 |
 |
 |
 |
 |
 |
 |
 |
 |
 |
 |
 |
 |
 |
 |
 |
 |
 |
 |
 |
 |
 |
 |
 |
 |
 |
 |
 |
 |
 |
 |
 |
 |
 |
 |
 |
 |
 |
 |
 |
 |
 |
 |
 |
 |
|
|
|
|
|
|
|
|
|
|
|
|
|
|
|
|
|
|
|
|
|
|
|
|
|
|
|
|
|
|
|
|
|
|
|
|
|
|
|
|
|
|
|
|
|
|
|
|
|
|
|
|
|
|
|
|
email: tony@lathes.co.uk Home Machine Tool Archive Machine-tools Sale & Wanted Machine Tool Manuals Catalogues Belts Books Accessories
lathes.co.uk Hurth V10a Precision Toolroom Boring & Milling Machine
Hurth V10a Continued Page 2 Hurth WF10 Gear Hobber
Literature for Hurth Machines Tools can be found here
Manufactured by Carl Hurth at the Company's Machine-Tool and Gear Woks in Munich, Germany, the , the 2-ton (1.950 kg) V10a was designed as a machine for both toolroom use in the manufacture of jibs, fixtures, one-off parts and short production runs. Its accuracy was claimed to be that of a jig borer, while for milling its table could be moved under power longitudinally and vertically and also tilted, by a worm-and-wheel gearing, front to back 15° each side of horizontal. The head was fixed in place vertically but could be moved from side to side and, in addition to the usual hand feed, was also provided with separate sets of fine and coarse downfeed under power. Just one table size was offered, 11.75" x 39.25" (300 mm x 1000 mm) with (reflecting its specialised nature) rather short travels: longitudinally by both hand and power of 15.75" (400 mm), in traverse by hand only of 9.5" (240 mm) and vertically by both hand and power of 14" (360 mm). Three T-slots were fitted, each 0.623" (16 mm) wide. Able to be adjusted to eliminate backlash, the table feed screws were fitted with very large diameter, satin-chrome plated and finely engraved micrometer dials. When equipped with the optional dial indictors (that read to an accuracy of 0.0005"/0.01 mm) their associated brackets to mount gauge blocks and a vernier-equipped, high precision rulers - very high levels of setting precision could be achieved. As offered on many other contemporary machines, an optical positioning system was also listed by the makers for later models. Provided at extra cost was a rather unusual (possibly unique) design of indexing rotary table 19.75" (500 mm) in diameter and listed as the Model ST500. Fitted with five T-slots, the table was machined with a circular slot close to the outside edge of the top surface, this leaving a separate annulus into which the T-slots continued. Indexing, by a plunger, was at 15°° intervals. As a very high-accuracy machine, the spindle of the V10a was of a special type, claimed by the makers to be