 |
 |
 |
 |
 |
 |
 |
 |
 |
 |
 |
 |
 |
 |
 |
 |
 |
 |
 |
 |
 |
 |
 |
 |
 |
 |
 |
 |
|
|
|
|
|
|
|
|
|
|
|
|
|
|
|
|
|
|
|
|
|
|
|
|
|
|
|
|
|
|
|
|
|
|
|
|
|
|
|
|
|
|
|
|
Not as well known as other Italian lathes, it appears that numbers of these machines were exported to the United States, the one-time agent being S & S Machinery of S & S Machinery of 140 53rd. Street, Brooklyn, NY 11232 and 6945 Bandini Blvd. Los Angeles 22, California. However, "Lancing", as a manufacturer, does not appear in any of the contemporary Italian machine-tool trade directories, so it's likely that S & S just chose a suitable name with which to market their imports. Although a variety of sizes was branded as Lansing, details are hard to come by - though one of the more common types to appear on the used market is the 20 and 24-inch from the 1950s, these being identical in all respects - even to their weight - and with centre heights of 10 and 12 inches respectively. The larger of the two would have been intended (as was often the case with such "jacked-up" models) for lighter work on larger diameters. Five bed lengths were listed that gave distance between centres of 40, 60, 80, 100 and 120 inches with weights of, respectively, 4900, 5100, 5700, 6000 and 6200 lbs. Braced by massive oval ribs between its walls, the heat-treated bed was 14 inches wide, exceptionally deep and fitted with a detachable gap section that allowed work to be turned on a faceplate up to 5 inches deep and 28" in diameter on the 20-inch model - and 33" on the 24-inch version. Bed ways were of the conventional V and flat type - with the front V, following contemporary fashion, made much wider and set at a shallower angle on its outside surface than the shorter and steeper inside. The bed on shorter versions was carried on cast-iron plinths, a single large one beneath the headstock and a smaller under the tailstock - though with an additional central support on the longer models; all had either one or two slide-out chip and coolant trays. Of open-box construction, the headstock had a top cover that incorporated a sight glass to check the oil flow, this being provided by a chain-driven pump lifting filtered lubricant from a tank in the plinth. Machined from a forging of a "high-alloy" steel, the No. 4 Morse headstock spindle (with a rather small bore of just 1.75") ran in a pair of precision tapered roller bearings at the front, another pair at the rear and carried an American long-taper nose in an L1 size. The central section of the spindle ran in a sealed housing (to protect the four V-belts that took