 |
 |
 |
 |
 |
 |
 |
 |
 |
 |
 |
 |
 |
 |
 |
 |
 |
 |
 |
 |
 |
 |
 |
 |
 |
 |
 |
 |
 |
 |
 |
 |
 |
 |
 |
 |
 |
 |
 |
 |
 |
 |
 |
 |
 |
 |
 |
 |
 |
 |
 |
 |
 |
 |
 |
 |
|
|
|
|
|
|
|
|
email: tony@lathes.co.uk Home Machine Tool Archive Machine-tools Sale & Wanted Machine Tool Manuals Catalogues Belts Books Accessories
EXE 2.5" Lathe
EXE 2.5" Lathe Continued Here
EXE Home Page EXE Miniature Surface Grinder
EXE Exlet Lathe A Fine & Original EXE
Main EXE Page Continued Here EXE Photographic Essay
|
|
|
|
|
|
|
|
|
|
|
|
|
|
|
|
|
|
|
|
|
|
|
|
|
|
|
|
|
|
|
|
|
|
|
|
|
|
|
|
|
|
|
|
|
|
|
|
|
|
|
|
|
|
|
|
|
|
|
|
With only an archdeacon and a professional engineer as owners, the early, black-painted EXE 2.5" shown below has survived in excellent, original condition. The dividing plate fitted to the front face of the headstock pulley is not original (as standard a single ring of 60 holes was provided) - but, astonishingly, the bronze set screws let into the tailstock casting that bear against the bed to align the unit are. This was the Company's first lathe and introduced to the public at the 1923 National Model Engineering Exhibition in London. Available in both short and long-bed versions it was to stay in continuous production until 1939. Although a small lathe, the EXE 2.5 is a very useable and effective lathe and owners appear to enjoy owning and using them. Typically, one finds that a 1923 example was bought from a Melbourne (Australia) and used for over 30 years. It was in beautiful condition, with little wear, in its original green paintwork - and remains as such today. It came equipped with a good range of accessories and is driven most usefully from a 1/3 h.p. variable speed DC motor. This particular example is unusual and clearly very early; the nameplate is 'Exeter' rather than 'Exe', it has no serial numbers or manufacturer's information on the headstock or on the rectangular 'steady bar' below the lead screw - or the Exeter mark on the cross slide either. It can be seen at the bottom of the page..
|
|
|
|
|
|
|
|
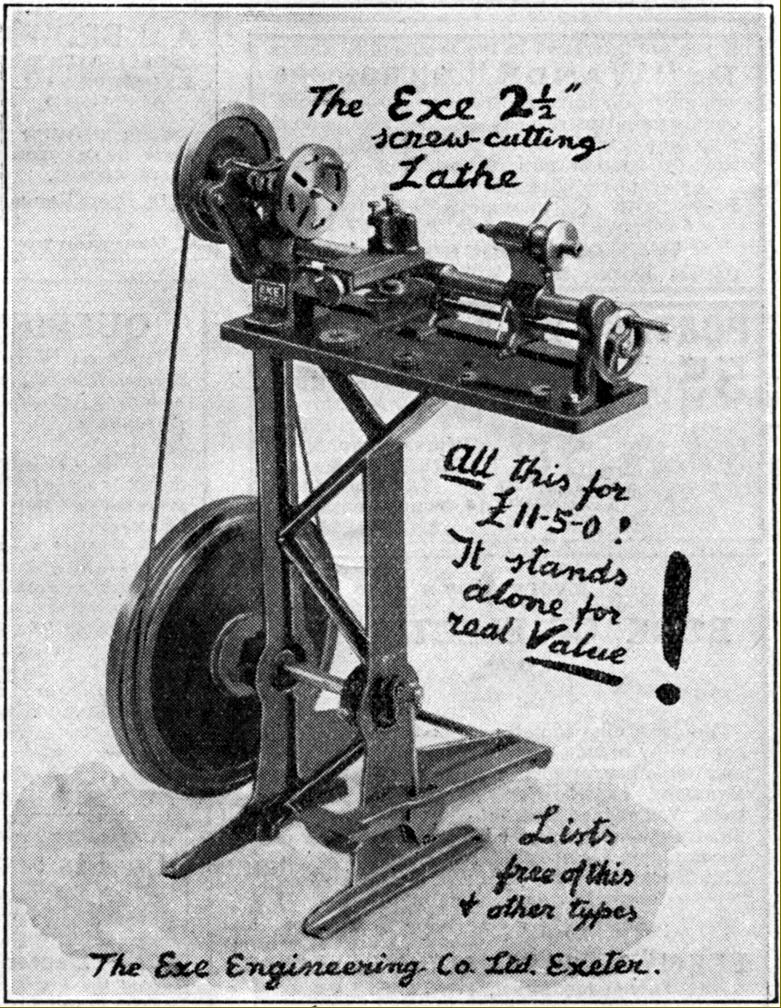 |
|
|
|
|
|
|
1927 advertisement for the Exe 2.5-inch lathe. A photograph of an identical lathe on its stand here
|
|
|
|
|
|
|
|
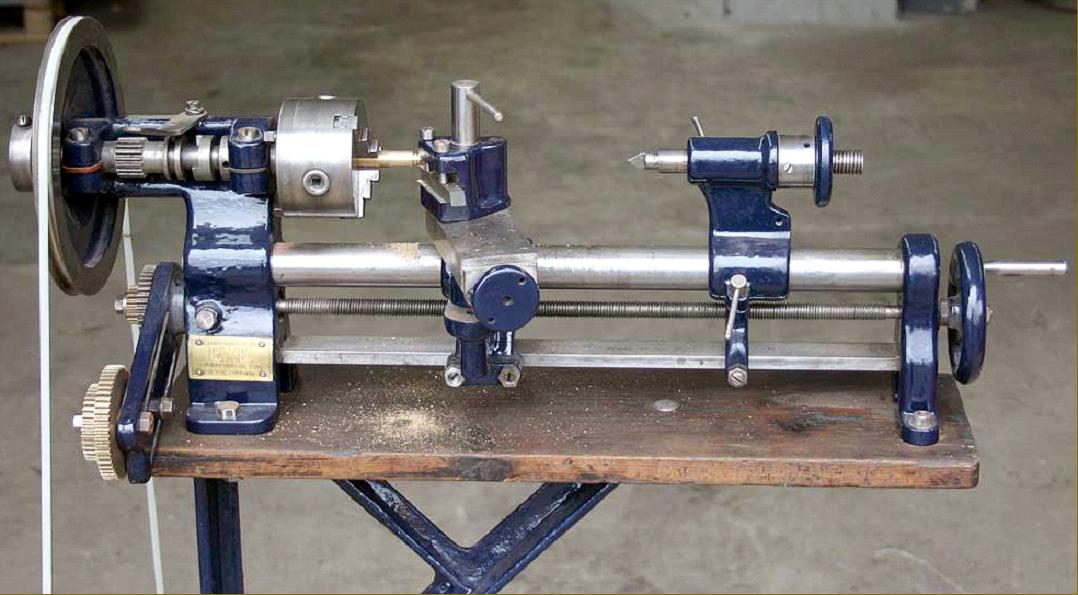 |
|
|
|
|
|
|
|
|
|
|
|
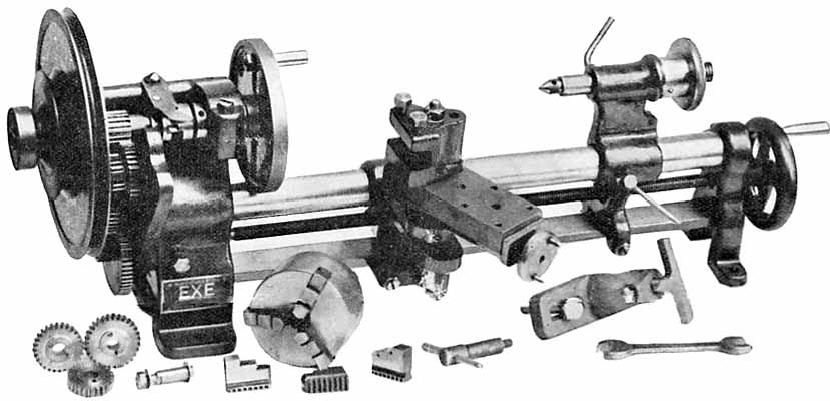 |
|
|
|
|
|
|
The 2.5" EXE lathe shown here in its 1926 form. Besides a 3-jaw chuck, faceplate, centres and changewheels a wood-turning test was also included as part of the standard equipment.
