 |
 |
 |
 |
 |
 |
 |
 |
 |
 |
 |
 |
 |
 |
 |
 |
 |
 |
 |
 |
 |
 |
 |
 |
 |
 |
 |
 |
 |
 |
 |
 |
 |
 |
 |
 |
 |
 |
 |
 |
 |
 |
 |
 |
 |
 |
 |
 |
 |
 |
 |
 |
 |
 |
 |
 |
 |
 |
 |
 |
 |
 |
 |
 |
 |
 |
 |
 |
 |
 |
 |
 |
 |
 |
 |
 |
 |
|
|
|
|
|
|
|
|
|
|
|
|
|
|
|
|
|
|
|
|
|
|
|
|
|
|
|
|
|
|
|
|
|
|
|
|
|
|
|
|
|
|
|
|
|
|
|
|
|
|
|
|
|
|
|
|
|
|
|
|
|
|
|
|
|
|
|
|
|
|
|
|
|
|
|
|
|
|
|
|
|
|
|
|
|
|
|
|
|
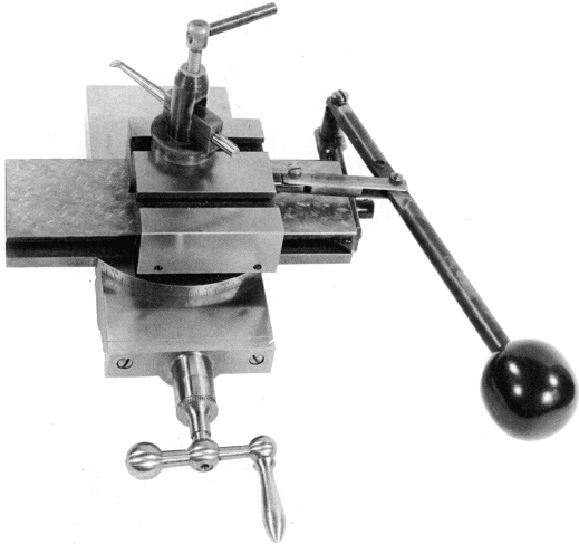 |
|
|
|
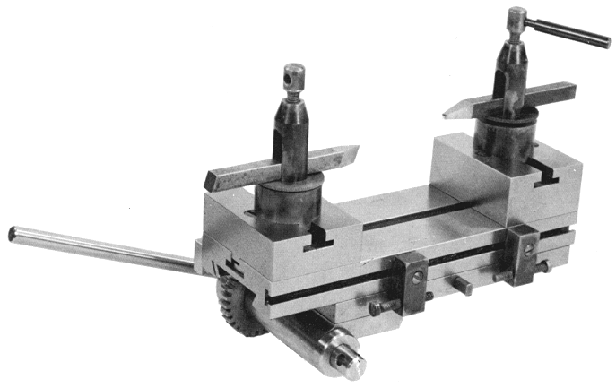 |
|
|
|
|
|
|
Lever-operated slide rest with front and rear toolposts. Often used for forming fork - or for parting off with an inverted tool in the rear post.
|
|
|
|
|
|
|
|
|
|
|
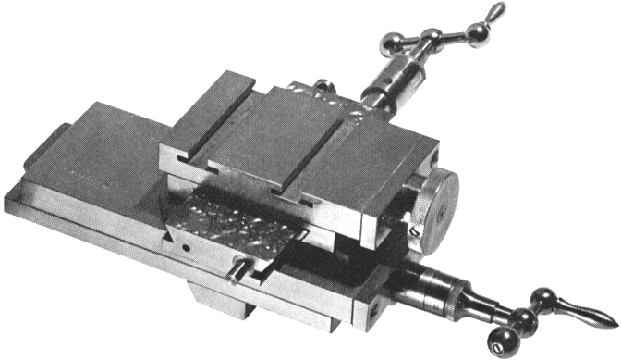 |
|
|
|
|
|
Screw-feed cross slide and lever feed tool slide - this was listed as being available for all but the smallest of the Derbyshire lathes.
