 |
 |
 |
 |
 |
 |
 |
 |
 |
 |
 |
 |
 |
 |
 |
 |
 |
 |
 |
 |
 |
 |
 |
 |
 |
 |
 |
 |
 |
 |
 |
 |
 |
 |
 |
 |
 |
 |
 |
 |
 |
 |
 |
 |
 |
 |
 |
 |
 |
 |
 |
 |
 |
 |
 |
 |
 |
 |
 |
 |
 |
 |
 |
 |
 |
 |
 |
 |
|
|
|
|
|
|
|
|
|
|
|
|
|
|
|
|
|
|
|
|
|
|
|
|
|
|
|
|
|
|
|
|
|
|
|
|
|
|
|
|
|
|
|
|
|
|
|
|
|
|
|
|
|
|
|
|
|
|
|
|
|
|
|
|
|
|
|
|
|
|
|
|
|
|
|
|
|
|
|
|
|
|
|
|
Hayes was a small but respected Leeds-based machine-tool company founded in about 1930 by George Hayes, a practical engineer of great skill whose original interest (and one that involved the company for many years), was the production of dies for dies-casting machines. The firm was to be eventually run by his son, Gerald, until a management buy-out in the 1960s. Besides work for die-casting companies and the production of numerous specialised, one-off machines, Hayes was famous for their very high-quality precision milling machines including the "Tracemaster TM54" range of two and three-dimensional copy profile millers, the "Tapemaster 1380", an early numerically-controlled vertical miller; the "Gemini" automatic miller; the "Tracemaster TM43 and TM43-3D" two and three-dimensional copy-profile millers built for exceptional accuracy and with either hand or automatic guidance; the "Linemaster", a two-dimensional precision copy-milling machine with Linerider optical following equipment able to work from a line drawing; the "Tapemaster 1090", a vertical milling machine controlled in the usual two axes but with control of the third from pre-set trips and tapes and the "Economill", a very heavily built, high-precision profile miller. The company's smallest conventional machine (and the one most likely to be encountered today), was the "Diemaster Universal Die and Mould Milling Machine" - a machine distributed during the 1950s and 1960s through Dowding & Doll Ltd. of Greycoat Street, Westminster, London S.W.1. The Diemaster, typical of a Hayes' product in being directly associated with the top-quality toolroom work (and carefully thought out in every detail of its design), was superbly constructed (alignments were to within 0.0002" per foot) and mounted on a substantial cast-iron base that held, in its rear section, a 1 h.p. 1425 rpm 3-phase motor. Twin A-section V-belts took the drive from the motor to an integral, 9-speed gearbox with ball-bearing supported shafts and nickel-chrome gears; speeds were changed by -lever, concentrically mounted controls mounted on the right-hand face of the main column. The speed-change dials were connected by a pair of chains to the gearbox, the drive from which was taken up to the ram by a wide flat belt on early machines and, on later models, by 4 V-belts. The resulting, very useful spindle-speed range ran from 50 through 100, 150, 200, 400, 600, 800, 1600 to 2400 r.p.m. As a point of interest, once all the adjustment of the belts has been used up, or the belts deteriorate, replacing them is a straightforward procedure - providing you have a copy of the machine manual where the procedure is explained in detail. The best type of belt to use is a modern, UK-made Super Tensile type that can be ordered to the required dimensions here (the belts varied in length and its essential to measure around the pulleys on your particular example to get the right size) The ram slide, fitted with a capstan-handle operated rack-and-pinion drive and linear vernier scales, could be wound in and out over a range of 7 inches. The head, which swivelled through 360 degrees, was equipped with a 2.5-inch travel, No. 2 Morse taper quill with a wheel-controlled fine feed on the right-hand side and a quick-action drill-feed lever on the left. Both the head spindle and its horizontal drive shaft were made from hardened and ground 'nitralloy' steel running in pre-loaded ball journal bearings with the right-angle drive into the head through nickel-chrome spiral bevel gears. The direct-fitting, draw-in collets used in the head had a maximum through-capacity of 0.5". A large weight, supported by a pair of bars inside the column, balanced the knee assembly and made its elevation a remarkably light and simple one-handed affair; access to the weight allowed it to be adjusted if a very heavy job was mounted on the table. The 5.5" of traverse and 12" of longitudinal travel of the 21" x 6.5" table were similarly smooth and easy - the feed screws passing through pre-loaded ball thrust races in their support plates at each end of the table and on the face of the knee. As an option a larger table was also offered - though few have been seen - some 28" x 8.5" and with the longitudinal travel increased to 16 inches but that of traverse unaffected. The larger table can be immediately distinguished in photographs by a cast-in coolant trough that runs around its periphery. The design of both table ways was unusual: the traverse was set at two levels with (two) independent gibs (that allowed the clearance to be set with great accuracy), whilst the longitudinal travel was ingeniously arranged with the table-support casting made as long as possible to give the table the maximum support no matter how far out it was moved. In order to obtain a decent amount of travel (though it was still only 12 inches), the sides of the knee casting was formed with large semi-circular cut-outs to let the table feed-screw end plates travel into it right up to the inside face of the balanced handwheels. The vertical travel of the knee was 14" and the maximum clearance between table and spindle nose 19.5". Combining many of the elements of a small jig borer and a conventional vertical miller the Diemaster makes an ideal machine for the model or experimental engineer who needs to combine, in one machine, strength and rigidity for heavy cuts as well as a sensitivity of touch and the fine accuracy required for smaller, delicate jobs. Production numbers and dates are not precisely known but it is certain that machine No. 222 was built in 1965. Although very few can have been produced (only one having been recorded in recent years), there was also a conversion unit available for horizontal milling. This involved removing just the vertical head and replacing it with a very heavy casting that carried both a dive shaft and twin-bar overhead arbor supports - the drive being taken from the same shaft. As such, the position of the cutter could be changed by turning the rear capstan handle and the speeds altered as normal (the assembly is illustrated below). The Diemaster stood 59" high, was 43" from the back of the stand to the tip of the cross-feed handwheel and approximately 38" wide over the ends of the table's longitudinal feed-screws handles. At over half a ton its weight, for a relatively small machine, was considerable, being approximately 12 cwt (1344 lbs). An interesting article, My Time at Hayes by Anthony Boyes, can be found at the bottom of the page together with other stories from the Company..