|
|
|
|
|
|
|
|
|
|
|
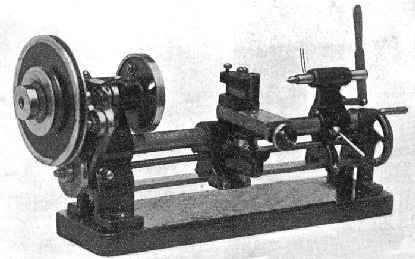 |
|
|
|
|
|
A 1/4 scale model 2.5" EXE lathe just 6" long and built by the makers from parts machined on the prototype of its full-sized brother.
|
|
|
|
|
|
|
|
|
|
|
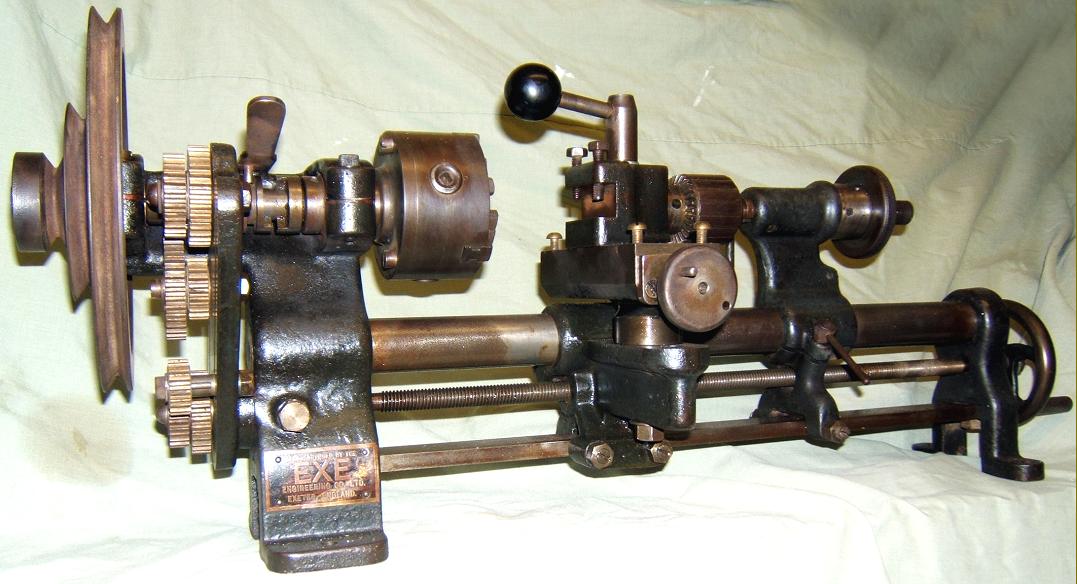 |
|
|
|
|
|
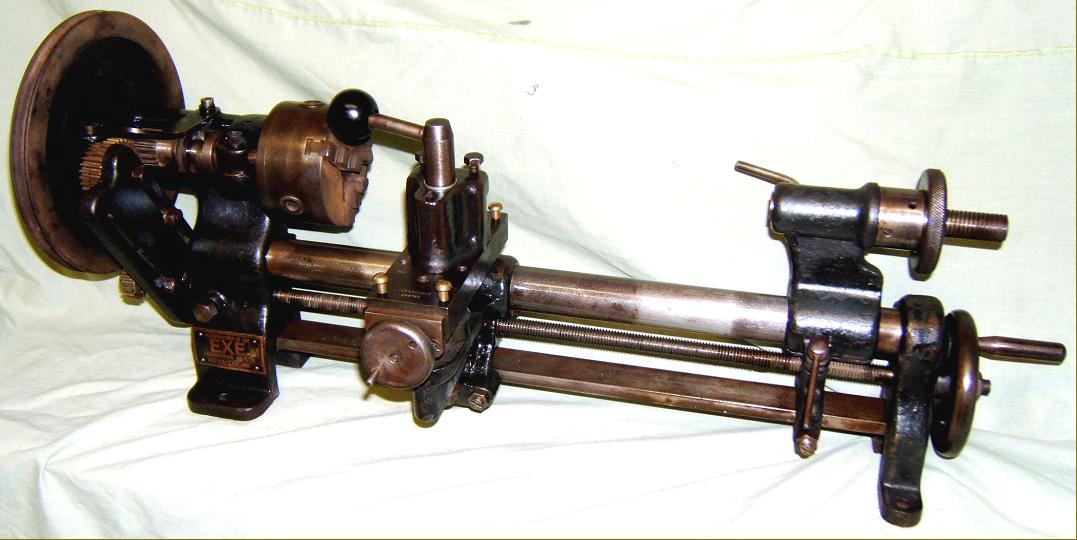 |
|
|
|
|
|
|
|
|
|
|
|
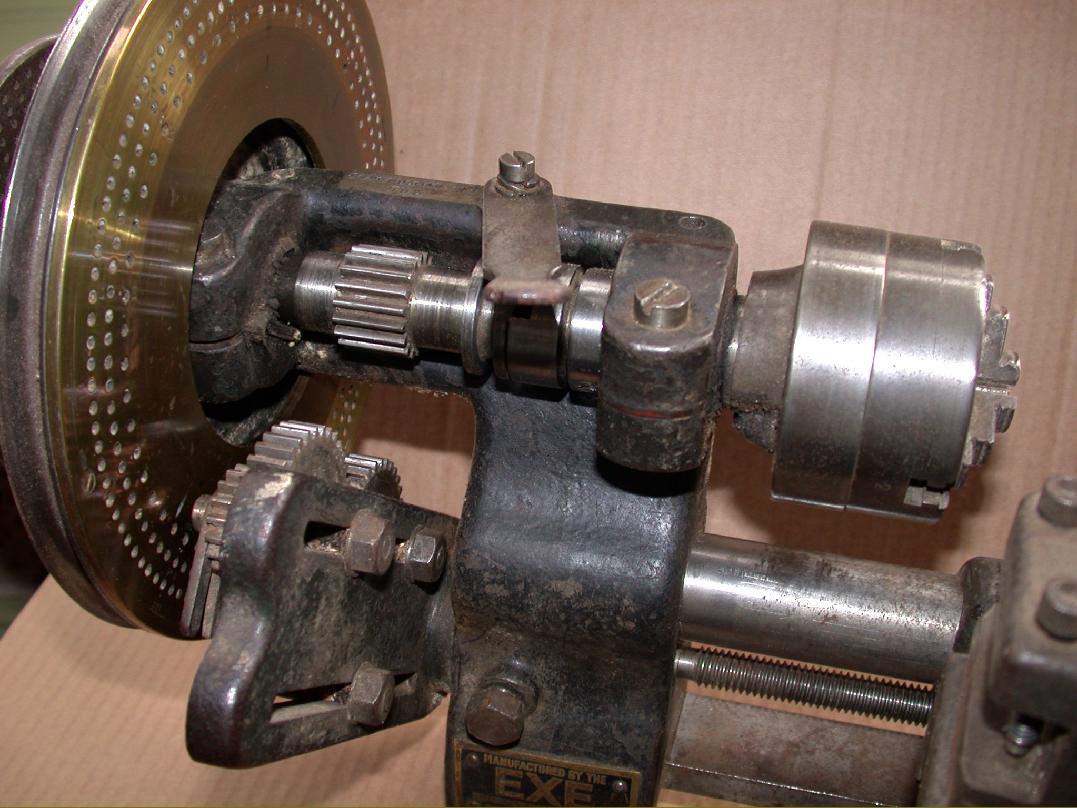 |
|
|
|
|
|
|
The headstock design, with adjustable bronze bearings was of unusual construction being "open" at the front with the back wall of the headstock rising up level with the top of the bearings. Fitted to the exposed spindle was a unique "screw-cutting dog clutch" that, the makers claimed, allowed "even those without previous experience (to) cut any thread easily and quickly" - if only the generation of good-quality threads were so simple. However, in the sense that it was impossible to "pick up" a thread at the wrong point and spoil a job, the device did work efficiently - and was well received in articles written at the time by experts.