|
|
|
|
|
|
|
|
|
|
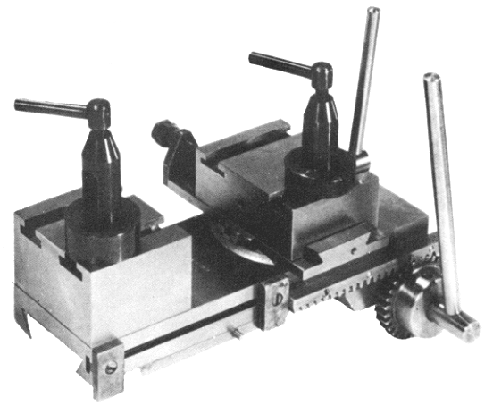 |
|
|
|
|
|
|
The famous Derbyshire "Triple Slide Rest" - a compound assembly with a third slide on top.
|
|
|
|
|
|
|
|
|
|
|
|
|
|
|
Double Compound rack and pinion driven slide rest.
|
|
|
|
|
|
|
|
|
|
|
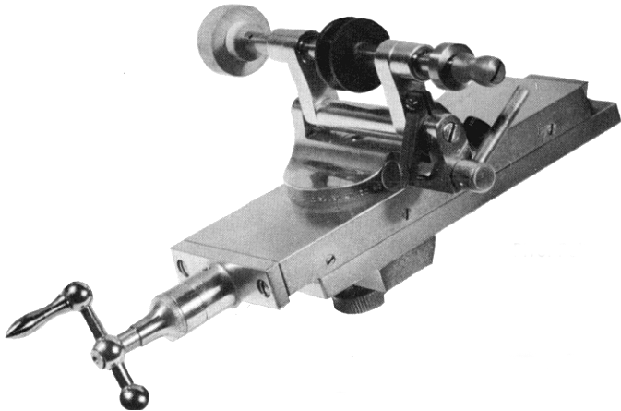 |
|
|
|
|
|
|
Pivot polisher on swivel base mounted on a special cross slide
|
|
|
|
|
|
|
|
|
|
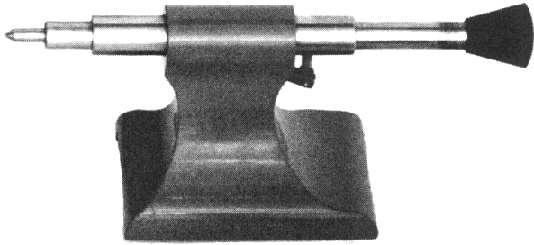 |
|
|
|
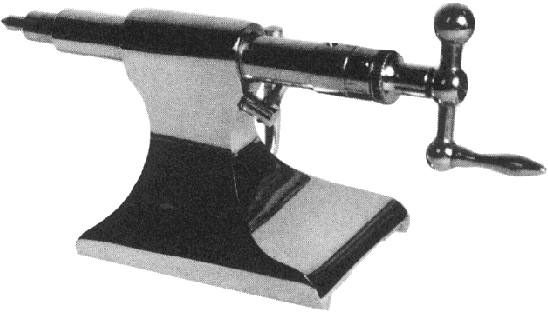 |
|
|
|
|
|
|
|
The simplest form of tailstock available for a watchmaker's lathe. The "push barrel" is capable of holding small collets and the unit is intended for centring, turning work between centres and checking the concentricity of components.
|
|
|
|
|
|
|
|
|
|
|
|
|
|
|
|
Basic screw tailstock - this has a long barrel which, even when fully extended, is still fully supported within the main casting.
|
|
|
|
|
|
|
|
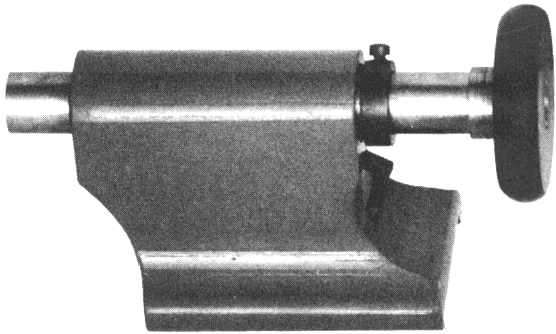 |
|
|
|
|
|
|
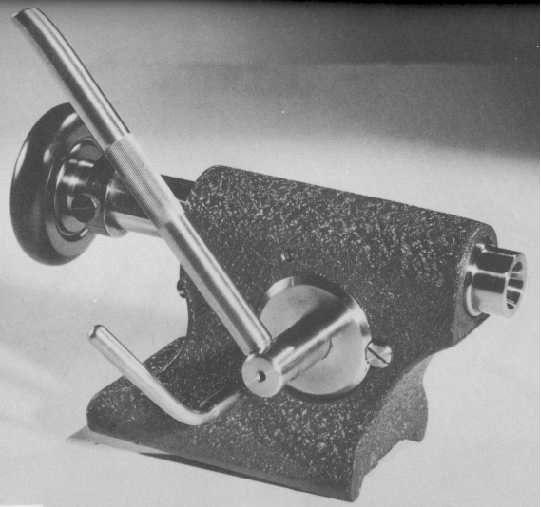 |
|
|
|
|
|
|
|
Plain (no screw or lever feed) but heavier-duty tailstock which holds the same type of collet as the headstock. This design was available for the WW, Large Lathe, Magnus, Elect 750 and Model A.