|
|
|
|
|
|
|
|
|
|
|
|
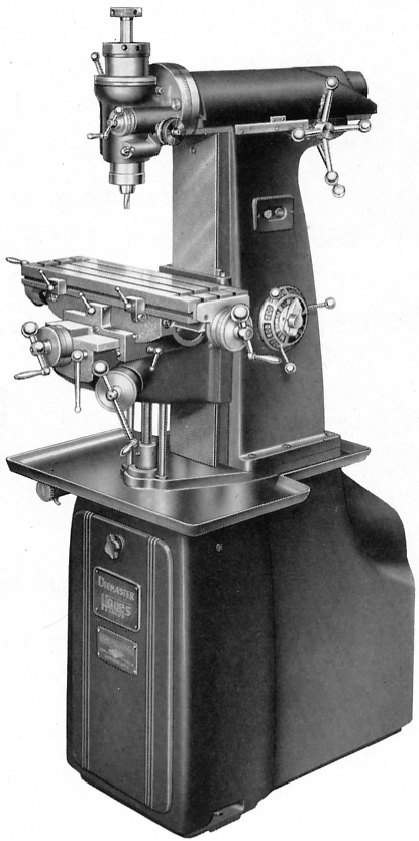 |
|
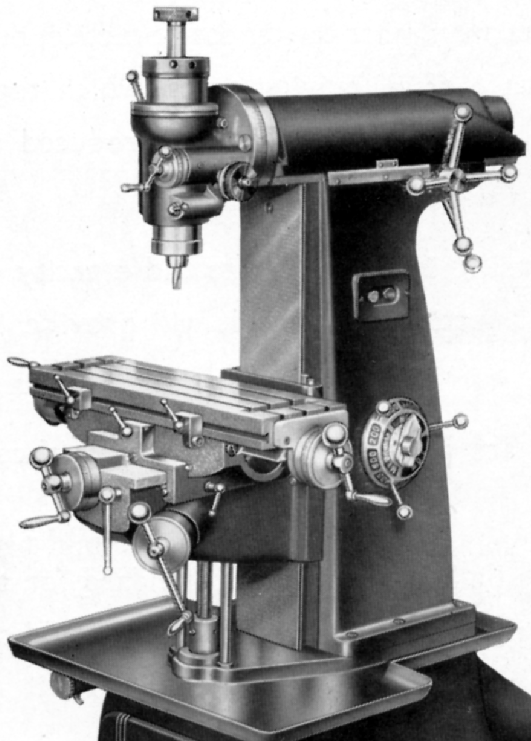 |
|
|
|
|
|
|
|
|
|
|
|
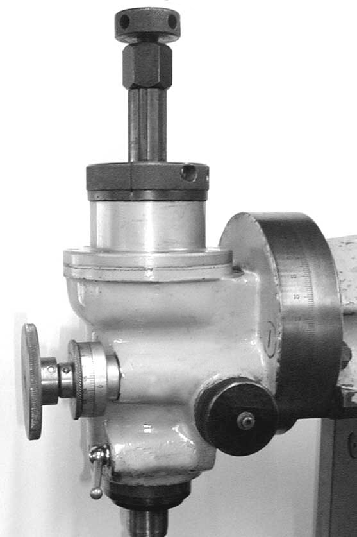 |
|
|
|
|
|
|
A later model with minor improvements to the controls including longer handles on the table and head ram
|
|
|
|
|
|
|
|
|
|
|
|
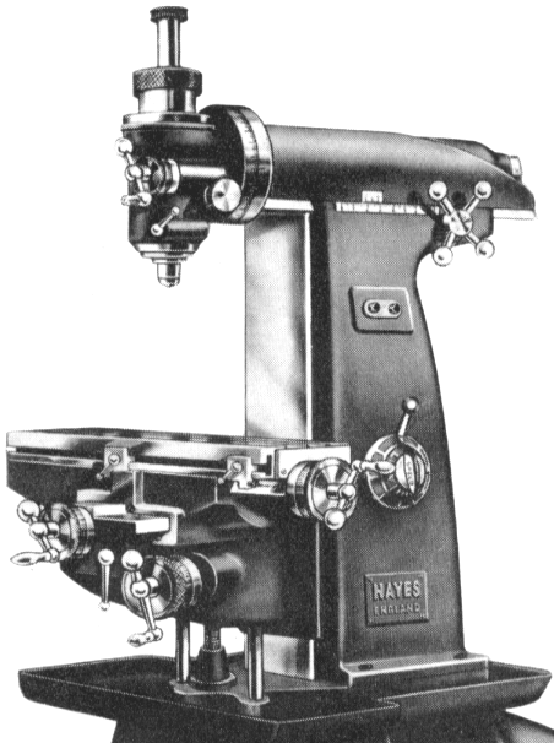 |
|
|
|
|
|
|
|
|
|
|
The very heavily built swivelling vertical head.
|
|
|
|
|
|
|
|
|
|
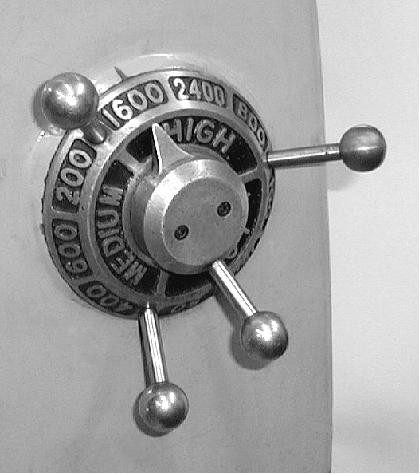 |
|
|
|
|
|
|
|
Earlier model with shorter table and head ram handles
|
|
|
|
|
|
|
|
|
|
|
|
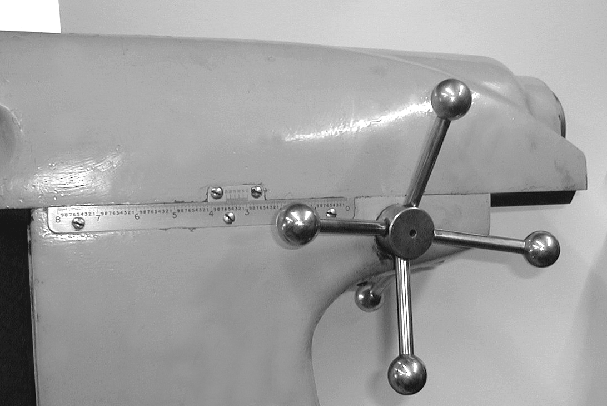 |
|
|
|
|
|
|
|
|
|
Vernier scale on the head-traverse ruler.
|
|
|
|
|
|
|
|
|
|
|
|
|
|
|
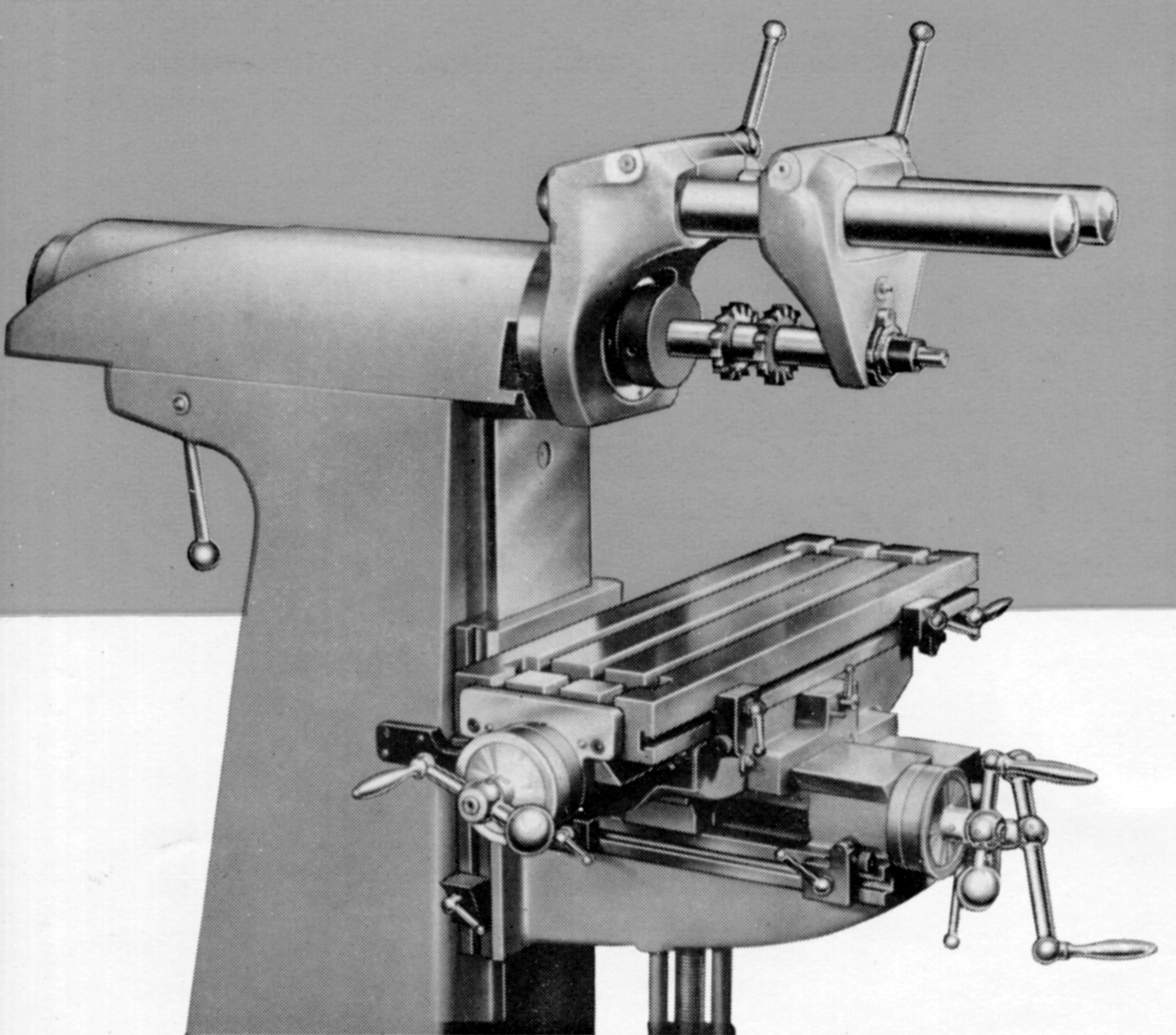 |
|
|
|
|
|
The horizontal conversion unit
|
|
|
|
|
|
|
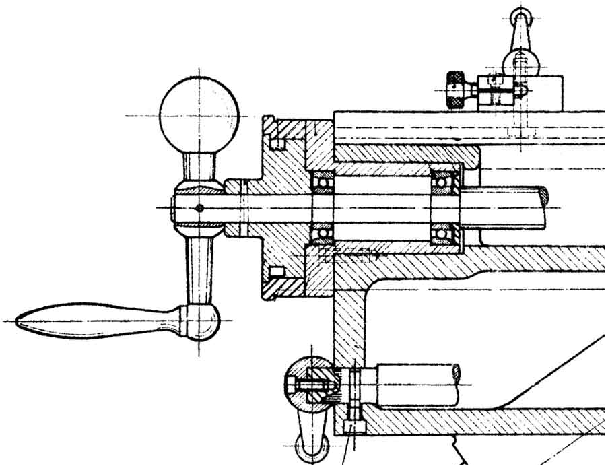 |
|
|
|
|
|
|
Table feed screws were very well supported and passed through pre-loaded ball thrust races at each end of the table and on the knee face.
