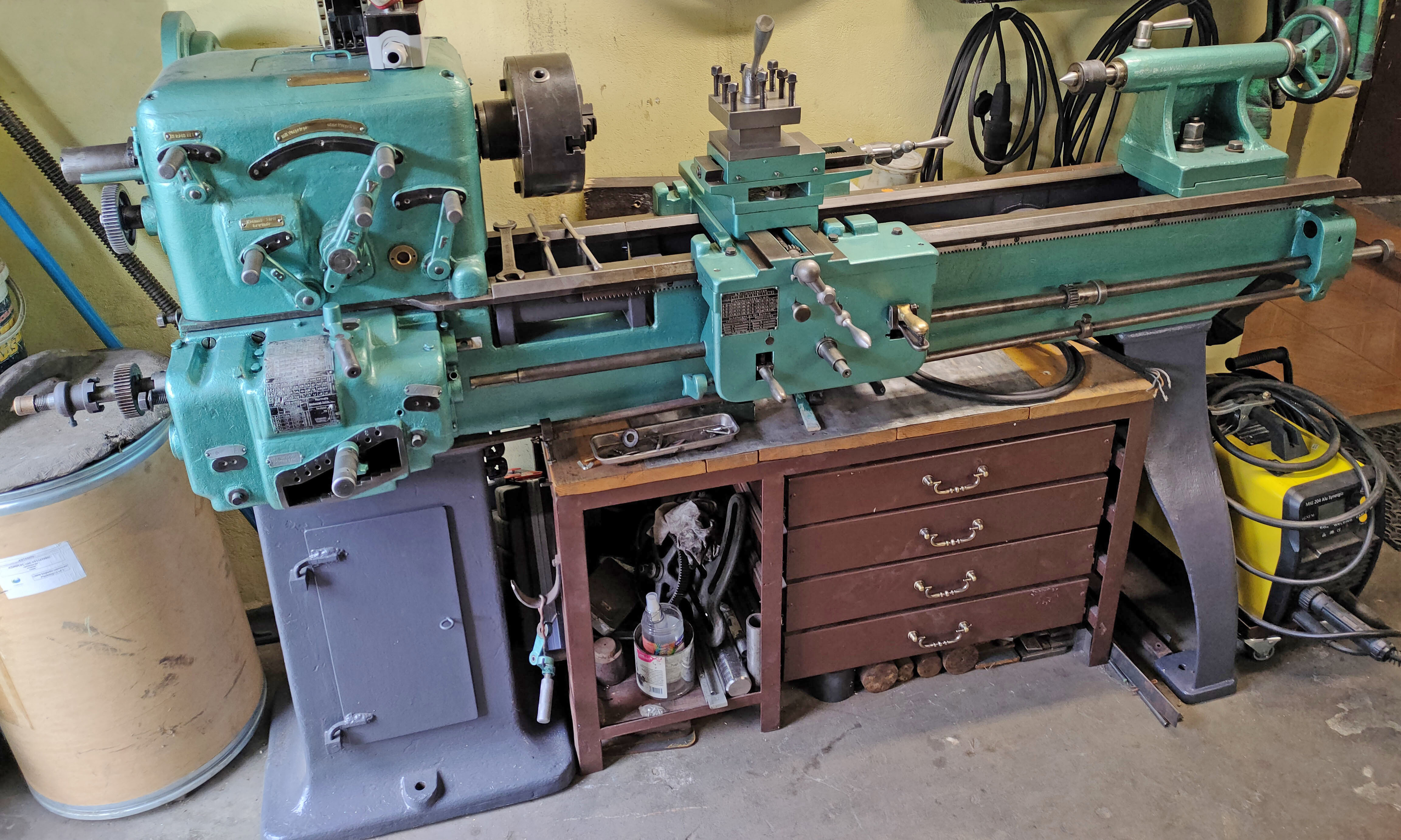 |
|
|
|
|
|
|
|
|
|
|
|
|
|
|
|
Continued: Machined from a forging, hardened and ground, the headstock spindle carried either an A1-6 nose fitting, that allowed a though bore of 2.125", or a D1-6 - in which case the bore was reduced to 1.75". Spindle bearings were a single Timken at the front with an ID of 3.9375", an OD of 6.1875" and a load capacity of 20,700 lbs and at the rear another single Timken with an ID of 3.375", an OD 5.589" and a load capacity 20, 700 lbs. Instead of a leadscrew for threading and a separate powershaft for the power sliding and surfacing feeds, the A-20 was fitted with a single recirculating ball screw that performed both functions. Made from an alloy steel and hardened to above Rc60, the makers claimed to have tested this installation for durability by running successful life tests equal to "several years" of use. Because of its combined nature, a single handle, below and to the left of the cross-feed screw, sufficed to both engage and disengage both pitches and feeds - while a separate lever, to the left of the apron, was used to reverse the feeds. Also fitted was useful 4-step "speed multiplier", this supplying an easily-accessed range of four faster feed rates for rough or semi-finish machining that could be engaged without stopping the headstock spindle. As a safety feature, an adjustable over-load disengagement mechanism was fitted to the drive, this being adjustable by a lever on the apron's left-hand face. Screwcutting pitches (all available without changing the pick-off gears incorporated in the changewheel drive) were suitably sized for the lathe's intended use: English from 1.125 to 60 t.p.i., metric from 0.5 to 32 mm, Module from 0.25 to 8 and Diametral from 0.75 to 56. Selection of pitches was by a juxtaposition of the levers mounted on the left and central bosses on the headstock's front face. Sliding (longitudinal) feed rates were set in groups, each having twenty four changes available between slow and fast: coarse from 0.18" to 0.25" per revolution of the spindle. Normal from 0.0022" to 0.32" and fine from 0.0008" to 0.011" Fitted with enormous, beautifully engraved micrometers dials (that on the cross slide being locked by a neat, thumb-operated operated, non-upsetting, through-feed