 |
 |
 |
 |
 |
 |
 |
 |
 |
 |
 |
 |
 |
 |
 |
 |
 |
 |
 |
 |
 |
 |
 |
 |
 |
 |
 |
 |
 |
 |
 |
 |
|
|
|
|
|
|
|
|
|
|
|
|
|
|
|
|
|
|
|
|
|
|
|
|
|
|
|
|
|
|
|
|
|
|
|
|
|
|
|
|
E-Mail Tony@lathes.co.uk Home Machine Tool Archive Machine Tools For Sale & Wanted Machine Tool Manuals Machine Tool Catalogues Belts
Parkson M1200 and M1250 Milling Machines
Parkson/Parkinson Home Page Parkinson Adapta Mill
Operator's Manuals and Parts Book are available for the M1200 and M1250
Advice and possibly further help from a retired Parkinson engineer is available by phoning 0793-944052
"Parkson" was the name given to machine tools built by J. Parkinson & Son (Shipley) Ltd., an old-established English company founded during the late 19th century in an area famous for precision engineering. Manufactured from the late 1960s until the late 1970s (and into the 1980s as the improved M1250, shown lower down this page) the M1200 marked a radial departure for the Company in terms of both mechanical and cosmetic design. However, as an ordinary knee-type milling machine, it was offered in the three traditional models for the type: the P1 Plain Horizontal; U1 Universal (Horizontal with a swing table) and the V1 Vertical. These could, additionally, be equipped as the P2, U2 and V2 with auto-cycle table control on the longitudinal axis only or as the P3, U3 and V3 with the addition of a 25 mm (1") auto rise and fall to the knee. A more complex version, the Type 80PBT plug-board-controlled Millermatic, was also listed and designed for medium to large batch production - though it could also be operated in a manual mode. Because the standard machines were intended for regular use using only power feeds (and had only a single, removable handle for the feed screws) if sensitive, direct hand control of the table was needed (as in a toolroom for one-off jobs) the makers offered a special version fitted with handles that were permanently mounted. Distinctly styled, with ultra-modern, clean lines, the M1200 hid it mechanical complexity well with no exposed rotating parts, very tight packaging of components and easy-to-operate, all-electric joystick table controls complimented by an adjustable pendant that held a large table feed-rate selection dial, warning lights for mains power and correct operation of the pressure oil supply system, push buttons for emergency stop, feed-motor start, coolant on/off, spindle start, stop and inch and a spring-loaded rapid-traverse motor control button. Continued below:
|
|
|
|
|
|
|
|
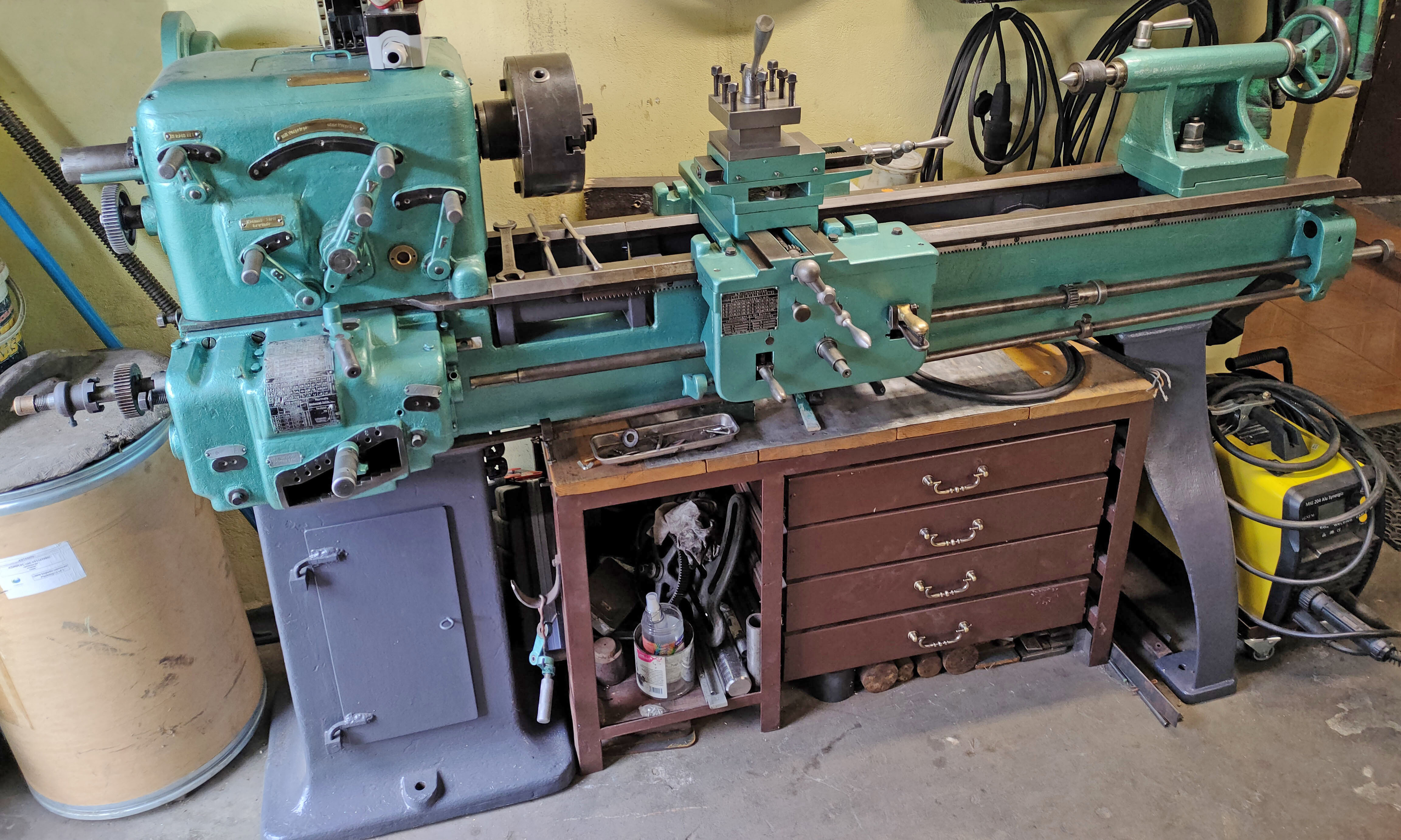 |
|
|
|
|
|
|
Parkinson M1200 vertical miller
|
|
|
|
|
|
|
|
|