|
|
|
|
|
|
|
|
|
|
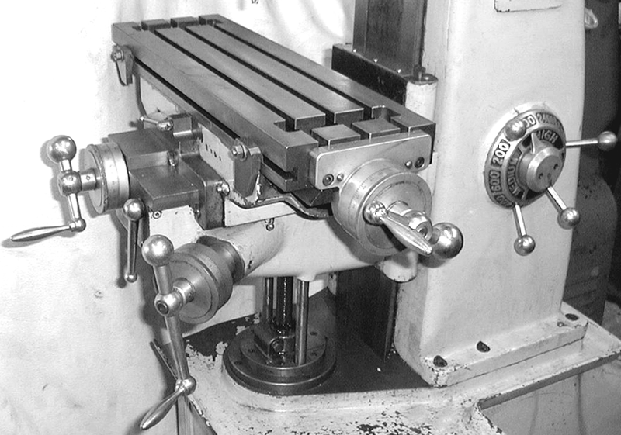 |
|
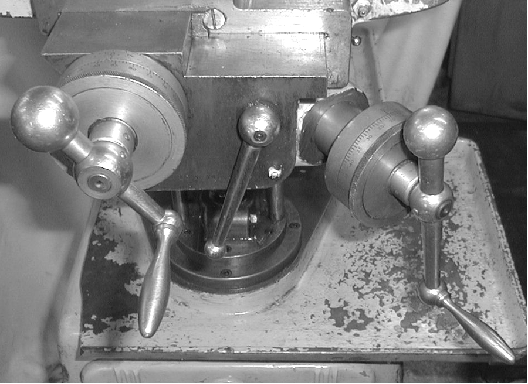 |
|
|
|
|
|
|
Large diameter, zeroing, satin-chrome micrometer dials. Notice that the knee carries its slide on two levels of sliding surface - with two gib strips to adjust the setting.
|
|
|
|
|
|
|
|
|
|
|
|
|
Very well-supported table with heavy knee casting.
|
|
|
|
|
|
|
|
|
|
|
|
|
|
|
|
|
|
|
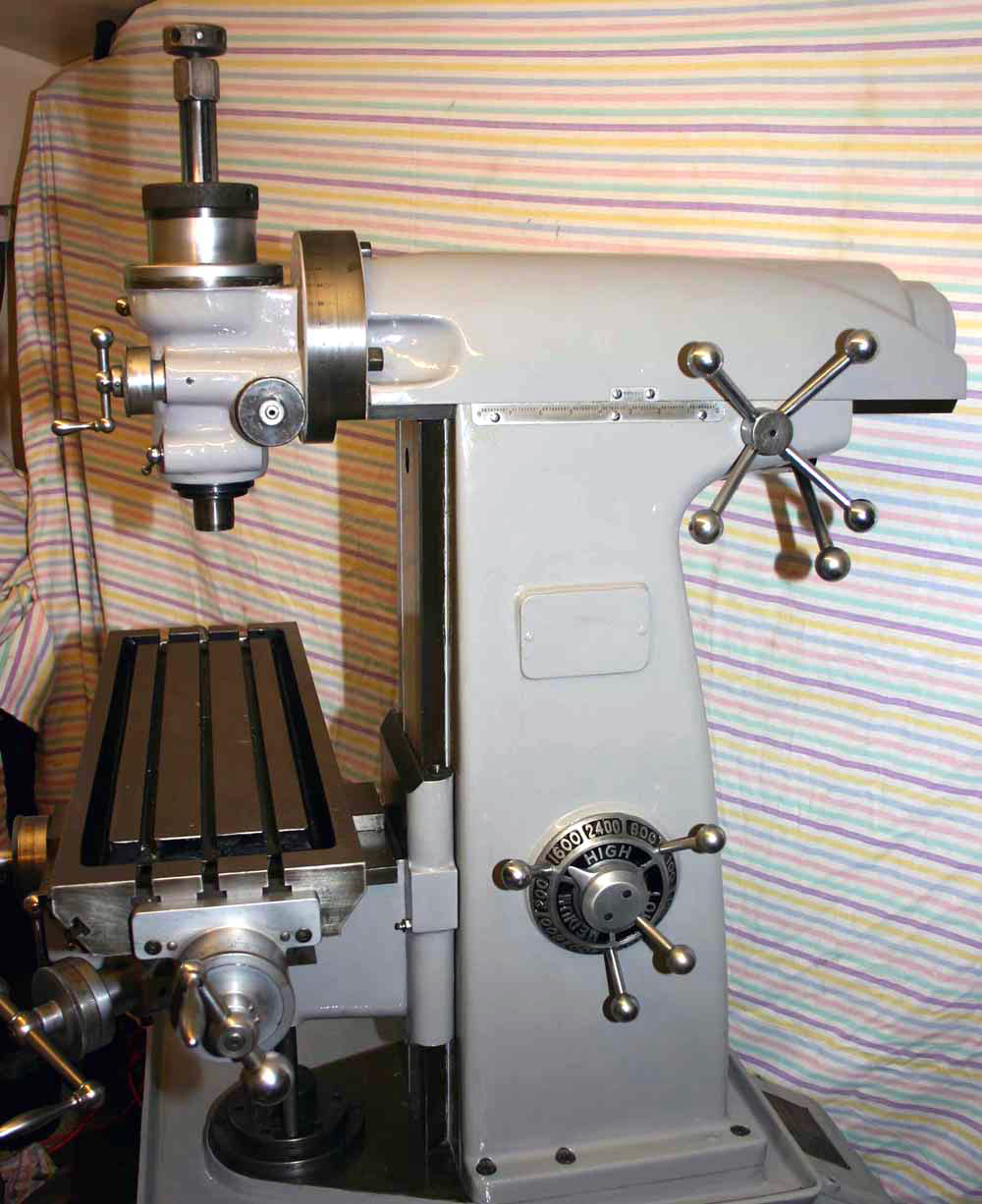 |
|
|
|
|
|
|
Twin spindle-speed control levers were carried on a concentric mounting on the right-hand face of the main column.