the result of many years of experience in research, design and application of such assemblies. Mounted in a heavy, season casting, the spindle was of unusual length and ran in several high-class ball and roller bearings from which only hand-selected examples were used. Drive from the spindle-speed gearbox was by a smooth-running, flat belt tensioned by a jockey pulley with thirteen speeds provided in direct drive of 45, 63, 90, 125, 180, 250, 355, 500, 710, 1000, 1400, 2000 and 2800 r.p.m. As flat belts perform badly at low speeds - unless considerable and undesirable tension is applied - the belt pulley held a compact 4 : 1 ratio epicyclic reduction gearbox, this giving six low speeds and allowing large diameter cutters to be used for heavy rates of metal removal. As usual, on many machine tools of this class including lathes, the spindle was relieved of belt-pull loads by running in its own set of bearings, the drive being transmitted from pulley to spindle by a key or peg. Spindle vertical travel by hand up and down, or under power downwards only, was 3.9375" (100 mm). As the machine was also designed for jig boring, for each spindle speed the operator could select from nine slow rates of boring feed. For example, with the slowest speed of 45 r.p.m. selected, boring feeds rates per revolution of the spindle could be set from 0.005" (0.12 mm) to 0.080" (1.95 mm) and at the highest speed of 2,800 r.p.m. from 0.00008" (0.002 mm) to 0.0012" (0.031 mm). In addition to the boring feeds, a separate set of ten faster downfeeds was provided by a crank mechanism, these ranging from 0.22" (5.6 mm) to 3.54" per minute. Continued below:
|
|
|
|
|
|
|
|
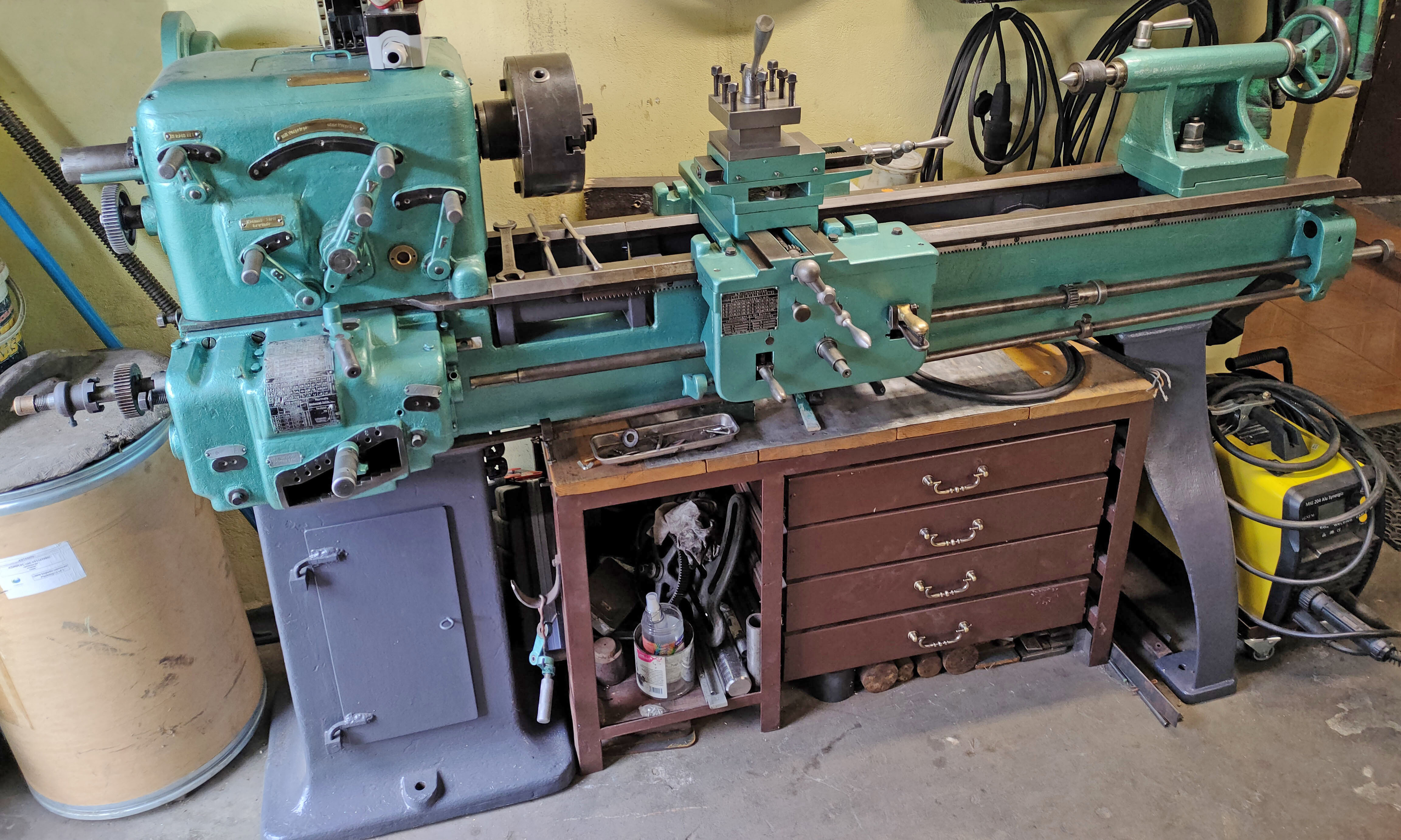 |
|
|
|
|
|
|
|
|
|
|
|
|
Continued: Mounted to the left-hand side of the head was a crank mechanism that gave nine rates of side-to side-feed over a distance of 5.9" (150 mm) - these traverses being set at rates of 2, 2.8, 4, 5.6, 8, 11.2, 16, 22.4 and 31.5 inches per minute and adjustable to an accuracy of 0.1mm. With combined with power downfeed, this mechanism enabled "gradual-infeed" milling to be accomplished and sloping ramps and other surfaces machined. The drive for the head's side-to-side travel was by a system used on several other Hurst machines (including the Type L.F.V.I. automatic keyseating machine) and described by the makers as, "The well-known and proven Hurst crank mechanism, which guarantees an absolutely smooth and precise reversal." When used for milling and similar operations that required the spindle to be locked, a special non-upsetting