 |
 |
 |
 |
 |
 |
 |
 |
 |
 |
 |
 |
 |
 |
 |
 |
 |
 |
 |
 |
 |
 |
 |
 |
 |
 |
 |
 |
 |
 |
 |
 |
 |
 |
 |
 |
 |
 |
|
|
|
|
|
|
|
|
|
|
|
|
|
|
|
|
|
|
|
|
|
|
|
|
|
|
|
|
|
|
|
|
|
|
|
|
|
|
|
|
|
|
|
|
|
|
|
|
|
|
|
|
|
Heid lathes, built in Austria, have a reputation for exceptionally clever design, heavy construction and a build quality of the highest order. Even their smaller conventional lathes of the 1950s and 1960s - including the more common DNK 26/32 Series and even the 200 mm centre height D400 - enjoying the same very high standards of fit and finish and lavish attention to detail included in the much larger and more profitable models. The DNK 26/32 lathe was available in five versions: the standard DN26 with a relatively simple apron assembly as the general-purpose model; the K26 equipped for copying; the R26 fitted with a turret tailstock for production work; the H26 with a relieving attachment and the KH26 fitted for both copying and relieving (these lathes are shown towards the bottom of the page). Built to the German DIN 8605 toolroom accuracy standard, the D400 Series was available in four models: the DLZ was the backgeared and screwing version, with power sliding and surfacing feeds; the DLZK added a fully integrated profiling (copying) unit of a Heid patented type (it could not be added later and is a type easily recognised by a second "cross-feed dial" to the right of the usual one); the DZK was intended as a specialised copying/profiling lathe and lacked a leadscrew while the DZ, a production version of the DLZ, also omitted screwcutting. All types, with the exception of the production version, could be had with the centre height increased to 250 mm, an option intended to be selected where the majority of jobs undertaken would require lighter cuts on larger diameter workpieces. Carried on strong, cast-iron headstock and tailstock plinths, the 360 mm (14") wide bed was made from an alloyed iron and consisted of two parallel, double-wall spars braced by roof-shaped transverse girders with sufficient room left between for chips to fall freely into