Continued: Built as standard to an all-metric specification, it was possible to order (at extra cost) either dual-reading Imperial/metric feed-screw dials or with just inch feed screws and micrometer dials. All versions of the miller were fitted with the same size of table: on the first examples to be produced this was 1170 x 306 mm (46" x 12") but by 1971 had been increased in size to 1250 x 324 mm (49" x 12.75") with all types having three 18 mm (0.7") T-slots on 70 mm (2.756") spacing. Early short-table models had a longitudinal travel of 710 mm (28"), in traverse of 240 mm (9.5") and vertically of 430 mm (17") with long-table types having the same cross and vertical movements but with the longitudinal increased slightly to 750 mm (29.5"). On Universal Models the table could be swung 40° each side of central, the satin-chrome plated degree scale protruding neatly though a cut-out in the face of the table below the swing release knob. Table feeds were infinitely variable and powered by a Thyristor-controlled, 3 h.p. D.C. motor working through a flexible coupling that drove a speed-reducing worm-and-wheel gearbox - with the final drive transmitted through electro-mechanical clutches. Early models had their table-feed rates set at 13 to 812 mm (1/2" to 32") per minute on longitudinal and across motions and at 4 to 270 mm (1/6" to 10.6") per minute vertically. Later types, with the longer table, were modified to produce a rate of 13 to 1016 mm (1/2" to 40") per minute longitudinally and across and at 6 to 508 mm (0.3" to 20") per minute vertically. Rapids were provided on all feeds: on every type produced longitudinal and across were set at 1800 mm (72") per minute with the vertical rate suitably reduced to 610 mm (24") per minute on the short-table models and at 500 mm (20") per minute on the longer. Control of the table and knee movements was by two joysticks that provided drive in a directional sense (move a lever left and the table moved left, lift a lever up and the knee rose, etc.): the control for longitudinal and cross travel was positioned on the top face of the knee (but moved to the front face on Universal models in order to give clearance for the table to swing) and for vertical on the knee's left hand face. While early types of joystick were more akin to control rods; later ones were reduced in size and given a lighter action. For hand operation of the table and knee a single crank handle was provided (called a "swape" by the maker) that could be inserted into the appropriate socket to move table or knee as required. Normally it was left parked in a holder on the right-hand side of the knee - removing it