clamp was provided that removed any lateral forces on the quill (the element in which the spindle rotated) and so prevented wear on the quill's finely honed guide hole in the head casting. As standard, the spindle end was fitted with a No.40 National Standard taper, though a No.30 was optional and others could be provided to special order. Also part of the regular equipment was a hand-operated, quick-change chuck by Stieber, this allowing boring heads, face mills and other fittings to be changed without recourse to a self-hiding spanner. The maximum distance from the spindle nose to the table was 19.75" (500 mm) and the throat around 10.2" (260 mm). Power came from three 3-phase motors: one of 4 h.p. running at 1400 r.p.m. driving the table; another of 3 h.p. for the head cross-feed and spindle and finally one of 8 h.p. (controlled by a convenient push-button) to lift and lower the very heavy knee and its mounted jobs. Supplied a part of the standard equipment was a complete electrical and coolant installation; a socket from which to run a lamp; the Stieber quick-action spindle chuck; dial indicator for worktable zero adjustment (only in the horizontal plane); a set of spanners and an instruction book. Accessories at extra cost included a 12.375" (315 mm) diameter rotary table, Model RV315, with indexing plates and with a connection that enabled it to be driven from the table's power-feed; the previously mentioned indexing rotary table; a set of collets ¼" to 1" (6 to 26 mm) to holder cotters, etc; a micrometer adjustable boring head, Model AK2, for boring holes up to 4.3" (110 mm) and a universal dial-test indicator designed to fit the AK2; a face milling cutter 110 mm in diameter for machining cast iron with inserted carbide-tipped blades; dial indicators with mounting brackets to carry gauge blocks when working by co-ordinates; a swivel-base machine vice, Model LSt2, with a jaw capacity of 3.9" (100 mm); a self-centring vice, Model LZ3, for holding round work; centre sleeve adaptors Morse 1 to 3 to fir the Stieber chuck; a precision-class drill chuck with a capacity of 25/64th" (10 mm); ; special keyway and slot-milling cutters for use with the downfeed milling feature; an end-mill gauge, Model FPL, for checking cutting edges on the keyway and slot-milling cutters; a set of end mills for jig boring work, Model STS, with Morse taper shanks 5/16 th to 19/16 " (4 to 40 mm) and a machine lamp with a universally-joined arm. The Hurth V10a required a space of 71" x 53" (1800 mm x 1350 mm) and weighed, crated for delivery, 4800 lbs (2200 kg)..
