 |
 |
 |
 |
 |
 |
 |
 |
 |
 |
 |
 |
 |
 |
 |
 |
 |
 |
 |
 |
 |
 |
 |
 |
 |
 |
 |
 |
 |
 |
 |
 |
 |
 |
 |
 |
 |
 |
 |
 |
 |
 |
 |
 |
 |
 |
 |
 |
 |
 |
 |
 |
 |
 |
 |
 |
 |
 |
 |
 |
|
|
|
|
|
|
|
|
|
|
|
|
|
|
|
|
|
|
|
|
|
|
|
|
|
|
|
|
|
|
|
|
|
|
|
|
|
|
|
|
|
|
|
|
|
|
|
|
|
|
|
|
|
|
|
|
|
|
|
|
|
|
|
|
|
|
|
|
|
|
|
|
email: tony@lathes.co.uk Home Machine Tool Archive Machine-tools for Sale & Wanted Manuals Catalogues Belts Books Accessories
Juvenia Lathes Switzerland
Based in La-Chaux-de-Fonds, at the heart of Switzerland's precision watch and engineering area, the Juvenia Watch Company manufactured top quality, hand-made timepieces - though it's possible that their lathes were badge-engineered from another makers. Who might they have been? Ones that come to mind - and show some similarities with their products - include Waltham in the USA (known to have exported to Switzerland) - and some Swiss-based makers, possibly Agathon or even Mikron (Bergeon or Favorite from the French-speaking cantons might also be in contention). However, it is entirely possible that the machines were produced in-house - for Juvenia marketed not only a range of precision bench lathes but also (shown towards the bottom of this page) a beautifully designed and desirable - if strangely conceived - geared headstock lathe with a complex screwcutting gearbox - yet with its carriage and bed arranged along plain-turning lines. A further connection between Juvenia and the U.S.A. was through the firm of Breguet Frères & Cie. based in Le Locle, the twin town of La-Chaux-de-Fonds situated just five miles away. The Breguet lathe also bore an uncanny resemblance to the Waltham and may well have been another "branded" machine imported through the Waltham's Swiss agent, Mr. L.Ariste Gindrat. In addition to their standard, quite-ordinary bench precision lathe, Juvenia also offered a most unusual machine, plain-turning lathe but fitted with geared headstocks and, quite incredibly, a most complex slide-on-and-off screwcutting and feed gearbox. With a centre height of 110 mm (4 inches), a between-centres capacity of around 600 mm (20 inches), weighing 160 Kg (252 lbs) and powered by a 0.22 h.p. 1400 r.p.m. motor, Juvenia listed this lathe as their Universal Turner's Lathe. The bed featured twin V and flat carriage ways, with very distinctive, robustly proportioned T-slots down the top and both front and back faces - and was identical in form to that used on the maker's ordinary bench lathes. However, instead of being a simple flat-belt drive unit, the headstock was an oil-bath, all-geared type, with an amazing 20 speeds (7, 10, 13, 17, 22, 29, 38, 48, 63, 81, 105, 139, 177, 232, 299, 394, 513,656,861 and 1087 r.p.m.) driven by a motor mounted on the back of the lathe driving into the headstock not through belts but, using more expensive complexity, by a universally-jointed shaft. Speeds were selected by a quadrant lever on the left-hand face of the headstock in combination with a centrally-mounted rotary control that gave 4 speeds for each setting of the quadrant. The headstock spindle was "clutched" and engaged by a second quadrant lever on the right-hand face of the headstock. Made from carbon steel the headstock gears were hardened to either 70 kg per mm2 (for the lightly loaded components) to 110 kg per mm2 for those under the heaviest stress. Also in carbon steel, the headstock spindle ran in bronze bearings (with their own, separate, lubrication system) and was fitted with a threaded nose. The draw-in collet fitting was described by the makers as designed for a 70 mm Waltham chuck - ("chuck" is the term used by watchmakers for collet) - a reference that would seem to confirm a link between the two companies. In contrast to the sophistication of the headstock, the carriage was unable to slide along the bed and was bolted in place, the long-travel top slide providing the longitudinal feed. Perhaps the most amazing feature ever found on a plain-turning, precision toolmakers' lathe was the slide-on-and-off screwcutting and power feed gearbox, this being held by two bolts into the bed's front T-slot. The box could generate metric and English threads and also "Lowenhertz" pitches of gauge 0.25 to 2.5 for manufacturing worm milling cutters. Three power take-offs emerged from the box: one drove the top slide for screwcutting, another provided power (also through a jointed shaft) to a worm gearbox on top of the vertical milling attachment - whilst the third was for connection to a backing-off attachment, a fitting necessary in the production of milling cutters. Advertised as being an "...all-purpose machining centre…", the lathe was supplied complete with a wide range of accessories including a full set of wire, stepped and other collets, a "tracing table"; a universal vertical milling and helical gear-cutting attachment that was capable of being power driven; a dividing attachment - with worm drive - that fastened to the left-hand end of the headstock and a toolpost-mounted grinding attachment driven (rather neatly) though a flexible cable powered from a small countershaft (held in the rear T-slot of the bed) - itself turned by a belt from a pulley on the main motor. Juvenia lathes are rare, with few known. However, besides those few found in Europe one example (shown in the first picture below) has been discovered in the United States. Hence, should you have machine tool of any kind produced by Juvenia, the writer would be very interested to hear from you..
