 |
 |
 |
 |
 |
 |
 |
 |
 |
 |
 |
 |
 |
 |
 |
 |
 |
 |
 |
 |
 |
 |
 |
 |
 |
 |
 |
 |
 |
 |
 |
 |
 |
 |
 |
 |
 |
 |
 |
 |
 |
 |
 |
 |
 |
 |
 |
 |
 |
 |
 |
|
|
|
|
|
|
|
|
|
|
|
|
|
|
|
|
|
|
|
|
|
|
|
|
|
|
|
|
|
|
|
|
|
|
|
|
|
|
|
|
|
|
|
|
|
|
|
|
|
|
|
|
|
|
|
|
|
|
|
|
|
|
|
Announced in 1921 at £2 : 10s : 0d for the basic version, the little Wade CAV lathe was manufactured by C.A.V. Small Tools Ltd. of Portland Road, Hove, Sussex, England - a Company that had been founded in 1917 as C. A. Vandervell & Co Ltd. (C.A.V.) to produce war materials including munitions. The background to the Charles Anthony Vanderell Company is complicated, with several branches producing high-quality electrical equipment - magnetos, dynamos, starters, lamps, horns and batteries, etc. Originally based in Willesden Green, Birmingham, expansion took place with a factory in Acton and then, in 1917, a further manufacturing plant in Hove was opened, this to cope with, on a temporary basis, extra war-time demand including munitions. After the war, in 1918, the Hove factory traded as C.A.V.Small Tools and, looking around to see what was most in demand from the civilian market, decided upon the manufacture, amongst other items, of a small lathe to be branded as the "Wade C.A.V." With the little lathe already in production, on December 18th, 1922 one Francis Richard Wade of London, in conjunction with C.A.V. Small Tools Ltd., applied for a British patent to cover certain aspects of the design - this being granted on March 18th, 1924 under number 212,976. The Wade was eventually offered in a variety of forms - short and long-bed versions (with 12" and 18" between centres respectively) and as either a simple plain-turning type or fully equipped with backgear and screwcutting. As a sign of the model's appeal, although most were badged with the maker's name some carried a Selson label and were sold through that large organisation's London-based company who also imported (and often re-branded) a variety of continental European machines. In addition to home-market sales, the lathe also had some success in America and Canada with examples occasionally appearing on the used market in both countries. Made from a single drawn-steel tube of 1.75" diameter and 0.1875" wall thickness ground over its entire length to within 0.001", the bed of the CAV was held at each end in what was described as, "pressure die-cast, tough copper-aluminium alloy castings". A slot, running along the underside of the bed, acted as an alignment guide for the saddle and tailstock. Very unusually, the headstock bearings were formed from cast-in white-metal instead of bronze - and split on one side to be adjustable over a small range for taking up wear. The spindle, fitted with a 5/8" x 14 t.p.i. thread, was bored hollow - an unusual luxury on this class of lathe. The use of white metal attracted a comment in an article: "The Mandrels of Small Lathes" in the Model Engineer magazine of 14 October, 1926: The Wade...has an unusual construction of bearing, though of simple character. Instead of putting divided brasses, the heads are cast solid, and whitemetal is run in, in a jig, so as to assume the sectional appearance seen in Fig. 3. Then to give adjustment, the head and whitemetal are split through from the back only, so that the tightening of the screw (seen in plan) of each bearing, contracts the whitemetal around the spindle. Fibre washers at the ends receive the thrust." Very early machines (of which few appear to have survived) had oil holes in the headstock caps, and four narrow flat-belt pulleys; later machines were fitted with tiny, hinged-cap oilers, handles on the various hand-wheels and a 3-step "V" headstock pulley designed to take a small-diameter (5 mm) round leather-rope of the type frequently found driving sewing machines. There is a problem with the non-backgeared models where, for some inexplicable reason, the clearance between the bottom of the largest headstock pulley and the casting is insufficient to be able to get a 5mm belt back onto the next smaller pulley. It might be that the judicious use of file could solve the problem…. The small headstock spindle meant that there was no room to machine a taper in the nose to accept a centre, instead, a screw-on boss was used (a device frequently used on light, amateur lathes as far back as the 1800s) that had sufficient diameter to be bored to carry a short No. 1 Morse taper centre and, at the same time, act as a simple form of drive plate for between-centres work. Continued below:
|
|
|
|
|
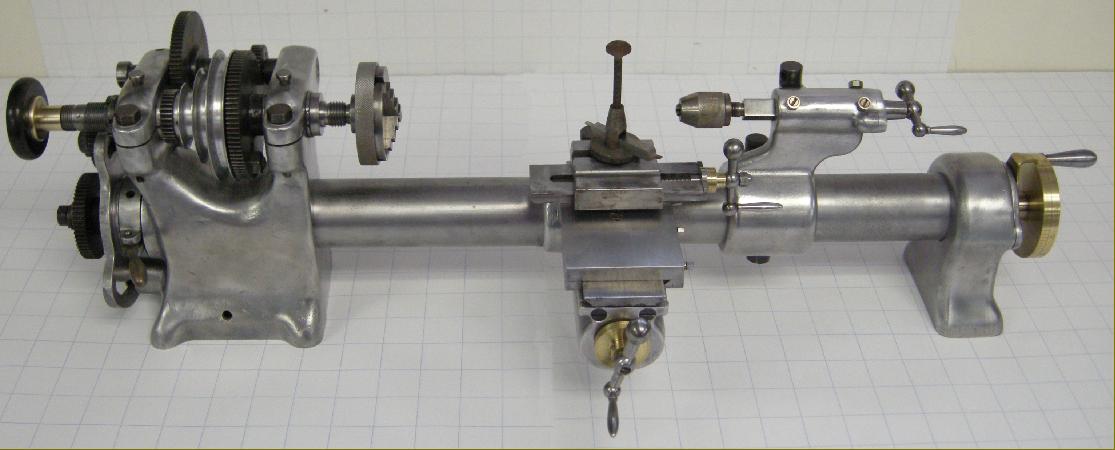 |
|
|
|
|
|
