 |
 |
 |
 |
 |
 |
 |
 |
 |
 |
 |
 |
 |
 |
 |
 |
 |
 |
 |
 |
 |
 |
 |
 |
 |
 |
 |
 |
 |
 |
 |
|
|
|
|
|
|
|
|
|
|
|
|
|
|
|
|
|
|
|
|
|
|
|
|
|
|
|
|
|
|
|
|
|
|
|
|
|
|
|
|
|
|
|
|
|
|
|
|
|
|
|
|
|
|
The pictures below span from the mid 1920 until the late 1940s and show views within what was known as the "Main Works" - covering and extending beyond land at the Butts, in central Coventry, where the Company had first set up in 1889. Other illustrations were taken within the branch factory at Edgwick, on the north-east boundary of the city - a 23-acre site where a pattern shop, three foundries - Heavy for iron up to 5 tons, Light for smaller items and another for bronze and aluminium - a chemical and physical laboratory, a machine shop, erecting shop - and a sports ground were situated.
|
|
|
|
|
|
|
|
|
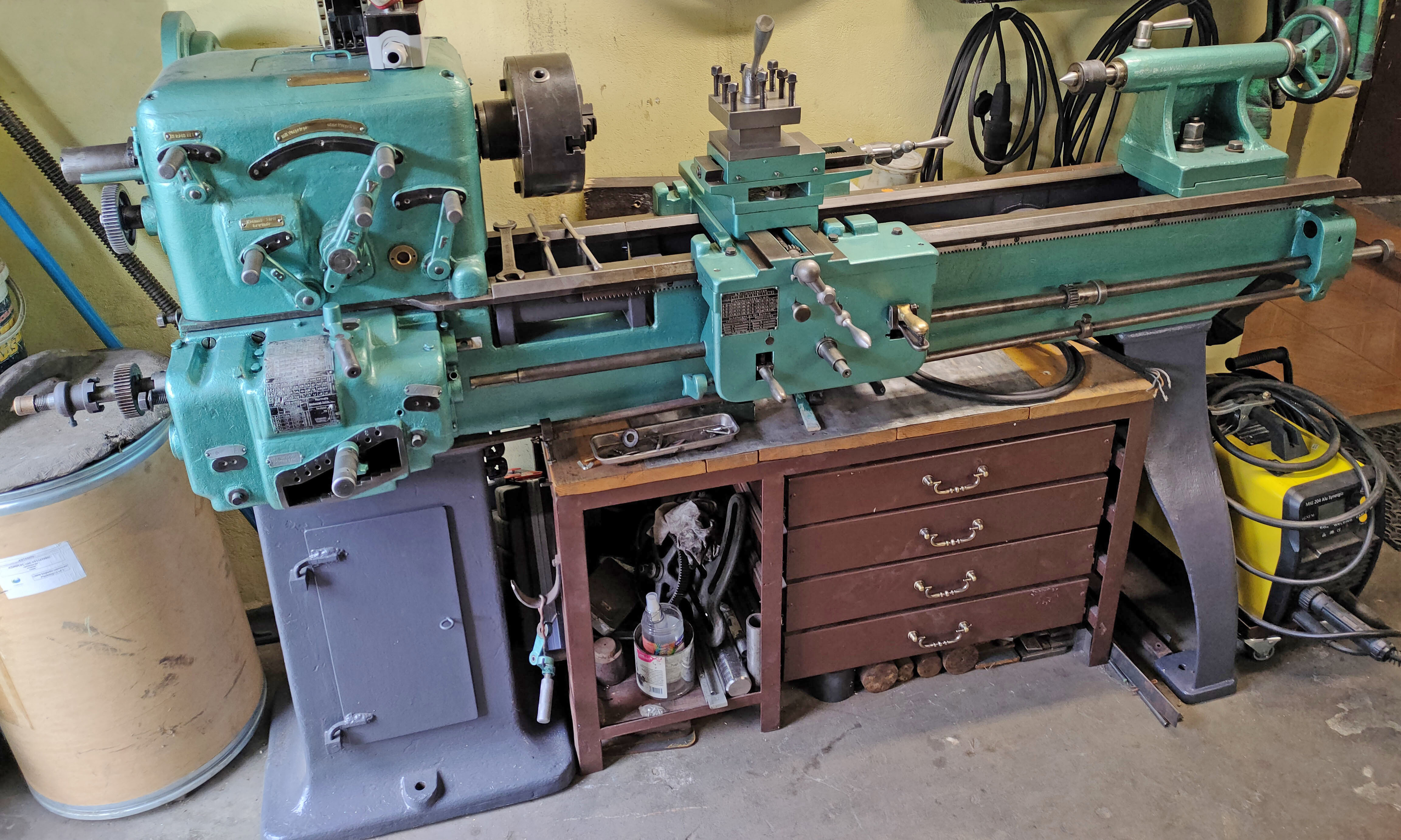 |
|
|
|
|
|
|
Late 1940s and the Capstan Lathe Department at Herbert's Head Works (central Coventry) - making parts for other capstan lathes
|
|
|
|
|
|
|
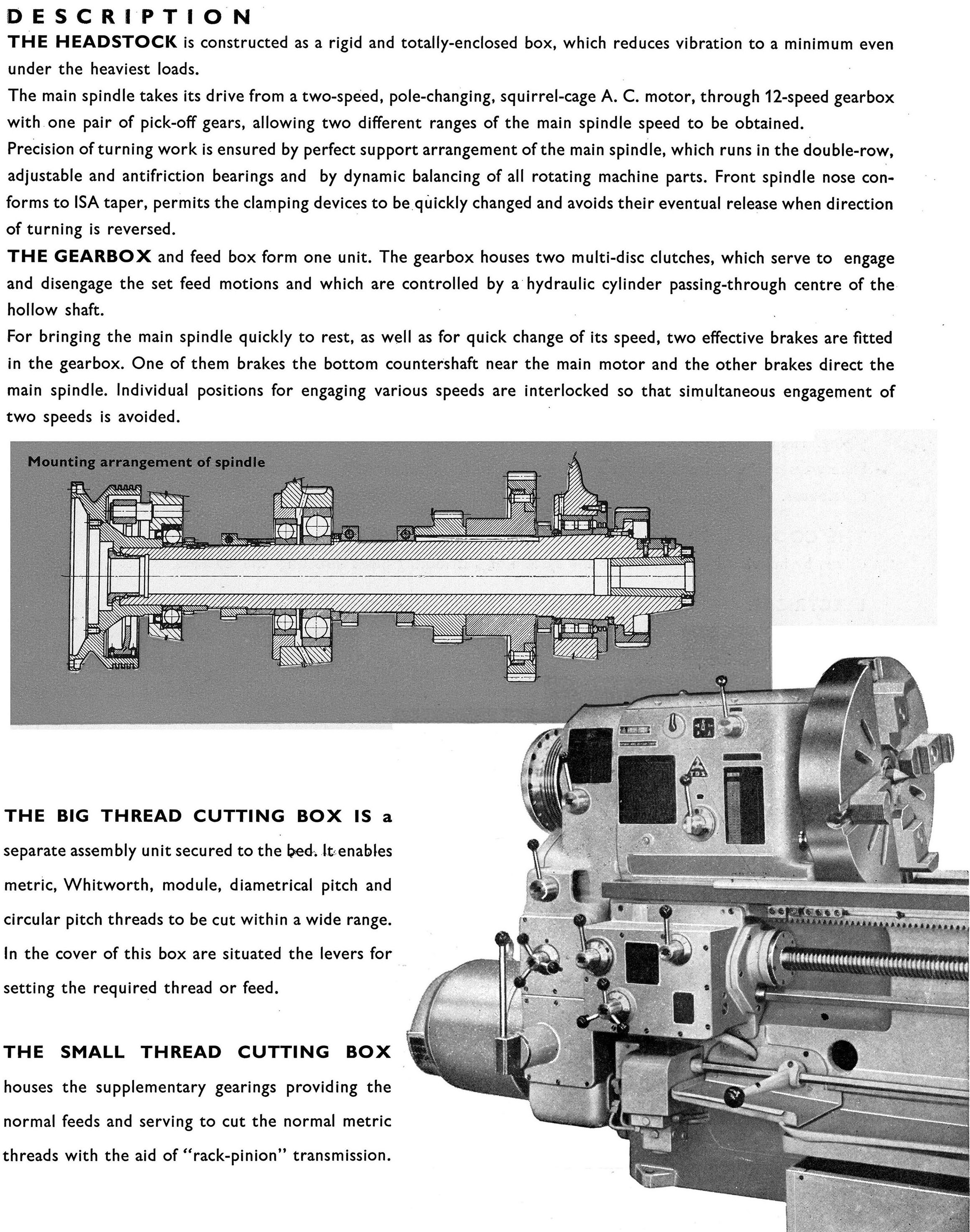 |
|
|
|
|
|
|
A view of the Edgwick Factory machine shop taken in the mid 1920s. Seemingly just a simple, large room, it was, in fact, carefully organised so that each bay was identical to its fellows and able - when required - to be converted with minimum loss of time to become an erecting shop complete with cranes. The overhead line shafting - required at the time as machines fitted with their own electric motors had yet to become standard - was also cleverly engineered. Adjustments to the alignment of drives (to accommodate new machines or rearrange existing ones) could be made by sliding the bearings hangers along longitudinal and traverse sections of channel sections and clamped in place without the need to drill extra holes. As a half-way house to independent machines, in this factory, instead of a large, remote, single electric motor driving everything via the line shafting, individual motors were mounted on the overhead rails and arranged to drive one or more machines
|
|
|
|
|
|
|
 |
|
|
|
|
|
|
Grinding Department, mid 1920s. At this stage in the evolution of mass production, grinding had changed from being a process used solely to obtain a precision fit or finish work after hardening, to one used on a daily basis as part of the effort to improve both quality and rate of output. In this department the holes in castings were made to a standard size, the "tolerance allowance" then being made by varying the diameter of the shafts that fitted into them. Darcie Kerwin, a neighbour of the writer when young, recalled that when the time-and-motion man was taking his measurements, the men would "work to the drawings". It so happened that the men, highly experienced in the practicalities of the job, knew that the blueprints left more metal on the turned parts than necessary for the finishing grind and by means devious (involving the turners), could shorten the job time considerable and so earn a very healthy weekly bonus.