the tray beneath. With a natural hardness of BHN-260, the V and flat ways were ground to ensure long life. Although most other makers would also have offered a fully hardened bed, instead Heid listed the option of ways built from screwed-on strips of hardened steel. With its wide surface and shallow angle, the outer face of the front V-way was designed to absorb wear while the narrower and steeper inside face took the majority of the tool thrust. Continued below:
|
|
|
|
|
|
|
|
|
|
|
|
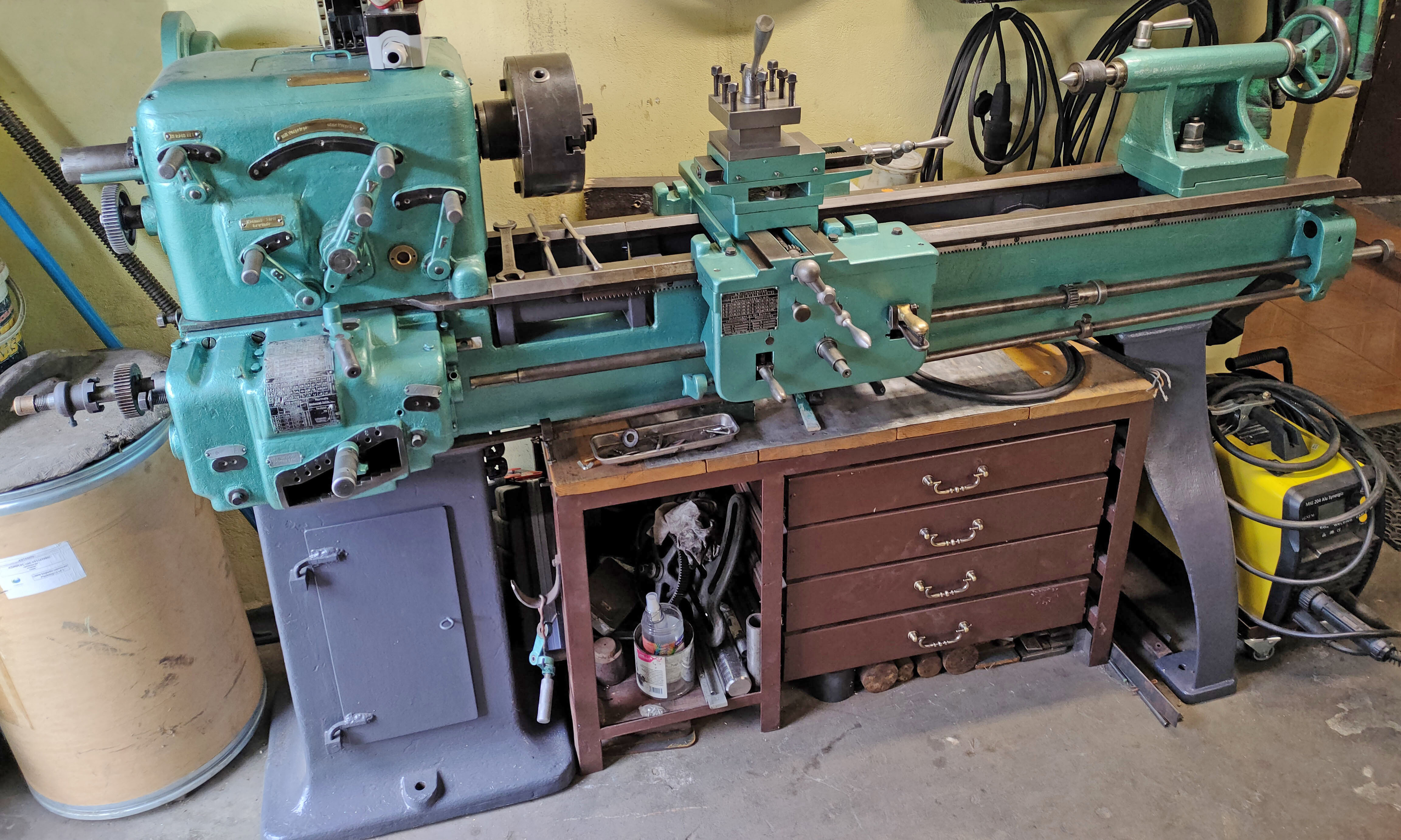 |
|
|
|
|
|
|
Log-bed version of the Heid DLZ400 Universal Lathe
Continued: Drive came from a dynamically balanced 4.04 kW (optionally 5.15 kW) motor housed in the left-hand leg with stop and start control by a lever protruding from a control box fastened to the right-hand face of the apron. As this arrangement involved direct, on-line starting (forbidden in some areas by electricity companies) an alternative could be fitted (at extra cost) of automatic star-delta commutation. A manually operated star-delta switch, positioned under the screwcutting and feeds' box, enabled the lathe to be run at reduced power when screwcutting or taking a finishing cut. In addition, the switchgear was arranged to allow the motor to reverse while running forwards and so provide a "wear-free" braking system. From the motor the drive was taken by three V-belts to a 4-speed gearbox mounted directly above - its location in the base of the plinth helping to isolate the headstock spindle from the effects of vibration. The oil-immersed box held a cluster of hardened and ground gears sliding on 6-spline shafts supported in ball races with control by a long lever on the front face of the stand. From the other end of the gearbox the drive was taken, by four V-belts, to a pulley mounted outboard of the spindle end. The pulley rotated in its own bearings with the connection between it and the spindle through a dog clutch - the arrangement relieving the headstock spindle of belt pull. As well as the four belt-driven high speeds, the headstock also had two backgear groups