Cylindrical and other Grinders. Pultra Capstan lathes. Unknown Pultra lathes.">
 |
 |
 |
 |
 |
 |
 |
 |
 |
 |
 |
 |
 |
 |
 |
 |
 |
 |
 |
 |
 |
 |
 |
 |
 |
 |
 |
 |
 |
 |
 |
 |
 |
 |
 |
 |
 |
 |
 |
|
|
|
|
|
|
|
|
|
|
|
|
|
|
|
|
|
|
|
|
|
|
|
|
|
|
|
|
|
|
|
|
|
|
|
|
|
|
|
|
|
|
|
|
|
E-MAIL tony@lathes.co.uk lathes.co.uk Home Page Machine Tool Archive Machine Tools Sales & Wants Machine Tool Manuals Machine Tool Catalogues Belts PULTRA Type "P" Miniature Cylindrical and other Grinders
Manuals and Sales Literature is available for most Pultra Models
Pultra Home Page Unlisted Pultra Lathes Pultra 17/70 Capstan Lathe
Designed for use by instrument, optical, watch and clock-making repair shops and in experimental and development workshops today the little Pultra cylindrical grinder is a rarely-encountered machine but, like the similar (though more heavily built) Jones and Shipman versions, is a highly sought-after addition to the machine shop of any truly ambitious model or experimental engineer. On cylindrical grinders, in order to grind very small diameters to a high degree of accuracy, the surface speed needs to be very high. To achieve this the workpiece spins in one direction and the grinding wheel, often powered by a separate motor, in the other. With a little ingenuity this type of grinder can also be adapted to other tasks and an examination of the pictures below will show the machine set up for grinding between dead centres, a method also used for many years on horological and precision bench lathes. The Pultra could take a maximum length and diameter between centres of 5.5 and 2 inches respectively and run a 5-inch by 0.75-inch wide grinding wheel at up to 4400 r.p.m. The slides were all provided with pressure oil nipples, for positive lubrication, and the longitudinal slide had a maximum stroke of 3.5 inches. The feed micrometer dial wheel was 4 inches in diameter with 250 divisions - 10 revolutions moving the slide 1/4 " towards stone (1 div =0,00254 mm) On the Pultra a cast-iron table at the rear with a single longitudinal T-slot was used to carry the grinding head and motor assembly (the arrangement allowed the head to be positioned anywhere along the length of a workpiece) whilst the bed, headstock and drive motor were formed as part of a compound slide immediately in front of it. The headstock, whose spindle ran in ball races and took WW-20 collets, was arranged to carry a simple bracket on which was mounted the drive motor. With no power feed fitted to either traverse the operator was required to move the table left and right with a small handwheel connected to rack-and-pinion gearing and make the necessary in-feed by the use of a very fine-pitch screw fitted with a large-diameter micrometer dial. For grinding tapers and awkward shapes the bed could be swung on its mounting and, in addition, the head assembly rotated in its housing. To minimise vibration the grinder was mounted on a heavy, purpose-built stand with built-in coolant and electrical controls - three separate push-button switches for the head, grinding wheel and coolant motors and a reversing switch. Though the machine appears to have used no standard Pultra parts, the headstock, with its overhung drive pulley, bore a strong family resemblance to that employed on the 17/50 and 17/70 lathes. There are two other known models of Pultra grinder, the 18C5 radius type and the other whose exact function is, at the moment, uncertain - though possibly of the tool and cutter grinding type; both are shown at the bottom of the page..
