 |
 |
 |
 |
 |
 |
 |
 |
 |
 |
 |
 |
 |
 |
 |
 |
 |
 |
 |
 |
|
|
|
|
|
|
|
|
|
|
|
|
|
|
|
|
|
|
|
|
|
|
|
|
|
|
|
|
|
|
|
|
|
Maxnovo lathes were manufactured by Officine G.C.Bossetti (Precision Mechanical Works) in Novara, Italy with world-wide marketing rights held by Emanuell Mascherpa of Milan. Unfortunately, apart from the Model T.A.M., little is known of their conventional centre lathes and only outline details of their later machines that appear, from the evidence available, to have concentrated on cleverly-engineered duplicating lathes in "universal" and "programme" types, "production" and "programmed-production" models, turret copying lathes and a variety of specialised models that could be custom constructed to a customer's particular requirements from standard basic units. These latter machines, described by the makers as "block" type lathes, could be adapted for a variety of specialised tasks such as the production of camshafts, gun barrels, gear blanks and piston turning, etc. and were often to be found with multiple tool-holders and front and rear copying slides each able to simultaneously follow a different profile. Precise production dates for the T.A.M. 210 mm (8.25-inch) centre height screwcutting centre lathe are not known, but from the design, styling and features a reasonable guess would be that it was current from the late 1930s until some point in the 1950s. Before manufacture started the makers produced two successive prototypes - subsequently put to work in the factory - from which experimental data was gathered to further improve and refine the design. The lathe was built in "A" and "B" versions - identical apart from the power of the motor and the number of spindle speeds. Cast from a chrome-nickel alloy cast iron, the deep, beam-section bed was subjected to a series of heat treatments designed to stabilise the grain structure and relieve any internal stresses. Each bed was checked to ensure it reached the minimum of 100 Rockwell B Series (242 Brinell) and sample batches taken to ensure that the metallurgical and mechanical properties were within limits. Instead of simple cross, diagonal or web-type bracing the front and back walls were stiffened by elliptical ribs with chip clearance vertically onto a large slide-out swarf tray. The ways were of the V and flat type with the V at the front following contemporary fashion in having a short, steeply-angled inside face, to better absorb tool thrust, and a wide, shallow-angle outer designed to provide a greater bearing surface for the saddle and a slowing down of normal wear and tear. The bed was mounted on separate cast-iron plinths under tailstock and headstock with each having a small storage compartment. On the back of the bed was mounted an electrically driven coolant pump interlinked to the spindle control so that, instead of having to manual turn off the supply when the lathe stopped and on again when it started this was done automatically. The coolant was made to pass through a double filtering system and over three decanting walls before being drawn back up for use. Continued below:
