 |
 |
 |
 |
 |
 |
 |
 |
 |
 |
 |
 |
 |
 |
 |
 |
 |
 |
 |
 |
 |
 |
 |
 |
 |
 |
 |
 |
 |
 |
 |
 |
 |
 |
 |
 |
 |
 |
 |
 |
 |
|
|
|
|
|
|
|
|
|
|
|
|
|
|
|
|
|
|
|
|
|
|
|
|
|
|
|
|
|
|
|
|
|
|
|
|
|
|
|
|
|
|
|
|
email: tony@lathes.co.uk Home Machine Tool Archive Machine-tools Sale & Wanted Machine Tool Manuals Catalogues Belts Books Accessories
Vison Tool & Cutter Grinder
An operating Manual and catalogue set is available for Vision Tool & Cutter Grinder
Manufactured by D. Vinell & Son, Ltd. at their Hadlow Stair Engineering Works in Tonbrige, Kent, early (Mk. 1) versions of the Vision tool and cutter grinder appear to have been sold through the exclusive agency of the Stedall Machine Tool Company of 145 - 157 St. John Street, London, E.C.1. Sales spanned from the 1930s until the 1960s, with a later (Mk. 2) model marketed directly by the makers. Although the machine has been identified in the two forms mentioned - Mk. 1 and Mk. 2 - there may have been others; however, both were exceptionally well made and capable of handling a wide range of tool and cutter grinding jobs. On early models the twin-T-slot, swivelling 32" x 3.75" worktable sat on a sub-base sliding table, the latter's longitudinal movement being operated through rack-and-pinion gearing by a front-facing handwheel fitted with a long lever, adjustable into any one of six positions - the design allowing the operator to select either slow or rapid movements through a maximum travel of 19" (though as an option a 38" table could be provided with a travel of 25 inches). With its swivel boss graduated 50° each side of central, when fitted with the maker's standard centres the standard worktable could accept jobs up to 18" long and 10" in diameter (or 24 inches long with the bigger table). At the left-hand end of the table was a small graduated dial, used to obtain very fine sub-divisions of the degree marking when grinding tapers and leads. Arranged at the back of the machine was a vertical slideway, mounted on a swivelling base (with a graduation-degree scale marked 90° each side of central) that carried the grinding wheel spindle and a 1/4 h.p. 3-phase motor -drive from the latter being by a V-belt covered by an aluminium guard. Running at speeds between 3500 and 6000 r.p.m., the double-ended, No. 3 Morse taper spindle could carry a wheel at each end - adjustable guards being provided so as to cover