|
|
|
|
|
|
|
|
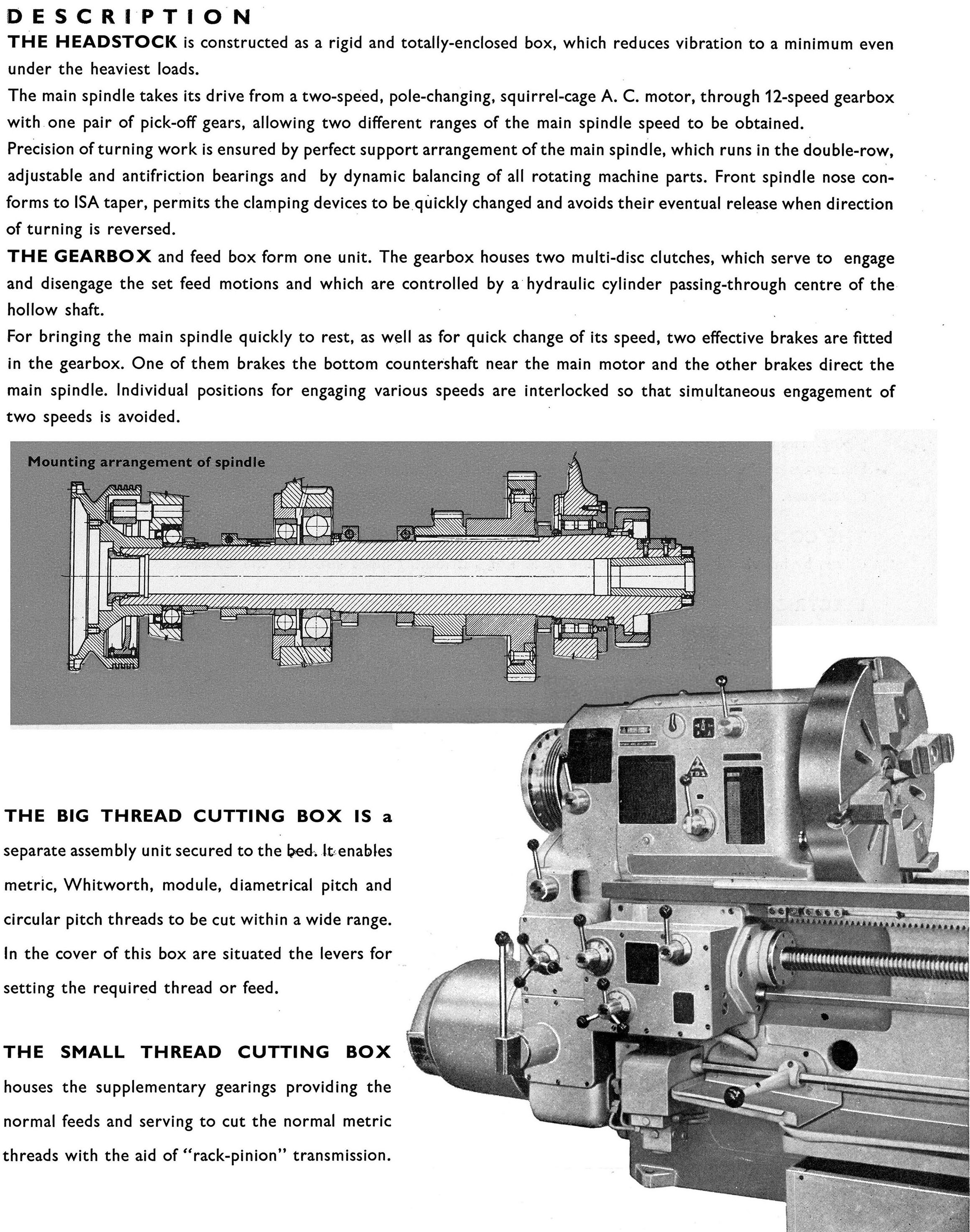 |
|
|
|
|
|
|
Hurth V10a with the table tilted forward to its maximum inclination of 15°
|
|
|
|
|
|
|
|
 |
|
|
|
|
|
 |
|
|
|
|
|
|
|
|
|
Provided at extra cost was a rather unusual (possibly unique) design of indexing rotary table 19.75" (500 mm) in diameter listed as the Model ST500. Fitted with five T-slots, the table was machined with a circular slot close to the edge of the top surface, this leaving a separate annulus into which the T-slots continued. Indexing, by a plunger, was at 15°° intervals.
