 |
 |
 |
 |
 |
 |
 |
 |
 |
 |
 |
 |
 |
 |
 |
 |
 |
 |
 |
 |
 |
 |
 |
 |
 |
|
|
|
|
|
|
|
|
|
|
|
|
|
|
|
|
|
|
|
|
|
|
|
|
|
|
|
|
|
|
|
email: tony@lathes.co.uk Home Machine Tool Archive Machine-tools Sale & Wanted Machine Tool Manuals Catalogues Belts Books Accessories
Sunderland Gear Planers
Operation manuals are available for Sunderland gear machines
Sunderland Models Nos. 5B and 5C
Sunderland Models Nos. 16 and 16S
Sunderland Models Nos. 19 and 19s
Sunderland Models Nos. 23 and 26
Sunderland Models Nos. 27S, 27DH & 27SDH
Sunderland Models Nos. 30S. 30DH & 30SDH
Sunderland Models Nos. 35S, 35DH & 35SDH
Sunderland Models G150 Series
Sunderland Models G300 Series
All Sunderland gear-planing machines work on a principle established in the early years of the 20th century by the inventor and patentee Sam Sunderland of Keighley in Yorkshire, England. Sunderland realised that if the principle of the involute curve could be applied to a gear-cutting machine, the gears produced would (to simplify matters) always mesh perfectly and so produce a smooth and consistent delivery of power from one to the other. Even better, when the gears (either spur or helical) were allowed the necessary clearances to accommodate expansion due to heat and the avoidance of excessive friction, the involute rule still held and the meshing remained unchanged. The practical solution lay in his realising that a rack (in effect a gear laid out in a straight line) would always mesh perfectly with a gear of the correct specification, if the rack were to be made be made of a cutting