the different diameters. At the top of the column was a glass-covered chart giving the clearance values for straight and cup wheels. Supplied with each new machine was a universal motorised "workhead" able to be rotated through 360° in two planes with, in its top surface, a deep V-grooved flanked by two T-slots. Its spindle was threaded on one end to mount chucks and faceplates and also machined, on both ends, with a V-pulley groove to pick up the drive from the 1/4 h.p. motor - the smaller of the two pulleys gave 320 r.p.m. the larger 600 r.p.m. In order to increase its versatility the motor and its mounting platform could be removed, leaving just the bare unit in place. Other accessories included as standard were a spring-loaded tailstock; a universal tool rest; height gauge; diamond holder; a basic spindle 1-inch in diameter, hardened and ground and complete with nut, plate and friction washer; a set of 4 spindle collars; one each of 1.125", 1.25" and 1.5" bushes to fit the spindle; a universal joint; a plain tooth rest with 2 blades and three bars; spring-loaded holders for end-mills; universal distance stop for end mills, one each of 15" x 1", 15" x 1.25" and 15" x 1.5" spindles to hold roller mills; one 5" x 0.5" x 0.5" dish wheel; one 3" x 1.25" x 0.5" flaring cup wheel - and a set of spanners. Optional extras listed were: 4-inch 3-jaw self-centring chuck mounted on a backplate; 6-inch independent 4-jaw chuck on a backplate; T-slotted faceplate; dividing plates; Low-voltage lighting equipment; internal grinding attachment with an extra-long grinding quill for surface grinding work up to 6-inches wide; an attachment on the workhead for dead-centre grinding; a draw-bar collet attachment with a collet set up to 0.5" capacity and concertina guards over the vertical ways that carried the spindle assembly. Used in conjunction with the motorised workhead (which turned in the opposite direct to the job to give the necessary high speeds required on small-diameter work) the internal grinding attachment was fixed to the underside of the grinding motor plate and turned by a flat belt from an integral countershaft unit - this being driven by taking the V-belt from the motor to spindle drive and swapping it over. The countershaft spindle ran in ball races held in an eccentric housing, the rotation of which was used to tension the belt. With its quill easily