|
|
|
|
|
|
|
|
|
|
|
|
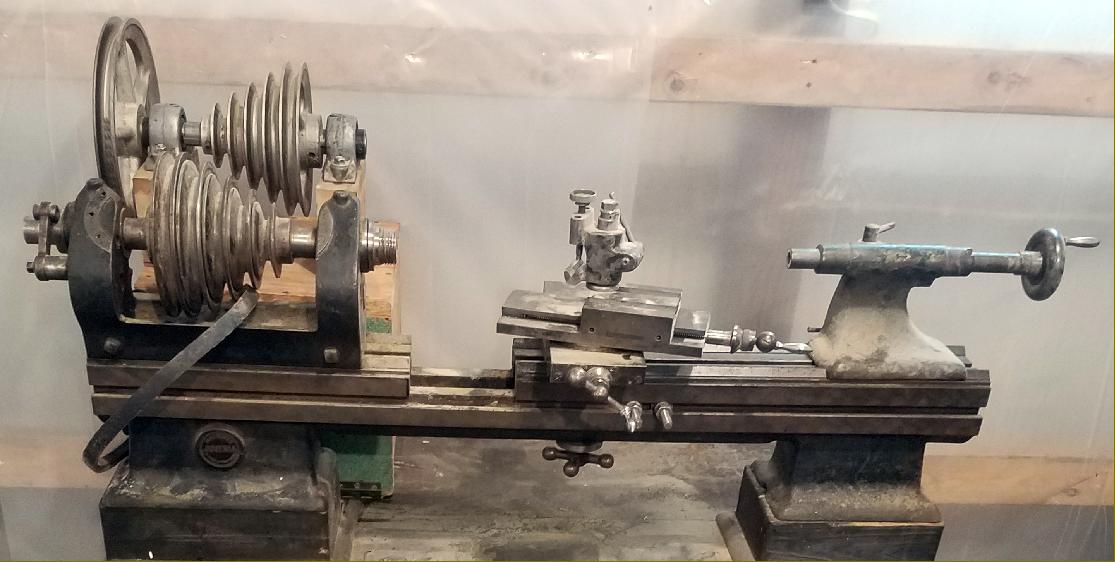 |
|
|
|
|
|
|
|
|
|
What may be an earlier Juvenia precision bench lathe with a 5-step V-belt drive headstock pulley and a screw-feed compound slide-rest assembly
|
|
|
|
|
|
|
|
|
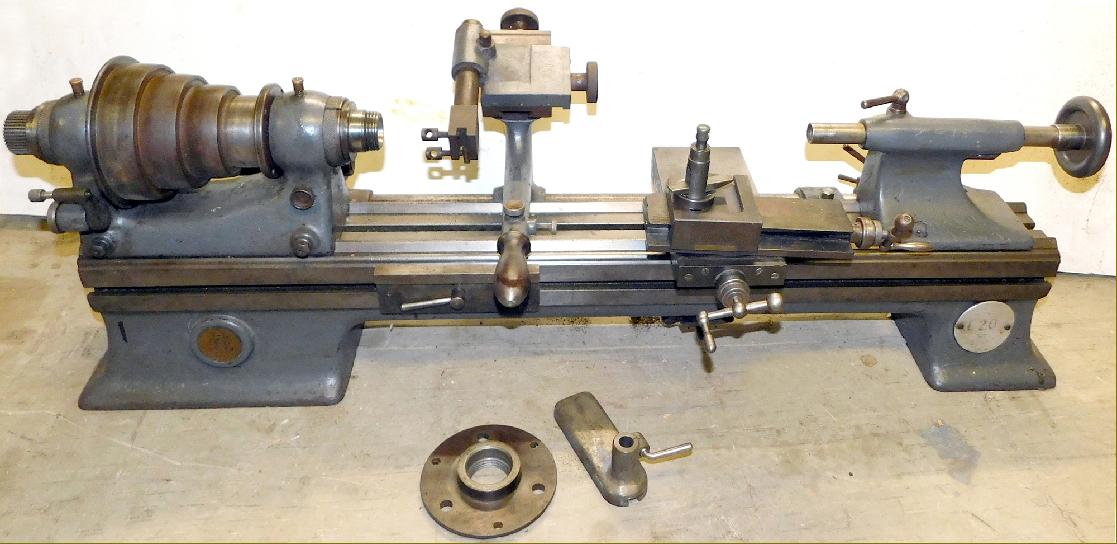 |
|
|
|
|
|
|
|
Juvenia precision bench with a 4-step flat-belt cone pulley, chase screwcutting and a screw-feed a compound slide-rest assembly This lathe may have been constructed for production use in a watch and clock factory