steel it could generate a gear with the correct involute form - but not only that, in normal use only a small stock of cutters would be needed as each could cut any number of teeth providing they were of the same pitch and pressure angle (in comparison, ordinary "form" cutters are limited to a small range of teeth and dozens are required to cover the needs of a commercial workshop). Possibly the easiest way to understand the Sunderland method is to imagine a gear blank in a soft material being rolled backwards and forwards, under pressure, along a rack until the tooth form of the rack is reproduced in the blank - the analogy being that as the rack (cutter) is planing the blank to produce teeth and spaces, the blank is being rolled along the rack and the tooth form generated directly. In addition, even when blanks are over or under-size they can still be cut so as to run together correctly - an example being when stronger teeth are required by either increasing the outside diameter of a gear or the "addendum". As Sunderland wrote, "….uniformity in the shape of the teeth is obtained as perfectly as possible by a commercial method and all gears that are cut by the same cutter will gear correctly with one another." The easiest way to understand the method is to watch it in action: here are two rather shaky videos showing a Sunderland No. 19 and 27SDH at work. Once established, the Sunderland Company (soon to became part of J.Parkinson & Son, the Shipley-based milling machine makers) called their system "rack generation of involute gears" and employed a hardened and ground high-speed steel cutter (or cutters) having straight-sided, rack-shaped teeth that, in operation, are made to reciprocate parallel with the axis of the gear being cut while simultaneously travelling at a tangent to its pitch circle - the gear rotating slowly at the same linear speed on the pitch line. To keep the length of the rack cutters down, after the traverse of one or more pitches this movement is stopped and the cutter slide automatically withdrawn from the gear teeth at the end of the pitch movement - this action permitting the cutter to step back one or more teeth on the partially-formed blank. The cutter is then automatically re-engaged and the generating motion resumed. Thus, on its cutting stroke, the cutter is in contact with several teeth at the same time - but with a different part of each individual tooth - and so planes over a comparatively narrow band at every stroke. With a different part of each tooth submitted to the action of the cutter at every stroke, every tooth is acted upon by the same teeth in the cutter in exactly the same way, the result being the production of a uniformly shaped gear. In addition, by using multiple or gang loading of blanks loaded to the full capacity of the machine, a very high rate of production can be achieved.Based on simplicity and what the makers called (as a reference to the involute principle) "mathematical accuracy", the design of a Sunderland gear machine calls for a gear blank (or blanks) to be mounted on a horizontal arbor held in the work spindle at one end and supported by