activated a micro-switch that, as a safety precaution, isolated the powered traverses. To allow climb milling - an essential operation on some settings when using automatic cycle feeds - a longitudinal feed-screw backlash eliminator was fitted, its engagement being by turning a large castellated knob on the front face of the table. Common to all versions - horizontal and vertical - was, on the first two years' production, a spindle with a 40 INT nose and a 50 INT thereafter - though the 50 INT had always been offered as an extra-cost option from the start of production. Fitted at first with a 5.5 h.p. (flange-mounted) motor as standard, a 7.5 h.p. was listed as an extra - this situation lasting only a couple of years before the more powerful unit became part of the ordinary specification. 12 spindle speeds were provided in two ranges, Low and High: early machines had the slower set at 33 to 1250 r.p.m. and the faster at 66 to 2460 r.p.m. Later models (with the 7.5 h.p. motor) had speeds reduced, the two ranges being 27 to 995 r.p.m and 54 to 1950 r.p.m. Speeds were selected by three lever on the right hand face of the column, with the changes generated by a cartridge-type gearbox built into the main column and fitted with hardened and ground gears running on shafts supported in ball races. Manufactured from Nitralloy that had been induction hardened and ground, the horizontal spindle ran in a pair of opposed Timken taper roller bearings at the front and a ball race at the rear. Immediately behind the Timken bearings was a large drive gear, the mass of which (as argued by many makers of similar arrangements over the years) was supposed to impart a beneficial flywheel effect on work that involved interrupted cuts. Also made in an hardened and ground Nitralloy, the spindle in the swivelling vertical head ran in a pair of opposed precision Timken taper roller bearing immediately behind the 50 INT nose and a single roller bearing at the rear. The whole bearing assembly was mounted, in the usual way, inside a quill and could be moved through 75 mm (3") of travel by a handwheel. Able to be swung through 50° each side of upright, the head was located its vertical position - on a very large diameter mounting flange - by a tapered dowel and clamped in place by 4 widely spaced bolts. Surprisingly, in view of the potential need to turn small diameter cutters at higher revolutions, the vertical machines had exactly the same speed range as the horizontal models. Well ribbed internally for stiffness, the overarm was of box construction and mounted on ground slideways. Two arbor supports were provided, each fitted with a