|
|
|
|
|
|
|
 |
|
|
|
|
|
Erecting Department - assembly of complete machines. Around twenty are shown being built up
|
|
|
|
|
|
|
 |
|
|
|
|
|
Another view of a Herbert factory and its Erecting Department
|
|
|
|
|
|
|
 |
|
|
|
|
|
A jump to the 1960s and Monoslide lathes being assembled in the main works
|
|
|
|
|
|
|
 |
|
|
|
|
|
Heat Treatment Department. To the side was a section equipped with Brinell-type hardness testers
|
|
|
|
|
|
|
 |
|
|
|
|
|
A picture believed to have been taken during the mid 1920s showing a customer's works equipped with a huge number of Herbert capstan lathes
|
|
|
|
|
|
|
 |
|
|
|
|
|
|
Auto-Lathe and Automatic Screw Machine Department in Herbert's Edgwick Factory. In this section of the works items such as screws, bolts, pins, collars, handles and similar parts were turned from steel bars. The lathes could be single or multiple spindle and incorporated many ingenious features that made them largely automatic in action. Auto-Lathes were a development of the Automatic Screw Machine and used for machining items made from individual parts such as castings, forging - or blanks sawn from bars. Items used in capstan lathes - pulleys, gear blanks, sleeves, friction clutches and chuck bodies, etc., could be bored, reamed, turned, faced or formed in other ways to close limits and entirely automatically - save for an operator loading and loading them
|
|
|
|
|
|
|
 |
|
|
|
|
|
Another section of the main Herbert works dedicated to Auto lathes for the mass production of turned and threaded parts
|
|
|
|
|
|
|
 |
|
|
|
|
|
A Herbert Foundry - one of several that the company ran. A bowler-hatted manager is posing for the camera and the men in the background obviously fascinated by the photographer,,,
|
|
|
|
|
|
|
 |
|
|
|
|
|
Milling Department with rows of horizontal machines
|
|
|
|
|
|
|
|
|
|
|
|
 |
|
|
|
|
|
|
Specialised "Die-Making" Department. In this area parts for the well-known automatic, self-releasing Herbert "Coventry Diehead" were made. Constructed to very close tolerances using jig and fixtures, die heads were made in a variety of sizes and widely used in industry for all manner of production processes.
|
|
|
|
|
|
|
 |
|
|
|
|
|
|
Testing Department. Each complete machine was brought to this section for examination under power - and where a customer had specified that it was to be used for a particular type of job, tests would aim to replicate that use. In addition the department ran investigations where parts samples or drawings were submitted that required a guarantee that a particular Herbert model was suitable for their manufacture - or if suitable tooling need to designed and made so that they could be. Customers' representatives were also able to visit and see how machines performed, which of several might be the best choice - and how they might be employed to maximise production consistent with the lowest possible cost.
|
|
|
|
|
|
|
 |
|
|
|
|
|
|
An important part of the Herbert business was the manufacture and retailing of what were listed in the Company's hard-backed sales books as "Small Tools and Machine Tool Accessories" - hence almost anything used in an engineering plant including tooling for capstan lathes, taps, dies, reamers, Coventry dieheads, cutting tools of all types for lathes and milling machines, gear-cutter hobs, chucks, guards, inspection and measuring equipment, rotary tables, dividing heads, grinding wheels and vices, etc. In addition Herbert also factored a wide range of machine tools and accessories for other makers.
|
|
|
|
|
|
|
 |
|
|
|
|
|
Component Parts Stores. For employees in this department, a brown coat, clip-board, pencil behind the ear and a curt manner were all compulsory
|
|
|
|
|
|
|
|
|
|
|
|
|
|
|
|
|
|
|
|
|
|