A fine example of the backgeared and screwcutting Wade CAV fitted with what may well be a home-made compound slide assembly Continued: Of the two models listed, the "No. 1" was plain-turning with its split headstock-bearing clamping screws to the rear, whilst the "No. 2", with three direct speeds and three geared speeds, was equipped with both a 5:1 reduction backgear system (using steel gears) and a screwcutting facility. The headstock on this lathe was almost twice as long and much more substantially constructed than the one fitted to the plain lathe - and had the bearing-clamp screws to the front. Formed - most unusually - from a square-section steel bar threaded on its end to accept accessories, the tailstock spindle was locked by a slot in the aluminium casting closed down by a set-screw. As it was fitted with an ordinary Whitworth-form right-hand thread, the cross-slide had a "cack-handed" feel when applying a cut - turning the wheel clockwise resulted in the tool being retracted instead of advanced, an awkward arrangement with great potential to wreck jobs, until the owner became used to it (and especially dangerous if conventionally-arranged machine tool were in the same machine shop. The toolpost was a simple "clog-heel" type, made in either aluminium or bronze - through the latter, being expensive, is rare and must have been abandoned early in the machine's life. Thirteen changewheels (80t, 70t, 63t, 60t, 55t, 52t, 50t, 42t, 40t, 38t, 35t, 32t and one of 30t the headstock spindle) were included in the basic set and these were able, in combination with a 12 t.p.i leadscrew, to generate threads between 6 and 70 t.p.i. Astonishingly for an inexpensive lathe, the steel changewheels were heat-treated and ran on gunmetal bearings - as did a neatly-engineered dog clutch, fitted to the end of the leadscrew and enclosed within the headstock casting. Exported to Canada and the USA, the lathe was offered in the latter country by the Gerold Company of 120 Liberty Street, New York who listed the full range of accessories including an American "Whiton" 3-jaw ring-scroll chuck of 2.5" diameter (an item also fitted to English-market versions), a 3-inch diameter 4-jaw chuck, two simple "bell" and "ring" chucks, an offset centre for taper turning, a travelling steady, various wood-turning centres, a faceplate with adjustable dogs to convert it into a large 4-jaw chuck, three hand-T-rests of different lengths, a tailstock chuck mounted on its own square barrel, a tailstock drilling pad and, to "special order" (and hence very rare), a compound slide rest and milling slide - neither of which the author has ever seen on English-market Models. With improved engineering facilities to hand, in the last years of production (when, judging by the numbers discovered, sales must have been declining) some changes were introduced including a heavier and more rigid headstock with a flat front face and a conventional round (instead of square) tailstock barrel with a proper Acme feed screw. Some of these last models were also given a very much more rigid and heavy cast iron bed supports and carriage units. If the cast-iron models had tapped holes in bottom face of the bed-support feet is not known - but none of the aluminium, ones so far examined had. How was the lathe intended to be bolted down. It's believed that two tapped holes in the bed, one at each end, were intended for this purpose but, unusually, these are set at a slight angle - one wonders why. Finally, very late in the day (and too late to be a commercial success) a revised "cast-iron" model was introduced that, while it followed the design of the earlier type, had Morse taper centres and was fitted with T-slotted cross-slide that rotated about a short but stout steel post - so allowing a milling attachment to be mounted. As well as being decently made, the detail engineering of the No. 2's headstock and changewheel drive to the leadscrew (through a dog-clutch) was quite exceptional for so inexpensive a product. In reality, however, the design was a triumph of hope over practicality as any attempt to turn more resilient materials, or take large cuts, quickly showed up the machine's inherent weakness - a lack of rigidity. However, it did provide the impecunious amateur with an opportunity to buy a new lathe on which to learn the essentials of turning and screwcutting. Another "Wade" product - and vanishingly rare - was a tiny sensitive bench drill. With its main body in aluminium, like the lathe, it had the usual arrangement of two jockey pulleys at the rear guiding a round rope belt around the spindle pulley - of which just one step was provided. It was intended for drive by a treadle unit which must, at the expensive 1927 price of £3 : 5s : 0d., have been included along with the advertised 3-jaw chuck..