tapered bearing bush lubricated from a built-in oil well.. In standard form, in order to make best use of the huge amount of inch-specification tooling in use, the inner support was bored 2.25" and the outer 0.72". Likewise, the standard spindle drawbars were 1-in and 5/8-in BSW - though metric equivalents for all the parts associated with the arbor could be supplied. Lubrication was taken care of by a pressure pump driven from the spindle gearbox; both a sight-glass window and a green light on the pendant were provided to ensure oil was flowing - and should the oil pressure have fallen, to prevent the machine being used, a fail-safe device cut the power to the table's control joysticks. Oiling arrangements were particularly thorough with lubricant being pumped around the speed-change gearbox, the spindle bearings, the vertical, cross and longitudinal slideways and to the feed-screw nuts and backlash eliminator. In addition, the heavily stressed one-piece knee elevation screw was, like those on many Cincinnati machines, bathed in oil automatically supplied from a reservoir positioned higher up, inside the column. Continued below with details of the Parkson M1250
|
|
|
|
|
|
|
|
|
|
|
|
|
|
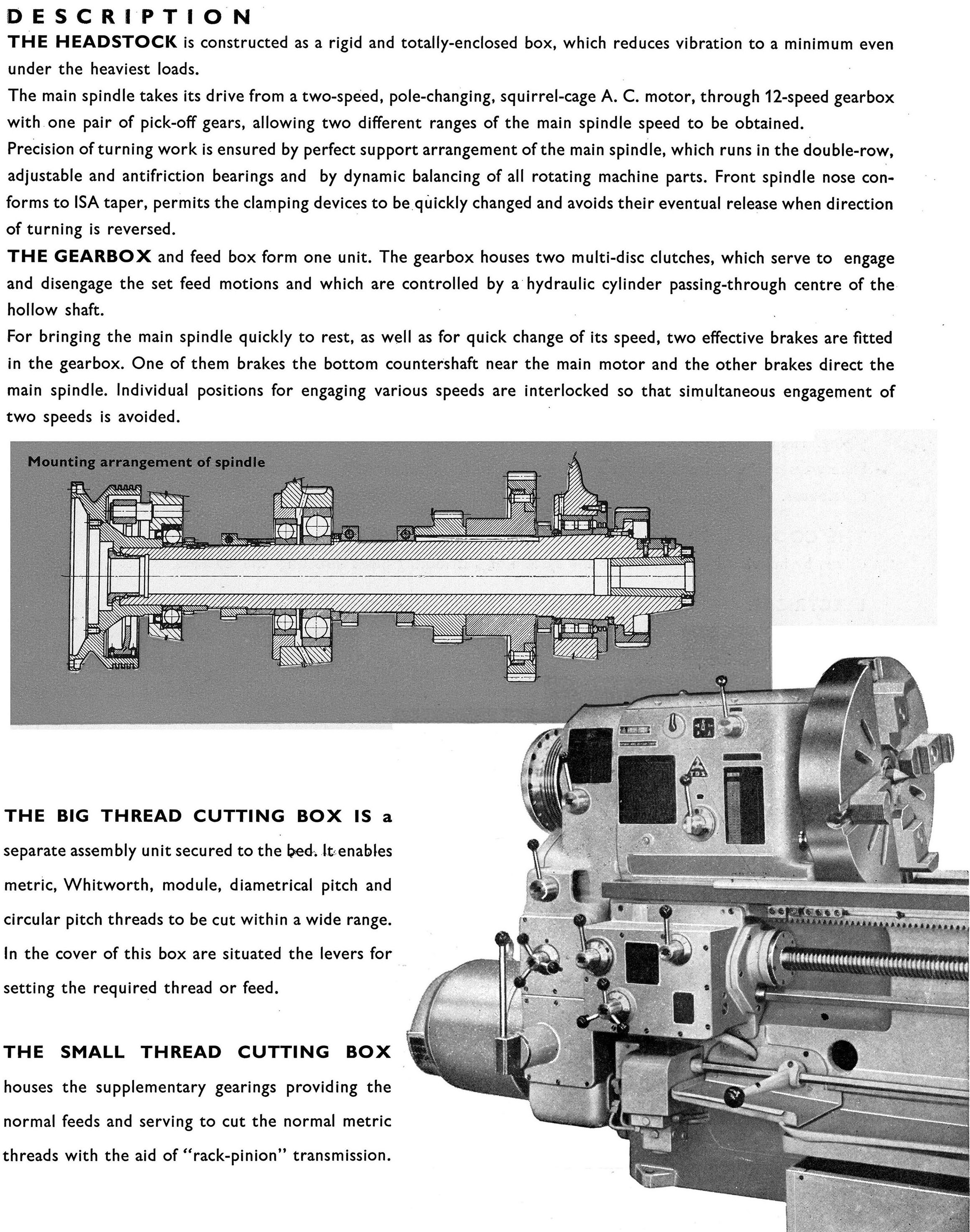 |
|
|
|
|
Parkinson M1200 plain horizontal miller
|
|
|
|
|
|
|
|
 |
|
|
|
|
|
|
M1200: standard vertical head
|
|
|
|
|
|
|
|
 |
|
|
|
|
|
|
M1200: Joystick controls for table and knee feeds
|
|
|
|
|
|
|
|
|
|
|
|
|
|
 |
|
|
|
|
|
|
M1200: Universal miller - locking knob for swing table and table-turn degree scale
|
|
|
|
|
|
|
|
 |
|
|
|
|
|
|
M1200 Spindle-speed chart and speed-change levers
|
|
|
|
|
|
|
|
 |
|
|
|
|
|
|
M1200: anti-backlash control for climb milling
|
|
|
|
|
|
|
|
 |
|
|
|
|
|
|
Detachable hand-feed handle parked on the right-hand face of the knee. Removing it isolated the drive motor
|
|
|
|
|
|
|
|
|
|
|
|
|
|
 |
|
|
|
|
|
 |
|
|
|
|
|
|
M1200: electrical control cabinet
|
|
|
|
|
|
|
|
|
Parkson M1250 Milling Machines
Developed during the late 1970s for sale during the 1980s, the M1250 was a direct descendent of the M1200 with an almost identical layout and the same 7.5 h.p. main and 3 h.p. feed motors. Intended to span the market for conventional, hand-operated machines and a rapidly increasing need for CNC control, a number of different versions were offered, though all still followed the tradition of being based on Plain horizontal, Universal (with swing table) and Vertical types, the maker's designations being, respectively: M1250P, M1250U and M1250V. As on the M1200, models fitted with Auto Table Cycle control were available, this time indicated