|
|
|
|
|
|
|
|
|
|
|
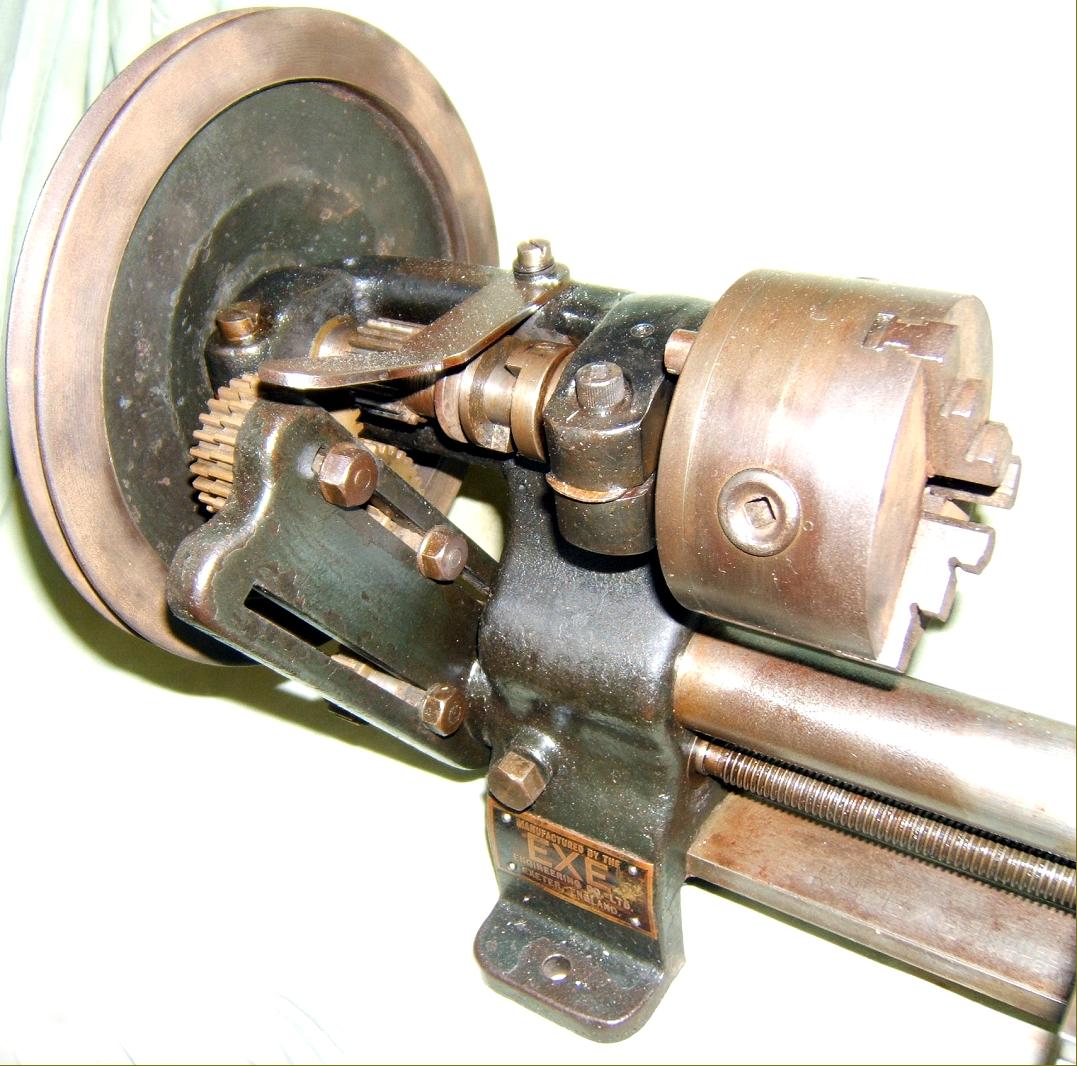 |
|
|
|
|
|
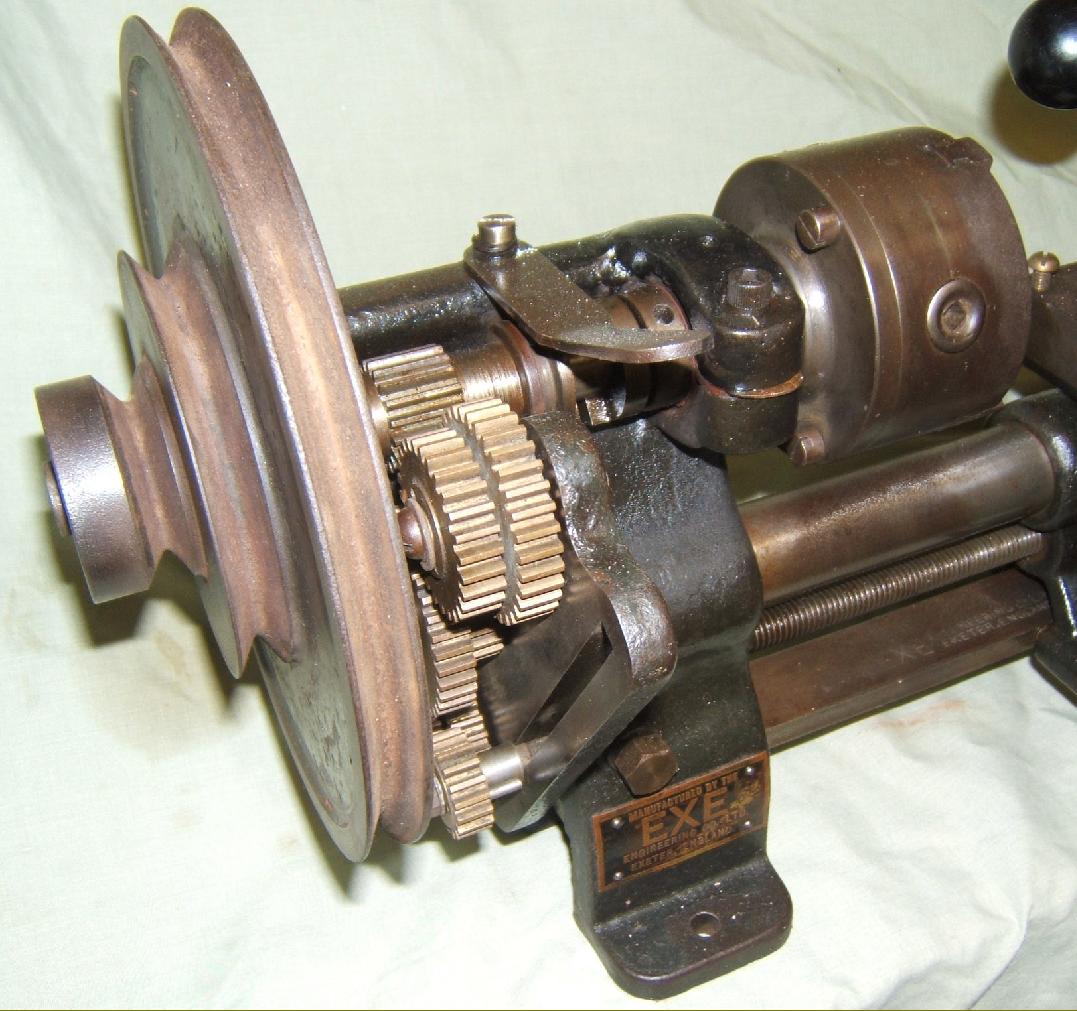 |
|
|
|
|
|
|
Extravagant but pleasing engineering--changewheels in bronze
|
|
|
|
|
|
|
|
|
|
|
|
|
|
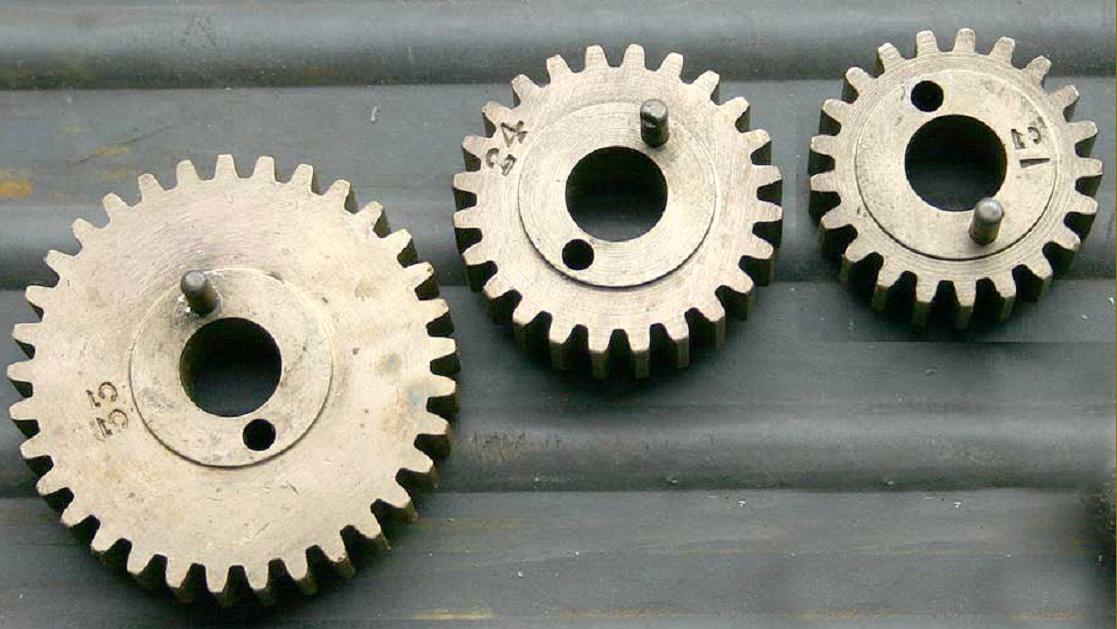 |
|
|
|
|
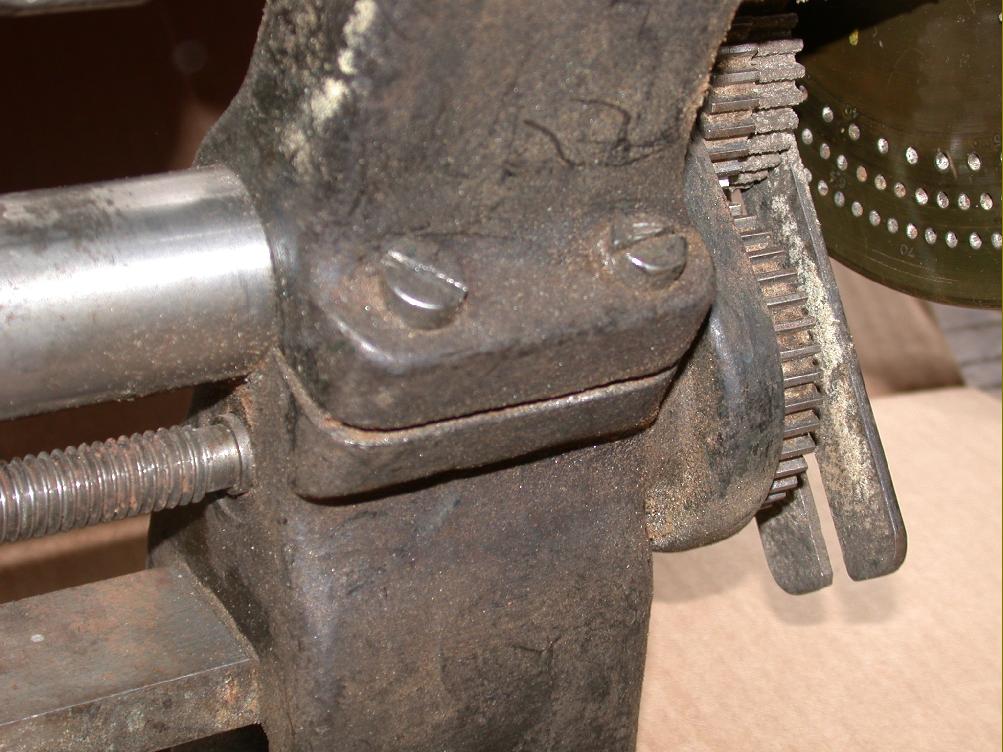 |
|
|
|
|
|
|
The rear wall of the headstock casting was built up level to top of the spindle bearings. The headstock and left-hand foot were cast as one, precision bored and slit along the rear side with two screws to close the casting up and tighten it to the lathe bed.
