 |
 |
 |
 |
 |
 |
 |
 |
 |
 |
 |
 |
 |
 |
 |
 |
 |
 |
 |
 |
 |
 |
|
|
|
|
|
|
|
|
email: tony@lathes.co.uk Home Machine Tool Archive Machine-tools Sale & Wanted Machine Tool Manuals Catalogues Belts Books Accessories
lathes.co.uk Kämph FK1 Die and Mould Copying Machine
Kämph Tool and Cutter Grinder
Michael Kämph KG of Bad Homburg V.D.H., in Germany, were manufacturers of specialised, high-precision machine tools. By the 1960s their range of products included die and mould copy milling machines types FK2a, FK3, the Model B 111 engraving machine, the A 111 SUPRA geometric lathe, Model SL 1 cutter grinder and lapper, Model S 1V tool and cutter grinder, a medallion ruling machine the Model C 111, the Model SP 18 column pantograph, a rubber roller engraving machine the WG1, a step-and-repeat machine the H111, a tranfer press TP 1 and, the subject of this short description, the FK1 Die and Mould Copy Milling Machine. Designed to meet the needs of companies producing a huge range of items in materials varying from rubber to plastic to metal formed using moulds, stamped out of sheet steel, forged, die-cast or plastic-injection moulded, etc., the Kämph FK1 was used to copy the shape of an existing mould into another block of metal. Although of very high precision construction and expensive, die and mould copying machine have a simple operating mechanism with a stylus - the form of which can vary from a fine tip to a ball - guided either freehand, or against limit stops, around an existing shape. In order to copy fine details, the stylus - as on the FK1 - is normally balanced - by adjustable weights and the motion transmitted at a chosen or fixed ratio to a milling cutter held in a rotating spindle. The simplest machine in the Kämpf range, the FK1 was of the hand-operated type and copied at a fixed 1 : 1 ratio. The makers claimed that, due to its simplicity, it could be operated by semi-skilled labour with only a short period of instruction - indeed, as the finish achieved would have been "as-machined" and not the final, polished perfection required for production use (applied by skilled labour), this was, in all likelihood, a correct statement. To resist vibration, the base casting and column of the FK1 were of massive, construction, the machine standing 1780 mm (70") high, occupying a floor space of 1400 mm x 915 mm (55" x 36") and the weight a considerable 1320 kg (2910 lbs). Drive came from a 742 Watt (1 h.p.) 3-phase motor that drove through a mechanical variable-speed system to give spindle speeds that ranged from 700 to 10,000 r.p.m. - these allowing both very heavy roughing cuts to be taken and finer details machined. Speeds were changed by a full-circle handwheel tucked away under the left-hand side of the head - the chosen speed being shown by a pointer (connected to the speed-change screw feed) travelling vertically on a scale fastened to the left-hand face of the main column. Continued below:
High-resolution pictures - may take time to open
|
|
|
|
|
|
|
|
|
|
|
|
|
|
|
|
|
|
|
|
|
|
|
|
|
|
|
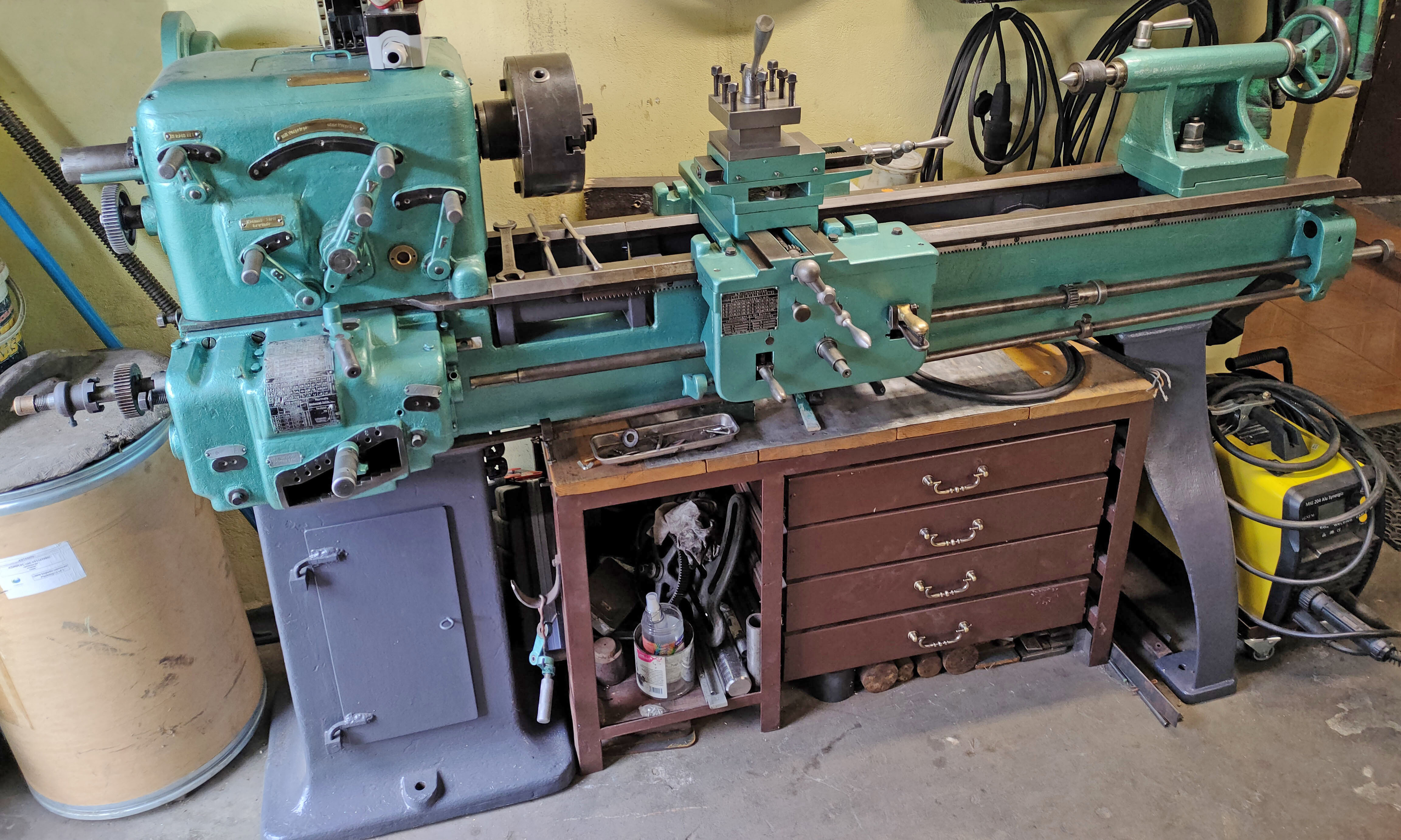 |
|
|
|
|
|
|
