 |
 |
 |
 |
 |
 |
 |
 |
 |
 |
 |
 |
 |
 |
 |
 |
 |
 |
 |
 |
 |
 |
 |
 |
 |
 |
 |
|
|
|
|
|
|
|
|
|
|
|
|
|
|
|
|
|
|
|
|
|
|
|
|
|
|
|
|
|
|
|
|
|
|
|
|
|
|
|
|
|
|
|
|
|
Now well known for their advanced CNC machining centres, the Yamazaki Machinery Works Ltd. of 1, Norifune, Oguchi-cho, Niwa-gun, Aichi Pref. Japan, produced some fine centre lathes during the 1950s, 1960s and 1970s. Amongst their most popular models was the "Mazak", a lathe originally produced with an 18-inch swing and a choice of 40, 60, 80 and 100-inches between centres. The lathe was made in two ranges: a lighter-duty type designated as the "A" and "B" with centre heights of 18 and 20-inches respectively, a spindle bore of 2.125" and a 7.5 h.p. motor and a heavier-duty variety, the Models "C" and "D" with 18 and 21-inch swings, the spindle bore increased to 3.125" and a 10 h.p. motor. Although the sales literature listed specific models it appears (though the brochures contradicts themselves on the point) that the final specification was down to the customer who could choose from a range of specifications. By 1969 the appearance of the lathes was revised to make them look more modern: although the disposition and action of the headstock and carriage controls remained unchanged their levers were given "styled" bosses and the original quadrant-style indicator plates replaced by bright-finished rectangular aluminium sheets with colour-etched symbols. Well made and yet competitively priced (at the time Japan was a low-cost manufacturing centre) the lathes proved very popular and were exported world-wide with many examples still currently in use in the U.S.A. Europe and Australia. All versions were constructed around an exceptionally deep, 14.6-inch wide box-section bed mounted on separate cast-iron plinths at headstock and tailstock (joined by a deep, roll-out chip tray on caster wheels) and featured flame hardened and ground ways of an asymmetrical pattern (a shallow angle wide way at the front to absorb wear and a more steeply-angled steep back way to take thrust) with the tailstock running on it's own V and flat inside the carriage ways. Heavy diagonal ribs between front and back walls provided improved stiffness, yet allowed chips to fall through The ways were all ground but with mating surfaces, including the tapered gib strips (with lock screws at each end), hand finished by scraping. With the standard gap bridge removed 25" x 7" could be turned on the faceplate of the 18-inch and 28 inches on the 21-inch swing version. Continued below:
|
|
|
|
|
|
|
|
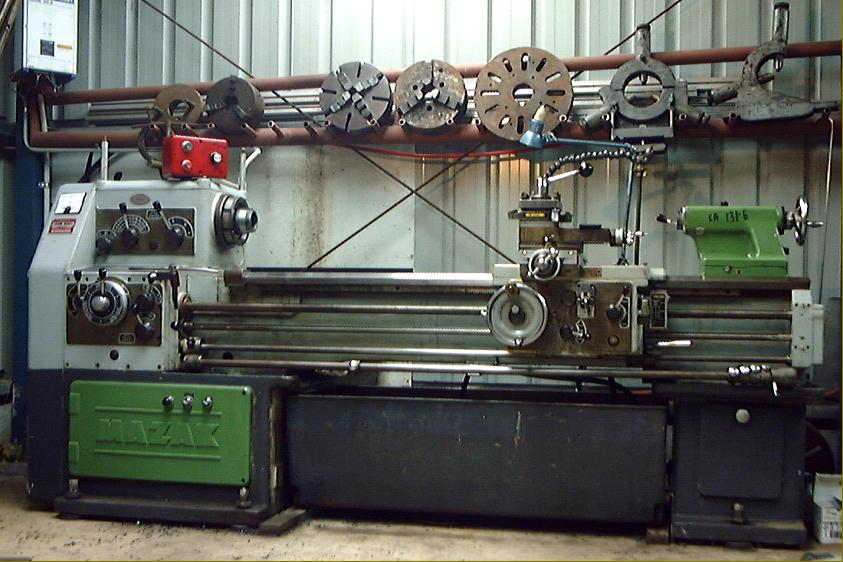 |
|
|
|
|
|
|
Continued: Equipped with two adjuster bolts for horizontal spindle alignment, the headstock was a solidly-built unit with, on the very earliest versions, 9 speeds from 25 to 1500 rpm with later models having 12 and a choice of 25 to 1500 r.p.m or 33 to 2000 r.p.m on the 2-inch headstock and a single range of 25 to 1500 r.p.m on the 3-inch. Speeds were selected by 2 clearly-marked levers with convenient but unintended neutral positions between gears. Though handy for experienced users this arrangement could trap the unwary who, after setting up or clocking a large or out of balance job in "neutral", could inadvertently select the higher-speed range - the difference between 310 and 1500 rpm being guaranteed to provide at least amazement, if not an accident, as 25-times more centrifugal force was