a sliding pedestal at the other. Two setting adjustments are available: the cutter headstock can be slid along the bed to suit various gear diameters and the cutter box moved along the cutter slide to suit the axial position of the blank. For spur and single helical gears an infinetly variable adjustment of stroke length, to suit the width of the blank, is made on the crank-driven cutter slide while the hand-wheel, used to move the headstock along the bed, is also used to set the feed depth with the setting, once made, locked. The rate of feed - stated as the number of strokes of the cutter slide per pitch movement - is selected by a dial on the feed gear box with a lever to stop and start the feed as required. Changing the setting of cutting strokes per minute is varied by easily-changed pick-off gears mounted on fixed centres. A train of "pitch changewheels" are arranged to suit the pitch of the rack cutter and the particular gear to be cut and "division changewheels" selected to give the number of teeth required. Charts, matched to the capacity of the machine, are supplied to show the setting of changewheels for division and for all standard pitches D.P., C.P. and Module and provision made to rotate the work spindle to check the truth of mounting. A counter is usually fitted, complete with an automatic knock-off device, to stop the mechanism on completion of the cut. Lubrication provision varied throughout the decades with, on early models usually a combination of automatic and one-shot hand-operated plunger pumps. Later models, including the G Series built in the 1970s and 1980s, used two automatic centralised ststems were employed, one to feed oil continiously to the cutter head and feed gearboxes, the other an intermittant arrangement that lubricated the workspindle and various slideways. On the later machines the machine was interlocked with an oil pressure switch that would not allow the main motor to either start, or continue running, if the pressure was too low. As all Sunderland gear planing machines work on the same principle, the maker's original very detailed instruction manual can be used as guide for the setting up and use of all models, though individual publications were also prepared for some types..
|
|
|
|
|
|
|
|
|
|
|
|
|
|
|
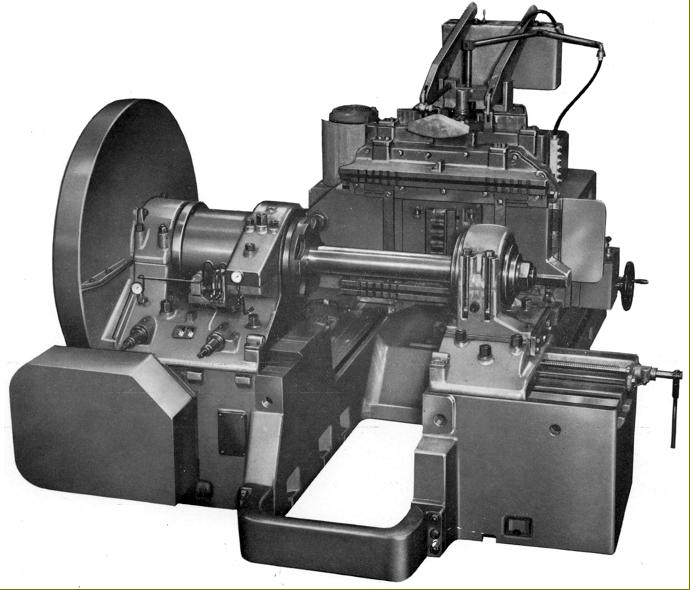 |
|
|
|
|
|
|
Typical Sunderland gear-planing machine
|
|
|
|
|
|
|
|
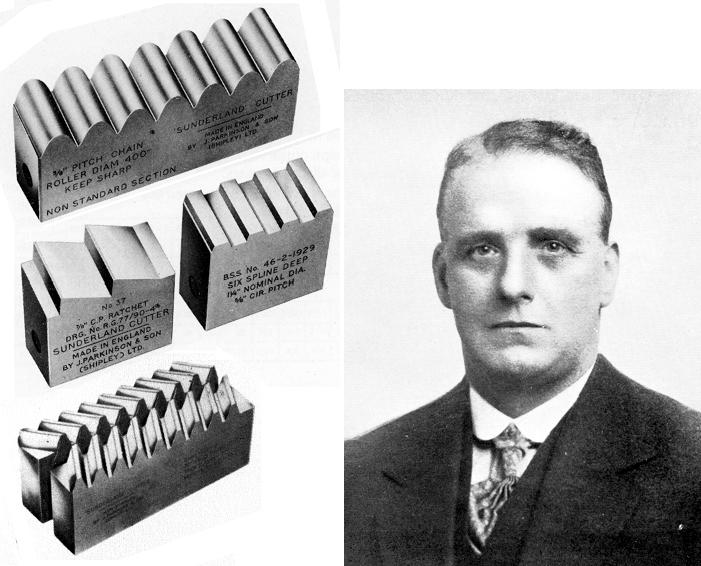 |
|
|
|
|
|
|
Sunderland high-speed steel rack cutters Sam Sunderland
|
|
|
|
|
|
|
|
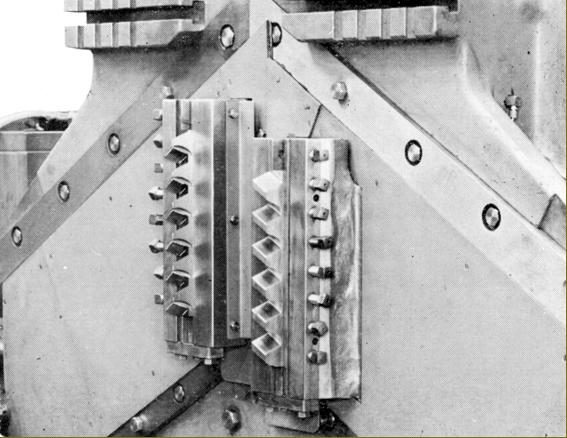 |
|
|
|
|
|
|
Arrangement of rack cutters to produce double-helix gears. These cutters could be mounted on the model 16 and 19 machines - though Sunderland recommended, should continuous production of such gears be required, that a dedicated, double-helix only machine was used
|
|
|
|
|
|
|
|
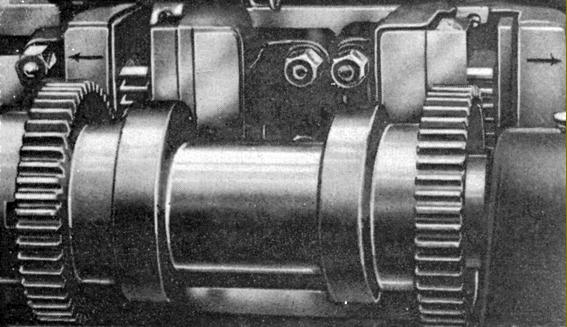 |
|
|
|
|
|
|
For higher rates of production if was possible, on some models of Sunderland gear cutters, to mount two cutter boxes side by side. If a gang of blanks were loaded on the arbour, each set would be separating by a distance piece or, in many cases, an additional mid-way support