|
|
|
|
|
|
|
|
|
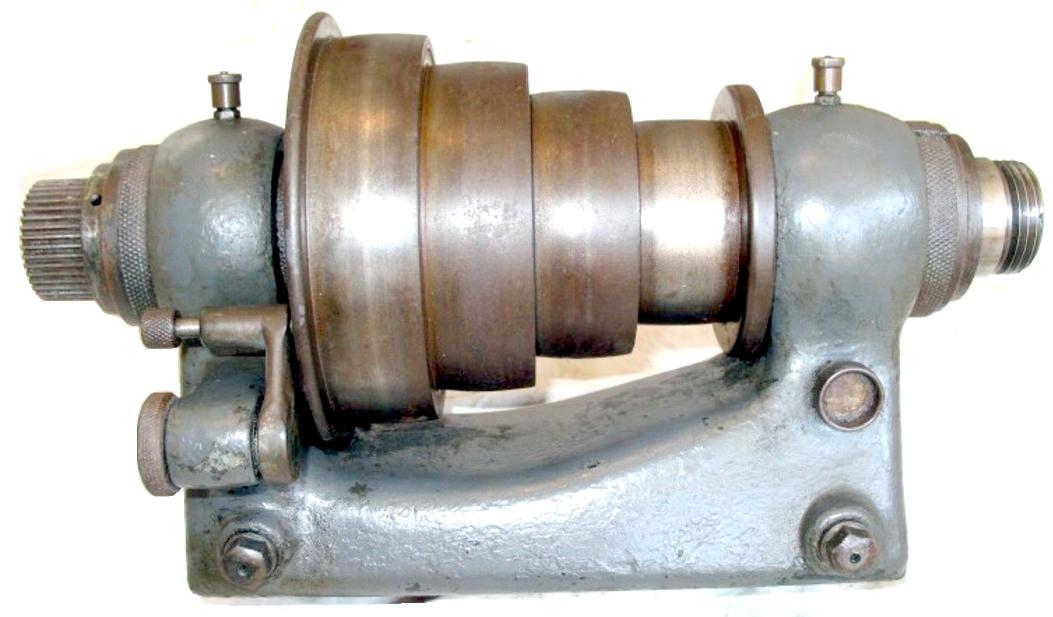 |
|
|
|
|
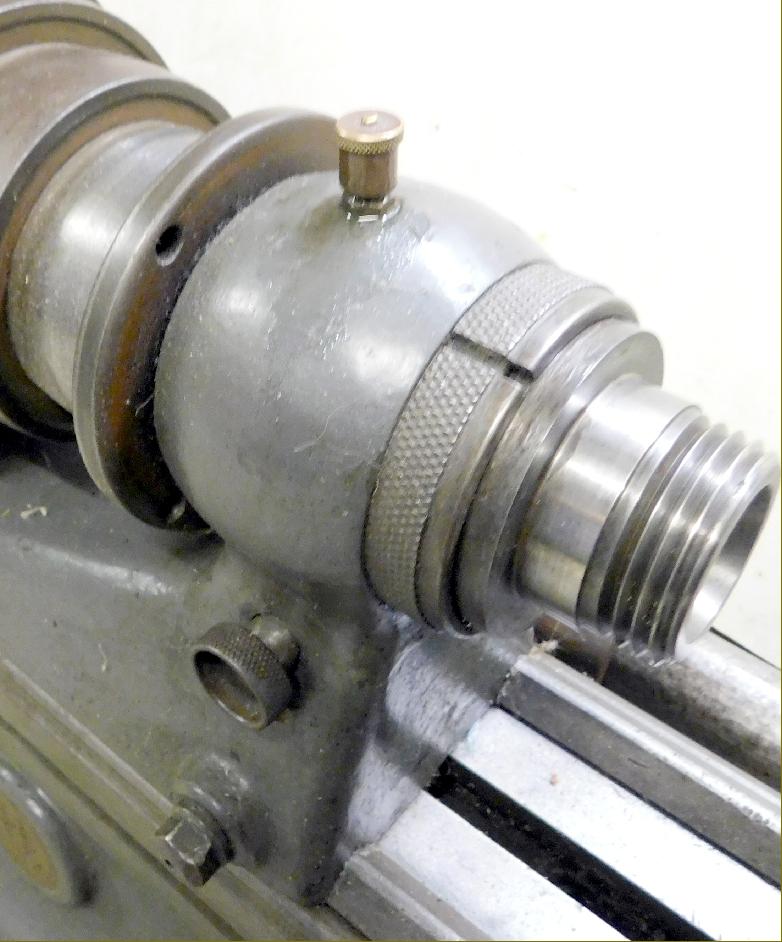 |
|
|
|
|
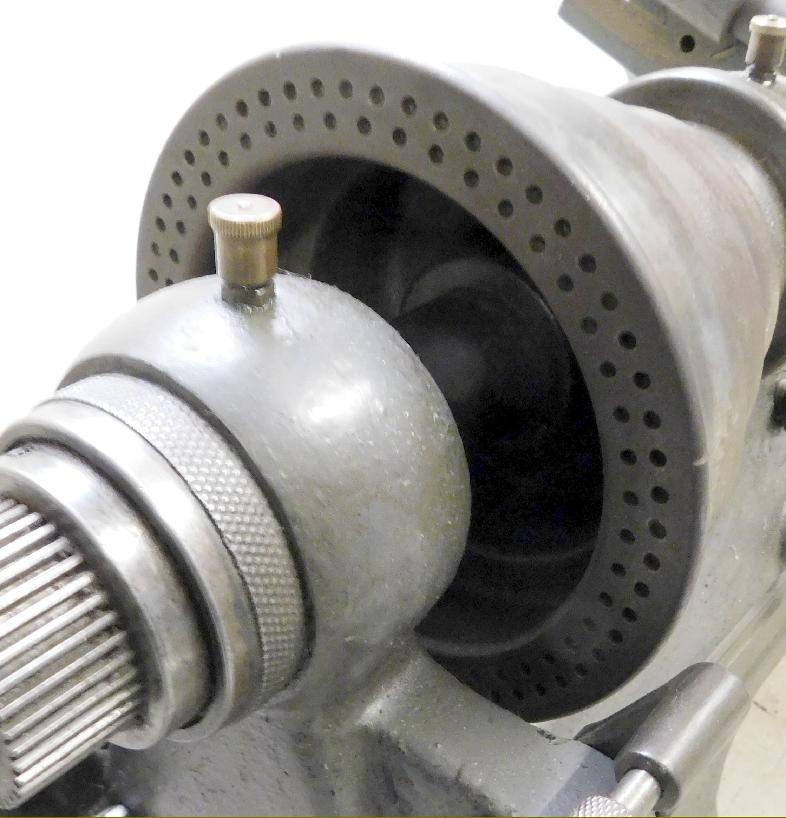 |
|
|
|
|
|
|
|
|
|
Found on most bench precision lathes: two circles of indexing holes drilled into to flange of the largest headstock pulley
|
|
|
|
|
|
|
|
|
|
|
|
|
|
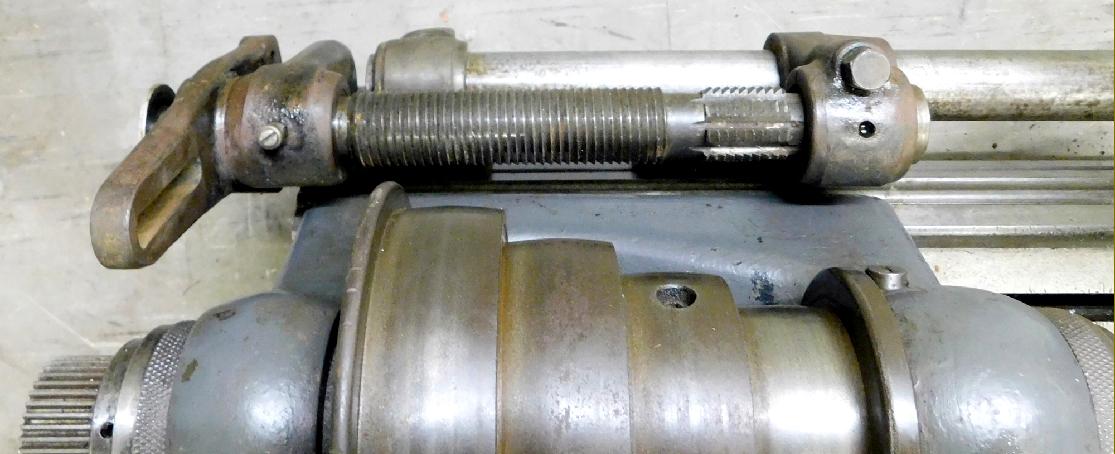 |
|
|
|
|
|
|
|
|
|
|
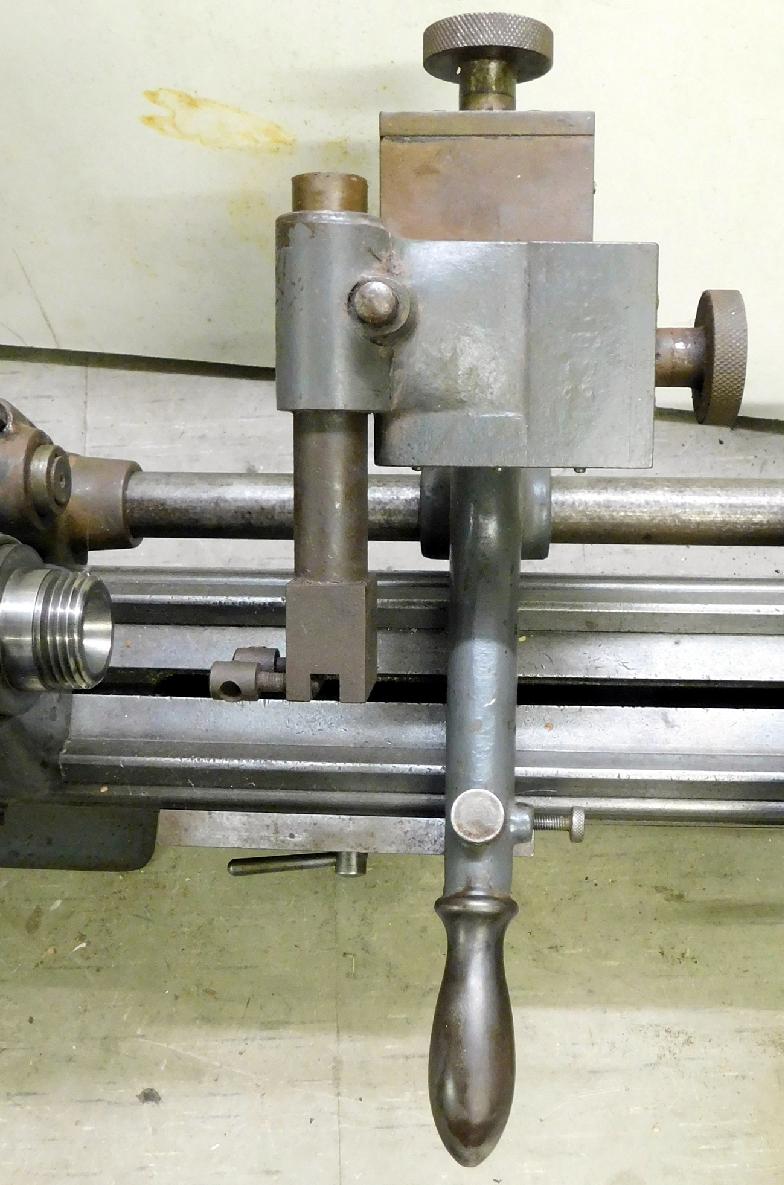 |
|
|
|
|
|
|
|
|
|