that gave eight slower speeds for roughing out and screwcutting, etc., selection being by the juxtaposition of four levers on the front face of the headstock. Bearings and gears were positively lubricated through pipes fed from a gear pump with the oil cleaned by being passed though an easily accessed multi-disc filter. To let the operator know that the system was functioning correctly, oil was sprayed into a domed glass set into the top of the headstock - the latter also having a rubber-mat covered rectangle recess to take tools, spanners and other odds and ends. The standard speed range ran from 31.5 to 1400 r.p.m. with the option of a high-speed set from 63 to 2800 r.p.m. With a 45 mm bore, a bayonet-lock DIN55022 nose and a metric No. 50 taper, the headstock spindle ran in a pair of opposed, high precision taper-roller bearings at the front, a single taper-roller bearing in the centre and a ball race at the far end. Formed as a sealed housing, the screwcutting and feeds gearbox ran in an oil bath, drove a 36 mm diameter, 6 mm pitch leadscrew and could generate a total of 32 metric and English pitches (and rates of feed) without changing the end gearing. The English range ran from 2 to 28 t.p.i., metric from 1 to 14 mm while to cut Module and DP threads just one change of gear was required on the end bracket; this change giving a range from 0.25 to 3.5 module and 8 to 118 DP. Sliding feed rates ranged from 0.09 to 1.25 mm and cross feeds from 0.045 to 0.63 mm per revolution of the spindle. Of very heavy build, the carriage was fitted with an apron holding a small piston-type oil pump that operated automatically whenever movement took place. Oil, fed through a network of pipes, lubricated the inside of the apron, the bed ways and leadscrew. Protecting the drive was an overload clutch that could also be set to trip against dead stops - a handy convenience on long, slow jobs when the lathe could be left to get on with it and yet stop safely finished. Fitted with a hardened and ground cross-feed screw running in an oil bath, the compound slide rest assembly had