|
|
|
|
|
|
|
|
|
|
|
|
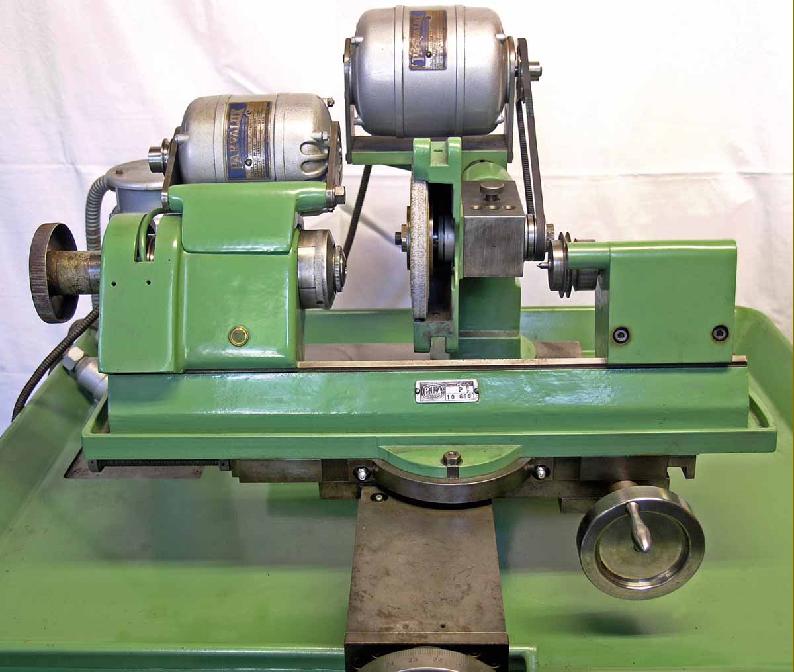 |
|
|
|
|
|
|
Pultra Type P miniature cylindrical grinder
|
|
|
|
|
|
|
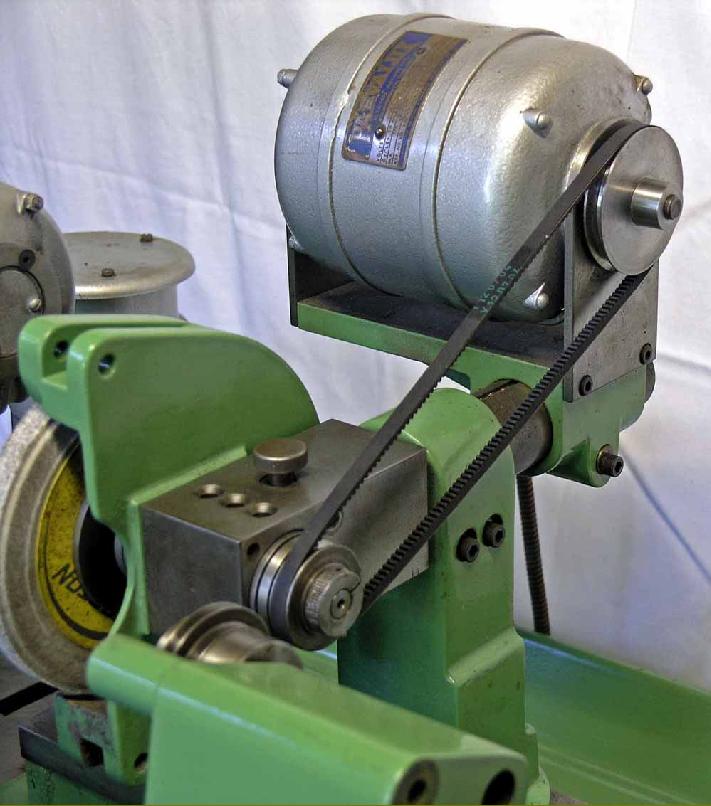 |
|
|
|
|
|
|
The grinding head and motor assembly could be rotated in the top of the support column
|
|
|
|
|
|
|
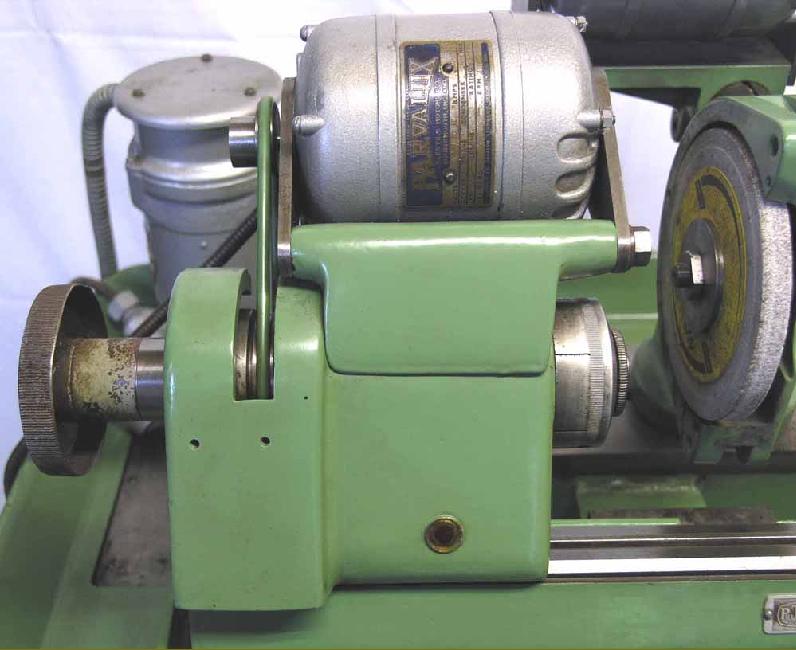 |
|
|
|
|
|
|
Though the machine appears to have used no standard Pultra parts, the headstock, with its overhung drive pulley, bore a strong family resemblance to that used on the 17/50 and 17/70 lathes.