|
|
|
|
|
|
|
|
|
|
|
|
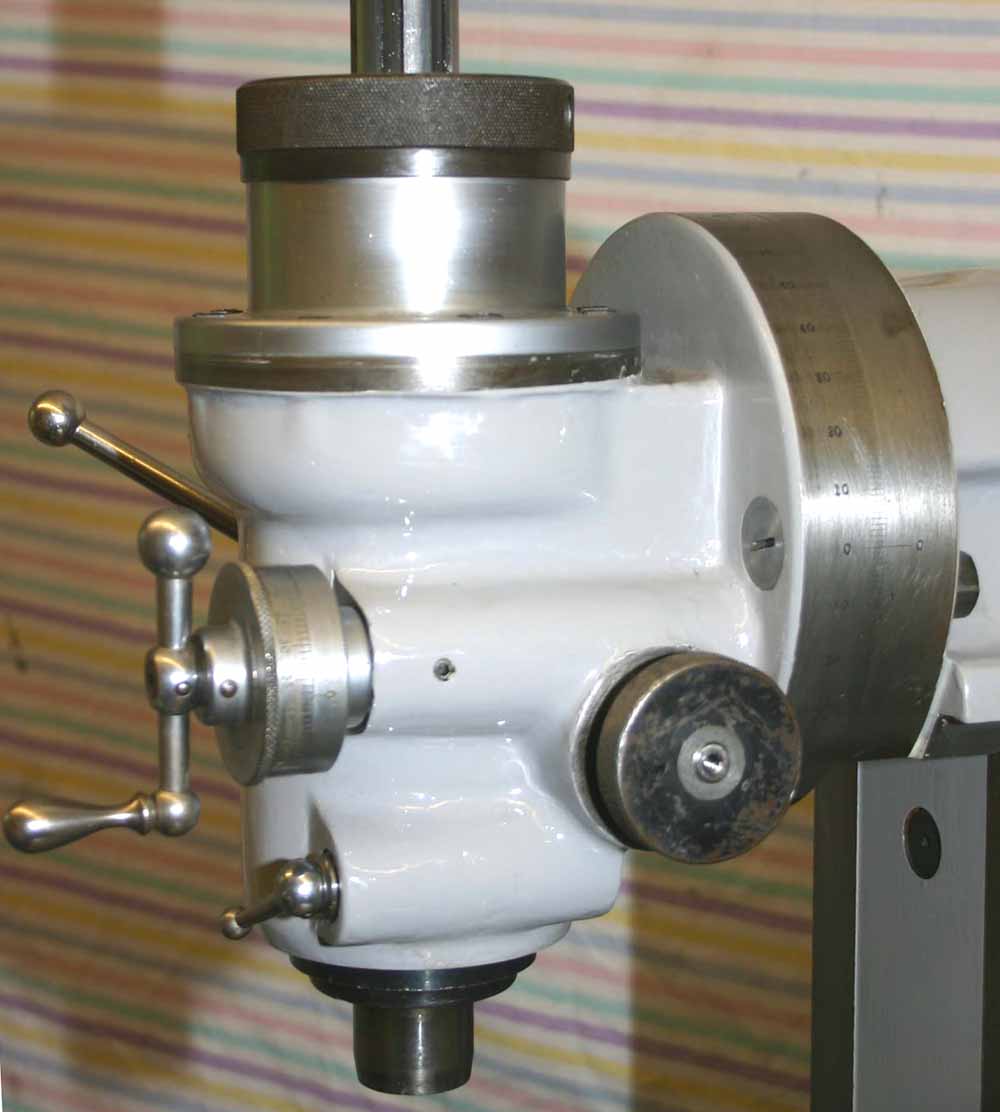 |
|
|
|
|
|
|
The very heavily built swivelling vertical head.
|
|
|
|
|
|
|
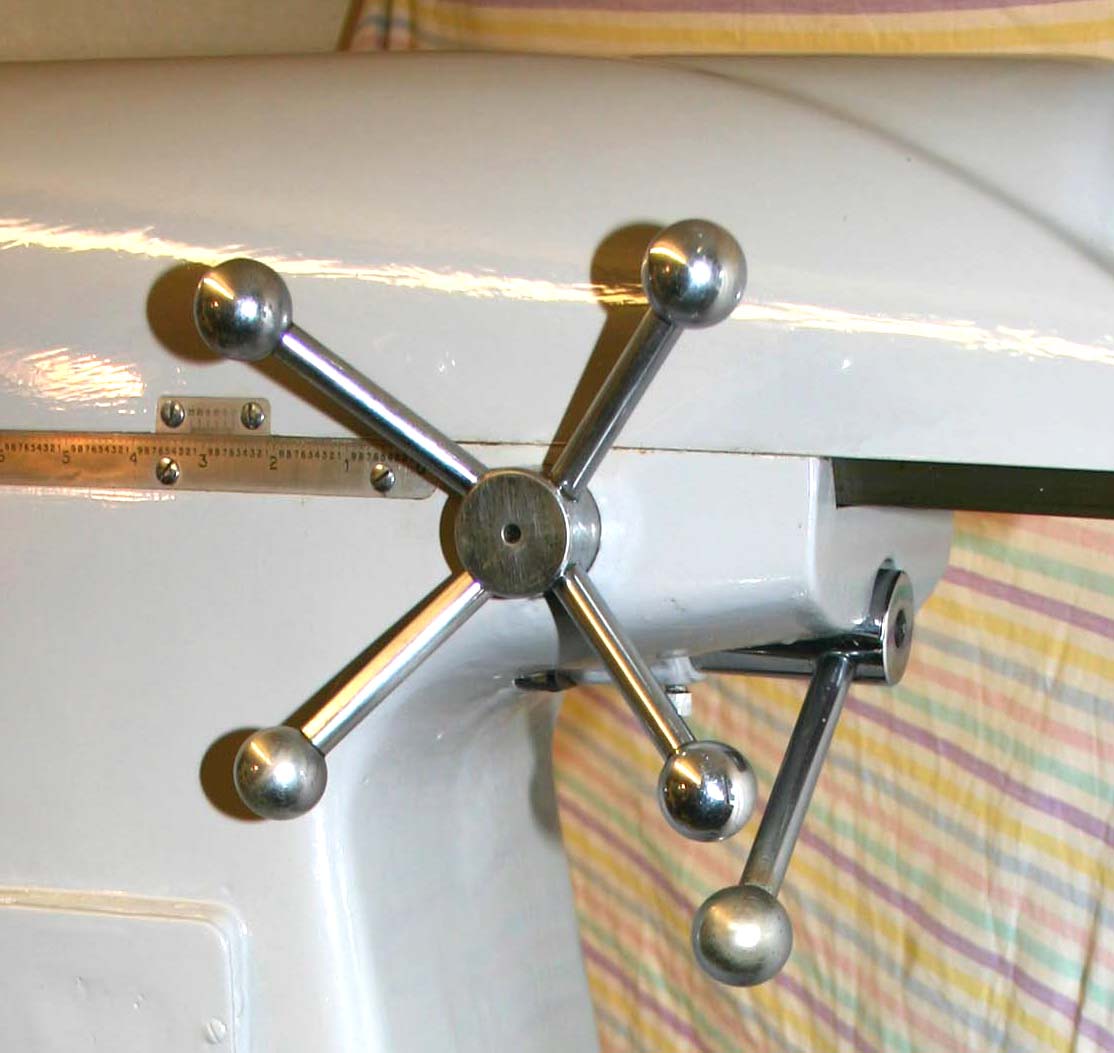 |
|
|
|
|
|
|
Vernier scale on the head-traverse ruler.