applied than intended. Headstock gears were generously proportioned, hardened and ground and relatively quiet except at 1500 rpm. Also hardened and ground, the headstock spindle carried an American long-nose taper (in an L1 size for the "A" and "B" models and an L2 for the "C" and "D") and turned in 3 roller bearings - tapered at each end and cylindrical in the middle. Headstock lubrication was by a trochoid-type pressure pump with oil held in a cast container bolted to the bottom rear of the headstock. The filtered oil was lifted to the top of the headstock and distributed by a manifold and pipe system to precise locations. The "clamped-disc" filter unit originally used is easily changed for a modern paper-cartridge type. In line with changes made by most other lathe makers during the 1960s later versions of the lathe used the more compact and easily changed "Camlock" style of spindle nose. Drive was by four B-section V-belts from a massive drip-proof motor mounted in the base of the headstock-end plinth on a hinged adjustment plate. Unfortunately the 7.5 h.p. motor was barely adequate when running at full speed and for heavy-duty work on the "A" and "B" versions a 10 h.p. unit was offered as an option. Today, another problem might concern the oil pump which, being driven from the spindle, can (when worn and driven at less than 60% of full speed) fail to deliver enough lubricant. Early models appear not to have been fitted with a spindle brake but later versions were equipped with a Colchester-like arrangement - a pair of brake shoes operating inside the headstock V-belt input pulley. The brake was operated by a motorcycle-type cable arrangement from a foot-bar across the front of the stand. Unfortunately the brake drum is too small to retro-fit one of those excellent twin-leading shoe backplates popular on Japanese sports motorcycles of the era The motor was arranged for both star and delta connection - raising the possibility of running it from a 230/240V single-phase inverter. A trap when rewiring these machines is that some had the star point of the motor brought out by a blue wire to a terminal in the electrical cabinet that was adjacent to the earth terminal - also dark blue. Electrical start, stop and reverse was controlled by a "third shaft" system with control levers mounted just outboard from the screwcutting gearbox and, essential on a long-bed model, on the right-hand face of the apron and moving with it so the operator could reach it when following the carriage. Switching was direct on-line, a simple but relatively brutal method not uncommon in industry where heavy-duty switchgear and wiring was taken for granted. Although a current meter was provided to gauge motor load on early machines the dial was mounted on the belt and changewheel cover and arranged to face outwards; on later models it was repositioned facing toward the tailstock-end of the bed, so allowing the operator a chance to read it from a normal working position. Continued below:
|
|
|
|
|
|
|
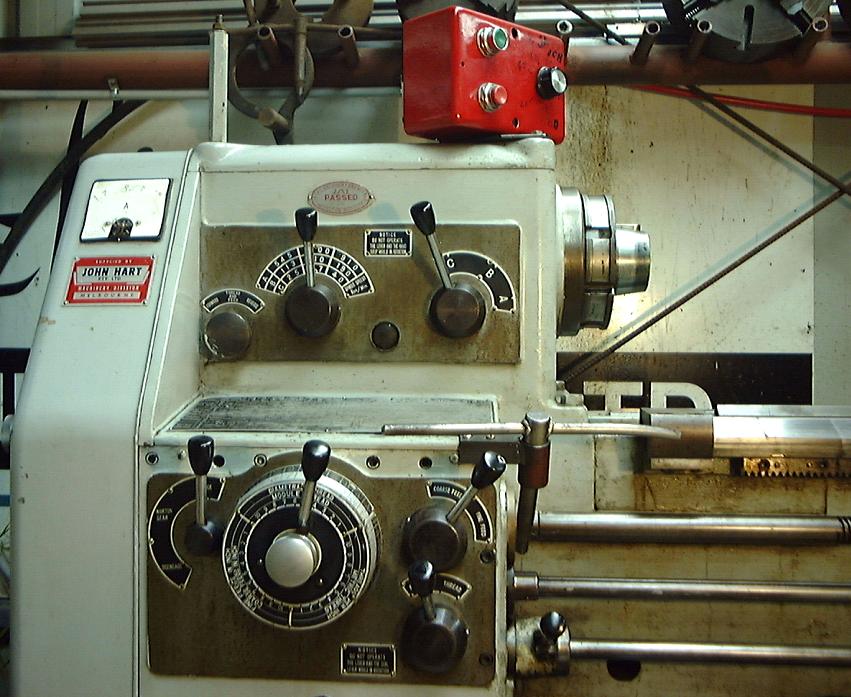 |
|
|
|
|
|
|