|
|
|
|
|
|
|
|
|
|
|
|
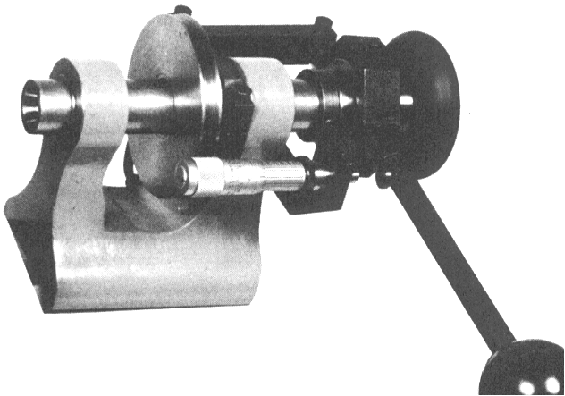 |
|
|
|
|
|
|
|
The most complete, versatile (and expensive) of the tailstocks the "Combination" had a rack-and-pinion drive to the barrel - and accepted the same collets as the headstock. A version of this tailstock was available for all Models of Derbyshire lathe
|
|
|
|
|
|
|
|
|
|
|
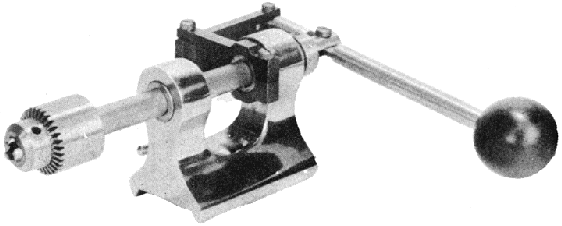 |
|
|
|
|
|
|
|
Lever-action Revolving Tailstock - intended for deep-hole, high-precision, small-diameter drilling this was, in effect a modified headstock which allowed a drill, held in a collet, to be rotated at very high speed. A micrometer barrel was attached to the side of the unit to allow precise depthing. With tiny drills the problem is to attain the correct cutting speed; by rotating the headstock (holding the workpiece) in one direction and the drill in the other - at up to 10,000 rpm - an efficient cutting speed is more easily obtained.
|
|
|
|
|
|
|
|
|
|
|
|
|
|
|
A simple type of lever-action tailstock based on a modified headstock casting.
|
|
|
|
|
|
|
|
|
|
|
|
|
|
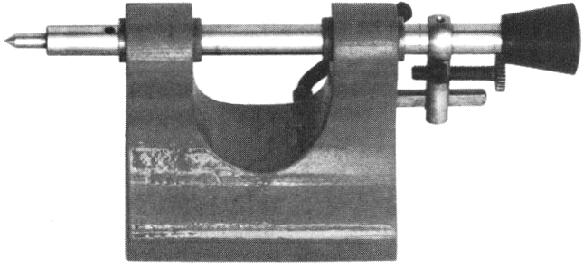 |
|
|
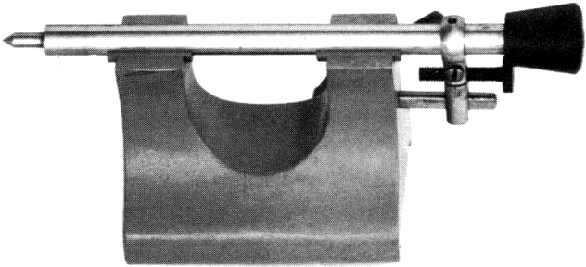 |
|
|
|
|
|
|
|
Closed tailstock with lever feed - designed for the same type of work as the open tailstock - but slower and more cumbersome to use, if rather safer and stronger when handling heavier jobs.
|
|
|
|
|
|
|
|
|
|
The Half-open tailstock is a traditional design originally intended for light duty, mass-production work. The idea is to have a selection of barrels to hand, each equipped with a different tool, so that a series of operations can be carried out in rapid succession - in effect, a poor-man's capstan unit.