|
|
|
|
|
|
|
|
|
|
|
|
|
|
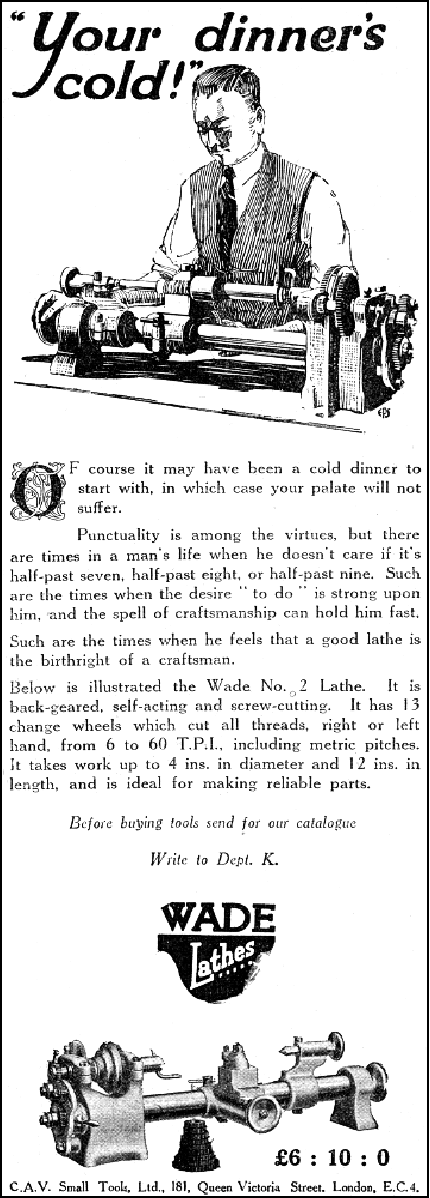 |
|
|
|
|
|
|
|
|
A familiar cry in days gone by when men were men and, upon returning from a 12-hour shift in the foundry, would dismount from a 600cc sloping-cylinder Panther motorcycle and Bursmar double-adult sidecar, strip off their soaking-wet Belstaff Storm Guard coat and gauntlets, stride purposefully into the garden shed and recommence work of the 1/8" scale steam locomotive intended as a present for their son's forthcoming 7th birthday. Meanwhile, in the