Continued: With a 22-inch long contact with the bed the saddle ways had a total bearing area of 83 sq inches, all hand scraped and with oil grooves cut for the full length. The apron was a double-wall design with an oil sump in the base from which lubricant was drawn through a gauze strainer by an automatic pump driven (only as the carriage moved along the bed) from the carriage handwheel shaft. The pump was provided with a hand-operated plunger button for occasions when the carriage was stationary for some time but the apron mechanism was engaged for surfacing feeds. Lubricant was circulated around the apron, and also fed to the bed ways, though not to the cross slide or its feed-shaft nut which were oiled by removing three screws. Unless carefully sealed with Teflon tape the screws allowed coolant to leak through and cause corrosion of the screw and ways--though it's likely that later models overcame these problems by removing the screws and extending the pumped oil supply. Power sliding and surfacing feeds were selected by one lever on the face of the apron (up for cross feed, down for sliding) and engaged by a drop-out worm-and-wheel mechanism whose operating handle protruded from beneath the lower edge. As is common with this design of mechanism the feeds could be instantly and easily disengaged no matter how heavy the cut being taken. Sliding feeds extended from 0.0024" to 0.0593" per revolution of the spindle with the cross feed set at one-half of those rates. A useful, pre-set 5-position knockoff mechanism could be provided at extra cost for the sliding feed and worked through a cam pin that bore on the bottom of the worm carrier. The drive mechanism was protected from overload damage by an adjustable bronze-cone safety clutch that worked well so long as the apron oil sump was kept topped up. Placed where it could catch hot turning the carriage handwheel was on the left of the apron and geared down so one revolution produced an inch (25mm) of travel. The handle was equipped with a finely-engraved (0.001" graduations) stainless-steel micrometer dial (with a rather faint zero line) and the micrometer dial locked by a through bolt, so guaranteeing no disturbance to the setting, As might be expected the compound slide rest reflected the lathe's heavy build with the cross slide a generous 23.5" long by 8" wide running on scraped dovetail ways with adjustment provided by a hand scraped tapered gib and a felt way-wiper to keep out swarf. The rear section of the slide was machined with a groove in each side face to mount accessories including a number 4-Morse taper drill holder and a rear toolpost. Unfortunately the rear toolpost had its tool-holding slot set incorrectly for the use of conventionally-mounted cutting tool; instead it had to be mounted upside down and the lathe run forwards - immediately obviating the reason for a rear-mounted holder where (with the lathe running in reverse and a conventionally-set tool) cutting forces resolved themselves downwards and forced the saddle into hard contact with the bed instead of trying to lift it up. Happily, the heavy build of the lathe meant that parting off by using the front toolpost was entirely satisfactory. With just over 14" of travel the cross slide could be used to make facing cuts up to the limit of the machine's capacity and was driven by a large diameter (around 20mm) 5 t.p.i leadscrew equipped with preloaded ball thrust bearings that ran through a pair of bronze nuts bolted to the underside of the slide - the nuts being adjustable relative to each other in order to reduce backlash. With 45/16" of travel and a slide length of 8" the topslide was a moderately robust affair with clearance adjustable by the usual tapered gib with a locking wedge pin - but with