Above and below: "operating arm" of the chase screwcutting attachment
|
|
|
|
|
|
|
|
|
|
|
|
|
|
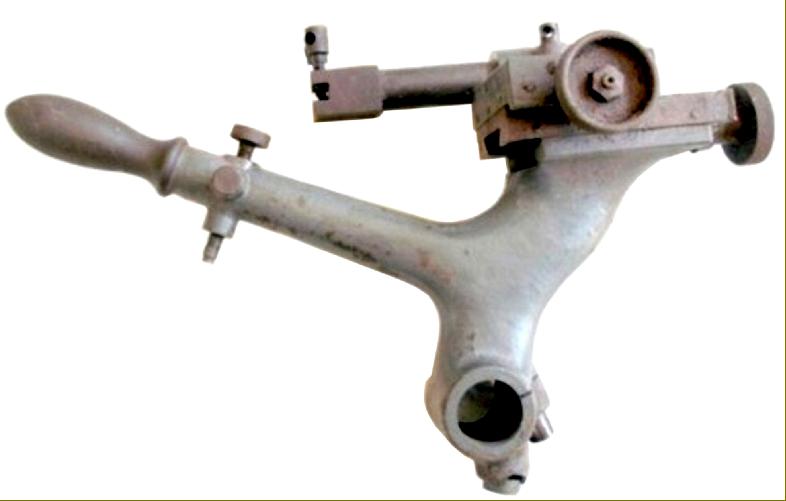 |
|
|
|
|
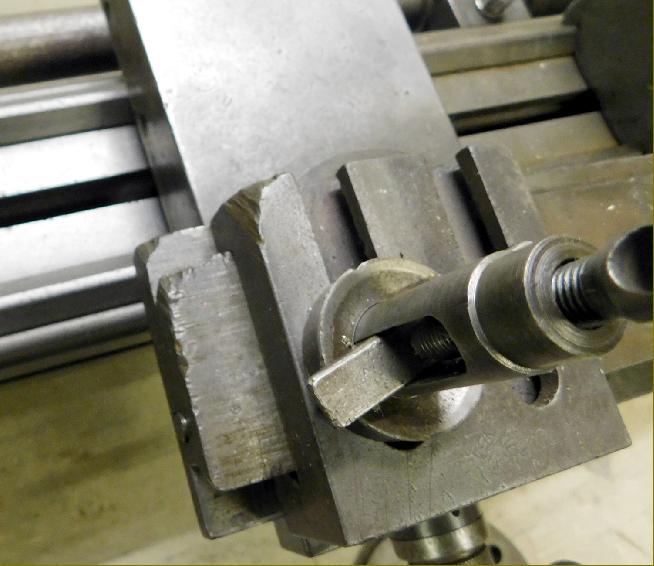 |
|
|
|
|
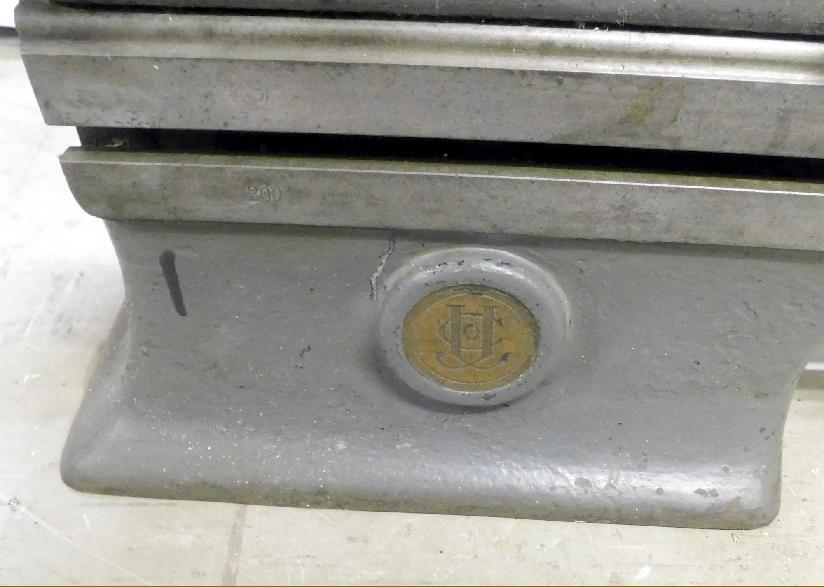 |
|
|
|
|
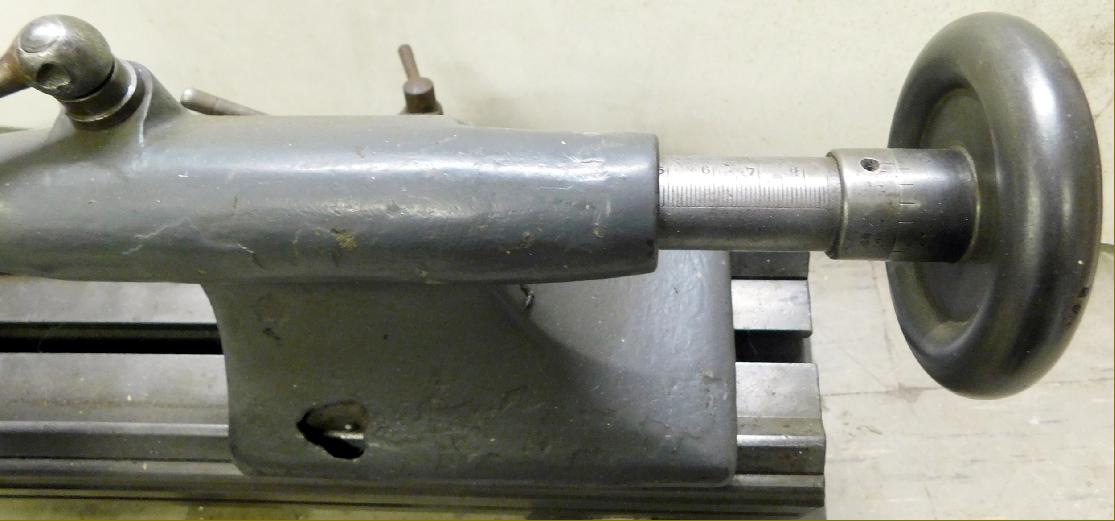 |
|
|
|
|
|
|
|
|
|
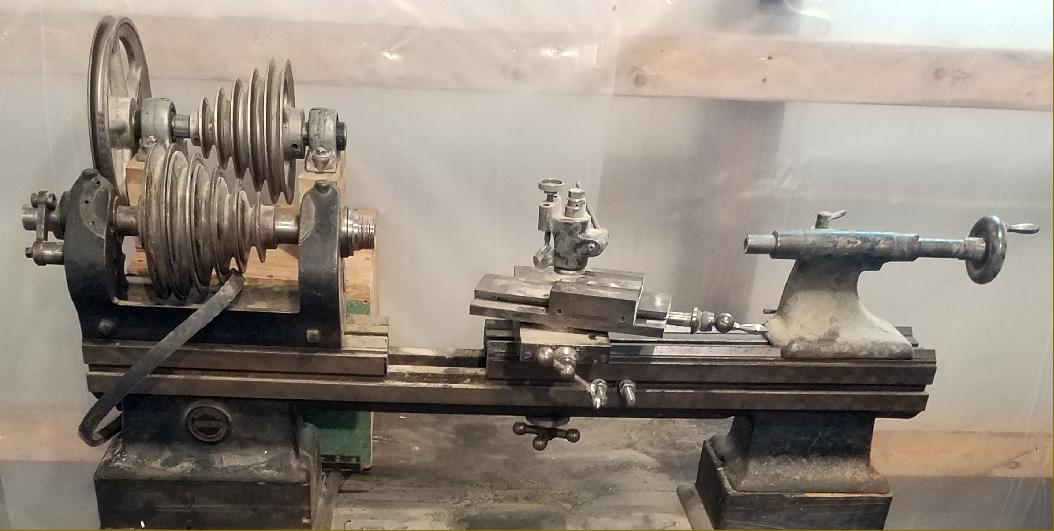 |
|
|
|
|
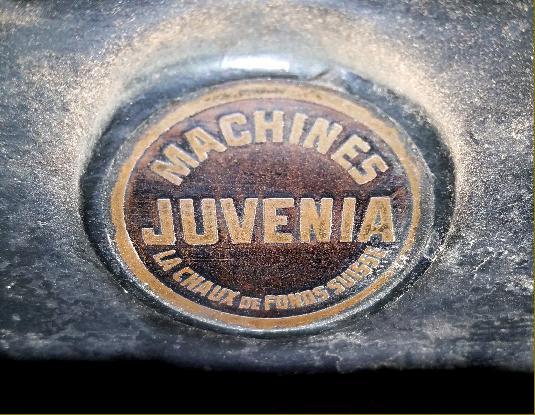 |
|
|
|
|
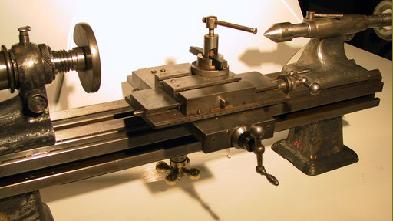 |
|
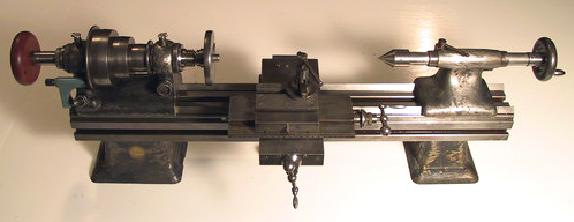 |
|
|
|
|
|