|
|
|
|
|
|
|
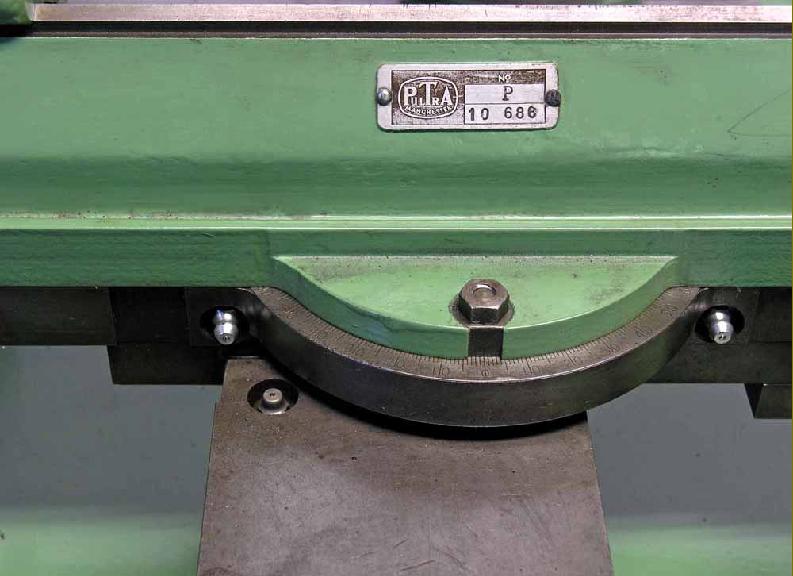 |
|
|
|
|
|
|
|
|
|
|
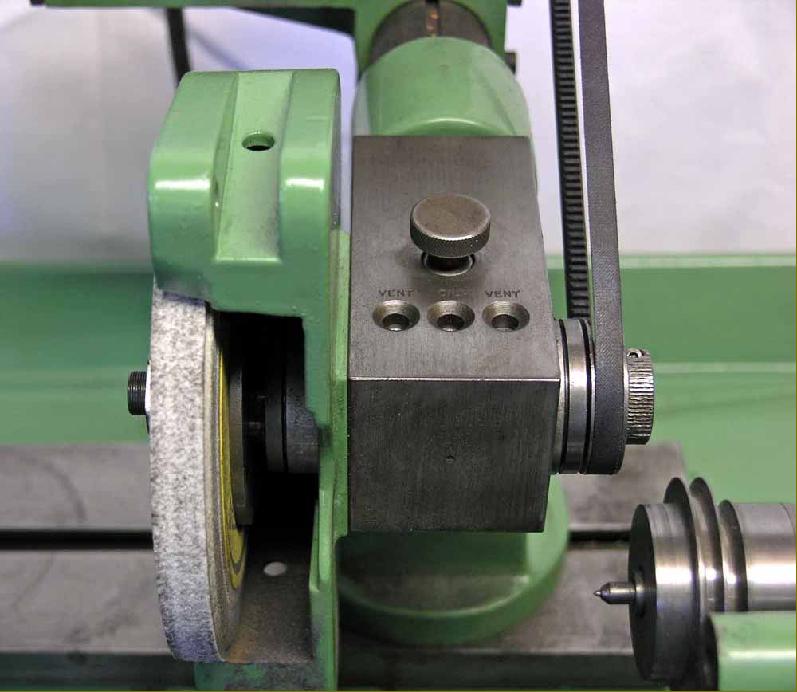 |
|
|
|
|
The grinding head used plain hardened steel bearings, not unlike those in the company's precision lathes.
|
|
|
|
|
|
|
|
|
|
|
|
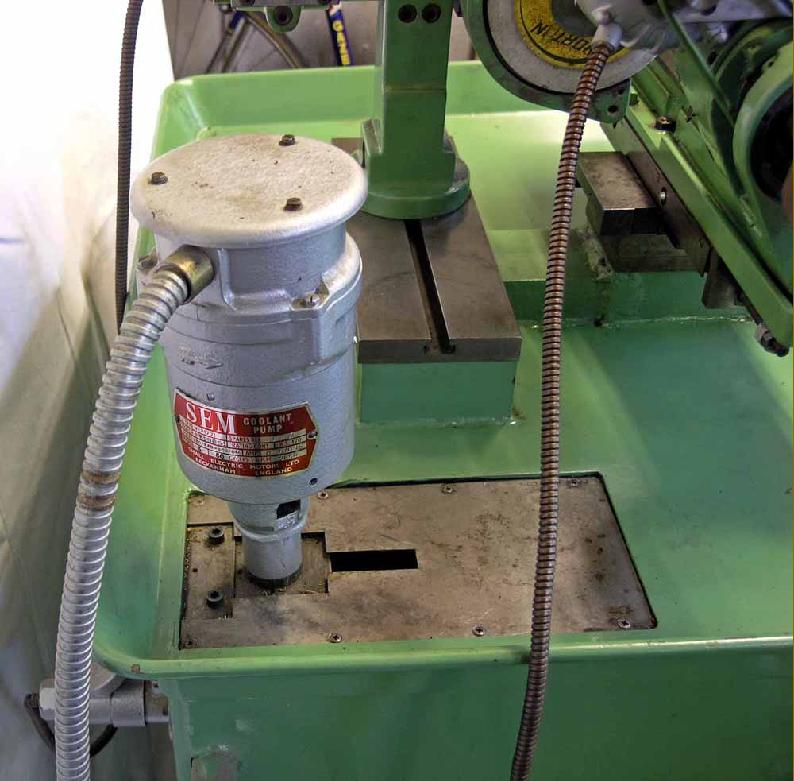 |
|
|
|
|
|
|
A view showing the coolant pump and the T-slotted table that carried the grinding head and motor assembly