removed, the attachment could be left in position permanently with jobs from 3/8" to 4" diameter and up to 4" long able to be ground. Late model Vison grinders, though they worked in exactly the same way and had the same size of drive motors, were completely redesigned with the main changes being to the stand (this becoming a separate casting no longer integral with the body of the grinder), the mounting of the spindle drive assembly and the size of the workhead spindle - this being increased from a No. 3 to a No. 4 Morse taper. The spindle and motor, instead of being carried on tall, flat-faced vertical flat ways, were instead fitted to a bellows-protected, large-diameter tube that emerged from behind the table with lift through it 9.25" of travel by a screw and bronze nut (adjustable to remove backlash) and control by a handwheel fitted with a large diameter micrometer dial. While the distance between centres was the same as for the Mk. 1 (18" and, optionally, 24"), the centre height of the workhead and its tailstock were increased slightly to allow jobs up to 11 inches in diameter to be mounted. Although the exact specification of the table assembly on the Mk. 1 is not known, on the Mk. 2 it ran on needle roller races, providing an exceptionally smooth and easy travel. Standard equipment and accessories were much as for the Mk. 1 but with the addition of equipment to allow wet grinding and a dust extraction unit..
|
|
|
|
|
|
|
|
|
|
|
|
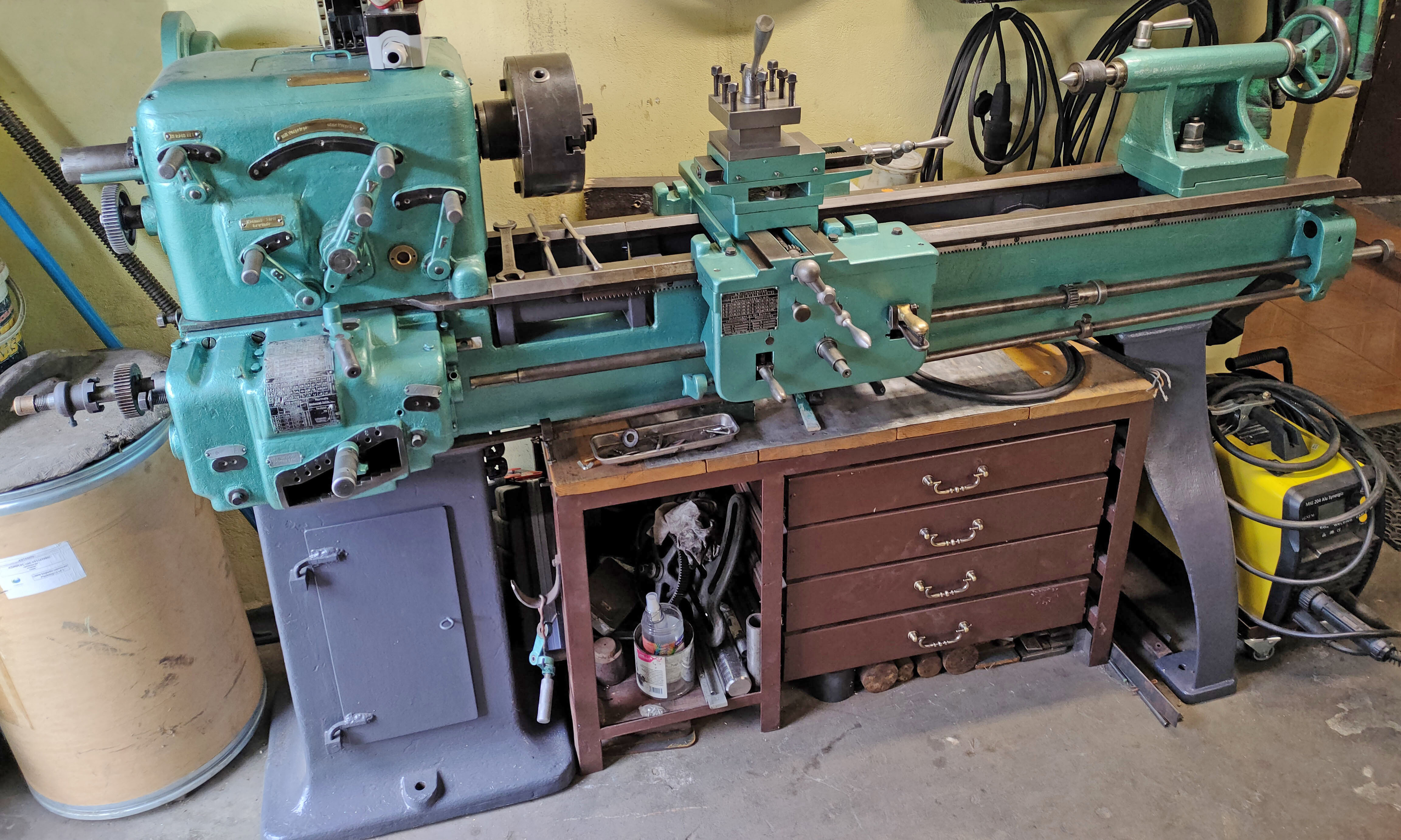 |
|
|
|
|
|
|
|
|
|
The "Vision" tool & Cutter Grinder as sold during the 1950s and 1960s
|
|
|
|
|
|
|
|
|
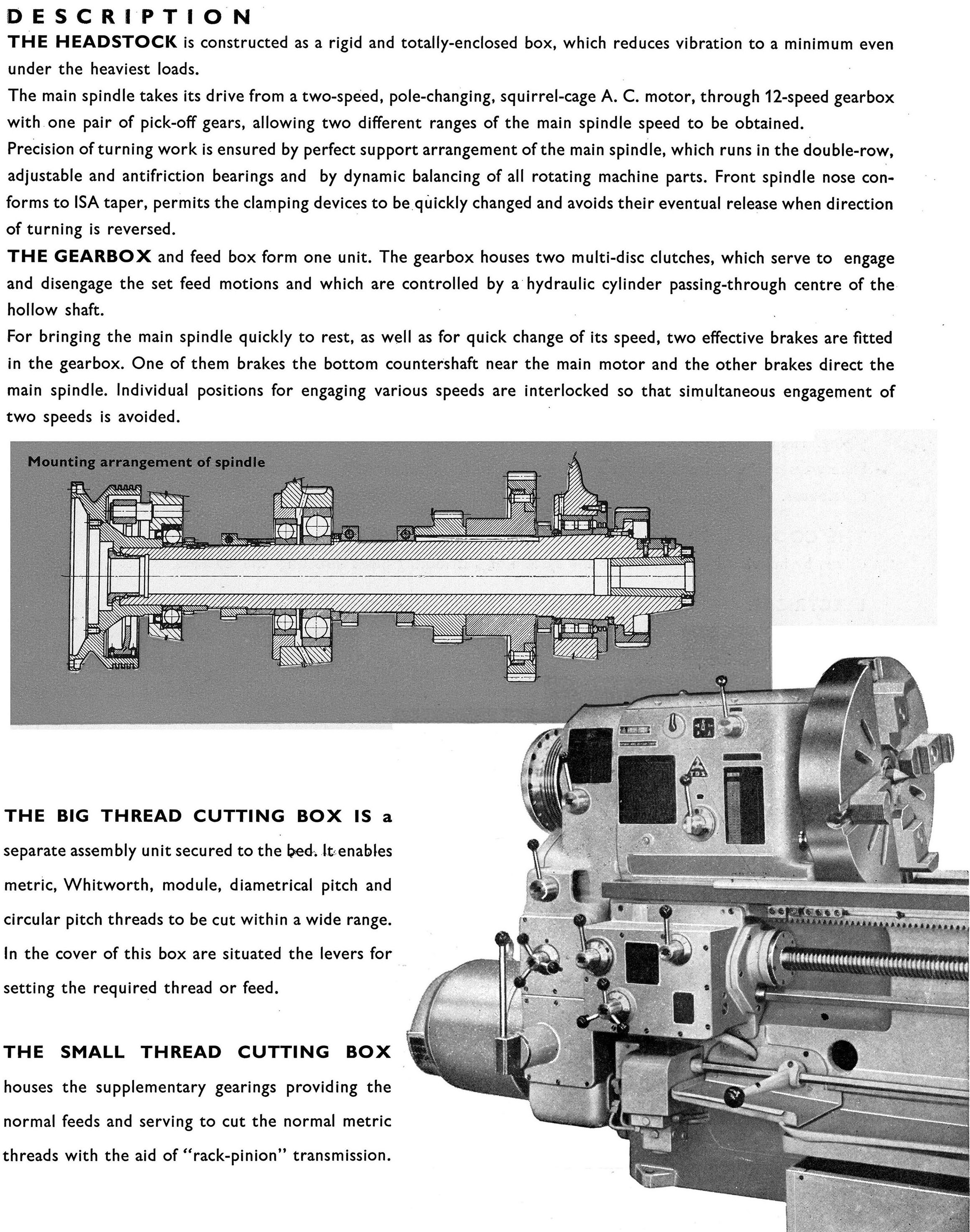 |
|
|
|
|
|
|
|
|
|
The "Vision" tool & Cutter Grinder as sold during the 1930s and 1940s
|
|
|
|
|
|
|
|
|
 |
|
|
|
|
|
|
|
Early Model: Grinding of a formed-tooth cutter used for the generation of gear teeth. With the motor drive assembly removed, an indexing attachment was secured by two T-bolts to the top face of the Universal Workhead with a spring loaded hand lever causing a steel pin to be pressed down firmly into a dividing plate. Three plates were supplied with the attachment (with others available) and held on by two Allen screws that went into the front face of the spindle's V-pulley. The set enabled divisions of 2, 3, 4, 5, 6, 7, 9, 10, 12, 14, 15, 18, 28, 30 and 36 to be achieved. Note, facing forwards at the side of the indexing unit, a knurled-edge wheel - this was calibrated in thousandths of an inch and used for feeding the cutter radially into the flat side of the mounted saucer wheel.