|
|
|
|
|
|
|
|
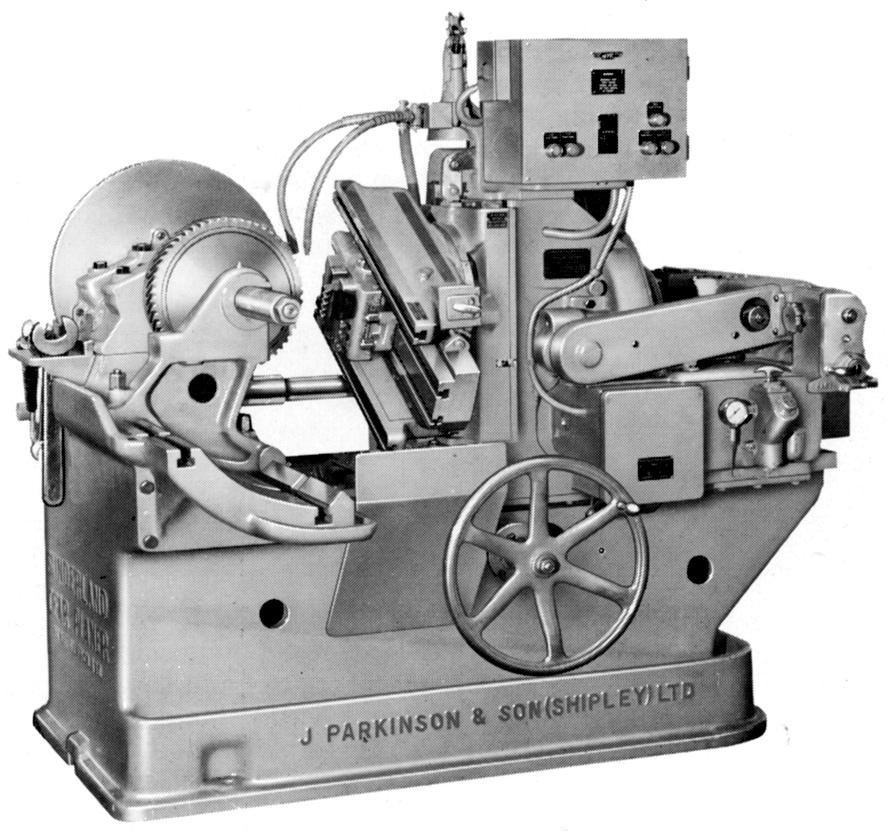 |
|
|
|
|
|
|
|
|
|
|
|
|
|
|
|
|
|
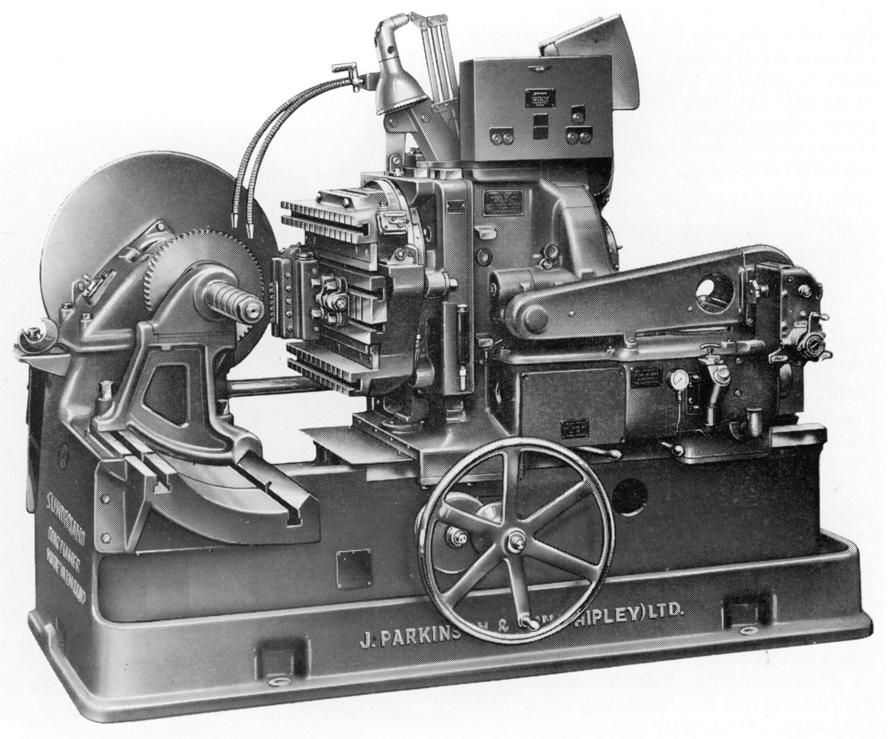 |
|
|
|
|
|
|
Sunderland Model No. 16 for cutting both spur and spiral gears and No. 16S for cutting spur gears only. Catalogue extract here
|
|
|
|
|
|
|
|
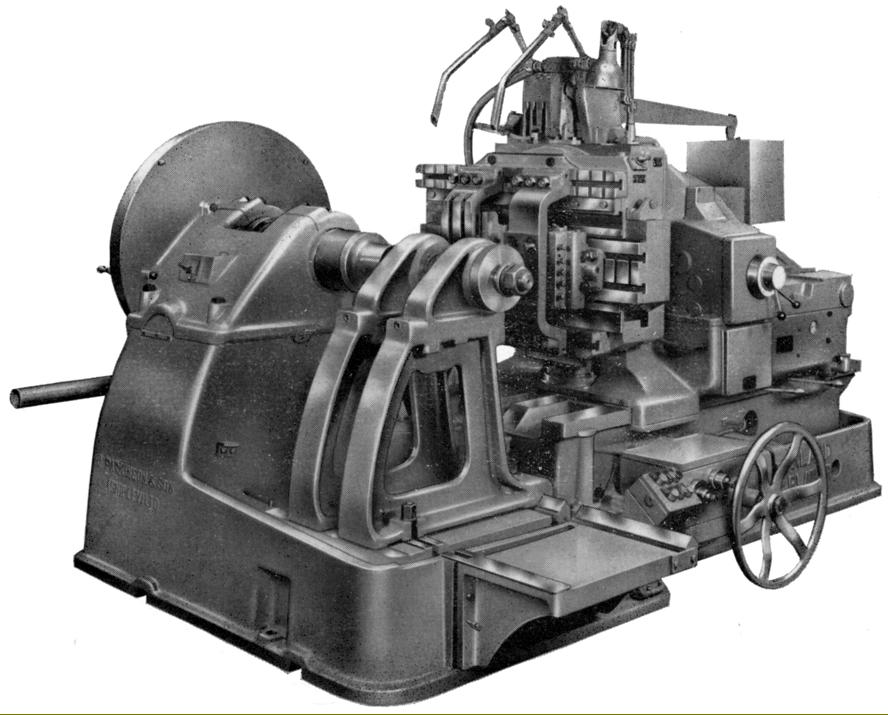 |
|
|
|
|
|
|
Sunderland Model No. 19 a medium capacity machine for spur and spiral gears and the No. 19s a model designed specifically for spur gears only , Catalogue extract here
|
|
|
|
|
|
|
|
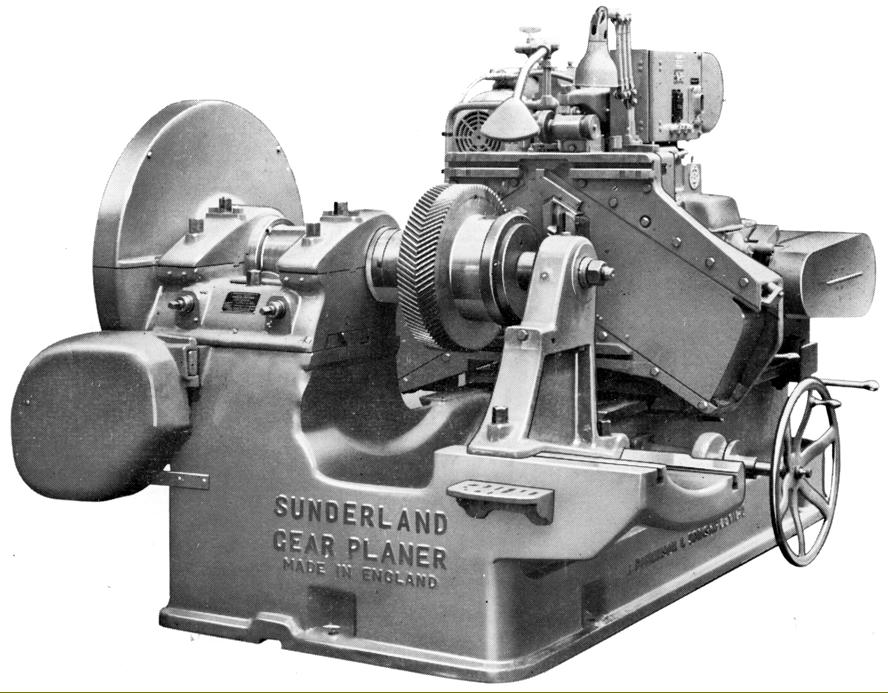 |
|
|
|
|
|
|
Sunderland Model 23 for double-helical gears and the No. 26, a larger machine for gears up to 52 inches in diameter Catalogue extract here
|
|
|
|
|
|
|
|
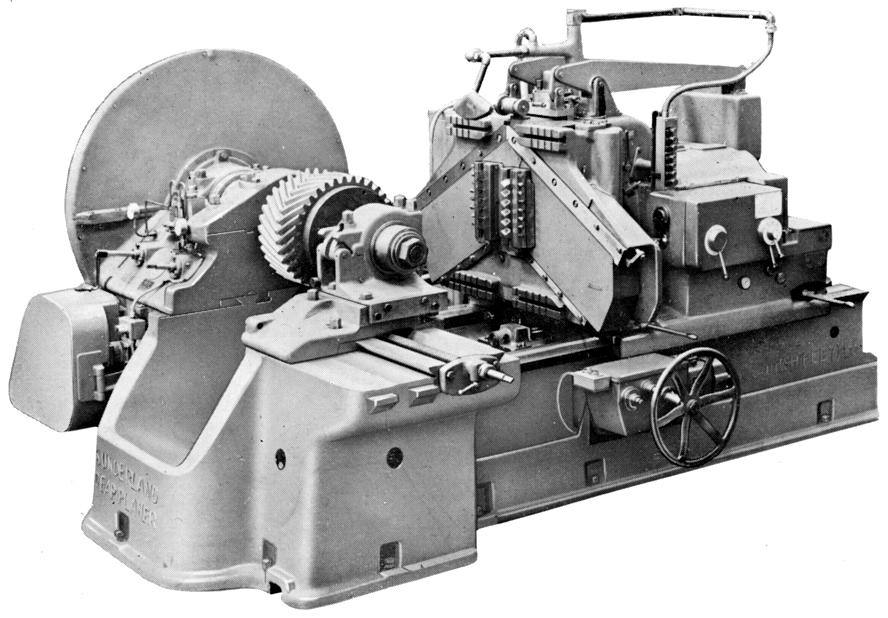 |
|
|
|
|
|
|
Sunderland Model 27S for spur gears only, the No. 27DH for double-helix gears only and the No. 27SDH for cutting both spur and double helix gears Catalogue extract here
|
|
|
|
|
|
|
|
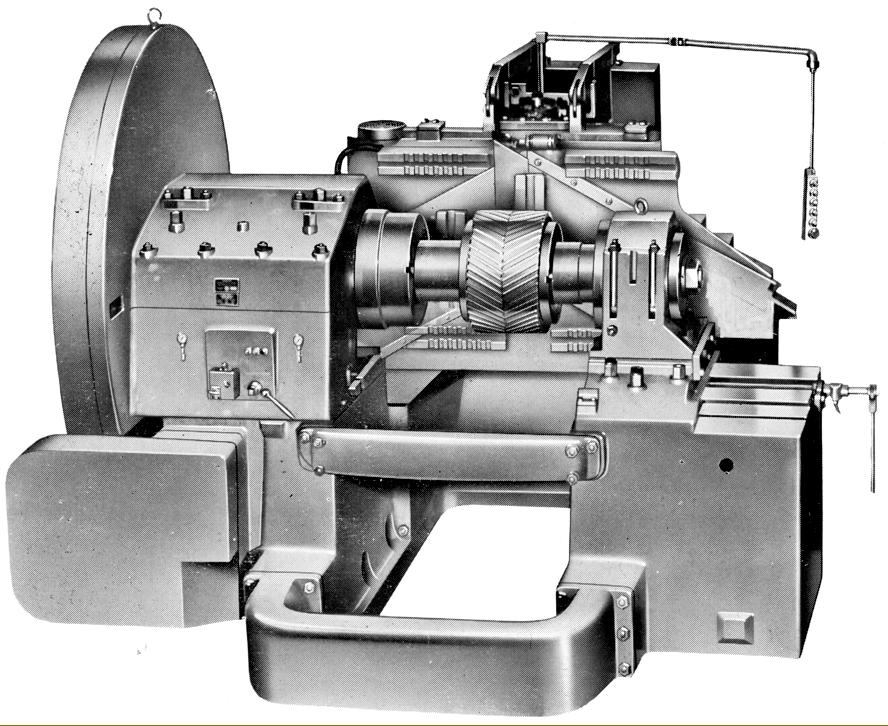 |
|
|
|
|
|
|
Sunderland Model No. 35S for spur gears only; the No. 35DH for double-helix gear only and the 36SDH that could cut both spur and double-helix gears. Catalogue extract here
|
|
|
|
|
|
|
|
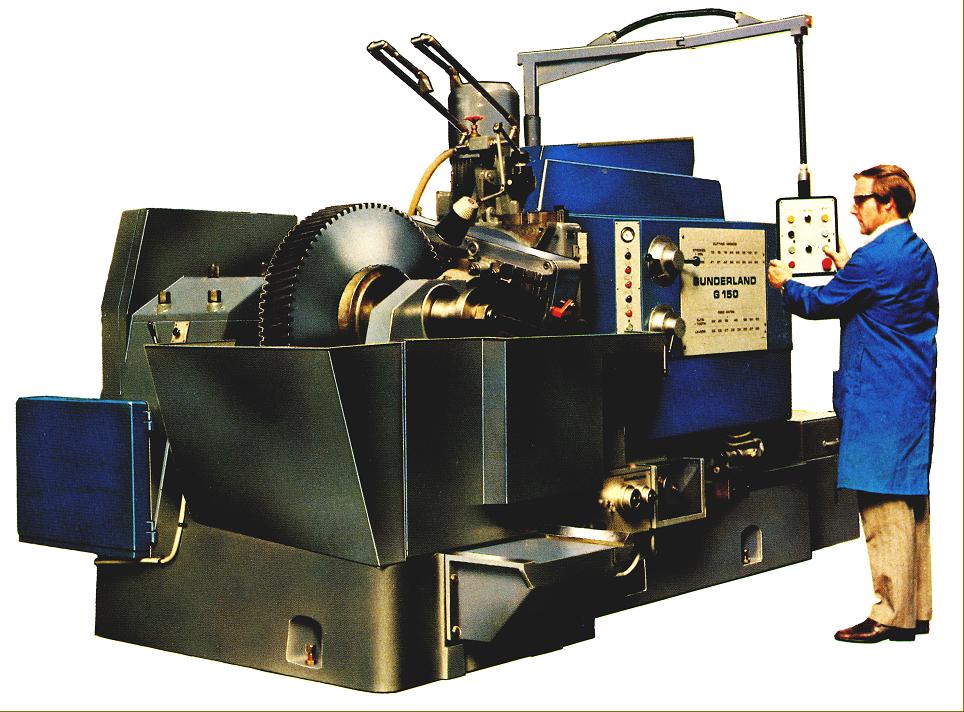 |
|
|
|
|
|
Sunderland G150, a replacement for the Models Nos. 219 and 26, the G150 could manufacture, with the necessary attachments, spur and both single and double helical gears. Design improvements concentrated upon increasing the machine's rate of output by automating