|
|
|
|
|
|
|
|
|
|
|
|
|
|
|
|
|
|
|
|
 |
|
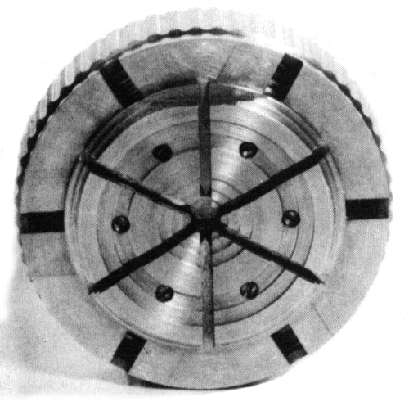 |
|
|
|
|
|
|
|
|
|
|
|
|
Designed to fit the Magnus and Elect lathes (but also used on many other makes of watchmakers' lathes) the Snyder-Bezel 6-jaw chuck was designed to grip thin work with either its outer or inner rings. The six hardened jaws were moved by rotating the outer milled ring on the inside of which was machined a highly-accurate scroll. This type of workholder is sometimes referred to as a "ring-scroll" chuck.
1. Chuck stem 2. Split lock ring 3. Scroll 4. Face plate 5. Jaw nut 6. Jaw 7. Jaw screw
|
|
|
|
|
|
|
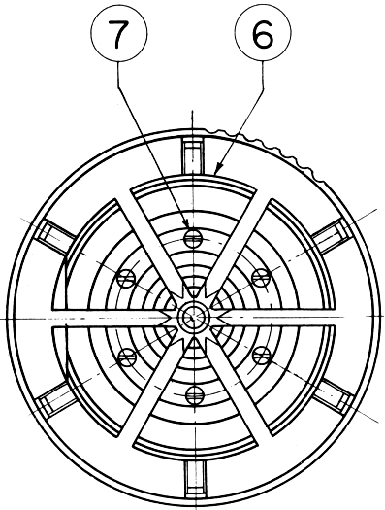 |
|
|
|
|
|
|
|
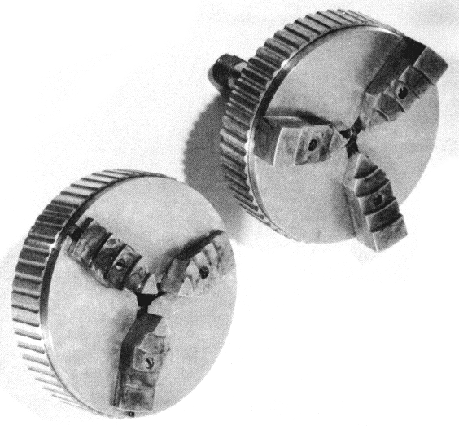 |
|
|
|
|
|
|
|
2.5" diameter Precision Universal 3-jaw chucks with "ring-scroll" operation. Each jaw has a detachable face which can be removed and
|
|
|
|
|
|
|
|
|
|
|
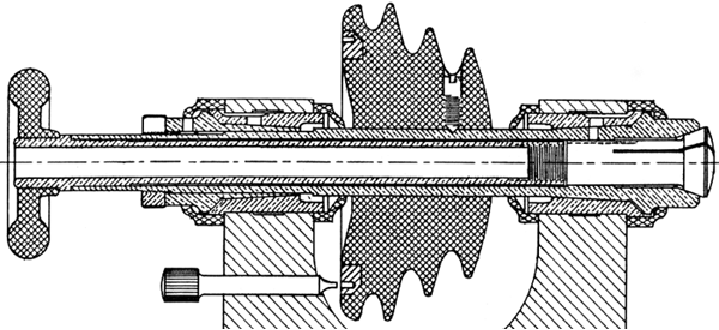 |
|
|
|
|
|
|
An American Watch Tools Company drawing from about 1890 showing a section through the headstock of an early WW lathe. The unit consisted of the main "frame", a Spindle, a Rear Adjusting Bearing, a Bearing Adjusting Nut and the Headstock Bearings themselves. All the bearing surface were hardened, ground and finally lapped to a perfection of fit. The Headstock Bearings were pressed into bored and honed holes in the casting - the Front Bearing having the same angles of 3 and 45 degrees as the Spindle Nose. The Rear Adjusting Bearing was a sliding fit on the spindle - and kept from turning by a key pin; its two angles of 3 and 45 degrees matching the angles formed on the "inner" Headstock Bearing. The single Adjusting Nut screwed onto a very fine thread on the end of the spindle. Like many other makes of watchmaker's lathe, close-fitting dust caps were snapped onto flanges at each side of both bearings.