|
|
|
|
|
|
|
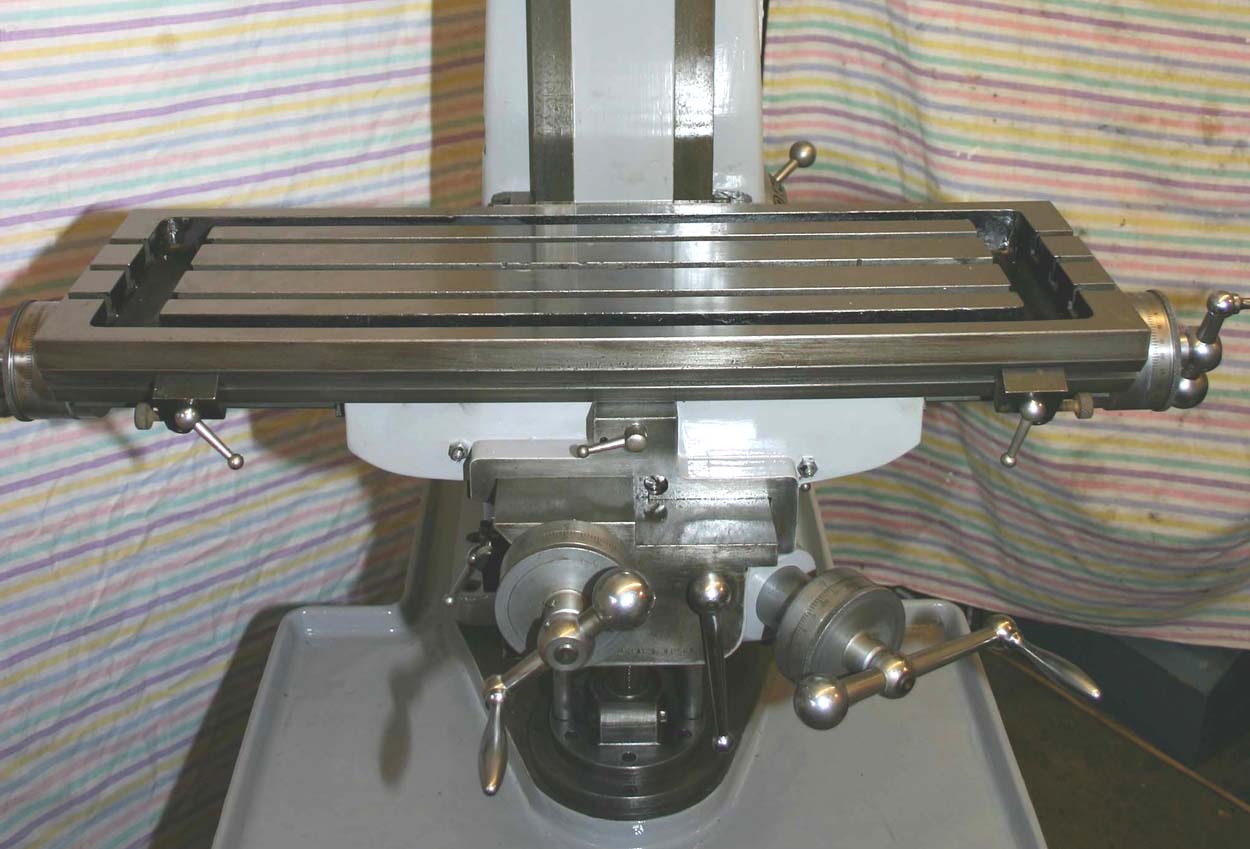 |
|
|
|
|
|
|
Larger 28-inch table--well supported on a heavy knee casting and with large diameter, zeroing, satin-chrome micrometer dials. Notice that the knee carries its slide on ways at two levels - with separate gib strips to adjust the clearances.
|
|
|
|
|
|
|
|
|
|
|
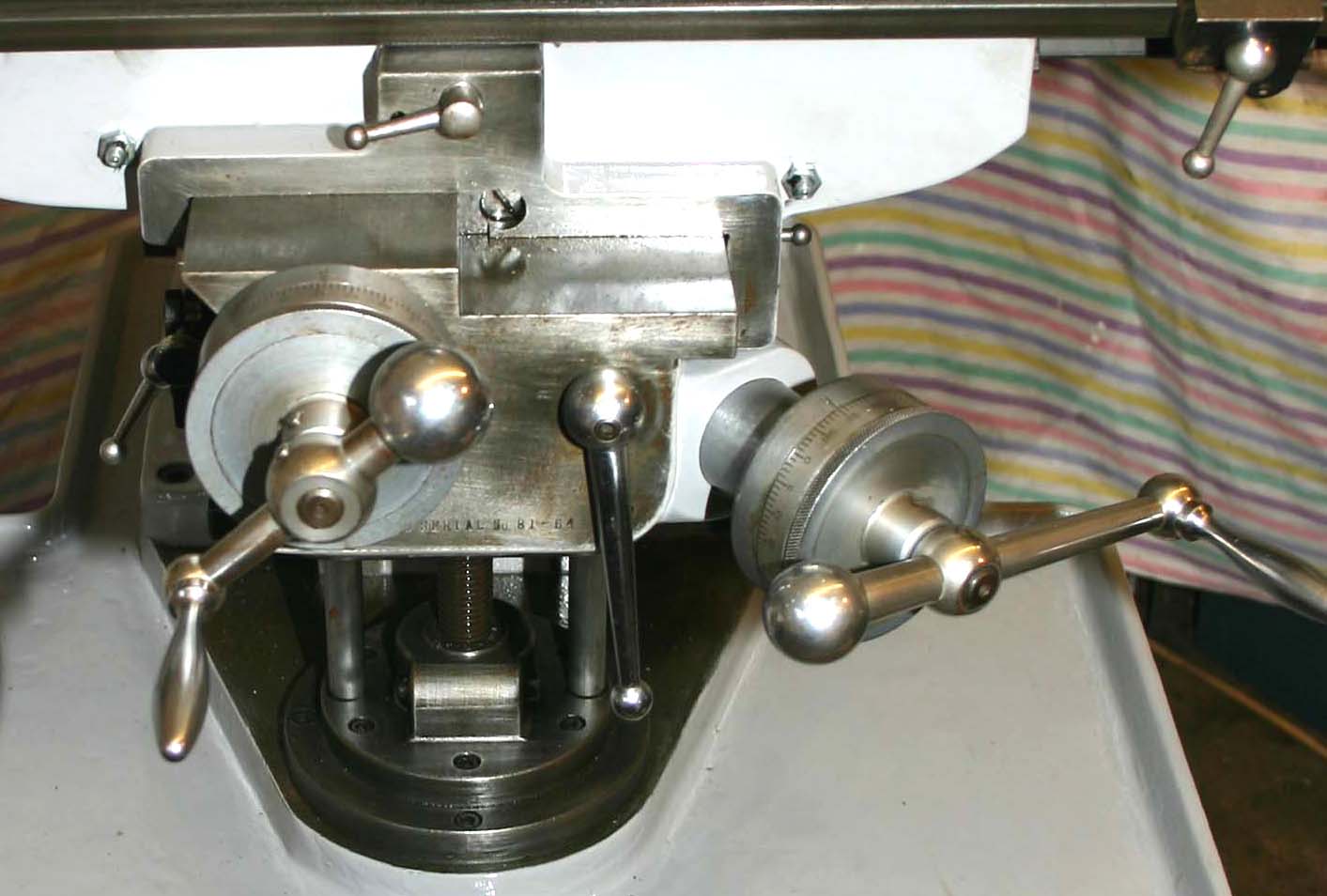 |
|
|
|
|
|
|
The longitudinal travel was cleverly arranged - the table-support casting was made as long as possible to give the table the best possible support no matter how far out it was moved In order to obtain a decent amount of travel the casting was formed with large semi-circular cut-outs to let the table feed-screw end plates travel into it right up to the handwheel abutment face (see picture below).