|
|
|
|
|
|
|
|
|
|
|
 |
|
|
|
|
|
|
|
Grinding a side and face cutter using a saucer wheel.
|
|
|
|
|
|
|
|
|
|
|
 |
|
|
|
|
|
|
|
Sides of a side and face cutter being ground with a cup wheel. The workhead has been tipped to give the desired angle of clearance.
|
|
|
|
|
|
|
|
|
|
|
 |
|
|
|
|
Grinding of the end teeth on a parallel shank end mill. The cutter is held in the V-groove formed in the top of the workhead and held down by a spring-loaded in the front fixing. The rear clamp shows how the endwise location was obtained by the use of a floating pointer. The head is tipped to give the correct clearance.
|
|
|
|
|
|
|
|
|
 |
|
|
|
|
|
|
|
A "slab" or "roller" milling cutter being sharpened with a saucer wheel using the plain tooth-rest set to the helix angle of the cutter tooth
|
|
|
|
|
|
|
|
|
|
|
 |
|
|
|
|
|
|
|
Internal grinding attachment. Used in conjunction with the motorised workhead (which tuned in the opposite direct to the job to give the necessary high speeds required on small-diameter work) the internal grinding attachment was fixed to the underside of the grinding motor plate and turned by a flat belt from an integral countershaft unit - this being driven by taking the V-belt from the motor to spindle drive and swapping it over. The countershaft spindle ran in ball races held in an eccentric housing, the rotation of which was used to tension the belt. With its quill easily removed, the attachment could left in position permanently with jobs from 3/8" to 4" diameter and up to 4" long able to be ground. Note the use of a 3-jaw chuck screwed to the nose of the workhead spindle.
|
|
|
|
|
|
|
|
|
|
|
 |
|
|
|
|
|
|
|
The Vison being used as a cylindrical grinder with the job held between centres - the tailstock having a spring-loaded spindle. The motorised workhead spun the work in one direction while the grinding wheel revolved in the opposite.
|
|
|
|
|
|
|
|
|
|
|
 |
|
|
|
|
|
|
|
Screw-on, T-slotted faceplate
|
|
|
|
|
|
|
|
|
|
|
|
|
|
|
|
 |
|
|
|
|
|
|
|
Late-model Vision showing the spindle head carried on a tube that emerged from the back of the main casting
|
|
|
|
|
|
|
|
|
|
|
 |
|
|
|
 |
|
|
|
|
|
 |
|
 |
|
|
|
|
|
 |
|
|
|
|
|
 |
|
|
|
|
|
 |
|
|
|
|
|
|