|
|
|
|
|
|
|
|
|
|
|
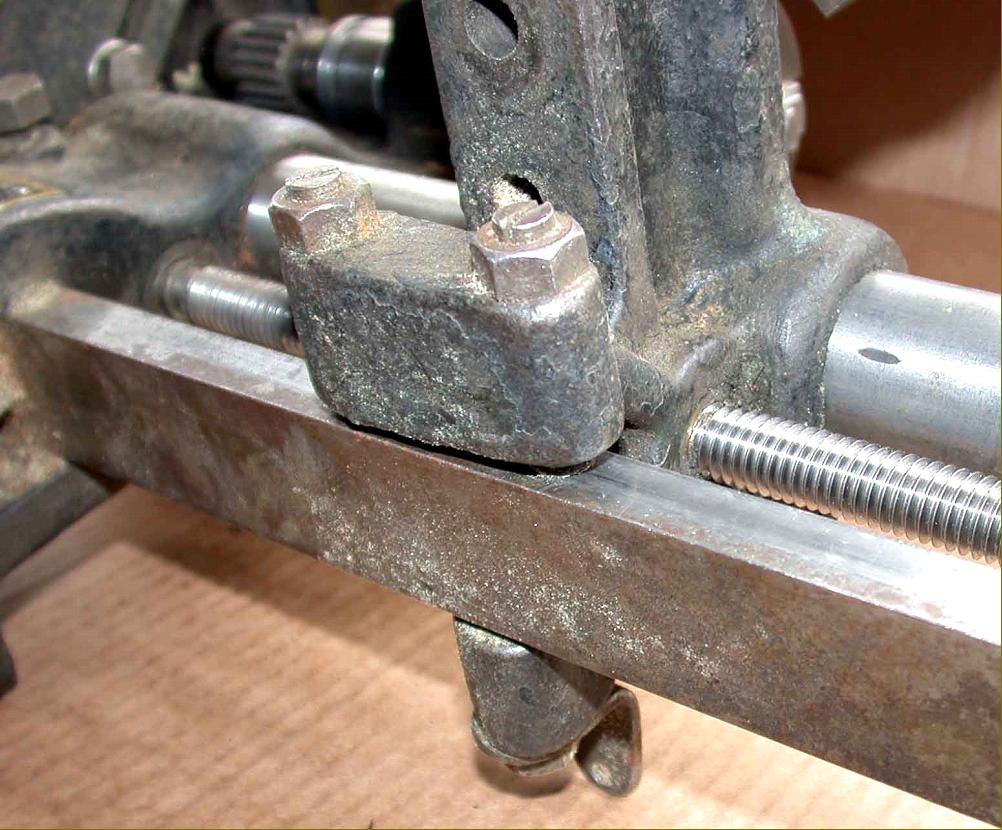 |
|
|
|
|
|
|
Another view of the carriage-to-lower bar fitting
|
|
|
|
|
|
|
|
|
|
|
|
|
|
|
|
|
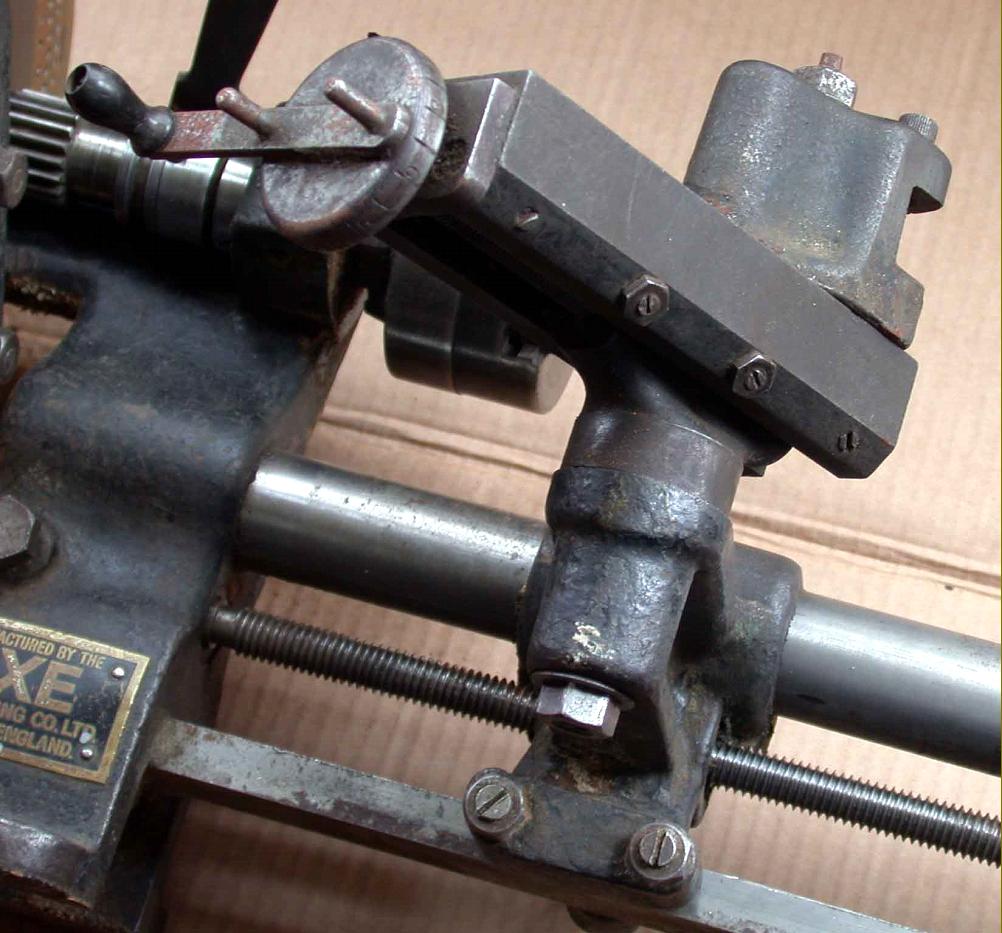 |
|
|
|
|
|
|
EXE fitted a separate flat bar, placed horizontally below the round bar, to provide a "lever point" against which the twisting forces from the tool could be absorbed - and also to reduce the effects of wear on the main bed. In order to align the carriage and tailstock they were fitted with an adjustable gib strip at each side of the flat bar, so allowing both a small amount of lateral adjustment and a way of obtaining a good sliding fit.