by the suffix 2 for models with this facility on table and knee and 3 for models that could have more complex arrangements built in to a customer's specific requirements. Just one size of table - 1250 x 324 mm (49" x 12.752) - was offered for all versions, a size that made it identical to that used on all but the earliest of the M1200 models, through it did have 4 instead of 3 T-slots, each 18 mm (0.708") wide on a spacing of 70 mm (2.756"). Also unchanged were the table travels - 750 mm (29.5") longitudinally, 240 mm (9.5") in traverse and vertically at 430 mm (17") - and the variable-speed feed rates - from 13 to 1016 mm per minute on longitudinal and across and 6 to 508 mm per minute vertically. Changes to the controls meant the elimination of the table movement joysticks and their replacement on the pendant by 6 electrically interlocked push buttons to operate the 3 axes of travel in each direction. Instead of a single crank handle used on the M1200 to share between the feed screws when the table had to be positioned by hand, on the M1250 the screws were each fitted with spring loaded cranks - but only one was fitted to the table, at its left-hand end. One minor change was to the knee-locking handle, this being moved from the inside edge and extended outwards so that the operator could reach it from the front. On the vertical miller the bearing arrangement inside the head was altered, the top ball race being replaced by a pair of opposed taper-roller bearings, as at the bottom - this change in design resulting in a particularly stiff and well-supported spindle. As an option the head could be fitted with a power down-feed unit - though this is so rare a device that specification details are unavailable. CNC controls were offered by Phillips, Anilam, Heidenhain and RSF - Parkinson suggesting that customers study the detailed and particular features offered by each before making a decision.
|
|
|
|
|
|
|
|
|
|
|
|
|
 |
|
|
|
|
|
|
Parkson M1250 plain horizontal miller
|
|
|
|
|
|
|
|
 |
|
|
|
|
|
|
Parkson M1250 universal miller
|
|
|
|
|
|
|
|
 |
|
|
|
|
|
|
Parkson M1250 vertical miller
|
|
|
|
|
|
|
|
|
|
|
|
|
|
 |
|
|
|
|
|
|
M1250: Anti-backlash control for climb milling
|
|
|
|
|
|
|
|
 |
|
|
|
|
|
 |
|
|
|
|
|
|
M1250: knee mounted controls for traverse and vertical feeds
|
|
|
|
|
|
|
|
|
|
|
|
|
|
 |
|
|
|
|
|
|
M1250: section through the front bearing of the horizontal spindle showing the taper roller bearings
|
|
|
|
|
|
|
|
 |
|
|
|
|
|
|
M1250: universal model, degree indicator for table swivel
|
|
|
|
|
|
|
|
 |
|
|
|
|
|
|
M250: standard vertical head
|
|
|
|
|
|
|
|
 |
|
|
|
|
|
|
|