Kitchen, SWMBO was preparing a hearty hot meal - as instructed at school when asked to consider the O-Level question: "Your husband and son return from a day outside in freezing weather working on the family car. Describe the dishes you would prepare for the family evening meal. Present the budget, an account of the nutrition provided and justify your choices".
|
|
|
|
|
|
|
|
|
|
|
|
|
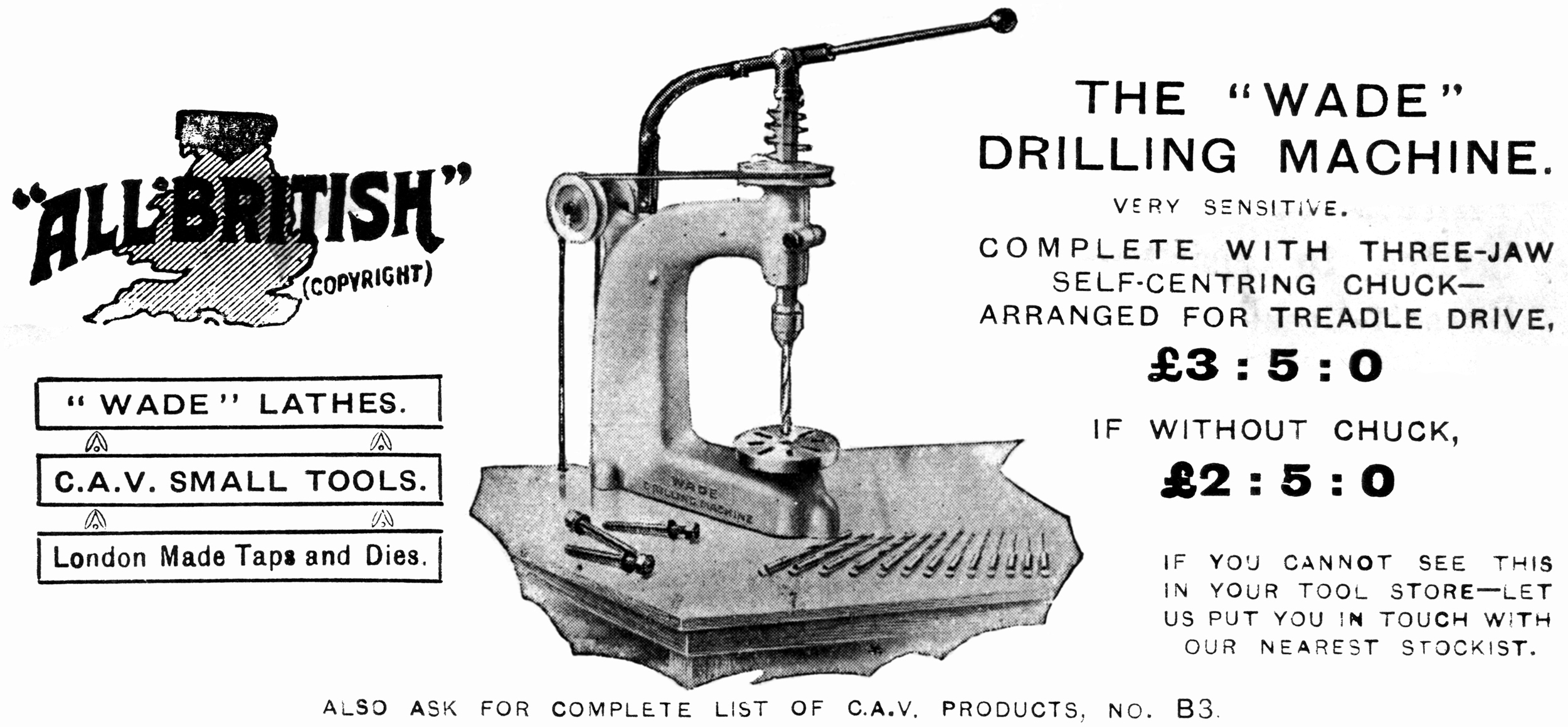 |
|
|
|
|
|
|
|
|
|
The once expensive and now very rare "Wade" treadle-operated sensitive drill
|
|
|
|