|
|
|
|
Of conventional "precision bench lathe" appearance - and similar to the American Waltham - the plain-turning Juvenia precision was distinguished by an unusually wide top slide that carried two T-slots.
|
|
|
|
|
|
|
|
|
|
|
|
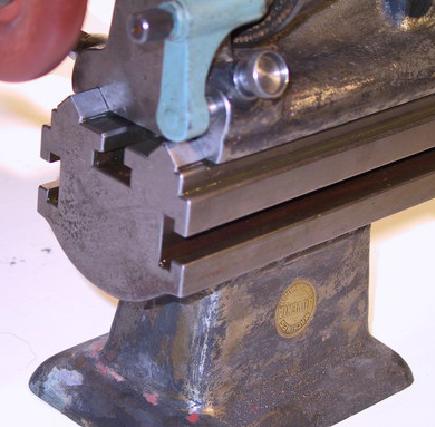 |
|
|
|
 |
|
|
|
|
|
|
|
|
|
|
T-slots at the front and back of the bed - a feature of all Juvenia lathes - point to the likelihood that both chase-screwcutting and power-feed to the top slide were on list of available options
|
|
|
|
|
|
|
|
|
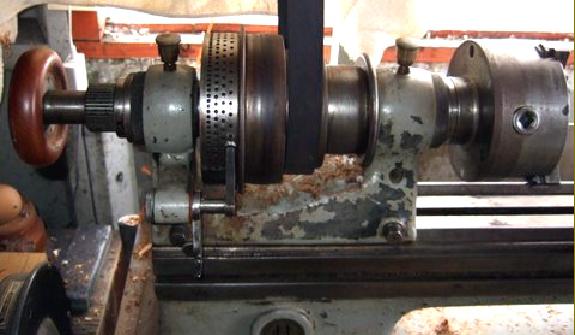 |
|
|
|
|
|
Juvenia precision plain-turning lathe with an epicyclic reduction gear fitted inside an extension to the flat-belt drive headstock pulley. With no space to drill rings of division holes in the outside flange of the housing (as would have normally been provided) instead they were bored into its face. This unusual arrangement called for a boss to be cast integral with the headstock to hold a suitable location arm.