|
|
|
|
|
|
|
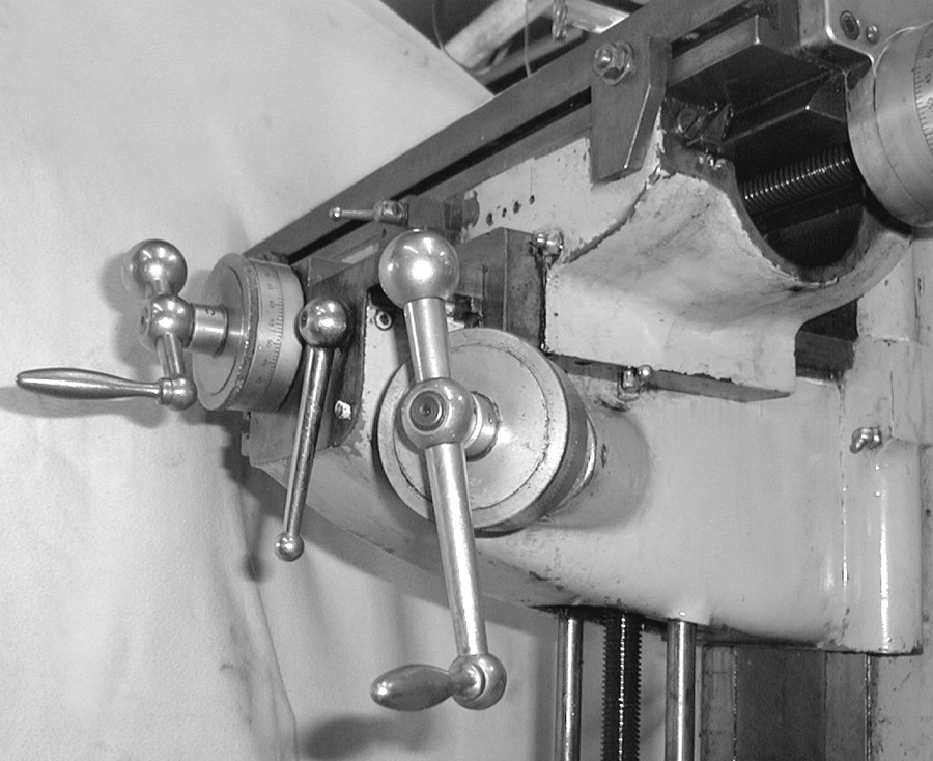 |
|
|
|
|
|
|
Semi-circular cut-out in the side of the knee casting to improve table travel
|
|
|
|
|
|
|
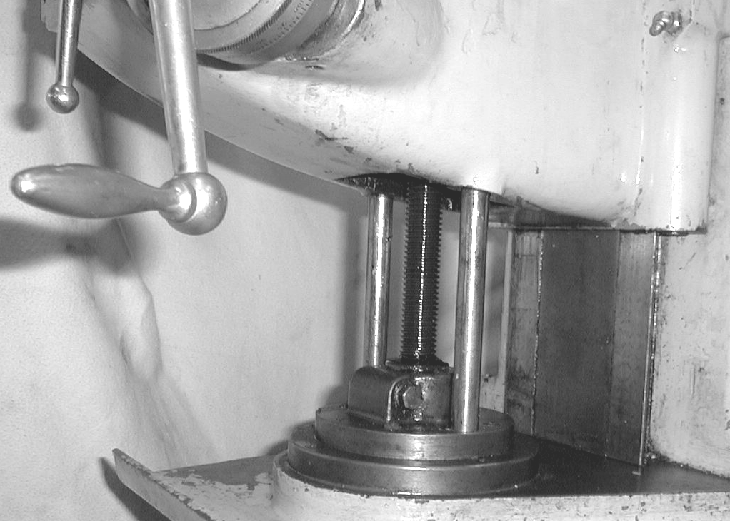 |
|
|
|
|
|
|
The vertical rods at each side the knee-elevation screw held the knee-balance weight within the cabinet
|
|
|
|
|
|
|
|
|
|
|
|
|
|
|
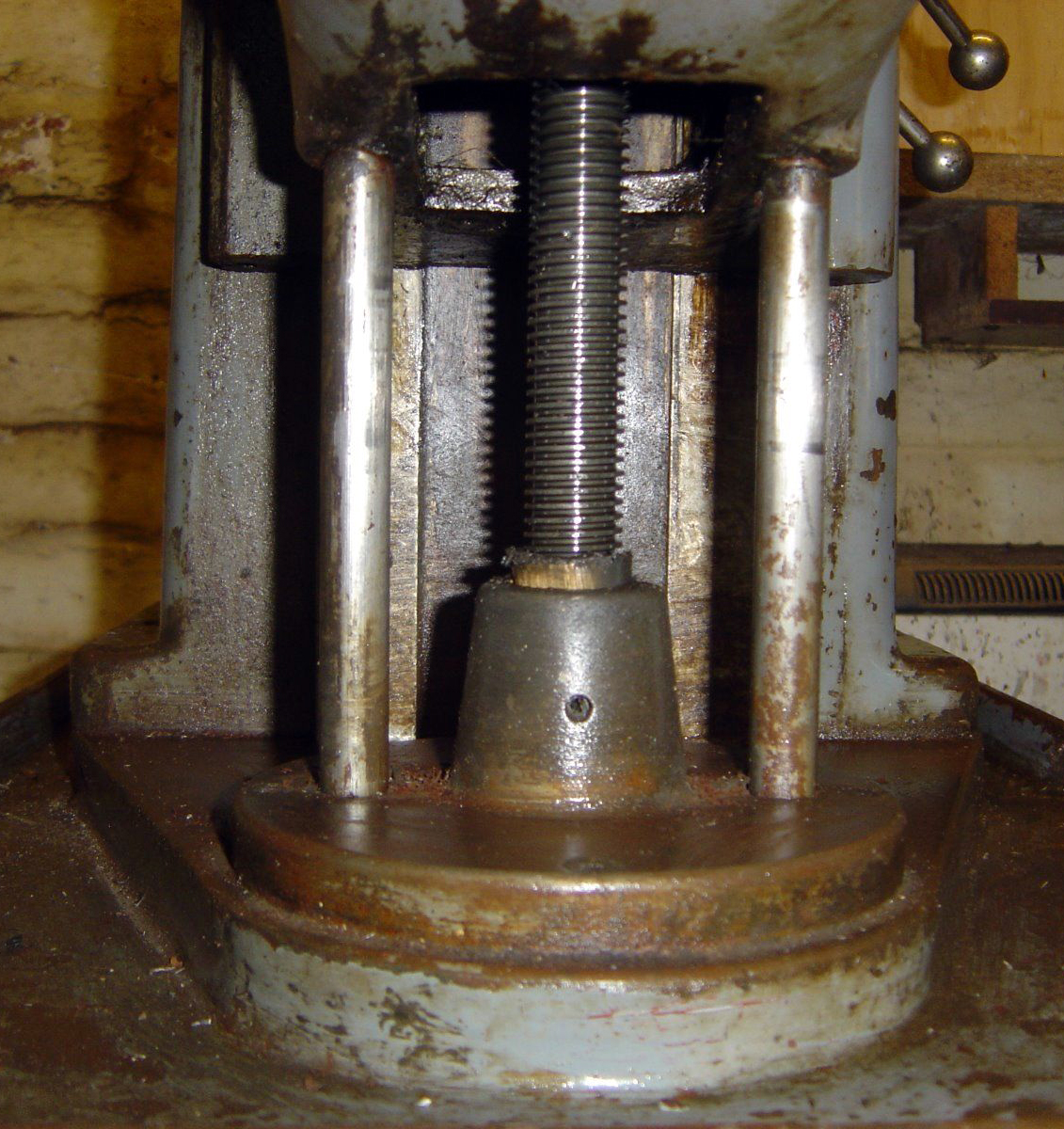 |
|
|
|
|
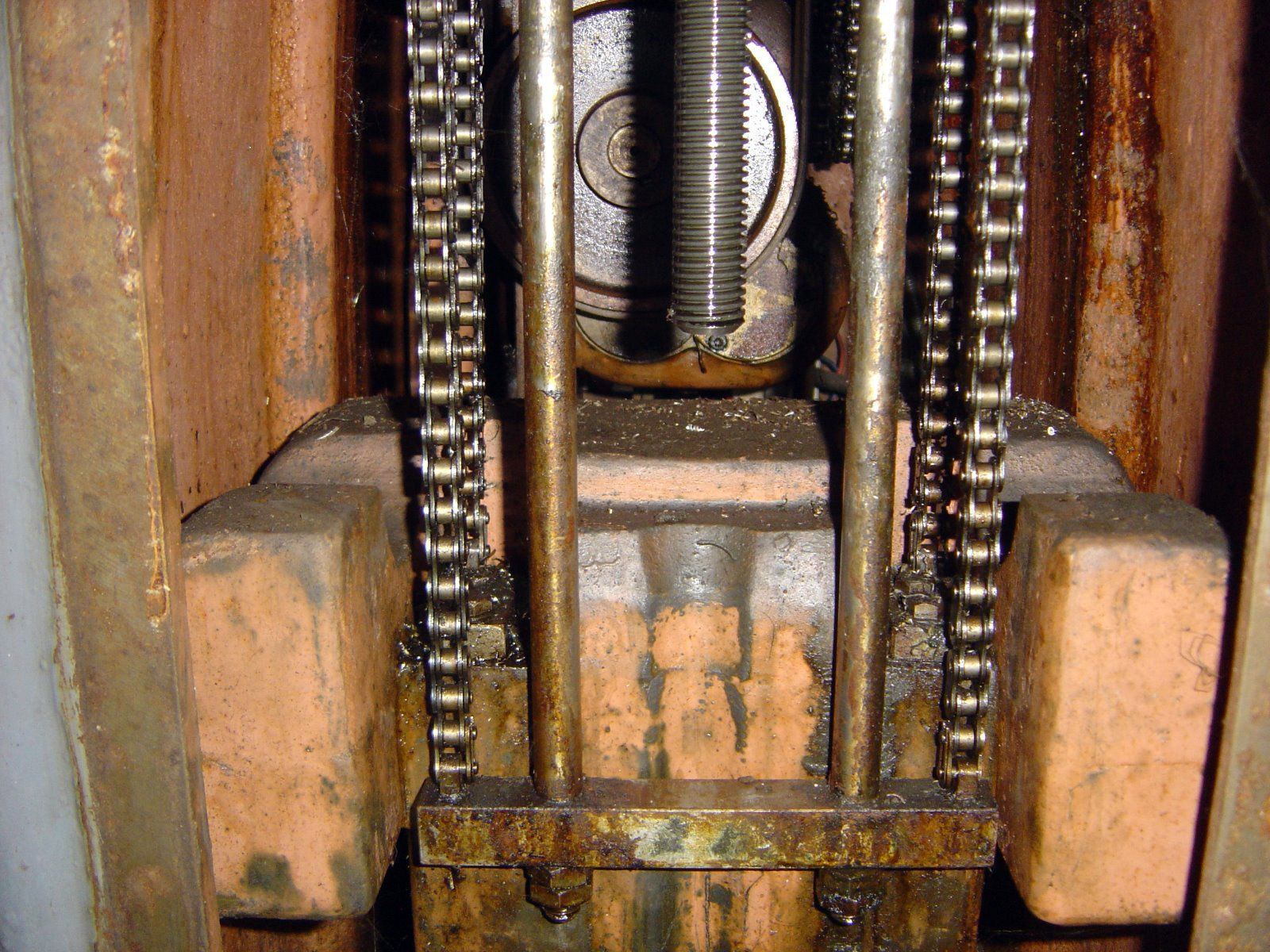 |
|
|
|
|
|
|
Chain-supported weight inside the column
|
|
|
|
|
|
|
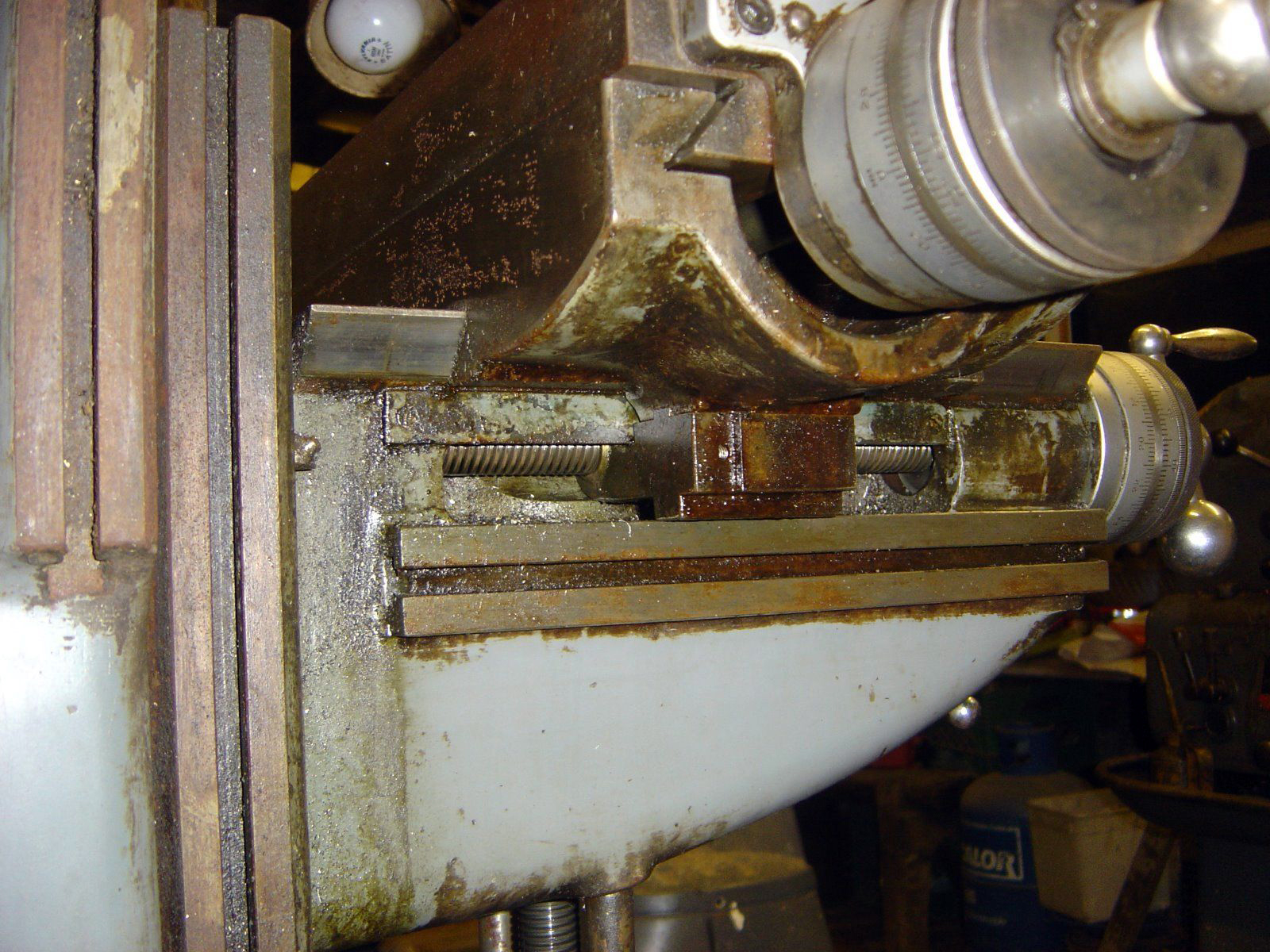 |
|
|
|
|
|
|
|
|
|
|
|
|
|
|
|
|
|
My Time at Hayes by Anthony Boyes - and other stories from the Company -
On leaving my Leeds, Yorkshire school in 1955 I worked for a few months in the same city at W. H. Baxter (Engineers) in Gelderd Road, Leeds 12 but, as this was heavy engineering making stone crushing machinery, I soon moved to Hayes, who were a proper precision engineering company, just 400 yards up the same road. I was with Hayes from mid 1955 to mid 1966 and, around 1962, we moved from Gelderd Road to 'Limewood Approach' to a brand-new, purpose-built factory near the ring road at Seacroft I finally left the company because I was playing in a band and we got a spot on TV "Hughie Greens - Opportunity Knocks" I mention this because I received a letter from all at Hayes wishing me good luck and, on checking this letter today, I counted it had been signed by 140 employees, so that's roughly how many worked at Hayes in mid 1966. Besides making the well-known milling machines (for which everything was produced in house except the castings), we also did a wide variety of sub-contract work; one job in particular I can remember was for DCMT (Die Cast Machine Tools) of London, for who we made "diecasters", a hot-metal casting machine that used two closed die blocs with hot metal injected under pressure and with a mechanism that, upon the opening of the blocks, ejected the finished casting. I believe the famous "Matchbox" and "Lesney" die-cast toys were made on these machines. DCMT sold the machines on to various companies but later on made toys themselves under the trade name "Lone Star". Gelderd Road The Gelderd Road works had earlier been a jam factory (Althams I believe). I know that whenever the maintenance department dug out the foundations to install a new machine they often found broken jam jars mixed with the soil. The factory had its goods' entrance on the main Gelderd Road with the office entrance down the street at the side. The factory was split level with the first 75ft having, on the right, a heat-treatment room and the flame profiling machines, on the left was the 'goods-inward' office and material store complete with a cut-off saw. 3 steps led up to the canteen and kitchens. At the end of this floor was a drop of about 30ft to the main production area, which was about 300 yds long and, at the bottom of the factory, another area, raised on columns, housed the electricians' department, the joiners' shop (we made our own packing cases for the finished machines), and an area for storing jigs. Upstairs, along the left-hand side of the factory, were the separate workers' and staff canteens, a kitchen and the administration and drawing offices. The main floor was divided into areas for capstan lathes, centre lathes, shaping machines, milling machines, grinding