 |
 |
 |
 |
 |
 |
 |
 |
 |
 |
 |
 |
 |
 |
 |
 |
 |
 |
 |
 |
 |
 |
 |
 |
 |
 |
 |
 |
 |
 |
 |
 |
 |
 |
 |
 |
 |
 |
 |
 |
 |
 |
|
|
|
|
|
|
|
|
|
|
|
|
|
|
|
|
|
|
|
|
|
|
|
|
|
|
|
|
|
|
|
|
|
|
|
|
|
|
|
|
|
|
|
|
|
|
|
|
|
|
|
|
|
|
|
|
|
|
|
|
Long known for producing grinding machines of the highest quality, the Swiss firm of Fritz Studer is also active in the manufacture of machines for the setting of high-precision gauges and other measuring equipment. During the 1950s their Model RLS-300 (and larger RLS-400/1000) was offered for work to set and calibrate "snap" and other precision measuring gauges. In an engineering shop, a means of checking the dimensions of production work quickly is essential, with one of the more commonly used items for this task being the C-shaped "snap" and "go/no-go" gauges. While a snap gauge (as its name implies, it "snaps" over the dimension to be checked) can check only one tolerance - the two-ended go/no-go gauge can determine if a component lies between two upper and lower limits of tolerance - one end having a "go-gap" just above the acceptable size (say + 0.001") and the other end a "no-go" gap just below (say - 0.001"). If the part being tested passes through the "go" end, but not through the "no go", it's within the required limits. Obviously, the gauges used are made to very fine limits indeed and need to have their accuracy maintained - this latter process being the purpose of the Studer "Snap Gauge" grinding machine. Designed for preparing - by first grinding and then lapping the "anvil" faces of gauges - it could handle items with a capacity up to 8" (200 mm) while, in addition, also be employed to grind distance gauges and general workpieces that needed to be made parallel on two facing surfaces. Simple in concept, but built to the very highest standards of accuracy, the machine carried its grinding and lapping wheels side by side, thus enabling work to be carried out at a single setting. The accuracy achieved depended, to some extent, upon an experienced operator who, with suitable care, could achieve results within the range of plus or minus 0.000040" (0.001 mm). Continued below:
|
|
|
|
|
|
|
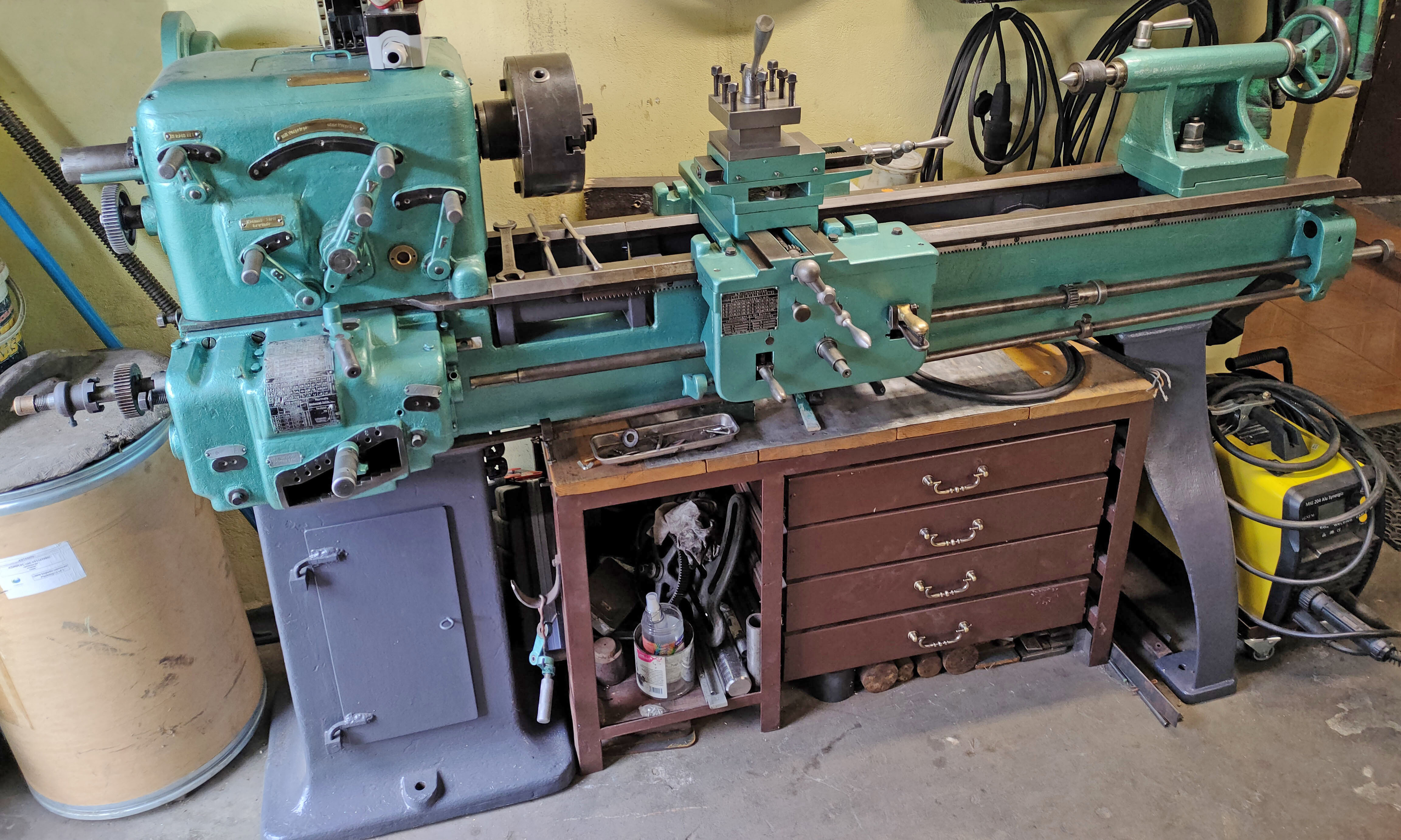 |
|
|
|
|
|
Studer RLS-200 Snap Gauge Grinding and Lapping Machine shown holding a double-opening gauge and fitted with the work-holder table and measuring apparatus
|
|
|
|
|
|
|
|
|
Continued: Flange mounted against the left-hand face of the machine's cast-iron stand, a single reversible motor was used to power the entire mechanism, its drive being arranged to run in two directions: first, passing right through the stand to emerge from the opposite face from where a smooth-running flat belt - inimical to the onset of vibration - that took the drive upwards to the linkage that imparted a front-to-back reciprocating motion grinding wheel slide; second, the drive was taken rearwards, by another flat belt, to a pulley mounted on an external swinging arm and from there upwards, by twin V-belts, to a countershaft on top of the grinding