clamp), the mechanisms of the cross-feed and carriage-traverse handwheels also incorporated cleverly-engineered numerical read-outs for, respectively, workpiece diameter and length travelled. The operator merely had to zero the reading against the face and end of a job for the read-out to subsequently inform him of the dimensions achieved as the work progressed. As part of the standard equipment, the bed was fitted with a micrometer-adjustable, carriage-travel stop. Of the full-length type - and provided with a row of closely-spaced gib-strip adjustment screws, the cross slide carried a top slide that could be swivelled through 360° and available in various forms - with, for example, a T-slot for the American market or various combinations of stud and boss mountings to take either the standard-fit, high-precision-indexing 4-way toolpost or third-party makes of a quick-change type. A very heavy 5-Morse tailstock (4 Morse on early models) was fitted with retractable rollers on its base to ease its travel, a ruler-engraved spindle, a micrometer dial on the large-diameter, internally-ribbed handwheel and a handy tool tray on its top face. It was locked to the bed by both a "light-touch" lever turning an eccentric cross shaft and, to assist with heavier work, supplemented by a through bolt. A two-speed spindle quick-retractor mechanism was incorporated, operated by a lever on the tailstock's front face - this mechanism allowing jobs turned between centres to be loaded and unloaded quickly. Also listed was a 5:1 gear reduction attachment that assisted with the drilling of large holes by hand. Available as optional extras was the usual range of accessories (including items that should really have been included as standard): coolant equipment; 5.5-inch capacity fixed steady; travelling steady; micrometer-equipped carriage stop; carbide-tipped tool-steel No. 5 Morse centres; a heavy-duty, precision rotating centre; 12-inch 4-jaw chuck; a range of 3-jaw chucks; drive plate; 16-inch faceplate; levelling-type foundation bolts; ordinary hydraulic and automatic copying attachments; production turret attachment; tailstock gear-reduction and a rear toolpost. Floor space required by the A-20 was 135" x 55" for the 40-inch between-centres model and 155" x 55" for the long-bed model. Should you have an Ikegai lathe, the writer would be interested to hear from you..