|
|
|
|
|
|
|
|
|
|
|
|
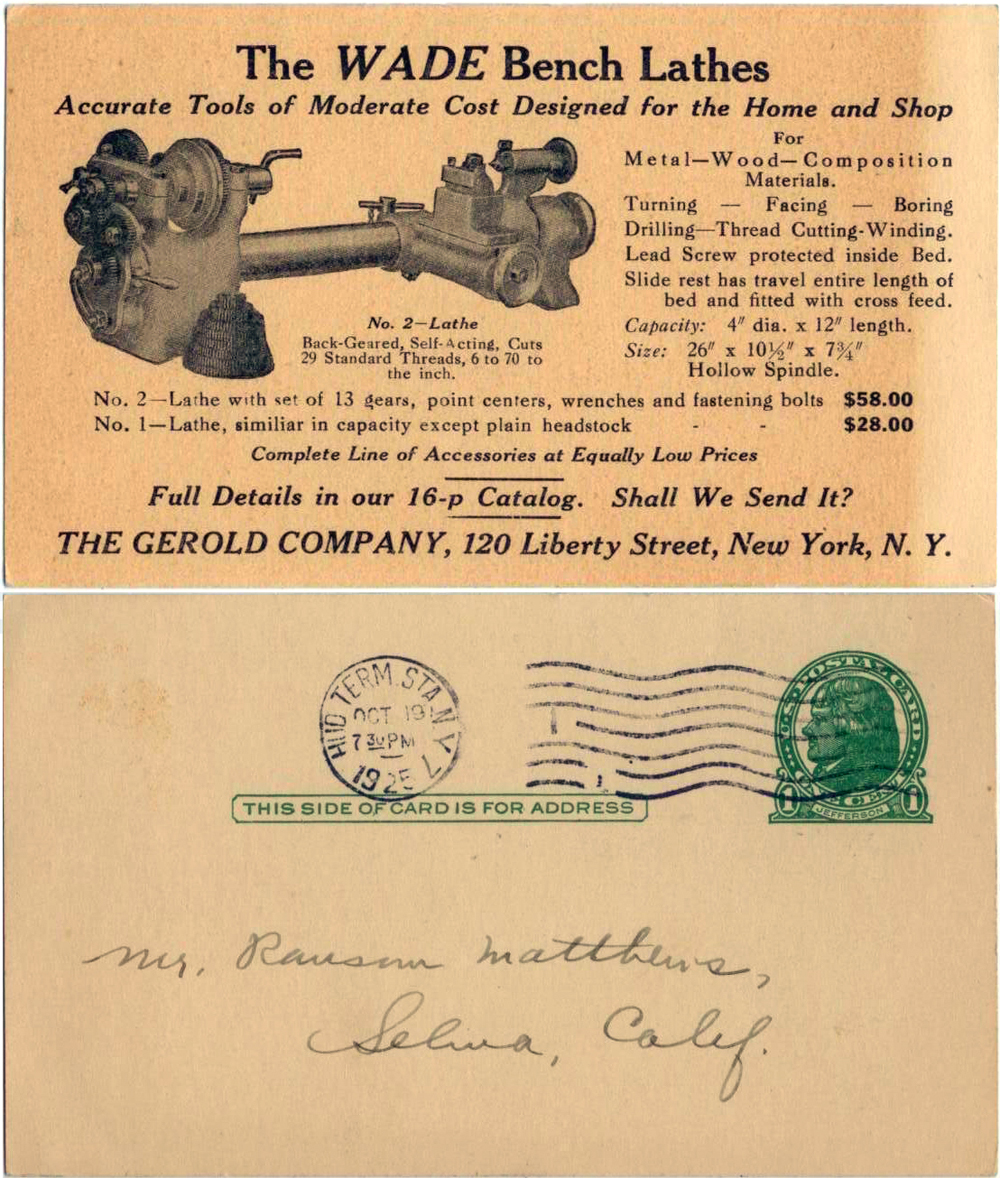 |
|
|
|
|
|
|
An American postcard advertising the Wade dated 19th October, 1925
|
|
|
|
|
|
|
|
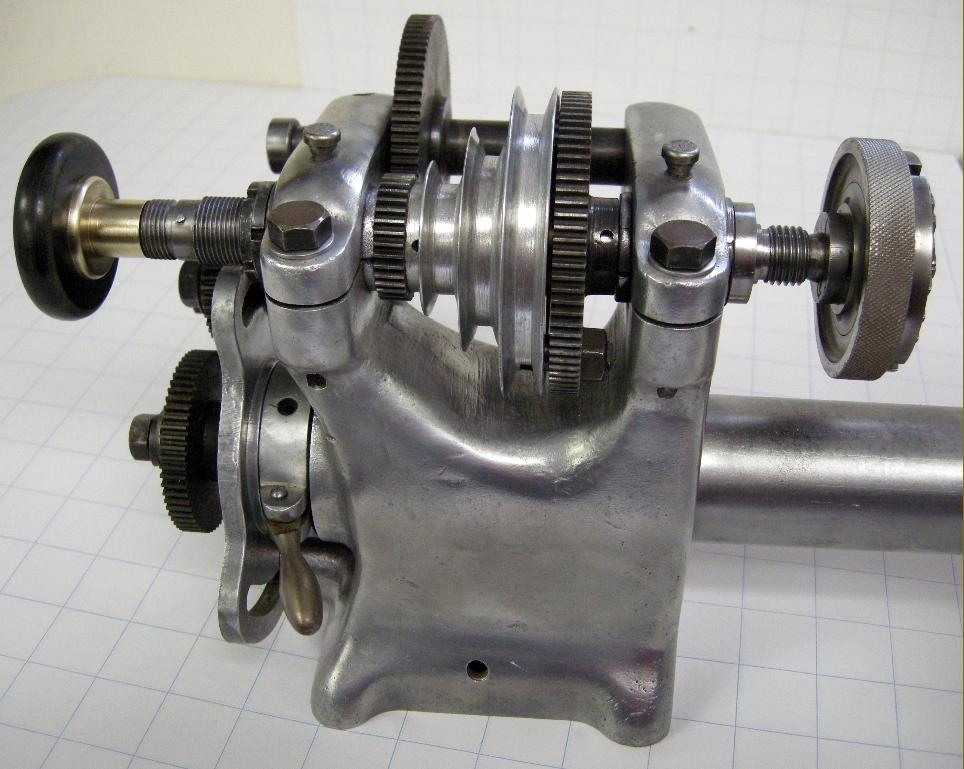 |
|
|
|
|
|
|
Backgeared and screwcutting stock
|
|
|
|
|
|
|
|
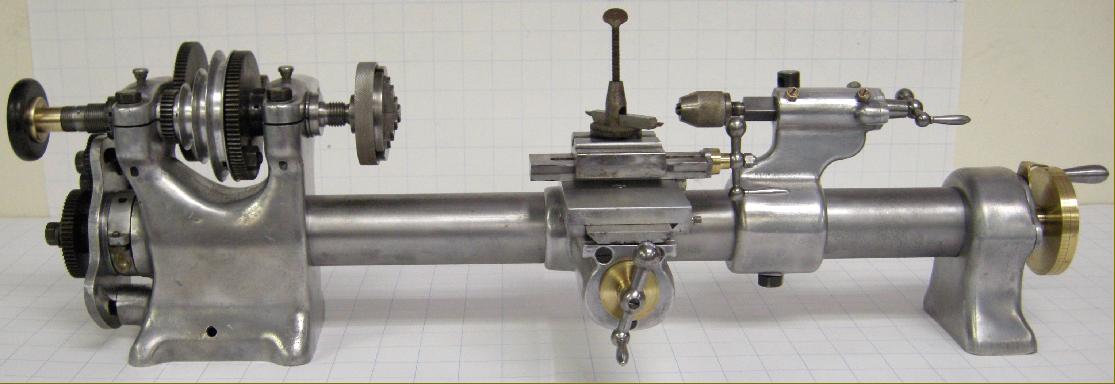 |
|
|
|
|
|
Additional pictures of this fine example can be seen at the bottom of the page (and here)
|
|
|
|
|
|
|
|
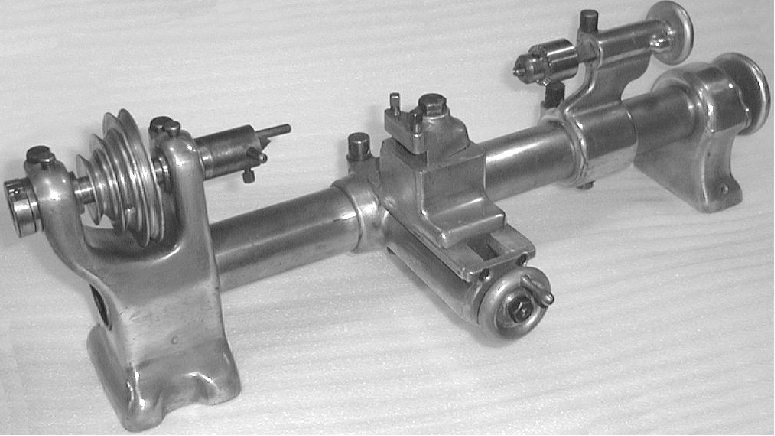 |
|
|
|
|
|
|
The "No. 1" Plain-turning version of the Wade CAV lathe.