wheel slide. Located so the belt tension could be adjusted in two transverse T-slots, the countershaft had its driven pulley between two bearings with, a flat-belt pulley at each end driving the grinding and lapping wheels. The wheels were driven separately at different rates, the grinding having a peripheral speed of about 72 ft/sec. (22 m/sec.) and the lapping, using a double-step intermediate speed-reduction pulley, at the slower rate of 11 ft/sec. (3.5 m/sec.). If the job required it, the lapping disc and its speed-reduction pulley could be removed and a second grinding wheel mounted in its place. In addition, another pulley on the motor shaft drove, by a round belt passing over a pair of jockey wheels, the coolant pump, this being mounted together with its tank on the left-hand face of the column. Aiming to provide perfect concentricity, the makers arranged for the grinding and lapping wheels to be carried on collets, these being mounted on steel quills fitted with tapered and adjustable bronze bushes (sealed against grit) that turned on fixed studs. When very thin wheels were needed - to grind gauges with an opening of less than 0.25" (6 mm) - the design changed, with the thin and hence fragile wheels still collet mounted but given additional support by metal flanges that covered the greater proportion of their diameter. A spring-loaded, ball-thrust washer took up longitudinal play of the grinding wheel spindle, while the bush of the lapping wheel was also spring-loaded in both directions to push it, very lightly, against the workpiece. In action, as the lapping wheel bore against the job, the grinding slide was reciprocated, rapidly, front to back; when one face had been lapped, by the right-hand turning disc, the motor was reversed and the other face finished by the other disk turning to the left - the makers claiming that this arrangement resulted in an improved parallelism of the two surfaces. To free the wheels from the effect of belt pull and the possibility of distortion, each was fitted with two dogs that engaged with holes in the face of their drive pulley. In addition, as vibration-free running was essential, the wheels had to be balanced, this being achieved by the securing collets carrying weights adjustable in a circular slot - a balancing arbor being supplied with each machine. To assist with accurate balancing - but at extra cost - a balancing device was offered, this having a cast-iron base fitted with two levelling screws and carrying a pair of hardened and ground parallel bars, set horizontal by two built-in spirit-levels, on which the wheel on its arbor rested. So that the grinding wheel could be trued up in place, a pair of diamond holders was mounted on a bar in front of the wheel, each being arranged to dress one side of the stone. Lapping discs were made from a special, fine-grained cast iron that was charged with a lapping compound, this being applied by a hardened and ground steel roller fitted with a handle - a sample tin of a suitable paste being supplied with each machine with