|
|
|
|
|
|
|
|
|
|
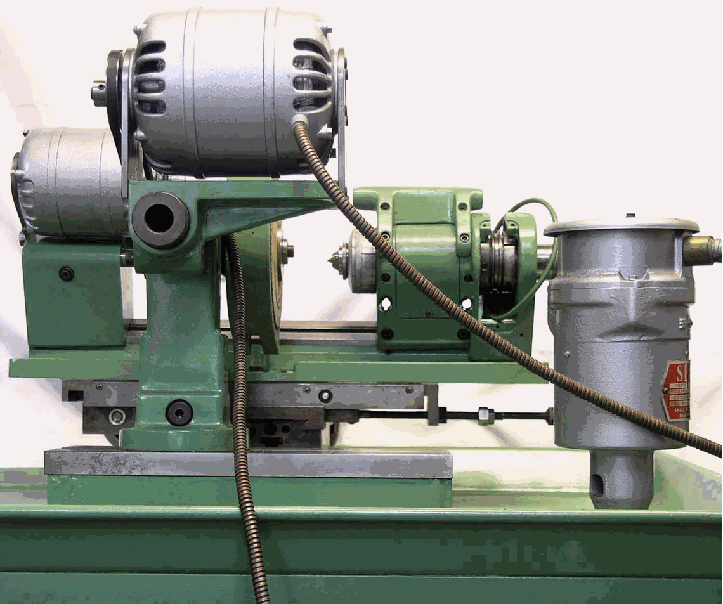 |
|
|
|
|
|
|
|
|
|
|
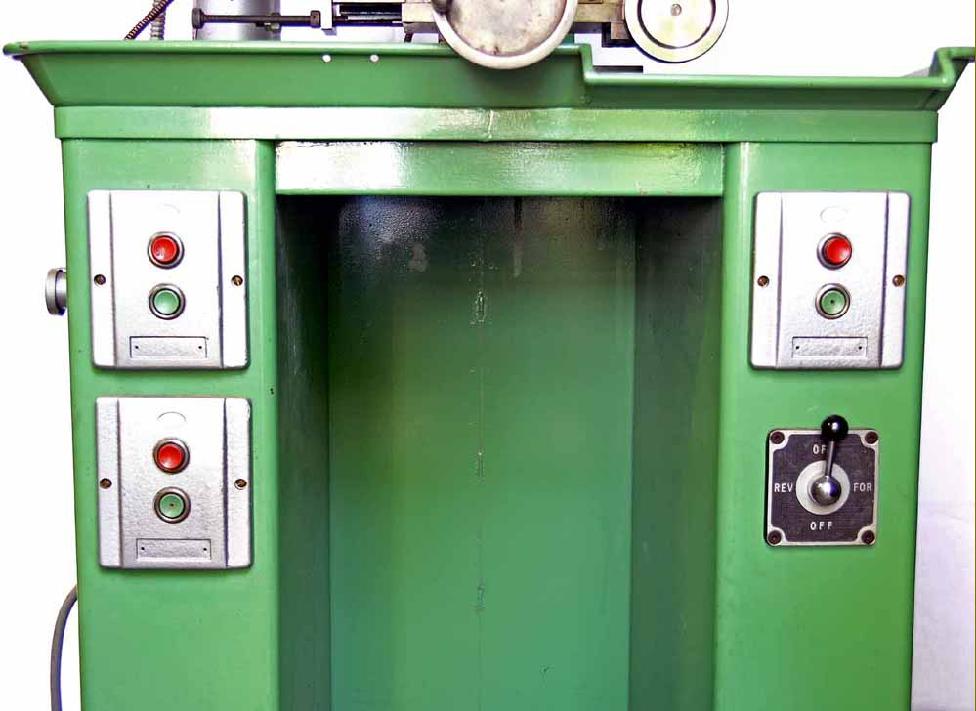 |
|
|
|
|
|
|
To minimise vibration the grinder was mounted on a heavy, purpose-built version of the "Mardive" stand with built-in coolant and electrical controls - three separate push-button switches for the head, grinding wheel and coolant motors and a reversing switch.
