 |
 |
 |
 |
 |
 |
 |
 |
 |
 |
 |
 |
 |
 |
 |
 |
 |
 |
 |
 |
 |
 |
 |
 |
 |
 |
|
|
|
|
|
|
|
|
|
|
|
|
|
|
|
|
|
|
|
|
|
|
|
|
|
|
|
|
|
|
|
|
|
|
|
|
|
|
|
|
|
|
|
|
Until the late 1970s, and an influx of cheap examples from the Far East, any small used lathe would command a premium price. In fact, so hard to find were reasonably-priced ones in sound order that many enthusiast resorted to making their own. Today, for better or worse, small lathes are freely available at knock-down prices and building one - unless to fulfil some special function - is an exercise done for its own inherent pleasure and sense of achievement. Below can be seen the end result of 3-years' such work, in a modestly-equipped workshop, by a 80-year old Hubert Elffers - a handsome, compact, neatly-designed and effective little 2" x 8" backgeared and screwcutting lathe of remarkably simple construction. Incorporating several ingenious design features (and aided by its rugged construction, taper-roller bearing headstock, wide flat-topped bed and generously-proportioned slides) it has proved, under test, to turn smoothly and accurately. However, with its drive coming via a Poly-V belt from a 3-phase motor with variable-speed inverter control, it was found that when cutting heavier threads, or turning larger diameters, the slower speeds had insufficient torque. Because the original design did not include backgear (partly because of the restraints of space, but mainly because it was wished to avoid gears affecting the turned finish) a dismountable 8.7-1 gear-reduction drive was arranged that could be bolted in place behind the headstock as and when required. In order to ease the fitting and dismounting of spindle nose fittings a circle of indexing holes was drilling into the nose abutment flange on the 13/4" diameter carbon-steel headstock spindle. To ensure that it had the strength to hold the mandrel firmly whilst even a very tight chuck was unscrewed, the detent pin was made as robust as possible. Continued below:
|
|
|
|
|
|
|
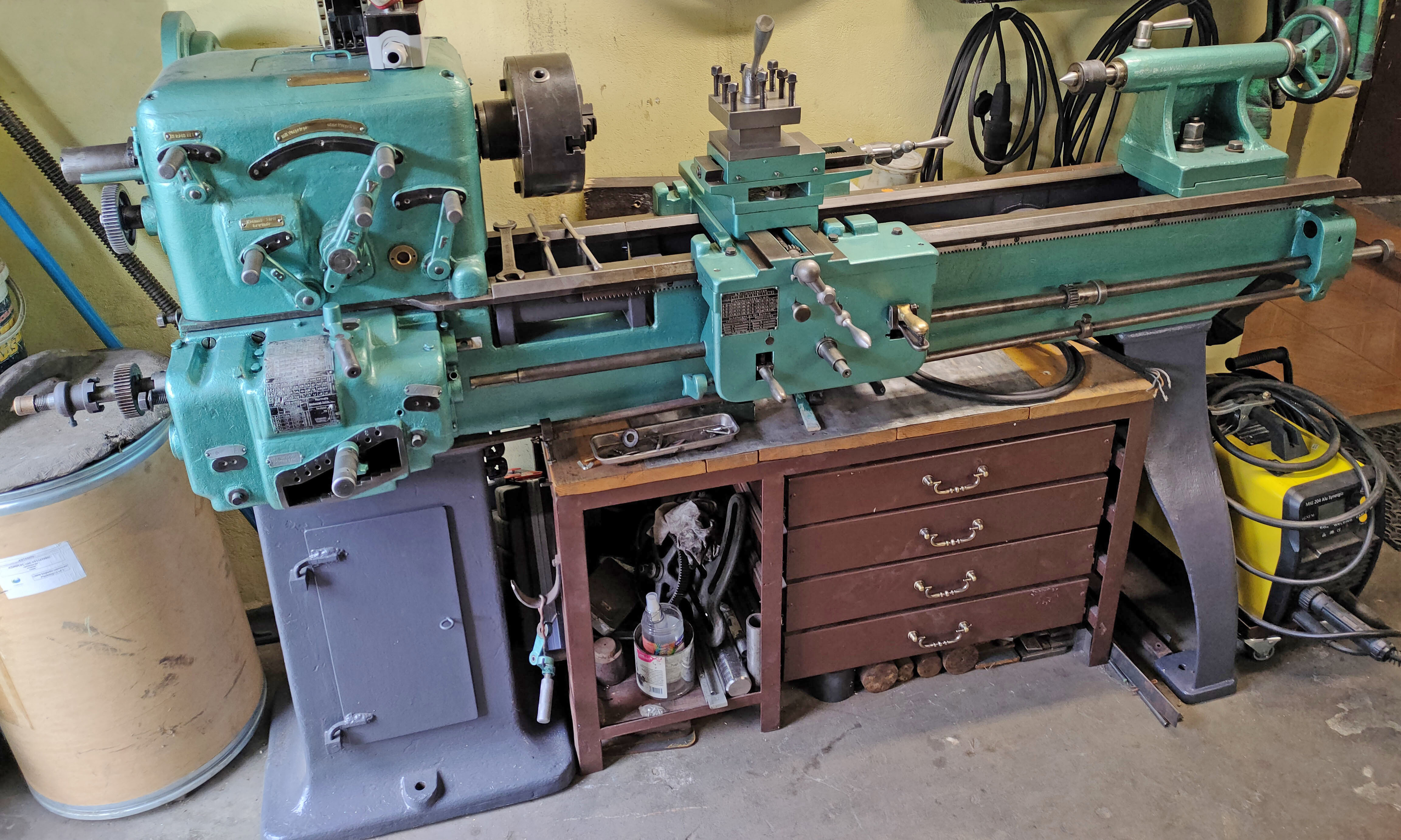 |
|
|
|
|
|
The completed lathe - 3-years' part-time work by a very active octogenarian
|
|
|
|
|
|
|
|
|
|
|
|