|
|
|
|
|
|
|
|
|
|
|
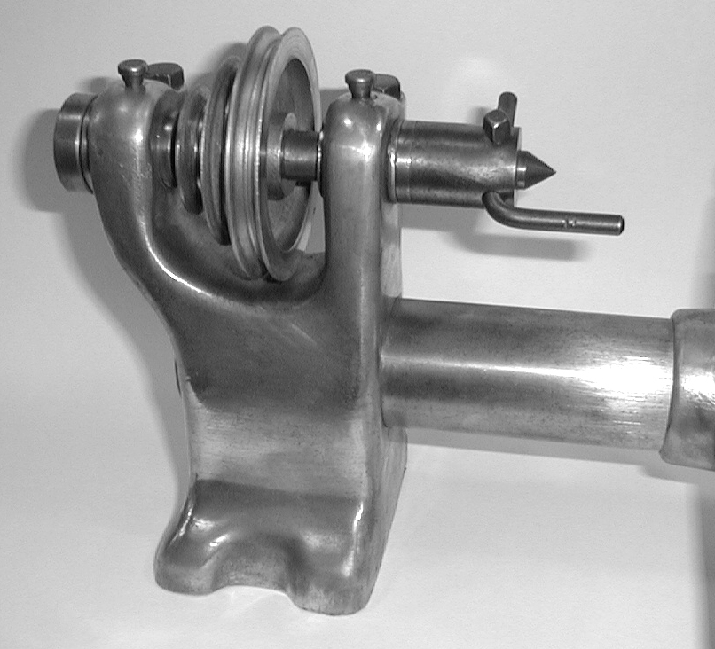 |
|
|
|
|
|
|
The small diameter of the headstock spindle meant that there was no room to machine a taper in its nose to accept a centre, instead, a screw-on boss was used (a device frequently used on light, amateur lathes of the 1800s) which had sufficient diameter to carry a short No. 1 Morse taper centre and, at the same time, act as a simple form of drive plate for between-centres work.
|
|
|
|
|
|
|
|
|
|
|
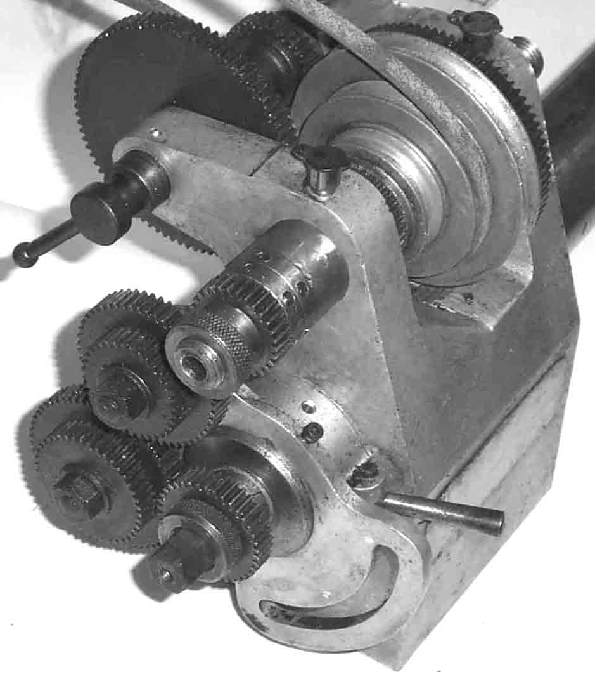 |
|
|
|
|
|
|
The distinctly different and far more robust "flat-faced" headstock of the late-model "No. 2" backgeared and screwcutting model.
|
|
|
|
|
|
|
|
|
|
|
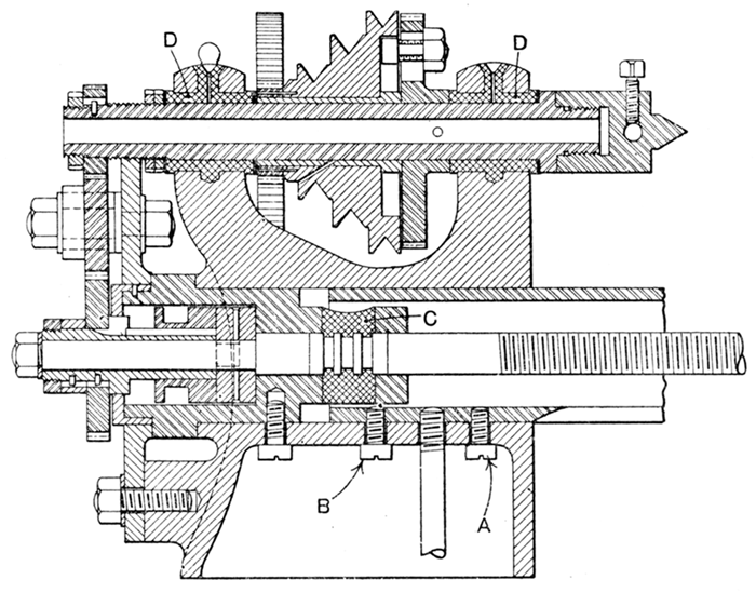 |
|
|
|
|
|
|
Section through the headstock, bed and changewheels of the earlier backgeared and screwcutting No. 2 lathe. Note the headstock bearings--the drawing clearly showing them to have been "poured in"
|
|
|
|
|
|
|
|
|
|
|
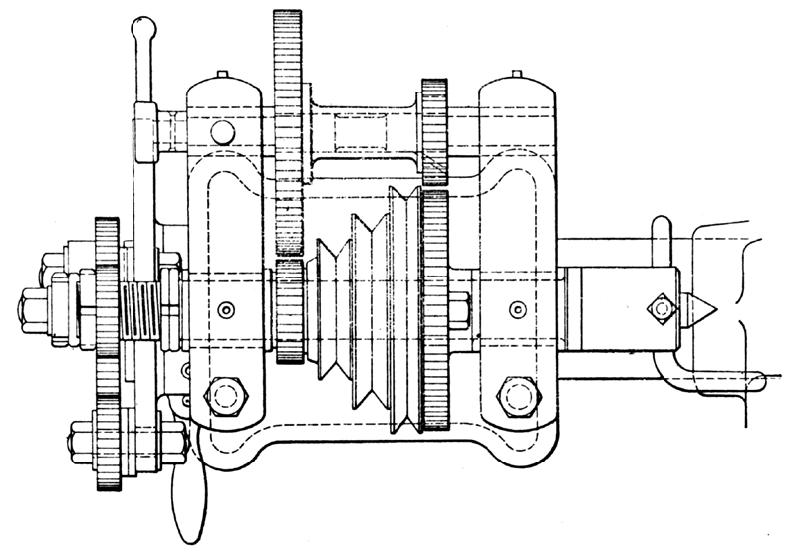 |
|
|
|
|
|
|
Plan section through the headstock of the earlier No. 2 Lathe