no means of adjusting backlash between screw and nut. Although the slide could be turned full circle the deep degree graduations only extended to +/- 60 degrees and, whilst the slide's base plate covered the full width of the cross slide, it was held down by two inadequate 12mm bolts - unlike the equivalent Okuma which had 4. As a consequence, some movement can be felt at this point during heavy interrupted cuts, a fault also present on many Colchester lathes of the same period whose designer also appeared to believe in tiny bolts and a belief that cutting forces would clamp the slides together. The micrometer dials were large and easy to read but locked by concentric knobs that, when operated, tended to move the setting slightly. For most markets a forged alloy-steel 4-way toolpost was fitted with the indexing components properly hardened; unfortunately the slots are not deep enough to take standard 25 mm tooling set to centre height but only need grinding out a little to allow the correct adjustments. Continued below:
|
|
|
|
|
|
|
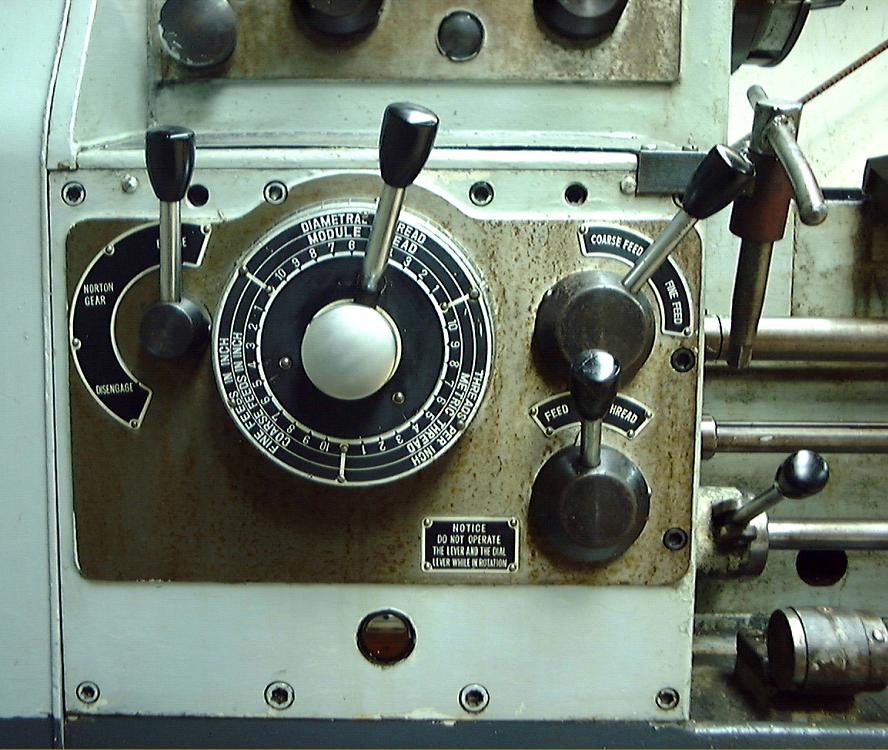 |
|
|
|
|
|
Continued: Bolted as a separate unit to the lower face of the headstock the screwcutting gearbox enjoyed its own pumped oil supply from an independent (trochoid pump) with sight glasses to check levels and flow rates. Drive to the box was by changewheels, with output from a shaft running at half spindle speed. Besides the standard changewheels others, including 55, 80, 63, 90, 91, 95, 110, 117, 126 and 127 were provided to extend the threading range and to provide metric or Imperial conversions. Without dismounting any changewheels the box could generate 40 feeds selected by a ten-position lever dial and a 4-position central knob. The feeds were clearly marked and easy to select with each position on the central knob doubling the feed rate selected on the dial. A coarse-feed setting was also provided that multiplied the rate by 1.75, though the mechanism's effect was to reverse the progression of feed rates on the 10-position feed dial. Although the rates of coarse and fine feed overlapped it was still possible to select from any of 60 individual settings (0.0024" to .0593"). Screwcutting pitches ranged from 4 to 56 t.p.i., 0.5 mm to 7 mm, 0.5 to 7.0 Module and 4 to 56 D.P.. The ten position dial had a rotating drum scale engraved with 3 positions for feed rates and metric, imperial and module threads. Diametrical threads were listed on a separate aluminium plate riveted to the top of the feed gearbox - though given the amount of swarf that accumulated here and tools that were thrown on to it a stainless steel or old-fashioned cast bronze plate would have been better. Although marked with both metric and English feed rates the former were just conversions of the inch rate; to obtain true metric pitches, and feeds, the box required driving by the metric conversion changewheel set that comprised: 80, 65 and 127t gears. Protected by a simple shear pin the 1.35-inch diameter, 4 t.p.i. leadscrew was grasped by bronze nuts around 3 inches long and fitted with a preloaded ball thrust race at its tailstock end. Continued below:
|
|
|
|
|
|
|
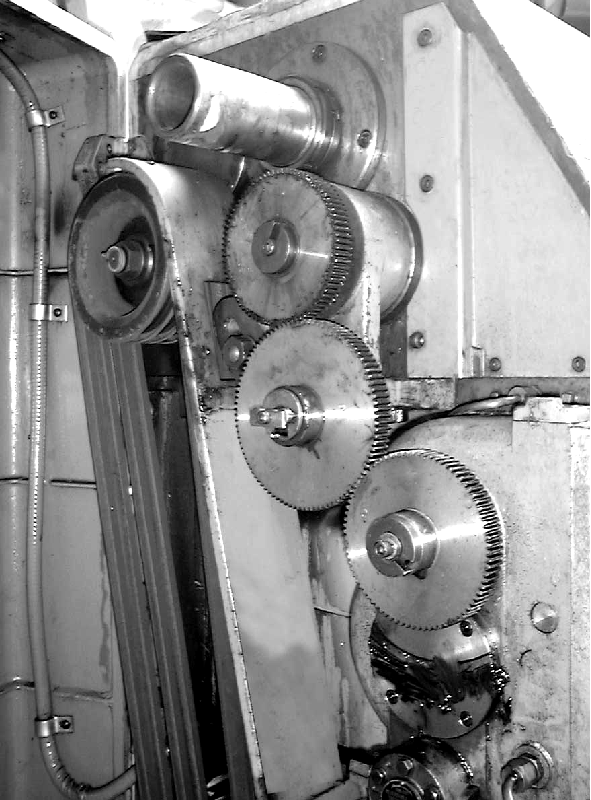 |
|
|
|
|
|
|
Changewheel drive showing the swing bracket and quickly detachable slotted washers
|
|
|
|
|
|
|
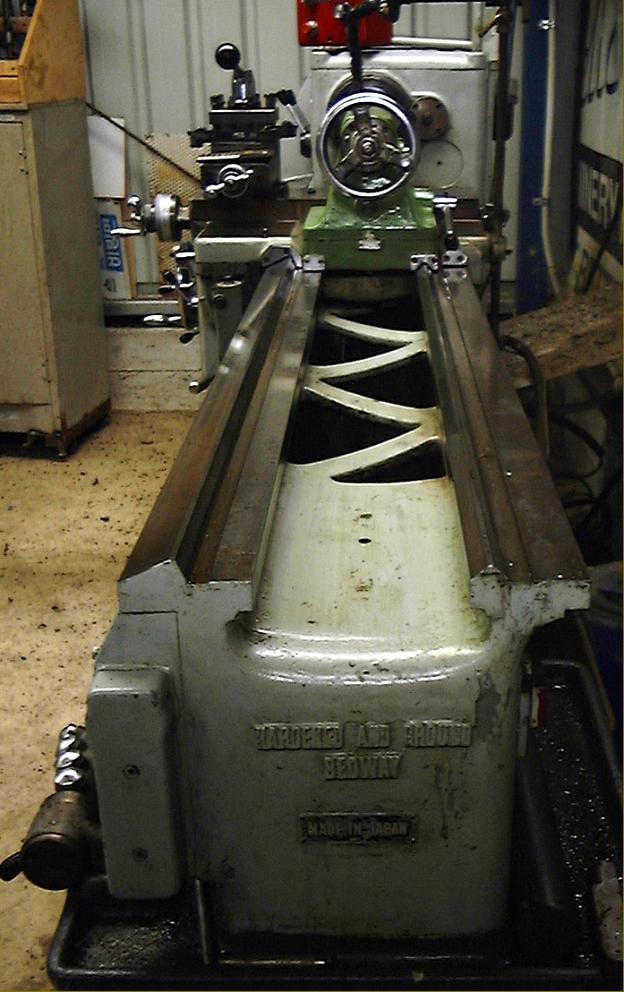 |
|
|
|
|
|
|
Heavily braced hardened and ground bed
