 |
 |
 |
 |
 |
 |
 |
 |
 |
 |
 |
 |
 |
 |
 |
 |
 |
 |
 |
 |
 |
 |
 |
 |
 |
 |
 |
 |
 |
 |
 |
 |
 |
 |
 |
 |
 |
 |
 |
 |
 |
 |
 |
 |
 |
 |
 |
 |
 |
 |
 |
 |
 |
|
|
|
|
|
|
|
|
|
|
|
|
|
|
|
|
|
|
|
|
|
|
|
|
|
|
|
|
|
|
|
|
|
|
|
|
|
|
|
|
|
|
|
|
|
|
|
|
|
|
|
|
|
|
|
|
|
|
|
|
|
|
|
|
|
|
|
|
|
|
|
Made by the Jackson-Rigby Company of Shalford, Surrey - established railway engineers who concentrated on parts for miniature steam locomotives - the "JR" is also found badged as the "JRC. Some lathes had these letters cast into the front of the headstock while others had a screwed-on aluminium "JR" badge - presumably on top of the original "JRC" lettering. Production of lathe may have resulted from the company becoming associated, in 1922, with the well-known locomotive designer, Mr. Henry Greenly. Greenly is said to have made some improvements to the original JR design, but the lathe cannot have been manufactured for long, probably only from 1922 until 1926 - the year Jackson-Rigby was sold (or merged) into the Romney, Hythe, and Dymchurch Railway in Kent and just before that company launched its "miniature" main-line steam service from the Cinque Port of Hythe. Much smaller than it appeared (just 26 inches long and 18 deep - the length of the foot pedal - and standing 43 inches high) it was made in 3 and 4-inch centre heights with around 12 inches between centres (the example below is a 3-inch version ) and was especially well-built, with a number of thoughtful and beautifully engineered details. The unusual (and very compact) cast-iron stand resembled that used on many EXE lathes with a flywheel overhung on the left-hand side and a foot pedal, connected to a very heavy crank on the other. Huge individual "JR" letters were cast between the stand uprights - there could be no mistaking who the maker was. Two slower speeds were provided by grooves (to take round 1/4" leather belt) cut near the rim of the 18.5-inch diameter flywheel, while a single, much smaller pulley, was mounted close to the centre for a single high speed that required the use of a separate belt.. Cast as-one with the headstock, the flat-topped, 60-degree edged, cantilever-form bed had a gap as standard - with a faceplate capacity of 8-inches in diameter by 2-inches thick. The design allowed the structure to remain distortion free as it was bolted down (using three closely-spaced bolts under the headstock end) the makers using a wooden tray between the lathe and stand through which the fastenings had to pass. As a finishing touch, the ground top surface of the bed, and the top of the lower tool-slide casting were given a number of decorative scraping marks - though these might also have served to trap a little oil on the surface. Fitted with Hoyt "copper-hardened" split bearings, closed down by slots positioned to the rear, the elegant headstock carried a spindle with the No. 1 Morse taper and a large 3-step cast-iron pulley arranged for drive by a leather 'gut" rope. The bearings were lubricated by wick-feed oilers (so precluding any dirt from entering the assembly) with each protected by a tight-fitting, snap-on cover (when most other small lathes made do with a crude, unprotected hole drilled through the casting). With no backgear fitted (nor any evidence that one could be mounted as an option) the size of the pulley (again, like that on an EXE) would have allowed a reasonably slow bottom speed to be obtained. Continued below:
|
|
|
|
|
|
|
|
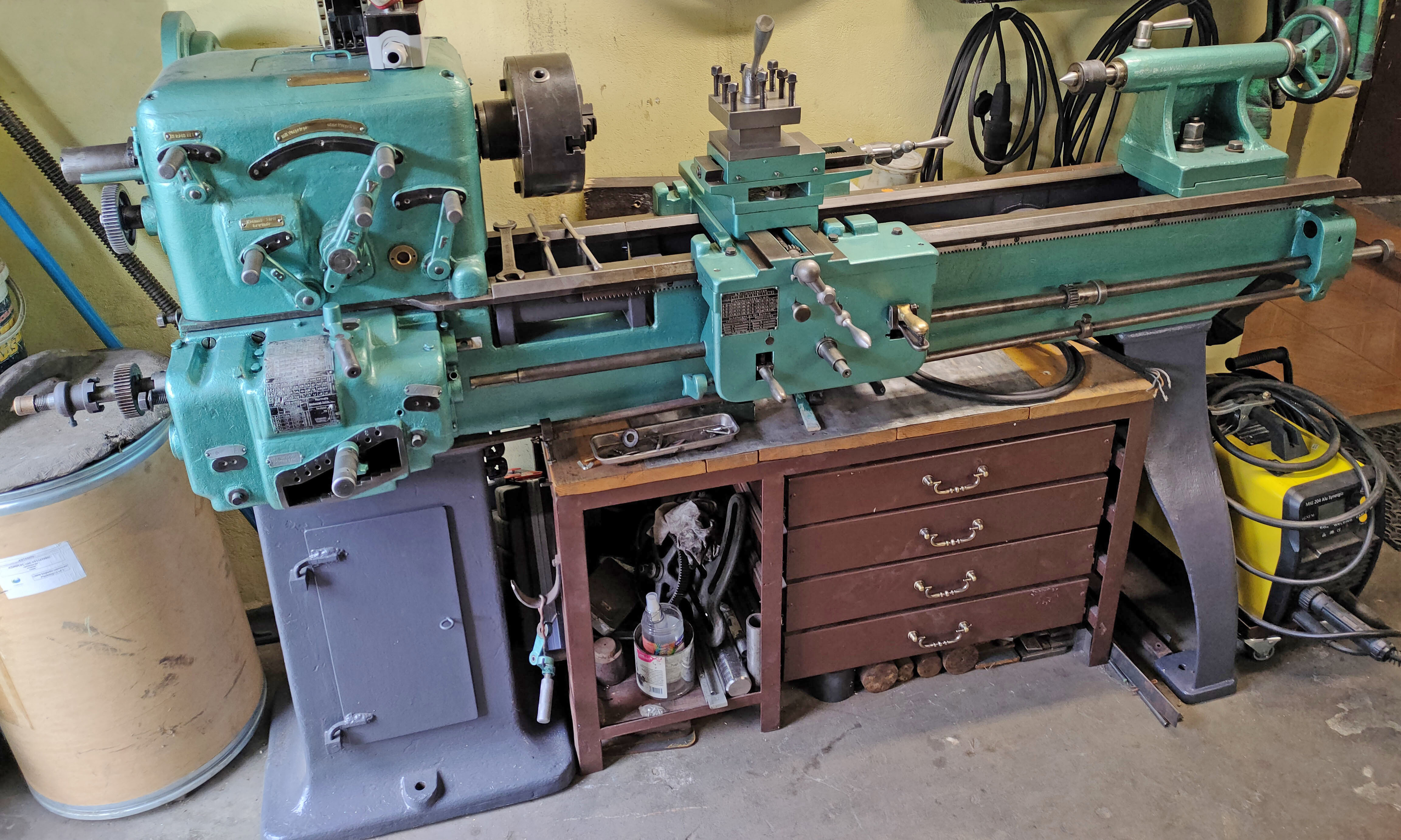 |
|
|
|
|
|
|
|
|
|
Jackson-Rigby lathe of the early 1920s
|
|
|
|
|
|
|
|
|
|
|
Continued: Screwcutting was by changewheels, of the same pitch as used on Myford lathes, carried on a bracket with three slots of a rather complex arrangement. The gears were retained by simple and quick-to-release wire clips each of which was sprung into a groove on the end of the mounting studs, Unfortunately, the arrangement of the bracket slots, although it permitted (via a fourth curved slot at the back) very fine adjustment of the gear mesh, precluded the fitting of a compound gear train with large-diameter wheels - a forked bracket would have been so much more effective in this respect. However, by incorporating two 20t gears in the train, feeds as fine as 268 t.p.i could still be achieved. Drive to the 5/8" diameter, 10 t.p.i. square-thread leadscrew passed through a dog clutch, built neatly into the headstock-end leadscrew hanger bracket. Cleverly, in order to allow precise alignment and obtain the smoothest possible feed, the leadscrew support bearings units were bolted on, that at the headstock to the face of the casting whilst at the tailstock end a bracket was fastened across the end face of the bed (just like a Lorch LAS). Saddle and apron were cast as-one, with the latter carrying an inserted bronze nut of the "full" type - and thus the carriage could only be moved along the bed by either a power feed through the changewheels or by a handwheel on the end of the leadscrew. The latter was, very unusually for a lathe of this class and size of lathe, fitted with a friction-setting micrometer dial. Instead of being bolted on, the cylindrical leadscrew nut was well supported by a simple apron, cast as-one with the saddle - the makers resisting the cost-cutting temptation to put the thread inside the cast-iron of the apron itself….. A usefully large boring table (6" x 3.5") was fitted with three, good-sized traverse T-slots, and a single, swivelling top slide complete with an "American" style "lantern" toolpost. The slide's feed screw (with an ordinary Whitworth thread) ran though a bronze nut and was fitted with a small but finely-engraved micrometer dial. The slide, which had 2.5" of travel, was secured to the boring table by a single round-headed "T-bolt" turned by a rear-facing lever that permitted a movement arch of only some 30° (it was not necessary to use a spanner to adjust the position of the slide). Combined with the ingenious but frustrating design of the T-bolt - it was pushed up into a cavity, threaded into a distance piece and then dropped to engage a pin on its side with a slot in the hole - meant that some care had to be taken with the settings so that the slide could be fitted and then locked securely. The writer found that the only way of obtaining a satisfactory comprmise on his JR (the little-used example below) was to surface grind the lower face of the distance piece, a little at a time, to achieve the right setting. For a small lathe the tailstock was very robust, with a 2.25-inch travel spindle that automatically ejected its No. 1 Morse taper centre at the end of the travel. If you can add anything to the JR story, the writer would be pleased to hear from you..