the drive from an oil-bath lubricated 4-speed gearbox mounted below in the bed-support plinth) while the section immediately behind the spindle nose carried a set of gears that gave the low-speed range - the change from one to the other being made by a lever on the headstock's front face. Mounted inside the headstock end plinth was a 10 h.p. motor that drove the speed-change gearbox through five V-belts (though some examples, possibly with a more powerful motor, used six). Carrying spur gears mounted on splined shafts - all in a hardened and ground chrome nickel steel and running in precision ball races - the box incorporated a pair of heavy-duty, multi-disc clutch-cum-brakes (one for forward, the other reverse) that gave almost instantaneous starting, stopping and reverse. The drive system was carried on a large cast-iron plate that formed the rear wall of the plinth, this being adjustable, up and down, to set the tension of the final-drive belts. The rear wall was also equipped with an inspection opening through which the clutch/brake unit could be adjusted. Continued below:
|
|
|
|
|
|
|
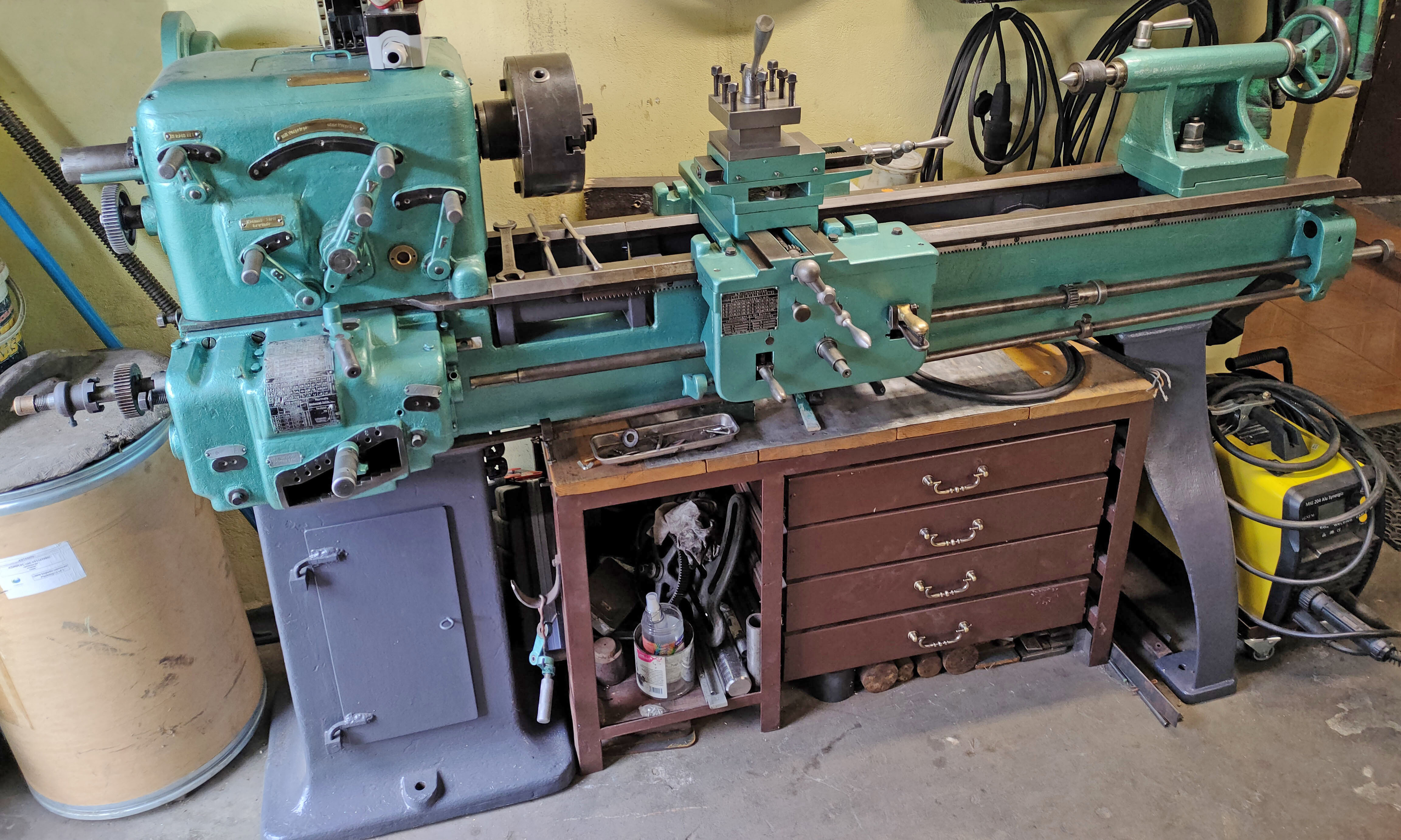 |
|
|
|
|
|
|
|
|
Continued: Electrical control of the spindle stop, start and reverse was by the usual and very convenient "third-rod" system and controlled by two levers, one just outboard of the screwcutting gearbox and the other pivoting from the apron's right-hand face. Pump lubricated with filtered oil from the same tank that supplied the headstock, the screwcutting and feeds gearbox used a Norton-pattern sliding tumbler in conjunction with lever control with drive to a 1 37/64" diameter, 2 t.p.i. leadscrew. As standard just inch pitches were provided, these totalling (with the help of an 8:1 multiplier dial) sixty-three in number and ranging from 1/2" to 56 t.p.i. Driven by a separate power shaft, ten rates of power sliding and surfacing feed were available, the range in longitudinal feed being from 0.0024" to 0.06" and across at exactly half those rates. Fitted as part of the standard equipment, a bar, extending along the full length of the bed's front face held six adjustable stops, their use in production work being a great time saver - as well as a most useful safety feature that allowed a long, slow feed to be left running with the certainty that it would safely disengage before running into the chuck or tailstock. Also offered, as an option, was a six-position stop for the power cross feed. Lubricated by an oil bath, the apron held gears and a clutch for the sliding and surfacing feeds that were selected by one lever - and engaged by another - the arrangement giving an easy in-out control no matter how deep the feed. A large diameter, 3-spoke carriage handwheel was fitted to the left (in the usual American position), its smooth rim necessitating use of the fixed handle when hands were oily... Carriage, cross and top slides were all equipped with taper gib strips, the cross slide being a full-length type with two front-to-back T-slots that could be fitted, at the rear, with a block of cast iron machined with a T-slot along its top surface that held in place a V-way slide that carried a double toolpost - each element of which could be adjusted, independently, left to right. Locked down by four bolts (and able to be adjusted in position front to rear in the T-slots), the top slide was, as standard, fitted with a T-slot holding a simple easy-to-set American "lantern" toolpost of the kind that accepted tool-bit holders by the likes of Armstrong and Jones & Shipman. Fitted with a hardened and ground 2.25-inch diameter spindle with a No. 4 Morse taper socket and 9 inches of travel, the tailstock was locked to the bed by a lever-operated eccentric cross shaft and could be set over for the turning of slight tapers. Standard equipment supplied with each new machine was generous and included a full electrical installation, coolant equipment with a powerful 2 h.p. motor, a 16-inch independent 4-jaw chuck, drive plate, two steady rests (with capacities of 4.75 and 7.5 inches), a following steady, thread-dial indicator, two Morse taper centres, light unit, a set of wrenches, grease gun and instruction book. Offered as extras were faceplates of 11, 14 and 16.5 inches in diameter, hydraulic copying, a 10.625-inch 3-jaw chuck, attachments for taper and spherical (ball) turning, an over-size, 8-inch capacity steady rest, a rear toolpost mount and twin, adjustable side-to-side tool holders, a collets attachment and various collet sets..
|
|
|
|
|
|
|
|
|
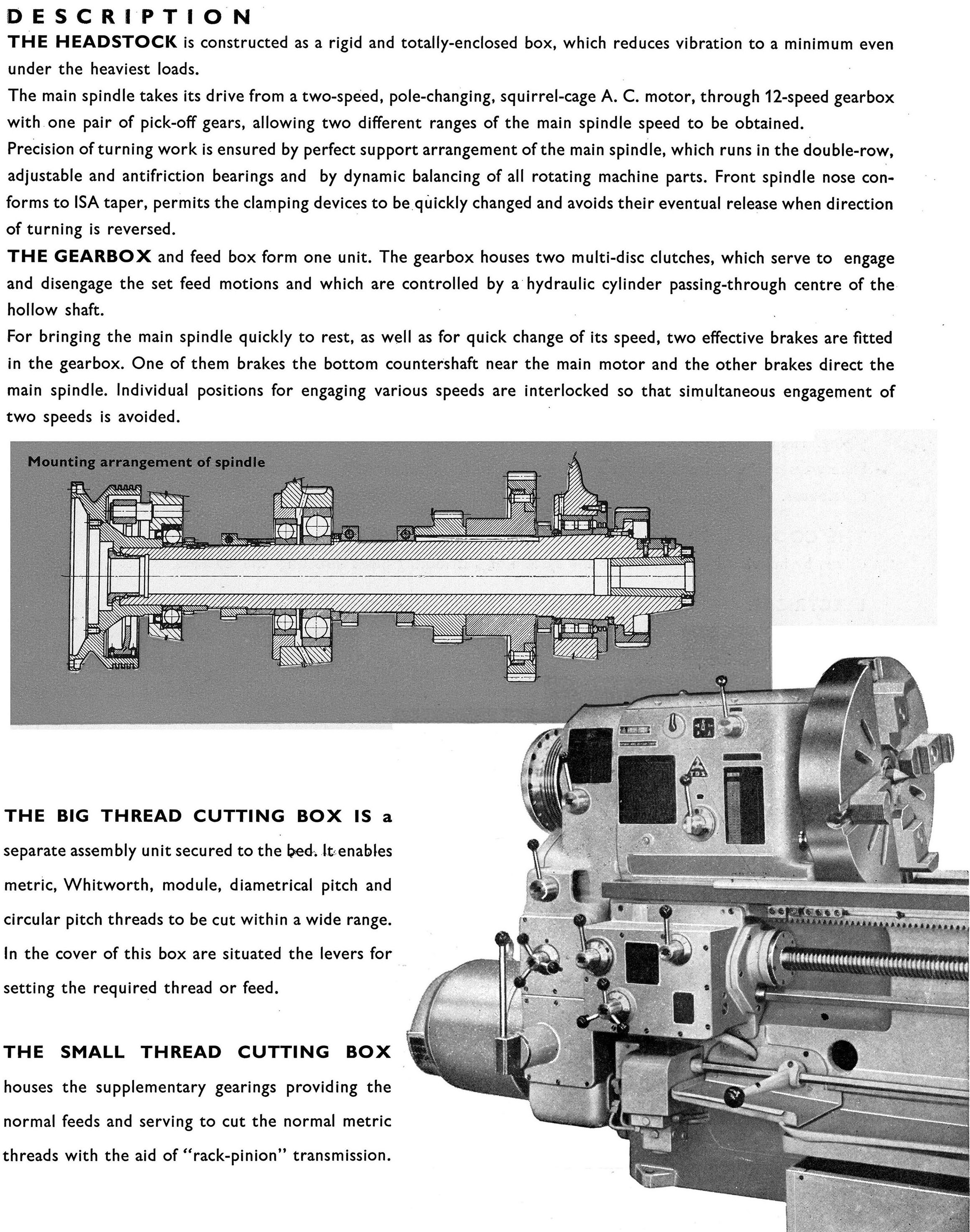 |
|
|
|
|
|
|
|
|
|
 |
|
|
|
|
|
|
Machined from a forging of a "high-alloy" steel, the No. 4 Morse headstock spindle (with a rather small bore of just 1.75") ran in a pair of precision tapered roller bearings at the front, another pair at the rear and carried an American long-taper nose in an L1 size
|
|
|
|
|
|
|
 |
|
|
|
|
|
Inside the headstock plinth showing the 10 h.p. motor on the left, the spindle-speed gearbox on the right and, in front of the gearbox, the tank holding the oil supply for the headstock and screwcutting and gearbox with its chain-driven pump
|
|
|
|
|
|
|
|
|
|
|
 |
|
|
|
