 |
 |
 |
 |
 |
 |
 |
 |
 |
 |
 |
 |
 |
 |
 |
 |
|
|
|
|
|
|
|
|
|
email: tony@lathes.co.uk Home Machine Tool Archive Machine-tools Sale & Wanted Machine Tool Manuals Catalogues Belts Books Accessories
lathes.co.uk Yamazen Milling Machines - Japan
A considerable presence in modern CNC machine tools with many subsidiaries scattered worldwide, the Yamazen headquarters are in Japan at 156 Miyazaki, Miyamae-ku, Kawasaki 216-8505. Of their earlier, conventional milling machines, as built from the late 1940s to the 1960s, little is known and few appear to have been exported to the United Kingdom; as a result, information on just four examples is known: the ram-head vertical/horizontal Type VHR-G, the plain horizontal SP-CH, the vertical SV-CH and the smaller No.1/2 NK-63. Resembling the Italian-built Rambaui VSR2 and VSR3 millers, the Yamazen VHR-G used the same form of box-type main base casting as the Yanazen horizontal Type SP-CH, was fitted with the same knee and table assembly and retained the internal, speed-change gearbox and spindle that allowed it to be used as a horizontal miller. Castings were in an iron claimed to be of the same type as Meehanite, being artificially seasoned with a tensile strength in the region of 30 to 32. Stress was relieved by heating for five hours at 500°C and then a gradual cooling with the next stage in manufacture being to first shot blast and then apply a coat of an anti-rust "oil primer". Built into the column was the gearing for the horizontal spindle, this being in nickel chrome or carbon steel with the gears shaved and hardened by a high-frequency induction process. Coolant, fitted as part of the standard equipment, was held in a tank incorporated into the base of the column. Powered by a 7.7 kW motor, the horizontal spindle had nine speeds that spanned 78 to 1200 r.p.m. on a 50 Hz motor and from 95 to 1500 r.p.m. on 60 Hz. The spindle is believed to have been fitted, as standard, with a 40 International nose. With a working surface of 1100 x 280 mm, the table was machined with three 16 mm wide T-lots, had a longitudinal travel of 820 mm, in traverse of 260 mm and vertically of 450 mm. Two motors were used for the table drive - a 0.4 kW for the horizontal and 0.5 kW for the vertical - with twelve rates of feed ranging, with a 60 HZ supply, from 15 to 700 mm/minute horizontally and vertically; rapids were set at 1800 mm/minute horizontally and (sensibly) reduced to 900 mm/minute vertically. With a 50 Hz supply feed rates slowed to 12 to 560 mm/minute horizontally with rapids at 1500 mm/minute horizontally and 750 mm/minute vertically. Automatic