further (no doubt very expensive) supplies available from the maker. Before being charged with compound, the lapping wheel had its axial play removed by the tightening of a nut and then trued by being ground flat on both sides, the work being performed by another extra-cost attachment, a motor-driven grinding head. However, as the head could be moved from machine to machine as required, only one was required. So that the grinding wheel on the grinding head was, itself, perfectly true, a diamond holder was fitted to the grinding slide and the wheel trimmed before use. As the rotation of the motor could be electrically reversed, each side of the lapping wheel could be ground so that the opposing surfaces moved in the opposite direction relative to each other. Continued below:
|
|
|
|
|
|
|
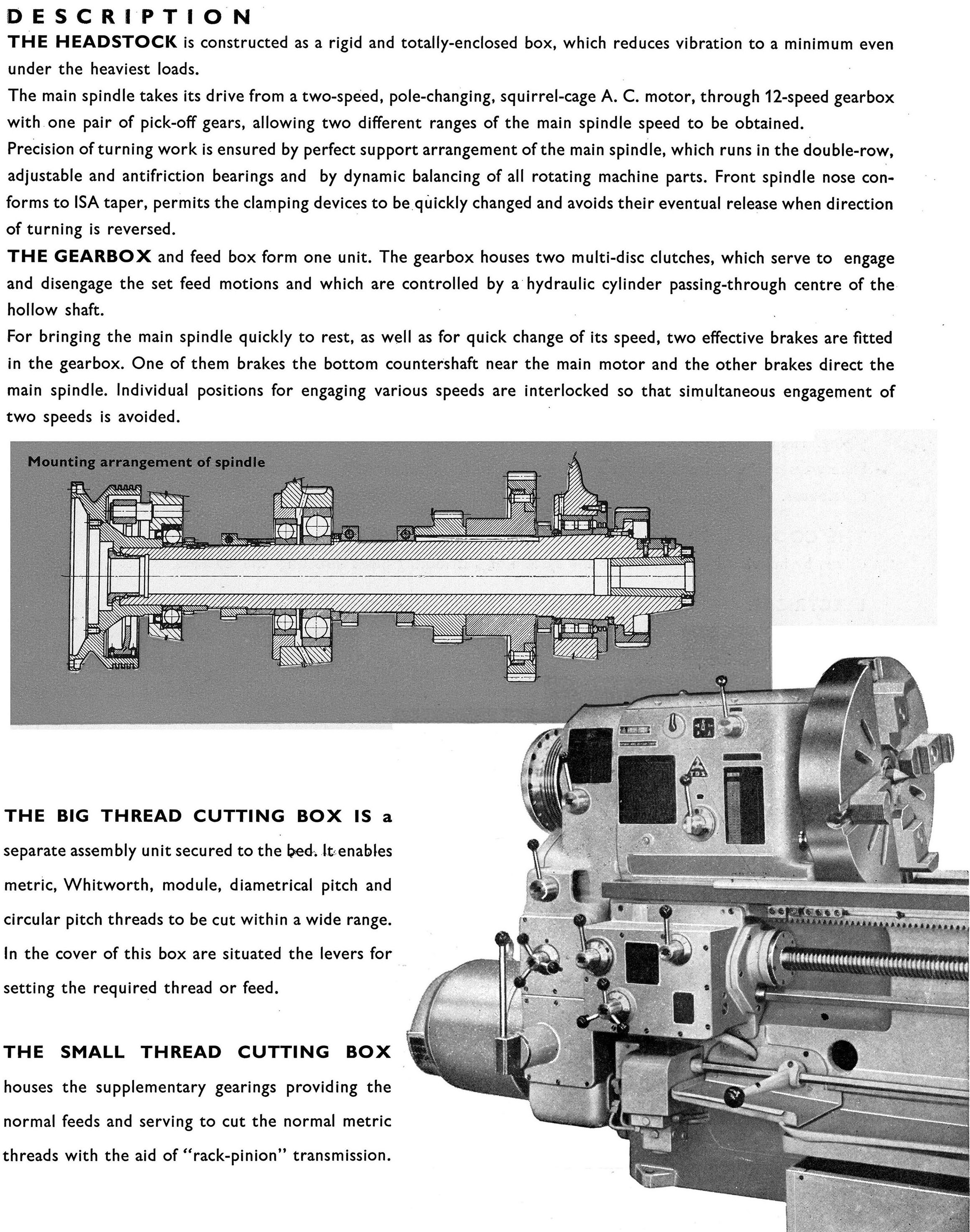 |
|
|
|
|
|
Studer RLS-200 snap gauge grinding and lapping machine in its basic form on the maker's stand
|
|
|
|
|
|
|
|
|
|
|
|
|
|
Continued: Running on Vee and flat ways, the reciprocating grinding wheel slide could be operated by power or hand - the change from one to another being by a single lever. When in automatic mode, travel could be set in a stepless range (against a scale) that ran from 0.315" to 2.36" (8 to 60 mm), a safety stop being provided to prevent the assembly over-running its travel and damaging the gauge support mechanism. Ingeniously, to keep out dust, the slide's ways were fitted with "protectors" that dipped into a channel filled with coolant. Supported by prismatic guides, the front-mounted longitudinal table had a travel of 20" (500 mm) and was fitted with a single, central T slot used to hold an upper work table - this being machined with two T-slots on its top surface and another, along the front edge, that took a hinged support to carry gauge blocks. Supplied as part of the standard equipment was a choice of two holding fixtures: either a Type A, used to secure double-fork gauges, or a Type B, for single-fork types. The A holding fixture consisted of two hardened and ground blocks, one with a stop for clamping inserts and both adjustable lengthwise using a micrometer-equipped screw. Into the fixture was fitted what the makers described as a "clamping insert", these being made in a variety of sizes to suit different gauges - one clamp being suitable for several sizes. Also included in the basic kit of parts was a bracket with a spring-acting, eccentric clamping device for holding the clamping inserts in place, and one specimen of an insert for gauges with an opening from 0.6" to 1" (15 to 25 mm). For single-opening gauges, the B holding fixture comprised three hardened pads arranged radially in the table's T-slots with the middle pad carrying a reversible clamping block to secure the central part of the gauge. The other two, fitted with simple, screw-operated finger clamps, were positioned as required at the outer ends of the gauge. Inwards feed could be driven in two ways: either directly, using the (adjustable) micrometer screw with a feed of 0.00040" (0.01 