|
|
Speed-change gearbox with spur gears mounted on splined shafts - all in a hardened and ground chrome nickel steel and running in precision ball races. The box incorporated a pair of heavy-duty, multi-disc clutch-cum-brakes (one for forward, the other reverse) that gave almost instantaneous starting, stopping and reverse.
|
|
|
|
|
|
|
 |
|
|
|
|
|
The drive system was carried on a large cast-iron plate that formed the rear wall of the plinth, this being adjustable, up and down, to set the tension of the final-drive belts. The rear wall was also equipped with an inspection opening through which the clutch/brake unit could be adjusted.
|
|
|
|
|
|
|
 |
|
|
|
|
|
Pump lubricated with filtered oil from the same tank that supplied the headstock, the screwcutting and feeds gearbox used a Norton-pattern sliding tumbler in conjunction with lever control with drive to a 1 37/64" diameter, 2 t.p.i. leadscrew. As standard just inch pitches were provided, these totalling (with the help of an 8:1 multiplier dial) sixty-three in number and ranging from 1/2" to 56 t.p.i. Ten rates of power sliding and surfacing feed were available, the range in longitudinal feed being from 0.0024" to 0.06" and across at exactly half those rates.
|
|
|
|
|
|
|
 |
|
|
|
|
|
|
Carriage, cross and top slides were all equipped with taper gib strips, the cross slide being a full-length type with two front-to-back T-slots that could be fitted, at the rear, with a block of cast iron machined with a T-slot along its top surface that held in place a V-way slide that carried a double toolpost - each element of which could be adjusted, independently, left to right. Locked down by four bolts (and able to be adjusted in position front to rear in the T-slots), the top slide was, as standard, fitted with a T-slot holding a simple easy-to-set American "lantern" toolpost of the kind that accepted tool-bit holders by the likes of Armstrong and Jones & Shipman.
|
|
|
|
|
|
|
 |
|
|
|
|
|
|
Fitted as part of the standard equipment, a bar, extending along the full length of the bed's front face held six adjustable stops, their use in production work being a great time saver - as well as a most useful safety feature that allowed a long, slow feed to be left running with the certainty that it would safely disengage before running into the chuck or tailstock.
|
|
|
|
|
|
|
 |
|
|
|
|
Hydraulic copying attachment with quick-change toolpost in use
|
|
|
|
|
|
|
 |
|
|
|
|
Another view of the hydraulic copying attachment showing the rear-mounted template holder and hydraulic accumulator
|
|
|
|
|
|
|
|
|
|
|
|