|
|
|
|
|
|
|
|
|
|
|
|
|
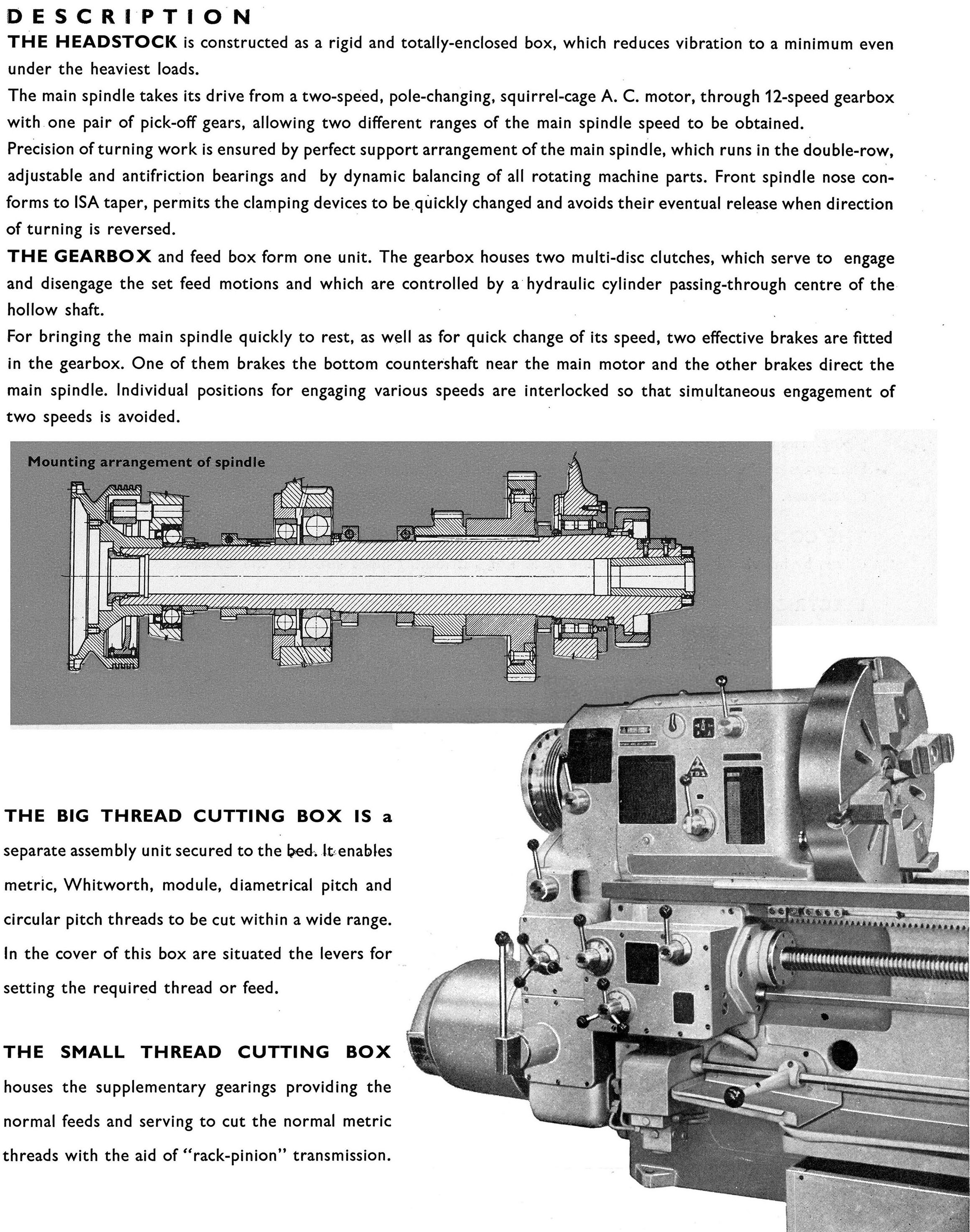 |
|
|
|
|
|
|
|
|
Complete on its treadle stand. The lathe was much smaller than it appeared: just 26 inches long and 18 deep (the length of the foot pedal) and standing 43 inches high
|
|
|
|
|
|
|
|
|
|
 |
|
|
|
|
|
|
|
|
|
Fitted with Hoyt "copper-hardened" split bearings, closed down by slots positioned to the rear, the elegant headstock carried a spindle with the No. 1 Morse taper and a large 3-step cast-iron pulley arranged for drive by a round leather 'gut" rope.