the machining cycle and reducing set-up and changeover times. In addition to the auto-cycle facility, hydraulically operated in-feed, rapid traverse and cutter-head clamp release was provided. Main controls were moved to a walk-around pendant holding push-button and rotary switch that operated the main motor and hydraulically-powered in-feed and rapid-traverse actions. Other design improvements for quicker setting times included easily accessible change-gears, axially adjustable workhead, power rotation to the gear blank to facilitate checks for side-face run-out and concentricity and a new design of self-compensating cutter which, after sharpening, could be replaced without resetting the machine. A full specification chart can be found here
|
|
|
|
|
|
|
|
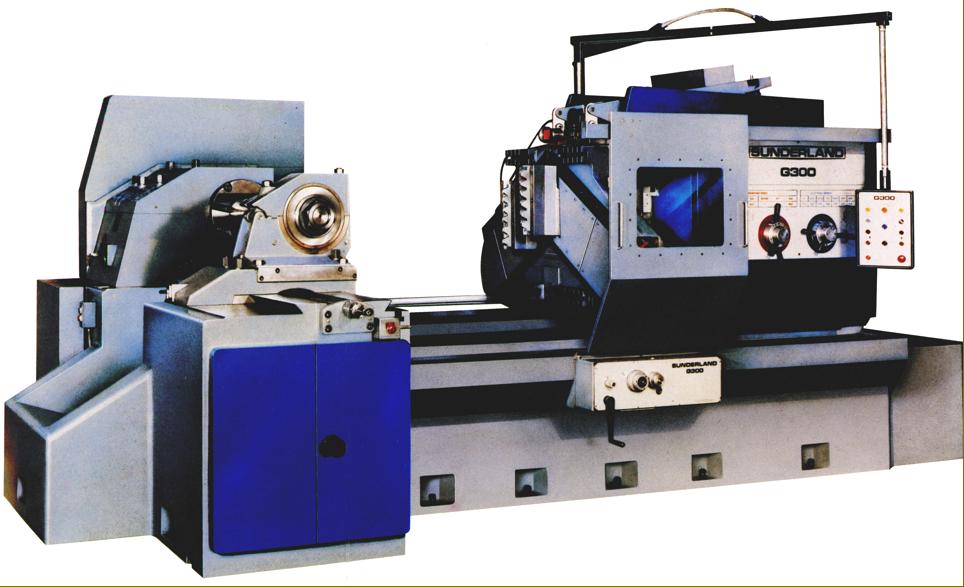 |
|
|
|
|
|
Sunderland G300, a replacement for the Model No. 27 the G300 could manufacture, with the necessary attachments, spur and both single and double helical gears. Controls were centralised with a walk-around pendant holding push-button and rotary switch that operated the main motor and hydraulically-powered in-feed and rapid-traverse actions. Other design improvements for quicker setting times included easily accessible change-gears, axially adjustable workhead, power rotation to the gear blank to facilitate checks for side-face run-out and concentricity and a new design of self-compensating cutter which, after sharpening, could be replaced without resetting the machine. A full specification chart can be found here
|
|
|
|
|
|
|
|
|
|
|
|
|
|
|
|