|
|
|
|
|
|
|
|
|
|
|
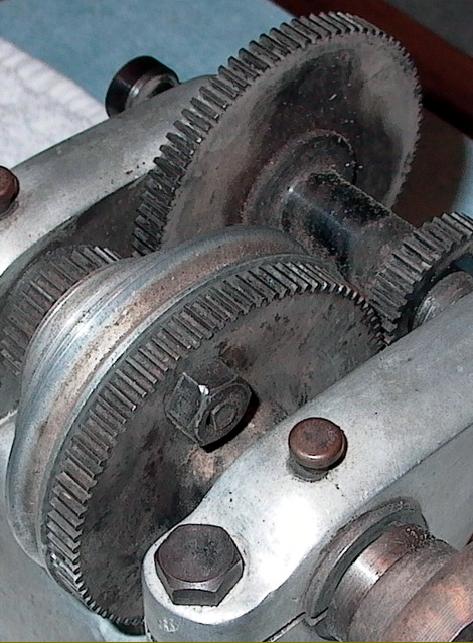 |
|
|
|
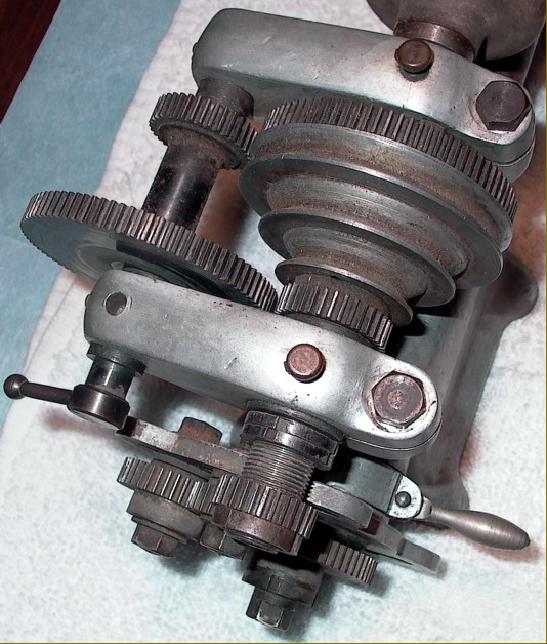 |
|
|
|
|
|
|
|
|
|
|
Original and unmodified backgeared and screwcutting headstock of the early type - a neat installation in a confined space
|
|
|
|
|
|
|
|
|
|
|
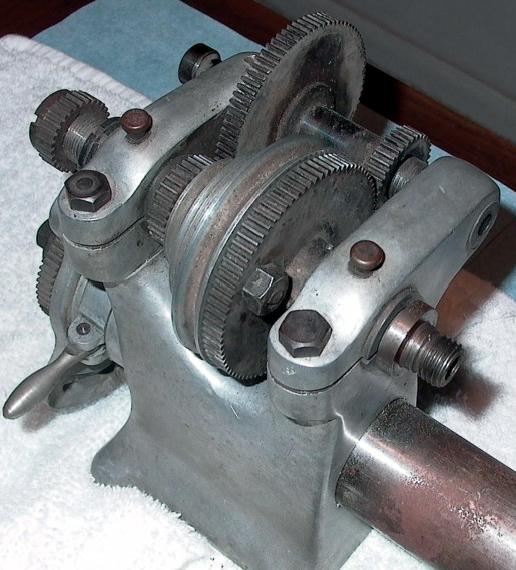 |
|
|
|
|
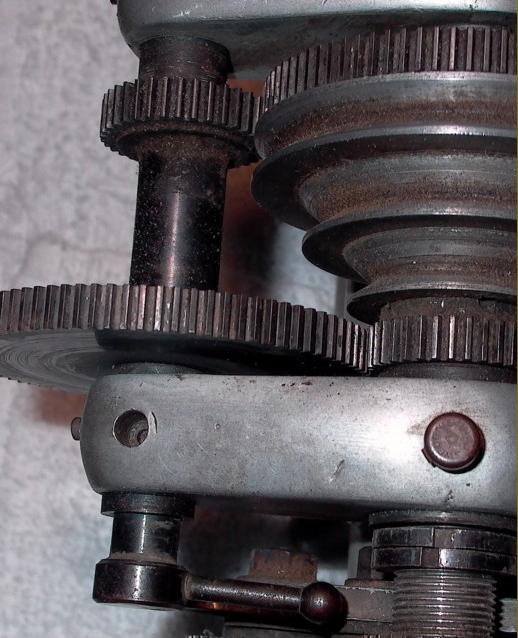 |
|
|
|
|
|
|
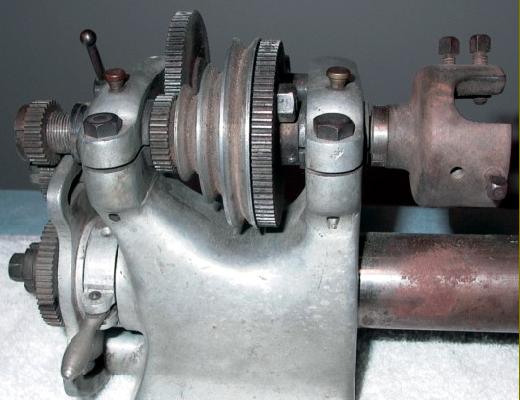 |
|
|
|
|
|
|
|
|
|
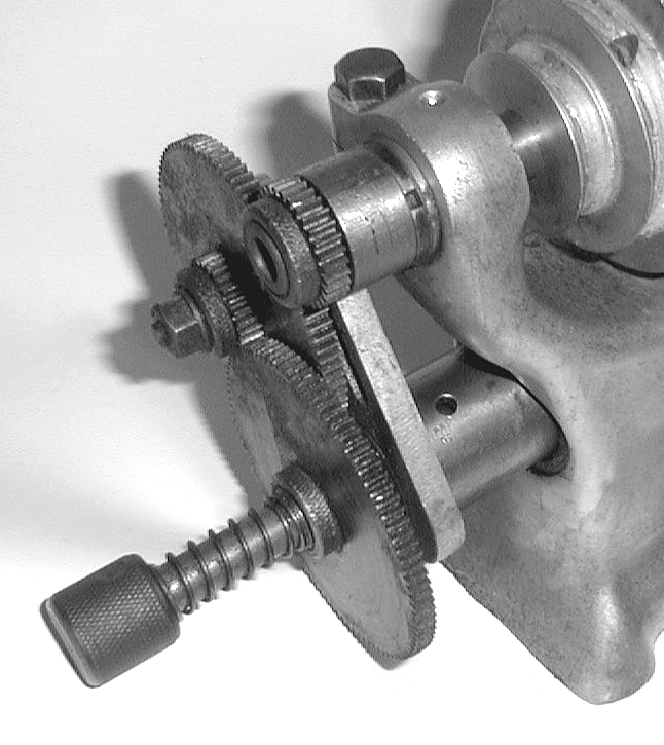 |
|
|
|
|
|
|
|
|
In order to give the standard lathe a power feed, and the possibility of screwcutting, a very-well constructed unit (Provisional Patent 10988) was made by Aird & Company of Brighton. The assembly plugged into the end of the bed and was located by a single bolt, tapped into the underneath of the bed where it passed through the headstock casting. Some means of quickly engaging and disengaging the drive was required, and the solution, eminently simple and practical, was to arrange for a spring-loaded plunger to engage the drive, via a half-dog on the end of the