|
|
|
|
|
|
|
|
|
|
|
|
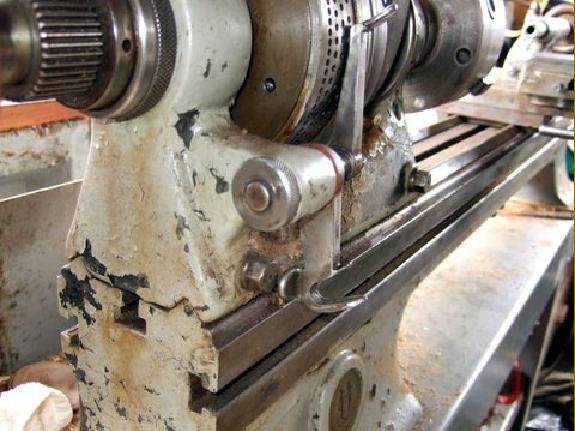 |
|
|
|
|
|
|
|
|
|
Above and below: views showing the spindle indexing arm assembly and, concentric to it and hanging downwards, a "hook" used to withdraw the pin that locked the epicyclic gears into their non-operable position.
|
|
|
|
|
|
|
|
|
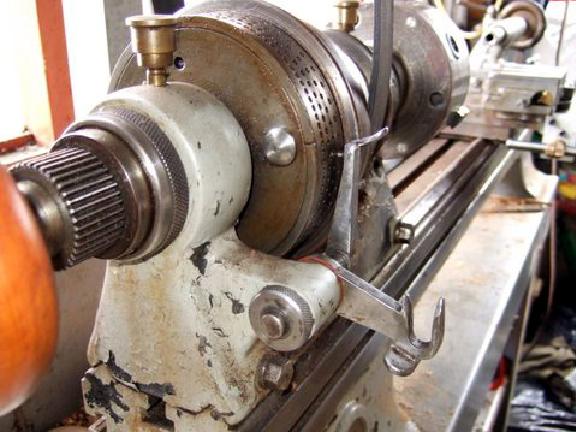 |
|
|
|
|
|
|
|
On the end face of the pulley extension can be seen a shiny domed button - this is the head of a pin which, when withdrawn, allows the epicyclic gears to operate (once another pin has been screwed into the housing). The end of the forked arm was shaped with a sharp edge so that it fitted behind the head of the button and, as it was pressed inwards, drew it outwards and secured it against further movement
|
|
|
|
|
|
|
|
|
|
|
|
|
|
|
|
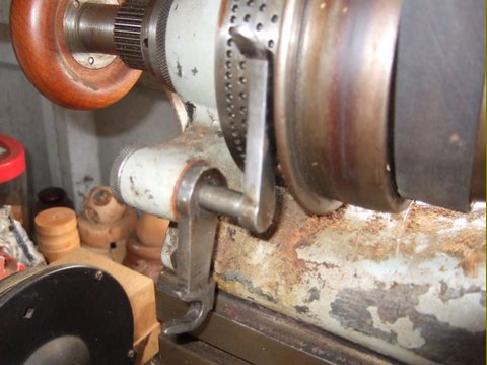 |
|
|
|
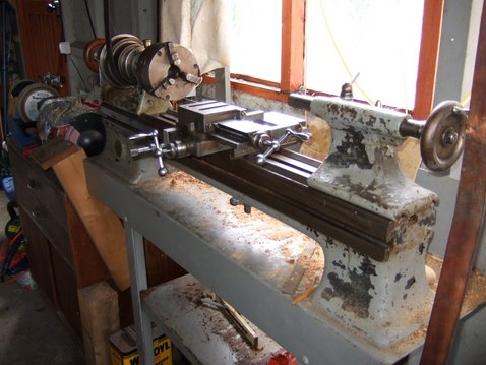 |
|
|
|
|
|
|
|
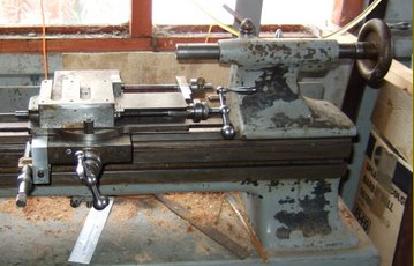 |
|
|
|
|
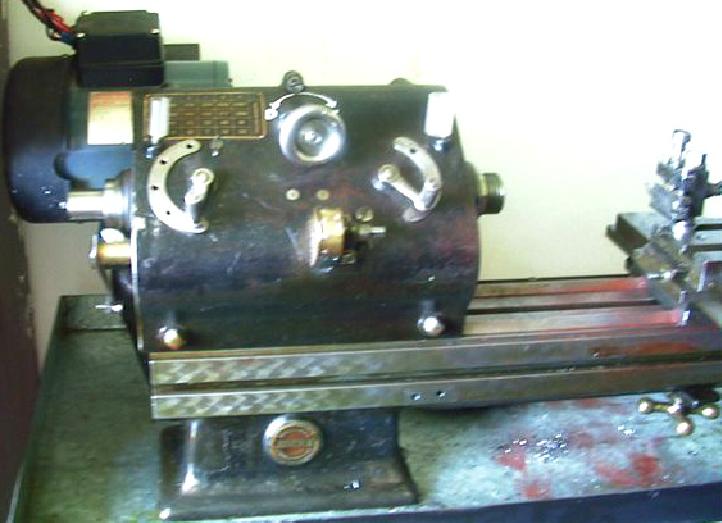 |
|
|
|
|
|
|