Continued: After some thought a tumbler-gear system was installed to drive the leadscrew; unusually (and ingeniously) this was placed on the right-hand side of a metal plate fastened to the headstock end of the bed. In addition to the usual forward, neutral and reverse this novel arrangement allowed a stub 'leadscrew' to be placed about 2" lower than the actual leadscrew, thus making space for a standard Myford 'banjo' and changewheels. To avoid the necessity of having to use metric conversion changewheels the leadscrew was cut 10 t.p.i (Acme form) and, as 10 t.p.i = 2.54 mm, this was considered near enough to 2.5 mm pitch. When the first metric screwcutting job was tried - a 0.5 mm thread - the builder was delighted to find no detectable error over a distance of several cm. In addition to the changewheel drive a separate power feed was been arranged to the carriage using that old favourite - a car windscreen wiper motor controlled by a variable resistor. The motor was mounted on a shelf, beneath the lathe, to drive via speed-reducing pulleys to a small countershaft. The drive them passed upwards (again through a pair of step-down pulleys) to the tailstock-end of the leadscrew. This arrangement gave that most desirable of effects - normally only available on an expensive toolroom lathe like the Hardinge HLV-H - where a precise sliding speed could be set for a particular combination of workpiece material, diameter and spindle speed. A good deal of thought went into the compound slide rest. The result was exceptional: a unit with slides having generous travel, fitted with large and clear micrometer dials and, with closely-spaced gib-strip adjustment screws, a silky feel with no loss of rigidity. The first toolpost used was an home-made "Norman Patent" type (as employed for many years on Drummond M-Type lathes) - a block of steel, split on one side, that dropped over a central pin and able to be locked at any height. This was replaced by the central part from a simple but effective commercial quick-set type - for which a large batch of extra toolholders was then manufactured. For a delicate touch when drilling a lever is far superior to a thread - and so the tailstock was constructed with its No. 1 Morse taper spindle driven by rack-and-pinion gearing controlled through a 3-spoke capstan handwheel. Arranged so that it sat underneath the barrel (in order to pass though a greater mass of material) a spindle lock of the proper (and powerful) split-barrel type was chosen. A further advantage of this location (as used on the Myford ML7) is that it removed the need to incorporate a boss on the back of the tailstock body to hold the lock, though there remained the slight inconvenience in having to reach over to operate the lever..