centre shaft; to keep the cut going however, the knurled wheel had to be held in, releasing it caused the drive to immediately stop. The screwcutting attachment provided by the makers included a well-engineered positive dog clutch, operated by a lever positioned between the end of the bed and the banjo arm. By using combinations of the three slots on the end bracket, and the two supplied studs, it was possible to obtain a multitude of drive ratios to the leadscrew - however, screwcutting would have been difficult without a backgear assembly, and only the use of a modified countershaft would have reduced the spindle speeds to a level where a thread could be safely generated. To fit the assembly a longer pain headstock spindle was required to carry the drive gear, and this was included in the kit of parts supplied with the accessory..
|
|
|
|
|
|
|
|
|
|
|
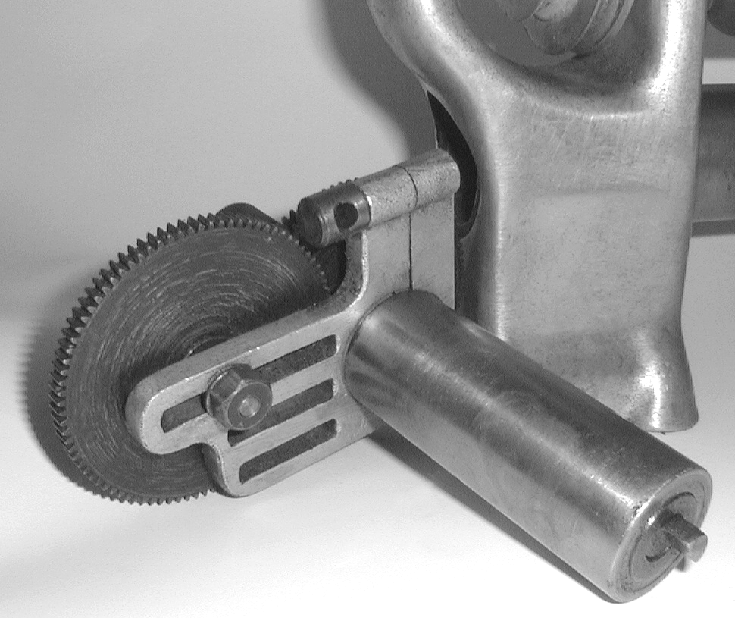 |
|
|
|
|
|
|
The three slots to mount the changewheels and the "half-dog" on the end of the feed shaft are clearly visible
|
|
|
|
|
|
|
|
|
|
|
|
|
|
|
|
|
|
|