|
|
|
|
|
|
|
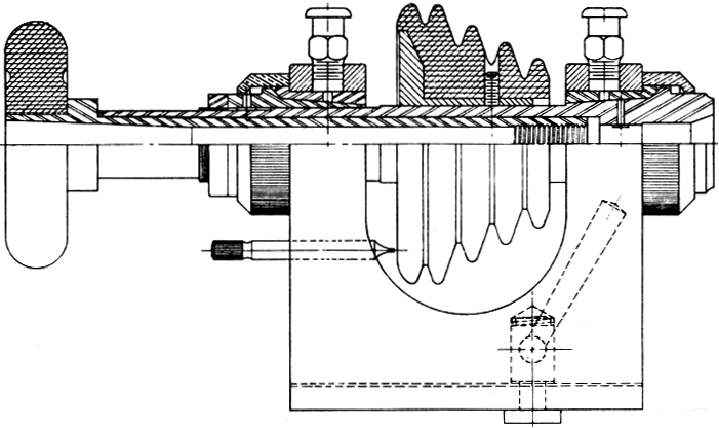 |
|
|
|
|
A drawing from 1950 of the headstock fitted to the Magnus lathe - with the same 50 mm centre height as a standard WW, but with a collet capacity of 0.3125" (5/16" - or 80 metric) compared to the 0.1969" (50 metric) of the original. The assembly was essentially the same as the one above but the headstock frame was more massive with a greater thickness of material around the bearings. On this model dust caps were fitted to the outside of each bearing - but not to the inside faces.
|
|
|
|
|
|
|
|
|
|
|
|
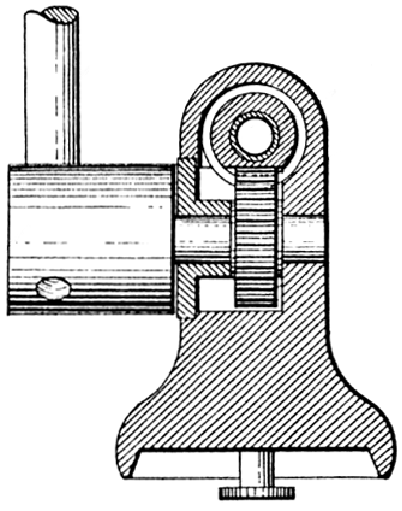 |
|
|
|
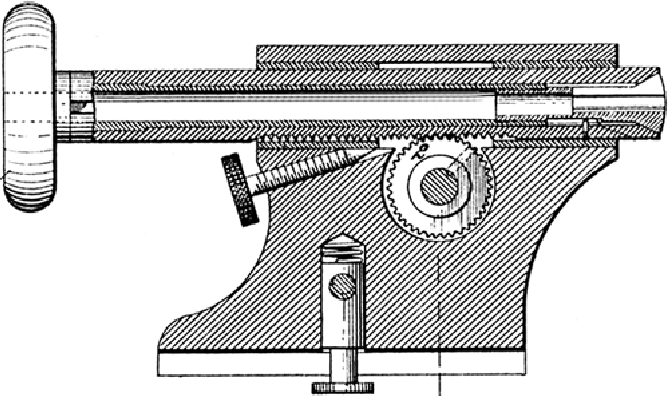 |
|
|
|
|
|
|
Combination Tailstock with patented rack-feed barrel. The patent (No. 1,168,063) was applied for on June 4, 1913 and granted on January 11, 1916.
|
|
|
|
|
|
|
|
|
|
|
|
|
|
|
|
|
End section through the Combination Tailstock.
|
|
|
|
|
|
|
|
|
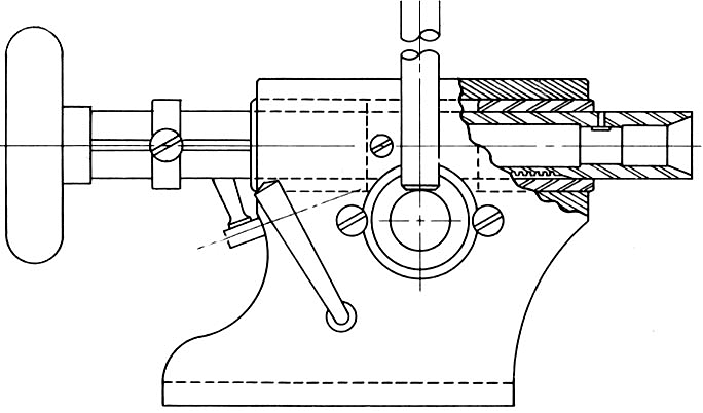 |
|
|
|
|
|
|
A later partially cut-away drawing of the Combination Tailstock.