|
|
|
|
|
|
|
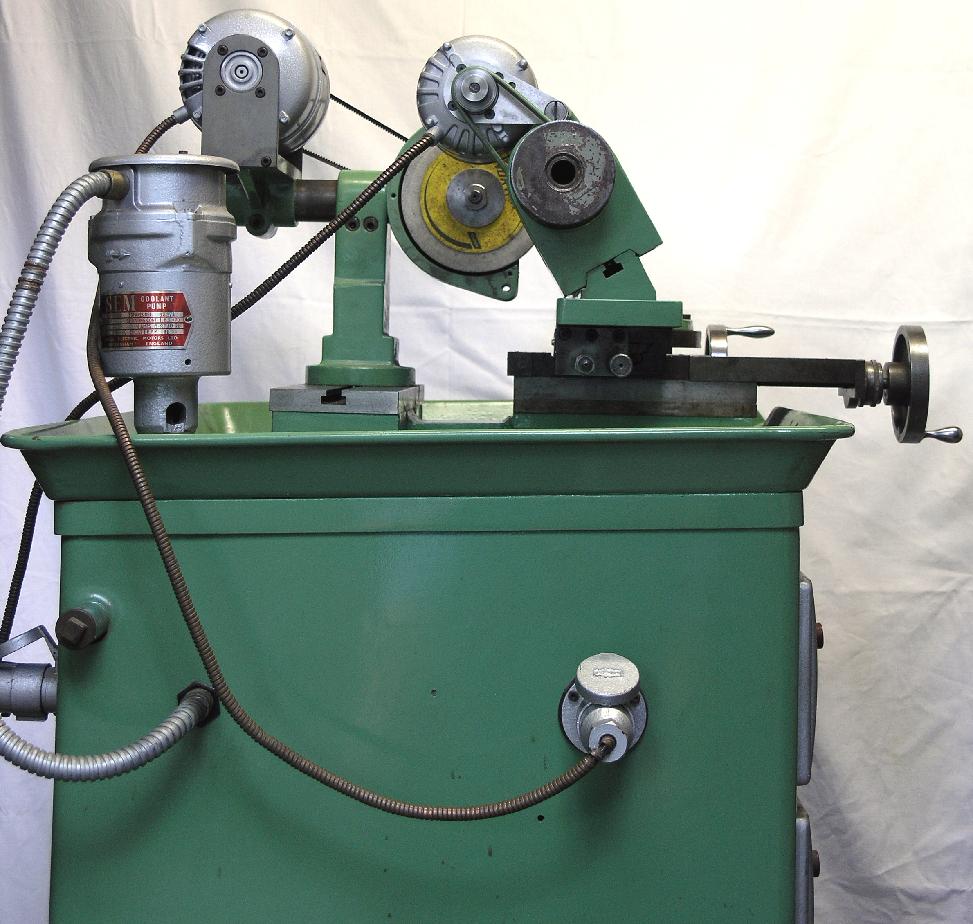 |
|
|
|
|
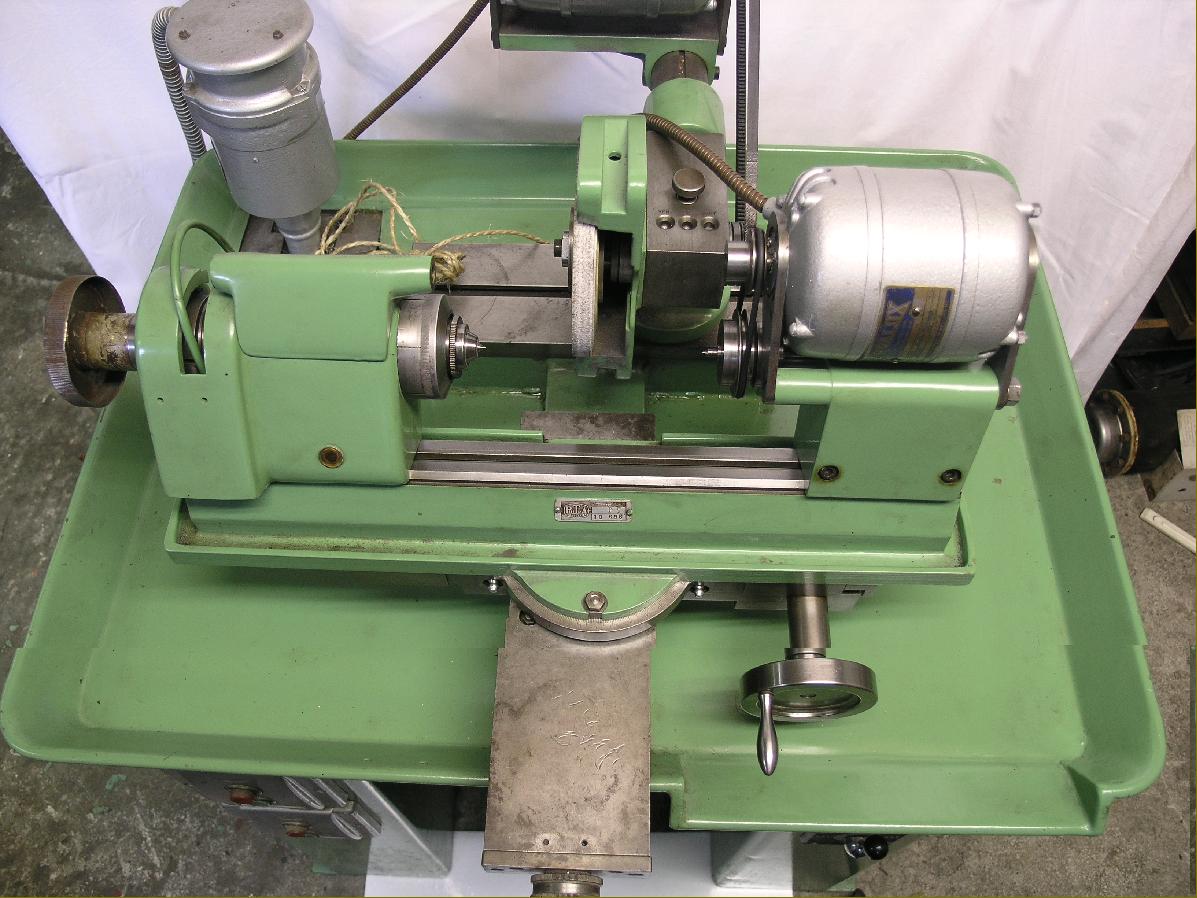 |
|
|
|
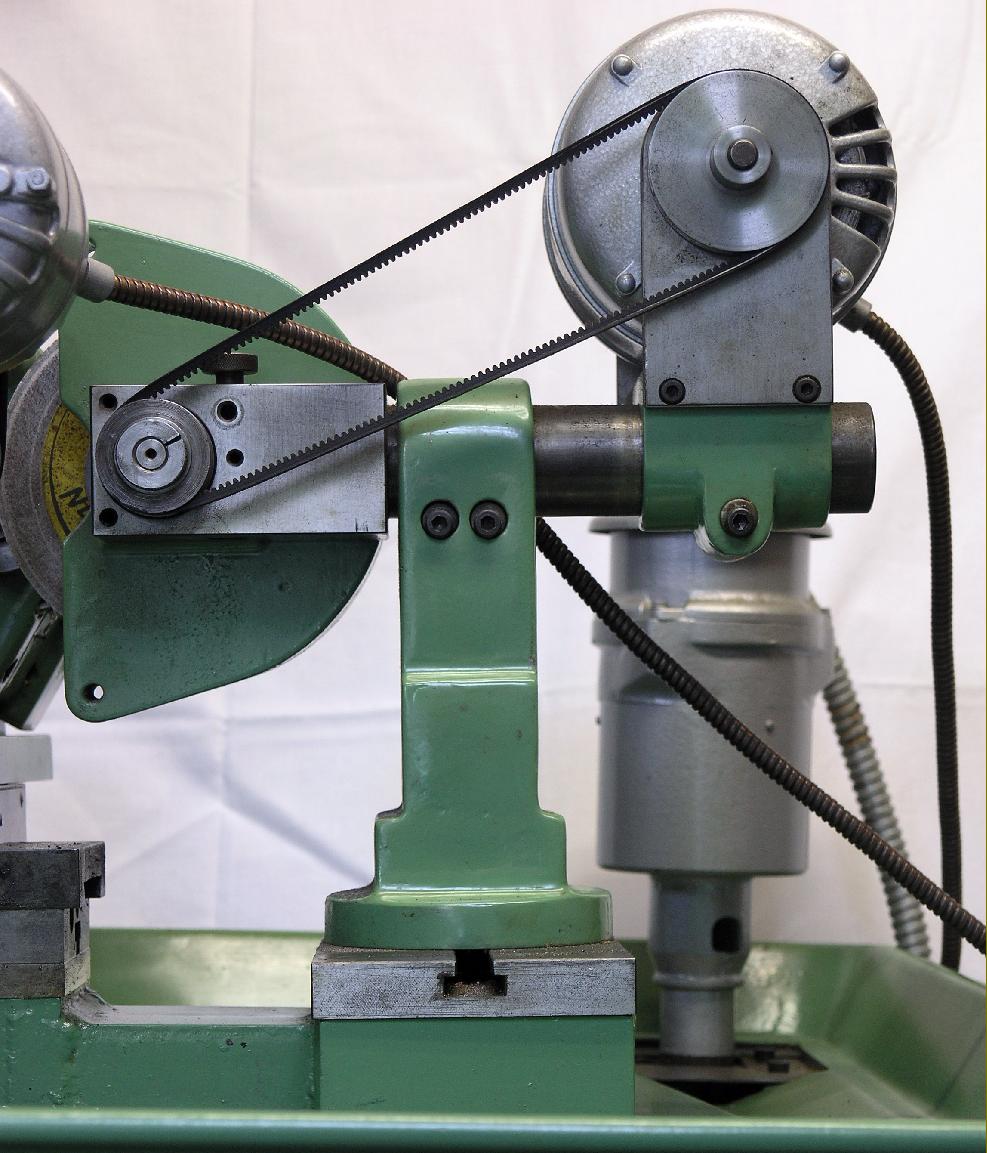 |
|
|
|
|
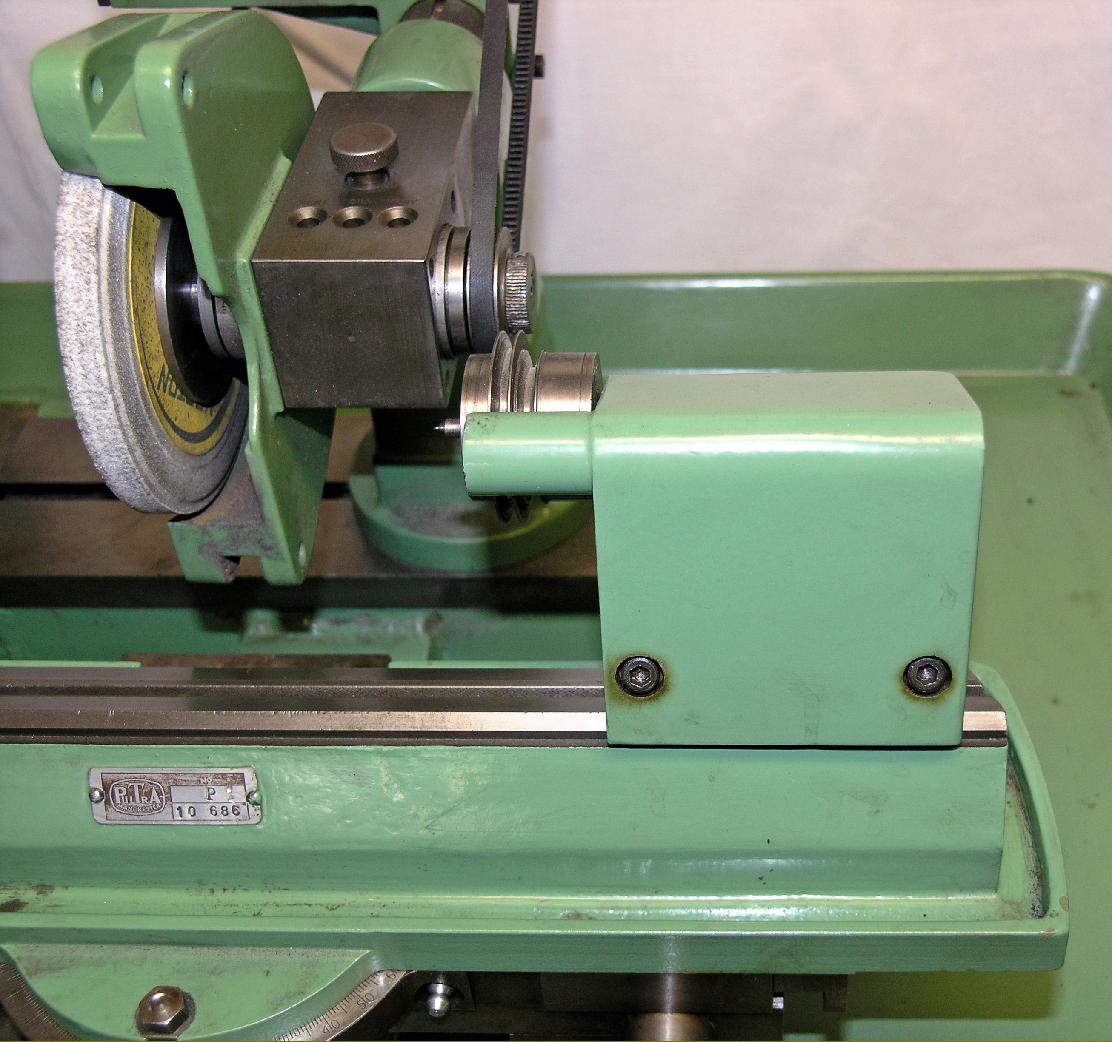 |
|
|
|
|
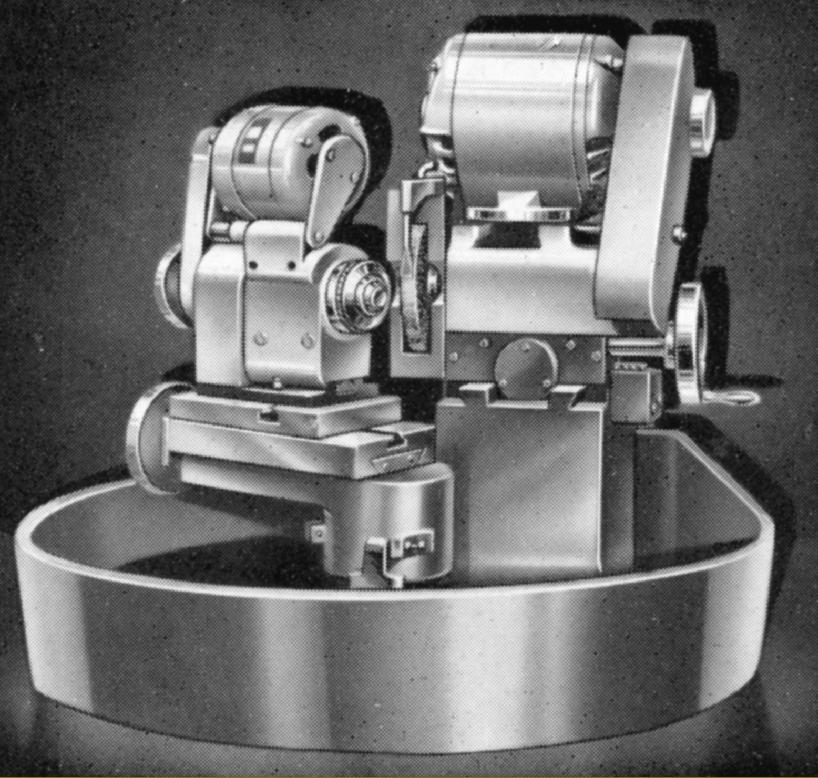 |
|
|
|
|
|
|
The rare Pultra Radius Grinder Model 18C5 produced during and just after