its 360° swivelling top slide fitted as standard with an ordinary clog-heel tool post, though the option existed of ordering either a 4-way type of a high-quality, quick-set model by Boni. Micrometer dials were large, beautifully engraved, satin-chrome plated and fitted with face-screws that ensured no change of setting occurred as the reading was locked or unlocked..
|
|
|
|
|
|
|
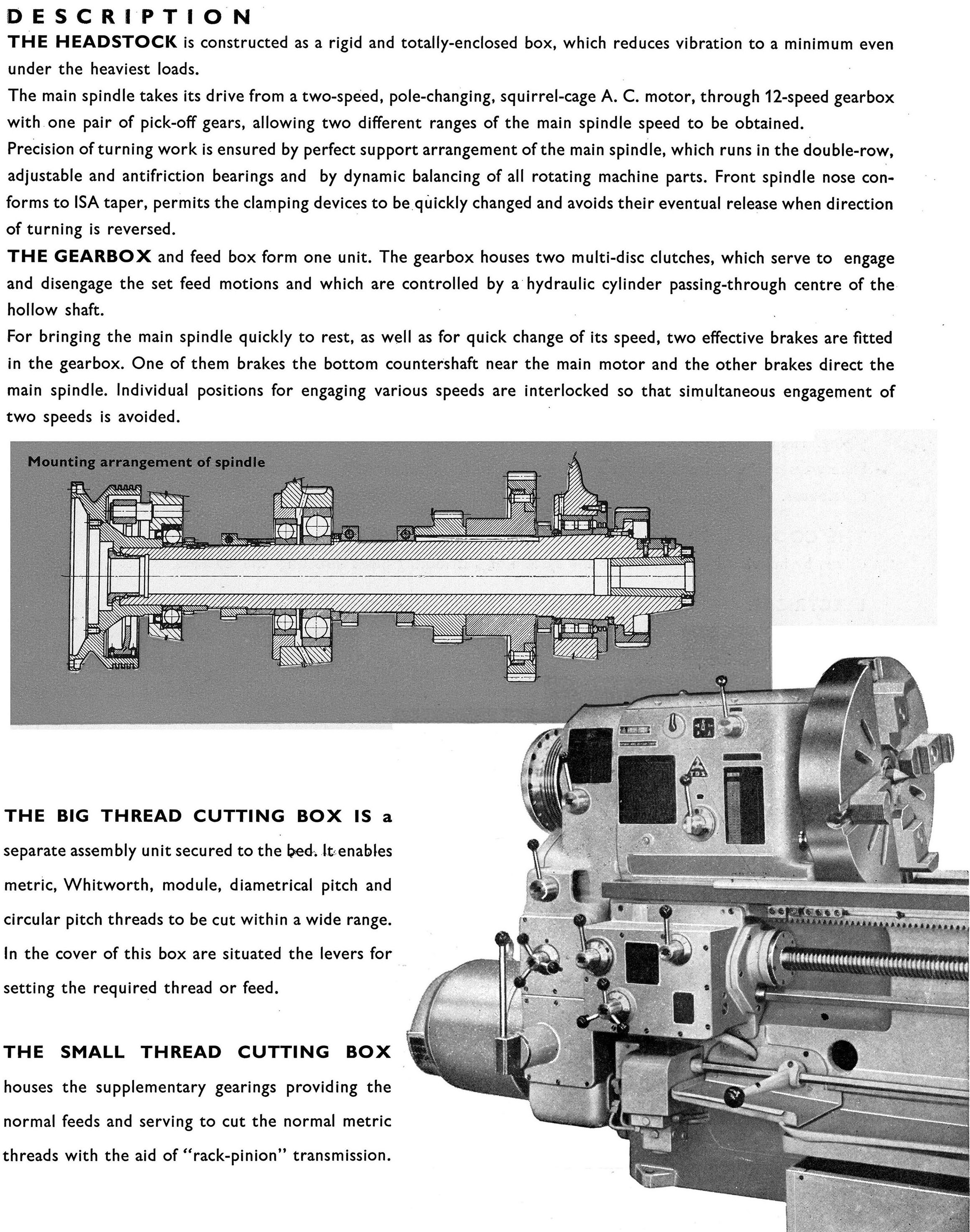 |
|
|
|
|
|
|
The 360 mm (14") wide bed was made from an alloyed iron and consisted of two parallel, double-wall spars braced by roof-shaped transverse girders with sufficient room left between for chips to fall freely into the tray beneath.
|
|
|
|
|
|
|
 |
|
|
|
|
|
|
Heid D400 Series drive system
|
|
|
|
|
|
|
|
|
|
|
|
 |
|
|
|
|
|
|
Standard Model DLZ400 with the optional 4-way toolpost
|
|
|
|
|
|
|
 |
|
|
|
|
|
|
Standard Model DLZ400 with the optional 4-way toolpost
|
|
|
|
|
|
|
 |
|
|
|
|
|
Heid tracer/copying head. Built onto its own slide, the head could be independently adjusted relative to the template and further settings made while work was in progress, a handwheel and micrometer dial being provided that matched that of the normal cross feed. Turning accuracy to within ±0.02 mm (0.0008") on diameter was possible. The template carrier, fitted with two adjustable centre carriers, was carried on a separate slideway at the rear of the bed. To hold flat templates, the makers provided a special carrier (illustrated) that allowed the unit to be bolted in place or, as an option, a fan-type holder that took three templates, each being manually indexed into position as required. To switch to copy-facing work the unit was simply turned through 90°. The unit was ingenious, the movement of the stylus over the template being converted into the required profile by alternatively opening and closing three pairs of contacts, each contact pair controlling one of the three directions of feed motion (along and in and out). The electrical signals from the tracer head were converted into mechanical movements by the electromagnetic clutches in the apron.