|
|
|
|
|
|
|
|
|
|
|
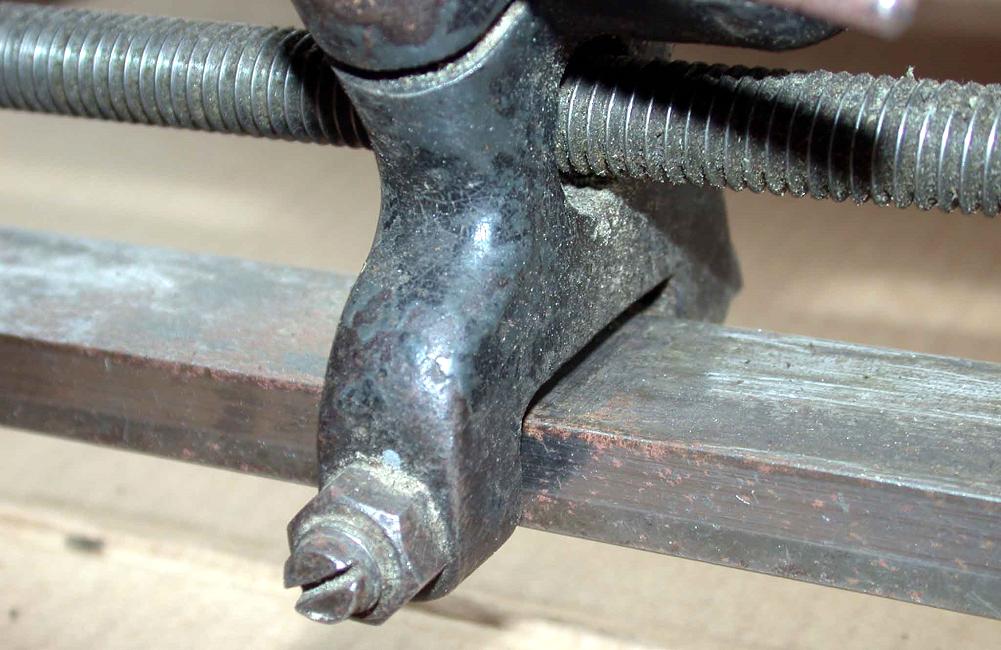 |
|
|
|
|
|
|
|
|
|
Adjustable fitting of the tailstock to the lower bed bar
|
|
|
|
|
|
|
|
|
|
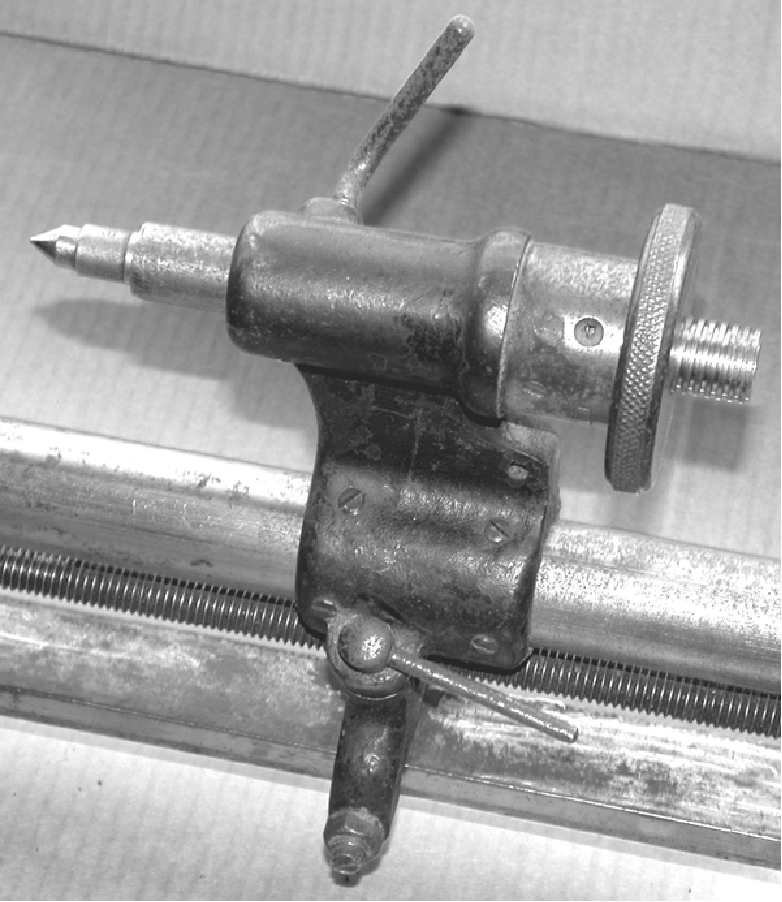 |
|
|
|
|
|
|
The tailstock barrel was given the usual No. 1 Morse taper, and could be ordered with either a square-thread screw-feed or lever-action barrel with the operating arm arranged to point vertically upwards. Note the slotted set screws (in bronze) screwed into the casting to achieve final alignment with the headstock; this was a method adopted by the makers from the start of production in 1923.
|
|
|
|
|
|
|
|
|
|
|
|
|
|
|
|
|
 |
|
|
|
|
|
|
|
|
At the 1924 Model Engineering Exhibition the EXE 2.5" lathe was shown fitted to the company's "patented, self-contained friction motor drive" - the patent number for the unit being GB 165/24.. There were two types of drive arrangement: the first consisted of a pivoting plate to which was fitted a large-frame, 0.25 hp motor together with a bracket bolted to its end that held a ball-bearing spindle. The spindle carried a fibre gear at one end that was driven, at a reduction ratio of 1 : 3, by a steel gear on the motor; at the other end of the spindle was a "friction disc" made from compressed sections of leather and arranged so that when the frame was pivoted by a foot-operated pedal it came into contact with the inside rim of the (normally foot-operated) flywheel and drove it by friction; when the foot pedal was released, a brake automatically stopped the lathe. The second form of drive did away with the platform (carrying the motor and gearing) and instead a bracket carrying a countershaft was mounted on the rod normally used as a fulcrum for the treadle drive. The same type of ball-bearing spindle was used with a friction disc at one end, but in this case a pulley, rather than a gear, at the other. An additional fitting is shown in the illustration, an overhead drive unit that not only provided power to a milling or grinding head held in the toolpost but also to a drill press carried on a vertical bar socketed into lugs on the back of the stand. Also at the 1924 Exhibition, and built by the EXE and displayed on its stand, was a beautifully detailed 1/4 scale working model of the 2.5-inch lathe. Even the leadscrew, so reduced in size that it required a 48 t.p.i thread, was true to the original, as was the spindle thread. Very unusually (and probably uniquely) the exhibit was a model of a lathe-maker's lathe built in-house on a prototype of the machine it represented.
|
|
|
|
|
|
|
|
|
|
|
|
|
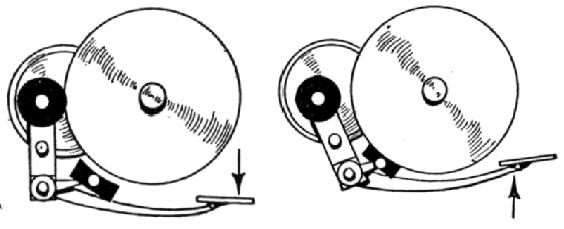 |
|
|
|
|
|
|
Depressing the foot pedal engaged the drive.
|
|
|
|
|
|
|
|
|
|
|
Releasing the foot pedal automatically engaged a spring-assisted brake.