mm) that corresponded to one division on the thimble scale - or indirectly, after tightening a screw cap, by worm-and-wheel gearing that reduced the feed to two-hundred thousandths (0.00002" or 0.0005 mm) per division on a separate "worm drum" scale. A vital part of the machine was the measuring apparatus - this served to check tolerances while lapping was in progress by the use of a comparison process. The accuracy of measurement, claimed to be independent of operator skill, was 0.000040" (0.001 mm) within a range from 0.25" to 10" (8 to 250 mm). The holder for the measuring equipment needed to be as mobile as possible, not only to allow the two feelers of the comparator dial to be brought easily between the measuring surfaces of the gauge, but also to be swung out of the way when not in use. Hence, the assembly was in the form of a column - able to be tilted forwards and backwards and adjusted vertically - that carried, in a bracket, a horizontal arm. Swinging free from the arm and suspended on two parallel bars provided with ball bearings, was a holder for the quadrant-faced comparator holder with its two measuring pointers, a dial gauge and a high-precision measuring rule. Of the two feelers that contacted the inside faces of the snap gauge's anvils, one was set to give a needle reading of 0.00040" (0.01 mm) within a large range, while the other was used for reading to 0.000040" (0.001 mm) within a range restricted to 0.0040" (0.1 mm). In use, the operator swung the apparatus gently backwards and forwards; when the job was finished, and before dressing the stone or lapping wheel, the whole assembly was hinged backwards to be clear of splashing coolant and grinding dust. Continued below:
|
|
|
|
|
|
|
 |
|
|
|
|
|
Rear of the machine: drive motor, coolant tank and twin V-belt drive to the grinding slide countershaft
|
|
|
|
|
|
|
|
|
Continued: Supplied with each new machine were the following: 3-phase flange-mounted 1 h.p. motor with reversing switch; grinding wheel 10" (250 mm) in diameter and 0.70" (17.8 mm) wide with mounting collet; a 10" (250 mm) lapping disc 0.5" (12 mm) wide with mounting collet; grinding wheel truing device (without diamonds); snap gauge holding fixture, either Type A for double-fork snap gauges, with specimen clamping insert for gauges with an opening from 0.6" to 1" (15 to 25 mm), or Type B for single fork snap gauges of all sizes up to 12" (300 mm); coolant system consisting of a pump, tank, piping and fittings; extractor nut for collets; balancing arbor for grinding wheels; roller for charging lapping wheels and fourteen spanners and other tools all neatly carried around the periphery of a plate to the right of the lapping wheel. Available at extra cost were other sizes of snap gauge holders and clamping inserts; a variety of grinding wheels and lapping discs, holding collets and flanges for narrow wheels; a lapping wheel truing device with electric motor; a balancing device and a special version of the measuring apparatus for checking distances on the outer faces of a job..