|
|
|
|
|
|
|
|
|
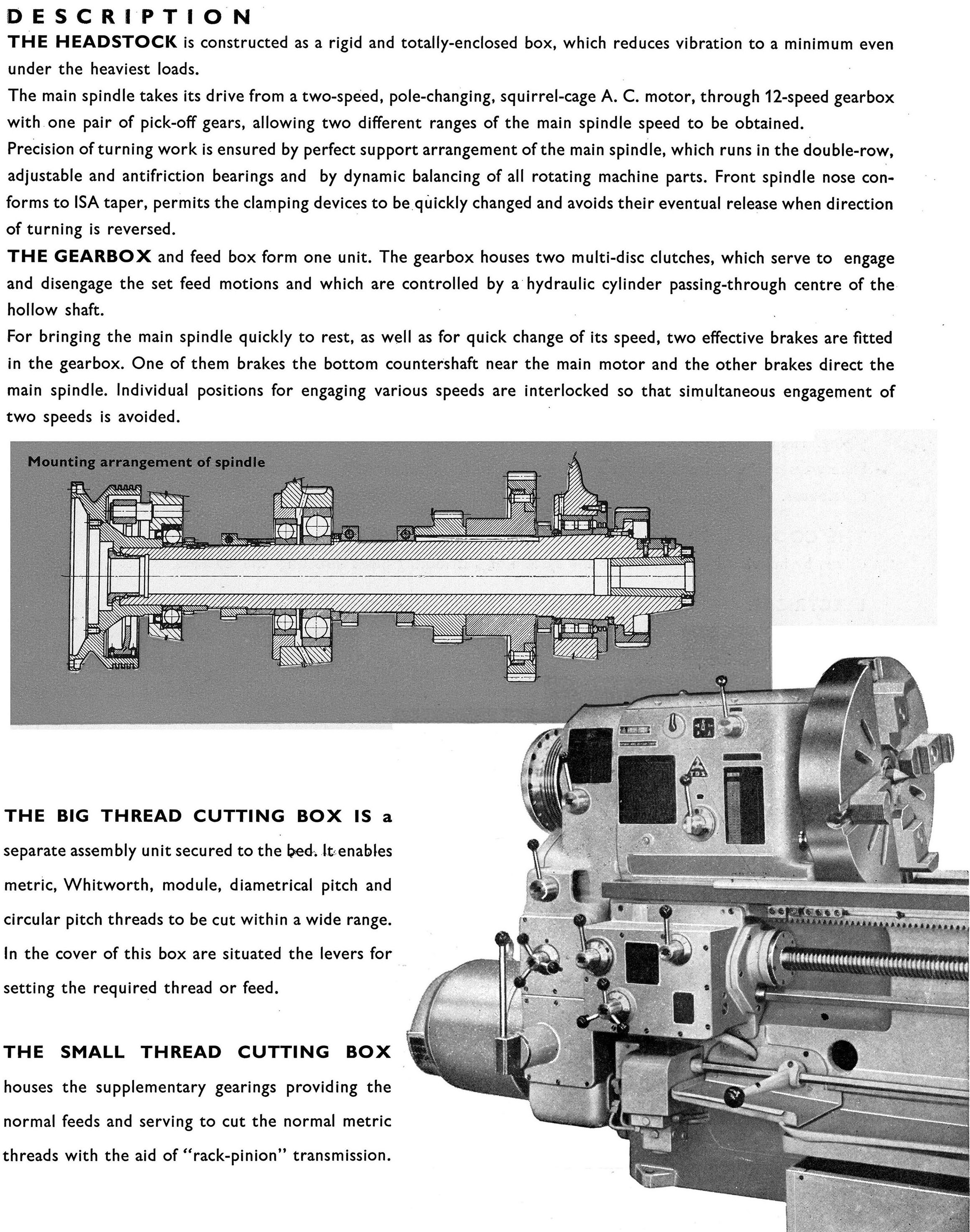 |
|
|
|
|
|
The neat changewheel cover was professional made by a sheet-metal worker - from a cardboard pattern prepared by the owner
|
|
|
|
|
|
|
 |
|
|
|
|
|
|
Spindle-end collet holder and a power feed fitted to the leadscrew - the drive pulley can be seen at its tailstock end
|
|
|
|
|
|
|
 |
|
|
|
|
|
The changewheels mounted and the drive to the leadscrew arranged
|
|
|
|
|
|
|
|
|
|
|
|
 |
|
|
|
|
|
The basic lathe complete but awaiting a backgear system, tumble-reverse and a variable-speed drive to the leadscrew
|
|
|
|
|
|
|
 |
|
|
|
|
 |
|
|
|
|
|
|
The windscreen wiper motor (bottom left) driving by speed-reducing pulleys to a small countershaft - all mounted on a shelf below the lathe. The right-hand belt (also by speed-reducing pulleys) drives upwards to the tailstock-end of the leadscrew.
|
|
|
|
|
|
|
 |
|
|
|
|
|
|
Because the Myford changewheels are really too big to fit on this little 2-inch centre height lathe the problem of accommodating them was neatly (and ingeniously) solved by placing the tumbler-gear mechanism on the right-hand face of the wall used to mount the Myford changewheel bracket - thus creating a stub 'leadscrew' placed lower down and towards the front to provide the required additional space.
|
|
|
|
|
|
|
 |
|
|
|
|
|
|
A professional appearance to the compound slide rest
|
|
|
|
|
|
|
|
|
|
|
|
|
|