Continued: Of conventional design the tailstock carried a 2.5" diameter spindle with a 5.5" stroke and 4-Morse taper socket. The top section could be off-set on the sole plate for the turning of slight tapers whilst an unusual touch was the provision of a tapered gib strip on the square transverse way to ensure that the quill always remained parallel to the bed ways. Although a micrometer dial was fitted to the feed screw, some models lacked ruler scales making quick drilling to an approximate depth an awkward process. The feed rate of the handwheel screw was 0.2" per revolution whilst later machines were fitted with the refinement of a 2-speed drive through a gearbox with a 1:1 ratio for quick setting and a 5:1 for use in heavy drilling operations. The spindle was also given an increased travel of 6.7 inches. Although centres and drills were self-ejected a wise addition was the provision of a slot for the use of a removal wedge and all the sliding surfaces, including the quill, were fitted with felt wipers. The quill was prevented from rotating by a keyway cut into its underside and locked by a lever that pulled bronze half-nuts against its underside - an interesting departure from the "split-nut" type of clamp frequently found on smaller lathes and the subject of a patent No. 43-69266). The unit was locked to the bed by two plates drawn upwards by eccentric shafts: the main lock was operated by a long handle at the rear whist the other, designed to be employed as a supplementary lock on heavy work, required the application of a socket spanner on a hexagon-headed shaft that protruded through the right-hand end of the casting. Accessories: Supplied with the lathe as standard were the motor, electrical switchgear and drive belts, a set of changewheels for metric and English screwcutting, a thread-dial indicator, two No. 4 Morse centres, one in steel the other carbide tipped; a Morse reduction sleeve to take the headstock spindle down from a No. 6 to a No. 4; a sheet metal oil pan/chip tray to fit between the bed support plinths, a toolbox with the necessary spanners, an Instruction Book and Parts List and a can of touch-up paint. Accessories covered the usual range with 3-jaw chucks available up to 12-inches in diameter and 4-jaws up to 16-inches; a 14-inch faceplate, 9-inch catchplate, fixed and travelling steadies with a capacity of 6.5 inches, a No. 4 Morse rotating centre, an infeed plunge-cutting attachment, a heavy-duty cross-slide mounted drilling attachment, telescopic-type taper-turning, high-speed threading attachment (probably by Ainjest), coolant system, hydraulic copying, hardened and ground top and cross slide screws with positive lubrication, micrometer carriage stop, a multi-position turret-type carriage stop, chip cover and an automatic multiple-feed bar stop (this last item shown fitted to the lathe below). Take care if nuts and bolts have to be replaced: although the lathe was built to a metric standard some of the fastening are Whitworth and some, like the bed gap socket head bolts with an AF socket head and 1/2" Whitworth thread, are distinctly unusual. Bolts smaller than 6 mm seem to have been specified as BA (itself a metric-derived thread) or a variation on it. The lathes varied in weight from 4620 lbs for the short-bed 18-inch Model "A" with a small headstock spindle and 7.5 h.p. motor to 7080 lbs for the longest-bed, large-spindle bore 10 h.p. Model "D"..