disengage of the power feeds was provided by knock-off stops adjustable in a T-slot running down the length of the table's front face. Instead of handwheels at each end of the table, a single forward-facing wheel was used, this having the advantage of enabling the operator to see both side of a job from a normal working position. Lubrication of the longitudinal and vertical slideways was by a hand-operated pump, fitted at the top of the knee's right-hand face. Mounted on a base able to be swivelled through 360° by worm-and-wheel gearing, the ram carrying the vertical head could be moved (by rack-and-pinion gearing) through a travel of 500 mm Able to be swivelled through 60° each side of vertical (by worm-and-wheel gearing) the vertical head held a spindle with a quill travel of 150 mm, control being by a fine-feed handwheel, a quick-action drilling lever or power at three rates of feed, 0.035, 0.07 and 0.114 mm per revolution of the spindle. The power up and down feed was fitted with adjustable, automatic micrometer-equipped stops, a fitting that aiding precision boring and drilling. Powered by a two speed, 1.5 kW motor, the vertical spindle ran in precision roller bearings, carried a 40 International nose and had, through direct drive by V-belt and a slow-speed backgear, a useful sixteen speeds from 68 to 3300 r.p.m. on a 50 Hz supply and from 75 to 3600 r.p.m. on 60 Hz. Electrical control was by a set of push buttons clustered together on the front face of the knee, these proving start, stop and inching control - the presence of electricity being shown by a pilot light Equipment supplied with each new machine included a horizontal cutter-holding arbor and end support bracket, coolant equipment with a 0.5 kW motor, base levelling screws, the necessary tools, a toolbox, oil gun and an operation manual and the final inspection chart. Optional extras appear to have limited to a vertical head raiser block, an optical measuring system, a single machine vice - but with no mention of dividing heads or rotary tables. Continued below:
|
|
|
|
|
|
|
|
|
|
|
|
|
|
|
|
|
|
|
|
|
|
|
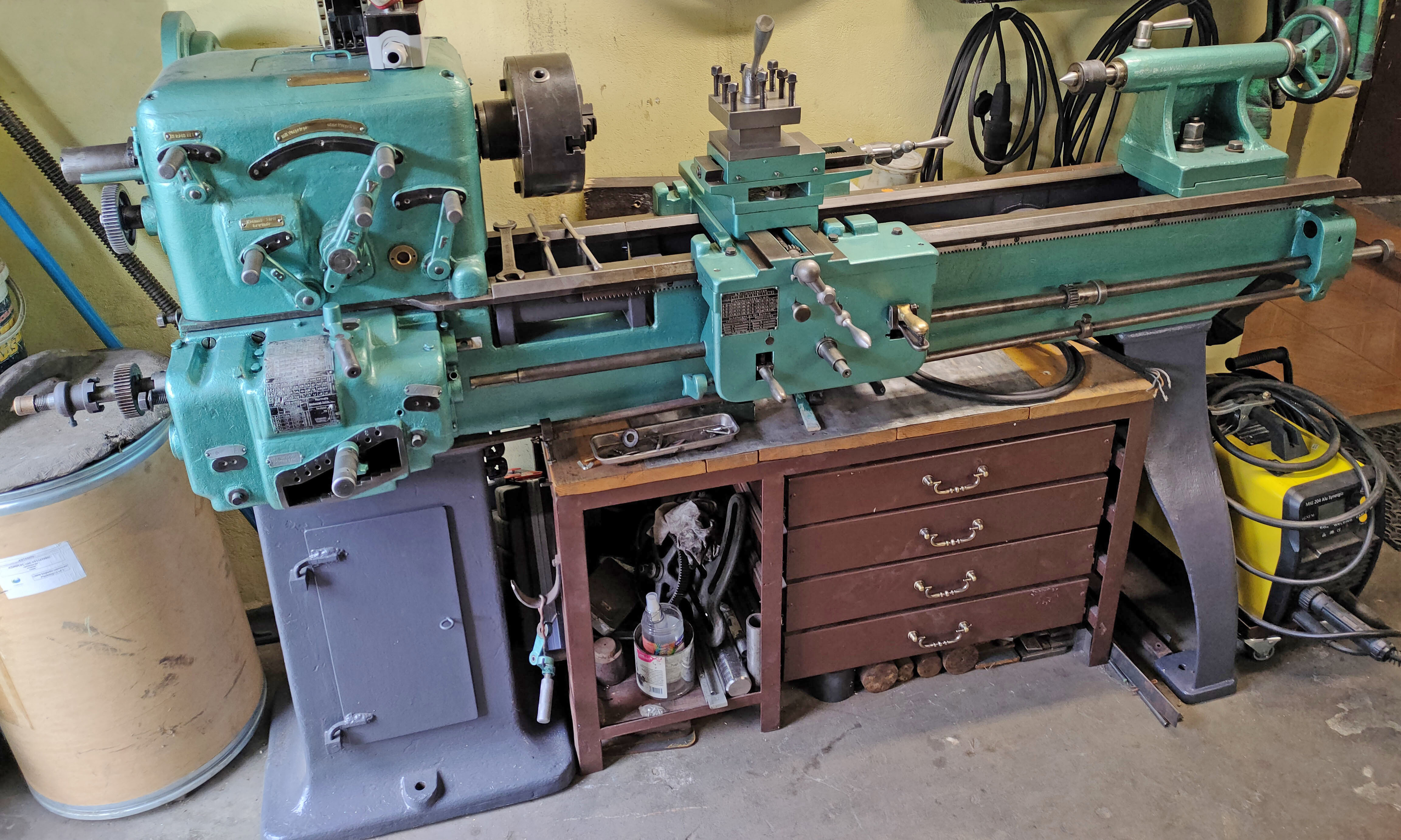 |
|
|
|
|
|
|
The Japanese Yamazen ram-head VHR-G horizontal and vertical milling machine as sold during the 1950s
|
|
|
|
|
|
|
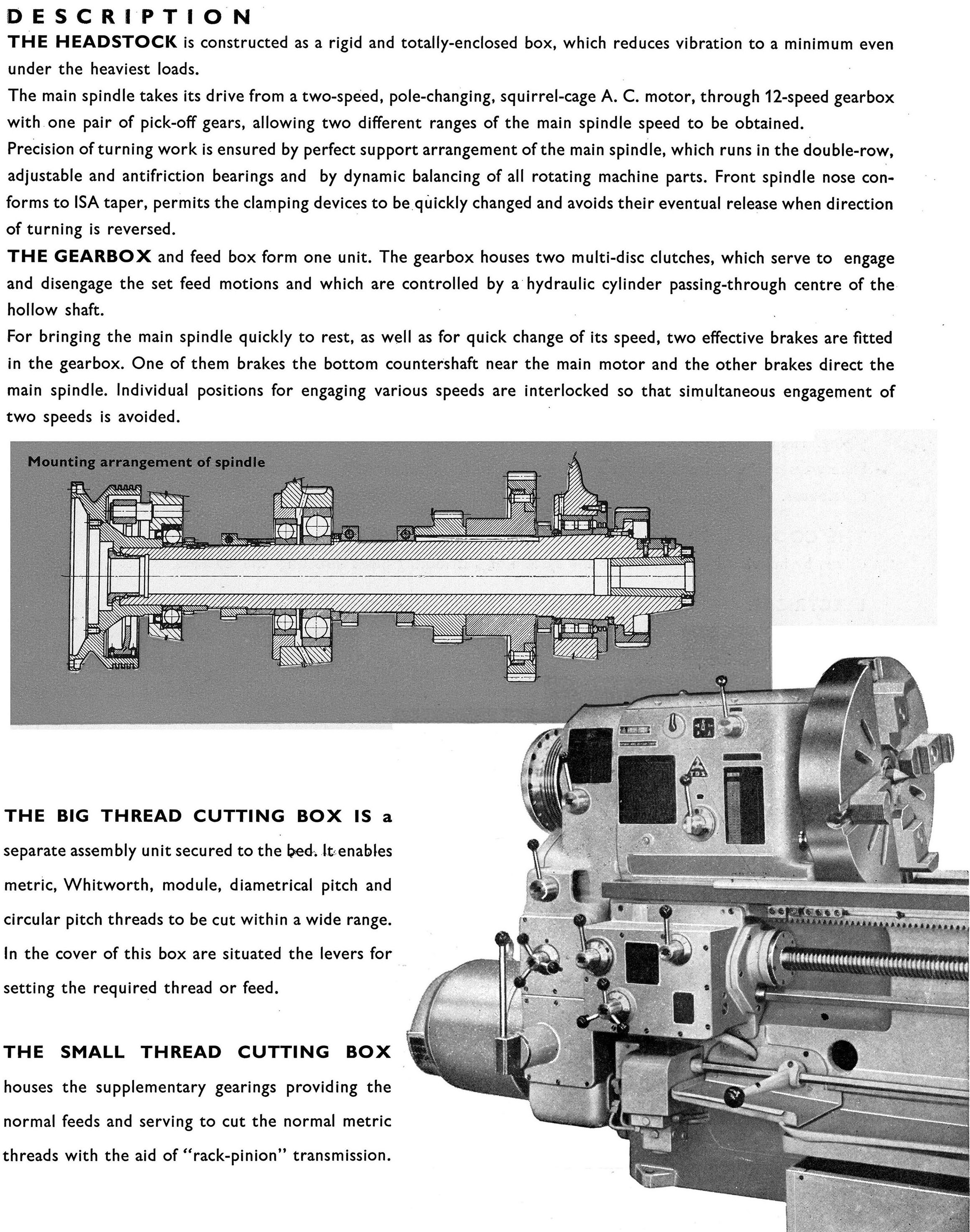 |
|
|
|
|
|
|
Yamazen horizontal milling machine Type SP-CH