|
|
|
|
|
|
|
|
|
|
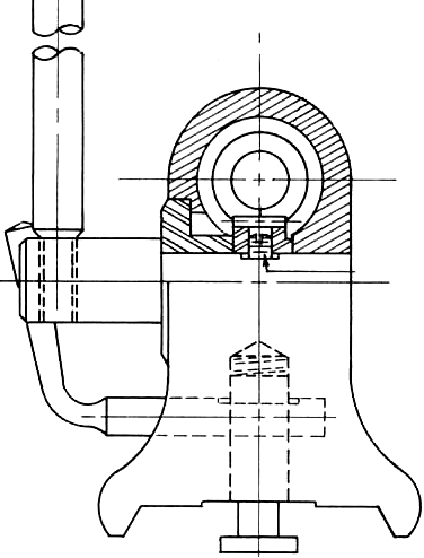 |
|
|
|
|
|
|
|
End elevation of the Combination Tailstock.
|
|
|
|
|
|
|
|
|
|
|
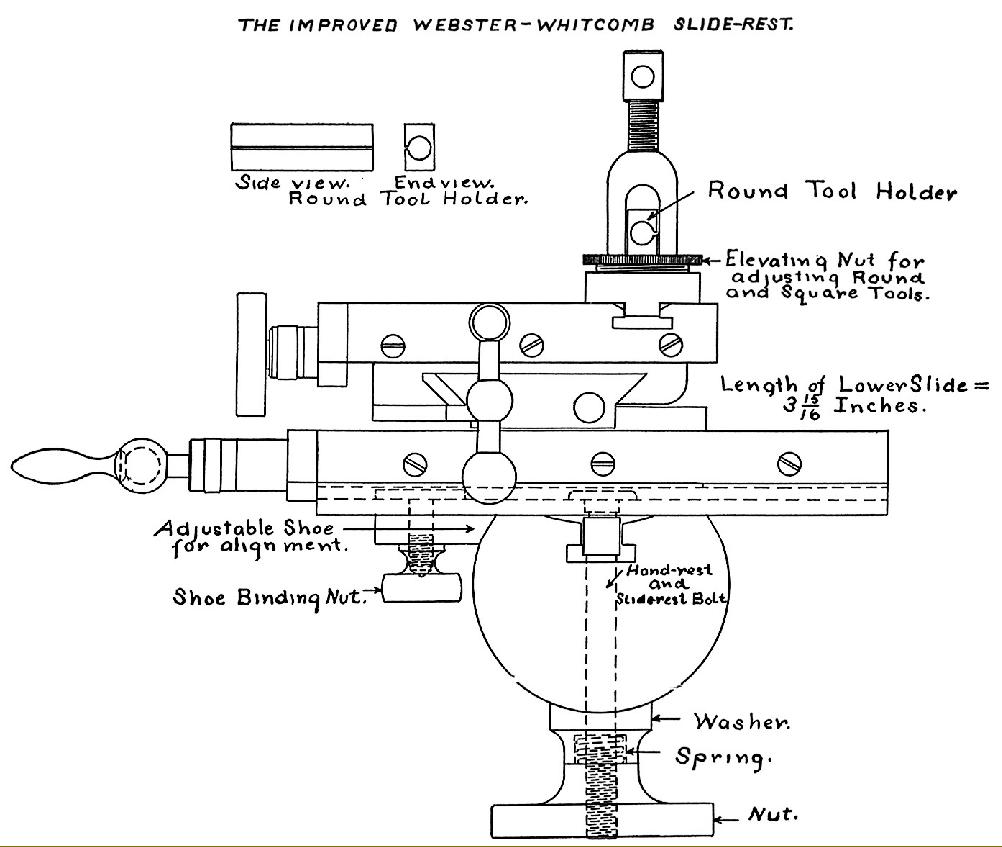 |
|
|
|
|
|
|
|
|
|
The improved slide rest assembly with an easily-adjusted tool holder
|
|
|
|
|
|
|
|
|
|
|
|
|
|
|
|