|
|
|
|
|
|
|
|
|
|
|
 |
|
|
|
|
|
|
Swivelling holder able to mount three templates at once. A lever, set to the right-hand side of the device, enabled the operator to being each into position as required, an indent pin ensuring that the alignment was correct. In a typical, short-run production job if the number of templates required exceeded three, extra holders could be set up with the turner mounting them as required. Heid also offered this unit with automatic re-cycling, ideal for situations where the depth of cut was too great to be achieved in one pass and up to three might be required.
|
|
|
|
|
|
|
 |
|
|
|
|
|
|
DLZK400 opying/tracing lathe apron. This contained two electromagnetic reversing clutches, one for the cross and the other for the longitudinal feed. The clutches were built in an easily removed cassette that could be removed for servicing or repair. When used for ordinary work, the clutches improved convenience for the operator, allowing the automatic trips to be set with far greater accuracy than the mechanical units on the standard lathe.
|
|
|
|
|
|
|
 |
|
|
|
|
|
As well as the four belt-driven high speeds, the headstock also had two backgear groups that gave eight slower speeds for roughing out and screwcutting, etc., selection being by the juxtaposition of four levers on the front face of the headstock. Bearings and gears were positively lubricated through pipes fed from a gear pump with the oil cleaned by being passed though an easily accessed multi-disc filter.
|
|
|
|
|
|
|
|
|
|
|
|
 |
|
|
|
|
|
Formed as a sealed housing, the screwcutting and feeds gearbox ran in an oil bath, drove a 36 mm diameter, 6 mm pitch leadscrew and could generate a total of 32 metric and English pitches (and rates of feed) without changing the end gearing. The English range ran from 2 to 28 t.p.i., metric from 1 to 14 mm while to cut Module and DP threads just one change of gear was required on the end bracket; this change giving a range from 0.25 to 3.5 module and 8 to 118 DP. Sliding feed rates ranged from 0.09 to 1.25 mm and cross feeds from 0.045 to 0.63 mm per revolution of the spindle.
|
|
|
|
|
|
|
 |
|
|
|
|
|
|
Rapid traverse unit with automatic "single-pass" cycles. Flange mounted against the tailstock end of the bed, the unit was designed to speed up production process by shortening the time between cuts. With addition control equipment the device could be set for rapid tool approach, cut feed rate, repetitive skip feeds, tool withdrawal, rapid return and stop at the end of the cycle.
|
|
|
|
|
|
|
|
|
|
|
|
 |
|
|
|
|
|
|
Available as an ordinary hand-feed type, the tailstock could also be equipped with a powered spindle for boring. With a travel of 250 mm (9.84") the unit was capable of boring a 32 mm (1.26") hole in carbon steel of about 60 kg/mm (38ton/sq.in). So equipped, the lathe could both turn and bore simultaneously. A further option was the electric tailstock, a motor driving the spindle through reduction gearing with the thrust pressure adjustable between set limits. The unit could be integrated into a control system enabling the spindle to advance or withdraw.
|
|
|
|
|
|
|
 |
|
|
|
|
 |
|
|
|
|
|
|
DLZK400 Universal and copying lathe and (when less the leadscrew) DZK400 production and copying lathe
|
|
|
|
|
|
|
|
|
|
|
|
 |
|
|
|
|
|
The basic Heid DNK 26/32 as the DN26 general-purpose lathe
|
|
|
|
|
|
|
 |
|
|
|
|
|
Heid DNK 26/32 in its H26 form with relieving equipment
|
|
|
|
|
|
|
 |
|
|
|
|
|
Heid DNK 26/32 type K26 with copying equipment. Note, on this and the KH26, the much more complicated apron
|
|
|
|
|
|
|
|
|
|
|
|
 |
|
|
|
|
|
|
Heid DNK 26/32 built as the HK26 with both copying and relieving attachments
|
|
|
|
|
|
|
 |
|
|
|
|
|
Heid DNK 26/32 in its R26 form with a capstan tailstock attachment
|
|
|
|
|
|
|
|
|
|
|
|
|
|