|
|
|
|
|
|
|
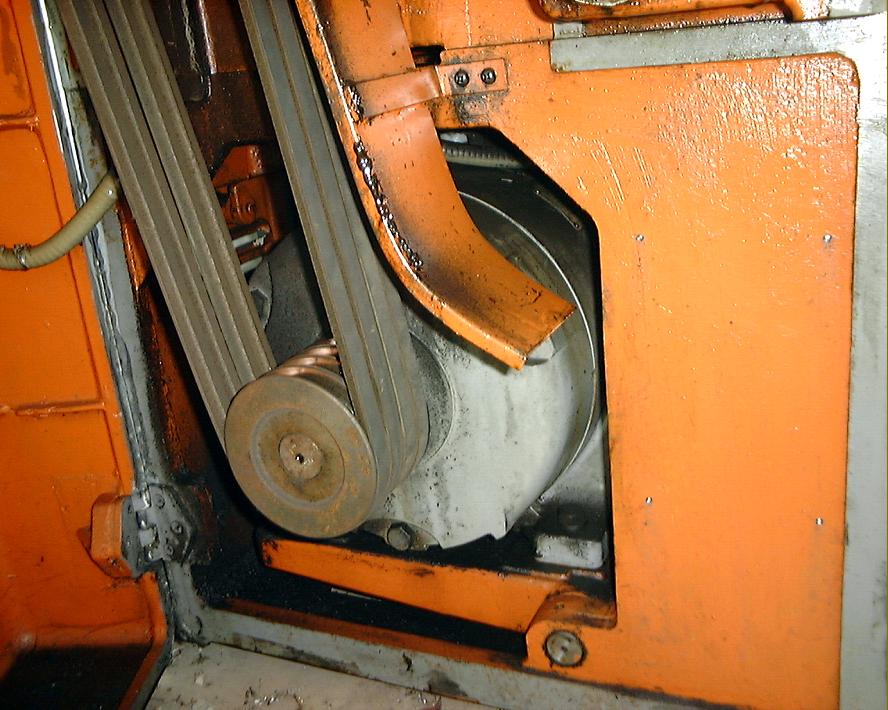 |
|
|
|
|
|
7.5 h.p. motor with 4-step "B" section V-belt drive
|
|
|
|
|
|
|
|
|
|
|
|
|
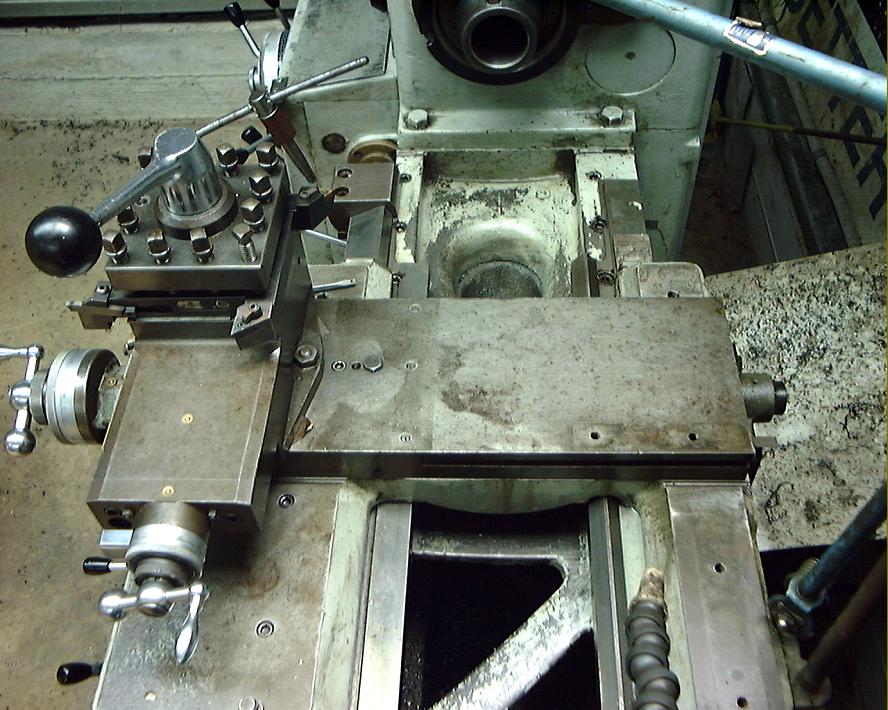 |
|
|
|
|
|
Full-length cross slide devoid of fittings