machines, a fitters' section, tool-room, inspection department and various 'downstairs' offices. In the middle of this area were the really large machines: a Butler Planer about 150ft long, a horizontal borer, a Lumsden magnetic-table grinder (which stood about 30 feet high) and other similar equipment. The employees on the large machines often had to work until late at night and on Saturday mornings to keep up with the demands of production. In Gelderd Road I started as an apprentice on the Capstan Lathes and later, with improving skills, became a Ward Capstan Lathe setter/operator. We used to employ a number of semi-skilled, handicapped people from Remploy to work the capstans and one day I was told to "Hurry up with the setting !"as he (the operator) was loosing bonus. This annoyed me no end, there being no bonus for the setter ! The semi-skilled workers normally tended one machine while I was busy setting another. During my first year with the company the main product was the Diemaster and, to a smaller extent, the sub-contracting mentioned earlier. I always thought the Diemaster owed its concept to the Bridgeport (we had one in the toolroom) a suspicion confirmed when, on occasions, the draughtsmen came down to measure it. The Tracemasters were then brought on line and, of course, the Hayes Ferranti Tapemaster (the Tapemaster used finely engraved rules to control its movement, one for each of the 3 axes under control of information on the tape). While the table remained on traditional Vee slides, the vertical knee and cross slide of the Tracemaster each used a hardened steel bar about 3" x 2" to guide the movement. Besides standard production models, over the years many special machines were made to fulfil one-off orders including a miller with 4 heads and a copy arm to machine, at one setting, all four combustion chambers of a car cylinder head. Another specially-constructed job was equipped with a loading and unloading conveyer system that offered up and removed camshafts to be machined with woodruff keys. Limewood Approach The Limewood Approach factory is now a textile wholesalers but it looks just like it did in the 60s, except for a newly-erected fence. The works had two bays each with its own crane whilst a pair of tracks with a bogey was used to move heavy things between the areas. At one point a nightshift was started but it didn't last very long, the dayshift putting forward the long-used excuse that they spent more time putting the nightshift work right than they did doing their own tasks. When we moved to Limewood Approach my job changed and I would move round from job to job depending on what needed to keep production moving smoothly. I worked mainly on the Butler Shaper, the Butler slotting machine and a very old broaching machine used to machine splines in gears, etc. This machine used to moan a lot and we fed it lard oil as a coolant. During this period other machines and hydraulic pumps, valves and copying valves were also made-- the latter three products also being offered to other manufacturers for fitting to their own machine tools. Machines were often sent to machinery exhibitions in London and, when sold abroad, one of our luckier fitters would be sent over to get the machine commissioned. After I left Hayes I still saw my old workmates here and there and they kept me up to speed with