|
|
|
|
|
|
|
|
|
|
|
|
|
|
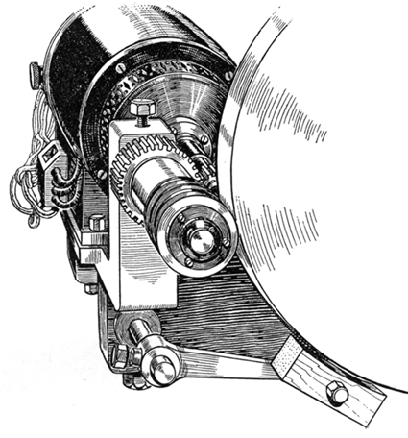 |
|
|
|
|
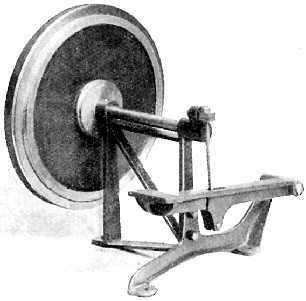 |
|
|
|
|
|
|
|
|
Designed to supply power to a bench mounted machine the "Foot-motor" was a self-contained unit
|
|
|
|
|
|
|
|
|
|
|
|
The motor and its bolted-on bracket carried a speed-reducing gear and friction disc. The assembly was so arranged that moving a foot pedal engaged the drive whilst releasing it caused a spring to automatically brake the heavy flywheel to a stop.
|
|
|
|
|
|
|
|
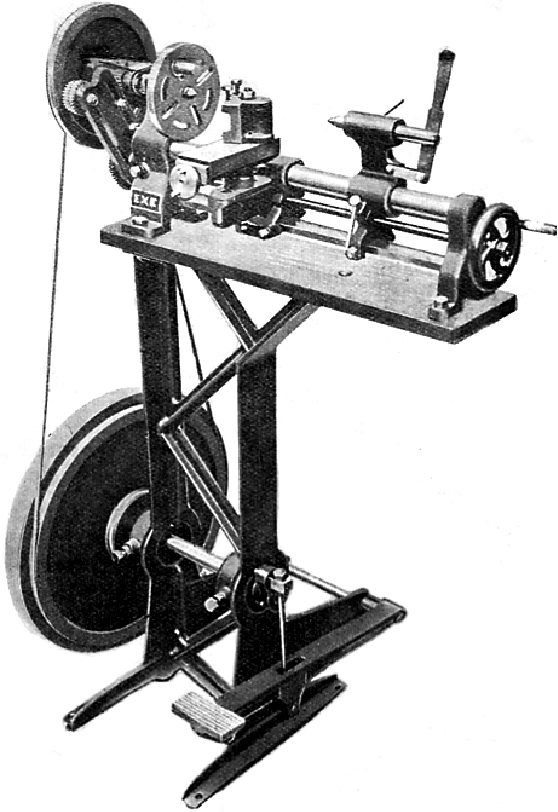 |
|
|
|
|
|
|
|
|
|
|
|