The astonishingly different Juvenia with a geared-headstock and the ability to take a slide-on-slide-off screwcutting gearbox. Its name appears to have been the "Universal Turner's Lathe. In this picture the gearbox is removed
|
|
|
|
|
|
|
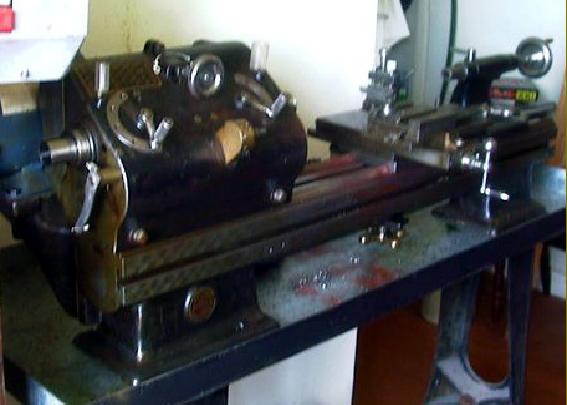 |
|
|
|
|
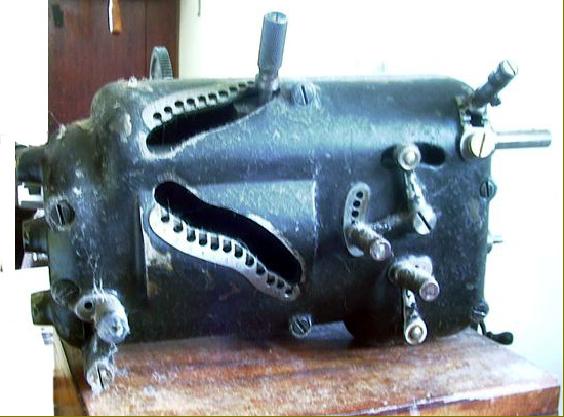 |
|
|
|
|
|
|
|
The remarkably complex slide-on, slide-off screwcutting and power feeds gearbox
|
|
|
|
|
|
|
|
|
|
|
|
|
|
|
|
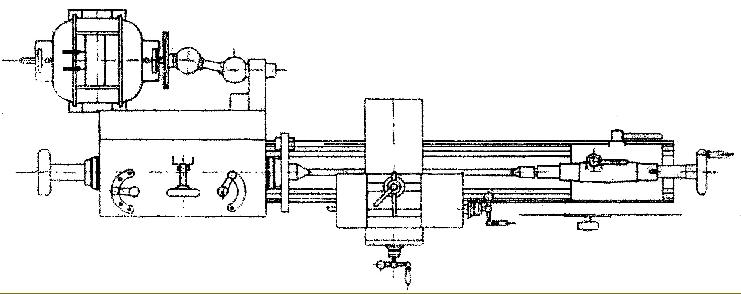 |
|
|
|
|
|
|
|
|
|
Note the unusual layout of the drive system with motor connected to the headstock through a universally-joined shaft.
Left: bed section of the lathe with "V" ways, T-slots on both front and back faces
|
|
|
|
|
|
|
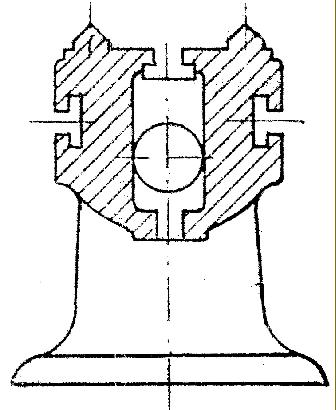 |
|
|
|
|
|
|
|
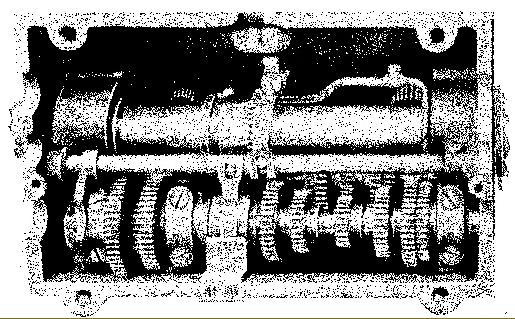 |
|
|
|
|
|
|
|
A view into the 20-speed headstock
|
|
|
|
|
|
|
|
|
|
|
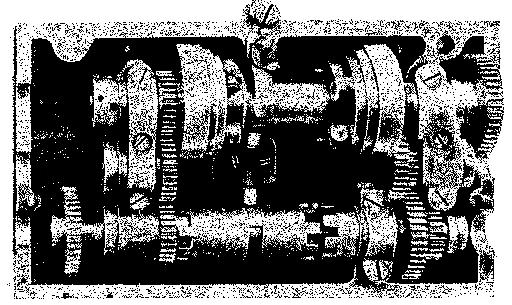 |
|
|
|
|
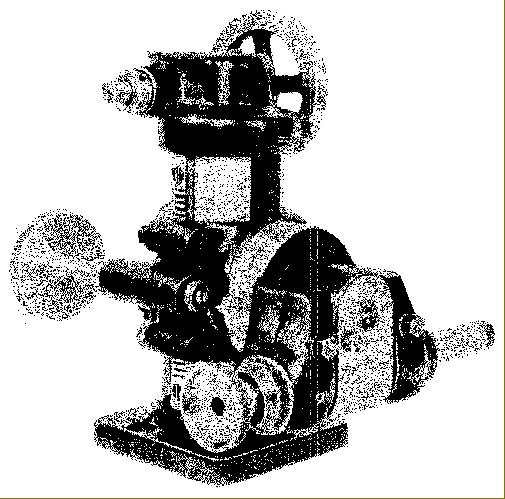 |
|
|
|
|
|
|
|
The complex milling and gear-cutting attachment. A shaft from the screwcutting gearbox could be attached to a worm gearbox built into the top of the unit.
|
|
|
|
|
|
|
|
|
|
|
|
|
|
|
|
|
|