Like the VHR-G ram-head model, the horizontal Type SP-CH and SV-CH vertical had their castings in an iron claimed to be of the same type as Meehanite, being artificially seasoned with a tensile strength in the region of 30 to 32. Stress was relieved by heating for five hours at 500°C and then a gradual cooling with the next stage in manufacture being to first shot blast and then apply a coat of an anti-rust "oil primer". On both models, the speed-change gearbox was built into the main column and held gears in nickel chrome or carbon steel with the gears shaved and hardened by a high-frequency induction process. Coolant, fitted as part of the standard equipment, was held in a tank incorporated into the base of the column. Powered by a 7.7 kW motor, both the horizontal and vertical model shared the same nine identical spindle speeds that spanned 78 to 1200 r.p.m. on a 50 Hz motor and from 95 to 1500 r.p.m. on 60 Hz. Both spindles, horizontal and vertical, ran in precision roller bearings and are believed to have been fitted, as standard, with a 40 International nose. While the table had the same working surface as the ram-head model - 1100 x 280 mm and three identical three 16 mm wide T-lots, the longitudinal travel was considerably reduced - from 820 mm to 750 mm. The traverse travel was also 10 mm less, at 250 mm, while the vertical suffered a reduction from 450 mm to 400. Two 60 motors were used for the table drive - a 0.4 kW for the horizontal and 0.5 kW for the vertical - with twelve rates of powered feed ranging - with a 60 HZ supply - from 15 to 700 mm/minute horizontally and vertically and, with rapids, at 1800 mm/minute horizontally and (sensibly) reduced to 900 mm/minute vertically. With a 50 Hz supply these rates were slowed to 12 to 560 mm/minute horizontally, with rapids at 1500 mm/minute, and vertical rapids at 750 mm/minute. Electrical control was by a set of push buttons clustered together on the front face of the knee, these proving start, stop and inching control - the presence of electricity being shown by a pilot light. Instead of handwheels at each end of the table, a single forward-facing wheel was used, this having the advantage of enabling the operator to see both side of a job from a normal working position. Automatic disengage of the power feeds was provided by knock-off stops adjustable in a T-slot running down the length of the table's front face. Lubrication of the longitudinal and vertical slideways was by a hand-operated pump, fitted at the top of the knee's right-hand face. On the vertical SV-CH the head could be inclined 90°each side of vertical and was fitted with a fine-feed handwheel to control the 80 mm of quill travel. The net weight of the SP-CH horizontal was approximately 1650 kg and the SC-CH vertical 1850 kg. Equipment supplied with each new machine included a horizontal cutter-holding arbor