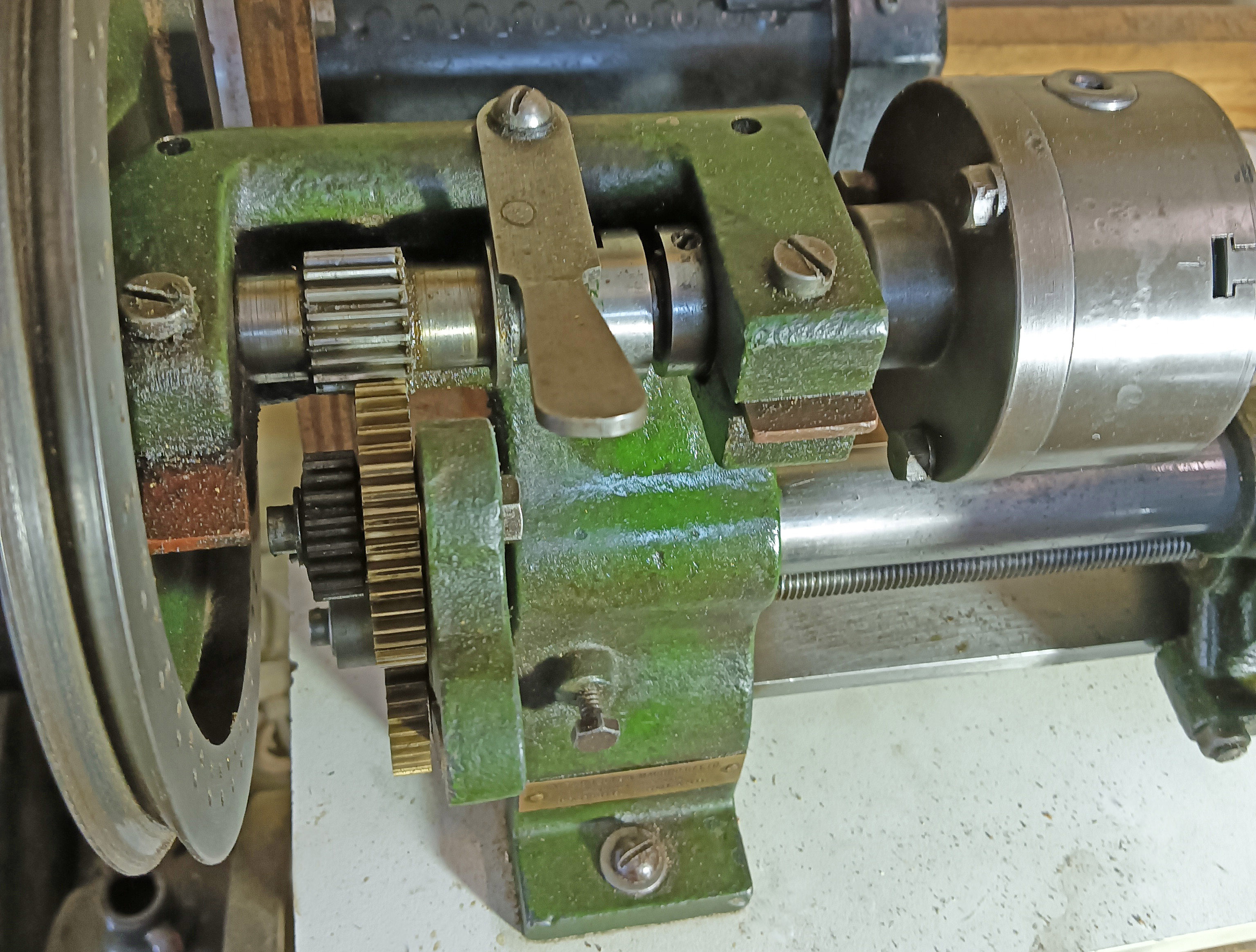 |
|
|
|
|
|
|
|
|
|
A 1923 EXE 2.5" with a different maker's badge and a lack of other data plates
|
|
|
|
|
|
|
|
|
|
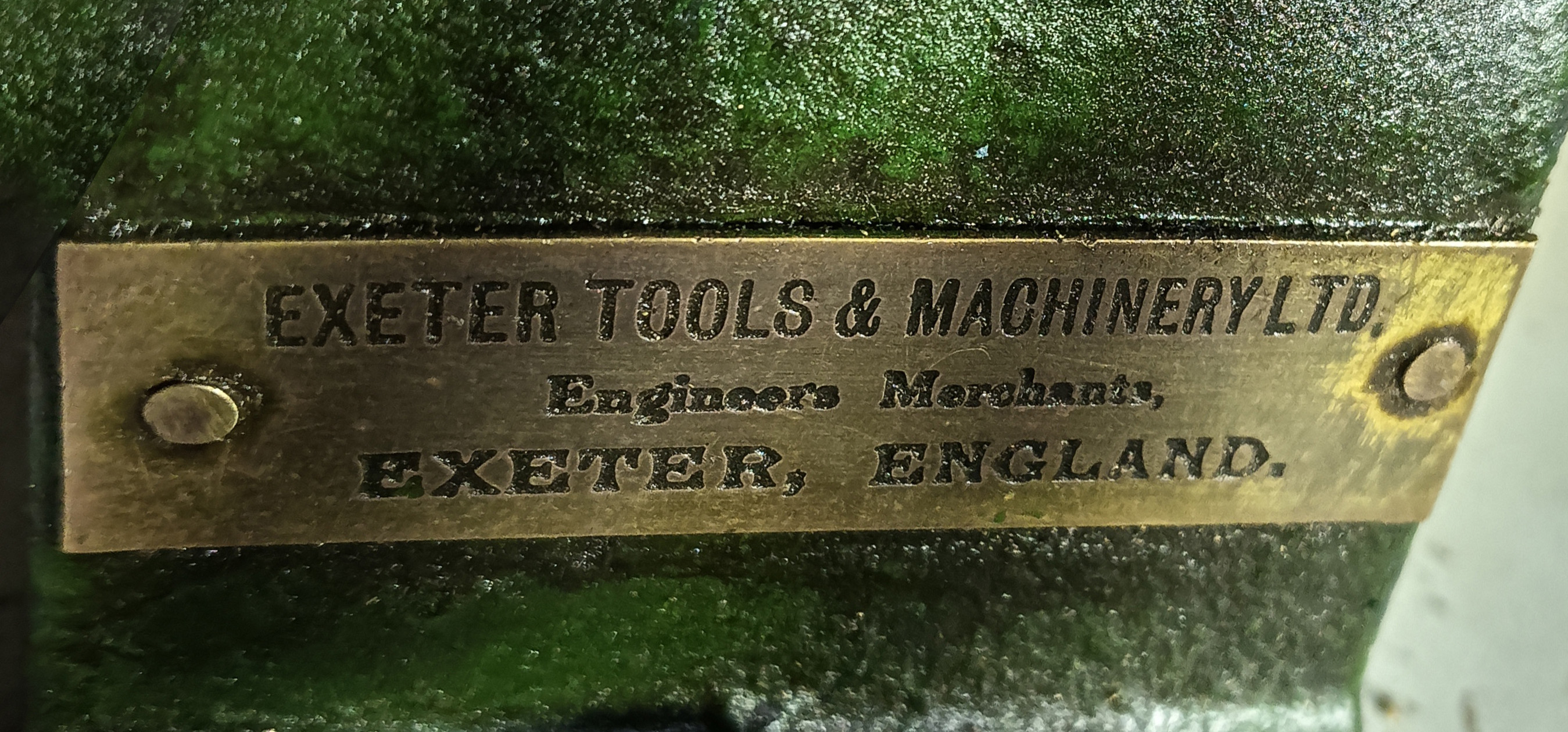 |
|
|
|
|
|
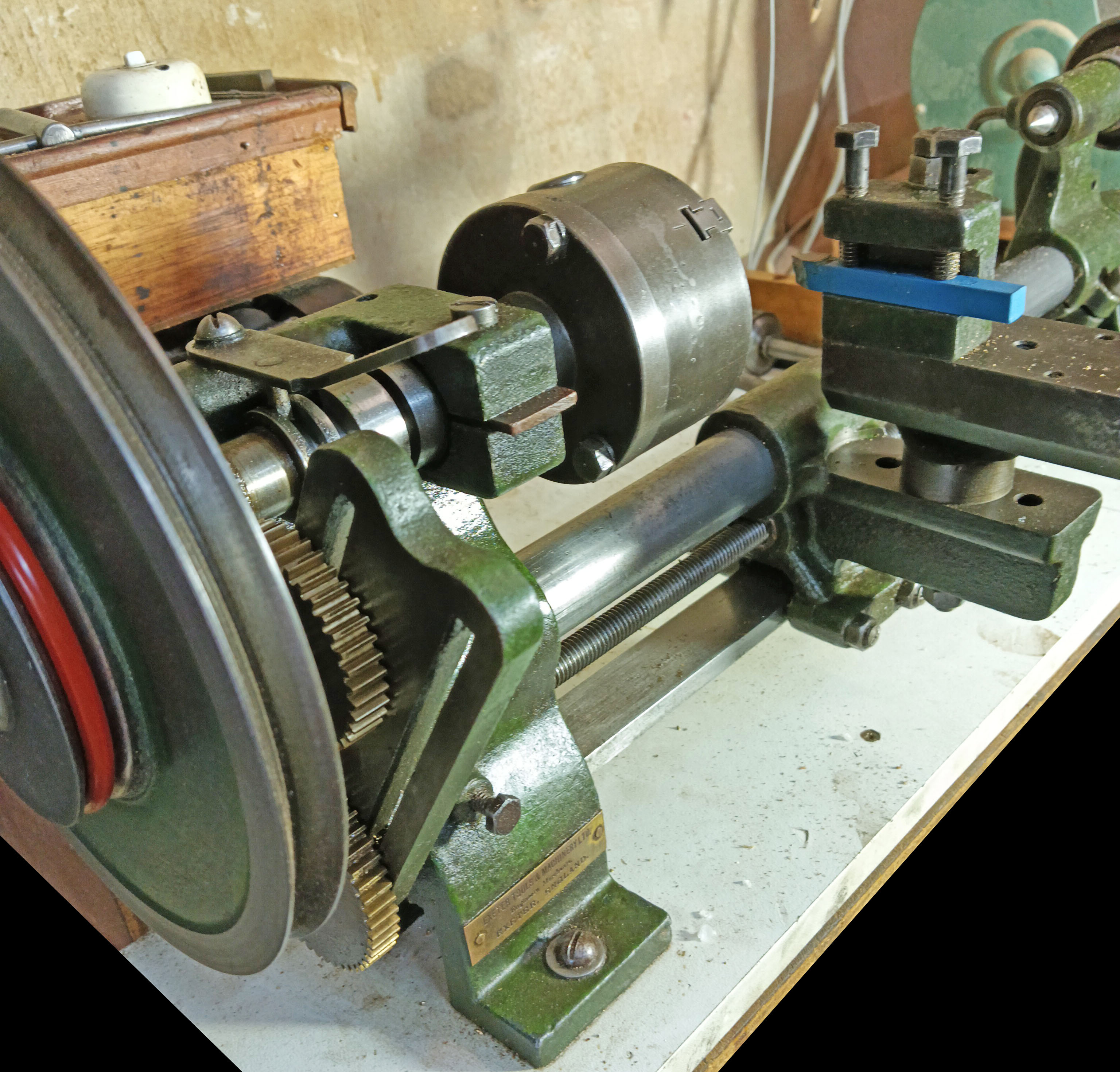 |
|
|
|
|
|
|
|
|
|
|
|
EXE 2.5" Lathe Continued Here
EXE Home Page Main EXE Page Continued Here
EXE Photographic Essay
EXE Miniature Surface Grinder
EXE Exlet Lathe A Fine & Original EXE
EXE 2.5" Lathe email: tony@lathes.co.uk Home Machine Tool Archive Machine-tools Sale & Wanted Machine Tool Manuals Catalogues Belts Books Accessories
.
|
|