|
|
|
|
|
|
|
|
|
|
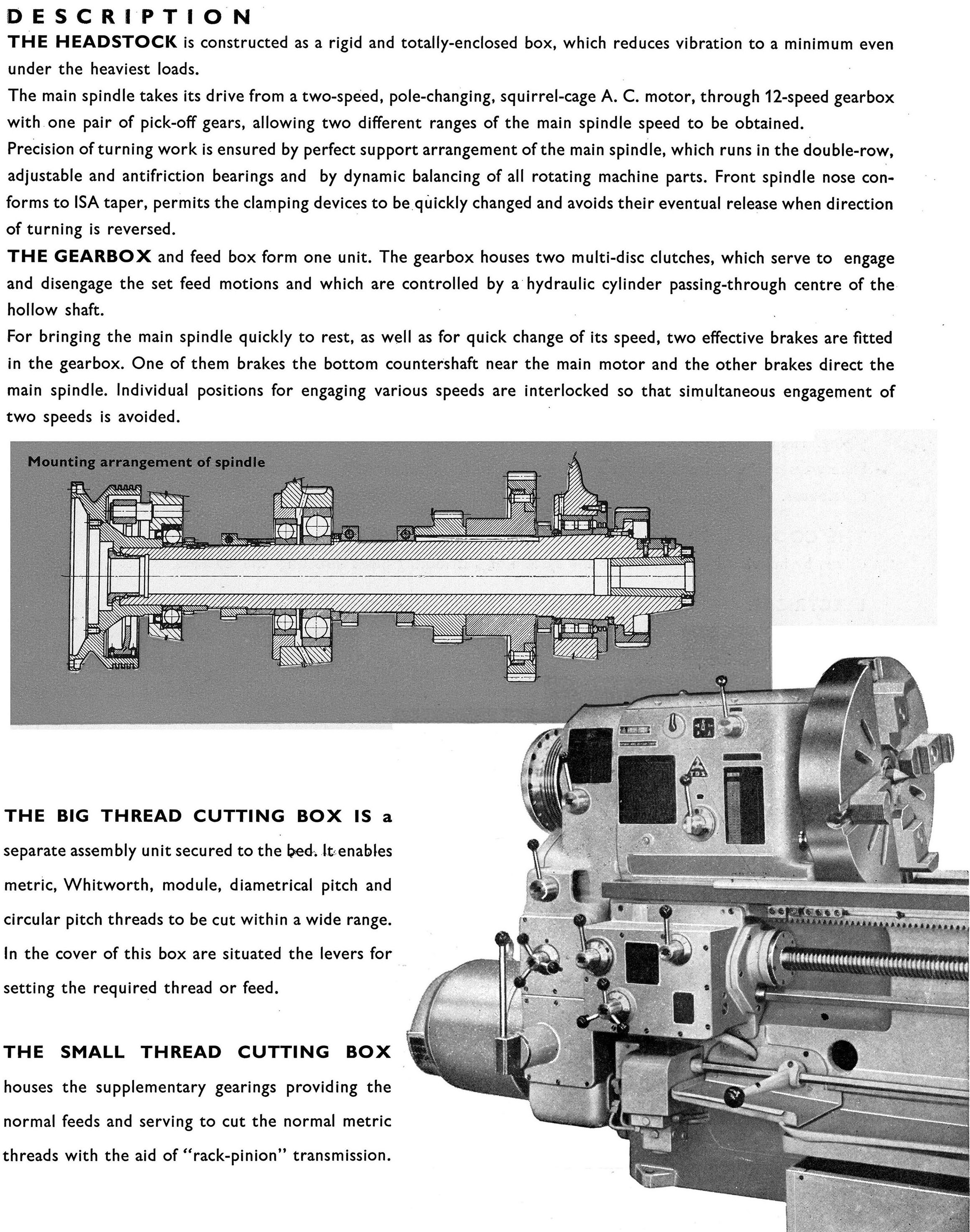 |
|
|
|
|
|
|
Ikegai A-20 Precision Lathe
|
|
|
|
|
|
|
|
 |
|
|
|
|
|
|
…..apart from the dangerous, too-long hair….
|
|
|
|
|
|
|
|
 |
|
|
|
|
|
 |
|
|
|
|
|
|
End cover removed showing the motor drive and screwcutting changewheels.
|
|
|
|
|
|
|
|
 |
|
|
|
|
|
|
|
|
|
|
|
 |
|
|
|
|
|
|
The upper lever was for starting and stopping the spindle, the lower to select the speed in use (the speed range in use - high, medium or slow - being set by a headstock lever)
|
|
|
|
|
|
|
|
 |
|
|
|
|
|
|
Carriage handwheel with its direct-reading, analogue length indicator
|
|
|
|
|
|
|
|
 |
|
|
|
|
|
|
The careful positioning of the main function controls, their graduations and markings is evident in the plan picture of the carriage
|
|
|
|
|
|
|
|
|
|
|
|
|
|
 |
|
|
|
|
|
|
"F4" - the 4-speed multiplier control that gave four feed ranges for "rough" or "semi-finishing" feeds
|
|
|
|
|
|
|
|
 |
|
|
|
|
|
Headstock levers: the two mounted on the left-most boss together with the one in the centre provided - by a juxtaposition of their settings - change of screwcutting pitch and feed. The right-hand lever set the high, medium and low spindle speed ranges - changes within each range being made by an apron-mounted control.
|
|
|
|
|
|
|
|
 |
|
|
|
|
|
|
Top slide with T-slot--as specified for the American market
|
|
|
|
|
|
|
|
 |
|
 |
|
|
|
|
|
|
Large-diameter cross-feed micrometer dial locked by a non-upsetting, through-feed clamp.
|
|
|
|
|
|
|
|
An automatic adjustable-thrust disengage was fitted to the sliding feed
|
|
|
|
|
|
|
|
|
|
|
 |
|
|
|
|
 |
|
|
|
|
|
|
|
Massive cross ribs between the bed walls
|
|
|
|
|
|
|
Standard equipment: micrometer-adjustable, carriage-travel stop
|
|
|
|
|
|
|
|
|
|
|
|
|
|
|
|
|
|
 |
|
|
|
|
 |
|
|
|
|
|
|
|
|
|
Top face of the tailstock formed as a handy tool tray/ The "gate change" lever operated the 2-speed spindle retractor mechanism
|
|
|
|
|
|
|
|
Tailstock to bed locking lever
|
|
|
|
|
|
|
|
|
|
|
 |
|
|
|
|
|
 |
|
|
|
|
|
|
|
|
|
|
|
|
|
|
|
|
|
|
|
 |
|
|
|
|
|
|
Hydraulic copy attachment
|
|
|
|
|
|
|
|
 |
|
|
|
|
|
|
Capstan turret attachment
|
|
|
|
|
|
|
|
|
|
|
|
|
|
|
|