Continued: Mounted at the front of the machine, on a common platform able to be elevated through 300 mm (12"), was a pair of T-slotted tables, one at the front to take the master copy, the other at the back to take the workpiece. The tables were the same size - 355 mm x 300 mm (14" x 12") - and could be moved, individually, by screws equipped with micrometer dials, both towards and away from each other and to the left and right. To allow accurate setting of jobs, each table had longitudinal and traverse travel of four inches while, typical of the attention to detail found in the FK1, to prolong their accuracy and service life, all elevation screws and slideways were protected by a combination of bellows and metal covers. Although the normal maximum working area that could be covered was 255 mm x 200 mm (10" x 8") at one setting, this could be increased to 355 mm x 300 mm (14" x 12") by what the makers described as "careful readjustment" of the tables. In addition, as there was clear access at each side of the machine, it was possible to mount and clamp longer jobs, though the support column was only intended to take loads appropriate to the dimensions of the standard tables. As an aid to help with more difficult jobs, an auxiliary T-slotted work table was available to mount on either the milling or pattern table. It was possible to nudge the table 4° either side of central to help alignment of the master mould. Differences in height between the a and master could be taken up by adjustment of the stylus holder - or in combination with the use of the Auxiliary table. The 2 Morse taper milling spindle and stylus holder were set 355 mm (14") apart with cutters and stylus rods held in both by collets - the maximum capacity of the former being 12 mm (15/32") and the latter 15 mm (19/32"). The maximum distance between the end of the milling spindle and the table was 355 mm (14"), the spindle itself able to be moved through a vertical range of 75 mm (3"). Running in special, high-precision, double-row angular-contact ball races, the milling spindle was a design "proven over many years of use in similar machines"; the designer's intention was for it to be capable of taking heavy roughing cuts while being equally capable of high-quality finishes when using tiny cutters running at high r.p.m. Milling on the FK1 could be by "line motion" - where one motion of the milling head in the horizontal plane was locked and the feed applied by hand or against pre-set stops - or "contour milling" where both horizontal motions of the head were free and the feed of milling depth applied in steps. In addition, "free copying" was also possible where all motions were unlocked. Operator control was by the use of a vertically disposed control lever, tipped with black plastic knobs, and fitted with adjustable balance weights that enabled fine details to be better followed. Today, die and mould copying has, like many machine-tool operations, been computerised, the result being a reduction in the time required to complete jobs combined with an improvement in the quality of the work produced..