and end support bracket, coolant equipment with a 0.4 kW motor, base levelling screws, the necessary tools, a toolbox, oil gun and an operation manual and the final inspection chart. Optional extras appear to have limited to an optical measuring system, a single machine vice and, for the horizontal model a vertical head that attached to the horizontal spindle nose - but no mention of dividing heads or rotary tables. Continued below:
|
|
|
|
|
|
|
|
 |
|
|
|
|
|
|
|
|
|
|
|
|
|
|
 |
|
|
|
|
|
|
Yamazen horizontal milling machine Type M-17
Smallest of the Yamazen milling machines listed during the 1950s was the Type M-17. Like all their other models, this miller was built from castings in an iron claimed to be of the same type as Meehanite, being artificially seasoned with a tensile strength in the region of 30 to 32. Stress was relieved by heating for five hours at 500°C and then a gradual cooling with the next stage in manufacture being to first shot blast and then apply a coat of an anti-rust "oil primer". Coolant, fitted as part of the standard equipment, was held in a tank incorporated into the base of the column. Built into the main column and driven by a base-mounted 1.5 kW motor, the speed-change gearbox held gears in nickel chrome or carbon steel with the gears shaved and hardened by a high-frequency induction process. Running high-precision roller bearings, the spindle had twelve speeds, six in low range from 100 to 560 r.p.m. and in high range from 330 to 1650 r.p.m. Just one size of table was available, 750 x 190 mm, machined with three T-slots and with travels of 370 mm longitudinally was 370 mm, 150 mm in traverse and 400 mm vertically. Power feeds were provided by a universally-jointed carden shaft driven by belt from a take-off on the main motor to gearbox drive. Three rates of feed were available, 0.08, 0.12 and 0.16 mm per revolution of the cutter arbor. Automatic disengage of the power feeds was provided by knock-off stops adjustable in a T-slot running down the length of the table's front face. Surprisingly for a small miller, lubrication of the longitudinal and vertical slideways was provided, this being by a hand-operated pump, fitted at front of the knee and drawing oil from a transparent reservoir fastened to the right-hand face of the main column. Available as options were single machine vice, the Model K, and a vertical head which, being driven directly from the horizontal spindle, had the same 100 to 1650 r.p.m. speed range. Standing 1400 mm high, the miller needed a floor space of 650 by 700 mm and weighed approximately 850 kg.
|
|
|
|
|
|
|
|
|
|
|
|
|
|
|
|