|
|
|
|
|
|
|
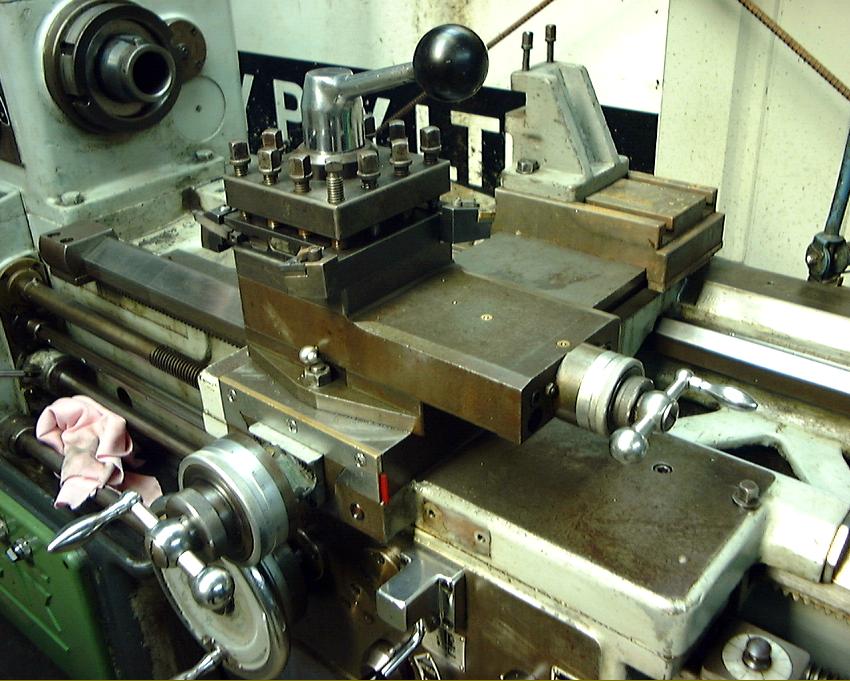 |
|
|
|
|
|
|
Cross slide fitted with the optional T-slotted raiser block and rear toolpost
|
|
|
|
|
|
|
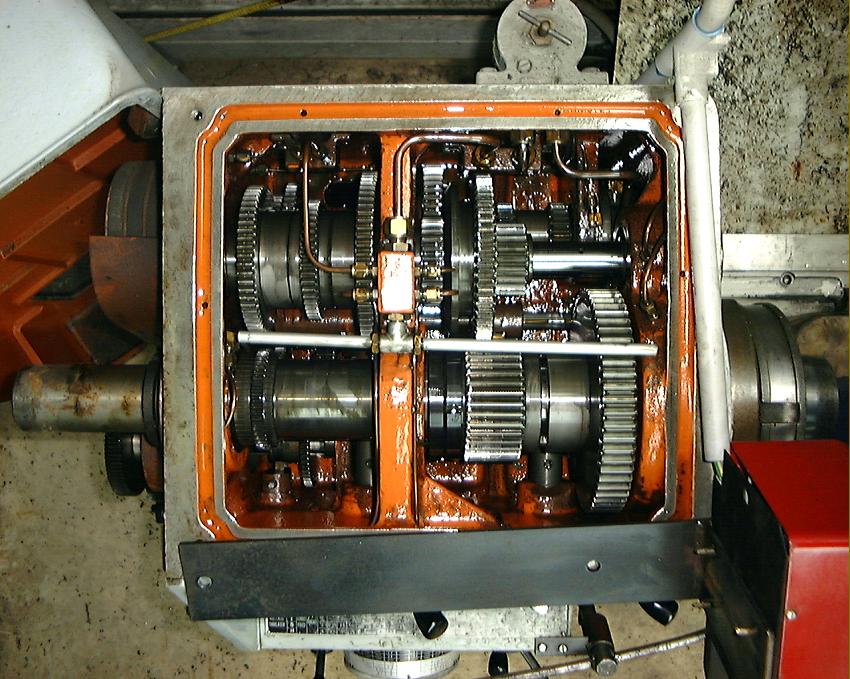 |
|
|
|
|
|
|