|
|
|
|
|
|
|
 |
|
|
|
|
|
|
Front of the Studer RLS-200 showing the two pipes, twin diamond holders for dressing the grinding wheel and, centrally, the holder for the diamond used to dress the wheel of the attachment that ground the lapping wheel
|
|
|
|
|
|
|
 |
|
|
|
|
|
|
Left-hand side of the Studer RLS-200 showing the speed-reducing pulley set used to drive the lapping wheel. Note the typically neat Swiss tool storage facility - absolutely no excuse at all to lose an item
|
|
|
|
|
|
|
|
|
|
|
|
 |
|
|
|
|
|
With the lapping wheel and its speed-reducing pulley set removed, it was possible to mount a second grinding wheel
|
|
|
|
|
|
|
 |
|
|
|
|
|
|
Mounted on the work table is the special attachment needed to grind the side faces of the lapping disc. The picture shows the attachment's stone being dressed by a diamond before use
|
|
|
|
|
|
|
 |
|
|
|
|
|
|
Truing the lapping wheel: before being charged with compound, the lapping wheel had its axial play removed by the tightening of a nut and was then trued by being ground flat on both sides, the job being performed by an extra-cost attachment - though a toolroom would have required only one, as it could be moved from machine to machine as required.
|
|
|
|
|
|
|
|
|
|
|
|
 |
|
|
|
|
|
|
A double-fork snap gauge, secured in its special holder, positioned against the lapping wheel
|
|
|
|
|
|
|
 |
|
|
|
|
|
|
On the left a grinding wheel of standard width fitted to its collet. On the right a very thin 0.16" (4 mm) wheel with its fragile structure though still collet mounted supported by metal flanges that covered the greater proportion of its diameter
|
|
|
|
|
|
|
 |
|
|
|
|
|
|
Lapping disc with its collet, extractor nut and the roller by which means the lapping compound was applied
|
|
|
|
|
|
|
 |
|
|
|
|
|
|
Wheel balancing device: a pair of hardened and ground parallel bars, set horizontal by two built-in spirit-levels, that carried the arbor and grinding wheel
|
|
|
|
|
|
|
|
|
|
|
|
|
 |
|
|
|
|
|
|
Holding Fixture Type A to secure double-fork gauges. This consisted of two hardened and ground blocks, one with a stop for clamping inserts and both adjustable lengthwise by means of a micrometer-equipped screw. Into the holding fixture was fitted what the makers described as a "clamping insert" (see below), these being made in a variety of sizes to suit different gauges - though one clamp was able to hold a number each side of its nominal capcity
|
|
|
|
|
|
|
 |
|
|
|
|
|
|
Clamping inserts of various sizes to hold double-ended snap gauges. The gauges were first secured in a clamp (one clamp suiting several sizes of gauge) and the camp then held in the holding fixture on the work table
|
|
|
|
|
|
|
 |
|
|
|
|
|
|
Holding Fixture Type B for single-opening gauges. The fittings comprised three hardened pads secured in the table's T-slots. The central pad, fitted with a reversible clamping block to secure the central part of the gauge, remained in place while the other two, fitted with simple, screw-operated finger clamps, were positioned as required at the outer ends of the gauge.
|
|
|
|
|
|
|
 |
|
|
|
|
|
|
Clamping a very small single-opening snap gauge
|
|
|
|
|
|
|
 |
|
|
|
|
|
|
The measuring apparatus being adjusted by using gauge blocks set in the front holder
|
|
|
|
|
|
|
 |
|
|
|
|
|
|
Measuring apparatus in position taking a reading. In use, the operator swung the apparatus gently backwards and forwards; when the job was finished, and before dressing the stone or lapping wheel, the whole assembly was hinged backwards to be clear of splashing coolant and grinding dust.
|
|
|
|
|
|
|
|
|
|
|
|
|
|