|
|
|
|
|
|
|
|
|
|
|
|
|
|
|
|
 |
|
|
|
|
 |
|
|
|
|
|
|
Just table size was offered, 11.75" x 39.25" (300 mm x 1000 mm) with (reflecting its specialised nature) rather short travels: longitudinally by both hand and power of 15.75" (400 mm), in traverse by hand only of 9.5" (240 mm) and vertically by both hand and power of 14" (360 mm). Three T-slots were fitted, each 0.623" (16 mm) wide. Able to be adjusted to eliminate backlash, the table feed screws were fitted with very large diameter, satin-chrome plated and finely engraved micrometer dials. When equipped with the optional dial indictors (that read to an accuracy of 0.0005"/0.01 mm) their associated brackets to mount gauge blocks and a vernier-equipped, high precision rulers - very high levels of setting precision could be achieved. As offered on many other contemporary machines, an optical positioning system was also listed by the makers for later models.
|
|
|
|
|
|
|
|
 |
|
|
|
|
|
|
Section through the vertical head
|
|
|
|
|
|
|
|
 |
|
|
|
|
|
|
Sectional view of the head's side-to-side drive gearbox, this being was by what the makers claimed to be "The well-known and proven Hurst crank mechanism, which guarantees an absolutely smooth and precise reversal."
|
|
|
|
|
|
|
|
 |
|
|
|
|
|
|
Crank-arm assembly showing the feed -rate adjustment system, this working to an accuracy of 0.1mm
|
|
|
|
|
|
|
|
|
|
|
|
|
|
 |
|
|
|
|
|
|
Table-drive gearbox showing the "Wendegetrieb" - the reversing gear and the wheel for control by hand
|
|
|
|
|
|
|
|
 |
|
|
|
|
|
|
Another vew of the table-drive gearbox showing the "Anschlub fur Rundtischantrieb" - the connection to drive a rotary table
|
|
|
|
|
|
|
|
 |
|
|
|
|
|
|
Section through the table's feed screws showing the backlash adjustment nuts
|
|
|
|
|
|
|
|
 |
|
|
|
|
|
|
Section through the knee's lift-and-lower mechanism
|
|
|
|
|
|
|
|
 |
|
|
|
|
|
|
|
|
|
Table inclination driven by worm-and-wheel gearing
|
|
|
|
|
|
|
|
|
|
|
|
|
|
|
|
 |
|
|
|
|
|
|
|
|
The Stieber quick-action chuck
|
|
|
|
|
|
|
|
|
|
|
|
|
|
|
|
Type SP collets for the Stieber chuck
|
|
|
|
|
|
|
|
|
|
|
|
|
|
|
|
Type MH adapter sleeves Morse taper 1,2 and 3 for the Stieber chuck
|
|
|
|
|
|
|
|
|
|
|
|
|
|
|
|
Special keyway and slot-milling cutters for use with the "gradual- infeed" method that combined spindle power downfeed and the head's side-to-side travel
|
|
|
|
|
|
|
|
|
|
|
|
|
 |
|
|
|
|
|
|
|
|
Type AK2 Boring bar holder
|
|
|
|
|
|
|
|
|
|
|
|
|
|
|
|
The maker's "Universal" dial indicator intended to be used with the boring bar holder Type AK2
|
|
|
|
|
|
|
|
|
|
|
|
|
|
|
|
Type STS end mills for jig-boring work in sizes 8 to 40 mm
|
|
|
|
|
|
|
|
|
|
|
|
|
|
|
|
Type BF10 precision drill chuck with a capacity of 10 mm
|
|
|
|
|
|
|
|
|
|
|
|
|
 |
|
|
|
|
|
|
Roughing out a die cavity using the "gradual infeed" method
|
|
|
|
|
|
|
|
|
|
|
|
|
|
 |
|
|
|
|
|
|
Finishing the die using the table's power longitudinal feed
|
|
|
|
|
|
|
|
|
|