|
|
|
|
|
|
|
|
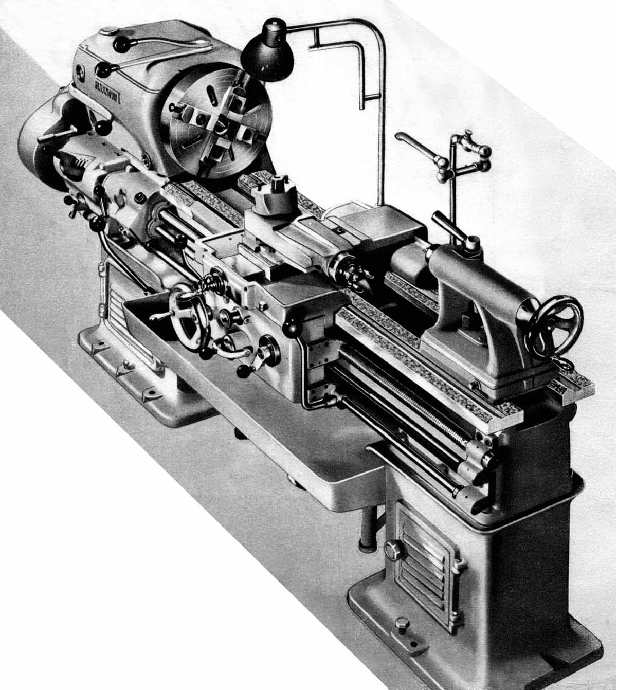 |
|
|
|
|
|
|
Maxnovo T.A.M. Lathe 210 mm (8.25-inch) centre height lathe
Continued: Although the makers claimed great rigidity for the headstock it was formed as an open-topped rectangular box sealed by a hinged lid - a design then fault then common even lathes designed for toolroom work. By way of compensation the 39 mm-diameter bore, 5 Morse taper spindle was supported at three points: at the front in a pair of precision-grade pre-loaded taper roller bearings; in the middle by a single roller bearing and at the rear a ball race. The critical setting for the pre-load on the front bearing was "sealed" (presumably against casual interference); however, the arrangement was designed so that a toothed ring could be moved slightly to alter the setting of the seal housing, but without disturbing the seal itself. With the deflection of a shaft varying in proportion to the cube of the distance from the bearing, by ensuring that the spindle was held rigidly within the headstock the makers had built in excellent anti-vibration qualities, an increasingly important characteristic in the days when the use of carbide and other hard tools capable of greatly increased rates of metal removal without overheating and wearing out were showing up the limitations of earlier machine tools. As a further aid to smooth running the main spindle gears were of helical form - the extra end thrust generated by this type confirming the need for a particularly well-supported spindle nose. All gears inside the headstock were made from chrome-nickel-molybdenum steel, case hardened and with their teeth profile ground. All shafts ran on ball or roller races and only one group of gears had to be slid into engagement, the other ratios being obtained by face dogs. Lubrication was by pump with a flow window set into the top left-hand corner of the headstock front face and a level window at the bottom right. Held within a water-tight but ventilated compartment at the rear of the headstock-end plinth. The electric motor was carried by what the makers termed an "oscillating anti-vibration system", with drive to the spindle by 3 V-belts covered by a guard that was open on the inside; from the input pulley the drive passed through an easily adjusted, oil-immersed multi-plate clutch with alternate hardened steel and phosphor bronze discs. Connected to the clutch was a powerful brake, also oil immersed and claimed to be maintenance free for its service life. The number and range of spindle speeds varied according to the model: the "A" was fitted with a 2-speed 4.5 h.p. motor that gave, as standard, 12 speeds from 39 to 760 