WW2. It was fitted with a live workhead and a hydraulically operated wheelhead thus allowing a rapid approach and withdrawal of the wheel. The workhead (to the left in the picture) was mounted on a swivelling slide and both it and the wheelhead were adjustable by screws fitted with large micrometer dials. Both workhead and wheel head had independent motors - 1,400 r.p.m. on the former and 5,600 on the latter--with each, to ensure the correct, very high speeds needed for the grinding of tiny diameters, revolving in opposite directions. Four models were produced, the Mk. 1, Mk. 2, Mk. 3 and Mk. 4, though they differed only in the capacity of the workhead spindle bore - 10 mm for the Mk. 1 and Mk. 2 and 20 mm for the other two - and the fitting of hand or lever-feed drawbars.
|
|
|
|
|
|
|
|
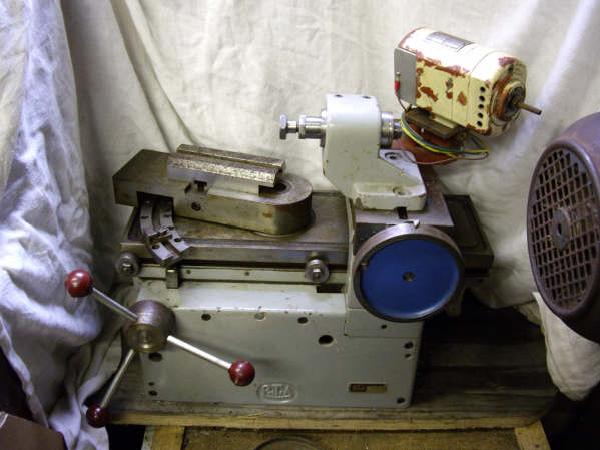 |
|
|
|
|
|
|
A Pultra of unknown model designation and uncertain function - though possibly a form of tool and cutter grinder
|
|
|
|
|
|
|
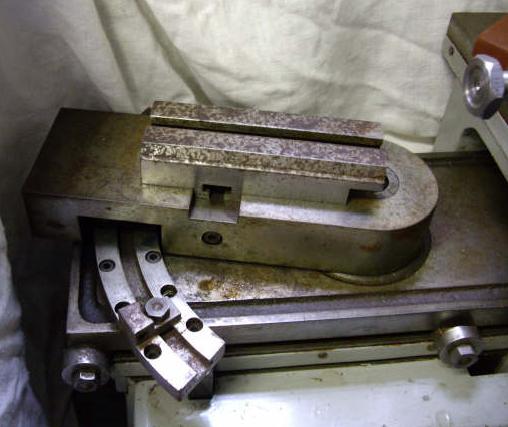 |
|
|
|
|
|
|
|
|
|
|
|