events. After that there was a management buy out and a move to smaller premises off Amberley Road, Tong Road, Leeds 12. I saw the factory there once, but I didn't seem to last long before it was gone. One of the fitters who used to go with the new machines when they were installed had all the plans and a customer list and began to offer a spare parts service--but this must have been before Tong Road finished because he was told that had no right to do this and he would be prosecuted if he carried on. However, the foreman of the capstan department, having managed to secure orders from DCMT for the sleeves and pistons for the Diecasters, left and set up his own company. These special parts, being made of EN32 or EN3 steel, were very difficult to machine and required specialist knowledge to get right.. A note from David Emmett: I was married to Moira, maiden name Hugill. Moira's dad Jim Hugill worked for Hayes as a senior engineer and works manager in the years before WW2. I don't know about his education or training except to say they he was an exceptional man, intelligent and gifted. He regularly gave talks/lectures to the Workers Educational Institute. I have a copy of the Socialist Sunday School hymn book that belonged to my wife Moira. Post 1945, he drove his little Morris 8 car to take people to the General Election, resulting in Atlee's Labour Government. He was a bit apprehensive about the prospect of victory because of the 'mess' that would have to be cleared up. A couple of stories ; in the years leading up to WW2 Jim, a committed member of the Labour Party was trying to warn people about the rise of Nazism and the persecution of Jewish people in Germany. Warning people about Oswald Mosley and the propaganda Mosley was promoting. While at Hayes, due to his senior position, he had a secretary. Her name was Adelheid Schweitzer. Adelheid had come to the UK in 1933. The reason being that she was told that, as a Jew, she could not attend University. She came to Leeds and was able to secure a passage for her husband Alfred, a medical scientist, to come to the UK. At the very last minute she was able to secure passage for her parents as well. Adelheid went back to London after the war to live in Hatch End, North London. Sadly, Adelheid's husband Alfred died in a climbing accident in the Swiss Alps in the early post-war years. So, Adelheid became Jim's secretary at Hayes. Jim died in 1946, the cause of death was Mitral Stenosis, a condition that is treatable today. He was a great cyclist, I think he belonged to a cycle club in Hunslet. He met his wife Harriet (Hetty) there. Jim. Hetty and their friends would take off on their tandems to explore the UK and Ireland whenever they could. The story is that Jim fell for Hetty when one day she fell off her bike for some reason and just sat there laughing. I hope this missive is a suitable addition to the Hayes annals. Dave Emmett. PS , Moira told me about her attendance at the annual Christmas Ball the company used to throw. My Beloved Moira died 4th Sept. 2020 due to Motor Neurone Disease. If you, too, worked at Hayes, or know more about the Company - especially dates - we would be delighted to hear from you.
|
|
|
|
|
|
|
|
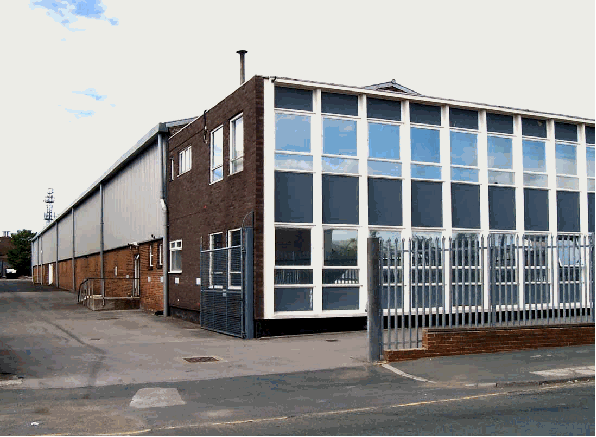 |
|
|
|
|
The former Hayes factory at 'Limewood Approach' photographed in 2005
|
|
|
|
|
|
|
|
|
|
|
|
|