r.p.m. or 48 to 900 r.p.m. or, alternatively at extra cost ranges of 26 to 760 r.p.m. or 32 to 900 r.p.m. The model "B" also had a 4.5 h.p. motor but with only one speed that gave 6 speeds from 39 to 380 r.p.m., 48 to 450 r.p.m. or, at additional cost: 32 to 305 r.p.m or 95 to 900 r.p.m. Control of the spindle appears to have been rather involved with a selector lever on the front of the box changing the operation of a "third-shaft" handle mounted on the right-hand face of the apron from its normal use as an electrical start, stop and reverse switch to controlling the clutch and brake. The electrical control gear was contained within in a sealed compartment, formed as an extension to the screwcutting and feeds' gearbox, with (as a rather unusual fitting) a light to show when the machine was running. Continued Below:
|
|
|
|
|
|
|
|
|
|
|
|
|
|
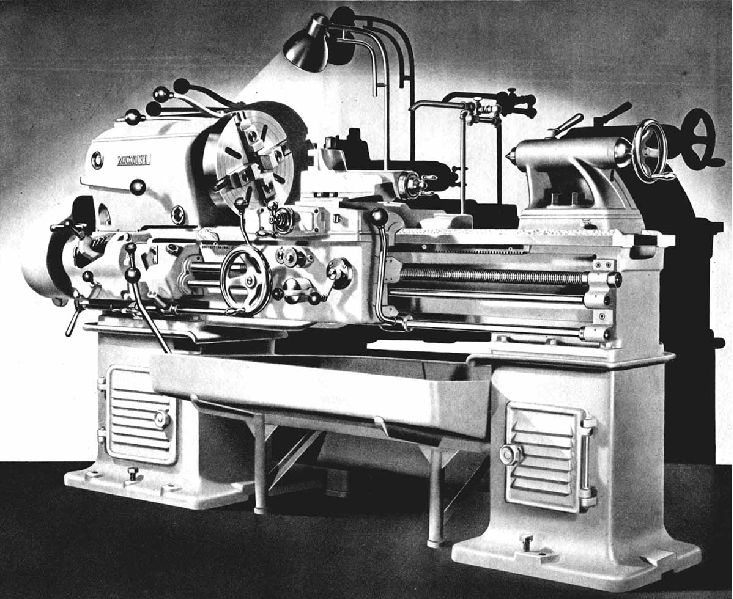 |
|
|
|
|
|
|
Continued: A separate unit of conventional, straightforward design, the screw-cutting and feeds' gearbox was bolted to the front of the bed. Selection of ratios and feeds was by a sliding tumbler and two levers that manipultaed 24 standard metric pitches from 0.5 to 7.5 mm, 12 special metric pitches from 0.6 to 12 mm, 32 English threads from 3 to 44 t.p.i and 10 Module from 0.5 to 6 were available without disturbing the changewheels with further ranges were available by the use alternative drive gears. 64 feeds were provided - sliding from 0.03 to 2.5 mm per revolution and cross feed at half that rate. The heat-treated leadscrew could be had as a metric or inch unit or, at extra cost, as a precision unit in either measurement system. The leadscrew right-hand support bearing and thrust washers were ground on all mating faces to ensure absolute alignment and the arrangement of the fitting within the screwcutting gearbox allowed for temperature expansion and contraction. An option was available to fit the lathe with an automatic threading reversing mechanism, a very useful fitting that would have saved many jobs from being spoilt, especially when threading up to a shoulder or into a blind hole. Of rugged construction, the carriage was cast in the same chrome-nickel alloy iron as the bed and also subjected to artificial aging by heat treatment. An unusual feature of the saddle was a strengthening rib formed around its top edge that was deep enough to come above the level of the cross-slide ways. A single very long chip guard (that could pass in front of the headstock) was fitted to the front right-hand saddle wing and self-adjusting, double-action wipers fitted to clean the bed ways; to lubricate them a store of oil was held within a cast-in compartment and distributed by felts. Instead of simple anti-lift keeper plates the fit of the saddle to the bed could be adjusted by proper gib strips. Formed as a box-section (though with a bolt-on rear wall for ease of construction) the apron had selection of sliding and surfacing feeds by a push/pull button and engagement though a yolk-lever-operated adjustable friction clutch that doubled as an safety overload knock-off device. The feeds could be flicked in and out of engagement with ease; the operating pressure required being the same no matter what the cutting load. Continued Below:
|
|
|
|
|
|
|
|
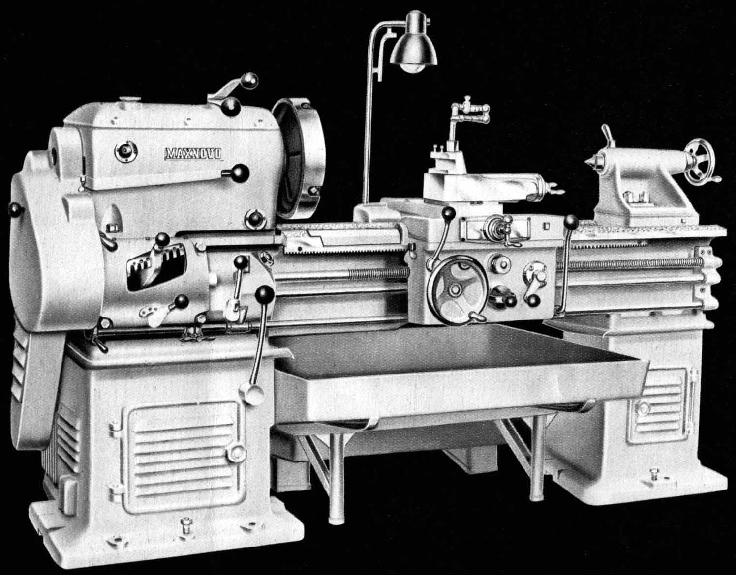 |
|
|
|
|
|
|
Continued: Heavily built, the compound slide rest assembly was built from heat-treated cast iron and employed taper gib strips. Both top and cross slide feed screws ran through ball races and, to allow backlash to be eliminated, the nuts were constructed in two halves with an adjustable wedge between them. Although the cross slide was of the short rather than full-length type an auxiliary T-slotted rear slide (with its own independently-adjustable gib strip) was available that, ingeniously, connected to the front element by a tenon joint. The satin-chrome finish micrometer dials were engraved to be "direct reading" - that is, the divisions indicated the amount that would be taken off the diameter, rather than the radius, of a workpiece. An ingenious addition to the micrometer dials was a set of adjustable sliding indexes that allowed work to be duplicated without constant measuring. The top slide was clamped down by 4 bolts and its angular degree scale properly engraved on an inserted, chrome-plated ring. Of great weight and massively constructed, the tailstock was clamped to the bed by two bolts - unfortunately each of which required the application of a loose spanner - and adjustable for off-set on the sole plate. To increase service life the bore for the ruler-graduated barrel was given a mirror-like finish by honing. Jigs to hold major parts for machining were constructed from heat-treated steel and the makers claimed patents had been taken out on methods of improving the roundness, accuracy and finish of the bores used to hold anti-friction bearings. Both "A" and "B" types were well equipped as standard: a complete coolant system; a 14-inch diameter "light-duty" 4-jaw chuck-cum-faceplate; 13 changewheels to extend the threading range of the screwcutting gearbox; a fixed steady with round, hardened and ground screw-adjusted jaws and a set of spanners. In addition the "A" had a light unit on an articulated bracket - and the preciously-mentioned 2-speed motor and control switchgear. Net weights varied from 1650 kg (3640 lbs) for the 1000 mm between-centres' model B (no motor) to 2050 kg (4410 lbs) for the 1500 mm capacity Model A..
|
|
|
|
|
|
|
|
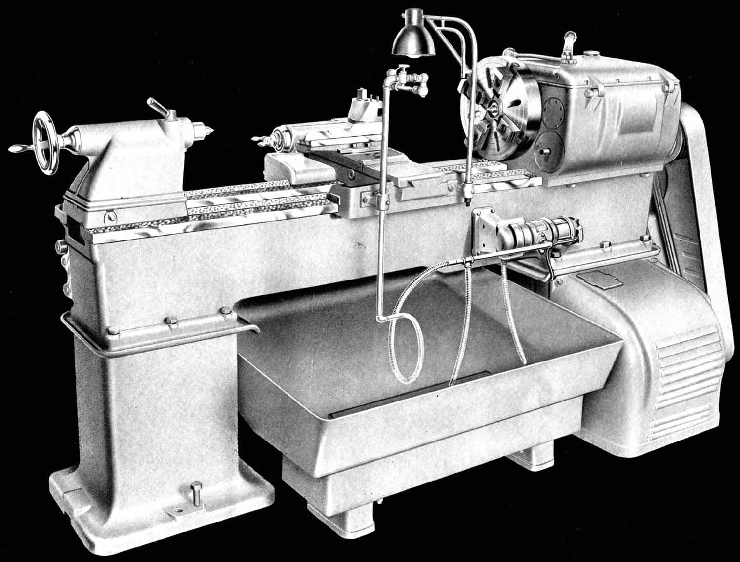 |
|
|
|
|
|
|
A rear view of the Maxnovo T.A.M. Lathe showing the large chip tray, the easily reached coolant pump and the large housing at the rear of the headstock to hold the drive motor
|
|
|
|
|
|
|
|
|
|
|
|
|
|
|
|
|
|
|