|
|
|
|
|
|
|
|
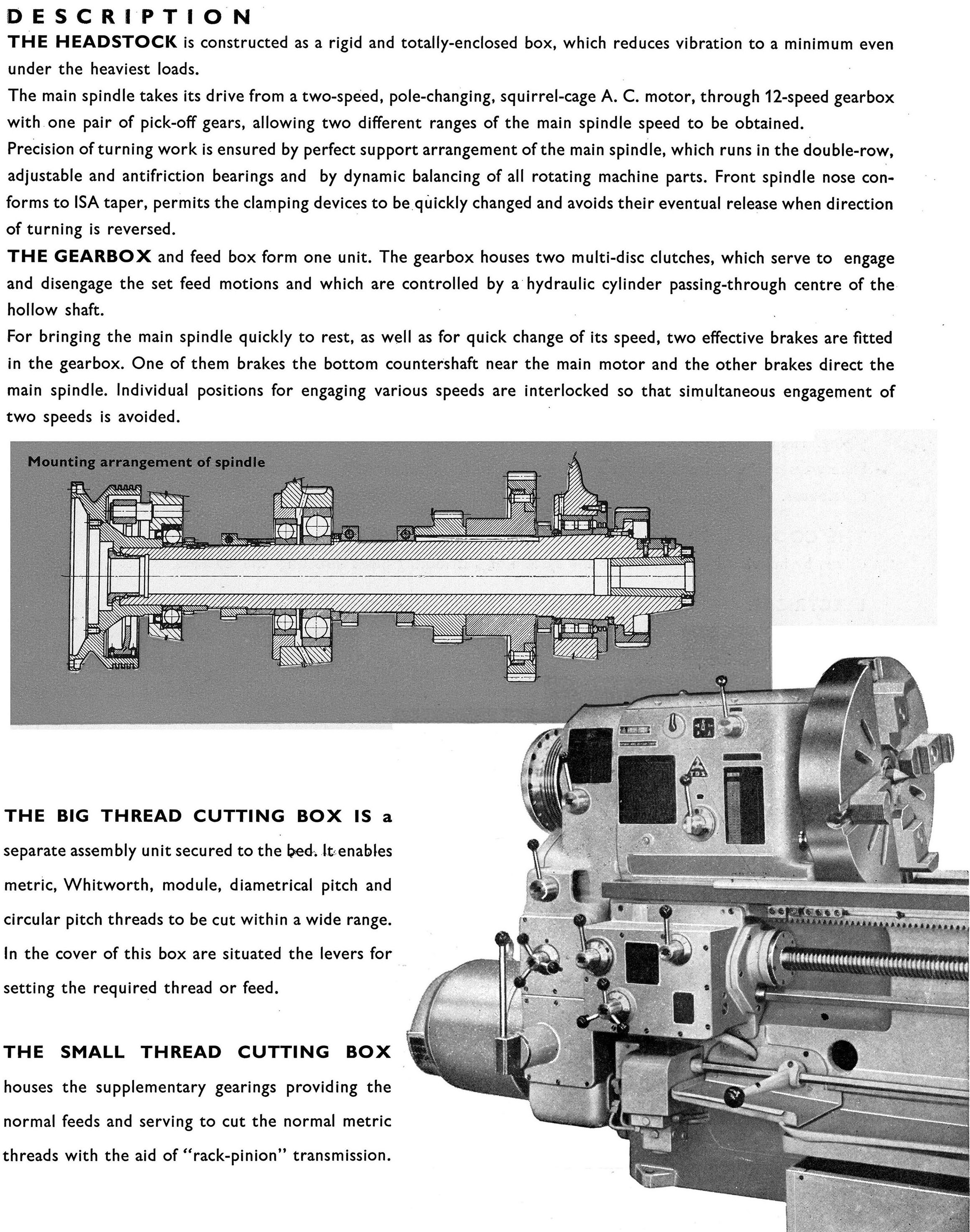 |
|
|
|
|
|
|
Drive came from a 742 Watt (1 h.p.) 3-phase motor that drove through a mechanical variable-speed system to give spindle speeds that ranged from 700 to 10,000 r.p.m. - these allowing both very heavy roughing cuts to be taken and finer details machined. Speeds were changed by a full-circle handwheel tucked away under the left-hand side of the head - the speed chosen being shown by a pointer (connected to the speed-change screw feed) travelling vertically on a scale fastened to the left-hand face of the main column.
|
|
|
|
|
|
|
|
 |
|
|
|
|
|
|
Operator control was by the use of a vertically disposed control lever, tipped with black plastic knobs, and fitted with adjustable balance weights that enabled fine details to be better followed.
|
|
|
|
|
|
|
|
|
|
|
|
 |
|
|
|
|
|
|
An auxiliary T-slotted work table was available to mount on either the milling or pattern table. It was possible to nudge the table 4° either side of central to help alignment of the master mould. Differences in height between the a and master could be taken up by adjustment of the stylus holder - or in combination with the use of the Auxiliary table.
|
|
|
|
|
|
|
|
 |
|
|
|
|
|
|
Running in special, high-precision, double-row angular-contact ball races, the milling spindle was a design "proven over many years of use in similar machines"; the designer's intention was for it to be capable of taking heavy roughing cuts while being equally capable of high-quality finishes when using tiny cutters running at high r.p.m.
|
|
|
|
|
|
|
|
|
|
 |
|
|
|
|
|
|
|
|
|
Milling on the Kämph FK1 could be by "line motion" (left illustration) - where one motion of the milling head in the horizontal plane was locked and the feed applied by hand or against pre-set stops - or "contour milling" (right illustration) where both horizontal motions of the head were free and the feed of milling depth applied in steps. In addition, "free copying" was also possible where all motions were unlocked.
|
|
|
|
|
|
|
|
|
|
|
|
|
|
|
|
|
|