Headstock internals showing the oil-distribution manifold positioned across the centre
|
|
|
|
|
|
|
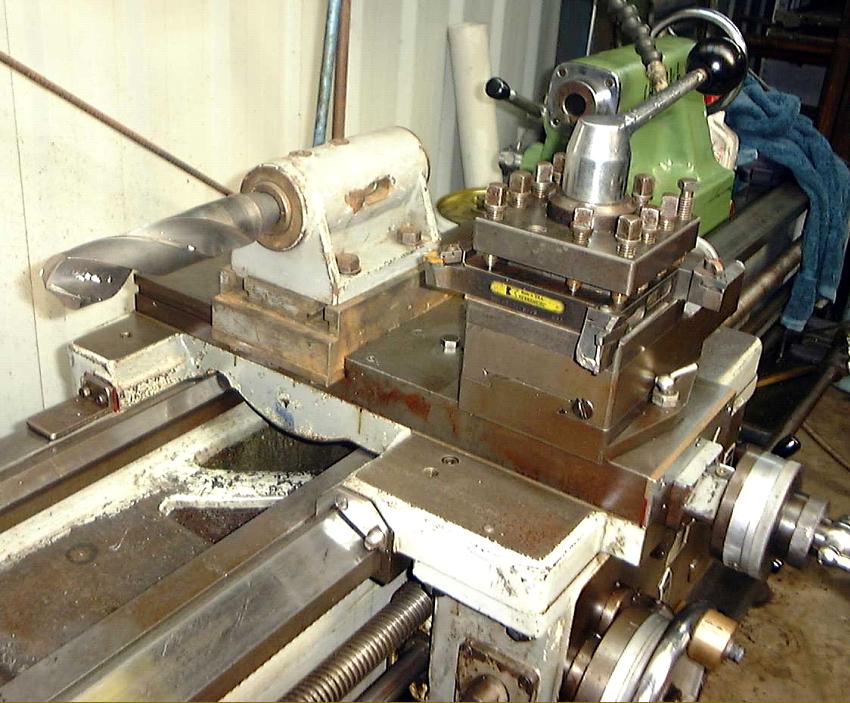 |
|
|
|
|
|
|
Power drilling attachment
|
|
|
|
|
|
|
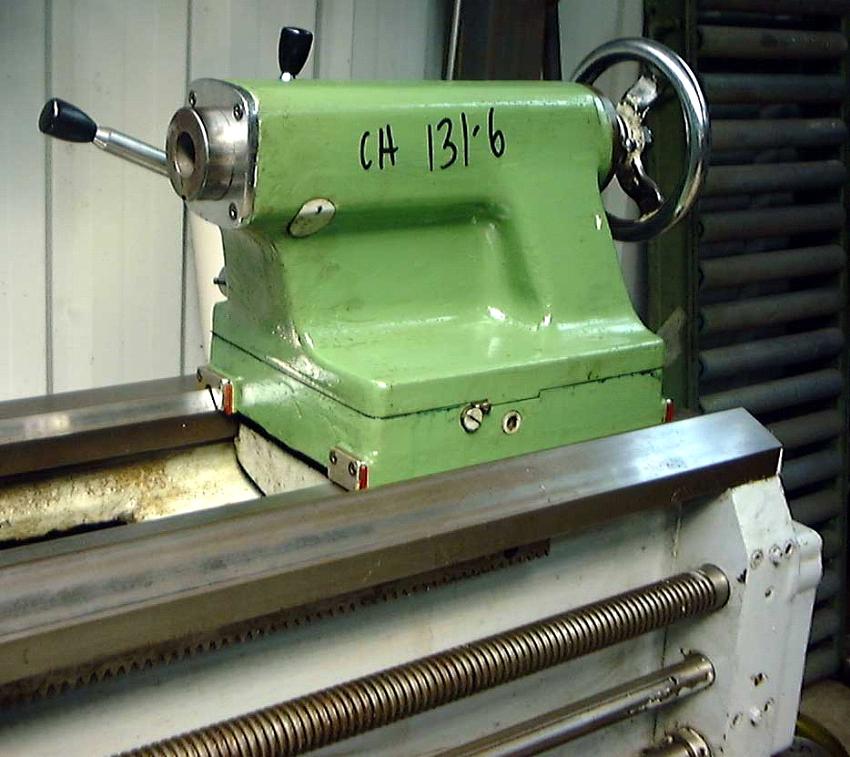 |
|
|
|
|
|
|
|
|
|
|
|
|
|