|
|
|
|
|
|
|
|
|
|
|
|
|
|
|
|
 |
|
|
|
|
|
|
|
|
|
Each headstock bearing was lubricated by a wick-feed oiler covered by a snug-fitting snap-on cap. Note the changewheels - secured by spring clips that snapped over the ends of their mounting studs
|
|
|
|
|
|
|
|
|
|
 |
|
|
|
|
|
|
|
|
|
A dog clutch was built neatly into the headstock-end leadscrew hanger bracket
|
|
|
|
|
|
|
|
|
|
 |
|
|
|
|
|
|
|
|
|
An almost unheard of luxury on a small lathe from the early 1920s - a graduated handle to the leadscrew end.
|
|
|
|
|
|
|
|
|
|
 |
|
|
|
|
|
|
|
|
|
Cleverly, in order to allow precise alignment and obtain the smoothest possible feed, the leadscrew support bearings units were bolted on, that at the headstock to the face of the casting whilst at the tailstock end a bracket was bolted across the end face of the bed (just like a Lorch LAS).
|
|
|
|
|
|
|
|
|
|
|
|
|
|
|
|
 |
|
|
|
|
|
|
|
|
|
A usefully large boring table was fitted, with three good-sized traverse T-slots, with a single swivelling tool-slide complete with an "American" style "rocking" toolpost and a feed screw (that ran though a bronze nut) fitted with a small but finely-engraved micrometer dial.
|
|
|
|
|
|
|
|
|
|
 |
|
|
|
|
|
|
|
|
|
The boring table was fitted with three good-sized T-slots
|
|
|
|
|
|
|
|
|
|
 |
|
|
|
|
|
|
|
|
|
Underside of the swivelling tool-slide. It was secured to the boring table by a single round-headed "T-bolt" turned by a rear-facing lever that was permitted a movement arch of only some 30° ( it was not necessary to use a spanner to adjust the position of the slide).
|
|
|
|
|
|
|
|
|
|
 |
|
|
|
|
|
|
|
|
|
|
|
 |
|
|
|
|
|
|
|
|
|
Component parts of the tool-slide locking mechanism
|
|
|
|
|
|
|
|
|
|
 |
|
|
|
|
|
|
|
|
|
Lower casting of the single swivelling tool-slide
|
|
|
|
|
|
|
|
|
|
 |
|
|
|
|
|
|
|
|
|
Unfortunately, the arrangement of the changewheel bracket slots, although it permitted (via a fourth curved slot at the back) very fine adjustment of the gear mesh, precluded the fitting of a compound gear train with large-diameter wheels - a forked bracket would have been so much more effective in this respect
|
|
|
|
|
|
|
|
|
|
 |
|
|
|
|
|
|
|
|
|
|
|
 |
|
|
|
|
|
|
|
|
|
Saddle and apron were cast as-one with the latter carrying an inserted bronze nut
|
|
|
|
|
|
|
|
|
|
 |
|
|
|
|
|
 |
|
|
|
|
|
|
|
|
|
|
|
 |
|
|
|
|
|
|
|
|
|
The unusual (and very compact) cast-iron stand resembled that used on many EXE lathes with a flywheel overhung on the left-hand side and a foot pedal, connected to a very heavy crank, on the other.
|
|
|
|
|
|
|
|
|
|
 |
|
|
|
|
|
 |
|
|
|
|
|
|
The "JR" badge may have been screwed on top of the original "JRC" cast-in badge
|
|
|
|
|
|
|
|
 |
|
|
|
|
|
|
|
|
|
The "JRC" badge cast into the headstock
|
|
|
|
|
|
|
|
|
|
|
|
|
|
|
|
|
|